课程设计 多晶硅的生产工艺.docx
《课程设计 多晶硅的生产工艺.docx》由会员分享,可在线阅读,更多相关《课程设计 多晶硅的生产工艺.docx(16页珍藏版)》请在冰豆网上搜索。
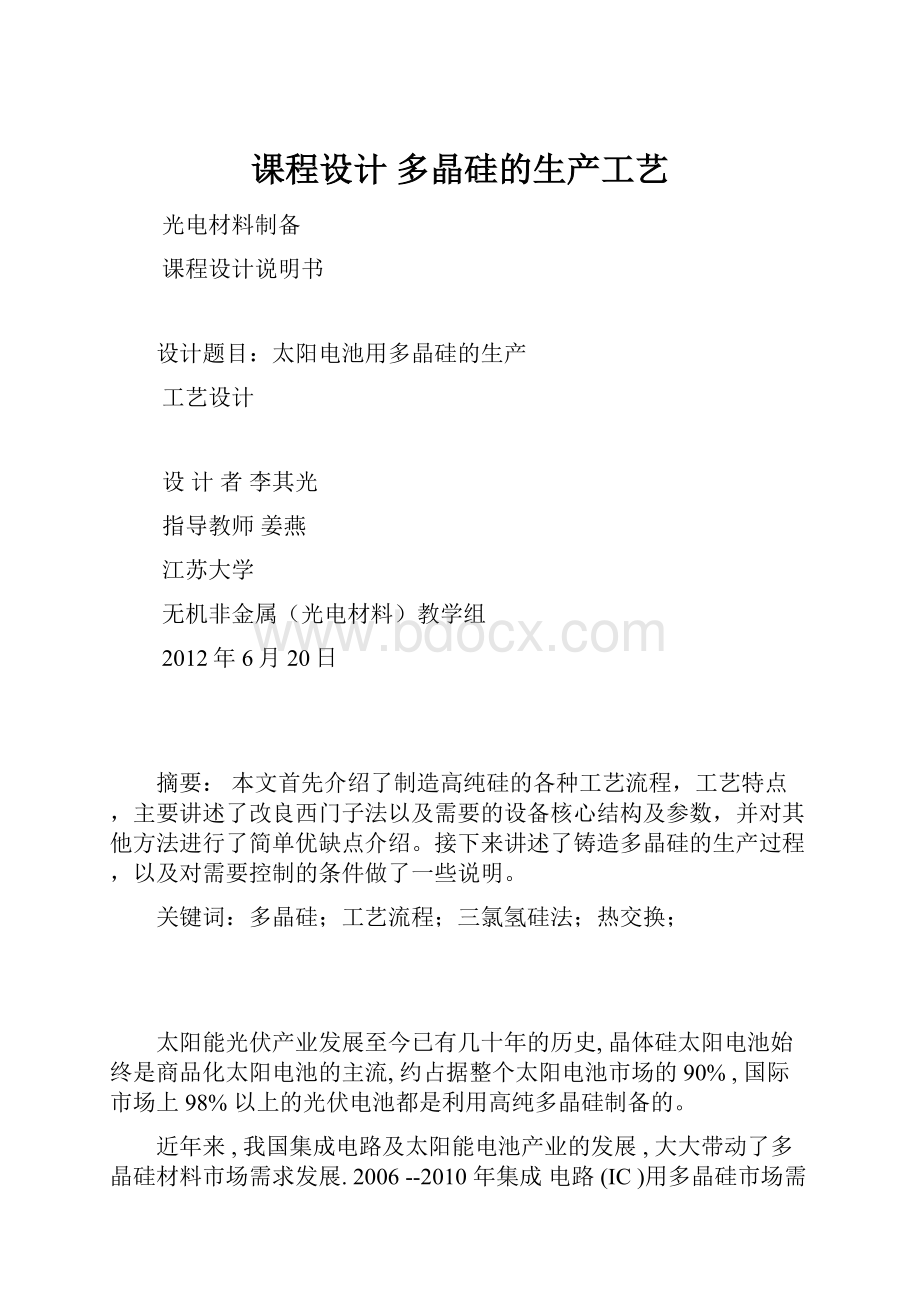
课程设计多晶硅的生产工艺
光电材料制备
课程设计说明书
设计题目:
太阳电池用多晶硅的生产
工艺设计
设计者李其光
指导教师姜燕
江苏大学
无机非金属(光电材料)教学组
2012年6月20日
摘要:
本文首先介绍了制造高纯硅的各种工艺流程,工艺特点,主要讲述了改良西门子法以及需要的设备核心结构及参数,并对其他方法进行了简单优缺点介绍。
接下来讲述了铸造多晶硅的生产过程,以及对需要控制的条件做了一些说明。
关键词:
多晶硅;工艺流程;三氯氢硅法;热交换;
太阳能光伏产业发展至今已有几十年的历史,晶体硅太阳电池始终是商品化太阳电池的主流,约占据整个太阳电池市场的90%,国际市场上98%以上的光伏电池都是利用高纯多晶硅制备的。
近年来,我国集成电路及太阳能电池产业的发展,大大带动了多晶硅材料市场需求发展.2006--2010年集成电路(IC)用多晶硅市场需求量年均增长41.9%,太阳能电池产量则以年均157%的速度高速增长,6年内太阳能电池产量及对多晶硅的需求量扩大了110多倍.随着国内在建项目陆续投产,2007年我国多晶硅产量已达1000t.不过由于近两年经济危机的影响,就国内除个别企业坚持低负荷开车外,三氯氢硅行业近九成企业停产或检修,市场低迷行情持续。
国内三氯氢硅主流报价在每吨4500~5000元。
三氯氢硅价格已低于成本线[1]。
2012年以来,新兴的美国光伏市场因“双反”对中国光伏企业关上了大门。
亚洲及其他国家光伏市场虽发展迅速,但总量和规模均不足以支撑和消化快速扩张的光伏产能。
据统计,2012年,全球光伏电池和多晶硅需求量仅为215亿瓦特、17.88万吨,而全球产能却达到660亿瓦特和29.5万吨[2]。
1.高纯多晶硅的制备
目前,化学提纯制备高纯硅的方法很多,SiHCl3氢还原法,新硅烷法等,其中SiHCl3氢还原法具有产量大,质量高,成本低的优点,是目前国内外制取高纯硅的主要方法。
硅烷法可有效地除去杂质,无腐蚀性,分解温度低,但是存在安全方面的问题,有待很好地解决。
本文设计第一种方法进行提纯硅,并对新硅烷法进行简单介绍。
1.1新硅烷法简介
所谓新硅烷法就是在硅烷法的基础上进行改进而打得到的。
新硅烷法是美国UCC公司首先开发的硅烷生产新工艺,该工艺克服了传统硅烷法的缺点,不需用较昂贵的硅镁合金,而是以SiCl4为原料,且体系呈闭路循环系统,几乎无副产物排出.新硅烷法工艺:
主要化学反应:
1.1.1优缺点分析:
1)缺点:
硅烷是易燃易爆气体,不易保存,其分解设备较复杂,存在一系列安全问题。
2)优点:
硅烷热分解温度较低,耗电少,硅烷容易提纯,产品纯度高,硅烷中硅质量分数较高,原料消耗低等[3]。
1.2改良西门子法的三氯氢硅制备工艺
