玩具厂实用注塑工艺.docx
《玩具厂实用注塑工艺.docx》由会员分享,可在线阅读,更多相关《玩具厂实用注塑工艺.docx(29页珍藏版)》请在冰豆网上搜索。
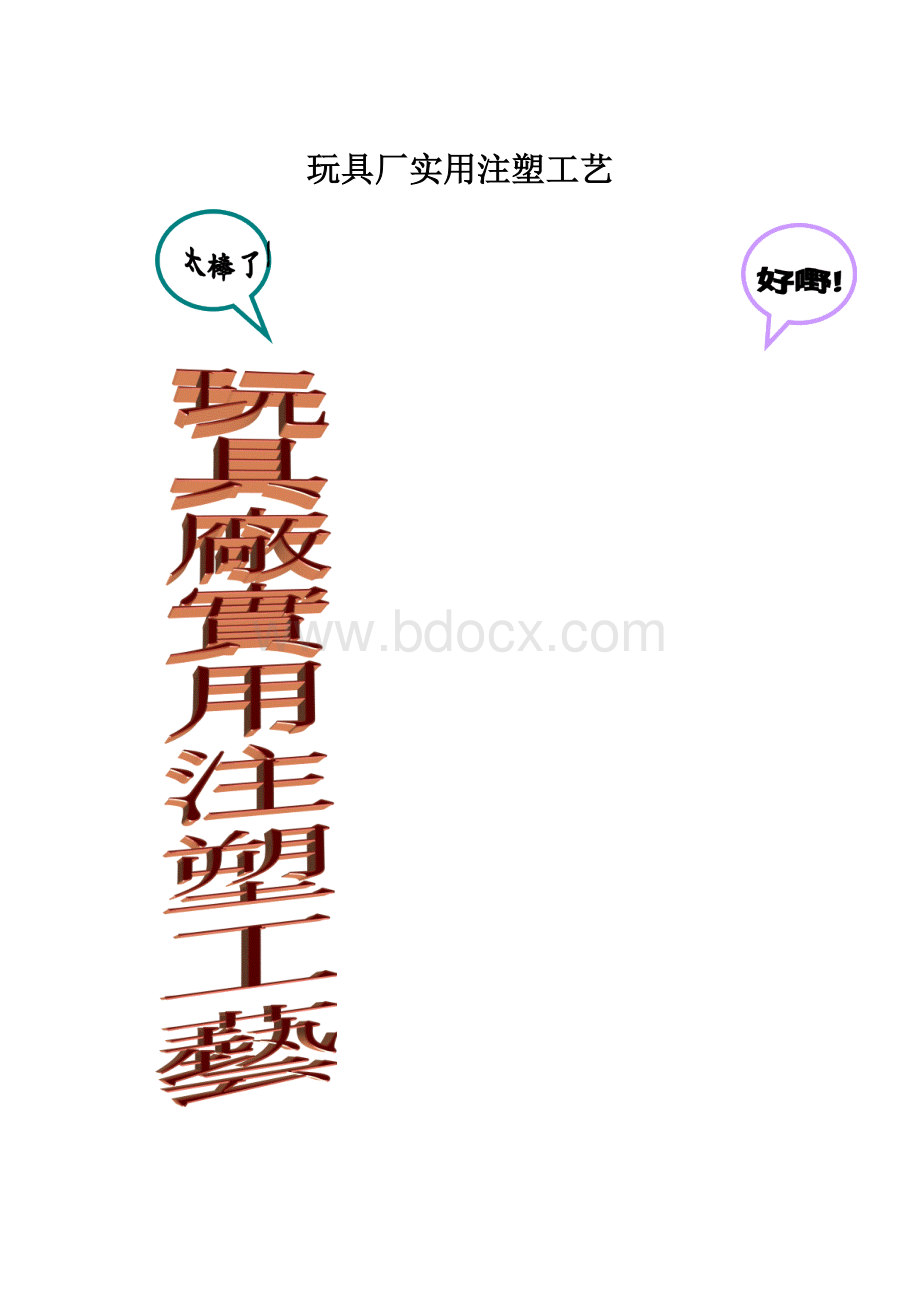
玩具厂实用注塑工艺
玩具廠
用注塑工藝
內容簡介
此書的實用性強,道理深入淺出,是所有硬件玩具工程人員必讀的基礎課程!
