二氯车间氯化岗位操作规程岗位操作规程.docx
《二氯车间氯化岗位操作规程岗位操作规程.docx》由会员分享,可在线阅读,更多相关《二氯车间氯化岗位操作规程岗位操作规程.docx(27页珍藏版)》请在冰豆网上搜索。
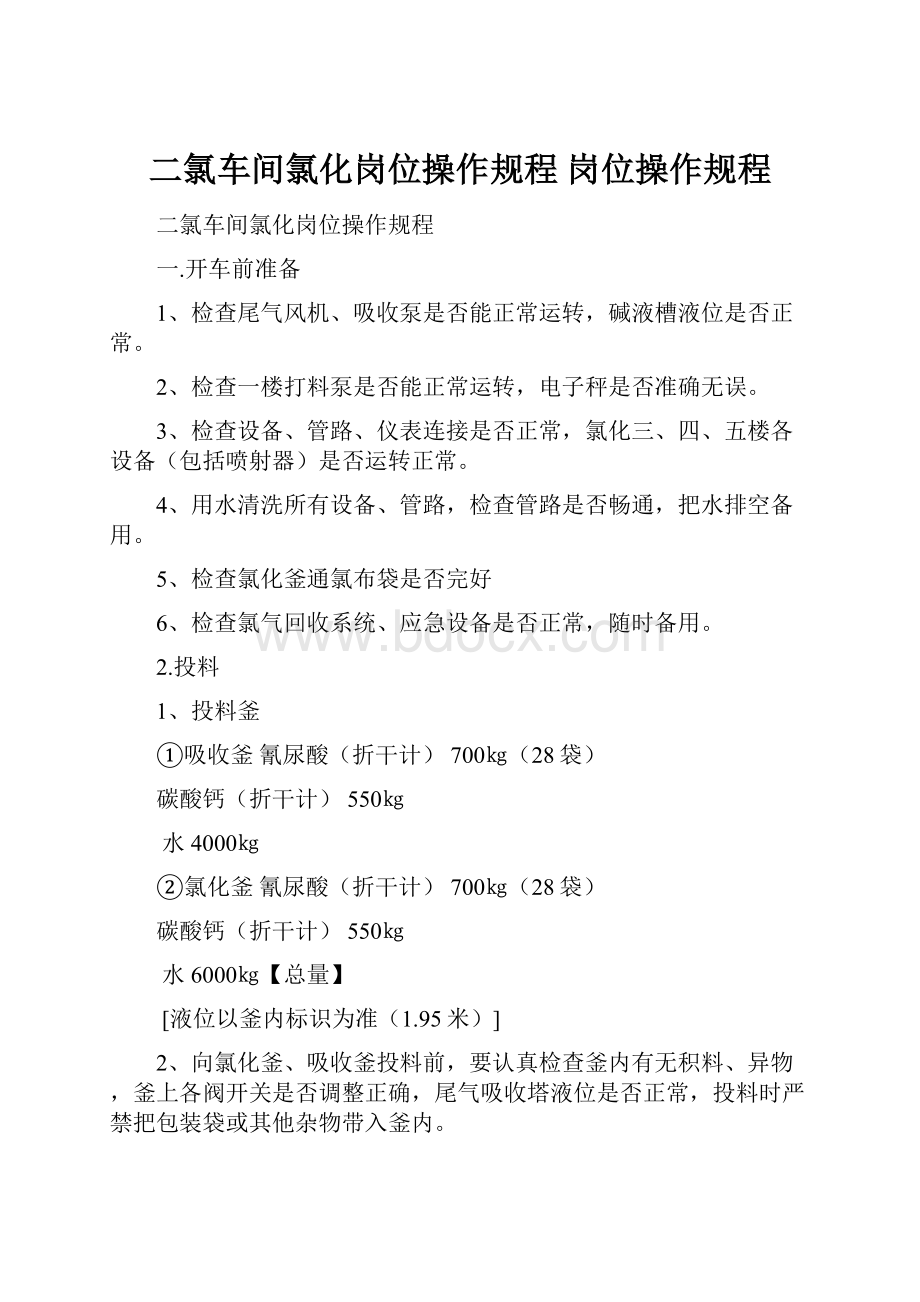
二氯车间氯化岗位操作规程岗位操作规程
二氯车间氯化岗位操作规程
一.开车前准备
1、检查尾气风机、吸收泵是否能正常运转,碱液槽液位是否正常。
2、检查一楼打料泵是否能正常运转,电子秤是否准确无误。
3、检查设备、管路、仪表连接是否正常,氯化三、四、五楼各设备(包括喷射器)是否运转正常。
4、用水清洗所有设备、管路,检查管路是否畅通,把水排空备用。
5、检查氯化釜通氯布袋是否完好
6、检查氯气回收系统、应急设备是否正常,随时备用。
2.投料
1、投料釜
①吸收釜氰尿酸(折干计)700㎏(28袋)
碳酸钙(折干计)550㎏
水4000㎏
②氯化釜氰尿酸(折干计)700㎏(28袋)
碳酸钙(折干计)550㎏
水6000㎏【总量】
[液位以釜内标识为准(1.95米)]
2、向氯化釜、吸收釜投料前,要认真检查釜内有无积料、异物,釜上各阀开关是否调整正确,尾气吸收塔液位是否正常,投料时严禁把包装袋或其他杂物带入釜内。
3、首次投料,向投料釜内先加入深井水4000㎏,开启搅拌,加入氰尿酸(折干)700㎏,加碳酸钙(净重)550㎏,搅拌3~5分钟后,开启打料泵向吸收釜打料,等打到搅拌搅不到液位时,停搅拌,用扒子搅拌料液,并用水冲洗干净物料,开始下一釜投料。
4、打开吸收釜放料阀向氯化釜放料,并用水冲净吸收釜内物料,关闭吸收釜放料阀,再次向吸收釜打料,等吸收釜打好料后,开启循环泵,向氯化釜投入十二烷基硫酸钠150g,补充液位至液位标线,开氯化搅拌。
5、正常生产投料向投料釜内先加入深井水4000㎏,开启搅拌,加入氰尿酸(折干计)700㎏,加碳酸钙(净重)550㎏,搅拌3~5分钟后,开启打料泵向余氯回收釜(1楼)或吸收釜打料,等打到搅拌搅不到液位时,停搅拌,用扒子搅拌料液,并用水冲洗干净物料,开始下一釜投料。
6、余氯回收釜(1楼)内打入物料后,开启循环泵,每釜循环不超过2小时,温度不超过35℃,即可向吸收釜打料,待料液打净冲洗干净后,即可进入下一轮投料循环。
三、通氯
1、通知通氯岗位人员开启循环降温水泵,打开相对应的氯化釜通氯阀,并调节流量小于50m3/h,同时据情决定是否开启尾气吸收塔风机及碱液循环泵。
氯化釜温度超过31℃时应适当减小通氯量或停氯降温。
如降温效果不明显,可以往氯化釜内加深井水,以达到降温的效果。
2、观察釜内液面泡沫情况,泡沫不宜过大,如过大可适当关小通氯阀门或停止通氯,防止溢釜。
3、通氯1.5小时后每间隔10分钟测一次PH值,当PH值小于3.5时开压缩空气阀吹扫,流量控制100m3/h左右,氯化釜口要不显正压,要保证尾气抽力负压不低于50㎜水柱[上人孔盖时]。
