桩基超声波检测技术方案.docx
《桩基超声波检测技术方案.docx》由会员分享,可在线阅读,更多相关《桩基超声波检测技术方案.docx(34页珍藏版)》请在冰豆网上搜索。
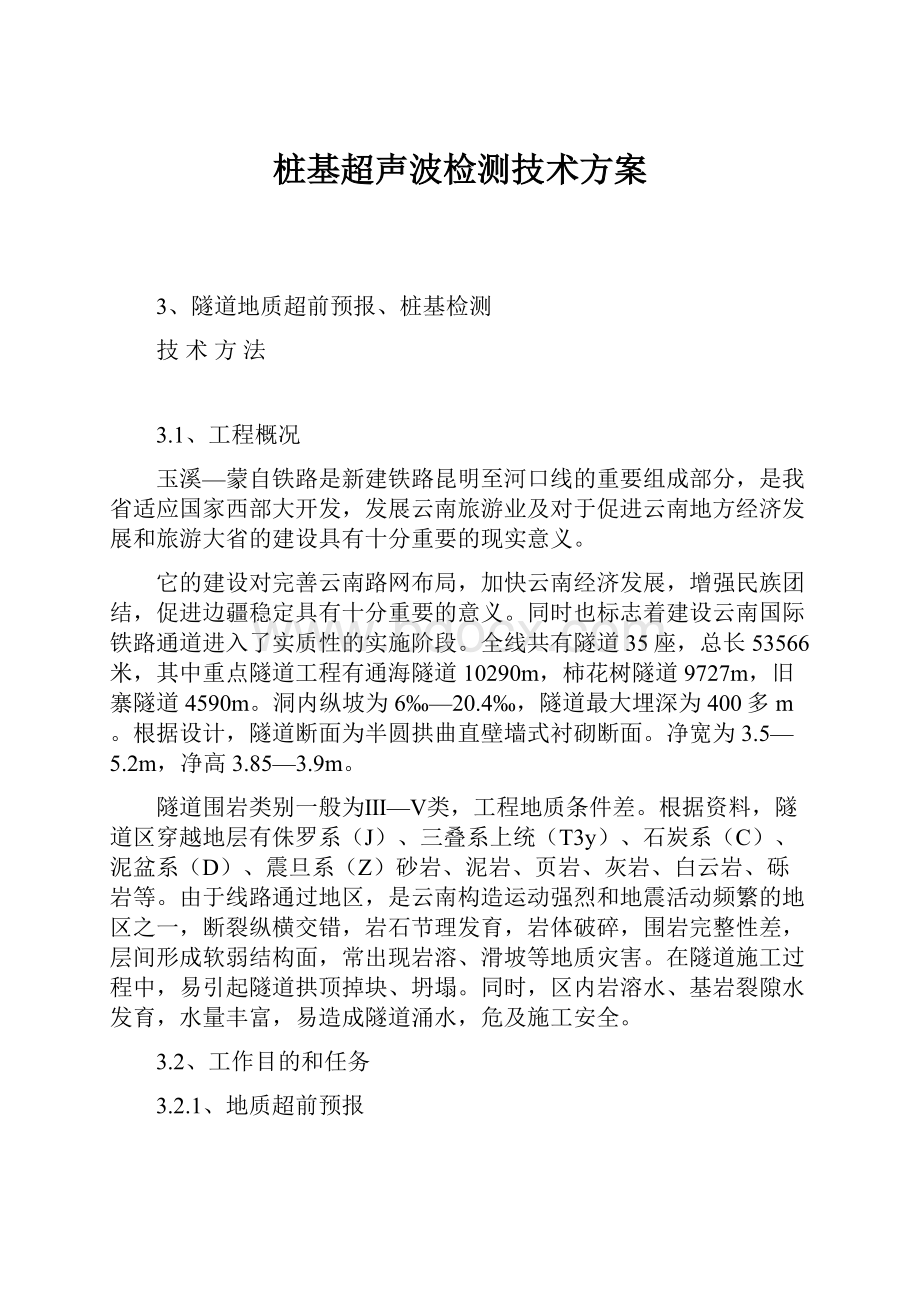
桩基超声波检测技术方案
3、隧道地质超前预报、桩基检测
技术方法
3.1、工程概况
玉溪—蒙自铁路是新建铁路昆明至河口线的重要组成部分,是我省适应国家西部大开发,发展云南旅游业及对于促进云南地方经济发展和旅游大省的建设具有十分重要的现实意义。
它的建设对完善云南路网布局,加快云南经济发展,增强民族团结,促进边疆稳定具有十分重要的意义。
同时也标志着建设云南国际铁路通道进入了实质性的实施阶段。
全线共有隧道35座,总长53566米,其中重点隧道工程有通海隧道10290m,柿花树隧道9727m,旧寨隧道4590m。
洞内纵坡为6‰—20.4‰,隧道最大埋深为400多m。
根据设计,隧道断面为半圆拱曲直壁墙式衬砌断面。
净宽为3.5—5.2m,净高3.85—3.9m。
隧道围岩类别一般为Ⅲ—Ⅴ类,工程地质条件差。
根据资料,隧道区穿越地层有侏罗系(J)、三叠系上统(T3y)、石炭系(C)、泥盆系(D)、震旦系(Z)砂岩、泥岩、页岩、灰岩、白云岩、砾岩等。
由于线路通过地区,是云南构造运动强烈和地震活动频繁的地区之一,断裂纵横交错,岩石节理发育,岩体破碎,围岩完整性差,层间形成软弱结构面,常出现岩溶、滑坡等地质灾害。
在隧道施工过程中,易引起隧道拱顶掉块、坍塌。
同时,区内岩溶水、基岩裂隙水发育,水量丰富,易造成隧道涌水,危及施工安全。
3.2、工作目的和任务
3.2.1、地质超前预报
采用“负视速度”法,对开挖面前方进行地质超前预报,根据波形特征、能量及频率变化,分析推断开挖面前方一定范围内地质构造、岩性特征和不良地质现象,预测岩体的完整性、岩溶发育情况,判定围岩类别,为采取安全有效的施工方法和确定初期支护参数提供地质依据。
在岩溶水、基岩裂隙水发育的地方,采用红外线探水仪,预报涌突水位置、水量、水压及岩体的综合渗透系数,确保隧道安全施工。
3.2.2、衬砌质量检测
应用地质雷达法、声波法等物理勘探方法对隧道衬砌(包括:
喷锚衬砌、整体式衬砌、复合式衬砌、装配式衬砌、下锚式衬砌、底板和仰拱等)的混凝土厚度、强度及结构进行无破损性的检测。
提供钢拱架间距和数量、砼厚度、砼强度及衬砌背后的密实程度等资料,为工程质量监控和工程验收提供依据。
3.2.3、桥桩桩身质量检测
应用声波投射法、低应变动力法、高应变动力法、静荷载法等方法对桥涵桩基础进行无破损性的检测。
其中要求直径大于0.8米的桥梁钻孔桩和桥梁挖孔桩,100%采用声波透射法进行桩身混凝土质量检测。
锚固桩、抗滑桩基础,100%采用声波透射法进行桩身混凝土质量检测。
即在桥桩浇注施工完成后,利用桩体予埋管,采用声波仪对桩体混凝土质量进行检测,检查是否有断桩、裂纹出现,判断桩身质量等级,为工程质量监控和工程验收提供依据。
3.3、执行标准及依据
3.3.1、建设方提供的设计文件;
3.3.2、《铁路工程物理勘探规程》(TB10013-98);
3.3.3、《铁路隧道衬砌质量无损检测规程》(TB10223-2004);
