先进航空发动机关键制造技术研究.docx
《先进航空发动机关键制造技术研究.docx》由会员分享,可在线阅读,更多相关《先进航空发动机关键制造技术研究.docx(15页珍藏版)》请在冰豆网上搜索。
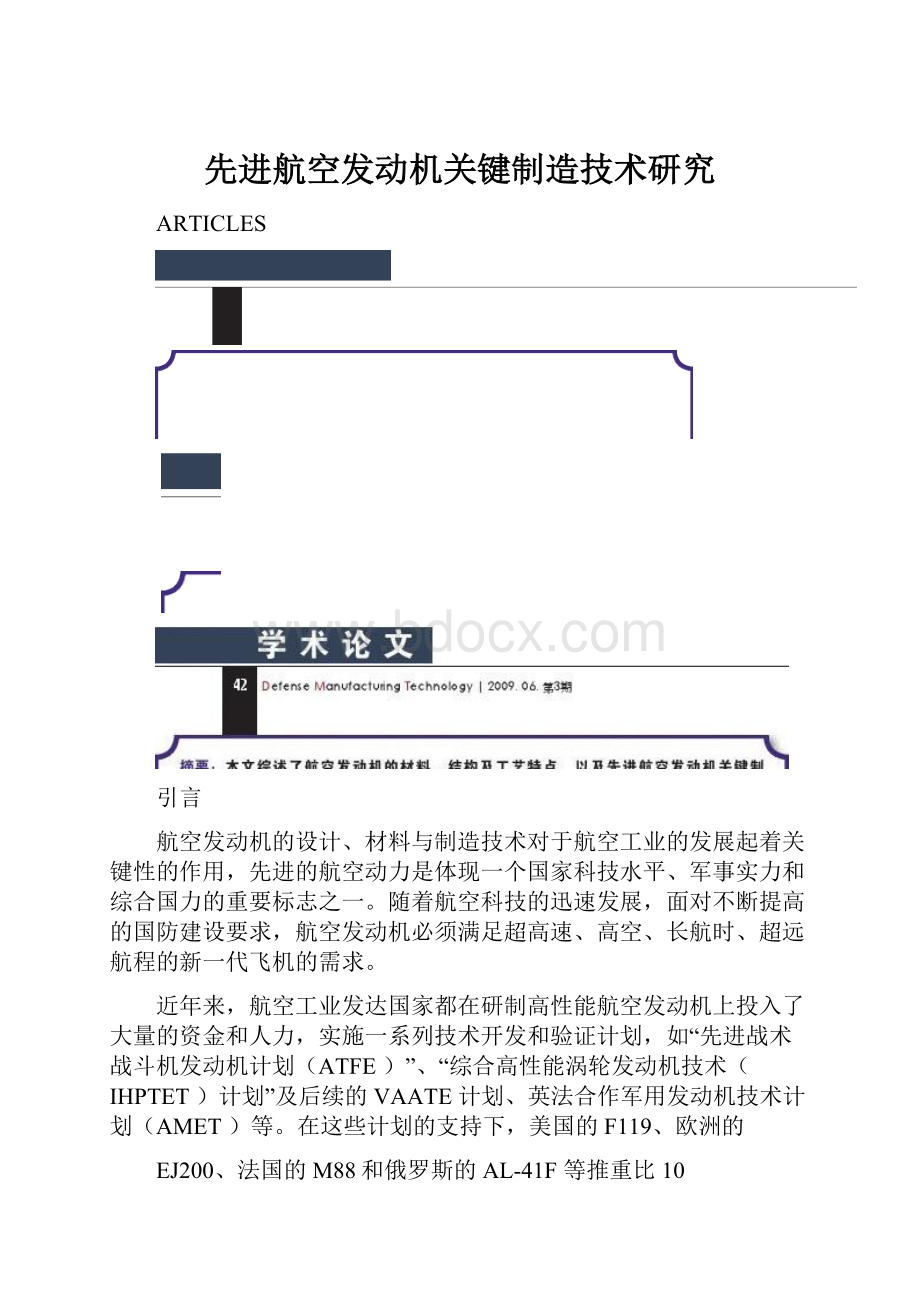
先进航空发动机关键制造技术研究
ARTICLES
引言
航空发动机的设计、材料与制造技术对于航空工业的发展起着关键性的作用,先进的航空动力是体现一个国家科技水平、军事实力和综合国力的重要标志之一。
随着航空科技的迅速发展,面对不断提高的国防建设要求,航空发动机必须满足超高速、高空、长航时、超远航程的新一代飞机的需求。
近年来,航空工业发达国家都在研制高性能航空发动机上投入了大量的资金和人力,实施一系列技术开发和验证计划,如“先进战术战斗机发动机计划(ATFE)”、“综合高性能涡轮发动机技术(IHPTET)计划”及后续的VAATE计划、英法合作军用发动机技术计划(AMET)等。
在这些计划的支持下,美国的F119、欧洲的
EJ200、法国的M88和俄罗斯的AL-41F等推重比10
一级发动机陆续问世。
为了提高发动机的可靠性和推力,先进高性能发动机采用了大量新材料,且结构越来越复杂,加工精度要求越来越高,对制造工艺提出了更高的要求。
而且,在新一代航空发动机性能的提高中,制造技术与材料的贡献率为
50%~70%,在发动机减重方面,制造技术和材料的贡献率占70%~80%,这也充分表明先进的材料和工艺是航空发动机实现减重、增效、改善性能的关键。
1航空发动机的材料、结构及工艺特点
在提高发动机可靠性和维护性的同时,为了提高发动机的推力和推重比,航空发动机普遍采用轻量化、整体化结构,如整体叶盘、叶环结构。
钛合金、镍基高温合金,
以及比强度高、比模量大、抗疲劳性能好的树脂基复合材
先进航空发动机
关键制造技术研究
黄维,黄春峰,王永明,陈建民
(中国燃气涡轮研究院,四川江油621703)
Keymanufacturingtechnologyresearchofadvancedaero-engine
HUANGWei,HUANGChun-feng,WANGYong-ming,CHENJian-min
(ChinaGasTurbineEstablishment,Jiangyou621703,China)
Abstract:
Thispaperdescribesthefeaturesofaero-enginematerial,structureandtechnology,andthen,developmentstatusandtrendofkeymanufacturingtechnologyforadvancedaero-enginewasanalyzed.Finally,thedevelopmentofadvancedaero-enginemanufacturingtechnologyinChinaisintroducedandsomeproposalsareputforward.KeyWords:
aero-engine,manufacturing,summarization
作者简介:
料,耐高温、抗疲劳及蠕变性能好的金属基复合材料和陶瓷基复合材料在航空发动机上的应用越来越广泛。
