降低车钩三态作用不良故障率QC课件.docx
《降低车钩三态作用不良故障率QC课件.docx》由会员分享,可在线阅读,更多相关《降低车钩三态作用不良故障率QC课件.docx(33页珍藏版)》请在冰豆网上搜索。
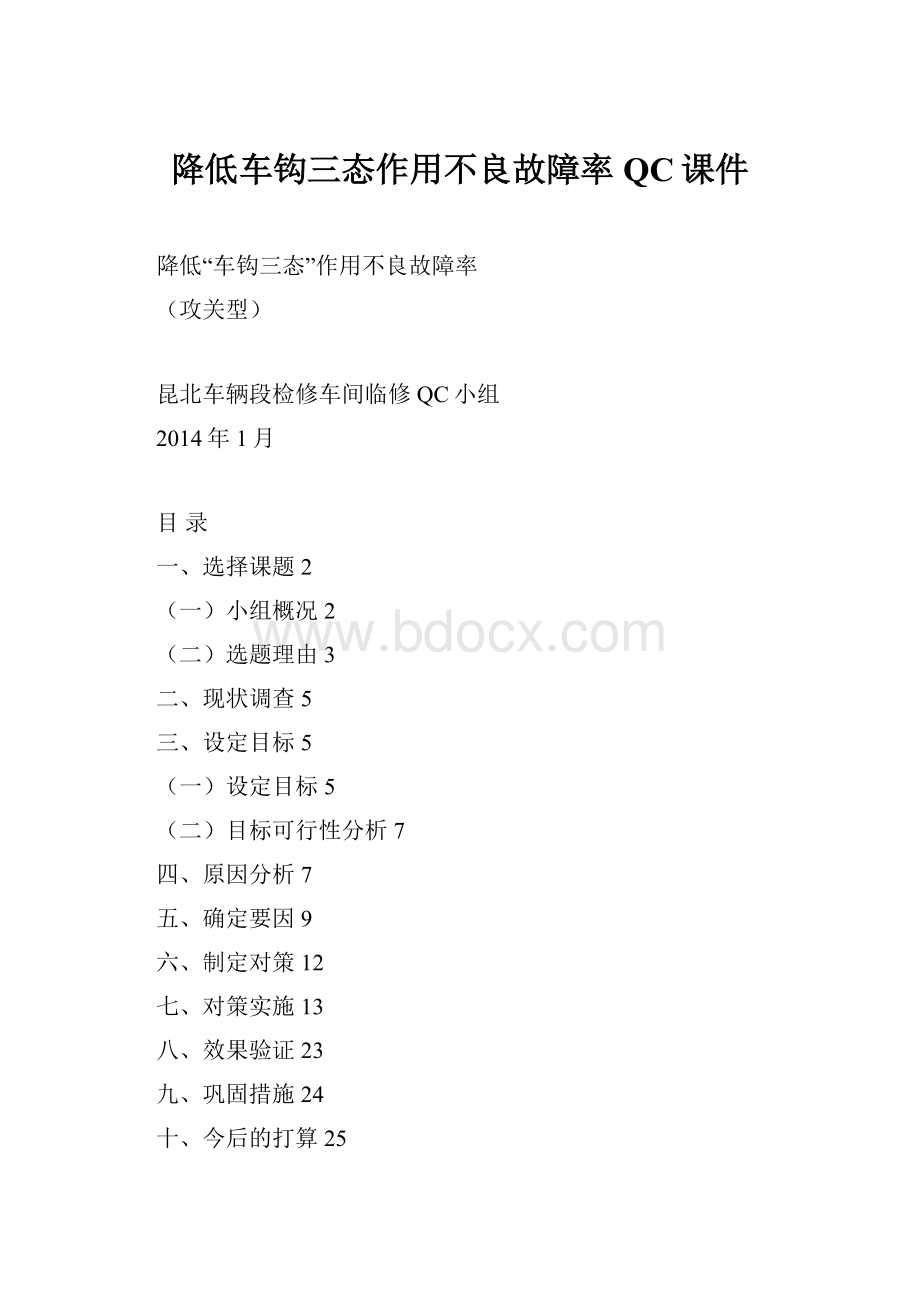
降低车钩三态作用不良故障率QC课件
降低“车钩三态”作用不良故障率
(攻关型)
昆北车辆段检修车间临修QC小组
2014年1月
目录
一、选择课题2
(一)小组概况2
(二)选题理由3
二、现状调查5
三、设定目标5
(一)设定目标5
(二)目标可行性分析7
四、原因分析7
五、确定要因9
六、制定对策12
七、对策实施13
八、效果验证23
九、巩固措施24
十、今后的打算25
一、选择课题
(一)小组概况
QC小组名称
临修组QC小组
注册号
RN506-10-2014
成立日期
2014年6月10日
登记
日期
2014年6月10日
小组活动
每月一次,有内容,有目的,记录完整
小组人员情况
顺序
姓名
年龄
性别
职务
文化
程度
组内
职务
顺序
姓名
年龄
性别
职务
文化
程度
组内
职务
1
李锐
36
男
工长
大专
组长
4
熊成华
43
男
副工长
中专
组员
2
唐明星
41
男
技术员
中专
组员
5
刘智辉
35
男
组员
大专
组员
3
白萱琦
25
女
组员
大专
组员
6
余丽仙
37
女
组员
大本
组员
培训情况:
小组成员均经过完整的培训,并且每年脱产和半脱产培训时间为6课时以上,都熟练掌握TQC(TQM)知识。
小组成员掌握TQM(TQC)知识情况:
一般3人,熟悉3人,
(二)选题理由
段2014年度质量目标:
段修一次交验合格率≥96%;车间质量分目标:
段修一次交验合格率≥97%;班组结合现场生产实际情况,车钩岗位2013下半年一次交验合格率仅为90%,并未能完成段及车间所要求的质量任务目标。
为在2014年内确保实现段及车间的质量目标,我们必须努力提高车钩检修质量合格率。
我们QC小组针对2013下半年内班组车钩作业岗位质量漏检故障统计表进行原因分析,共分为五类重点常见故障见下表:
序号
故障原因
2013下半年
合计
故障比率
6月
7月
8月
9月
10月
11月
12月
1
钩提杆座螺栓松动
3
2
2
1
1
2
3
14
26%
2
车钩三态作用不良故障
4
2
3
3
2
3
3
20
38%
3
钩提链松余量不足
1
2
1
2
1
1
8
15%
4
钩提杆裂纹及变形
1
1
2
1
5
9.6%
5
车钩钩腔防跳台磨耗超限
1
2
1
1
5
9.6%
6
累计故障数
9
7
8
7
4
9
8
52
从上述表中可以看出:
1、车钩三态作用不良故障发生率频繁,周期性长,隐蔽性强,是2013下半年内导致班组质量漏检合格率不达标的主要因素。
2、钩提杆座螺栓松动漏检故障的发生频率仅次于车钩三态作用不良故障。
也是导致车钩岗位检修质量不达标又一因素。
3、根据2013下半年班组每月对车钩检修累计故障统计数来看:
