热轧钢管生产工艺流程.docx
《热轧钢管生产工艺流程.docx》由会员分享,可在线阅读,更多相关《热轧钢管生产工艺流程.docx(30页珍藏版)》请在冰豆网上搜索。
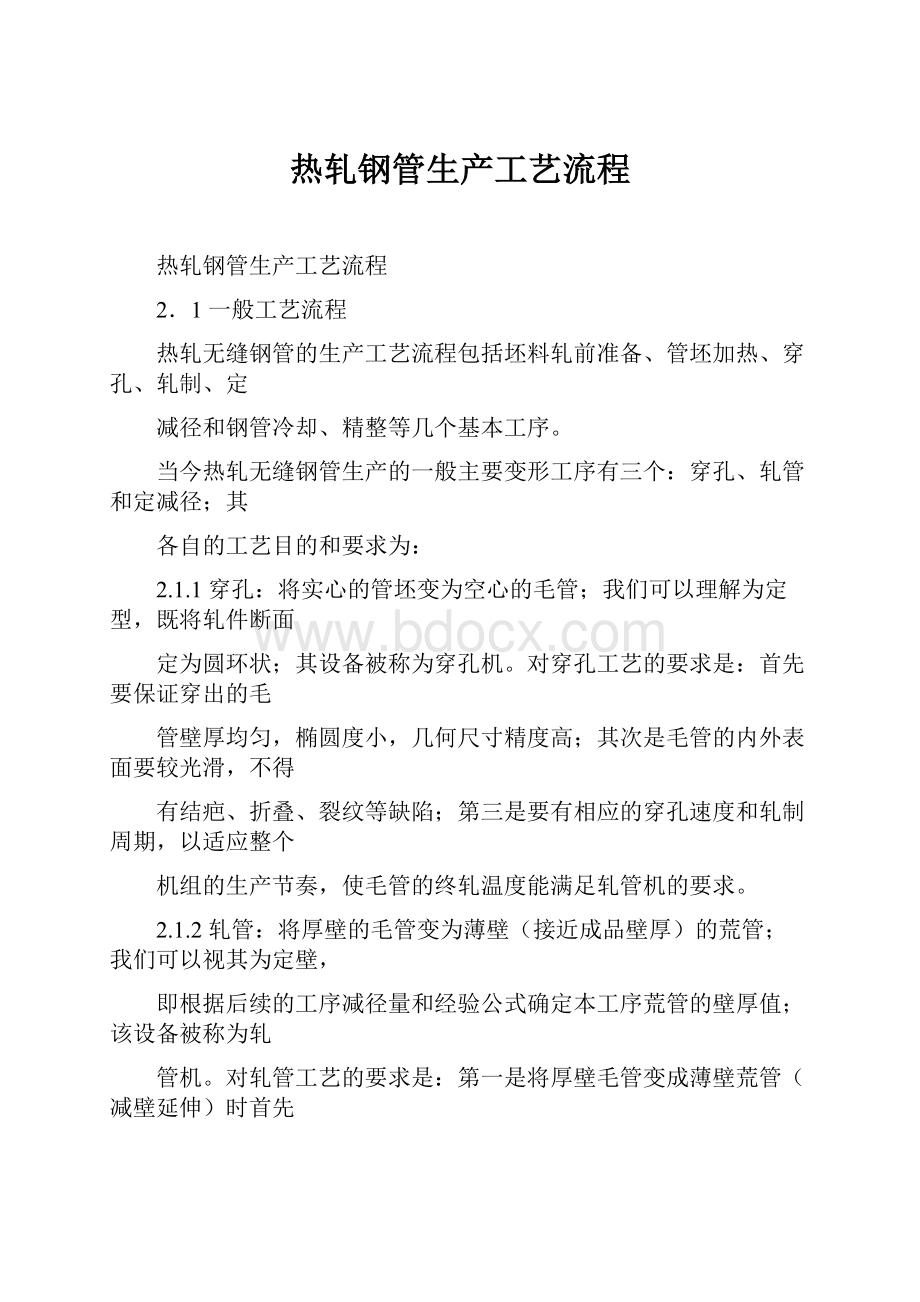
热轧钢管生产工艺流程
热轧钢管生产工艺流程
2.1 一般工艺流程
热轧无缝钢管的生产工艺流程包括坯料轧前准备、管坯加热、穿孔、轧制、定
减径和钢管冷却、精整等几个基本工序。
当今热轧无缝钢管生产的一般主要变形工序有三个:
穿孔、轧管和定减径;其
各自的工艺目的和要求为:
2.1.1 穿孔:
将实心的管坯变为空心的毛管;我们可以理解为定型,既将轧件断面
定为圆环状;其设备被称为穿孔机。
对穿孔工艺的要求是:
首先要保证穿出的毛
管壁厚均匀,椭圆度小,几何尺寸精度高;其次是毛管的内外表面要较光滑,不得
有结疤、折叠、裂纹等缺陷;第三是要有相应的穿孔速度和轧制周期,以适应整个
机组的生产节奏,使毛管的终轧温度能满足轧管机的要求。
2.1.2 轧管:
将厚壁的毛管变为薄壁(接近成品壁厚)的荒管;我们可以视其为定壁,
即根据后续的工序减径量和经验公式确定本工序荒管的壁厚值;该设备被称为轧
管机。
对轧管工艺的要求是:
第一是将厚壁毛管变成薄壁荒管(减壁延伸)时首先
要保证荒管具有较高的壁厚均匀度;其次荒管具有良好的内外表面质量。
2.1.3 定减径(包括张减):
大圆变小圆,简称定径;相应的设备为定(减)径机,其主
要作用是消除前道工序轧制过程中造成的荒管外径不一(同一支或同一批),以
提高热轧成品管的外径精度和真圆度。
对定减径工艺的要求是:
首先在一定的总
减径率和较小的单机架减径率条件下来达到定径目的,第二可实现使用一种规
格管坯生产多种规格成品管的任务,第三还可进一步改善钢管的外表面质量。
20 世纪 80 年代末,曾出现过试图取消轧管工序,仅使用穿孔加定减的方法
生产无缝钢管,简称 CPS,即斜轧穿孔和张减的英文缩写),并在南非的 Tosa 厂进行
了工业试验,用来生产外径:
33.4~179.8mm,壁厚 3.4~25mm 的钢管,其中定
径最小外径为 101.6mm;张减最大外径我 101.6mm。
经过实践检验,该工艺在产
生壁厚大于 10mm 的钢管时质量尚可,但在生产壁厚小于 8mm 的钢管时通过定
径、张减不能完全消除穿孔毛管的螺旋线,影响了钢管的外观质量。
在随后的改
造中不得不在穿孔机于定减径机之间增设了一台 MINI-MPM(4 机架)来确保产
品质量。
2.2 各热轧机组生产工艺过程特点
我们通常将毛管的壁厚加工称之为轧管。
轧管是钢管成型过程中最重要的
一个工序环节。
这个环节的主要任务是按照成品钢管的要求将厚壁的毛管减薄
至与成品钢管相适应的程度,即它必须考虑到后继定、减径工序时壁厚的变化,
这个环节还要提高毛管的内外表面质量和壁厚的均匀度。