待此介紹給工程部各同事!
梁文先生
二○○二五月
第一章注塑工藝探討
塑料的原料的不斷發展,塑料產品就用範圍的日益擴大,使超性能、高精度的塑料製品更處於極大的需求之內。
這种需求不斷地把注塑機行業推向更高的科技層。
目前許多廠家所碰到最頭痛問題圍繞產品的品質控制。
影響塑料製品品質的因素包括塑原料、注塑機、輔助生產設備以及生產環境等等。
但最主要的是操作應用這些設備的工藝調整技術人員。
一個優秀的工藝師往往能夠在較差的條件下,利用較差的設備製出优質的製品。
在此就自已的工作經驗、體會,談談注塑工藝問題。
注塑過程是溶膠筒內熔融塑料以高壓力、高速注射入模腔內,整個注塑過程受許多方面因素影響,如注塑壓力、螺絲向前推進速度、塑料溫度、模腔表壁溫度、模腔形狀、射咀及流道內柵、模具彈性變形、塑料特性、塑化情況等等。
這許多因素每個都同樣重要,單個因素不能獨立決定塑件製品的質素。
因此可以講塑件品質是多變量的函數。
因此不了解這些可變因素對產品品質的影響,不懂變更或盲目的變更這些可變因素,很難製成優良質素的塑件。
然而最能反映許多多因素的相互協調作用的是模腔內塑料的壓力及流向動態。
因此正確的控制模腔壓力及流向動態,就能蕕得最佳的腔內膠料融熔溫度,是確保產品質量的關鍵因素。
第二章何謂模腔壓力
融熔塑料在模腔內流動所需的壓力實質上是塑料流動時要克服的阻力,這些阻力主要來自塑料與模臂間的磨擦力、塑料各層流間的磨擦力、因此模腔壓力與塑料本身粘度特性、料溫、剪切速率、模具溫度、模腔厚度、模腔形狀、注射速率等有關。
在特定的模具、模溫、塑料、料溫條件下,模腔壓力的大小決定於塑料的模腔內流動狀態,即決定於注射螺桿的推進速度。
第三章模腔壓力與鎖模力的關係
注塑過程中,模腔內各點的壓力存在壓力差,設Fcp為模腔的平均壓力。
模腔的平均壓力可通過模腔壓力—流長比曲線以及代表膠料流動性的粘度系數a計算得出。
則鎖模力Fcm>FcpXS,式中S為製成品在模板方向上的投影面積。
下表介紹一組適用於聚烯烴(PE、PP、PS、ABS、SAN等)注射過程所需的壓力值。
工件平均斷面厚度
模腔壓力(公斤/厘米2或磅力/吋2)
流徑長度與斷面厚度之比
毫米
吋
200:
1
150:
1
125:
1
100:
1
50:
1
1.02
0.04
—
9960
9000
7200
4500
—
706
633
506
316
1.52
0.06
12000
8500
6000
4500
3000
844
598
422
316
211
2.03
0.08
9000
6000
4500
2800
2500
633
422
316
267
176
2.54
0.10
7000
4500
3500
3000
2500
492
316
246
211
176
3.05
0.12
5000
4000
3100
3000
2500
352
281
218
211
176
3.56
0.14
4500
3500
3100
3000
2500
316
246
218
211
176
由上表可知模腔厚度及流動長度對模腔壓力影響極大。
上表對我們做工模設計、選擇機器時機為有益。
例某廠生產一週轉箱,產品尺寸約700X500X250mm,產品厚度約2.5mm。
