一般管螺纹滚压装置的设计仿真及受力分析综述Word格式.docx
《一般管螺纹滚压装置的设计仿真及受力分析综述Word格式.docx》由会员分享,可在线阅读,更多相关《一般管螺纹滚压装置的设计仿真及受力分析综述Word格式.docx(35页珍藏版)》请在冰豆网上搜索。
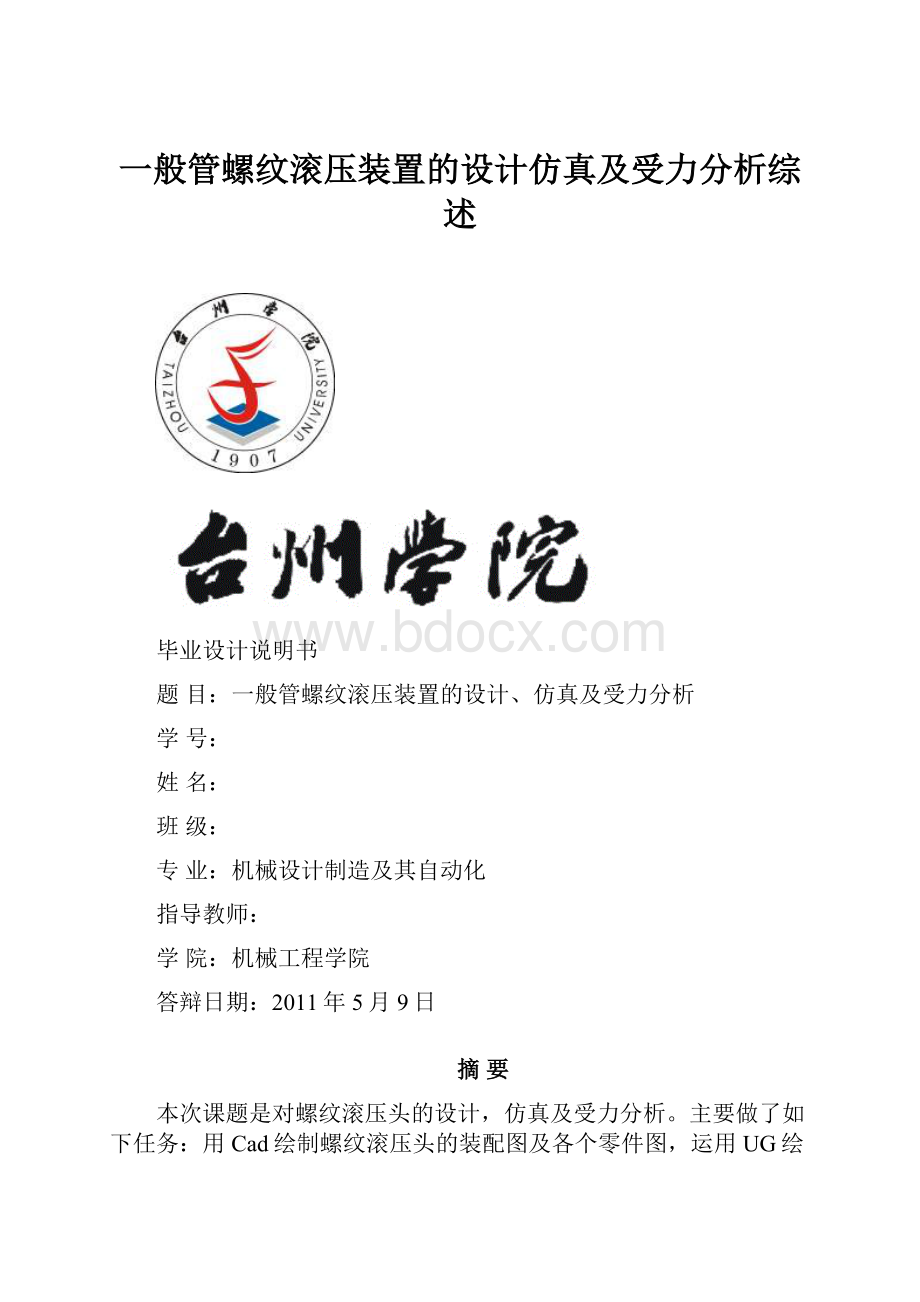
随着国内外航空、航天、汽车及械工业的迅速发展,各类螺纹零件的需求量日益增加。
根据报告:
1998年至2004年期间,美国紧固件需求量从1998年的92亿美元提升到112亿美元,是最大的紧固件消费国;
其次是欧洲,主要是西欧,从1998年的83亿美元一直提升到117亿美元;
第三就是中国,从1998年的20亿美元提升到2004年37亿美元。
在未来的几年中,中国的紧固件消费还会继续增长,每年将增长12.4%和亚洲其它国家增长率8.5%相比,中国紧固件需求的增长在全世界排行榜列第一名。
螺纹成形是一种非线性大变形过程,受力情况比较复杂,以及滚压过程中许多因素的不确定性,对于螺纹的冷滚压加工,尤其是对螺纹冷滚压参数的确定。
由于各种各样误差因素的存在,有时滚压螺纹零件会产生某种缺陷,甚至会产生废品。
为了得出各种参数对滚压螺纹质量的影响,并为冷滚压工艺提供最佳参数,必须分析其产生缺陷的原因来找到解决问题的方法。
从而能够有效地指导生产实践,促进冷滚压成形设备和成形技术的推广和应用。
通过本次毕业设计,得到如下锻炼:
1)通过绘制装置的装配图和非标零件图,提高了一般机械装置的设计能力。
2)运用机械制造基础、机械设计及其它有关课程的知识基础,在编制装置的主要零件加工工艺规程中,进一步提高了编制零件加工工艺的能力。
3)借助于相关计算机软件,建立三维图形及数模,并进行运动仿真及受力分析,便于装置的装配与调试,加强了对CAD/CAM应用软件的熟练使用。
综上所述,通过本次毕业设计不仅巩固了以往所学的专业知识,并且提高了
独自解决问题的能力,为毕业后工作打下了良好的基础,得到了一份宝贵的经验财富,对以后的发展具有重要的意义。
1.2设计的内容和思路
1)冷滚压螺纹的成形过程及其原理进行分析和研究。
2)绘制装置的装配图和非标零件图。
3)编制装置的主要零件加工工艺规程。
4)借助于UG,DEFORM计算机软件,建立三维运动仿真进行装置的制作与调试以及受力分析。