3.3.4、《回弹法检测混凝土抗压强度技术规程》(JGJ/T23-2001);
3.3.5、《建筑地基处理技术规范》(JGJ79-2002);
3.3.6、《混凝土强度检验评定标准》(GBJ107-87);
3.3.7、《建筑基桩检测技术规范》;
3.3.8、《普通混凝土力学性能试验方法》(GBJ81-85);
3.3.9、《铁路工程基桩无损检测规程》(TB10218-99);
3.3.10、《浅层地震勘查技术规范》(DZ/T0170-1997);
3.3.11、《岩土工程勘察规范》(GB50021-2001);
3.3.12、《公路软土地基路堤设计与施工技术规范》;
3.3.13、现场地质观察资料。
3.4、地质超前预报方法技术
3.4.1、根据有关规定,凡长度500米以上的中长铁路隧道在开挖和施工过程中,应进行工程地质超前预报工作,提供隧道开挖支撑面前方的围岩类别、地质构造、水文情况、岩溶位置。
3.4.2、采用BT—24型工程地震仪(地质探测仪)进行地震波“负视速度”法地质超前预报。
在隧道开挖面两侧后方、分别在高度为1.5m的地方沿洞壁布置检波器,用电钻打眼将其实插于边墙上。
采用频率为100Hz的检波器,仪器采样间隔为0.2ms,记录长度为2048个样点,道间距为2m,12道检波器接收,爆破激发。
根据我单位在澄阳公路净莲寺隧道、重庆主城排水工程6个隧道地质超前预报的工作经验,偏移距可确定为20m。
3.4.3、对野外观测的结果进行室内资料整理和增益调整、滤波等数据处理,对数据处理结果进行速度分析和波形特征分析,最终根据速度及波形特征、波的能量分布规律,结合开挖面的地质情况,综合判断围岩类别,预报开挖面前方的地质情况,为采取正确的施工方法和支护参数提供地质资料。
3.4.4、预报频率:
正常情况一般为每40—50m一次,但由于地质复杂、当地层岩性变化较大,或出现围岩异常时,施工人员应及时通知,我们将加大预报频率。
3.4.5、提交资料:
每次预报后的次日提交预报快报,5日内提交预报报告。
3.5、衬砌质量检测
3.5.1、地质雷达法检测
平行于隧道中轴线,沿隧道边墙及拱顶布置三条剖面,采用美国GSSI公司生产的SIR—20型地质雷达对钢拱架、砼厚度、砼密实性及衬砌背后密实性、进行检测。
天线为900MHz和500MHz收发合一的屏蔽天线,观测时窗为30ns和50ns。
3.5.2、声波检测法
平行于隧道中轴线方向,沿边墙布置检测剖面,采用武汉岩海公司生产的RSM—SY5型声波检测仪对隧道衬砌砼强度进行检测,采用20KHz平面式换能器,点距为2m。
3.5.3资料处理
将现场采集的各种数据资料全部输入计算机,采用相应的软件对资料进行处理、计算及成图,最后分别汇总成相应的检测结果表。
3.5.4检测频率
为减少对施工的干扰和影响,同时,便于资料的集中对比分析和处理,使获得的成果客观实际。
根据我单位以往检测的经验,并结合本工程的情况,单一隧道衬砌的质量检测段为500m—700m,并对多个隧道集中检测。
3.5.5、提交资料:
检测野外工作结束后,及时整理资料、处理数据,计算成图并编制各种检测结果表,10天内提交检测成果报告。
3.6、桩基检测方法及工艺
