筒式地下车库可行性报告.docx
《筒式地下车库可行性报告.docx》由会员分享,可在线阅读,更多相关《筒式地下车库可行性报告.docx(28页珍藏版)》请在冰豆网上搜索。
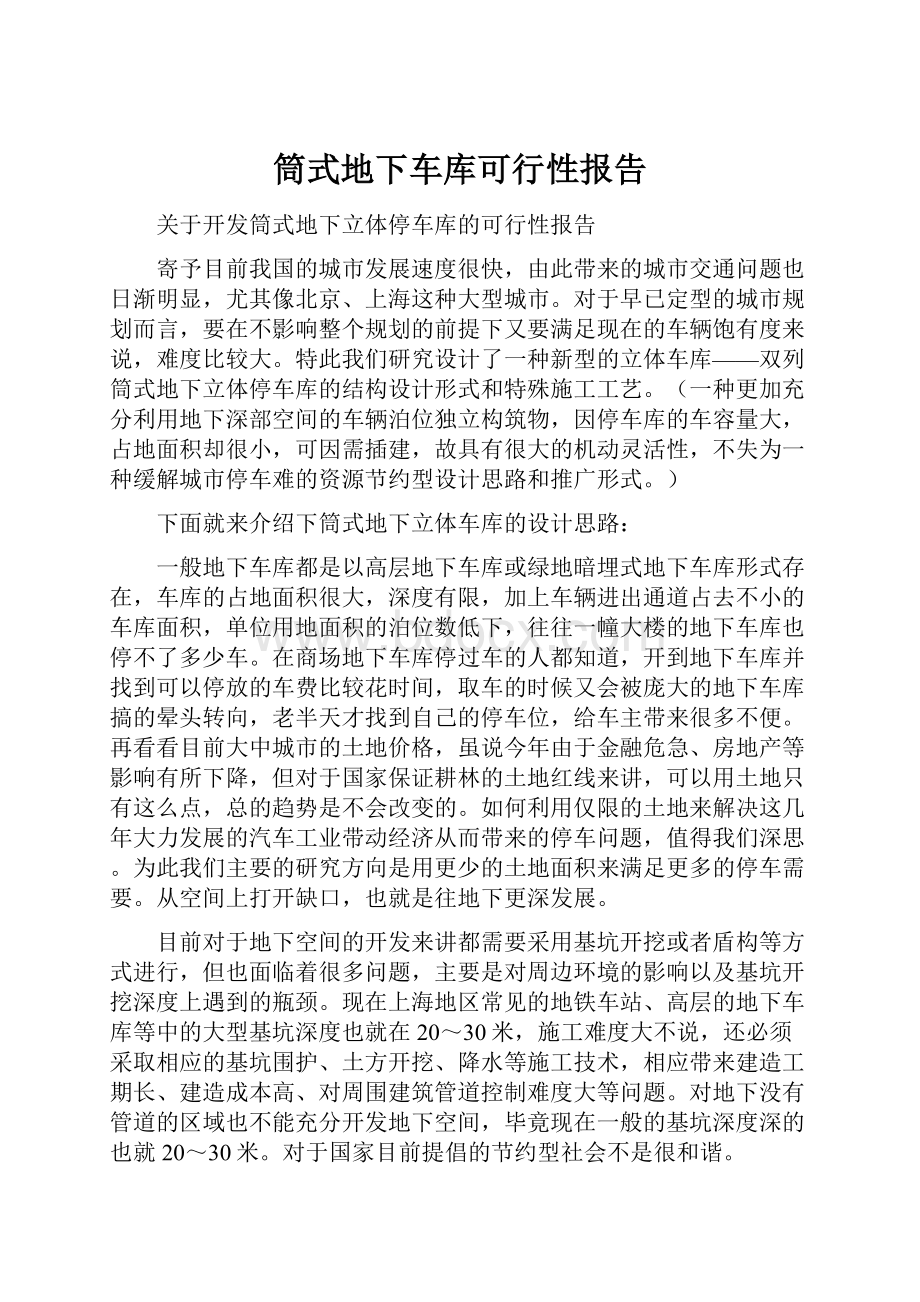
筒式地下车库可行性报告
关于开发筒式地下立体停车库的可行性报告
寄予目前我国的城市发展速度很快,由此带来的城市交通问题也日渐明显,尤其像北京、上海这种大型城市。
对于早已定型的城市规划而言,要在不影响整个规划的前提下又要满足现在的车辆饱有度来说,难度比较大。
特此我们研究设计了一种新型的立体车库——双列筒式地下立体停车库的结构设计形式和特殊施工工艺。
(一种更加充分利用地下深部空间的车辆泊位独立构筑物,因停车库的车容量大,占地面积却很小,可因需插建,故具有很大的机动灵活性,不失为一种缓解城市停车难的资源节约型设计思路和推广形式。
)
下面就来介绍下筒式地下立体车库的设计思路:
一般地下车库都是以高层地下车库或绿地暗埋式地下车库形式存在,车库的占地面积很大,深度有限,加上车辆进出通道占去不小的车库面积,单位用地面积的泊位数低下,往往一幢大楼的地下车库也停不了多少车。
在商场地下车库停过车的人都知道,开到地下车库并找到可以停放的车费比较花时间,取车的时候又会被庞大的地下车库搞的晕头转向,老半天才找到自己的停车位,给车主带来很多不便。
再看看目前大中城市的土地价格,虽说今年由于金融危急、房地产等影响有所下降,但对于国家保证耕林的土地红线来讲,可以用土地只有这么点,总的趋势是不会改变的。
如何利用仅限的土地来解决这几年大力发展的汽车工业带动经济从而带来的停车问题,值得我们深思。
为此我们主要的研究方向是用更少的土地面积来满足更多的停车需要。
从空间上打开缺口,也就是往地下更深发展。
目前对于地下空间的开发来讲都需要采用基坑开挖或者盾构等方式进行,但也面临着很多问题,主要是对周边环境的影响以及基坑开挖深度上遇到的瓶颈。
现在上海地区常见的地铁车站、高层的地下车库等中的大型基坑深度也就在20~30米,施工难度大不说,还必须采取相应的基坑围护、土方开挖、降水等施工技术,相应带来建造工期长、建造成本高、对周围建筑管道控制难度大等问题。
对地下没有管道的区域也不能充分开发地下空间,毕竟现在一般的基坑深度深的也就20~30米。
对于国家目前提倡的节约型社会不是很和谐。
一般目前有些采用沉井或者环向钢筋混凝土地下连续墙施工方法,通常都会带来一些技术上的问题,比方:
1沉井的深度不大通常也就20米左右且位移偏差大;
2环向地下连续墙各环向段之间的渗漏问题;
32种方法都采用底板后浇法,在底板和井壁连接处的渗漏问题;
4都需要采取基坑开挖及基坑降水,对周边环境影响较大
为了弥补这些问题,我们结合20年来在深层曝气井的施工经验,并参考沉井技术及煤矿矿井技术的技术推出一种新型的地下空间开发施工技术,并首先提出应用于地下车库的建造。
一个筒式地下立体车库的占地面积,井深50m或60m车库的轿车泊位60辆或72辆,平均每辆车的占地面积仅为m2或。