“车钩三态”作用不良故障是车钩岗位作用过程中五类重点漏检故障总数平均值的38%,车钩三态作用不良故障问题突出,直接影响班组交验检修生产任务合格指标,对此我们小组决定把2014年QC攻关课题确定为“降低车钩三态作用不良故障率”。
二、现状调查
序号
车钩岗位作业现状
存在问题
结果
1
作业人员在对现车车钩检修作业过程中,只对可视部位钩体外观检查、而对钩腔内部配件检查时,受到客观条件限制,无法全面彻底进行视觉故障判断。
检查互控人员无法有效进行质量监督卡控。
钩腔配件磨耗超限,导致三态作用不良故障率上升。
2
因车钩使用年限长,钩腔内部磨耗严重、钩体上、下防跳台磨耗、钩腕外胀等诸多因素导致钩体与钩腔内部(钩舌、钩锁、上锁销组成、钩舌推铁等)零部件间配合不良。
车钩检修作业人员无法直观检查发现车钩质量故障。
检修成本高,效率低。
3
不同作业人员在对车钩三态试验方法的掌握和经验积累程度上也有一定业务差距。
人员业务素养参差不齐。
车钩检修质量不稳定。
4
二硫化钼干性润滑油脂的使用,由于其水溶性属性导致在雨季受到环境因素影响,钩腔配件润滑效果不良。
车钩三态作用受外在环境条件限制。
雨季钩腔内锈蚀严重,配件润滑作用不良。
故障
车钩三态作用不良故障率频繁
2012年与2013年车钩质量故障对比表
项目
质量故障
2012年
2013年
故障上升
百分比
车钩三态实验故障率
钩提杆座螺栓松动
27
32
5
18%
车钩三态作用不良故障
39
56
17
43%
钩提链松余量不足
18
20
2
11%
钩提杆裂纹及变形
9
10
1
11%
车钩钩腔防跳台磨耗超限
10
11
1
10%
钩腕外胀
3
4
1
33%
钩舌外胀
4
5
1
25%
钩舌销变形
6
8
2
33%
三、设定目标
(一)设定目标
1、综合上述现状因素调查分析后,小组结合生产实际,设定QC活动目标值,即车钩三态作用不良故障漏检率在2014年活动前的38﹪基础上,到2014年底活动后实现车钩三态作用不良故障漏检率控制在4%,达到车间要求车钩岗位漏检故障卡控目标的97%。
(二)目标可行性分析
四、原因分析
根据漏检故障信息反馈,车钩作业岗位质量稳定不均衡,容易受外在因素干扰,我们小组人员共同研究,分别从人、机、料、法四个方面,并使用鱼刺图分析,总结导致车钩三态作用不良漏检故障的原因:
人员素质不均衡
车钩三态作用原理认识不深
新更换配件的质量复测
样板使用不规范
合格使用
五、确定要因
(一)小组制定了要因确认计划表:
序号
末端因素
确认内容
确认方法
指标
确认人及完成时间
1
车钩三态作用原理认识不深
对作业人员进行理论考试
测评分析
得分90分以下为不极格
李锐
5.8
2
现车自检实践经验不足
通过首席技术工人现车讲解演练方式进行培训
现场确认
不大于60%
张涛
5.13
3
人员业务素养不均衡
关键技术岗位进行定职
现场确认
不大于15%
熊成华
5.22
4
故障判断不准确
作业人员是否全面掌握故障车钩的多种检查方法
实做考评
不大于10%
李锐
6.5
5
车钩三态实验次数不规范
