模具设计料资.doc
《模具设计料资.doc》由会员分享,可在线阅读,更多相关《模具设计料资.doc(10页珍藏版)》请在冰豆网上搜索。
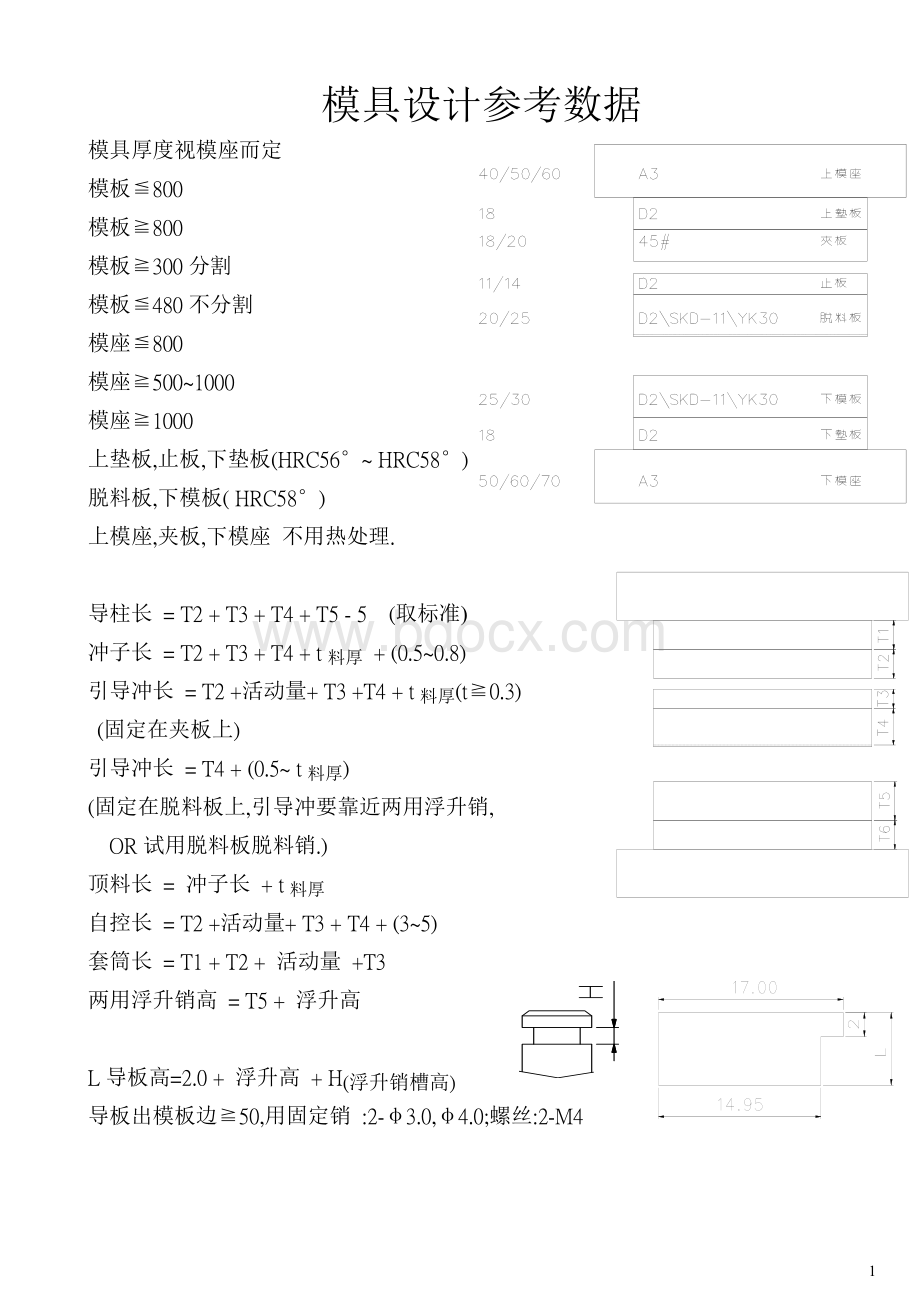
模具设计参考数据
模具厚度视模座而定
模板≦800
模板≧800
模板≧300分割
模板≦480不分割
模座≦800
模座≧500~1000
模座≧1000
上垫板,止板,下垫板(HRC56°~HRC58°)
脱料板,下模板(HRC58°)
上模座,夹板,下模座不用热处理.
导柱长=T2+T3+T4+T5-5(取标准)
冲子长=T2+T3+T4+t料厚+(0.5~0.8)
引导冲长=T2+活动量+T3+T4+t料厚(t≧0.3)
(固定在夹板上)
引导冲长=T4+(0.5~t料厚)
(固定在脱料板上,引导冲要靠近两用浮升销,
OR试用脱料板脱料销.)