与上述结构及材料的变化相适应,航空发动机的制造工艺特点突出表现在以下几点:
(1)材料难加工,切除率大
航空发动机核心转子部件通常采用钛合金、高温合金等难加工材料,材料的热硬度和热强度很高,切削过程中表现出很高的动态切变强度,会加剧刀具切削刃的磨损,降低工件表面的加工质量和表面完整性。
为了增加零件的强度和运行安全性,一些核心转子部件,如压气机整体叶盘通常采用整体锻造毛坯,加工过程中超过90%以上材料被切除掉。
因此,如何提高航空发动机核心转子部件的加工精度、加工效率以及加工结果的表面完整性至关重要。
(2)形状与结构复杂
为实现减重增效,航空发动机零部件大都采用复杂曲面和高结构效率的整体、轻量化结构,这对制造工艺以及制造设备提出了更高的要求。
在大飞机用发动机中普遍采用宽弦空心风扇叶片、整体叶盘/叶环、复合冷却层板等,均由于结构的复杂性导致现有的制造工艺方法无法满足实际生产的需要。
因此,必须针对不同的零件结构,在不断改善现有工艺的同时积极探索新工艺、新方法和新技术,提高复杂构件的制造水平,降低加工成本。
(3)加工精度高
航空发动机的制造精度直接影响其性能、运行安全性,因此发动机对加工精度的要求非常苛刻。
而发动机材料、结构和工艺的复杂性与其高精度制造之间形成了一对矛盾,造成我国发动机零部件的生产过程中产品一致性差、合格率低等问题,成为制约高性能航空发动机研制的一个瓶颈。
2先进航空发动机关键制造技术发展现状与趋势
2.1轻量化、整体化新型冷却结构件制造技术
整体叶盘是新一代航空发动机实现结构创新与技术跨越的关键部件,通过将传统结构的叶片和轮盘设计成整体结构,省去传统连接方式采用的榫头、榫槽和锁紧装置,结构重量减轻、零件数减少,避免了榫头的气流损失,使发动机整体结构大为简化,推重比和可靠性明显提高。
在第四代战斗机的动力装置推重比10发动机F119和EJ200上,风扇、压气机和涡轮采用整体叶盘结构,使发动机重量减轻20%~30%,效率提高5%~10%,零件数量减少
50%以上。
目前,整体叶盘的制造方法主要有:
电子束焊接法;扩散连接法;线性摩擦焊接法;五坐标数控铣削加工或电解加工法;锻接法;热等静压法等。
在未来推重比15~20的高性能发动机上,如欧洲未来推重比15~20的发动机和美国的IHPTET计划中的推重比
20的发动机,将采用效果更好的SiC陶瓷基复合材料或抗氧化的C/C复合材料制造整体涡轮叶盘。
如果将整体叶盘中的轮盘部分去掉,就成为整体叶环,零件的重量将进一步降低。
在推重比15~20高性能发动机上的压气机拟采用整体叶环,由于采用密度较小的复合材料制造,叶片减轻,可以直接固定在承力环上,从而取消了轮盘,使结构质量减轻70%。
目前正在研制的整体叶环是用连续单根碳化硅长纤维增强的钛基复合材料制造的。
推重比15~20高性能发动机,如美国XTX16/1A变循环发动机的核心机第3、4级压气机为整体叶环转子结构。
该整体叶环转子及其间的隔环采用TiMC金属基复合材料制造。
英、法、德研制了TiMMC叶环,用于改进EJ200的3级风扇、高压压气机和涡轮。
大小叶片转子技术是整体叶盘的特例,即在整体叶盘全弦长叶片通道后部中间增加一组分流小叶片,此分流小叶片具有大大提高轴流压气机叶片级增压比和减少气流引起的振动等特点,是使轴流压气机级增压比达到3或3以上的有发展潜力的技术。
