汽车内饰蒙皮加工工艺.doc
《汽车内饰蒙皮加工工艺.doc》由会员分享,可在线阅读,更多相关《汽车内饰蒙皮加工工艺.doc(8页珍藏版)》请在冰豆网上搜索。
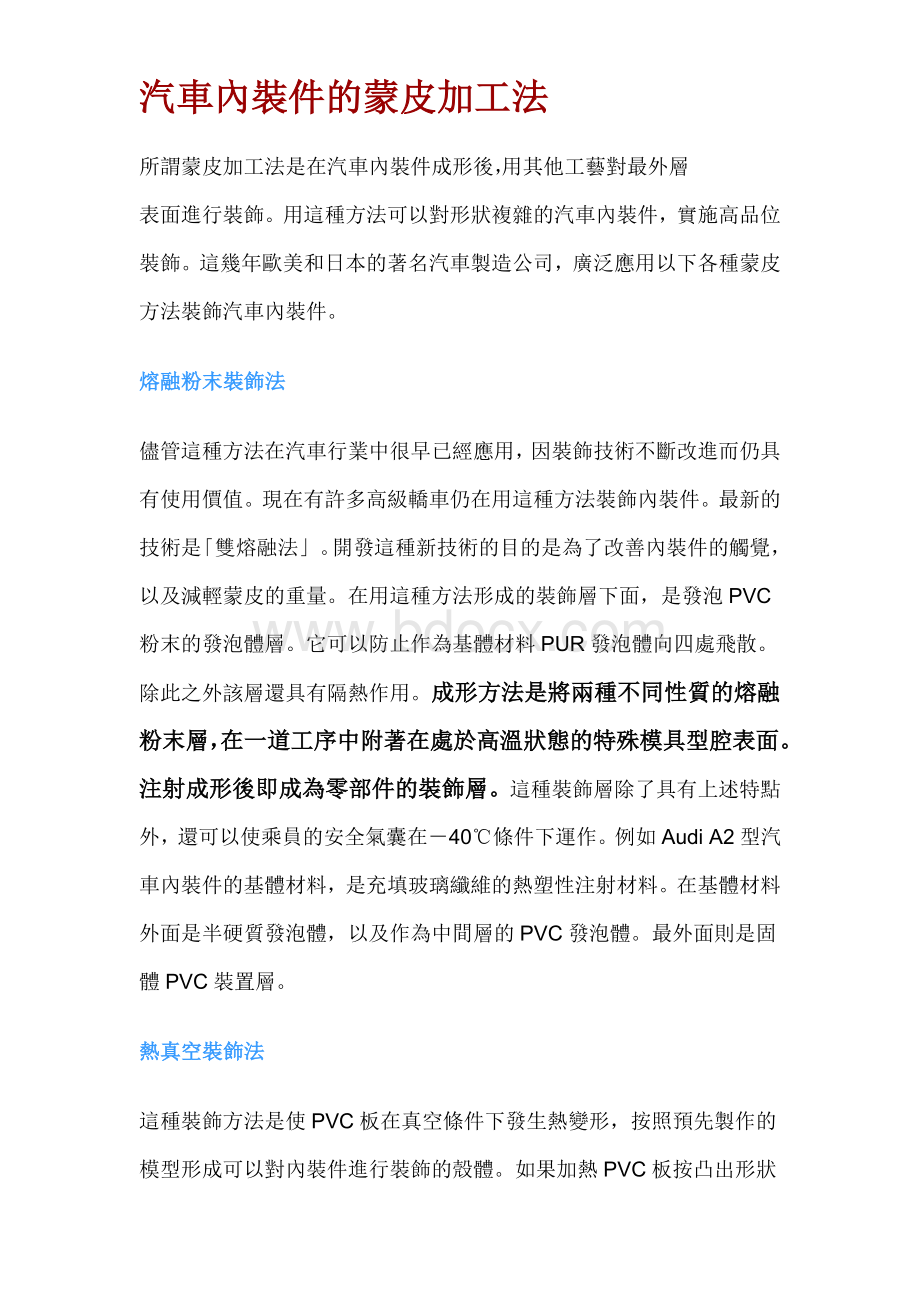
汽車內裝件的蒙皮加工法
所謂蒙皮加工法是在汽車內裝件成形後,用其他工藝對最外層表面進行裝飾。
用這種方法可以對形狀複雜的汽車內裝件,實施高品位裝飾。
這幾年歐美和日本的著名汽車製造公司,廣泛應用以下各種蒙皮方法裝飾汽車內裝件。
熔融粉末裝飾法
儘管這種方法在汽車行業中很早已經應用,因裝飾技術不斷改進而仍具有使用價值。
現在有許多高級轎車仍在用這種方法裝飾內裝件。
最新的技術是「雙熔融法」。
開發這種新技術的目的是為了改善內裝件的觸覺,以及減輕蒙皮的重量。
在用這種方法形成的裝飾層下面,是發泡PVC粉末的發泡體層。
它可以防止作為基體材料PUR發泡體向四處飛散。
除此之外該層還具有隔熱作用。
成形方法是將兩種不同性質的熔融粉末層,在一道工序中附著在處於高溫狀態的特殊模具型腔表面。
注射成形後即成為零部件的裝飾層。
這種裝飾層除了具有上述特點外,還可以使乘員的安全氣囊在-40℃條件下運作。
例如AudiA2型汽車內裝件的基體材料,是充填玻璃纖維的熱塑性注射材料。
在基體材料外面是半硬質發泡體,以及作為中間層的PVC發泡體。
最外面則是固體PVC裝置層。
熱真空裝飾法
這種裝飾方法是使PVC板在真空條件下發生熱變形,按照預先製作的模型形成可以對內裝件進行裝飾的殼體。
如果加熱PVC板按凸出形狀的陽模表面變形,稱為陽模正壓法。
反之加熱PVC板在真空條件下被吸附在凹入形狀的陰模表面,稱為陰模負壓法。
用正壓法裝飾的內裝件,耐擦刮性能較差。
用負壓法裝飾內裝件在-40℃溫度條件下也不會飛散,所以特別適合用於對車內氣囊覆蓋板進行裝飾。
PUR噴塗法
這種方法的特點是,用單層就可以滿足使用要求。
現在賓士和大眾汽車公司的很多內裝件是用這種方法裝飾。
最近又開發了廣受用戶青睞的直接後發泡工藝。
這是在噴塗結束後,由第二機器人控制PUR混合頭與半硬質發泡體相結合,可進一步提高內裝件的質量。
除了上面介紹的裝飾方法以外,還有PUR鑄造蒙皮、PUR反應注射、吹塑成形和雙蒙皮成形等方法,也都廣泛用於裝飾現代汽車的內裝件。
各种仪表板表皮制造工艺的性能对比
由于PVC材料具有良好的手感和花纹成型性且材料成本低等优点,因此目前PVC搪塑仍是使用最广的仪表板表皮加工工艺,PVC粉料占据了搪塑成型工艺的绝大部分市
由于PVC材料具有良好的手感和花纹成型性且材料成本低等优点,因此目前PVC搪塑仍是使用最广的仪表板表皮加工工艺,PVC粉料占据了搪塑成型工艺的绝大部分市场。