明确规定作业人员对现车车钩三态实验次数为3次
当日质量抽检抽验对规
漏检故障
率不大于10%
李锐
6.10
6
干性润滑油脂的正确涂抹
明确规定具体钩腔配件的润滑部位及润滑效果
班组预检员质量互控
漏检故障
率超标
余丽仙
6.18
7
车钩检测样板使用不规范
对车钩量具样板进行业务培训
测评分析
得分80分以下为不极格
唐明星
6.20
8
新更换配件的质量复测
对所更换钩腔配件进行信息备案
HMIS检修系统的准确录入
每周抽检抽查不少于3次
熊成华
6.24
5
学习培训不全面
是否掌握车钩岗位作业指导书技术标准
检查培训记录
达标率低于90%为不合格
余丽仙
6.27
6
班组管理不完善
班组是否及时制定相应措施
人员调查
是否制定相应措施,
余丽仙
7.2
1.要因确认一:
车钩三态作用原理认识不深
QC小组组织班组车岗位作业人员对13型、13A型、13B型、17型货车钩腔配件结构作用原理进行分析,讲解各部技术尺寸限度要求,通过理论考试,测试成绩统计如下表:
序号
姓名
成绩
是否达标
1
李锐
92
合格
2
熊成华
84
不达标
3
唐明星
88
不达标
4
周三强
86
不达标
5
章勇
90
合格
6
刘智辉
87
不达标
备注
90分以下为不极格,90分-95分为合格,95分以上为优秀
通过对车钩三态作用原理日常业务素养摸底考试反映出基础理论薄弱,不同型号车钩检修尺寸限度混淆。
结论:
车钩三态作用原理认识不深——要因。
2.要因确认二:
现车自检实践经验不足
QC小组2013年5月13日组织班组首席技术工人利用现车不同型号车钩,针对常见故障的问题缘由进行分析,并让新职人员亲自动手,进行现场现车一对一培训。
经过车间技术人员的现车模拟故障考试,车钩质量漏检故障依然严重。
序号
姓名
漏检故障点
是否达标
1
李锐
5
合格
2
熊成华
3
不达标
3
唐明星
4
合格
4
周三强
3
不达标
5
章勇
2
不达标
6
刘智辉
4
合格
备注
设置虚拟故障5个,发现4个为合格,遗漏3个为失格
经过车间技术人员现场对不同型号车钩设置常见故障进行实做模拟考评,其结果合格人数与失格人数各占一半,说明日常工作者在对现车车钩故障检查方面,实践经验不足。
结论:
现车自检实践经验不足——要因。
3.要因确认三:
人员业务素养不均衡。
QC小组2013年5月22日对班组全员职工进行岗位摸底技能鉴定考评,采取基础理论考试及专业素质展示形式,选定出部分关键质量控制岗位职工,进行系统车钩理论培训学习,并要求对所学内容进行学习记录。
通过对现场培训人员进行随机抽问,发现部分学习人员在对基础理论掌握方面存在不足。
对图示内容理解认识不深刻。
结论:
人员业务素养不均衡——要因
4.要因确认四:
故障判断方法不准确
QC小组2013年6月5日组织班组车钩岗位作业人员,分别对13型、13A、13B(上下作用)型车钩及17型(下作用)车钩进行虚拟故障查找,结合现车运用状态模拟限时检查,超时失格人员统计如下表:
车钩型号
13A、13B
上作用车钩
13A、13B
下作用车钩
17型
下作用车钩
序号
姓名