通过轧管减壁延伸工
序后的管子一般称为荒管。
轧管减壁方法的基本特点是在毛管内按上刚性芯棒,
由外部工具(轧辊或模孔)对毛管壁厚进行压缩减壁。
依据变形原理和设备特点
的不同,它有许多种生产方法,如表 1 所示。
一般习惯根据轧管机的形式来命名
热轧机组。
轧管机分单机架和多机架,单机架有自动轧管机、阿塞尔轧机、
ACCU-ROLL 等,斜轧管机都是单机架的;连轧管机都是多机架的,通常 4~8 个机
架,如 MPM、PQF 等。
目前主要使用连轧(属于纵轧)与斜轧两种轧管工艺。
1
变形
原理
设备、工具特点
加工工艺方式
延伸系
数
外工具、设备
芯棒
纵
轧
法
单机架
短(固定)
自动轧管机(plug mill)
1.5~2.1
多机架连轧
长(浮动)
MM
3~4.5
中长(半浮、限动)
Neuval-R,MRK-
S、MPM、MINI-
MPM、PQF
3~6.5
斜
轧
法
二
辊
导 板
短(固定、限动)
二次穿孔、延伸机
<2.5
导 盘
长(浮动)
狄舍尔延伸机
(Diescher)
2~5.0
中长(限动)
ACCU-ROLL
2~5.0
三 辊
中、长(浮动、限动、
回退)
三辊轧管机
(Assel,Transval)
1.3~3.5
多 辊
中长(固定)
行星轧管机(PSW)
5~14
锻轧法
周期断面辊
中长(往复)
周期式轧管机(Pilger)
8~15
顶管法
一列模孔
长(与出口管端同步)
顶管机
4~16.5
挤压法
单模孔
中长(固定)
挤压机
1.2~30
表 1 轧管减壁的工艺方法
2..2.1 连续轧管机的几种形式:
连轧管机是在毛管内穿入长芯棒后,经过多机架
顺序布置且相临机架辊缝互错(二辊式辊缝互错 90°,如图 1 所示;三辊式辊缝互
错 60°)的连轧机轧成钢管,它是当今被最广泛应用的纵轧钢管方法。
连轧管机轧
制过程中,轧件变形实际上是受多组(4~8 组)轧辊与芯棒的反复作用从圆到椭
圆…椭圆再到圆的过程。
连轧管机的发展历史悠久,早在 19 世纪末就曾尝试在长芯棒上进行轧管,
但种种原因,至 1950 年世界上仅有 6 台连轧管机。
1960 年后,随着科学技术的
进步和生产的发展,特别是电子计算机技术的飞速发展和应用,使连轧管机在生
产工艺和设备上日趋完善,得到了迅速的发展和推广。
在浮动芯棒连轧管机的基
础上,限动芯棒连轧管机于 20 世纪 60 年代中期进行了工艺试验,获得了可喜的
成果。
1978 年世界上第一套限动芯棒连轧管机(MPM)在意大利达尔明钢管厂建
成投产,连轧管工艺发展到了一个新的水准。
20 世纪 90 年代末又推出了三辊连
轧管机(PQF)技术,使连轧管工艺装备跃上了更高的台阶。
连轧管机在 PQF 出现以前,都是两辊式的,即由两个轧辊为一组组成孔型,
二辊式的机架既有与地面呈 45°交错布置的,也有与地面垂直、水平交错布置的;