由于PVC材料的玻璃化温度较高,材料在低温环境下发脆,易造成无缝气囊仪表板在低温状态爆破时,气囊区域PVC表皮碎裂而飞出,对乘客产生安全隐患,PVC在抗老化性、增塑剂迁移等方面也存在问题,因此出于安全及环保原因,目前各主机、饰件及材料生产厂商相继开发出了PVC的替代材料及工艺。
根据仪表板表皮性能这些发展要求,世界各主机、饰件及材料生产厂商不断开发出新的材料及成型工艺以满足表皮性能的发展要求,以下是对仪表板饰面表皮的各种制造工艺在性能方面的一个对比列表。
仪表板隐式安全气囊撕裂线加工工艺
来源:
中国塑料产业链图1最新发展的开口工具的基本原理和主要优势在汽车仪表板装饰层上预制安全气囊撕裂线,通常采用激光、冷刀或者热刀进行切割,而新工艺则采用C形系统来切割。
该系统在C形框架上装有一把切刀和一个滚球,并集成了高灵敏传感器技术,具有极高的加工精度、重复性、安全性以及成本效率。
过去,汽车制造商把安全气囊设计成一个可见的装置,然而今天的发展趋势是把安全气囊隐藏起来。
因此,在当今的汽车仪表板中,其必备的开口薄片都被覆于装饰性表皮之下,并且在其背面还必须预留撕裂线以确保可
图1 最新发展的开口工具的基本原理和主要优势
在汽车仪表板装饰层上预制安全气囊撕裂线,通常采用激光、冷刀或者热刀进行切割,而新工艺则采用C形系统来切割。
该系统在C形框架上装有一把切刀和一个滚球,并集成了高灵敏传感器技术,具有极高的加工精度、重复性、安全性以及成本效率。
过去,汽车制造商把安全气囊设计成一个可见的装置,然而今天的发展趋势是把安全气囊隐藏起来。
因此,在当今的汽车仪表板中,其必备的开口薄片都被覆于装饰性表皮之下,并且在其背面还必须预留撕裂线以确保可靠的打开。
为引入这一撕裂线,制造商需要解决两个问题:
一方面,要保证表面蒙皮强度足够低,以便于安全气囊的可靠释放;另一方面,撕裂线不能在装饰表皮的表面可见,即使经过数年的磨损也应如此。
由于这些要求以及这个与安全相关的部件一旦失败所面临的商业风险,目前对于切割的剩余壁厚的公差要求极为严格,为此必须采用非常昂贵的加工技术来加以满足。
目前,在装饰表皮上预制安全气囊撕裂线的主要方法有激光切割、冷刀切割和热刀切割。
激光切割
在用激光切割出低强度撕裂线时,材料被激光的热量气化,然后被另一种气体除去。
这种工艺将产生一个沟槽,从外侧看易于被发现,因为该工艺产生的撕裂线由一系列孔组成。
图2 机械手辅助开口工具详解
该工艺采用传感器监测和控制,传感器安装在工件的外侧,用来探测通过剩余壁的激光的辐射量。
但是,目前传感器的灵敏度水平只能在光线通过相对较薄的剩余壁时达到要求,而且还受到材料种类和材料颜色的影响。
另外,孔附近的剩余材料受热后极易降解,从而发生穿透。
另一个问题是激光工艺本身会产生有毒气体和沉积,需要进行排出和处理,这是一个费时费钱的过程。
同时,粘在部件上的污物也需要非常昂贵的清洗。
由于这种高维护性,该工艺与下面提及的技术相比,无论是在采购还是在使用方面,都会产生太高的成本。