不进行空气吹扫时釜内负压不应低于200mm水柱。
4、当PH值小于3.5时,加入一水柠檬酸1.5㎏,通氯流量控制在30m3/h以内,每间隔5分钟测一次PH值,随反应液PH值的降低,逐步减小通氯流量。
5、连续测三次以上PH值<2.0时,或PH值无变化时,及时通知液氯库人员关停相对应的通氯阀,盖釜口,进行抽余氯,约30分钟后,发现液面变白无泡沫,通知洗料人员准备放料,放料时关闭缓冲罐后的通氯阀。
在整个操作过程中,温度必须控制在31℃以下。
6、氯化釜放料完毕时,关闭空气阀,要用清水冲洗釜壁及釜底残留物料,冲洗干净后关闭釜底阀,停四楼循环泵,打开相对应的吸收釜放料阀放料,完毕后关闭四楼放料阀,通知一楼投料人员往吸收釜打料。
7、吸收釜往氯化釜放料时,将相对应的氯化釜釜盖盖严,停搅拌,打开余氯回收阀与正常循环的吸收釜抽余氯阀门串联吸收余氯,以达到抽吸氯化釜余氯的目的。
8、发现四楼循环泵管道堵塞或泵体漏液时,要及时停泵并通知维修工处理,并关相应的通氯阀,吸收釜内没有液体禁止开启循环泵,防止磨坏水泵密封。
以上操作过程周而复始循环。
四.注意事项
1、随时做好个人防护,确保个人安全。
取样、氯化釜观察时必须佩戴防护面具或眼镜。
2、严格按照各工艺要点执行:
氯化温度须控制在25---31℃,最宜温度28—30℃,不可>31℃;通氯压力≤0.2MPa;终点PH值为≤2.0;吸收釜温度≤35℃。
冷却盘管供水压力≮0.2MPa,氯化釜抽气负压正常时不得低于200毫米水柱,空气吹扫时不得低于50毫米水柱。
3、投料计量准确,碳酸钙要过磅计量,并打印记录,氰尿酸要检查包装袋完好无破损,破袋的氰尿酸不准使用,打料要干净,每釜投料后将原料包装袋捆好,放置在对应釜号位置。
4、当PH值≤3.5时开压缩空气吹扫,可根据负压情况开启四楼第二台循环泵,注意检查余氯回收流量计。
5、不能忘记加催化剂,一水柠檬酸在氯化PH值≤3.5时或液面泡沫消失,再加入氯化釜。
6、PH值≤2.0,(或液面变黄)达到终点后,停止通氯,取样分析。
7、通氯流量不能过大,防止液氯直接进入氯化釜或反应过急造成溢釜。
8、临近终点时,5分钟连续三次测量PH值不变时,立即停止通氯。
若经分析有效氯小于68%的物料,追究投料工的责任。
9、终点控制要连续测三次以上PH值,以保证准确性。
10、发现氯气缓冲罐结霜,立即联系液氯库人员调减通氯流量。
11、放料前必须抽余氯,以保证工作环境。
12、紧急停电时,立即关闭通氯阀,打开放空副线阀。
岗上人员要在场严密监控温度、料液变化情况,防止超温。
13、各釜打料或放料前,要检查有关釜底放料阀是否关闭,防止打重料或放下生料。
打重料在通氯过程中会造成溢釜,放下生料会造成氯化料缓冲槽内的物料损失。
14、氯化釜及搅拌器上发现油污立即清理干净,严禁油污进入氯化釜。
五.安全注意事项
1、各机械设备须按操作规程操作。
2、不得用潮湿手去摸电机或用湿棉纱擦试电机。