利用升降原理来停取车辆,筒式地下车库的驱动减速机安装在井筒顶部上方的机房内,车辆出入库由地面车道直接驶入位于井筒中间的载车升降台(俗称载车板),升降机将载车板降至预定深度后,经内置回转盘送入停放泊位。
顶部机房高出地表。
筒式地下立体停车库建造施工工艺流程如下:
(一)孔壁围护加固
鉴于筒式地下立体车库的超大筒体直径(结构体外径大于10m),从工艺要求出发,成孔直径约11m。
对于软土地区这样大的孔径,孔壁围护之目的就在于必须处理好成孔和筒体浇筑全过程的孔壁稳定性问题,防止孔壁缩颈、坍塌,继而引发周围地面的沉降,对周边邻近建筑、道路和地下设施造成结构或功能损害性影响。
孔壁围护加固方法的选择,主要依据成孔深度内的地层性质酌情确定,同时也要考虑加固方法的可行性、可靠性和经济性。
在此前提下,根据地层条件确定围护加固设计方案。
围护加固有多种方法可供选择,这里简要介绍适宜于第四系覆盖层的部分围护加固方法,如:
1)钻孔灌注桩排桩辅以桩间的高压旋喷或高压注浆方法的环状围护墙,或邻桩交割连接工艺方式的钻孔灌注桩环状围护墙。
这两种围护方法具有结构强度大、墙体入土深度大的特点,但造价比较高,故不予首选。
2)SMW工法环状连续墙。
该方法一般可满足泥浆护壁钻进成孔工艺的孔壁围护要求,造价比较低廉,但墙体入土深度受桩机设定能力的限制,国内三轴桩机的成桩深度不超过30m,近年从日本进口的同类三轴桩机可达48m深度,但数量很少;此外对于特别密实砂性土层,它的钻进搅拌功能会受到应限制,宜据土层性质和筒深而定。
3)高压旋喷法环状连续墙。
该方法可满足泥浆护壁钻进成孔工艺的孔壁围护要求,造价也较低廉,其有效旋喷深度一般为35m,超过35m的浆液旋喷半径趋小,但可配以高压注浆法予以处理,是较为适宜的加固手段。
环状连续墙的加固深度视筒底段的土层性质确定,一般应大于筒底标高2m以上(见附图13)。
(二)锁口施工
筒式地下双列式车库锁口规格表1
最小
井筒
内径
(mm)
井筒
外径
(mm)
钻孔
孔径
(mm)
围护
墙内
外径
(mm)
锁口
深度
/竖高
(m)
锁口内台肩深度/
最小宽度
(m)
台肩面以上部分竖高)锁
口的外宽/壁厚
(m)
深度
以下锁口
内径/壁厚
(m)
9400
10300
11000
11200/13200
12800/200
11200/450
说明:
1、锁口竖向总长(按上海正常地层,浅部为暗浜或松软填土的,宜适当加深),内侧设低于地面1m(低于锁口顶端)的作业台肩;台肩面以上锁口水平截面呈正方形,其内侧边长,壁厚200mm。
台肩厚700mm。
2、锁口砼总方量约100.5m3,锁口台肩总承压面积约75.7m2,单排桩桩端总截面积约36m2。
3、按排桩抗压强度1MPa、竖向应力偏心系数的锁口台肩允许承载力标准值为15120kN(×1000×36×,承载力设计值为13650kN(从尽量减小锁口沉降考虑,分项系数取:
(7560÷2)。