PQF 为三辊式的,即由三个轧辊为一组组成孔型;;MPM 与 PQF 孔型构成见(图
2);连轧管时,孔型顶部的金属由于受到轧辊外压力和芯棒内压力作用而产生轴
向延伸,并向圆周横向宽展,而孔型侧壁部分的金属与芯棒不接触,但它被顶部
轴向延伸的金属对它附加的拉应力作用而产生轴向延伸,并同时产生轴向拉缩。
不论两辊式的还是三辊式的连轧管机,按芯棒的运行方式可分为以下三种形式。
2
2.2.1.1 浮动芯棒连轧管机(或全浮动芯棒连轧管机):
简称 MM(Mandrel Mill),一
般设有 8 个机架。
轧制过程中对芯棒速度不加以控制,芯棒由被辗轧金属的摩擦
力带动自由跟随管子通过轧机,芯棒的运行速度是不受控的;轧制过程中芯棒的
运行速度随着各机架的咬入、抛钢有波动,从而引起管子壁厚的波动;轧制结束
后,芯棒随荒管轧出至连轧机后的输出辊道,在轧制中、薄壁管时芯棒的几乎全
长都在荒管内,见图 3;带有芯棒的荒管横移至脱棒线,由脱棒机将芯棒从荒管中
抽出以便冷却、润滑后循环使用。
其特点是轧制节奏快,每分钟可轧 4 支甚至更
多的钢管; 但荒管的壁厚精度稍低、设有脱棒机其工艺流程较长、芯棒的长度接
近于管子的长度;适合生产较小规格(外径小于 177.8mm)的无缝钢管。
比较有代
表性的浮动芯棒连轧管机有德国米尔海姆厂的 RK2 机组和我国宝钢的 φ140 mm
机组。
浮动芯棒连轧管机的工作特点是:
由于在轧制时不控制芯棒速度,因此在整
个轧制过程中,芯棒速度多次变化。
例如,在一台 8 机架的连轧管机上,当金属
进入第一机架时,芯棒在摩擦力的作用下,以接近第一机架的轧制速度运行;当
金属进入第二机架时,芯棒速度就要改变,以第一和第二机架轧制速度之间的某
个速度运行;当进入第三机架时,则芯棒速度已变为第一、第二和第三机架轧制
速度之间的某个速度;依此类推,直至进入第八机架,芯棒速度便经过了 8 次变
化,已 1~8 机架间的某个速度运行,进入一个相对稳定的轧制阶段。
在此阶段,
前面机架的轧制速度比芯棒速度慢(称为慢速机架),后面机架的轧制速度比芯
棒速度快(称为快速机架),如果中间某个机架的轧制速度恰好与芯棒运行速度
相同则称为同步机架。
随后当金属逐渐从有关机架中轧出时,在芯棒速度变化为
2~8 机架间的某个速度;当金属由第二机架轧出,则芯棒速度又变为第三至第八
机架间的某个速度,以此类推,直至金属从第八机架轧出为止。
由上可以看出,在钢管的轧制过程中,芯棒的速度至少要变化 15 次,芯棒
速度的变化将导致金属流动条件的改变。
浮动芯棒连轧管机由于轧制过程中芯
棒速度改变而使得金属流动发生变化,因金属流动的不规律而引起钢管纵向的
壁厚和直径变化,尽管对此采取了不少措施并取得了一定的效果,当轧制条件的
变化依然存在,且产品管的尺寸精度始终不如限动芯棒轧机。
此外,芯棒长,使