如果製造模具等採用單一的中點入水口(參看圖1),則流動長度約為670mm,則流徑長度與斷面厚度比約670÷2.5=270,因需極大的模腔壓力及鎖模力,極難注塑成型。
但該模具設計時由八個熱流道口注射(如圖2),這樣流徑長度與壁厚比約為150:
1(故所需鎖模力為70cmX50cmX246kg/c㎡=860噸,該廠使用震雄JM–1000生產,試模時,很順利生產出產品)(據上表查得平均模腔壓力只需246Kg/cm2)。
模腔壓力與注射缸的注射壓力(參看圖1)
設模腔壓力P3。
一般注塑機P3是反映不出來的,注塑機壓力表所反映的壓力為液壓缸壓力P1,而P2由注塑機本身特性決定,P2=S1xP1/S2(S1,為注射缸活塞面積,S2為螺桿裁面積)、P3取決於充填過程中,塑料在模腔所受的阻力。
一般注塑機采用一個注射速度注射,這時模腔壓力的最大值由注射壓力控制。
在注射過程中,螺桿的推進速度由所設定的注射速度決定,模腔壓力亦隨螺桿的推進而增高,當所設定的注射壓力不足以克服模腔壓力時,注射溢流閥排油,注射速度減慢。
因此若要提高注射過程末端的注射速度,應提高液壓缸的注射壓力。
但過高的注射壓力易使工模披開,產生飛邊(披鋒)。
更由於在注射過程中每一階段注射速度不能隨意控制,故制成品的表面不能控制到最佳效果。
第四章流向動態與產品壁厚之關係
我們在注射厚壁產品時,細小入水口會使產品表面出現“蛇形”紋(參看圖2),經多種方式的調整极難消除。
蛇形紋實質是塑料在該模腔內的流向,由於注射入口小,塑料以极快的速度沖入,料以蛇形沖入模腔前壁及流到後面填滿,故表面有蛇形紋以夾水紋。
若塑料以極慢的速度注入,則塑料的流向形成層流,克服蛇形紋,但由於速度慢,表面會出現波紋(如圖3)。
最佳方法為加大水口,大多采用多段的注射速度及增加模溫,若入水口大,則蛇形紋會消失,但會存在其他問題,如圖所示,大入水口,若以極快的速度注射,塑料先填滿前段及后段,兩膠流在中間結合,形成鬚表夾水紋,同時若以快速注射,在入水口的死角位由於產生渦流,死角位的氣體不能由排氣孔排出,使產品有空氣泡,透明時可看到,解決方法與上同。
第五章流向動態與模溫的關係
模壁低溫時,同一注射速度,塑料在模壁表面的流動短,中層流動長,即表壁與中層間塑料的流速梯度大;反之模溫高,速度梯度小。
流向動能的變化注塑機中較易觀察,變色注塑機就是利用塑料在模腔內的流向形狀而制成變色花紋,同一注射速度,同一料溫,不同的模溫有不同的流向,因此形成不同的花紋。
第六章流向動態與模溫的關系
注塑過程中,工模模腔壓力P3隨著膠料的推進而變化,模腔壓力P3隨注射時間T的變化曲線,如圖6所示,不同的注塑工藝具有不同的壓力曲線圖。
壓力曲線大致分四段:
(一)充填階段,
(二)施壓階段,(三)保壓階段,(四)冷卻階段。
(1)、充填階段
在這階段,模腔壓力就是熔融塑料在注入模腔時之反抗壓力,主要是由注射過程中熔融塑料與模腔內壁的磨擦阻力、熔融塑料各層流間的磨擦阻力所產生。
在相同的模腔內,這些阻力受塑料溫度、模具內壁溫度及塑料的流向動態等所影響,而模腔內塑料的熔融溫度亦受其流速所影響。
塑膠制品表面光滑的質量完全決定於此。
在充填過程中模腔壓力及塑料流向曲線、模溫及料溫對制成品之表面光滑度起決定性的作用。