1955年,西门子公司成功开发了利用H2还原SiHCl3在硅芯发热体上沉积硅的工艺技术,并于1957年开始了工业规模的生产,这就是通常所说的西门子法。
在西门子法工艺的基础上,通过增加还原尾气干法回收系统、SiCl4氢化工艺,实现了闭路循环,于是形成了改良西门子法——闭环式SiHCl3氢还原法。
改良西门子法的生产流程是利用氯气和氢气合成HCl(或外购HCl),HCl和工业硅粉在一定的温度下合成SiHCl3,然后对SiHCl3进行分离精馏提纯,提纯后的SiHCl3在氢还原炉内进行化学气相沉积反应得到高纯多晶硅。
改良西门子法包括五个主要环节:
即SiHCl3合成、SiHCl3精馏提纯、SiHCl3的氢还原、尾气的回收和SiCl4的氢化分离。
该方法通过采用大型还原炉,降低了单位产品的能耗。
通过采用SiCl4氢化和尾气干法回收工艺,明显降低了原辅材料的消耗[4]。
1.2.1工艺流程
改良西门子法的三氯氢硅制备工艺流程如图1所示。
简化的主要流程如图2所示。
图1改良西门子法的三氯氢硅制备工艺流程示意
图2流程简图
1.2.1.1原料制备
主原料:
纯度为99.5%金属级硅粉(MG-Si)、无水氯化氢气体(大部分来自CVD氢气还原单元循环利用,少量外购补充)。
金属级硅粉提升至硅粉加料斗,硅粉借助重力从硅粉加料斗进入硅粉干燥器,干燥器外设有盘管。
用150℃的氮气直接加热和180℃蒸汽盘管间接加热,经4~8h除去残留的水分。
加热后的氮气经袋式除尘器回收硅粉后放空。
干燥好的硅粉送至硅粉送料斗待用[5]。
1.2.1.2 反应过程
干燥好的硅粉经氯化反应器喷射器用HCl气体送入氯化反应器(流化床反应器FBR)。
为了更好地直接换热,氯化反应器(FBR)有内置盘管,用350℃的导热油将装有60%Si粉的氯化反应器床层温度加热至约300℃,当温度达到反应温度时,向氯化反应器中通入HCl气体,充分流化硅粉,使硅粉与HCl充分混合,流化床层的高度可通过床层的压降测量出来。
HCl与Si的反应是高放热反应,为了避免反应器超温而降低TCS的得率,必须将释放的热移走,此时导热油系统将从加热模式改为冷却模式。
在氯化反应器中发生的主要反应的反应式为:
Si+3HCl→SiHCl3+H2+Q
副反应的反应式为:
Si+2HCl→SiH2Cl2
Si+4HCl→SiCl4+2H2
在300~425℃,2~5kPa条件下,反应产物含有H2,SiHCl3,SiCl4,SiH2Cl2和少量未反应完的HCl和硅粉,SiHCl3含量高于88%。
反应生成物中还有一些高沸点的氯化物副产物(如AlCl3),及少量的金属杂质,如Fe,Ti反应生成的氯化物,在TCS净化中必须除去此类物质,才能使TCS反应产物达到99.999 999%的纯度,以生产出太阳能级的多晶硅。
氯化反应器设备上部设计为扩大段,使设备内部上升的工艺气体流速减小,减少离开氯化反应器的工艺气体夹带的硅粉量;气体进入旋风分离器、袋式除尘器回收绝大部分大颗粒硅粉,返回循环利用[6]。
1.2.1.3 蒸馏净化
工艺气体进入釜式蒸馏塔,该设备有多个作用。