制造费用加大,制造困难,且长芯棒的重量也很大,钢管带着过重的芯棒在辊道
上运行将会导致钢管表面损伤。
故目前浮动芯棒连轧管机均用于小型机组。
连轧管时,荒管可以看作是在不同直径的轧辊间连续轧制形成的。
穿在钢管
中的芯棒可以看作是曲率半径无穷大的内轧辊。
浮动芯棒轧制时,芯棒除受到轧
辊经轧件传递来的作用力外,再无其他外力作用。
当轧件头部经第一机架咬入后,
随着轧件逐一走向后面的延伸机架,作用在芯棒上的机架数相继增多,故芯棒速
3
度不断提高,这个阶段称为“咬入”阶段。
当轧件头部进入最末机架后,整个轧件
处在连轧管机所有机架的轧制中,芯棒速度维持不变,称为“稳定扎着急”阶段。
当轧件尾部离开第一机架后,芯棒速度友逐级提高,直到轧出延伸,称为“轧出”
阶段。
轧辊工作圆周速度是安“稳定轧制”状态下设定的。
轧制过程中轧件又是遵
循着体积不变定律的。
然而由芯棒引起的轧件速度的升高,使流入后面机架的金
属必然增多,也就是说,后面的机架由芯棒送入了比其设定的轧辊圆周速度所允
许的还要多的金属,这就出现了使断面积增大的金属积累。
这种逐步流入的附加
金属造成的较大断面,尽管在最后的机架上得到了加工,但仍然导致在荒管的一
些部位上直径变大和壁厚变厚,这种现象称为“竹节”。
原则上讲可能在整根钢管
上均出现“竹节”。
显然“竹节”现象属纵向壁厚不均,对随后的张减机轧制是不利
的,应尽可能防止。
为了防止或减少“竹节”形成,孔型设计分配压下量时,在保证总延伸不变的
前提下,适当增加前几架压下量。
这样,就可在后面几个机架中使芯棒速度的跃
增得到减弱,从而减轻芯棒速度变化的影响。
良好的芯棒润滑有利于延伸和降低
能耗,也可以减少竹节的形成。
还可以采用电控技术防止竹节的产生。
由电子计
算机进行预设定,轧辊转速按要求变化,当轧件通过时对轧辊进行校准,使各机
架的出口速度与芯棒速度的变化相适应。
70 年代盛行浮动芯棒连轧管机机组。
由于受到芯棒重量的限制,至今这种
机组仅能生产直径小于 177.8mm 一下的钢管。
2.2.1.2 半浮动(或半限动)芯棒连轧管机:
德国人称 MRK-S(Mannesmannbohr-
Kontimill Stripper);法国人称 Neuval-R。
半浮动芯棒连轧管机一般 7~8 个机架。
德国设计的工艺为:
在轧制过程中,前半程,芯棒不是自由地随轧件前进,
而是受限动机构的控制,以一恒定速度前进,芯棒与轧件的速差分布是不一致的,
第 1 架的轧件出口速度小于芯棒速度;自第 2 架开始,轧件的速度快于芯棒的速
度,形成稳定的差速轧制状态;当完成主要变形、管子脱离倒数第 3 架时,限动机
构加速释放芯棒,像浮动芯棒一样由钢管将芯棒带出轧机。
德国式的半浮动芯棒
连轧管机于 20 世纪 80 年代初在日本八幡厂建成投产。
法国研制的工艺为:
在钢管由最后一个机架轧出时才松开芯棒,即在轧制过