傳統的注塑機一般以一級注射速度、壓力、以及二級保壓壓力組成,在充填階段,只有一個注射速度及注射壓力來完成整個充填過程。
較快速充填時,其模腔壓界曲線如OA2線。
充填過程中最大模腔壓力被注射壓力所局限,當模腔的反抗力低於注射壓力所產生的推力時,塑料的流動速度以所設定的注射速度推進。
當反抗力大於推力時,流動速度減低,使其反抗力與注射力平衡。
因此其模腔壓力曲線與正碓的模腔壓力工藝曲線相距較大。
用過快的速度充填容易使充填過程中的模腔壓力過高,使模具產生過大的彈力變形,而產生飛邊或損壞模具。
同時亦會因不能及時排氣而使產品燒焦。
一些較厚身的製品會因過快的充填速度而產生注射口附近之射紋或夾水紋。
若以慢速充填,往往使產品難於成型或使其表面產生波紋線。
(2)、施壓階段
充填後,膠料由於模腔壓力的增加而受壓迫,在這階段,於极短時間內,模腔壓力直線上升,而模腔壓力的最高值完全依靠注射壓力。
最高的模腔壓力是生產一完美形態產品的主要因素。
若壓力太高,會產生飛邊,導致分界線離開及損毀模具,或由於施壓壓力過高增加產品內的應力,使產品變形。
若壓力過低,產品便會不成形。
在這兩個階中,我們要注意其中一個事實。
從模腔壓力曲線圖中可看到,施壓階段的模腔壓力大於充填階段的模腔壓力。
但從注射壓力而言,在充填過程中,由於要克服塑料流動的阻力,因此需要較高注射壓力。
若以此注力進入施壓階段,則由於注射壓力直接壓迫塑料施壓,塑料已無流動狀態。
這時往往產生過高的模腔最高壓力值,使產品不符合要求,因此要使模腔壓力達到一定值時,必需降低注射壓力為保壓壓力,保持施壓期間模腔壓力的穩定。
注塑機保壓壓力的起動有如下幾個控制形式:
(1)以行程開關控制螺桿的行程觸動保壓訊號。
以此控制保壓壓力的起動,存在一些缺點——
a.手動調整行程開關位置難調整到正確的位置;
b.由於熔膠筒內膠料溫度不穩定,螺桿計量段的公差,膠圈漏膠量的變動,導致即使是相同的螺桿行程亦注射出不同的膠量;
這種種因素,導致模腔壓力最高值的變動,使產品質量不能得到保證。
(2)以注射開始起計,到一固定時間后開始起動第二級保壓壓力,以時間計量注射量,除時間誤差外,其注射量亦因方向閥、壓力起動,時間誤差、以及上述種種因素,使其注射量不能精確控制。
(3)位置、時間組合式
首先由電子式行程尺調整充填的最終區間,當注射螺桿到這區間之后,到預定的時間間隔之后起動保壓壓力。
由於電子行程尺及電子時間精確,大大減少了保壓壓力起動的公差,提高製成品質量。
(4)注射壓力感應式
首先在注射缸內加裝一注射壓力感應器,由注射感應器觸動保壓壓力的起點。
由電子行程尺預定一充填區間,壓力感應器只有在螺桿完成充填區間之后才起作用。
在注射過程中,到達充填區間之前,降低注射速度,這時注射壓力降低,到施壓期間,感應器起作用。
這時模腔壓力隨注射壓力的上升開而增加,注射壓力開觸動感應器,起動保壓壓力。
(5)保壓階段
在這階段,注射壓力已轉為保壓壓力。
調整保壓壓力把施壓期間的模腔壓力保持穩定,直到水口柵封閉。
熔融塑膠的冷卻導致模腔壓力低跌。
保壓是用來補充容量減縮,以及防止模腔膠料的倒流,直至封關內柵為止。
產品的收縮取決於這階段。
收縮過度,會產生坑或真空氣泡。