本项目合同段桩基质量检测以声波透射法测定桥梁桩长、桩径、桩身及混凝土缺陷、混凝土强度等情况为主,并按规定对辅以5%的钻芯取样方法进行检测,以准确评定桥梁桩长、桩身混凝土强度、桩底沉渣等情况;桥梁桩基承载力根据地勘报告结合桩身质量采用桩土参数进行综合评定,同时还可采用静载荷试验、孔底载荷试验、自重法、高应变进行桥梁桩基承载力判定。
在检测过程中,若出现了新的方法技术、检测工艺;国家颁布了新的规范、规程、标准,则及时按新的方法技术、检测工艺、新的规范、规程、标准执行。
3.6.1、灌注桩声波透射法检测
声波透射法,适用范围为检测桩径大于0.6米混凝土灌注桩的完整性。
3.6.1.1、仪器设备
仪器设备采用目前国内较先进的中国科学院武汉岩土力学研究所研发的RSM-SY5声波测试仪两台。
换能器采用柱状径向振动的换能器,其共振频率为25~50kHz,长度为20cm,换能器装有前置放大器,前置放大器的频带宽度为5~50kHz。
换能器的水密封性满足在1Mpa水压下不漏水。
发射换能器的长度、频带宽度及水密封性能与接收换能器的要求相同。
声波检测仪器的技术性能符合以下规定:
接收放大系统的频带宽度为5~50kHz,增益大于100dB,并且带有0~60dB的衰减器,其分辨率为1dB,衰减器的误差小于1dB,其挡间误差小于1%。
发射系统能输出250~1000V的脉冲电压,其波形为矩形脉冲。
显示系统同时显示接收波形和声波传播时间,其显示时间范围大于2000μs,计时精度大于1μs。
3.6.1.2现场检测
预埋声测管符合下列规定:
本项目的桥梁桩径均在1.0~2.5米之间,埋设三根管;预埋声测管采用φ60×3.5焊接钢管,其技术指标满足GB3091-82的规定,钢管用螺纹套管连接或采用焊接,管的下端用φ70×10钢板封闭,上端加盖;检测管焊接或梆扎在钢筋笼的内侧,检测管之间互相平行;在检测管内注满清水。
现场检测前,测定声波检测仪发射至接收系统的延迟时间t,并按下式计算声时修正值t′:
t′=
式中:
D——检测管外径(mm)
d——检测管内径(mm)
d′——换能器外径(mm)
Vt——检测管壁厚度方向声速(km/s)
Vw——水的声速(km/s)
t′——声时修正值(μs)
3.6.1.3检测步骤
接收及发射换能器在装设扶正器后置于检测管内,并能在管内顺利提升及下降;
测量时发射与接收换能器置于同一标高,当发射与接收换能器置于不同标高时,其水平测角为30°~40°。
测量点距为20~40cm。
当发现读数异常时,加密测量点距。
发射与接收换能器同步升降。
各测点发射与接收换能器相对高差不大于2cm,随时校正。
检测时由检测管底部开始,发射电压值固定,并始终保持不变,放大器增益值始终固定不变。
调节衰减器的衰减量,使接收信号初至波幅度在荧光屏上为2或3格。
由光标确定首波初至,读取声波传播时间及衰减器的衰减量,依次测取各测点的声时及波幅并记录。
一根桩有多根检测管时,将每2根检测管编为一组,分组进行测试。
每组检测管测试完毕后,测试点随机重复抽测量10%~20%。
其声时相对标准差不大于5%;波幅相对标准差不大于10%。
对声时及波幅异常的部位重复抽测。
测量的相对标准差按下式计算:
σ
′
=
σ
′
=
式中:
σ
′——声时相对标准差
σ
′——波幅相对标准差
t
——第i个测点声时原始测试值(μs)
A
——第i个测点波幅原始测试值(dB)
t