程中具有限动芯棒轧机的工艺特点,而在终轧后松开芯棒;芯棒随荒管至连轧机
后的输出辊道。
法国式的半浮动芯棒连轧管机于 20 世纪 70 年代后期在法国的
圣索夫钢管厂投入生产。
不论德国工艺还是法国工艺,半浮动芯棒轧管机轧制结束后,约有 1/3 长的
荒管(尾部)包住芯棒前端,见图 4;带有芯棒的荒管横移至脱棒线,由脱棒机将芯
棒从荒管中抽出以便冷却、润滑后循环使用。
其特点是荒管壁厚的精度较高、节
奏较快,每分钟可轧 3 支甚至更多的钢管,芯棒长度虽然比浮动式的短得多,而
比限动芯棒轧机略长一些;设有脱棒机工艺其流程较长;适合生产较小规格(外径
小于 219mm)的无缝钢管。
德国模式的代表机组有日本的八幡厂的 φ194mm 机
组和我国衡阳的 φ89 mm 机组;法国模式的机组至今仅有一套,就是法国 V&M
公司圣索夫厂的 φ127 mm 机组。
半浮动芯棒连轧管机在扎着过程中对芯棒速度也进行控制,但在轧制结束
之前即将芯棒放开,像浮动芯棒连轧管机一样由钢管将芯棒带出轧机,然后由脱
棒机将芯棒从荒管中抽出。
在对芯棒速度进行限动时,就在一定程度上解决了金
属流动规律性的问题,将芯棒放开以后,又如同浮动芯棒连轧管机一样要考虑脱
棒条件的限制,因此半浮动芯棒连轧管机所轧制的钢管直径不宜太大。
4
半浮动芯棒连轧管机兼顾了限动芯棒与浮动芯棒轧管机的优点,既保持了
较高的轧制节奏,又确保了钢管的壁厚精度及内外表面质量,只是由于需要设置
脱棒机,使其轧制规格的上限受到限制。
2.2.1.3 限动芯棒连轧管机:
简称 MPM(Multi-Stand Pipe Mill),是意大利因西公
司推广应用的,一般 7~8 个机架。
轧管时芯棒的运行是限动的、速度是可控的;
芯棒的速度应高于第一架的咬入速度而低于第一架的轧出速度。
轧制的整个过
程中芯棒速度是恒定不变的,从而确保管子壁厚的精度,轧制不同的管子时芯棒
的速度可在一定范围内调节。
轧制结束后,芯棒停止,由脱管机将荒管从芯棒中
脱出,而后芯棒回送离开轧机,拨出轧线冷却、润滑后循环使用。
其特点是荒管
的壁厚的精度高,用脱管机取代了脱棒机,缩短了工艺流程,芯棒较短;但轧制节
奏慢,每分钟可轧 2 支或稍多一点的钢管;适合生产中等规格(外径小于 460mm)
的无缝钢管。
代表性机组有意大利达尔明的 φ356 mm 机组和我国天津钢管公司
的 φ250 mm 机组。
为了解决浮动芯棒连轧管机轧制过程中金属流动不规律的问题,缩短芯棒
长度,解决芯棒制造上的困难,20 世纪 60 年代国外就开始试验限动芯棒轧制,
70 年代获得成功,在意大利的达尔明厂投入工业生产。
限动芯棒连轧管机的基本特点就是控制芯棒的运行速度,使芯棒在整个扎
着过程中均以低于第一机架金属轧出速度的恒定速度前进,这是相当重要的工
艺改进,使限动芯棒轧机具有浮动芯棒轧机不可比拟的优越性。
近年来的实践表