此外,塑料制品的結晶狀態亦在此決定,若保壓過度會使產品變曲,故保壓壓力必須調整準確。
(6)冷卻階段
在這階段,腔內壓力不受保壓影響,並隨著塑料產品的冷卻而降低。
腔內壓力降低的速度亦即冷卻速度。
塑料產品的冷卻速度與熔融塑料及模溫的溫度差成正比。
過快的冷卻速度導致制品殘餘應力過大,使產品翹曲變形;增加模溫對減少殘餘應力有較大作用。
第七章注塑製品缺陷及處理方法
(1).飛邊(披鋒)
飛邊(披鋒)是注塑製品——尤其是大型製品——最常見的問題,要解決飛邊問題,首先要對飛邊產生的原因做一分析。
深殼產品的偏芯
公模結合面間隙
平稀度
模板不平衡
.機器鎖模力不足
注塑工藝
若公模的結合面間隙過大引致飛邊,一定要修理工模。
但在不能修理公模的條件下,則可用注塑工藝調整來補救公模之不足,以減少飛邊。
深殼產品的偏芯使注塑過程中塑料單邊行走,縱向受力不平衡,以致單邊不充填滿。
遇此情況,一定要修理模具。
由於公模不平衡或模板不平衡而造成的飛邊往往是單邊飛邊。
這時,把工模左右位置掉轉安裝。
若飛邊位置跟隨左右變動,則可斷定公模不平衡。
若飛邊位置仍然不變,則可斷定模板不平衡,這時則要修理工模或調整機器模板的平衡度,又或可加墊片試行注塑,檢查效果。
鎖模力不足往往反映產品全面飛邊(工模披開),這情況則要加大鎖模力,或改用較大鎖模力的機器。
但在特定工模、特定設備條件下,產品的好壞決定於注塑工藝的調整,亦即注塑過程中的模腔壓力曲線,為解決飛邊問題,要減低注射過程中平均模腔壓力,而注射速度對模腔壓力起決定性的作用。
在此對注射速度快慢對產品的影響作一分析:
注射速度快,流動長充大,能製成大面積,但隨著速度的增加,其模腔壓力隨之而提高,因此對模具需施加更大的鎖模力。
若鎖模力足夠強大,公模各面厚度均一,則可生產優良產品。
大家應注意的是——
(1)過快的注射速度,造成過大的模腔壓力,若鎖模力不足,將造成產品飛邊。
(2)由於模具壁厚不均勻,所造成充填不平衡,與注射速度的關係較大。
深殼產品公模,很難保證工模四周的壁厚絕對同一,壁厚之間有一定的公差。
注射速度越快,則由於模壁壁厚的不均勻,四周的流動長度差別越大(參看圖8)。
流動長度的不平衡使工模受到不平衡的縱向力,更促成工模的偏芯,結果造成壁厚的更大偏差,使產品單邊飛邊,另一邊不能填滿。
反之,注射速度較慢,雖然壁厚有一定的公差,但其周圍的流動長度仍可能大致相等。
但過慢的注射速度,使大型產品很難成型,因此,這時要適當地增加料溫、模溫,同時,采作快、慢、低壓力的注射形式成型,亦即其注射速度率隨成型面積的增大而減
低。
這類注射工藝問題,在生產水桶及面盆時又經常發生。
2.產品縮水
縮水是由於塑料熱脹冷縮所致,這种現象往往產生於制品柱位、拉筋、或厚壁制品。
現分機种情況分析:
(1).薄壁但有加強筋或柱位的產品——解決縮水的唯一方法是減低塑料溫度、增加注射保壓壓力、減低注射速度。
減低注射速度的目的是降低塑料在模腔內的溫度。
(2).不透明的厚身產品——這類產品只要求表面不縮水,故需模溫低,因低模溫使產品表面很快冷卻、定形,使產品表面不縮水,而內部縮水產生真空泡,不影響外觀,亦可以減少冷卻時間,在產品未縮水前,取出產品,浸入冷水,使表面盡快冷卻定型。