——第i个测点第j次抽测声时值(μs)
A
——第i个测点第j次抽测波幅值(dB)
3.6.1.4检测数据的处理与判定
由现场所测的数据绘制声时-深度曲线及波幅(衰减值)-深度曲线,其声时及声速按下列公式计算:
t
=t-t
-t
Vp=
式中:
t
——混凝土中声波传播时间(μs)
t——声时原始测试(μs)
t
——声波检测仪发射至接收系统的延迟时间(μs)
I——两个检测管外壁间的距离(mm)
Vp——混凝土声速(km/s)
桩身完整性按下列规定判定:
采用声时平均值μ
与声时2倍标准差σ
之和作为判定桩身有无缺陷的临界值;并按下列公式计算:
μ
=
σ
=
式中:
n——测点数
t
——混凝土中第i测点声波传播时间(μs)
μ
——声时平均值(μs)
σ
——声时标准差
按声时-深度曲线相邻测点的斜率K
及相邻两点声时差值△t的乘积K·△t作为判定桩身缺陷的依据:
K
=
△t=t
-t
K·△t=
式中:
t
——第i测点的声波传播时间(μs)
t
——第i-1测点的声波传播时间(μs)
z
——第i测点的深度(m)
z
——第i-1测点的深度(m)
K·△t值能在声时-深度曲线上明显地反映出缺陷的位置及性质,结合μ
+2σ
值进行综合判定。
由于波幅(衰减量)声速对缺陷的反应更灵敏,采用接收信号能量平均值的一半作为判断桩身缺陷临界值。
波幅值以衰减器的衰减量q表示,波幅判断的临界值qD有下列关系:
q
=μ
-6
μ
=
式中:
μ
——衰减量平均值(dB)
q
——第i测点的衰减量(dB)
n——测点数
对超越临界值的测区进行缺陷分析与判断。
桩的完整性采用以上几种方法进行判定,并辅以接收波形的视率做进一步的综合判定。
在作出缺陷判定后,如需判定桩身缺陷尺寸及空间分布,则进一步采用多点发射,不同深度接收的扇形测量方法,用多条交会的声线所测取的波速及波幅的异常加以判定。
综合判定桩完整性标准
类别
特征
Ⅰ
各个检测剖面的声学参数均无异常,无声速低于低限值异常(优秀桩)。
Ⅱ
某一检测剖面个别测点的声学参数出现异常,无声速低于低限值异常(良好桩)
Ⅲ
某一检测剖面连续多个测点的声学参数出现异常;
两个或两个以上检测剖面在同一深度测点的声学参数出现异常;
局部混凝土声速出现低于低限值异常(需经处理方能使用的桩)。
Ⅳ
某一检测剖面连续多个测点的声学参数出现明显异常;
两个或两个以上检测剖面在同一深度测点的声学参数出现明显异常;
桩身混凝土声速出现普遍低于低限值异常或无法检测首波或声波接收信号严重畸变(报废桩)。
3.6.2、桩基低应变动力检测
3.6.2.1、适用范围;
本方法对于检测桩身混凝土的完整性、判定缺陷类型及其部位,并对桩长进行核实、对桩身混凝土强度进行评价。
3.6.2.2、测试仪器
①现场测试仪器(采集仪)采用RSM-24FD浮点工程动测仪;
②拾振器:
小桩径采用高阻尼速度计、低阻尼速度计、高灵敏度加速度计;大桩径使用高阻尼速度计及加速度计。
③激振设备应有不同材质,不同重量之分,以改变激振的频谱和能量,供激振条件试验时选择或供不同的检测目的时选用。
④检测前应对仪器设备进行检查,性能正常方可使用。
3.6.2.3、现场检测
①对桩头处理,彻底去除浮浆,修复桩头破损部分并磨平桩头;
②测点布置,对于0.8m以上的大直径桩应布置5~9个测点;