在新一代航空发动机上有很多机匣,如进气道机匣、外涵机匣、风扇机匣、压气机机匣、燃烧室机匣、涡轮机匣等,由于各机匣在发动机上的部位不同,其工作温度差别很大,各机匣的选材也不同,分别为树脂基复合材料、铁合金、高温合金。
树脂基复合材料已广泛用于高性能发动机的低温部件,如F119发动机的进气道机匣、外涵道筒体、中介机匣。
至今成功应用的树脂基复合材料有PMR-15(热固性聚酰亚胺)及其发展型、Avimid(热固性聚酰亚胺)AFR700等,最高耐热温度为290℃~371℃,2020年前的目标是研制出在425℃温度下仍具有热稳定性的新型树脂基复合材料。
树脂基复合材料构件的制造技术是集自动铺带技
ARTICLES
术(ATL)、自动纤维铺放技术(AFP)、激光定位、自动剪裁技术、模压成形、树脂传递模塑成形(RTM)、树脂膜浸渍成形(RFI)、热压罐固化成形等技术于一体的综合技术。
英国罗·罗公司成功开发出遄达系列的超塑成形-扩散连接发动机宽弦风扇转子叶片,引起了国际航空界的高度重视,此类空心叶片的轻质量、高结构效率使航空发动机的综合性能得到显著提高。
如今,宽弦、无凸台、空心叶片是高性能发动机风扇和第一级压气机叶片的发展方向。
推重比10一级发动机F119,EJ200均采用了宽弦风扇叶片,GE公司的GE90,推重比15~20高性能发动机都采用复合材料风扇叶片。
现在宽弦风扇叶片主要采用超塑成形-扩散连接(SuperplasticForming/DiffusionBonding,SPF/DB)技术。
与传统工艺制造的零件相比,SPF/DB组合工艺技术具有重量轻、成本低、效益高、整体性好、成形质量高等优点。
目前国外正在研究的推重比15~20高性能发动机的金属基复合材料风扇叶片,是一种空心的、用连续碳化硅纤维增强的钛基复合材料(TiMMC)制造,采用超塑成形/扩散连接工艺制出空心风扇叶片。
多孔复合冷却层板结构是推重比10以上发动机采用的先进冷却结构,多用于燃烧室和涡轮叶片,它是一种带有复杂冷却回路的多孔层板,用扩散连接方法连接成形的冷却结构,其关键制造技术是计算机辅助设计和绘制复杂冷却回路,用“照相-电解法”制成冷却回路,扩散连接成多层多孔层板。
由此可知,整体化结构、新型冷却结构等新技术,使发动机诸多零件减轻了质量、降低了成本、提高了效率,从而保证了发动机高推比、高性能的相关要求。
2.2新材料构件制造技术
推重比15~20一级的航空发动机要求材料具有耐高温、高强度、高韧性等特性。
高性能发动机已经采用很多种类的新材料和新材料构件,尤其是金属基复合材料、陶瓷基复合材料、碳/碳复合材料是当前高温复合材料领域开发和应用研究的热点。
与其同时进行的高温复合材料构件制造技术正在深入地发展。
SiC长纤维增强Ti基复合材料(TiMMC)具有比强度高、比刚度高、使用温度高及疲劳和蠕变性能好的优点。
例如德国研制的SCS-6SiC/IMI834复合材料的抗拉强度高达2200MPa,刚度达220GPa,而且具有极为优异的热稳定性,在700℃温度暴露2000h后,力学性能不降低。
TiMMC叶环代替压气机盘,可使压气机的结构质量减轻70%。
美国制备的TiMMC叶环已在P&W的
XTC-65IHPTET验证机上成功地进行了验证,能够满足性能要求。
英、法、德也研制了TiMMC叶环,并成功地进行了台架试验。
未来发动机的低压压气机叶片和静子叶片、整体叶环、机匣及涡轮轴将采用金属基复合材料制造。