台肩最大允许附加重力(扣除桩顶正上方混凝土重力)为6880kN(13650-25kN/m3×45m2×0.6m)。
按表1尺寸进行钢筋混凝土锁口基坑开挖和锁口施工。
基坑开挖应防止对孔壁加固结构的损伤,开挖接近锁口台肩底面标高时,须用人工开挖修平。
一旦损坏,应用水泥砂浆予以修补。
期间还应进行以下工作:
(1)泄浆孔槽设置:
口浇筑前,于泥浆坑方位预设一根ф150PVC管作为泄浆孔,泄浆孔底标高低于地面1.2m(见附图1)。
(2)预埋件设置:
1)锁口Ф11000内壁按设计要求安设8对扶中装置的预埋钢板(见附图1);2)台肩面和锁口顶面分别安装8对卷扬提升滑轮支架固定安装预埋件(见附图1)。
(3)钻机坪台浇筑:
依据钻机进撤轨道方位,铺设适宜宽度、厚度的素砼地坪,使与锁口顶面标高一致。
(4)卷扬机地锚基础浇筑:
按见附图1浇筑8台卷扬机地锚基础。
在8个等分方位设置卷扬安装基础的地锚和钢筋混凝土基础,锚固力应不小于单个卷扬最大提吊力的2倍。
(锚固基础与地锚结构设计可与锁口结构结合起来,以借助锁口刚度和抗位移能力,节约锚固成本)
(5)井筒扶中装置安装:
按附图1所示位置,在钢锅底放入孔内后将8副扶中装置安装于圆形锁口内壁的预埋件上。
安装前,应先在扶中器内侧面安装防冲击木质条板或橡胶带。
8副扶中装置内侧面构成的直径宜为10.40m,即筒壁居中情况下,扶中装置内侧面与筒壁外壁面的单侧间隙为5cm,与底板钢模套外壁面的单侧间隙为4cm。
(三)钻进成孔
选用KTY-5000工程钻机,采用“一钻多扩法”泥浆护壁成孔。
钻进成孔孔径为,经“一钻四扩”达到设计孔径。
成孔垂直度允许偏差小于%。
钻进成孔前,需做好泥浆循环系统的准备工作。
泥浆池深度必须考虑其最高液面标高受锁口泄浆孔槽底面深度的制约。
钻进成孔前,宜先用小直径钻头按一定孔距均匀布点成孔,以减小大直径钻头成孔的阻力和排浆量,这样,可实现“一钻三扩”达到孔径11m之目的。
“一钻四扩”或“一钻三扩”钻进参数详见表2。
KTY-5000钻机“一钻多扩”成孔直径一览表表2
一钻
一扩
二扩
三扩
四扩
五扩
扭矩
孔径
扭矩
孔径
扭矩
孔径
扭矩
孔径
扭矩
孔径
扭矩
孔径
32.5f
5000
30.5f
7000
31.6f
8600
27.9f
9800
26f
10800
28.5f
11800
35.1f
5200
35.2f
7400
33.4f
9200
34.3f
10400
33.3f
11600
30.5f
12600
37.8f
5400
36.3f
7600
34f
9200
35f
10600
33.9f
11800
37.5f
13000
40.6f
5600
37.4f
7800
39.6f
9600
36.4f
11000
35.1f
12200
38.7f
13400
43.5f
5800
42.6f
8200
41.4f
10000
43.6f
11600
43.4f
13000
41.1f
14200
说明:
1.“一钻”所列扭矩为该钻机的最大扭矩,本表以第四系岩土层为条件,假设了KTY-5000钻机在不同土层条件下可能达到的最大扭矩。