3、氰尿酸、氯化料在存储、周转过程中严禁与油类、含氮类、铁锈以及粗品等接触,以免发生事故。
4、严禁敲击震动氯转子流量计,防止震碎流量计玻璃管,意外跑氯。
5,氯化放料后须检查釜内情况,观察通氯管、通氯布袋、搅拌翅等有无异常。
如放料后发现釜内存有结块物料,立即向带班主任报告,严禁私自随意处理,以防意外。
七、异常情况及处置措施
1、发现设备不正常运转时,及时通知维修人员进行处理。
2、在氯化反应发现液面局部冒泡时应减小通氯流量,缓慢通氯直至反应终点,放料后更换通氯布袋。
3、发现氯化釜循环冷却水不正常时,及时通知通氯岗位人员调减相对应的通氯阀,检查是否有结冰现象并停止通氯及时处理。
4、发现氯化釜有氯气外溢时应立即关闭通氯阀,停止通氯,检查釜口是否显负压状态、釜内温度及降温水是否正常。
A、如果釜口不显负压,则有可能是四楼循环泵出现故障,应应更换循环泵及调节三楼抽气副线阀,抽吸余氯;然后检查四楼循环泵及喷射器,通知维修工立即检修循环泵或喷射器。
B、如果是釜内温度过高,可适当往釜内加水达到降温的目的。
同时检查降温水是否正常,如不正常则检查该釜对应的降温水管道是否通畅、阀门是否全开以及降温水泵是否跳车。
5、氯化人员在操作过程中发现现场气味较大,应立即戴防毒面具、防护手套,携带包塑料F扳手及氨水查明情况。
如果在通氯管道或法兰连接处出现漏点,应立即关闭漏点前的阀门或通知通氯岗位人员关闭液氯槽车供氯阀(根部阀)。
6、通氯未结束而遇突然停电的氯化料,再次来电后,必须按以下操作:
首先启动喷射泵抽釜内尾气10—20分钟,然后再开搅拌5分钟,确认无异常后可恢复盘管冷却水、通氯。
目的是预防因停电温升而可能产生的三氯化氮集聚。
化工集团有限公司
二氯车间水洗岗位操作规程
一.开车前准备
1、检查真空泵、转鼓抽滤、循环槽液位、洗水泵、洗水槽液位是否正常,管路、仪表连接是否正常,阀门是否按要求调整好。
2、检查空气压力,排水、抽气管路是否畅通,分离器是否正常。
3、检查电磁阀,气缸是否正常。
4、检查滤布是否平整,是否有破损,如有破损应予以更换。
二.操作过程
1、打开真空泵放空阀,调节泵入口阀开度至1/3阀位,开循环水,开泵。
等泵运行正常后,全开泵进出口阀、关放空阀。
2、启动电磁阀、转鼓内搅拌、转鼓,洗水泵。
3、检查转鼓喷水水泵是否正常。
4、开氯化液储槽放料阀,向转鼓抽滤槽内放液,保持低液位(高于转鼓10公分)。
5、开始出的湿料要返回到转鼓料槽内。
6、等待水份合格后按要求做水份,准确称重,保证物料净重折干160㎏。
7、料车接满料后,联系中和岗位往楼上提料。
8、控制要求水份≤27%,折干后的重量误差小于1㎏。
三、停车
1、物料出完后,依序停洗水泵、转鼓搅拌、转鼓、电磁阀。
2、关真空泵循环水,关闭泵进口阀,开放空阀,停真空泵,关闭泵循环水,如泵长期不用,排净真空泵泵腔内积水。
四、注意事项
1、随时做好个人防护,确保个人安全。