③每个检测工地应进行激振和接收条件的选择试验,以确定最佳激振方式和接收条件;
④为提高反射波的分辩率,应使用小能量激振并选用截止频率高的传感器放大器;
⑤对于完好桩,各测点多次重复测试应具有很好的一致性,如出现异常波形应在现场及时研究,排除影响测试的不良因素再重测试。
3.6.2.4、桩身质量判别
①完整桩,其反射波具有波形规则、波列清晰、桩底反射明显、易于读取反射波到达时间、桩身混凝土平均波速较高等特征。
同一工地完整桩反射波形往往具有较好的相似性。
②桩身断裂时,其反射波到达时间小于桩底反射波到达时间,波幅较大,往往出现多次反射,难以观测到桩底反射波。
③严重离析时桩身混凝土的波速较低,反射波幅减小,频率降低。
④当在桩顶检测出的反射波与入射波初始相位一致时,则表明在相应位置存在截面缩小或混凝土质量较差的缺陷;反之,当反射波与入射波初始相位相反时,则表明在相应位置存在扩颈。
⑤根据测定桩身混凝土的波速,可评判桩身混凝土强度。
桩身混凝土的波速按下式计算:
2L
tr
Vp=
式中:
Vp——桩身内混凝土中的纵波波速(m/s);
L——桩长(m)
tr——桩底反射波到达时间(s)。
由上式获得的桩身混凝土波速,可推算桩身混凝土强度,其公式如下:
Rc=A.eBv
式中:
Rc——桩身混凝土强度值(MPa);
V——桩身混凝土波速(km/s)。
A、B——回归系数;
e——自然底数。
一般而言,桩身混凝土强度越高,其波速也高。
由于影响混凝土波速因素较多(如混凝土的骨料品种和大小、混凝土的含水量、龄期、设计标号及成桩质量),故不同工程的检测结果不具可比性,由波速推算所得的桩身混凝土强度指标有一定的局限性,但同一工程,良好桩的混凝土波速应具有较好的一致性。
3.6.3桩基高应变动力检测
3.6.3.1、适用范围
①用于检测基桩的竖向抗压承载力和桩身完整性;
②进行灌注桩的竖向抗压承载力检测时,应具有现场实测经验和本地区相近条件下的可靠对比验证资料;
③本方法不适应对大直径扩底桩或Q~S曲线具有缓变型特征的大直径灌注桩进行竖向抗压承载力检测。
3.6.3.2、仪器设备要求
①检测仪器的主要技术性能指标不应低于《基桩动测仪》JG/T3055中的有关规定,且应具有保存、显示实测力与速度信号和信处理与分析的功能;
②锤击设备宜具有稳固的导向装置;打桩机械或类似的装置(导杆式柴油锤除外)都可作锤锤击设备;
③重锤应材质均匀、形状对称、锤底平整,高径(宽)比不得小于1,并采用铸铁或铸钢制作。
当采用自由落体安装加速度感器的方式实测锤击力时,重锤应整体铸造,且高径(宽)比应在1.0~1.5范围内;
④进行承载力检测时,锤的重量应大于预估单桩极限承载力的1.0%~1.50%,混凝土的桩径大于600mm或桩长大于30m时取高值;
⑤桩的贯入度可采用全站仪或精密水准仪等仪器测定。
3.6.3.3、现场检测
①混凝土桩应先凿掉顶部的破碎层和软弱混凝土;
②桩头顶部应设置桩垫,桩垫可采用10~30mm厚的木板或胶合板等材料。
③距桩顶1倍桩范围内,宜用厚3~5mm的钢板围裹或距桩顶1.5倍桩径范围内设置箍筋,间距不宜大于100mm。
桩顶应设置钢筋网片2~3层,间距60~100mm。
④桩头混凝土强度等级宜比桩身混凝土提高1~2级,且不得低于C30。