并在此基础上计算各次扩径的可能达到的成孔直径。
表中孔径单位为mm。
2.表中f是以半径增量0.1m为最小力臂计算单位所对应的梳齿钻头刮刀平均扭阻力。
(四)底板钢模套拼装
本工序与钻进成孔同步进行,并于成孔结束前完成,以确保及时吊装。
拼装点宜位于邻近孔口,并不受钻机进撤位置、泥浆坑位置和卷扬锚固基础的干扰。
(1)按附图2将预先加工好的12块扇形椭球面钢板(中心为圆板)置于安装托架上拼接;
(2)按附图2将预先加工好的底板外周异径圆环钢模套与底板椭圆钢模套焊接;
(3)按附图2将预先加工好的1米高筒壁外周钢模套焊接;
(4)按附图2于底板顶面标高的异径圆环钢模套外缘安装顶滑轮起重吊点,起吊点应搭接于底板的钢筋上形成一定的通过底板混凝土路径。
具体情况详看钢模加工图纸。
(五)底板钢筋安装
钢锅底拼接完成后安装底板钢筋和第一段高滑模顶升承重钢管,凡钢筋端头和钢锅底的接触面之间全部焊接,竖筋和锅底径向筋的交界处全部焊接,见附图3,配筋计算如下:
筒体配筋计算表表3
外管内力计算
R0=
4.925m
t2=
0.45m
S=
1.13m
H=
65m
H/S=
Hc=
16.97m
H2c/dt=
Hm=
q_tri=
kPa
q_sq=
kPa
竖向弯矩和环向弯矩
Mx_tri=
kNm/m
Mx_sq=
kNm/m
Mx_sum=
kNm/m
Mt_sum=
kNm/m
环向轴力
Nt_tri=
kN/m
Nt_sq=
kN/m
Nt_sum=
kN/m
剪力
Qx_tri=
kN/m
Qx_sq=
kN/m
Qx_sum=
kN/m
圆形底板内力计算
Mr_=0
kNm/m(0*R)
Mt_=0
kNm/m(0*R)
Mr_=
kNm/m*R)
Mt_=
kNm/m*R)
Mr_=1
kNm/m(1*R)
Mt_=1
kNm/m(1*R)
筒壁抗弯刚度计算
+10Pa
MFw=
+08
圆形底板抗弯刚度计算
h_p=
1.6m
MFp=
+09
弯矩分配系数
k_w=
k_p=
径向分配弯矩
Mwp=
kNm/m
M_w=
kNm/m
M_p=
kNm/m
M_w=
kNm/m
M_p=
kNm/m
竖向配筋计算
MPa
A
N0
e0=M/N0
l0/h
(<15)
1=N
(>1)
2=
ei/h0
fcA
+08
ei
Fc
+08
fs
As=
(<0)
环向配筋计算(查表法)
e0=M/N0
l0/h
1=N
2=
ei/h0
nfcbh0
E=ei/h0
as/h0=
(%)=
As=As'=
实配
18@150
1696
底板构造钢筋
As=
实配
2@150
在底板顶层钢筋上,按半径圆弧线位置间隔焊接竖向钢筋,作为筒壁底部2米段高内侧木模地脚的限位装置,钢筋上端宜高出底板混凝土面7~8cm(或按大于木模板厚度2cm确定),竖向限位钢筋间距20cm(或与木模板宽度相同),钢筋直径以确保混凝土浇注过程木模板地脚不移动为度。
(六)底板钢模套吊装