故障
件数
时间
故障
件数
时间
故障
件数
时间
1
李锐
5
3分
4
3分15秒
4
3分05秒
2
熊成华
3
4分05秒
4
3分
3
3分17秒
3
唐明星
4
3分
3
3分17秒
3
3分15秒
4
周三强
3
3分20秒
4
3分15秒
4
3分20秒
5
章勇
4
3分15秒
3
3分20秒
2
3分10秒
6
刘智辉
3
3分50秒
4
3分
4
3分15秒
成绩
均未达标
备注
不同型号车钩虚拟故障件数为5件,漏检2件为失效,用时3分钟为合格。
超时部分为漏检故障件数。
通过现场模拟考试对不同型号车钩虚拟故障控时检修作业实施考评,其结果说明工作者在对故障判断方法上经验不足。
结论:
故障判断方法不准确——要因。
5.要因确认五:
车钩三态实验次数不规范
QC小组2013年6月10日对班组车钩岗位现场作业人员的三态实验次数进行对规对标,发现部分职工在对车钩三态实验作业环节上,存在实验次数不均衡,有实验多次进行故障查找,有的工作者仅仅实验一次就进行完工确认签字。
实际抽检抽验发现,经过三次及以上对车钩三态进行完整实验的作业者,其车钩漏检故障率低,产品质量稳定,实验次数少于三次的作业者,其车钩检修质量合格率很不稳定。
检修日期
2013年6月10日
进行三次车钩三态实验作业
未进行三次车钩三态实验作业
检修任务数
工作者
漏检故障数
故障率
工作者
漏检故障数
故障率
12头
李锐
0件
唐明星
3件
25%
12头
章勇
1件
8%
熊成华
5件
40%
12头
刘智辉
0件
周三强
4件
33%
通过上述图表指标可以充分反映出,三态实验次数的重要性,重复三态作用实验次数能够有效降低车钩三态作用不良的故障率。
结论:
车钩三态实验次数不规范——要因
6.非要因确认六:
干性润滑油脂的正确涂抹。
QC小组2013年6月18日通过对班组预检员所互控车钩完工质量调查,发现车钩检修人员在对钩腔配件润滑涂抹部位不统一,存在质量隐患,诱发部分车钩因三态作用润滑效果不良,开闭锁作用存在质量问题。
对此QC小组进步细化完善岗位作用指导书内容,规定钩腔推铁转轴部位、锁铁导向面部位及上锁销组成转轴部位必须均匀涂抹干性二硫化钼润滑脂,保障车钩三态作用灵活。
结论:
干性润滑油脂的涂抹部位不规范——非要因
7.非要因确认七:
车钩检测样板使用不规范。
QC小组2013年6月20日对班组车钩岗位部分职工进行车钩样板使用对规,发现作业者在使用车钩量具样板过程中,仅会使用常用样板,而对实际测量非常用样板的数据测量使用却模糊不清,磨耗限度尺寸记忆混淆。
结论:
车钩样板尺寸掌握不全—非要因
8.非要因确认八:
新更换配件的质量复测——非要因
2013年6月24日,车间在对货车检修记录单进行核对时发现,该记录单内所填写更换配件信息与HMIS系统记录信息不一致,同时对所检修车钩进行分解对规检查时,发现所更换配件并未涂打“合”字标记,存在质量隐患。
就此班组结合QC小组质量管理控制措施,制定每周抽检互控作业办法,确保车钩三态作用质量稳定。
结论:
新更换配件的质量复检复测不到位——非要因