TiMMC关键制造技术有、纤维涂层法、等离子喷涂法、浆料带铸造法、箔-纤维法。
推重比15~20高性能航空发动机的涡轮前温度将达到2200K以上,
连续纤维增韧陶瓷基复合材料(CMC)耐温高,密度低,具有类似金属的断裂行为,对裂纹不敏感,不发生灾难性的损毁,可代替高温合金作为热端部件结构材料。
CMC的应用使发动机大幅度减重,节约冷却气或无需冷却,从而确保发动机高推重比的有关性能。
美、英、法等发达国家以推重比9~10发动机(如F119、EJ200、F414等)作为CMC的验证平台,主要验证的部件有SiC基CMC的燃烧室、涡轮外环、火焰稳定器、矢量喷管调节片和密封片,甚至整体燃烧室和整体涡轮等构件。
SiC基CMC的关键制造技术包括纤维预制件的设计和制造、SiC基体的致密化技术、纤维与基体间界面层和复合材料表面防氧化涂层的设计与制造以及构件的精密加工等。
碳/碳复合材料(C/C)的最显著的优点是耐高温(1800℃~2000℃)和低密度(约1.9g/cm3),可能使发动机大幅度减重。
美、法、俄等研制的C/C复合材料部件有燃烧室喷嘴、加力燃烧室喷管、涡轮和导向叶片、整体涡轮盘、涡轮外环等。
美国将整体涡轮盘在1760℃进行了地面超转试验。
C/C构件的关键制造技术包括碳纤维预制体的设计与制备、C/C的致密化技术和C/C防氧化涂层的设计与制造。
C/C致密化方法有化学气相浸透法(CVI)和液相浸渍法。
液相浸渍法包括树脂浸渍炭化法和沥青浸渍炭化法,发展的方向是提高致密化速率,降低制造成本。
由
于航空发动机用C/C构件要满足富氧燃气环境下长寿命工作的要求,所以必须解决C/C抗氧化的问题。
通过设计和制备防氧化涂层是改善C/C抗氧化性的主要途径,也是国际研究的热点,目前尚未取得突破性进展。
由上可见,与现行推重比8的发动机相比,新材料构件不管在结构设计、制造技术方面,还是在整体质量方面,都有较大突破,因此可确保推重比15~20等高性能的实现。
2.3航空发动机制造技术新工艺
目前,先进精密毛坯制造技术正在向近净成形方向发展。
先进的精密制坯技术有定向凝固和单晶精铸制坯、精密锻造制坯和快速凝固粉末冶金制坯技术。
高性能航空发动机采用了大量的新型结构件,由于制坯技术的进步将导致毛坯件发生重大变化。
精铸件、精锻件、单晶和定向凝固精铸件以及快速凝固粉末冶金制坯毛坯将取代传统的大余量毛坯。
传统意义的锻件将由77%降至33%,精铸件由18%增至44%以上,粉末冶金件由3%增至8%,复合材料构件由4%增至15%。
切削加工一直是航空发动机关重件的主要制造手段。
随着航空发动机推重比的不断提高,特别是质量的不断减轻,发动机制造将越来越多地依赖于高比强度、低密度、高刚度和耐高温能力强的钛合金、高温合金以及金属基复合材料等新材料,而这些材料都属于典型的难加工材料。
同时发动机关重件往往型面复杂,对加工精度和表面完整性的要求极高,因此在新一代航空发动机的切削加工中迫切需要采用新型刀具材料、刀具结构以及高效的工艺方法,同时这种需求也大大推动了具有高刚度、高精度和大驱动功率的专用机床和通用机床的发展。
数控加工技术在航空发动机的制造中主要用于压气机及涡轮机的各类机匣、压气机盘及涡轮盘、涡轮轴和压气机轴等复杂构件的加工。