2、真空泵开启前认真检查加水阀是否打开,泵腔内是否有水,盘车是否灵活。
3、经常观察氯化料水份,氯化料水分高于27%的不准用于中和投料。
4、紧急停电时,关闭氯化液贮槽放料阀,防止转鼓抽滤料槽物料外溢。
5、空气压力低,电磁阀、气缸不能正常工作时,立即停真空泵,严禁分离器带液进入真空泵。
五、安全注意事项
1、各机械设备须按操作规程进行操作。
2、擦电动机不准戴手套,以防袖口和或棉纱绞进靠背轮。
3、电机必须在无负荷情况下启动,运行中不能超过额定电流。
4、电动机联轴器必须戴上防护罩。
5、不得用潮湿手去摸电机或用湿棉纱擦电机。
6、严禁靠近开关闸刀,待停车拉下闸刀后才能拉保险。
7、使用上料提升机须严格按车间规定制度执行。
六、异常情况及处理
1、发现设备不正常运转时,及时通知维修人员检查处理。
2、发现负压不正常时,检查相对应的真空系统是否有漏点,阀门是否调整正常,循环水是否正常,发现问题及时维修。
化工集团有限公司
二氯车间中和岗位操作规程
一.开车前准备
1、检查空气压力是否正常。
2、检查中和机、混拌机运转是否正常,中和机放料阀是否能正常开关。
3、检查纯碱绞龙运行是否正常。
4、检查锥形混拌机、打散机、1#加料绞龙保持系统无积存物料、无异物;检查设备内外无漏油现象(绝对杜绝油污染产品)。
5、检查变频调速器、混拌机、打散机、1#绞龙是否正常。
6、了解中和机供料时间、均匀供料量(一般每套折干2000kg/h)。
7、检查本工序设备操作现场无可燃物、油脂类、含氮类等物质。
如有,首先清除。
8、备足打散用网量,一般现场要保证正常5天的使用量。
9、检查打散机使用工具是否齐全,确保打散系统干净无异物。
10、检查打散机是否运转正常,尼龙网是否破碎;进料和出料软连接是否完好;开车前应检查打散机转向与箭头是否相符,严禁反转使用。
11、五楼料车备足16车物料及4吨纯碱。
二.配料
每批投湿品二氯异氰尿酸(折干)160Kg、碳酸钠40Kg。
三.中和开车
1、在投料前了解产品含水量情况,进入中和机的二氯酸含水量应小于27%;先开锥形混拌机、三楼混和机再开中和机及纯碱绞龙,将氯化料160Kg加入中和机后,用纯碱绞龙加入40Kg碳酸钠,混拌2-5分钟(夏季六、七、八月份1-2分钟,冬季2-3分钟),控制中和料PH值在5.3-6.3之间。
2、将中和料放到四楼缓存间,然后用锨均匀放料至三楼混拌机,直至物料到达混拌机限位标线位置。
3、中和机投料后,通知各干燥系统,升温待投料;按需要打开加料绞龙放料控制阀,依次开启3#加料绞龙、2#加料绞龙、1#加料绞龙。
4、当1#干燥机、2#干燥机升温至要求的进风温度时(按工艺要求执行),启动打散机,打开锥形混拌机放料阀,确保放料量不超过滚筒高度,保持能看到滚筒转动为准;下料量保持1#加料绞龙进料仓露出搅翅2-3厘米为宜,防止投料过多造成阻力过大,损坏机器和筛网,物料应均匀加入绞龙进料仓,不可集中进料。