明,芯棒的速度应高于第一机架的咬入速度而低于第一机架的轧出速度。
这样,
在整个扎着过程中芯棒的移动速度均以低于所有机架的轧制速度,避免了不规
律的金属流动和轧制条件的变化。
由于芯棒速度受到控制,每一机架的轧制压力
都较小,金属流动有规律,延伸系数可达一些,这就可以获得非常好的壁厚偏差。
由于芯棒速度限动,可大大缩短芯棒的长度,轧制 32m 的钢管,芯棒的工作
长度只有 15m。
钢管从芯棒上轧出后用脱管机将其从芯棒前端抽出,芯棒快速返
回,不像在浮动芯棒轧机上受脱棒条件的限制,因此可以生产中型和大型规格的
无缝钢管。
限动芯棒连轧管机是在浮动芯棒连轧管机的基础上发展起来的。
与浮动芯
棒连轧管机相比,限动芯棒连轧管机有如下优点:
1)降低了工具消耗。
由于限动芯棒连轧管机的芯棒较之浮动芯棒连轧管机的芯棒
要短,钢管与芯棒的接触时间短,从而提高了芯棒的使用寿命,一般使芯棒消耗
降至每吨钢管 1 公斤左右。
2)改善了钢管的质量。
由于限动芯棒连轧管机具有搓轧(芯棒与钢管内表面相对
运动)性质,有利于金属的延伸,加之带有微张力轧制状态,从而减小了横向变形,
根本不存在浮动芯棒连轧所产生的“竹节”现象,使钢管内外表面和尺寸精度有了
很大提高。
3)取消了脱棒机,缩短了工艺流程,提高了钢管的终轧温度。
部分品种可省去定
径前的再加热工序,从而节省了能源。
4)扩大了产品规格。
由于采用了限动芯棒轧制,可以减小芯棒的长度,减轻了芯
棒的重量,允许加大芯棒的直径,使钢管的最大外径由 177.8mm 扩大到 426mm
甚至更大.另外,限动芯棒连轧管机还可轧制径壁比更大(D/S>40)的钢管。
限动芯棒连轧管机代表着现代无缝钢管生产的先进技术,它集中体现了无
缝钢管生产的连续性、高效率、机械化及工业自动化的发展趋势。
80 年代以后已
5
经在无缝钢管生产领域占了主导的地位。
少机架限动芯棒连轧管机(MINI-MPM)是在上世纪 90 年代意大利因西公
司推出的工艺,它的实质与 MPM 一样;当时主要是针对南非托沙厂的技术改造,
设计为四个机架,基本保留了 MPM 机组的优点,与 MPM 相比它的最大特点是
实现了用更短的芯棒轧制长钢管,芯棒的工作段长度比 MPM 少 2~3 米;芯棒总
长度可缩短 5 米左右。
芯棒可以制造成整体,两端都加工有限动头可以调头使用,
降低芯棒的消耗。
随着锥形辊穿孔机的普及应用,使热轧无缝钢管的变形量前移
成为可能,连轧工序的延伸可适当减小,连轧管机不用再设置 7~8 架就可实现
所要求的热轧变形了,所以在而后兴建的限动芯棒连轧管机组大多采用 5 个机
架的 MINI-MPM。
代表机组有包头钢铁公司的 180 机组;鞍山钢铁公司的 159 机
组;衡阳钢管厂的 273 机组以及成都钢管厂的 340 机组。
芯棒芯棒
荒管
荒管
连轧机PQF连轧机
图 2 连轧管孔型构成