首先,作为蒸馏塔将高沸点组分与SiHCl3,SiCl4,SiH2Cl2分离,塔底脱除高沸点的硅组分和AlCl3,塔底的物料输送至重组分水解处理;其次,它还用于将气体从袋式除尘器夹带出的硅粉除去。
釜式蒸馏塔在160℃下运行,确保AlCl3从塔顶的工艺气中分离。
工艺气相物料从蒸馏塔顶出来,进入氯化钠反应器;向反应器加入氯化钠细粒,用来除去气体中剩余的AlCl3;液态AlCl3从反应器底部排出,去中和水解处理。
氯化钠反应器出来的气相物料进过一系列的冷却器冷却,直至将最后的工艺气体冷却至-50℃,然后将气体中的H2,HCl分别在HCl吸收塔和HCl蒸馏塔与硅的氯化物分离。
生成硅的氯化物都储存在受槽中,主要组成是SiHCl388%(质量分数),SiH2Cl2和SiCl42%(质量分数)。
受槽中TCS送去进行多级塔蒸馏净化,进一步净化合格后的TCS去CVD氢气还原生产出高纯度的多晶硅。
所产生的STC等物料送至转化单元循环利用[7]。
1.2.2废气及残液残渣处理工序
1.2.2.1废气及残液处理工序
①含氯化氢工艺废气净化SiHCl3提纯工序排放的废气、还原炉开停车、事故排放废气、氯硅烷及氯化氢储存工序储罐安全泄放气、CDI吸附废气全部用管道送入废气淋洗塔洗涤。
废气经淋洗塔用10%NaOH连续洗涤后,出塔底洗涤液用泵送入工艺废料处理工序,尾气经15m高度排气筒排放。
②残液处理在精馏塔中排出的、主要含有四氯化硅和聚氯硅烷化合物的釜地残液以及装置停车放净的氯硅烷残液液体送到本工序加以处理,需要处理的液体被送入残液收集槽,然后用氮气将液体压出,送入残液淋洗塔洗涤。
采用10%NaOH碱液进行处置,废液中的氯硅烷与NaOH和水发生反应而被转化成无害的物质(处理原理同含氯化氢、氯硅烷废气处理)。
③酸性废气硅芯制备和产品整理工序产生的酸性废气,经集气罩抽吸至废气处理系统。
酸性废气经喷淋塔用10%石灰乳洗涤除去气体中的含氟废气,同时在洗涤液中加入还原剂氨,将绝大部分NOx还原为N2和H2O[8]。
洗涤后气体经除湿后,再通过固体吸附法(以非贵重金属为催化剂)将气体中剩余NOx用SDG吸附剂吸附,然后经20m高度排气筒排放。
1.2.2.2废硅粉处理
来自原料硅粉加料除尘器、三氯氢硅合成车间旋风除尘器和合成反应器排放出来的硅粉,通过废渣运料槽运送到废渣漏斗中,进入到带搅拌器的酸洗管内,在通过31%的盐酸对废硅粉(尘)脱碱,并溶解废硅中的铝、铁和钙等杂质。
洗涤完成后,经压滤机过滤,废渣送干燥机干燥,干燥后的硅粉返回到三氯氢硅合成循环使用,废液汇入废气残液处理系统废水一并处理。
从酸洗罐和滤液罐排放出来的含HCl废气送往废气残液处理系统进行处理。
1.2.3 主要设备及操作参数
该工艺的主要设备有:
硅粉干燥器、硅粉贮仓、硅粉送料斗、氯化反应器喷射器、氯化反应器、旋风除尘器、袋式除尘器、釜式蒸馏塔、系列换热器、氯化钠反应器、氯化物受槽、HCl吸收塔、HCl蒸馏塔、TCS蒸馏塔、泵等。
其主要设备的操作参数见表1[9]。
表1主要设备的操作参数