5、调整1#加料绞龙前两个出口的出料量,下料量保持满足1#干燥机、2#干燥机使用量为宜,当干燥设备不能全部启动时,应按干燥能力,减少中和投料量。
确保系统不过多积存物料,保持物料进出平衡。
6、当1#干燥机、2#干燥机稳定运行后,通知流化床干燥升温运行。
当流化床干燥升温至140℃时,打开1#加料绞龙的第三个出料阀;通知五楼中和人员加大投料量,同时,调节锥形混拌机放料阀,确保流化床干燥的供给量。
7、所有加料绞龙料仓内物料不要高于破拱器搅拌齿片,否则易造成停机现象。
8、稳定后调整混拌机下料量,用1#锥型混拌机的放料调节板调节流化床干燥的出口温度;用2#锥型混拌机的放料调节板调节2#气流干燥的出口温度。
四、停车步骤
1、根据生产规定或要求,首先,停止中和机加料,并清理中和机内物料,待物料放净后停中和机。
中和断料要及时通知流化床停蒸汽,并及时往4#绞龙补料。
2、物料全部输出后,保持混拌机内不存料,停混合机,停锥形混拌机搅拌,关闭放料阀。
同时,通知干燥准备停车。
3、待打散机物料全部输出,停打散机,清理打散滚筒和尼龙网。
4、当1#加料绞龙内物料全部输出后,清理进料仓物料,停1#加料绞龙;分别关闭三个放料阀。
5、待2#、3#、4#加料绞龙内物料全部输出后继续空转5分钟,以清理进料仓物料,然后分别停上述加料绞龙。
如干燥系统长时间停车(超过7天),应对全部绞龙加元明粉清理。
五、安全注意事项
1、随时做好个人防护,确保人身安全。
2、中和放料要保证均匀,间隔时间要稳定。
3、锥形混拌机料仓内的物料要保持稳定,严禁缺料及超过安全标线(一般控制20%-60%)。
4、混拌机、打散机、加料绞龙内如有沾料、积料要及时清除干净;中和、混拌、输送过程中,避免含氮、铁锈等异物进入;避免带入油类、纸张、纤维、编织袋、塑料袋等可燃物。
5、环境温度过高时,中和物料结晶水易析出,会造成物料粘稠。
中和是放热反应,一般中和反应温度在45℃左右,如环境温度过高,中和反应温度将大于60℃,要以部分小苏打中和,用于平衡反应热量,当用碳酸氢钠代替部分碳酸钠时:
1kg碳酸氢钠等于0.63kg碳酸钠。
应确保反应温度不得大于50℃。
6、打散机内如物料停滞不下,切不可用手直接处理,以防造成伤手。
应用塑料铲清理或停机后处理,未经打散的物料不准直接进入干燥工序。
7、如有破碎尼龙网进入物料须及时取出,防止混在物料内进入干燥工序,造成不良后果
8、随时观察设备运行情况,出现异常,立即联系维修人员检修。
9、定时检查两设备之间连接处,防止物料堵塞。
10、氯化料水分超标时(水分高于27%)严禁投入中和机进行中和。
11、楼上物料少于3车或氯化料洗料跟不上时,要及时通知流化床岗位逐步减量停车。
11、交接班检查打散网,班中检查一次打散网,确保打散网正常使用。
六、异常情况及处理措施
1、四楼中和机如因开关问题搅拌时间过长产生粘料,要及时清理出料池,不许放入三楼混拌机。