锁口养护至设计强度后安装钻机钢梁结构施工平台,然后开始成孔钻进。
(1)卷扬提吊系统的安装:
卷扬安装应在成孔工序结束前完成,并与钻机及钢梁撤离后立即安装卷扬支架,敷设钢丝绳。
(2)底板钢模套整体吊装:
整体吊装重力包括底板钢模套、2米高筒壁外侧圆环钢模、底板钢筋与6米高筒壁钢筋和滑模系统(不包括系统的铺垫木板),总重约55吨。
起吊物竖高7.6米,入位最大半径(含外展作业坪台支架)6.7米。
底板钢模套吊至孔口并进入1.5米左右时,将卷扬钢丝绳穿入8个滑轮式吊耳,待钢丝绳安装紧固并验收后,再继续下放,直至在孔内泥浆浮托下处于平衡状态。
(3)卷扬提吊力调整:
渐渐拉紧卷扬钢丝绳,使钢丝绳处于初步绷紧状态,继而调节8台卷扬的提吊力,使8个吊点的提吊力基本均衡。
(4)滑模作业坪台木板铺设:
将木板陆续吊至作业坪台的支架上,内外顺序呈对称铺设,并对木板采取绑扎固定措施,杜绝木板发生起翘、滑移、腐朽、空挡等不安全情况。
(七)井筒底板与筒壁浇注
钢锅底模板到位后安装净高2m的筒壁内模,然后开始浇注混凝土:
(1)底板混凝土浇注:
底板中心高度(厚度)1.6m,周边高度0.8m。
自下而上分四个层次浇注并振捣。
顶层(第四层段)混凝土浇捣时应注意,由于筒壁内模的阻挡,对筒底最外圈的混凝土振捣时振捣棒应斜插入以便更好的振捣筒底外圈混凝土或同时将振捣棒从筒壁上方插入配合振捣。
(见浇注混凝土图流程1)
(2)第一段段高2m的筒壁混凝土浇注:
将混凝土从筒壁内外侧模的上方送入,每次浇注层高不得超过50cm,在净高2米范围内浇注混凝土,并环向均布设置若干振捣棒进行振捣,使其与下部底板混凝土充分粘结。
(见浇注混凝土图流程2)
本段混凝土浇筑时间必须严格控制:
即在底板顶层混凝土初凝时间点前推~小时的时间段完成浇捣。
这是因为:
a.若过早泵入筒壁混凝土,易引起附近刚浇筑的底板混凝土隆起;
b.若过迟泵入筒壁混凝土,则振捣效果不好,筒壁与底板混凝土的两次浇捣接合面易产生裂缝。
(3)滑模法筒壁混凝土浇注:
第一段2m筒壁浇注完成后开始利用滑模系统连续浇注筒壁,每段浇注高度位1m,浇注时应严格根据混凝土配方控制各段高浇注时间和间隙时间,以防止每1m浇注段之间产生冷裂缝。
以此逐段浇筑至设计筒顶(见浇注混凝土图流程3)。
(八)井筒沉放
筒壁浇注之同时,井筒按设定要求受控下沉:
通过调节平台上8台卷扬机提升力和筒内水位来控制井筒下沉位置(详见浇注混凝土图流程1~9)。
从筒壁总高第8米(含第8米)开始,每浇筑1米段高,使筒体下沉1米。
即此后最新浇筑的1米段高始终保持在高于地面4米到5米的高程。
后续竖筋连接后的总高度高出地面10米(若下沉1米后再连接后一段高竖筋)或11米(若筒体下沉前连接后一段高竖筋)。
当依靠筒体自重(包括滑模坪台系统重力)不能实现1米竖高的下沉量时,再向筒内泵入清水,使达到1米下沉量。
重复上述每米段高的筒壁混凝土浇筑,直至完成井筒设计总高度。