顶料长=冲子长+t料厚
自控长=T2+活动量+T3+T4+(3~5)
套筒长=T1+T2+活动量+T3
两用浮升销高=T5+浮升高
L导板高=2.0+浮升高+H(浮升销槽高)
导板出模板边≧50,用固定销:
2-φ3.0,φ4.0;螺丝:
2-M4
模板
上垫板:
套筒孔:
M8→φ11.5;M10→φ13.5
夹板螺丝孔:
M8→φ9.0;M10→φ11.0
自设:
M5(沉头)→2个/4个(固定夹板与上垫板)
固定销孔:
φ8.5,φ10.5
自控孔:
φ9.0
弹簧孔:
φ(弹簧直径+1.0)
夹板:
各冲子孔间隙单边+0.01
自控:
φ6.03横孔φ4.1
导柱:
沉头孔φ(D+4),沉头深(T+0.2);导柱孔间隙单边+0.005
套筒:
M8→φ11.5;M10→φ13.5
固定销孔:
单边间隙+0.005
自设:
M5(攻牙)→2个/4个(固定夹板与上垫板)
锁紧螺丝:
M8,M10
冲子挡板螺丝:
M5
止板:
各冲子逃孔:
间隙单边+0.5~1.0
各冲子挡板逃孔
自控:
φ7.0
套筒:
M8→φ11.5;M10→φ13.5
导柱:
φ(D+2.0)
自设:
M5(沉头)→2个/4个(固定止板与脱料板)
脱料板:
各冲子导向孔间隙单边+0.005
各入块挂沟:
5.0高(逃深5.2)倒C1.5~2.0
浮升销逃孔深:
h=H+t料厚+(t-T)/2
自控:
φd+0.02,沉头φ7.0深?
导柱:
导套\无导套间隙单边+0.005
套筒螺丝:
M8,M10
引导冲孔:
间隙单边+0.005
自设:
M5(攻牙)→2个/4个(固定止板与脱料板)
高度自控:
2-M5侧攻深15.0mm,在脱料板厚的一半处
导板逃孔
脱料板的料沟深:
t–0.05
下模板:
各入块孔:
间隙单边+0.005
螺丝孔:
M8,M10
顶出销孔:
φd+0.02
两用浮升销孔:
φd+0.02
引导冲孔:
φd+0.4
自设:
M5(攻牙)→2个/4个(固定下模板与下垫板)
固定销孔:
φ8orφ10间隙单边+0.005
导柱孔:
φd,间隙单边+0.005
高度自控:
2-M5侧攻深15.0mm,在下模板的5.0mm高处
下垫板:
各冲子下料逃孔:
间隙单边+0.5~1.0
折弯入块敲击孔:
φ3.5orφ4.0
锁紧螺丝:
M8→φ9.0;M10→φ11.0
浮升销孔:
φd间隙单边+0.25~0.5
固定销孔:
φ8.5,φ10.5
辅助导柱孔:
φd+1.0
铁材冲裁间隙:
异形6%,圆形5%
圆弧交切:
切线方向30∘,先切圆弧后切直线
折弯成形冲子直线(身)部:
侧切标准:
L=PH+(0.03~0.05)
引导冲:
先冲φd+0.03,引导冲用φd
字模标准:
字的大小为2.0,电极图
模具设计可能分为下列几个阶段
一.成品尺寸设定值二.成品展开尺寸及图形三.三连排料及尺寸
四.工程排列草图五.上下模块立图六.零件,草图之图形尺寸
七.交接图面之标示八.图面之校对
一.成品尺寸设定值
1.成品图上各尺寸均有标注公差,因此必须设定一个在公差范围内的值以作为模具尺寸.其目的在使成品能达到成品图上的要求,而以达到公差中间值为最高目标.
2.剪切时产生的毛边会影响成品尺寸,设定时必须补正.例如冲圆孔时所造成的毛边会使圆孔变小,因此要把设定值设大.(有时是考虑电镀后孔径的变化)
3.模具磨耗也会影响成品尺寸,设定时要加以考虑.例如打凸点时,凸点高度会因模具磨耗而降低,因此可以把高度设大.
4.材料的折弯反弹也有影响.例如折弯内R会因反弹而变大,因此可以设小.
5.某些情形的折弯,材料的拉伸很大,与展开的数值会有出入,设定时也要注意.例如U形折弯拉伸情况显著,因此可以把两侧的高度设小,以补正展开的误差.
6.设定值以不超出公差范围为原则,在公差范围小时可以设定在上限,下限的数值.
7.跨越中心线的尺寸尽量设成小数点后第二位是变量,可避免单边尺寸出现小数点后三位数的困扰.
二.成品展开尺寸及图形
1.将成品折弯部份长度展开,以决定其外形尺寸,才能进行排料等工程.
2.平板折弯时,外侧受拉应力拉伸,内侧受压应力而缩短,中有中性轴部份长度不变,因此展开时必须以中性轴位置来展开.
3.展开时尺寸以小数点后三位数之精度计算,待展开成平面时再四舍五入至小数点后第二位,可以避免直接以小数点后二位计算造成的累计误差.
三.三连图排料及尺寸
1.先看成品是否有压延方向,毛边方向等限制,然后考虑工程顺畅性及材料使用率等问题来决定排料,连料及下料的方式.(注意成品图上之注记)
2.决定料宽及送料长度时,除了省料的原则之外,也要考虑料带的强度是否足够.例如边料,桥接处等.