热刀切割
在热刀切割中,安装在冲孔附件上的特殊规格的预热穿孔刀嵌进工件表面,然后移动到某个固定位置。
该位置确定了剩余壁厚。
对于热塑性塑料来说,这是一个好办法,因为相对较宽的热刀刀刃,使切口变小,因而使必要的破裂力变大。
然而该工艺也有不足,即由于在剩余壁区域可能发生压缩和变形,从而使剩余壁厚发生急剧的变化。
此外,剩余材料的热降解和工件被强化的倾向也是影响该工艺的关键因素。
基于以上原因,这种方法被应用得较少。
冷刀切割
在冷刀切割工艺中,通过一台6轴机械手或者一台数控机床移动硬质金属切刀,使其穿过真空夹具固定的工件。
这种系统带有大量传感器,如一个被安装在切刀附近的履带式感应传感器,可间接测量刀尖与夹具的距离并将数据记录下来。
根据这些数据,可决定剩余壁厚是否因干扰而需要补偿,如温度漂移等。
该系统的一个问题是(特别是在3D尺度内),由于传感器被安装在切刀附近,因此无法测量刀尖与夹具表面的真实距离。
为克服这一问题,系统应该被修正,例如,将手动正确切割时的传感器跟踪曲线作为参考曲线,然后对每一次的加工曲线进行修正。
另外,为了监控加工路径,夹具上的工件位置也很重要,任何的偏差都会直接转化成工件剩余厚度的偏差。
因此,夹具需要进行非常昂贵的曲面铣,且要有稳固的设计,同时工件的固定位置需处于一个平坦的真空区域。
另外,工件与夹具的紧密接触应通过精密开关进行多点检查。
为获得夹具固定位置的重复性,还必须放弃惯用的用于并行加工的旋转工作台。
切刀的磨损通常由测量切刀的尺寸来确定。
切刀磨损,锋利程度降低,而切刀的长度保持不变,这会大大影响工件的剩余壁厚(本文将在下面做进一步解释)。
目前市场上在售的加工系统,都没有配置测量切刀切割性能的装置。
图3 TPO表皮剩余厚度和切割路径的关系
虽然数控机床具有足够高的路径精度,但为获得加工中的动态精度,必须有赖于与之配套的6轴机械手。
因此,只有相对昂贵的高精度机械手才能被选用。
尽管拥有上面提到的这些缺点,但是仍然有大量的冷刀切割设备被应用在这一领域。
这是因为,该设备的采购成本和运行成本都较低,且程序设计灵活,能够加工多种材料。
传感器控制切刀的切割
在切刀逆向切割时,切刀在相关的固定支撑或夹具上的移动距离精度主要依赖于机器手臂的动态精度。
在这里介绍一种新方法,可以用机械方法确定这一距离。
为了这一目的,部件支撑板用一个得到精密安装的滚球(可自由旋转)来代替。
该滚球通过一个C形框架与切刀相连。
工件表面位于球与刀之间,这使得在一个完整的行程内,球面与刀尖的距离能够通过伺服控制的精密芯轴驱动来自由调节,进而确定工件的剩余壁厚。
如果使固定在夹具上的表皮具有轻微的预张力,表皮的弹性则可补偿垂直于工件的加工运动路径的任何公差。
只要保证表皮层能够在滚球的表面延展良好,以上提到的因为加工路径不精确造成的问题,将会统统消除。