9.非要因确认九:
学习培训不全面
检查培训记录,作业指导书考试记录,季度星级评价考试试题库,发现所学内容与实际现场作业规程相脱节。
结论:
学习培训不全面——非要因
10.非要因确认十:
班组管理不完善
检查班组制定相应卡控措施,不明确、具体,可操作性不强。
结论:
班组管理不完善——非要因
(二)通过要因确认,造成“车钩三态作用不良故障”的主要原因是:
1.车钩三态作用原理认识不深
2.现车检查实践经验不足
3.人员业务素养不均衡
4.故障判断方法不准确
5.车钩三态实验次数不规范
六、制定对策
小组成员根据分析的要因,制订对策表如下:
序号
要因
对策
目标
措施
地点
时间
实施人
1
车钩三态作用原理认识不深
制作车钩“三态”试验方法教学课件。
让车钩岗位作业者通过视频方式,直观认识车钩三态试验的基本步骤及方法。
每季度岗位练兵实做培训,特殊案例故障查找教学课件。
站修检修库
2014年全年
李锐
2
现车自检实践经验不足
通过在现场作业过程中,发现特殊故障问题车钩进行现场小结分析,归档整理丰富故障车钩检修信息库内容。
由技师归纳整理,丰富完善特殊车钩故障的检查方法及检修技术。
在班组每周质量小结会议上,收集整理车钩岗位作业者所遇特殊故障问题车钩的检查与施修意见,并进行相关归档整理收存。
站修检修库
2014年全年
李锐
3
人员业务素养不均衡
加强对新入职人员的业务素养培训,特别是在理论素养方面的积累。
新入职职工必须掌握两种岗位及以上作业技能。
每季度进行岗位合格考试,同时必须掌握两项岗位技能。
学习室
2014年全年
班组全员
4
故障判断方法不准确
收集整理不同型号车钩常见故障信息库。
车钩作业人员熟练掌握故障检查判断方法。
根据车钩岗位作业指导书,归纳整理图示化检修手册。
学习室
2014年全年
李锐
5
车钩三态实验次数不规范
规定车钩三态实验次数及实验方法步骤。
增加车钩三态实验次数,把隐蔽性强的车钩故障充分暴露,展现出来。
通过增加车钩三态实验次数,模拟不同运用状态下可能引发车钩故障的非常规“车钩三态”实验。
站修检修库
2014年全年
李锐
七、对策实施
(一)实施一
1.针对车钩检修岗位作业人员在对车钩三态作用原理认识不深的问题,QC小组制作了“车钩三态试验方法”的教学培训课件,同时利用视频记录方式,分步骤、分环节、分检修方法等形式,直观展现培训人员。
对于业务技能较差的人员指定车间首席工人、技师等采取一帮一的措施进行业务补强。
1)指定业务技能较好的首席工人、技师等采取一帮一
的措施。
2)利用多媒体教学方式,播放车钩三态试验故障案例分析教学视频。
2.与此同时QC小组每季度利用岗位练兵时间进行实做培训,并相应开展一次小范围技术比武。
实施结论:
通过落实培训措施,结合多种形式强化培训,班组95%以上职工基本能够熟练掌握车钩三态作用原理。
(二)实施二:
为改善车钩岗位不同作业人员对现车自检实践经验不足的问题,班组在每周质量小结分析会议上,收集整理本周车钩岗位作业者所遇特殊代表性故障问题和具体有效的施修意见,并进行相关资料记录及归档整理收存。