经计算整个滑模系统、锅底钢模及其中的钢筋、内模板等总重大约90吨,经计算,单位高度的筒壁与筒内清水(两者之和)的平均比重为m3,若孔内泥浆比重也为m3,则筒体与筒内清水的重力与浮力恰好平衡,此时卷扬不承受重力;若泥浆比重小于m3,则每浇注1m段高筒壁并泵入1m高水柱时,重力大于浮力,这个浮力差需要卷扬机来分担。
下表4表示了不同泥浆比重情况下对提吊力的要求。
当然实际提吊力还要加上括号内重力:
(整个滑模系统、钢锅底及其中的钢筋、内模板等总重大约90吨+混凝土锅底重量—相对应浮力)。
泥浆比重及提吊力关系表表4
泥浆比重(t/m3)
外筒体截面积(m2)
内筒体截面积(m2)
筒体截面积(m2)
井筒深(m)
筒内总水位差(m)
卷扬提吊力(t)
50
浮力(t)
满水重力(t)
每米重力减浮力差(t)
对比每米水柱差(m)
总重力减浮力差(t)
(九)筒体下沉到设计深度
完成全部设计总高的筒壁浇筑后,撤除滑模坪台系统。
若泥浆比重平均不大于m3,此时筒内清水液面低于筒外泥浆液面几米。
然后将筒内注满水使其充分下沉到钻孔深度。
也可能因孔底沉淤较厚,因沉淤顶托,不再下沉,若和设计要求偏差比较大则需进行孔底沉淤处理。
若下沉深度稍大于设计深度,则筒体顶部再进行浇注,使筒顶和地面标高拉齐;也可在筒外骨料回填与水泥浆压注固化工序中抬升筒体。
(十)孔底沉淤处理
注水、冲淤法下沉筒体:
筒底受沉淤顶托不再下沉时,先向筒内注满清水,同时利用空压机,接通滑模顶升钢管中的6根均布钢管,对沉淤进行高压气流冲搅,使之悬浮,并在附加清水重力(最后注入筒内的几米水柱重力)作用下迫使筒体继续下沉,到达设计深度时停止冲淤。
同时利用卷扬机来微调筒体的整体垂直度和深度。
(十一)撤除卷扬起重装置
撤除卷扬起重装置,回收钢丝绳。
(十二)井筒外回填固化
(1)注浆管布设安装:
共设置16根注浆管。
其中8根系利用另外8根爬模钢管(该8根爬模钢管底端弯曲,使管口位与筒体外壁面齐整,钢管端口部位用橡胶胎包扎),水泥浆液从底板位置喷出。
另外在环状回填空间安装8根均布注浆管,钢管底端深度约30米。
(2)碎石围填:
选用粒径25~65mm级配碎石,将其均匀围填至锁口泄浆孔底面以下20cm。
(3)高压注浆固化:
先开通筒壁中的8根注浆管,注浆量达到设计水泥浆液总量90%时,暂停注浆。
随即再开通另外8根注浆管,当注浆量达到约5米以上高度时,继续完成先前8根注浆管的后续10%注浆量(到注浆压力比原先明显增大或难以注入为止)。
然后继续开通8根注浆管的浆液压注,直至水泥浆液从碎石顶面冒出为止。
然后起吊8根注浆管。
(十三)孔底后注浆
筒外注浆结束48小时后,实施井筒底板下方孔底剩余沉淤的固化处理。
开通剩余均布的6根筒壁爬模钢管,高压注入水泥浆液,直至达到设计注浆量或根据孔底土性确定的注浆压力为止。
筒体抗浮验算:
以筒外素砼环壁体与土体接合面计算侧阻的车库井筒抗浮验算(内径9400mm)如下:
井筒规格、浮力、自重与剩余浮力
井筒
内径
(mm)
井筒
壁厚
(mm)
井筒
外径
(mm)
围填素
砼环状
空间外径
(mm)
含围填砼
底板截面
(m2)
底板
埋深
(m)
地下水位
(m)