三氯氢硅制备工艺的核心设备是氯化反应器。
该设备的主材为16MnR,外形为塔形。
设备高径比大,气固接触时间长,有利于提高产品的质量与收率;气固分离段的直径为反应段的1.5~3.5倍,有利于气固分离;设备顶端设计为扩大段,有利于减小离开氯化反应器(FBR)的硅粒速度,使部分硅粉沉降下来,从而减少了硅粉被带入旋风分离器和袋式除尘器;设备内置导热油加热/冷却蛇管换热结构,有利于控制温度分布,强化传热与传质,通过导热油加热来提供硅粉与氯化氢反应所需的热量,同时通过冷却及时移去反应时产生的反应热,维持稳定的反应温度;反应器下部设有气体分布盘,用来均匀分布反应气体,使硅粉处于均匀流化状态,气固两相充分接触,提高硅粉的转化率和三氯氢硅的得率;设备下部为锥状设计,锥状体下部设置排渣口,利于硅粉残渣排出,用氮气吹扫,减少劳动强度。
1.2.4 工艺优点分析
a)该工艺直接用MG-Si和HCl作为原料,就地生产TCS自用,回收的
STC转化成TCS,是目前推广的生产方式,完全符合降低单耗和成本、
节约资源和有利环保的要求,原料来源广泛,成本低廉。
b)该工艺对产生的硅粉尘采用有效除尘设施,回收粉尘物料,充分利用能量,
成本低,每千克多晶硅电能消耗约120~150kW·h。
c)工艺成熟,安全性相对较高,操作弹性大,运行稳定,DCS自动控制系统,
有人值守,无需操作。
d)TCS的净化提纯采用了气固分离、反应、吸收、多级蒸馏等综合技术,去
除轻重组分杂质,有效提高TCS纯度,STC等物料得到充分循环利用,对环境不产生污染,节约了资源。
制备的三氯氢硅纯度高,生产的多晶硅产品质量好,具有明显的竞争优势。
e)氯化反应器实现反应与换热设备一体化。
在氯化反应器内流化床区域中,参
与反应的硅表面积大,生产效率高,硅粉转化率高,生成的SiHCl3含量高于88%[10]。
f)一般地,每生产1t多晶硅,副产10~20t四氯化硅、1~5t氯化氢,
对于非闭路循环生产多晶硅工艺而言,副产物STC难以处置,是生产多晶硅的瓶颈。
而改良西门子法多晶硅工艺采用闭路循环的生产系统,解决了副产物的出路问题,无环境污染。
2.铸造多晶硅的制备工艺
多晶硅铸锭定向凝固目前主要有4种方法,即:
a)布里奇曼法;b)浇铸法;c)热交换法;d)电磁铸锭法;本文主要采用热交换法,并对其他方法进行简单介绍,并分析其优缺点。
2.1布里奇曼法
这是种较经典的定向凝固方法,特点是设备内分固相区和液相区,固相区和热相区用隔热板隔开,用于晶体生长用的材料装在圆柱型的坩埚中,缓慢地下降,并通过一个具有一定温度梯度的加热炉,炉温控制在略高于材料的熔点附近。
根据材料的性质加热器件可以选用电阻炉或高频炉。
在通过加热区域时,坩埚中的材料被熔融,当坩埚持续下降时,坩埚底部的温度先下降到熔点以下,并开始结晶,晶体随坩埚下降而持续长大。
如图3所示。
它的长晶速度接近于常数且可以调节,受坩埚下移速度和冷却水流量的影响。
图3布里奇曼法示意图
但它的缺点是设备的结构比较复杂,坩埚底部需要水冷,坩埚的升降速度必须平稳。