2.2.1.4 PQF((Premium Quality Finishing)也是限动芯棒连轧管机,只不过每个
机架由三个轧辊组成孔型;采用三辊设计的孔型比传统的两辊设计的孔型圆度好,
且孔型的半径差小,有利于轧件的均匀变形和轧辊的均匀磨损。
轧槽底部和轧槽
顶部之间的圆周速度差较小,从而能在稳定的条件下使轧制时的金属变形更加
均匀。
凸缘面积(不与轧辊或芯棒接触的管子面积。
也就是辊缝处壁厚/外经的凸
起面积)有所减小,即流向凸缘的金属量减少了。
这一优点在轧制不受外端及
其它机架约束的钢管尾端时尤为重要。
事实上钢管尾端在三辊式轧管机上轧制
时受控是由于凸缘面积较小(比二辊式的小 30%左右)以及轧槽底部与轧槽顶部
间的圆周速度差较小的缘故。
因此,能避免或大大减少管端折叠和飞翅的形成。
因圆周压应力较高,从而能在轧制时使辊缝处产生的纵向拉应力的危险性大大
降低。
孔型中芯棒的稳定性较高。
PQF 机组可以生产高强度(P110 以上)特殊钢
级油井用管、高压锅炉管及 13Cr、304L 等不锈钢管。
PQF 最大的优势是:
由于三
辊孔型的半径差小于两辊,轧件变形更加均匀、平稳,使产品的壁厚精度和表面
质量高于 MPM。
φ168mmPQF 机组由于采用了独特的芯棒运行方式,使其轧制
节奏达到 24 秒/支。
代表性机组为我国天津钢管公司的 φ168 mm 机组。
限动芯棒连轧管机芯棒运行有两种方式:
一是轧制结束时,芯棒停止运动,
待荒管从芯棒中脱出后,芯棒快速返回,拨出轧制线,冷却、润滑后循环使用,传
统的 MPM 均采用此中运行方式;另一种运行方式为:
轧制结束时,芯棒停止运动,
6
待荒管由脱管机从芯棒中脱出后,芯棒不是回送,而是向前快速运行跟随荒管之
后依次通过脱管机,芯棒穿过脱管机后,拨出轧线再回送、冷却、润滑循环使用,
该方法减少了芯棒的在线待轧(非轧钢)时间。
从而有效地缩短了轧制周期,加快
了轧制节奏。
PQF 采用此中运行方式;两种运行方式的主要区别是脱管完成后,
芯棒是与荒管反向运行回退离开轧机后拨出轧制线冷却、润滑、循环使用;还是
同向运行芯棒前行离开轧机后、穿过脱管机后拨出轧制线冷却、润滑、循环使用。
第二种方法因芯棒要通过脱管机,在轧制薄壁管(脱管机的减径量大于等于 2 倍
的荒管壁厚)时要求脱管机轧辊必须具备快开快合功能,以免芯棒撞损脱管机轧
辊。
1
2
1-芯棒;2-荒管
图 3浮动芯棒轧制后芯棒/荒管示意图
1
1-芯棒;2-荒管
2
图 4半浮动芯棒轧制后芯棒/荒管示意图
2.2.1.5 关于脱管机和脱棒机
为了完成将连轧管机轧出的荒管与芯棒脱开分离的工艺目的,便于荒管在后
道工序进一步加工成品钢管,一般采用两种方法:
2.2.1.5.1 一是轧制结束后荒管/芯棒被一起移出轧制线,荒管受轴向约束不动,用
装置将芯棒从荒管中抽出;我们将这种荒管不动,芯棒动的设备称为脱棒机。