待物料在设备外挥发掉水分后再重新使用。
2、三楼混拌机堵塞停机,及时通知五楼和四楼中和人员,停止中和。
清理混拌机要先从下部开始,依次清理放料口、锥形混拌机、混合机,并通知干燥岗位降低负荷,减少投料量,待处理完后再恢复正常。
3、如中和机内部发生物料分解,应及时打开放料阀,将分解料放出并清理出料池,摊开降温就可以及时阻止物料分解。
4、锥形混拌机故障停车:
全部打开放料阀,用塑料管由上至下捣料促使物料全部流出;物料全部流出后,按停车程序操作,通知干燥部位停车。
5、打散机故障停车:
如是筛网破碎,可临时不需更换、应急使用,但不可超过30分钟;如打散机无法运行,应将打散机物料全部放入1#加料绞龙料仓,并将物料全部输出后,干燥停车修理。
6、1#加料绞龙、2#加料绞龙、3#加料绞龙、4#加料绞龙故障停车:
发现问题,通知干燥停车,并停止中和机、混拌机、打散机供料,及时组织人员抢修,确保系统物料及时输出。
7、突然断电时,要打开所有设备放料阀,及时将中和机、混合机、锥形混拌机内物料清理出来,防止物料分解。
8、当接到流化床岗位停车通知后要迅速关闭4#绞龙插板,在3#绞龙接料口把物料引出。
9、如在中和机放料时发现物料异常,要及时将物料清理出四楼缓存间。
禁止物料进入混合机,防止PH值高造成物料分解。
化工集团有限公司
二氯车间气流干燥工段操作规程
一、开车前的准备工作
1、检查蒸汽加热器、电加热器,准备升温。
2、检查本工序转动设备:
摇摆颗粒机、2#、3#送料绞龙、加料绞龙、送风机、引风机是否正常运转,有无异常声音,内部有无异物、积料。
3清理并检查除尘布袋和上升管各检查孔及旋流器、旋风分离器内的物料,特别是热风管路中的物料,清理后关闭手孔门。
4、检查本工序操作现场有无纸张油脂类等可燃物、含氮类、灰尘沙砾等物质,如有,首先清除。
5、系统运行时检查各连接管道是否漏风。
6、在二楼1#、2#投料口处存4袋中和料备用。
二、开车操作方法
1、先开引风机、送风机后,开启蒸汽加热器、电炉,联系中和岗位开车,开2#或3#绞龙及给料绞龙,待尾气温度80℃以后开始供料,启动摇摆颗粒机,调整合适的转速,开始向干燥系统加料。
此时,干燥操作人员要注意观察给料绞龙料斗内的情况,在料斗破料齿处形成空腔或角落形成死料时,及时用塑料管调整;同时注意调整加料速度,刚开始时加料速度要慢,避免供料太快溢出料斗或供料太慢使干燥系统空转,造成温度控制不稳。
2、干燥过程中,进口温度严格控制热风在190-195℃之间,混合温度120-150℃,尾气温度在90-95℃,不得超限,防止因高温分解。
发现温度异常及时进行调整。
3、注意调节脉冲除尘器后引风机风量,控制系统风压为微负压至微正压,一般可在10--200/260毫米水柱,注意负压不要过高,以免过多冷空气抽入系统,以及过多物料抽入脉冲除尘器。
4、干燥系统加料后,在出口处放好接料袋,将连接布袋口放入袋中。
