油缸和液压系统设计说明和计算DOC.docx
《油缸和液压系统设计说明和计算DOC.docx》由会员分享,可在线阅读,更多相关《油缸和液压系统设计说明和计算DOC.docx(13页珍藏版)》请在冰豆网上搜索。
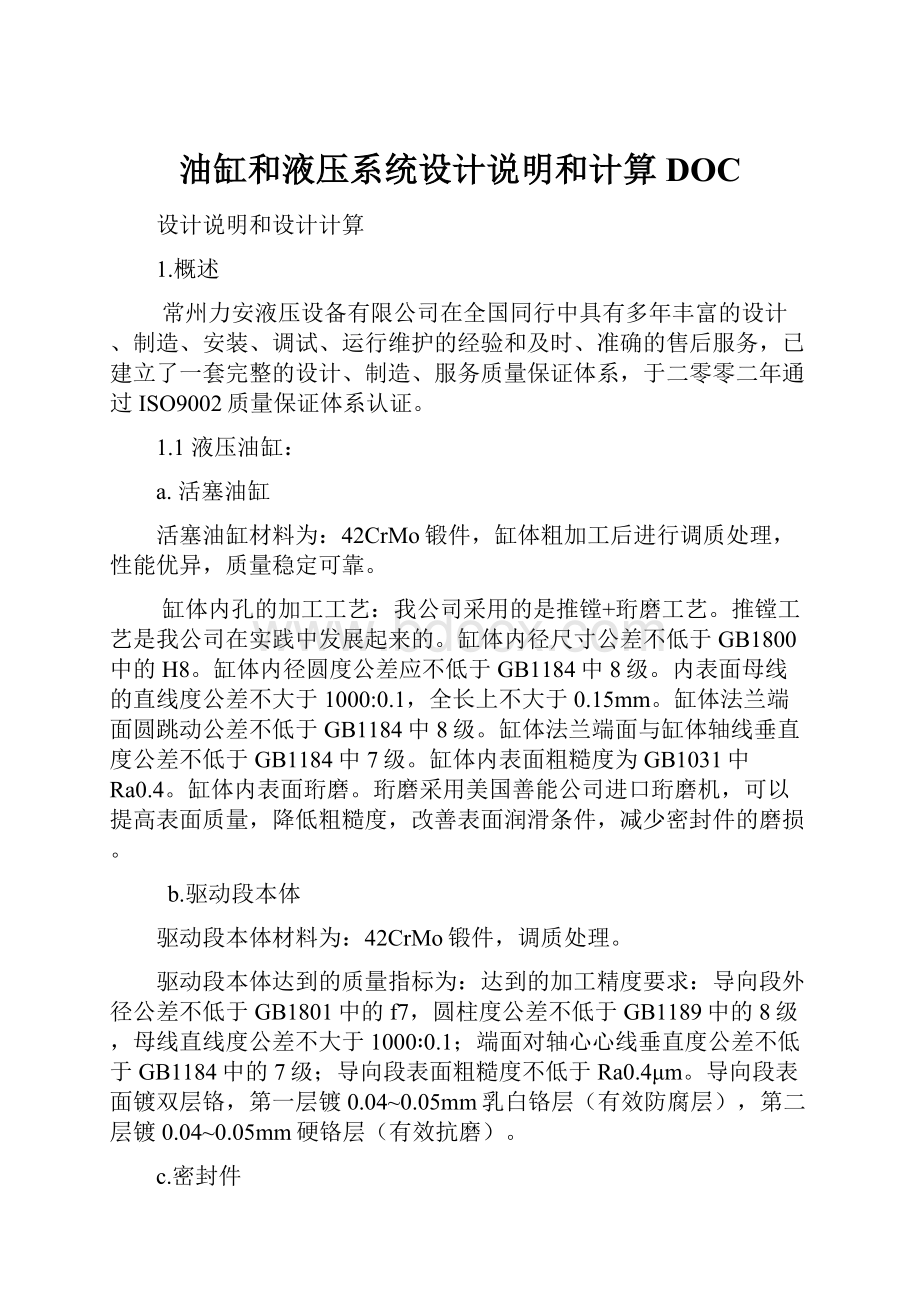
油缸和液压系统设计说明和计算DOC
设计说明和设计计算
1.概述
常州力安液压设备有限公司在全国同行中具有多年丰富的设计、制造、安装、调试、运行维护的经验和及时、准确的售后服务,已建立了一套完整的设计、制造、服务质量保证体系,于二零零二年通过ISO9002质量保证体系认证。
1.1液压油缸:
a.活塞油缸
活塞油缸材料为:
42CrMo锻件,缸体粗加工后进行调质处理,性能优异,质量稳定可靠。
缸体内孔的加工工艺:
我公司采用的是推镗+珩磨工艺。
推镗工艺是我公司在实践中发展起来的。
缸体内径尺寸公差不低于GB1800中的H8。
缸体内径圆度公差应不低于GB1184中8级。
内表面母线的直线度公差不大于1000:
0.1,全长上不大于0.15mm。
缸体法兰端面圆跳动公差不低于GB1184中8级。
缸体法兰端面与缸体轴线垂直度公差不低于GB1184中7级。
缸体内表面粗糙度为GB1031中Ra0.4。
缸体内表面珩磨。
珩磨采用美国善能公司进口珩磨机,可以提高表面质量,降低粗糙度,改善表面润滑条件,减少密封件的磨损。
b.驱动段本体
驱动段本体材料为:
42CrMo锻件,调质处理。
驱动段本体达到的质量指标为:
达到的加工精度要求:
导向段外径公差不低于GB1801中的f7,圆柱度公差不低于GB1189中的8级,母线直线度公差不大于1000∶0.1;端面对轴心心线垂直度公差不低于GB1184中的7级;导向段表面粗糙度不低于Ra0.4μm。
导向段表面镀双层铬,第一层镀0.04~0.05mm乳白铬层(有效防腐层),第二层镀0.04~0.05mm硬铬层(有效抗磨)。
c.密封件
油缸各固定密封部位选用材料为耐油橡胶的O形密封圈,其胶料硬度、间隙大小及沟槽尺寸均从GB1236中选取。
油缸的动密封在高压40MPa,低压0.5MPa时均有良好的密封性能和较低的启动压力,油缸内部的动密封件均采用MERKEL密封圈,耐久性好,无论高压、低压均密封可靠,且启动压力低(<0.5MPa),在工程上广为采用。
静密封件采用PARKER公司生产的O形密封圈。
油缸的动密封件有足够的抗撕裂强度,耐压32MPa并应具有耐油、防水、永久变形小、摩阻力小、无粘着、抗老化等良好性能。
这些密封件的耐压性都在32MPa以上,保证使用寿命大于10年以上。
d.驱动段底盖、活塞油缸底盖
材料为:
42CrMo锻件,调质处理。
缸盖与相关件配合处的圆柱度公差应不低于GB1184中8级,同轴度公差应不低于7级,缸盖与缸体配合的端面与缸盖轴线垂直度公差不低于GB1184中7级,端面圆跳动公差不低于GB1184中7级。
e.导向带
导向带材料采用德国知名品牌MERKEL公司的复合材料,导向面配合尺寸公差不低于GB1800中的H8与GB1801中f7,导向面、配合面的圆柱度公差不低于GB1184中8级,导向面与配合面的同轴度公差不低于GB1184中8级,导向面粗糙度不低于GB1031中Ra0.4。
f.驱动段后膨胀管
驱动段后膨胀管材料:
304,螺纹T460X16和YS420X16采用GB197中精度等级7A。
2设计计算
2.1液压缸计算
1)活塞油缸产生推力计算
计算输入
试验压力
Py=
31.5MPa
缸径
D=
605mm
杆径
d=
430mm
计算公式
Fmax=Py*【π·(D2-d2)】/4
计算结果
推力(试验压力下)
Fmax=
4481KN
2)驱动段本体产生推力计算
计算输入
试验压力
Py=
30MPa
缸径
D=
340mm
计算公式
Fmax=Py·(π·D2)/4
计算结果
推力(试验压力下)
Fmax=
2723.8KN
3)活塞油缸壁厚计算
计算输入
缸体材料
42CrMo锻件
缸体屈服强度
σS≥
550MPa
材料安全系数
n=
2.5
缸体许用应力
〔σ〕≤
220MPa
缸内最大压力:
Pmax=
31.5MPa
缸径
D=
605mm
计算公式
δ=PmaxD/【2·〔σ〕】
按薄壁公式计算
计算结果
缸体要求最小壁厚
δ=
43.3mm
备注
选择原材料为Φ715×65mm。
加工后,缸体净壁厚为50mm。
4)驱动段本体壁厚计算
计算输入
驱动段本体材料
42CrMo锻件
驱动段本体材料的屈服强度
σS≥
550MPa
材料安全系数
n=
2.5
缸体许用应力
〔σ〕≤
220MPa
缸内最大压力:
Pmax=
30MPa
缸径
D=
340mm
计算公式
δ=PmaxD/【2·〔σ〕】
按薄壁公式计算
计算结果
缸体要求最小壁厚
δ=
23.2mm
备注
选择原材料为Φ445×60mm。
加工后,缸体净壁厚为40~45mm。
5)活塞缸体强度校核
计算输入
缸内最大压力
P=
31.5MPa
缸径
D=
605mm
杆径
d=
430mm
缸体中心直径
D1=
655mm
缸体壁厚
δ=
50mm
计算公式
σzh1=(σz12+σh12-σz1σh1)0.5
σz1=P(D2-d2)/4D1δ
σh1=PD1/2δ
计算结果
纵向应力
σz1=
43.55MPa
环向应力
σh1=