当带
芯棒的荒管进入脱棒位置后,脱棒链上的脱棒卡紧装置就勾住芯棒的尾柄,而液
压开闭的卡板挡住荒管,脱棒链从荒管中抽出芯棒。
脱棒链转过半圈完成一次脱
棒动作,链所走过的距离约为芯棒长度的 1.1 倍.脱棒机的最大速度大于 4.5m/s。
7
到达终位的误差为±50mm。
脱出的芯棒经输送辊道送到芯棒定位升降挡板前,然
后由芯棒移送装置把芯棒送入芯棒冷却槽,循环使用。
脱棒机安装位置与连轧管
机平行。
脱棒机有两列脱棒链。
这两列脱棒链用横梁连接起来。
两列脱棒链间共
有两个脱棒横梁及多个承载横梁。
脱棒横梁用来从荒管中抽出芯棒,而承载横梁
用来在脱棒过程中支承芯棒。
在脱棒横梁上用螺栓紧固与轧件尺寸相关的脱棒
卡紧装置。
当更换轧制芯棒时,需要更换脱棒卡紧装置。
2..2.1.5.2 另一种是轧制结束后,芯棒停止运动,荒管在线被装置将其从芯棒中
脱出;我们将这种芯棒不动,荒管动的设备称为脱管机。
脱管机既有两辊式的,也
有三辊式的。
脱管机的设置有两个重要的工艺目的:
一是将荒管从芯棒上抽出,
完成脱管目的。
在轧制线上脱管,省去了脱棒机,缩短了工艺流程,提高了终轧
温度;二是起校正(定径)作用,也就是说在每一支钢管生产中,该机也有延伸和
定径作用。
为生产薄壁管和中厚壁管,每架脱管机的孔型名义直径必须小于轧管
机芯棒直径。
在生产薄壁管时,脱管机的减径量要相应加大,否则薄壁管不易被
脱出。
每架脱管机上都装有安全臼,以防止芯棒进入脱管机时损伤轧辊及相关的
机械部分。
在事故情况下,假如当带芯棒的荒管进入脱管机孔型时,若脱管机轧
辊承受的径向载荷大于预设值,则轧辊孔型会相应张开,防止芯棒顶坏轧辊及设
备。
2.2.1.6 连轧管机按芯棒运行方式进行分类的方法/原则?
2.6.1 连轧管机限动芯棒与半浮动芯棒工艺主要区别在于以下两点:
一是轧制过
程中芯棒速度是否恒定不变;二是使用脱管机还是脱棒机。
限动芯棒工艺应该同
时满足轧制过程中芯棒速度恒定不变和使用脱管机这两个条件。
因此,将目前建
成投产的这套 PQF 机组称为三辊限动芯棒连轧管机较为恰当,而称之为半浮动
芯棒显然是欠准确的。
2.2.1.6.2 曾有学者提出用半限动替代半浮动这一名称,意在强调对芯棒的限动功
能;但从已发表的许多文章来看,绝大多使用都半浮动这一名称。
还有人认为法
国式的机组因其轧制过程中芯棒速度是受控的,应该属于限动芯棒类型。
由于机
组配备的是脱棒机,轧管机孔型设计是要考虑脱棒间隙,孔型的侧壁开口角度要
比 MPM 的大,故将法国人设计的连轧管机组归为半浮动类型。
2.2.1.6.3 采用脱出荒管之后,芯棒向前行进通过脱管机、绕轧机出口侧进行循环
这一独特的运行方式,与传统的限动芯棒机组相比:
明显地减少了芯棒的运行时
间、加快了限动芯棒连轧管机组的轧制节奏、提高生产效率,实现了人们的对限
动芯棒连轧管机既要钢