(3).透明厚身產品——這類產品由於厚身,要求內外部都不可縮水,解決方法為降低料溫、增加注射及保壓壓力,加大入水口以延長封柵時間,慢速注射,避免塑料升溫,使流線成層流型,防止過流產生氣泡。
此外,還可增加模溫、增加塑料的流動性、延長保壓壓力施加的時間。
3.產品變形
產品的變形是由於制成品的殘餘應力所致。
若要減少產品變形,只需降低產品的殘餘應力,除公模設計存在的問題之外,工藝上一般採用如下步驟:
尺可能減低注射過程中的模腔壓力,因此要減低注射速度。
降低保壓壓力,增加料溫,增加模溫以延長冷卻時間,減少殘餘應力、精密的注射製品,對產品的變形量要求極高,可對公模的兩邊給予不同的模溫控制,使由於產品壁厚兩邊冷卻速度不同而產生的內應力與注射所產生的殘餘應力相抵消,使產品不變形。
4.水花紋
產品有水花紋,是由於塑料包含有過量水份,塑料熔融時,水份蒸發成水氣泡,混在塑料熔體內,在高壓力注射時,水氣泡破開裂,表面形成水花紋。
解決方法:
用焗爐烘干塑膠粒,或用排氣式注塑機,預塑過程中增加背壓。
5.入水口的射紋
注射起動過快,使模腔前段的空氣不能被膠料融體壓迫排出,空氣混合在膠料內形成射紋。
一般若採用以極慢速度充填流道、水口、及部份模腔,再逐漸速增速度注射,可消除現象。
6.夾水紋
模腔內兩股塑料流相碰,由於此時塑料流端面處於較冷凝狀態,使結合面留有相交線痕跡。
促使夾水紋產生的因素有二,現分述如下:
其一,是由公模產品本身所致。
(如圖9)所示產品有孔位,因此在孔之前端肯定有結合線。
提高塑料、模的溫度,加快注射速度,使兩股塑料流結合時過快的注射速度,往往使模腔內的空氣來不及排出,產生高壓氣體,使結合后更加明顯,或把塑料燒焦,因此,加大排氣孔,及在注射末端用慢速注射,有助於排氣,使結合減少。
其二,是由於產品設計不良或工藝不良所造成,(如圖10)中盒狀產品,底面較邊薄,注射過程中,塑料沿邊的流動多於底部,因此在邊緣先結合,而低部空洞地方因空氣排不出,產品明顯地有結合紋,塑料甚至不能充填其位,或至燒焦。
用末端較慢速度注射,以注射滿,但亦有明顯的夾水紋。
更改產品設計,邊緣部份較底部薄,因此,塑料先填滿底部才填滿邊緣,這樣,在底部無夾水紋,在邊緣只產生不明顯的夾水紋。
工藝上應注意的是:
過快的注射速度,由於邊緣膠料流動方向沒有突變,沿底部部份膠流方向有90°彎角形成阻力大。
過快的注射速度使產品底有孔,成夾水紋。
對這類產品一般采用快,慢的注射工藝解決夾水紋間題。
對於厚身產品(如圖11),為避免產品有夾水紋,對注射速度采用由慢漸快的注射工藝來解決。
7).燒焦的產生,一是由於流向的結合線不在結合面,使模腔內產生高壓氣體,同時,注射速度快,以致塑料燒焦。
又或是產品的柱位、槽位於充填時氣體不能排出所致。
解決方法,從工藝上盡可能使塑膠流結合在結合面上,氣體從結合面的排氣線排出。
在中央的結合處,一般利用頂針作排氣,工藝上要求塑膠流結合前降低注射速度,使有充份時間排氣。
(8).氣泡
厚身透明產品往往在產品中央有氣泡。
首先,對氣泡產生的原因作一分析。
氣泡本身有兩種,一為氣泡,二為真空泡。
氣泡的產生是由於注射速度過快,塑膠流不能把模腔內的空氣全部壓迫從排氣線排出,使空氣混入塑料內形成氣炮,因此,用慢、快、慢的注射速度可避免氣泡的產生。