5)撰写毕业设计说明书。
1.3解决的主要问题
1)尽可能的缓解滚压螺纹的破裂变形。
2)装置装配图和非标零件图的绘制。
3)主要零件加工工艺规程的确定。
4)运功仿真的制作与调试。
第2章螺纹滚压头的总体设计方案
本次毕业设计工作分为以下几部分:
1)在熟悉装置结构的基础上,利用AutoCAD、UG等计算机绘图软件绘制装置的装配图和非标零件图。
2)编制加工工艺规程。
在遵守机械加工工艺规程的设计原则下,分为以下几个步骤:
①分析研究产品的装配图和零件图。
②选择毛坯。
③拟订工艺路线。
④确定各工序所采用的设备。
⑤确定各工序所采用的工艺装备。
⑥确定各主要工序的技术要求及检验方法。
⑦确定各工序的加工余量、工序尺寸和公差。
⑧确定切削用量。
3)通过塑性成型仿真,对一般管螺纹滚压时的径向、切向、轴向滚压力及其关系的分析,对管螺纹的变形破裂问题进行仿真调试。
4)撰写毕业设计说明书。
螺纹滚压头的装配图如2.1所示,装置工作时,由工件通过盖板孔推动调距螺栓,调距螺栓带动滑动盘,控制滑块移动,拨盘解锁,手动扳动拨盘一定角度来卡住滑块保证偏心轴的位置不动,伸出工件,完成加工。
图2.1 螺纹滚压头装配图
第3章主要零件设计
3.1Ug软件介绍
UG全称Unigraphics软件是美国UGS公司(UnigraphicsSolutions)开发的CAD/CAM/CAE计算机辅助设计分析和制造应用软件,是世界三大CAD/CAM/CAE顶级软件之一。
主要应用于汽车、航空航天、机械、造船、电子等工业领域。
UG自1983年入市发展到最新版本为UGNX6。
随着版本的不断更新和功能的不断扩充,UG更扩展了软件的应用范围,面向专业化、智能化发展。
UG软件是一个集成化的CAD/CAM/CAE系统软件,它为工程技术人员提供料非常强大的应用工具,可完成产品的设计、分析、绘制工程图以及数控编程加工等操作。
所谓主模型是指唯一以“电子介质”存在的CAD零件的三维模型数据文件,其它应用文件(如加工、装配、二维绘图和分析等)则通过虚拟装配调用主模型,而不是直接在主模型上进行加工、装配、二维绘图和分析等。
单一数据库:
各模块数据存储在同一个数据库中,保证设计、制造和分析模块中的数据关联。
真正实现了CAD/CAM/CAE等个模块之间的数据交换的自动切换,可实施并行工程。
可保证设计资料的正确性,同时避免反复修改所造成的时间的浪费,提高工作效率。