3.排刀口时要考虑工程的顺序,以决定刀口的外形.
4.刀口交切要避免产生毛边,细屑,并注意成品是否允许过切等问题.
5.冲子的强度要考虑,是否需要补强,及补强的方式.下模刀品的强度是否足够,若强度不足则考虑将此刀口分开.
6.废料可以加以得利用,像是补强料带,增设导位孔等,但以不影响后续工程为原则.
7.改变刀中的方向和排列,找出最节省空间的排列方式.例如下面三种排列方式,第一种方
式则下模强度不足,第二种方式成品的两个角条件不相同,并且必须占用二个工程,所采取第三种方式最好.
8.三连图及侧视图之标注应详细,将模具上会使用到的尺寸均标示清楚,以方便后续作业.
四.工程排列草图
1.注意工程的先后顺序是否会影响模具的制造,冲压的顺畅性以及成品的精度.
2.先后顺序没有影响时,改变其顺序,找出最省空间或利于零件制作的排列方式.
3.考虑PILOT和浮升销的设置,必要时改变零件形状,或调整工程顺序.
4.注意零件强度以及位置,时否有互相干涉的情形.
五.上下模块立图
1.组立图上的尺寸以模板尺寸为主,在不影响模具功能的情况下尽量选择在整数的位置.
2.注意逃孔的设置必须完备,模板及零件的强度要加以考虑.
3.考虑零件的加工性才维护,在不影响成品精度的情况下,采用简单的设计.
4.注意零件的互换,对称性,考虑中否有设置防呆的必要.
5.成品下料要设置吹气装置辅助下料.
6.模板的标准厚度
7.折弯,侧击机构侧视图,有助于组立作业.
8.浮升高度太高会造成料带的巨幅振动,影响成品精度.因此不宜太高.影响浮升高度有几个因素:
A折弯机构
如右图所示情况,浮升高必须大于H
B侧击机构
浮升高度必须大于滑块活动量.
C送料
在不能设置逃孔的情况下,若要顺利送料,浮升高度要大于H.
以上提到的三种因往往同时出现,此时浮升高度则必须累加.
9.活动量太大则冲子长度必须加长,增加零件制作成本,对冲子的的耐用度也有不良影响.因此也不宜太大.
响活动量的因素:
A折弯机构
活动量必须大于H
B侧击机构
活动量必须大于滑块活动量X
六.零件草图之图形尺寸
(一)剪切零件
1.冲子
L=夹板厚+止板厚+脱料厚+料厚+0.3~0.5
a.0.3~0.5为冲子刺入下模的深度,和材料厚有关,材料较厚则刺入较深,刺入太深则冲子和下模磨耗较大,刺入太浅则容易浮料.成品下料好为满刀口,或几乎为满刀口时,切入下模之深度可为1.0并配合下模之刀口直线部以使成品下料顺畅,减少变形.
b.冲子和夹板之配合间隙单边0.005
2.脱料板入子
a.刀口部份成型参照冲子,单边0.005,直线部在导位长度以下10~15’.导位部份若不亦查不做推拔.
b.放电逃孔背深=脱料板厚-导位长度.
c.亦可采用分割的方式.
3.下模板入子
a.第1种方式采用线割,成型参照冲子,单边加上剪切间隙切刃部份研磨量以下30’.优点是四个角的条件均相同,缺点则是配合研磨的冲子时冲子需倒角,且无法达到直角的要求.
b.第2种方式和第1各种方式均用研磨成型,切刃部份研磨量以下放电逃开.若刀口并不在时,第2种方式平面那一块可以不需放电.休用分割入子的优点是转角处的R可以较小,缺点则是四个角的剪切条件不一样.第4种分割方式虽然四个角的条件一致,但是交界处容易有毛边.
c.第2种方式零件加工容易,且其中一块完全为平面,但是条件不同的角分别在同一边容易推单边.第3种方式零件加工容易,且不受刀口尺寸的限制,且分的角落在对角,作用力可以扺消.第4种方式零件加工较费时,且容易在交界处产生毛边,但应用在端切入子上,可以把有剪切的部份做成钨钢,而靠刀部份用ASP即可,可以节省最多的材料费.
d.剪切间隙:
剪切形成的端面如右所示,尺寸测量以剪断面为准.
间越小则剪断面越大,端面平直度越好,但模具也较快耗损.
间隙越大则剪断面越小,尺寸精度越差.意过小或过大,
均会造成较大毛边.正常剪切间隙与材料成正比,与材料硬度亦成正比.
单边剪切及修边间隙,艾较一般间隙为小.
(二)折弯零件
1.上折
a.基本的上折机构如上所示,由STP入子,DP入子和顶出块组成.
b.折弯直线部L一般取4t~6t,太小则角度不易达到要求,太大对折弯并无帮助,且影响浮升高度.
c.R1越大则回弹角度越大,但R1太小时则会断裂.
d.R2太小会造成成品刮伤.(R2一般约为t~4t)
e.顶出块的顶出力约为(1/3~1/4)的折弯力量.
2.下折
基本的下折机构台上所示,