另一种氣泡為真空泡,真空泡的產生是由於厚身塑料制品冷卻時收縮,而模腔表壁較冷,產品外壁不能縮水,中央縮水,形成真空泡。
生產時,我們往往發現,剛出模的熱產品中央光潔無泡,但過了一段時間,空泡出現,並隨塑料的冷卻而逐步擴大。
解決辦法:
降低料溫,增加模溫,加大水口,降低注射速度,增加注射保壓壓力,延長保壓時間。
9.水波紋
生產透明制品往往於制品表面有水波紋或彩虹紋,其產生的原因是由於模溫低,注塑慢所致。
解決辦法:
增加模溫、增加料溫及加注射速度。
10.產品的穩定性
在注射過程中,產品的穩定性取決於注射過程中模腔壓力曲線的穩定性。
為取得的模腔壓力曲線,最佳方法為採用閉環式注射控制系統,我們可根據工藝所需取得穩定的模腔壓力曲線。
對普通控制系統注塑機,如何得到較穩定的模腔壓力曲線,是我們所要探討的問題之一。
在注射過程中,影響模腔壓力曲線的主要因素有幾點:
其一,塑料溫度的穩定性。
注塑機需要有一個準確、控制靈後的料筒溫度控制系統,同時亦要確保塑料在料筒內有相同的受熱時間,受熱時間的穩定性取決於循環時間的穩定,因此用機械手生產較人工操作穩定得多。
另外,注塑機螺桿參數及注塑機的性能,亦會影響塑膠製品的穩定性。
其二,機器的穩定性。
注射速度、壓力的穩定性除機器性能之外,油溫影響較大。
因此,附加油箱的恆溫系統對產品的穩定性有一定的幫助。
例如溢流閥的工作,由於油溫升溫20℃,則所設定的排油壓力會降低約3kg/cm2。
其三,模溫的穩定性。
模溫對產品質量影響較大。
開始生產時,模溫由冷凍狀態升溫,因此,這時的塑料制品處於不穩定狀能。
當模具由塑料所吸收的熱量與模具運水所帶走的熱量達到熱平衡狀態后,產品才能達到穩定。
因此,一般清密注射,附加模溫控制系統,除工藝需要一定的模溫控制之外,亦可預先提高模溫,減少注塑初期的废品率。
其四,原料性能的穩定性。
不同牌號的同一類膠料,具有不同的特性,因此,原料牌號的更換,對產品質量具有巨大的影響,在工藝上需作重新的調整。
在生產過程中需要處理澆注口廢料,許多廢料可混入新料中使用,因此,新舊料混料的配匹都要一定的比例使用(一般15至20%舊料),才能達到產品穩定。
注塑成型缺點的成因及解決方法
不正確的操作條件,損壞的機器及工模會產生很多成型缺點,以后數頁資料提供了一些解決的方法.
為減少停機的時間,及能盡快找出操作問題的原因,操作人員應把所有最好的注塑成型條件記錄在附加於說明中的“注塑成型和條件記錄表”上,以供日后解決注塑機問題時參考之用。
按本公司所知,此手冊所提供的資料是精確的,但對於手冊中的資料的準確性及完整性,震雄機器廠有限公司並不承擔任何責任,使用這手冊的人仕應自行決定資料的可用性
A成品不完整
故障原因處理方法
塑料溫度太低提高熔膠筒溫度
射膠壓力太低提高射膠壓力
射膠量不夠增多射膠量
澆道杯司空(SPRUEBUSHING)重新調整其配合
射咀之配合不正,塑料溢漏
射膠時間太短增加射膠時間
射膠速度太慢加快射膠速度
枕壓調整不當重新調節
模具溫度太低提高模具溫度
模具溫度不勻重調模具水管
模具排氣不良恰當位置加適度之排氣孔
射咀溫度太低提高射咀溫度
進膠不平均重開模具溢口位置
澆道或溢口太小加大澆道或溢口
塑膠內潤滑劑不夠增加加潤滑劑
背壓不足稍增背壓
過膠圈,螺