⑤高应变检测的桩头测点截面积应与原桩身截面积相同;
⑥传感器的设定值应按计量检定结果设定;
⑦传感器宜分别对称安装在距桩顶不小于2D的桩侧表面处(D为试桩的直径);对于大直径桩,传感器与桩顶之间的距离可适当减小,但不得小于1D。
安装面处的材质和截面尺寸应与原桩身相同,传感器不得安装得在截面突变处附近;
⑧应变传感器与加速度传感器的中心应位于同一水平线上,同侧的应变传感器的中心轴应与桩中心轴保持平行。
⑨各传感器的安装面材质应均匀、密实、平整,并与桩轴线平行,否则应采用磨光机将其磨平。
采用自由落锤为锤击设备时,应重锤低击,最大锤击落距不宜大于2.5m;
⑩承载力检测时宜实测桩的贯入度,单击贯入度宜在2~6mm之间。
3.6.3.4、检测数据分析与判定
①当出现下列情况之一时,锤击信号不得作为承载力分析计算的依据;
a、传感器安装处混凝土工裂或出现严重塑性变形使力曲线最终未归零;
b、严重锤击偏心,两侧力信号幅值相差超过1倍;
c、四通道测试数据不全。
②综合确定桩身混凝土波速;
③锤击信号的调整应符合下列规定:
a、当测点处原设定波速随调整后的桩身波速改变时,相应的桩身材料弹生模量应按E=p·C2重新计算;
b、当采用应变式传感器测力时,应对原实测力值校正。
④承载力分析计算前,应结合地质条件,设计参数,对实测波形特征进行定性检查:
a、实测曲线特征反映出的桩承载状况;
b、观察桩身缺陷程度和位置,连续锤击时缺陷的扩大或逐步闭合情况。
⑤以下四种情况采用静载进一步验证:
a、桩身存在缺陷,无法判定桩的竖向承载力;
b、单击贯入大,桩底同向反射强烈且反射峰较宽,侧阻力波、端阻力波反射弱,即波形表现出竖向承载状况明显与勘察报告中的地质条件不符合;
d、嵌岩桩桩底同向反射强烈,且在时间2L/C后无明显端阻力反射;也可采用钻芯法核验。
⑥承载力计算方法:
a、凯司法;
b、实测曲线拟合。
⑦本法对单桩承载力的统计和单桩竖向抗压承载力特征值的确定高水平符合下列规定:
a、参加统计的试桩结果,当满足其级差不超过30%时,取其平均值为单桩承载力统计值;
b、当极差超过30%时,应分析极差过大的原因,结合全现场具体情况,综上所述来确定,必要时可增加试桩数量;
c、单位工程相同条件下的单桩竖向抗压承载力特征值Ra应按本方法得到的单桩承载力统计值的一半取值。
3.6.4、桩基常规静载荷试验
3.6.4.1、适用范围
①方法适用于检测单桩的竖向抗压承载力;
②当为设计提供依据的试验桩时,应加载至破坏;当桩的承载力以桩身强度控制时,可按设计要求的加载量进行;
③对工程桩抽样检测时,加载量不小于设计要求的单桩承载力特征值的2.0倍。
3.6.4.2、仪器设备及安装
①油压千斤顶、油泵;
②加载反力系统;
③荷载传感器;
④沉降测量系统采用位移型传感器或大行程百分表。
3.6.4.3、现场检测
采用反力系统布置
①堆载反力法
a、承重墙及堆重平台
采用四个特制钢架或砖墙作承重墙,上架钢梁,每个钢架自重1T,用吊车就位。
承重墙基础用碎石填实后,用方木铺垫出2m×7m范围,整平即可吊装钢架。
b、堆重体
根据现场条件,采用编织袋装上或用钢锭作为堆重体。
若用土、砂,甲方将在现场指定取土点,按平均每袋约45kg装土,总量以设计承载力的2.5倍计,装完后根据试验需要由人工搬运至平台上,对称堆高。