高端数控装备及技术作为国家战略性物资,对提高发动机整体制造水平起着举足轻重的作用,如美国洛克希德·马丁公司在研制JSF联合攻击机时,采用五坐标数控加工方法,将约1.5t的铁合金锻锻锭数控铣削加工成重约99kg的大型升力风扇整体叶盘,其切除率超过93%。
高效精密切削、变形补偿、自适应加工,以及抗疲劳制造等技术的研究和应用在新一代发动机的加工中需求迫切;同时,加工过程的知识积累对于提高加工效率、加工
质量和加工的自动化水平非常重要,应围绕发动机关重件和典型材料的高效数控加工建立相应的切削数据库。
磨削在先进的切削技术研究中占有重要地位。
在磨削加工技术的研究中,为了获得高加工效率,世界发达国家开始尝试高速、强力磨削技术,如利用强力磨削可一次磨出涡轮叶片的榫头齿形。
目前,磨削技术的发展趋势是:
发展超硬磨料磨具,研究精密及超精密磨削、高速高效磨削机理并开发其新的磨削加工技术,研制高精度、高刚性的自动化磨床。
以高能束流加工为代表的特种加工技术在难切削材料加工,复杂构件的型腔、型面、型孔、微小孔、细微槽及缝的加工中具有显著优势,解决了常规加工很难解决的问题。
特种加工技术主要包括:
激光加工、电子束加工、离子束加工、等离子加工、电火花加工、电解加工、超声波加工、磨料流加工、高压水射流切割等。
通过电磁场、温度场、化学场和力场(包括空间微重力场)等外加因素的综合应用以及激光、等离子束、微波等多种能量形式的结合,开辟材料加工成形技术创新的广阔途径。
先进焊接连接技术作为确保航空发动机结构完整性不可缺少的手段,其研究、开发与应用直接关系到新一代航空发动机的质量、寿命和可靠性。
特种焊接技术由于具有可明显减轻结构重量、降低制造成本、提高结构性能等特点,满足航空发动机轻质化、长寿命、低成本、高可靠性制造的要求,已成为航空发动机制造中的一项重要技术。
特种焊接技术主要包括:
钨极惰性气体保护弧焊(GTAW)、活性焊剂焊接技术、自蔓延高温合成焊接法、等离子弧焊(PAW)、电子束焊(EBW)、激光焊(LBW)、真空钎焊(VB)、扩散焊(DB)、摩擦焊等。
近年来,新型纤焊和扩散焊、摩擦焊和高能束流焊接等先进焊接技术在航空发动机制造中的发展和应用越来越广泛。
在欧美已相继用摩擦焊取代电子束焊用于发动机的粉末冶金等温锻造盘-盘及盘-轴一体化焊接。
摩擦焊接技术在发动机转子鼓筒、整体叶盘的焊接中得到和应用,并逐渐发展成为航空发动机制造中的一项关键技术。
先进的高推重比发动机结构中将大量采用以热障涂层
ARTICLES
技术为代表的先进热障涂层技术。
涂层技术在航空发动机关键零部件的耐磨、高温防护、隔热、封严以及钛合金零件的防微动磨损、阻燃等方面起了显著的作用,应用越来越广泛。
先进的涂层方法主要包括:
真空等离子喷涂、层流等离子喷涂、超音速火焰喷涂、电子束物理气相沉积、化学气相沉积、真空离子溅射涂层(MAП炉)等。
热端部件采用热障涂层以提高结构强度,其中有陶瓷涂层和多层隔热层。
陶瓷热障涂层需先在零件表面喷涂MCrALY底层以提高结合强度。
多层复合隔热涂层是在基体金属表面钎焊一层柔性金属纤维结构(材料为HFe22.5Cr5.5SiO0.1C)
,可减少冷却气流80%。
涡轮工作叶片和导向器的隔热涂层采用低压等离子喷涂涂敷,也可以采用电子束物理气相沉积(EB-PVD)涂敷。
发动机冷端部件均采用封严涂层、耐磨和防腐蚀涂层。
快速原型(RapidPrototyping,RP)制造技术出现于