进步补充完善车钩岗位作业指导书工作者在自检方面实践经验的空白。
1)指定业务技能较全面的班组技术员在现场进行质量互控,当工作者遇到或发现具有代表性特殊故障,及时通知班组技术员第一时间介入进行现场确认,如果一旦认定可以列为班组及车间典型故障案例,班组将给予工作者进行车间请奖。
2)由班组技术员每周组织开展质量分析小结会,通报本周质量漏检故障原因分析及整改措施,进步完善本岗位自检自查薄弱环节,巩固强化现场实践作业经验。
3)QC小组利用每月活动跟踪记录表对现场车钩岗位实践作业反馈的典型故障进行分类统计,完善工作者在对现车自检实践经验不足问题的质量卡控。
实施结论:
通过对现场工作者具体自检作业环节落实,结合不同作业人员所遇典型故障案例分析,归纳小结自检车钩作业过程中的实践经验,班组车钩岗位作业者业务技能得到有效提高,产品检修质量也得到有效控制。
(三)实施三:
根据近年来班组人员结构调整成老龄化趋势,能够适应车钩作业岗位人员素质或多或少都受到一定客观因素影响,有身体素质因素无法适应该岗位,有业务技能无法胜任该岗位,也有受安全生产责任意识不高因素限制无法适应次岗位。
最终导致车钩检修岗位作业人员业务素养不均衡。
1)QC小组通过组织班组内部岗位练兵的方式,进行全员职工岗位摸底,从中筛选出业务素养基础良好,能够胜任车钩检修岗位作业人员,并安排班组技术员定期阶段性业务培训,稳固提升车钩检修岗位工作者理论素养和业务技能。
2)班组同时考虑到车钩检修岗位作业者的临时替班人员培养,特意针对性的对班组副工长进行专项业务培训,满足临时替班生产需要。
3)QC小组根据车钩作业岗位的特殊性,设定岗位互控记录表,达到产品质量故障追溯有据可查,明确细化作业工序环节的风险控制项点。
车钩岗位互控记录表
岗位
自控
互控
互控人员
他控
车钩缓冲
1、工卡量具检测与维护保养
车钩作业人员之间
车钩检查
预检员与工长
2、车钩钩腔配件“三检一验”标记复查
车钩作业人员与预检员
预检员
3、车钩“三态试验”作业标准
车钩作业人员与技术员
技术员
4、钩提链松余量、钩提杆横动量、钩锁座入量(搭载量)及车钩高度各部尺寸限度技术要求
车钩作业人员与副工长
副工长
5、货车检修记录单填记及HMIS电脑系统信息录入登记
车钩作业人员与副工长
副工长
实施结论:
QC小组通过对班组现有人员结构状况,进行岗位间优化配置,克服作业者老龄化客观条件限制,达到满足现有生产实际需要的质量要求。
(四)实施四:
针对车钩岗位作业人员,在对车钩故障判断方法不准问题方面,归纳收集整理近年内,车钩三态质量故障的检修信息库、故障种类及故障比例。
2013年造成车钩三态作用不良故障统计表
序号
故障名称
件数
故障率
1
锁铁磨耗超限
108
25%
2
推铁变形
84
19%
3
上锁销组成变形卡滞
36
8%
4
钩腔防跳台磨耗超限
24
6%
5
钩提链松余量不足
72
17%
6
钩耳套脱出
48
11%
7
钩耳垫圈变形
60
14%
8
钩舌销变形
36
8%
从车钩三态作用不良故障统计比例图分析,可以看出钩腔配件磨耗变形故障是导致“三态”作用不良主要因素。