试验加压过程中需控制堆重速度,达到最大配重后需严密监测承重墙及试桩沉降,防止失稳。
试验加荷系统退压时,应结合试验要求分步卸重,保证总配重在承重墙和试桩上的合理分配。
②锚桩反力法
采用锚桩时,锚桩数量一般不少于4根。
锚桩、反力梁装置能提供的反力应不小于预估最大试验荷载的1.5~2.5倍。
③锚桩堆载联合反力法
当试桩最大加载量超过锚桩的抗拔能力时,可在横梁上放置或悬挂一定重物,由锚桩和重物共同承受千斤顶加载反力。
试验方法:
①加荷系统
根据规范,采用慢速维持荷载法
试验根据现场条件,采用锚桩横梁反力系统,或堆载反力系统。
压力采用油压千斤顶及高压手下动油泵分级加载,针对不同荷载情况,试验可分别采用一台或多台500T、300T、150T60T千斤顶协同出力的方法进行加载。
荷载采用联于千斤顶的压力表测定油压,根据千斤顶率定曲线换算荷载。
②荷载与沉降的量测系统
试桩沉降采用安装在桩帽四周的4只百分表测量,沉降测定平面离桩顶约30cm。
因定和支承百分表的夹具及基准梁在构造上按规范消除了气温、振动、及其他外界因素影响而发生的竖向变位。
③试验加载方式
试验采用慢速维持荷载法,即逐级加载、每级荷载达到相对稳定后再加下一级荷载,直到试桩极限承载力出现或2倍设计承载力以后,然后分级卸载到零。
加载分级:
每级加载为预估极限荷载的1/10,每一级按2倍分级荷载加荷。
沉降观测:
每级加载后每隔15分钟测读一次,一小时后每隔30分钟测读一次,并记入试验记录表。
沉降相对稳定标准:
每一小时内的沉降不超过0.1mm,并连续出现两次,则认为已达到相对稳定,可加下一级荷载。
终止加载条件:
当出现下列情况之一,即可终止加载。
a、某级荷载作用下,桩的沉降量为前一级荷载作用下沉降量的5倍。
b、某级荷载作用下,桩的沉降量大于前一级荷载作用下沉降量的2倍,且经24小时仍未达到相对稳定。
a、已达到锚桩最大抗拔力。
b、达到加荷系统的最大出力。
卸载与卸载沉降观测:
每级卸载值为每级加卸值的2倍,每级卸载后每隔15分钟测读一次残余沉降,读两次后,隔30分钟再读一次,即可卸下一级荷载,全部卸载后,隔3~4小时再读一次。
3.6.4.4、单桩竖向极限承载力的确定
①根据沉降随荷载的变化特征确定极限承载力;对于陡降型Q~S曲线取Q~S曲线发生明显陡降的起始点;
②根据沉降量确定极限承载力:
对于缓变型Q~S曲线取S=40~60mm对应的荷载。
③根据沉降随时间的变化特征确定极限承载力:
取S~logT曲线尾部出现明显向下弯曲的前一级荷载值。
3.6.4.5、单桩竖向极限承载力标准值的确定
①实测极限承载力平均值:
Qum=
②极限承载力实测值与平均值之比:
=
③标准差
④确定单桩竖极限承载力标准植:
当Sn≤0.15时,Quk=Qum
Sn≥0.15时,Quk=Qum(从规范中查表确定)
3.6.4.6、单桩竖向承载力设计值的确定
根据静载试验确定单桩竖向极限承载力标准值时,单桩的竖向承载力设计值为:
R=Quk/rsp
rsp——桩基竖向承载力抗力分项系数,按规范取值。
3.6.5、灌注桩钻芯取样法
钻芯取样法的工艺流程为:
施工准备→钻机调正水平、对孔位→开孔钻进→取芯→钻进结束→注浆封孔→取样→测试→提交成果。
3.6.5.1使用范围
本方法用于抽样检