206.3MPa
合成应力
σzh1=
188.36MPa
缸体许用应力
〔σ〕≤
220MPa
计算结论
σzh1<〔σ〕,强度满足要求
6)驱动段本体强度校核
计算输入
缸内最大压力
P=
30MPa
缸径
D=
340mm
杆径
d=
0mm
缸体中心直径
D1=
380mm
缸体壁厚
δ=
40mm
计算公式
σzh1=(σz12+σh12-σz1σh1)0.5
σz1=P(D2-d2)/4D1δ
σh1=PD1/2δ
计算结果
纵向应力
σz1=
57MPa
环向应力
σh1=
142.5MPa
合成应力
σzh1=
124.23MPa
缸体许用应力
〔σ〕≤
220MPa
计算结论
σzh1<〔σ〕,强度满足要求
7)拉杆强度校核
计算输入
拉杆材料
40Cr
拉杆屈服强度
σS≥
540MPa
拉杆螺纹
M80×3
拉杆最危险断面:
退刀槽
do=
75.6mm
拉杆所承受的拉力
F1=
4481kN
拉杆数量
n
4
计算公式
σ=F1/(n·A)
计算结果
活塞杆最危险截面积
A=
4488.8mm2
活塞杆计算应力
σ=
249.6MPa
活塞杆许用应力
〔σ〕=σS/2.1≤
257.1MPa
计算结论
σ<〔σ〕,强度满足要求
8)法兰承重螺纹计算
计算输入
法兰材料
42CrMo
法兰屈服强度
σS≥
550MPa
螺纹受力不均匀系数
Kz=
0.56
螺纹旋合圈数
Z=L/P=
5
法兰螺纹
T460X16
螺纹内径
d1=
460mm
螺纹牙根宽
b=0.75P=
3mm
螺纹实际高度
H1=0.54P=
2.16mm
螺纹中径
d2=d-0.65P=
137.4mm
活塞杆所承受的拉力
F1=
800kN
计算公式
τ=F1/(Kzπd1bZ)
σw=3F1H1/(Kzπd1b2Z)
σp=F1/(Kzπd2H1Z)
计算结果
螺纹计算剪应力
τ=
28.0MPa
螺纹许用剪应力
〔τ〕=0.2σs≥
56MPa
螺纹计算弯应力
σw=
52.2MPa
螺纹许用弯应力
〔σw〕=0.4σs≥
112MPa
螺纹计算挤压应力
σp=
44.5MPa
螺纹许用挤压应力
〔σp〕=0.62σs≥
173.6MPa
计算结论
强度满足要求
9)油缸底盖连接螺钉计算
计算输入
螺钉型号
M27×10012.9级
螺钉屈服强度
σS≥
970MPa
螺钉所承受的力
F1=
4481kN
螺钉预紧力系数
K1=
1.3
螺钉最小内径
d0=
23.75mm
螺钉数量
z=
32
计算公式
σ=4F1K1/(πzd02)
计算结果
螺钉计算应力
σ=
410.9MPa
螺钉许用应力
〔σ〕=σs/2.25
431.1MPa
计算结论