1.车钩三态作用不良故障产生原因分析
1)因车钩使用年限长,钩腔内部磨耗严重、钩体上、下防跳台磨耗、钩腕外胀等因素造成钩体与钩腔内部(钩舌、钩舌销、锁铁、推铁、上锁销组成等)配件配合不良而导致车钩三态作用不良。
2)钩锁接触面及钩舌尾部磨耗后堆焊过多,使钩锁不能落下;防跳部分磨耗或钩锁销反装因而失去防跳作用;上、下锁销杆防跳部位磨耗过限和上、下锁销二次防跳部位磨耗过限,都会导致闭锁不良。
3)上锁销杆挂钩口磨耗过限,在列车运行时,必然造成上锁销杆窜动加大,从而使上锁销杆防跳部位及钩腔防跳台磨耗加剧。
若在规定周期内失效,会进而造成上锁销二次防跳部位快速磨耗。
若二次防跳再失效,则列车运行中随时都有可能发生车钩分离事故。
4)钩舌尾部制造尺寸过大,闭锁时与钩体发生阻抗,使钩舌不能到达闭锁位,导致钩锁无法落下,从而造成闭锁不良。
5)13号下作用式车钩二次防跳性能不良,下锁销组成不能落实正位。
由于车钩在运行中因车辆振动发生钩锁上浮或车钩零部件磨耗、尺寸配合不当造成车钩二次防跳性能不良而引起闭锁不良。
6)另外,提钩链松余量过小、提钩杆弯曲、提钩杆与座的间隙过大不能阻止提钩杆转动、16型车钩开钩框弹簧折断等等,都会造成闭锁不良故障发生。
2.归类车钩三态作用不良故障类型
1)车钩三态作用不良可分为:
开锁不良、闭锁不良、全开不良等故障类型。
2)闭锁不良故障在现车运用状态下很难判断,而对开锁不良及全开不良故障判断则比较直观。
3.车钩“三态试验”故障判断方法
1)开锁试验:
在闭锁位时,右手压住钩舌,左手转动钩提杆的手把,使钩锁坐锁面抬高到钩舌尾部以上。
在此过程中钩舌不应转动,钩舌仍处在闭锁位置;当回转钩提杆并落下钩锁时,钩锁应坐在钩舌推铁的锁座面上;此时用手扳动钩舌鼻部,钩舌应能转动到全开位置,钩舌张开最大量时,须符合:
13A、13B型车钩全开位不大于242mm;13号车钩全开位:
装用13号钩舌时不大于245mm,装用13A型、13B型钩舌时不大于242mm。
开锁不良故障现象现象及施修方法:
①钩锁铁卡在钩舌座锁面上,导致钩锁导向面不正位,无法自然开锁,可更换合格钩锁铁。
②钩舌下牵引凸缘卡在下锁销孔下部,导致钩舌不能正常转动,可加调整垫圈或打磨钩舌下牵引凸缘。
③上钩耳套脱出,卡在钩舌与上钩耳之间,导致钩舌不能正常转动,须氧气配合割除旧钩耳套,重新镶套。
④钩舌推铁弯曲变形,导致钩舌不能正常转动,须更换钩舌推铁。
⑤钩舌园销弯曲变形,导致钩舌不能正常转动,须更换钩舌园销。
2)全开试验:
在闭锁位时,用手提起钩提杆,钩舌自然旋转展开达到全开最大位,同时用另一只手推动钩舌,钩舌无移动仍在全开位。
此时低头对推铁弯角前端,是否卡入钩舌尾部与推铁挡之间进行确认(特别是在全开尺寸偏大情况下),容易造成次故障发生。
全开不良故障现象及施修方法:
①钩舌推铁弯曲变形、钩舌销孔与钩耳孔中心偏差过大会造成全开位不良,可更换合格推铁及钩舌销。
②钩舌销孔上下面距离过大或钩舌尾部尺寸过大,组装后与钩体配合过紧,也会造成全开位不良,可通过更换合格原型钩舌进行解决。
③