5、接粉料人员及时更换接料袋防止粉料溢出,时刻注意物料干度(手感)、颜色、粒度变化。
6、正常停车时,干燥主操要先停电炉、蒸汽加热器。
在降温过程中,要逐步减小加料量,维持尾气温度在工艺要求范围。
当进风温度降到接近尾气温度时,停止加料。
当进风温度低于70℃后方可停送风机、引风机。
在停车期1小时内,人员不准离开现场,以观察监控。
7、停车后,要及时检查清理干燥上升管下部、干燥弯管、旋流器下部、旋风除尘器及脉冲除尘器内积料。
三、.安全操作注意事项
1、在干燥开车前,首先要彻底清理干燥绞龙尾部、上升管下部、干燥弯管、旋流器、脉冲除尘器内物料,清理后关闭手孔门,才能开启鼓引风机,开蒸汽加热器、电加热器。
2、严格控制进风温度控制在不得高于195℃,尾气温度须小于95℃。
3、干燥过程中旋风分离器不得过多存料,一定要注意及时出料,以防因高温物料集聚散热不良引起自然分解。
4、干燥开车期间,主操作要注意经常检查、协调、联系,特别时刻注意给料绞龙运行情况,严禁出现绞龙空转现象,打散网一旦出现破损及时更换。
干燥接料工必须坚守岗位,及时接料,及时调整,使旋风分离器内物料能够随时接出,确保系统内不积料,注意观察有无分解料接出,发现分解料块应及时通知主操作,便于迅速处理。
5、气流干燥在二楼扒料时,严禁大块物料进入绞龙,以减少成块的物料在上升管下部堆积。
6、干燥开车后每2小时,须检查清理干燥上升管下部物料,缩短物料在干燥上升管下部停留时间,防止物料分解。
7、干燥连续开车3小时后,投料工要控制加料速度,以防止干燥上升管堵塞,造成分解事故。
8、连续开车5小时,必须停机进行清理系统积料一次,包括脉冲除尘器布袋、干燥弯管、旋流器、上升管下部。
9、当环境温度超过32℃,干燥人员要对产品通风降温。
10、干燥岗位接料用制粒下来的包装粉剂的周转袋,同时检查无油污或其它杂物方可使用,由制粒岗位负责监督。
11、停止加料后,先关闭加料绞龙,继续以最大风量吹除系统内物料,待进风温度下降到70℃以下,方可停送风,严禁高温停车。
12、干燥过程注意加料底部掏料孔处温度,发现底部温度降低,说明底部积料,应及时停车清理。
13、保持送风机除尘布袋的完整,以免木质纤维、碳等易燃物质进入系统。
四、异常情况及处置措施
1、上升管堵塞及旋风分离器堵塞:
加料绞龙处显正压,接料口不出料及混合温度低,都有可能是上升管堵塞造成。
投料工在正常投料时发现混合温度及尾气温度持续下降,应及时查看进风温度是否正常;如正常,则应及时检查上升管下部检查孔。
发现上升管下部堵塞后,要及时通知干燥主操和带班主任,立即停止电加热、关闭蒸汽加热,停止引风机、鼓风机。
干燥主操要及时打开上升管底部检查孔、加料绞龙对面检查孔和旋流管底部检查孔,并清理物料。
同时安排人将除尘器内物料清理出来,待物料清理干净后关闭检查手孔,然后开引、送风机降温,进风温度降到120℃-150℃后准备开车。
2、绞龙跳车断料:
尾气温度持续上升或报警装置报警,投料工确认绞龙跳车后,要及时停止电加热,关闭蒸汽加热。
干燥主操要及时打开上升管底部检查孔、加料绞龙对面检查孔和旋流管底部检查孔,并清理物料。
待进风温度降到150℃后,停送风机,清理除尘器物料。
加料绞龙检修正常后关闭各检查孔,开引、送风机,准备开车。
3、干燥上升管下部物料分解:
发现干燥上升管下部物料分解,应立即停止电加热、关闭蒸汽加热,停止引风机、鼓风机。
迅速打开上升管下部检查孔、加料绞龙对面检查孔及旋流器下部检查孔,将分解料清理干净。
干燥主操要安排人将除尘器内物料清理出来,待物料清理干净后关闭检查手孔,然后开引、送风机降温,进风温度降到正常值(190℃以下)后准备开车。
4、旋风分离器内部物料分解:
发现旋风分离器内部物料分解,立即停止电加热、关闭蒸汽加热,停止引风机、鼓风机。
切断旋风分离器下部软连接,打开除尘器下部放料孔,并迅速切断分离器和除尘器之间的软连接,避免事态扩大。
5、脉冲除尘器内部物料分解:
发现脉冲除尘器内部物料分解,立即停止电加热、关闭蒸汽加热,停止引风机、鼓风机,打开除尘器下部放料孔,并迅速切断分离器和除尘器之间的软连接,迅速打开所对应的喷淋装置阀门,用大量水降温稀释物料,避免事态扩大。
6、物料分解事故发生后,应做好如下工作:
A、及时报告带班主任和前后工序人员;B、按前述异常情况及处置措施立即予以紧急处置;C、当分解物料量较多,氯气释放量较大时,在确保人身安全的同时,应采取积极的办法进行紧急捕消氯气,及时处理释放的氯气,尽量减少污染,为社会力量及时到来援助和人员疏散赢得宝贵时间;D、如事态难以及时控制,须切断气流干燥系统全部电源,防止发生二次伤害;如必要,须立即通知流化床干燥停车。
五、气流干燥系统水洗操作
1、气流干燥系统运行期间每月至少水洗一次,以及56%改产60%含量产品时,应进行系统水洗操作。
系统水洗的操作如下:
2、水洗管道前的准备
2.1、彻底清理干燥管道:
从加料绞龙、干燥上升管、顶倒U型弯、旋流器、旋风分离器到脉冲除尘器内部的物料要全部清理干净,防止水洗过程中造成物料损失。
2.2、清理干燥工段现场的物料:
所有可能漏水的部位不得存有物料,防止物料受潮分解。
2.3、将干燥管道各处检查孔封闭,达到开车备用的状态。
2.4、靠近干燥管道的电机要检查是否覆盖严实,以防水淋。
2.5、连接水阀到干燥上升管的加水管道,封闭严实防止漏气。
2.6、在旋风除尘器出料口处准备接水容器备用。
3、水洗步骤
3.1、开启引风机和鼓风机10分钟,敲打旋风分离器及脉冲除尘器,使系统内附着的物料尽可能脱落。
关停风机,清理系统内物料。
物料清理干净后,重新封闭各出料口,备用。
3.2、再次开启引风机和鼓风机,待风压正常后开启加水阀往系统供水。
刚开始加水时水流不宜太大,待旋风分离器有洗水流出时再逐步加大洗水量。
整个水洗时间大约需1个小时。
3.3、待洗水完全清澈后,关闭加水阀,关停所有风机,打开干燥上升管及旋流管下部检