2.2电磁感应加热连续铸造法(EMCP)
电磁感应加热连续铸造法的基本原理是利用电磁感应加热来熔化硅原料,其熔化和凝固过程可以在不同部位进行,节约了生产时间。
且随下部硅锭一起向下抽拉时,上部硅锭可以同时凝固,从而实现过程的连续操作。
与浇注法和定向凝固法相比,该工艺具有以下优点:
1)在熔炼过程中,由于不使用坩埚,避免了硅料和坩埚的接触污染以及坩埚损耗;
2)提高了生产率,可以实现连续操作;
3)由于电磁感应加热及连续铸造,硅锭性能稳定,避免了常规浇注过程中因杂质分凝导致的硅锭质量分布不均匀、需进行切除头尾料的现象,有利于提高材料的利用率。
EMCP法的不足之处在于:
1)生长的多晶硅中颗粒尺寸较小;
2)由于其凝固速率较快以及固液界面处不平而易产生较高的热应力,使得其位错密度相对较高,从而造成该工艺生产的多晶硅材料转换效率也相对较低。
比较快速热处理对电磁感应加热连续铸造法与定向凝固法制备多晶硅的影响,结果表明,经快速热处理工艺后,与定向凝固法相比,EMCP法制备的多晶硅材料中少数载流子的寿命明显延长。
2.3浇注法
浇注法于1975年由Wacker公司首创并用来制备多晶硅材料,其工艺过程是将硅料置于预熔坩埚内熔化,而后利用翻转机械将其注入预先准备好的凝固坩埚内进行结晶,结晶时始终控制固液界面的温度梯度,保证固液界面在同一平面上,最终使所有的硅熔体结晶(如图4所示)。
图4浇铸法基本原理示意图
浇注法工艺成熟、设备简单、易于操作控制,且能实现半连续化生产,其熔化、结晶、冷却都分别位于不同的地方,有利于生产效率的提高和能耗的降低。
然而,由于浇注法所用的坩埚材料多为石墨、石英等,并且熔化和结晶使用不同的
坩埚,硅锭二次污染较严重[11]。
所以用该法制备的多晶硅杂质元素含量较高,同时受熔炼坩埚及翻转机械的限制,炉产量较小。
2.4热交换法
热交换法定向凝固设备目前在国内用的是比较普遍的。
2.4.1特点
坩埚和加热器在硅的熔化及定向凝固整个过程中均无相对运动。
在加热熔料的时候外围的保温罩是密闭的;在生长过程中,保温罩逐渐从底部打开,以增强坩埚底部散热强度。
如图5所示,这种方法中长晶速度受坩埚底部散热强度控制。
图5热交换法定向凝固示意图
2.4.2所需设备及参数
2.4.2.1炉子型号
第一种炉型如图6所示,第二种炉型如图7所示。
图6炉型1示意图
图7炉型2示意图
图6所示的炉型是国内应用较多的一种热交换炉型,采用石墨电阻在四周加热。
容量240—260公斤。
凝固开始时通过提升保温框(0.12-0.2mm/min)以增大石墨块的散热强度[12]。
长晶速度平均为0.28/min.这种炉最大优点是结构简单,坩埚底部无需水冷。
其次是侧面加热底部温度较表层温度高,形成强烈对流,有利于提高纯度。
缺点是热效率不高,每公斤硅锭耗电约13—15度,循环周期长,约为50小时左右。
图7所示的这种炉由于生产量大,目前正为国内厂家引进。
具有以下优点:
1)采用石墨棒顶底加热。
四周无加热器。
2)在顶部装料,装料时炉盖平移推出,有助于提高晶体生长速度。