应用这一基本原理(如图1所示),可旋转的C形框架被安装在配有精密轴承和5轴机械手转矩支撑的切刀轴上(如图2所示)。
6轴机械手能够将切刀旋转到任何方向,C形框架与机械手臂之间保持固定角度。
工件的一侧进入C形框架,系统允许C形框架的开口宽度较小,同时也允许夹具设计简单。
图4 刀尖的力值和位置
为监控表皮与滚球的接触,在滚球和转轴之间安装了高精度力学传感器。
该传感器可以连续不断地对滚球上的轴向载荷进行监控,如果与预设值不符,那么可以确定这一工件为废品。
这个运动中的传感器能够监测表皮与滚球接触的任何切割位置。
一个改变刀/球距离的可能原因是C形框架的弹性。
C形框架的弯曲将直接影响工件的剩余厚度。
为确定这一因素的影响程度,可以通过实验来获得C形框架的载荷偏移曲线。
当载荷达到5N时,仅将C形框架弯曲0.01mm,这比系统要求的精度低10倍。
由于切割力在切割过程中的变化很小,因此,实际上对C形框架的影响程度远不及以上引用的数据。
系统的容许公差可通过不同材料、加工参数的改变而进行实验确定。
重要的加工参数包括给进速度、主预应力、切刀的磨损和刀/球之间的预设距离。
图3是一种聚烯烃弹性体(TPO)无纹理表皮的切割路径与剩余壁厚曲线。
剩余壁厚的变化范围在0.22~0.26mm之间,约为最大规定公差的50%。
剩余壁厚的测量使用了一种高精度数字显微镜。
虽然这种测量方法依据了当前的工业标准,但是测量结果还与许多因素有关,有时这些因素会对测量结果造成相当大的影响。
例如,抽样方法和测量点位置的确定是两个异常重要的因素。
另外,表皮颗粒也是一个干扰因素。
一般表皮颗粒的高度为0.2mm,因此没有一个合适的可供参考的平面。
基于这些困难,现行的办法是通过记录切刀与计量表面的近似距离来检查系统的能力和特性。
在常规的设备中,这些值的容许公差通常为±0.05mm,而在新设备中,这些值由促动器偏差和C形框架的弯曲构成,几乎比先前的要求低10倍。
因此从设备精度、系统可靠性来看,新设备比以前的设备更具优势。
图5 刀下表皮的弹性行为
刀刃与滚球计量表面的相对位置,能够作为每次换刀之后的参考。
为了这一目的,促动器运动到刀尖预期位置的前面并进行调节,以使推进速度降低。
在其随后的进一步运动中,作用在滚球上的力受到极高灵敏度传感器的监控,并被记录下来。
当刀尖与滚球接触时,传感器会传来信号进行指示。
此时,促动器立刻停止,它的这个位置被设定为新的零点位置。
图4显示了确定零点位置的可重复性,图中显示的实验为50次重复操作,其值小于5um。
第二条曲线显示了操作过程中的最大力均低于0.4N,这个结果令人满意。
刀尖与滚球表面的显微研究,表明了这种微小的力不会引起任何切刀和滚球的机械损坏,甚至在经过了50次重复实验之后也是如此。
新系统通过阴影传感器来监控表皮的切口以及和精密的刀刃测量相