σ<〔σ〕,强度满足要求
备注
油缸底盖螺钉布置圆直径为Φ655mm,共布置32个M27×100的螺钉,12.9级。
10)驱动段底盖连接螺钉计算
计算输入
螺钉型号
M20×10012.9级
螺钉屈服强度
σS≥
970MPa
螺钉所承受的力
F1=
2723.8kN
螺钉预紧力系数
K1=
1.3
螺钉最小内径
d0=
17.3mm
螺钉数量
z=
36
计算公式
σ=4F1K1/(πzd02)
计算结果
螺钉计算应力
σ=
418.4MPa
螺钉许用应力
〔σ〕=σs/2.25
431.1MPa
计算结论
σ<〔σ〕,强度满足要求
备注
油缸底盖螺钉布置圆直径为Φ380mm,共布置36个M20×90的螺钉,12.9级。
2.2液压系统计算
1)系统最高工作压力、最大工作流量,电机功率的计算
计算输入
系统最高压力
P1=
31.5MPa
系统压力损耗系数
n1=
1.05
系统最大流量
Q1=
12L/min
系统的泄漏系数
K=
1.05
电机转速
n=
1465r/min
油泵电机组效率
η=
0.88
计算公式
P=n1P1
Q=KQ1
Qv=Q/n
N=P·Q/(60η)
计算结果
系统最高工作压力
P=
15.3MPa
系统最大工作流量
Q=
2X28.9L/min
油泵最小排量
Qv=
39.4ml/rev
电机最小功率
N=
15.4kW
计算结论
油泵选用国产品牌,型号为A4VSO,其公称排量为46ml/r,压力等级为35MPa
因本工程海拔因素,电机功率考虑换算系数0.85,选用ABB公司产品,电机型号为QA180L4A-B3522KW1465rpm。
本系统选用两套油泵-电机组,,一台工作,一台备用。
2)
油箱容积的计算
计算输入
油泵流量的4倍
V1=
191L
油缸无杆腔容积
V2=
1093L
计算公式
V=1.1×(V1+V2)
计算结果
油箱需要的容积
V=
1413L
计算结论
考虑到油箱结构上本身所需的空油面与吸油高度,按照液压泵站油箱公称容量系列的规定,选定油箱液压泵站的油箱容积为1600L。
3)液压系统管路管径的设计计算
计算输入
油管内径
d
mm
工作流量
Q
L/min
允许流速
V
m/s
油管最大工作压力
Pg
MPa
油管许用应力
〔σ〕
MPa
计算公式
d=4.63(Q/V)0.5
δ1≥(Pg×d)/(2×〔σ〕)
计算结论
经计算,同时考虑到各个油管所承受的压力,因此:
有杆腔管路选用Φ27×3;
无杆腔管路选用Φ27×3;
控制油管路选用Φ18×2;
泄漏油管路选用Φ18×2。
备注
选用不锈钢无缝钢管和接头,为减失少压力损和压力冲击,管道系统所有弯头均采用自然冷弯成形弯头。