3)热效率高,生长周期约为46小时。
但缺点是:
首先这种炉型结构较复杂,而且是在顶部装料,装料难度大;其次,在凝固阶段是顶部加热,抑制了对流,提纯效果较差。
2.4.2.2坩埚参数
在铸造多晶硅过程中,坩埚是一个很重要的设备,不仅影响到效率,还影响到硅锭的质量,所以选择坩埚一定要考虑各种因素。
1)涂层材料
铸造多晶硅时,在原料熔化晶体生长过程中,硅熔体和坩埚长时间接触会产生粘滞性。
由于热膨胀系数不同,在加热或冷却时可能造成晶体硅或坩埚破裂。
再加上腐蚀的因素,工艺上一般采用S3N4作为涂层材料,不仅可重复使用,而且可降低硅中的氧,碳等杂质浓度。
2)坩埚尺寸理论上坩埚尺寸可以无限大,仅限于铸锭炉的尺寸。
一般硅锭越大,质量越好,所以国际上趋于生产大尺寸硅锭。
此处采用如下规格:
坩埚尺寸为32(784mm),目前国内铸造的硅锭尺寸大多为880mmx880mmx400mm,坩埚规格如图8所示[13]。
图8坩埚规格
2.4.3工艺流程
在国内应用较广,采用石墨电阻在四周加热。
在熔料时,保温罩是与底板密闭,但是凝固开始时通过提升保温罩(0.12~0.2mm/min)以增大热交换台的散热强度。
长晶速度为变数,平均为0.28mm/min。
一个生长周期分为6个阶段。
(1)装料。
将装好料的坩埚放置在热交换台上,然后炉内抽真空,使炉内压力为5~10Pα并保持真空。
通入氩气,使炉内压力维持在40~60kPα。
(2)加热。
用石墨加热器加热,首先使石墨部件、隔热层、硅原料等表面吸附的湿气蒸发,然后缓慢加温,使石英坩埚的温度达到1200℃~1300℃,该过程约需4~5h。
(3)熔化。
通入氩气,使炉内压力维持在40~60kPα,逐渐增大加热功率,使石英坩埚内的温度达到1500℃左右,硅原料开始熔化,熔化过程中一直保持此温度,直至化料结束,该过程约需9~11h。
(4)生长。
硅料熔化后,降低加热功率,使石英坩埚的温度降至1420℃~1440℃硅熔点。
然后逐渐打开保温罩,使硅熔料与周围形成热交换,使熔体的温度自底部开始降低,晶体硅首先在底部形成,并呈柱状向上生长,生长过程中固-液界面始终保持与水平面基本平行,直至晶体生长完成,该过程约需要20~22h。
(5)退火。
晶体生长完成后,晶锭保持在熔点附近2~4h,使晶锭温度均匀,以减少热应力。
这样可以减少硅片加工和电池制备过程中容易造成硅片碎裂。
(6)冷却。
退火完成后,关闭加热功率,提升保温罩,通入大流量氩气,使晶体温度逐渐降低至室温附近。
同时,炉内气压逐渐上升至大气压,最后打开炉室,取出晶锭,该过程约需10h。
这种炉型最大优点是结构简单,坩埚底部无需水冷。
其次是侧面加热,底部温度较表层温度高,形成较强烈对流,有利于提纯。
缺点是热效率不高,生长周期较长,约需55~60h。
热损耗太大,硅锭耗电约15~18(kW·h)/kg。
所以经上述比较得出,采用热交换法比较稳定与成熟,但电磁浇铸很有前途,它的很多方面表现出很多热交换法无法相比的优势,是未来铸造多晶硅的发展趋势。
3现状与展望