井筒
浮力
(kN)
含砼底板、底板钢模套与围填素砼井筒自重
(kN)
车架
自重
(kN)
剩余
浮力
(kN)
9400
450
10300
11000
95
48260×
34710
900
22300
不计车架自重的剩余浮力
23200
注:
①含围填素砼的筒壁总重力=(112—××50×+第一节壁厚增加部分:
×××4×24=31700kN
②底板重力=××()×25=2916kN
③底板钢模套(板厚10mm)重力=椭圆底模+环形外壁模=(112×+××)××=96kN
④井筒总重力=①+②+③=34712kN
⑤含围填素砼的筒壁重度取m3,第一节壁厚增加部分重度取24kN/m3,底板重度取25kN/m3。
浮力分项系数。
上海地区正常地层条件下的井筒侧壁阻力
土层
①②③
③
④
⑤
⑥
⑦1
⑦2
⑧1
侧壁极
限总
摩阻力
抗拔极限阻力
设计总
侧阻力
层厚(m)
6
9
7
4
5
10
单位极限
侧阻力(kPa)
20
25
25
45
65
75
105
60
分层极限
侧阻力(kN)
4146
5528
7774
10883
8983
12956
36277
6841
93388
52297
32686
注:
①筒体埋深,筒体有效侧壁摩阻竖向长度(——),围填素砼体外壁(Ф11000)面周长为;
②设计侧壁摩阻力系数取(即平均抗拔承载力系数取,设计抗浮力分项系数)。
③抗浮验算:
设计计算侧阻力(32680)大于扣除井筒总重力后的剩余浮力(23200),满足设计要求(32680/23200=。
上海地区第⑥层缺失区地层条件下的井筒侧壁阻力
土层
1②
③
③
④
⑤1
⑤2
⑤3
⑤4
⑦1
侧壁极限总摩阻力
抗拔极限阻力
设计总
侧阻力
层厚(m)
6
9
7
5
11
2
单位极限侧
阻力(kPa)
20
25
25
45
60
55
60
75
分层极限
侧阻力(kN)
4146
5528
7774
10883
10365
20902
4146
11142
74886
41936
26210
注:
①筒体埋深,筒体有效侧壁摩阻竖向长度(——),围填素砼体外壁(Ф11000)面周长为;
②设计侧壁摩阻力系数取(即平均抗拔承载力系数取,设计抗浮力分项系数)。
③抗浮验算:
设计计算侧阻力(26210)大于扣除井筒总重力后的剩余浮力(23200),满足设计要求(26210/23200=。
(十四)筒顶机房建造
筒体经过数天的养护达到设计强度后,将筒内水抽干,然后进行筒内停车钢框架的安装。
再根据框架结构厂商来配合筒顶的吊车梁等事宜,梁和筒壁、锁口浇注为一整体,初步定为井口设置梁高为800mm的井字型梁,来当作今后起重车辆的吊车梁,再在井字型梁上建造机房,机房外和筒体的空隙内建造楼板并在楼板上设置3个排风装置,见附图14,至此完成所有土建施工,然后再进行相关吊机调试、内部消防、照明系统等设施安装。
附图1
附图2
附图3
附图4
附图5
附图6
附图7
附图8
附图9
附图10
附图11
附图12
附图13
附图14