20世纪90年代中期,这种基于“离散-堆积”原理和增材制造的方法,能够实现高性能复杂结构金属零件的无模具、快速、近净成形,具有高度柔性的制造思想已经被企业界广泛接受,其应用已从最初的设计原型和测试原型制造向最终产品制造的方向发展。
快速原型/零件制造技术为航空发动机复杂零件的设计实现实体化提供快速方便的手段,可实现精铸复杂模具的制造,现在发展到直接快速成形零件,是一种很有发展前景的工艺方法。
主要方法有:
分层实体制造(LOM)、选择性激光烧结(SLS)、熔化沉积制造(FDM)、三维立体印刷(SLA)和三维焊接法等。
快速原型制造技术一经出现,就成为先进制造技术和激光加工领域研究的热点,美国军方对这项技术的发展给予了相当的关注和支持,在其直接支持下,美国率先将这一先进技术实用化,目前,F-22和F/A-18E/F上的几个关键零件已经采用了TC4钛合金激光快速成形件。
该技术能显著提高疲劳性能,降低成本40%,加工周期仅为传统工艺的1/5。
推重比10一级发动机涡轮前温度达到
1500℃~1700℃。
艾利逊公司研究了用Lamilloy多孔层板加柔性金属/陶瓷制造的浮壁式火焰筒结构。
普惠公司研究了用玻璃陶瓷基复合材料制造浮壁式火焰筒结构。
F119
采用的浮壁式火焰筒结构是用多环段连接而成。
环段背向火焰一面对流散热的凸环,并有缝隙形成冷却隔热气膜,隔热环是由浮动片组成,并用螺栓连接在外环段上。
浮动片用精密铸造而成,而冷却隔热环局部喷涂热障涂层,以降低部件表面温度。
2.4航空发动机零部件的无损检测技术
无损检测技术能为发动机产品提供内部质量信息,既可作为产品评价的依据,也为工艺分析提供参考信息,是确保发动机结构高可靠性的重要手段。
对于航空发动机而言,在服役过程中难免会出现一些疲劳裂纹、损伤以及恶劣工作环境下组织状态变化等问题,及时检测到这些问题对于减少事故、提高零部件的使用寿命有重大意义。
常用的检测技术有超声检测、涡流检测、工业CT无损检测等。
无损检验技术发展的总趋势仍是速度快,自动化程度高,分辨率高,易于解读,可靠性高,以及成本低。
例如,在传统的超声、电磁及声学检验中,广泛引入移动式自动扫描,综合应用了多种技术,出现了自动扫描的超声、电磁、传感器系统,声学-激光自动扫描系统。
2.5面向零件制造过程的专业化成套制造技术
作为单项数字化制造技术的集成,将信息技术与制造技术相结合而形成的数字化生产线技术的应用成为航空发动机行业提高生产质量和柔性的关键技术。
GE、罗·罗和普惠等主要航空发动机生产厂商应用数字化技术,建成了一系列航空发动机典型零件自动化生产线,取得了良好的效果。
(1)压气机叶片精密锻造生产线
目前航空发动机有33%的工作量来自于叶片的制造,叶片精锻生产线是解决叶片制造瓶颈的有效方法之一。
生产线由叶片制坯、叶片精锻成形、叶片型面化铣、叶片热处理、叶片检测5条子生产线组成,适合于高温合金、钛合金、铝合金和不锈钢等材料精锻叶片的批量生产。
(2)涡轮叶片精密铸造生产线
涡轮叶片制造质量对航空发动机的性能有很大影响。
由于其结构复杂、制造技术含量高,其精铸质量和尺寸精度与叶片研制过程中的设计、制造、冶金、化学、制模、炉工等人员密切相关。
国外航空发动机制造公司花费大量资金建立了发动机涡轮叶片精铸生产线。
(3)压气机转子叶片电化学自动化加工生产线