当前高纯多晶硅的制备和提纯技术只掌握在美、日、德等国的近10家大公司手中,如Hemlock、Wacker、Tokuyama、REC等公司,目前这4家大公司所生产的高纯多晶硅占据世界高纯多晶硅产量70%以上的份额,对整个世界高纯多晶硅材料市场形成了绝对的垄断。
表2为2006年国际上一些大公司生产的高纯多晶硅材料产能和所占份额。
表22006年世界各大公司多晶硅的产能及其份额
我国的多晶硅产量与产能如表3所示。
表32006—2007我国的多晶硅产量与产能
目前,我国和国外在多晶硅的制造方面存在一定差距,我们需在以下方加以改进:
(1)高纯硅材料已成为制约光伏产业发展的瓶颈。
打破技术垄断,引进国外先进技术,同时努力探寻制备高纯硅材料的新方法和新工艺,提高自主研发水平,降低高纯多晶硅料的生产成本势在必行。
(2)高纯硅的制备和提纯是一个技术含量高、能耗高、甚至对环境会造成污染的过程。
改良西门子法投资大、工艺复杂、若用其制造太阳能级多晶硅则显得成本太高,缺乏经济性,不太适宜,需要国内准备上线的多晶硅企业清醒判断;物理提纯法技术有难度,设备要求高,但成本低,工艺相对简单,技术发展空间比较大,是最有希望实现大规模太阳能级硅生产的技术。
(3)越来越多的高纯废弃硅材料的回收再利用已引起人们的兴趣和热情,这将对当前高纯硅材料供不应求的局面起到一定的缓解作用。
参考文献
[1].李俊峰,王斯成,等.2007年中国光伏发展报告.北京:
中国环境科学出版社,2007.16
[2].杨德仁.太阳能电池材料[M].北京:
化学工业出版社,2006.
[3].赵玉文,吴达成,励旭东,等.我国光伏产业和市场的发展概况[J].太阳能,2007(3):
7-10.
[4].郭景杰,黄锋,陈瑞润,等.太阳能电池用多晶硅铸造技术研究进展[J].特种铸造及有色合金,2008,28(7):
516.
[5].武冠男,张军,刘林,等.太阳能级多晶硅定向凝固技术的研究进展[J].铸造技术,2008,29(5):
673.
[6].马晓东,张剑,李延举.冶金法制备太阳能级多晶硅的研究进展[J].今
日铸造,2007(9):
1288.
[7].谢建生,李金华.太阳电池研究的现状与发展前景[J].江苏工业学院学报,2008,20(3):
69-37.
[8].梁骏吾.电子级多晶硅的生产工艺[J].中国工程科学,2000,2(12):
34-39.
[9].高宏存.新能源多晶硅领域获新进展[N].科学时报,2008,23(10):
290-298.
[10].蒋广生.三氯氢硅制备工艺介绍[J].化学工业与工程技术.2011,32(6):
46-50.
[11].王鹏选.太阳能电池多晶硅铸锭的凝固原理和方法浅谈[J].电子工业专业设备.2008,24(163):
15-19.
[12].武冠男,张军,刘林,等.太阳能级多晶硅定向凝固技术的研究进展[J].铸造技术,2008,29(5):
673.
[13].汪建军,刘金霞.太阳能电池及材料研究和发展现状[J].浙江万里学院学报,2006,19(5):
73.