该生产线集拉削加工技术、高精度测量技术、电化学技术、电火花加工技术、机器人技术以及无损检测技术等众多技术于一体,其关键技术为360°电化学加工技术。
首先采用组合的垂直拉床将预切长度的棒材拉削加工出叶片的榫齿,然后利用根部来定位,从叶盆和叶背两面进行电化学加工,一次完成叶身型面加工。
2.6以信息化技术为纽带,建立数字化工厂为发动机型号研制和数字化技术推广应用提供了重要保障。
异地协同设计制造平台建设已经起步,并行工程的思想被行业普遍接受,先进制造技术被设计部门采用,加快了新机研制的进度。
在关键重要件的制造环节,CAPP技术在工艺设计中得到了较普遍的应用;PDM已经在企业得到应用,并规划建设了以MES技术为基础的数字化制造车间信息管理系统。
在企业管理方面,数字化技术也成功应用于生产计划管理、物质供应、财务管理、项目管理、人力资源管理、办公自动化等方面,同时开展了管理流程优化工作,提高了管理效率,降低了管理成本。
(2)按照零件特点建立了航空发动机盘环零件生产线、叶片精锻生产线和大型钛合金机匣一体化制造生产线。
我国最大的叶片精锻生产线已在西安航空发动机集团公司建成技产,由叶片制坯、叶片精锻成形、叶片型面化镜、叶片热处理、叶片检测5条子生产线组成,可以满足高温合金、铁合金、铝合金和不锈钢等材料精锻叶片的批量生产。
该条生产线的建成和投产,改变了传统的叶片加工制造工艺技术,使生产效率和叶片的质量显著提高,产品合格率达到95%以上。
(3)重要件关键工艺研究取得了重大突破。
超塑成形扩散连接技术是宽弦空心钛合金风扇叶片成形的关键技术。
我国航空制造工程研究所在大型宽弦风扇空心叶片的超塑成形/扩散连接组合工艺方面已经开展研究,并成功应用于新型涡扇发动机。
(4)整体叶盘五坐标NC加工工艺技术在新机研制中得到了广泛应用,成功地应用于两级风扇整体叶盘。
这是目前国内整体叶盘制造最有效的技术。
(5)整体叶盘电解加工技术成功地应用于以高温合金为代表的难切削材料的整体结构件制造。
(6)整体叶盘线性摩擦焊接技术进入了实质性的研究阶段。
(7)空心叶片制造的关键工艺技术已经突破,并进入应用阶段。
(8)涡轮叶片定向凝固和单晶精铸的关键工艺已经突破,并在新机研制中得到应用和验证。
(9)涡轮盘、涡轮导向器、大型机匣整体精铸关键技术已经在新机研制中得到应用。
(10)快速成形技术、热障涂层技术、电子束焊接、激光束焊接、混合搅拌焊接等新工艺方法已在新机研制中应用。
信息化是振兴及提升航空发动机制造业的必要途径,必须将专业的制造技术与信息技术、管理技术相融合,运用先进的信息技术和现代管理思想,实现航空发动机设计、试验、制造、检测、管理、使用和维护等全过程的自动化、网络化和智能化。
在国外,航空发动机研制已利用信息化技术从传统的大批量制造模式转向现代先进精益制造模式。
例如,GE公司发动机部GEAE在1998年制订实施了航空发动机异地协同设计和制造的增量式发展规划,取得了显著的效益。
罗·罗公司建立了发动机典型零件的自动化生产线和协同的计算机工作环境,实施了并行工程,从整体上增强航空发动机的研制能力。
普惠公司采用集成产品开发团队的形式来管理发动机全生命周期内的计划、流程、技术、信息等经济技术活动,建立先进的数字化工厂。
3我国航空发动机先进制造技术发展状况与建议3.1我国航空发动机先进制造技术取得的