采用复合建模技术:
可将实体建模、曲面建模和参数化建模融为一体,具有较大的灵活性。
无需草图,直接通过成型特征和特征操作功能完成几何模型的创建。
同时可直接利用实体边缘进行特征操作,不需要定义和参数化新曲线。
交互式操作环境,提高设计人员工作效率
(1)全部界面可根据个人喜好定制;
(2)高品质可伸缩工具条和信息窗口;
(3)方便快捷的右击菜单,可快速访问常用命令;
(4)可直接在窗口中操作对象;
(5)可根据信息提示向导提示或按照顺序进行下一步操作;
(6)基于智慧型操作:
快速选择、判断选择、过滤器选择功能等。
3.2主要零件的设计
图3.1 主盘
主盘如图3.1所示在整个装置体系中属于最重要的部分,它是连接各个部件的核心零件。
它的中心孔为Ф46mm,主要是根据调距螺栓顶板Ф44mm与工件的尺寸26mm来确定它的大小。
倾斜面主要与滚丝轮相接触,保证滚丝轮的角度;
偏心轴与通孔相切,滚丝轮又与偏心轴连接,确定滚丝轮的位置,相互关联来得到他们的尺寸。
三个倾斜面以及倾斜面上的通孔分别为R52+0.5mm和Ф45+0.015mm,倾斜面的角度与工件螺纹配合得到1º
46'。
后面的通孔Ф60+0.022mm主要与连杆连接,根据连杆来确定尺寸。
图3.2 连杆
连杆如图3.2所示用于连接主盘,拨盘,调整盘和滑动盘,起到了轴心的作用,所以连杆用于连接的部位要求精度都非常高。
特别是前面Ф60+0.022mm外圆与Ф97-0.015-0.038mm端面与主盘相连,精度要求尤为重要。
Ф97-0.015-0.038mm外圆与调整盘相连,Ф65-0.018mm与滑动盘相连,尺寸以此来确定。
中间的键槽用于固定滑动螺母,滑动螺母又与滑动盘连接,滑动盘是靠滑动螺母的移动而移动的,两者相互关联。
图3.3 拨盘
拨盘如图3.3所示的中心通孔主要与主盘连接,所以它的尺寸根据主盘来确定为Ф112-0.015-0.038mm。
三个通孔分别用于拨销的定位,尺寸大小为Ф16+0.019mm。
半圆槽用于放置定位块,尺寸为R17+0.10mm与R15.5+0.05mm两个形成的缺角就是用于卡住滑块。
图3.4 调整盘
调整盘如图3.4所示是整个装置运动过程中人工所操控的一个零件,它在装置中不是完全的被固定,是可以有一定角度的旋转,以此来控制滑块的锁紧与张开。
中心孔连接连杆的,尺寸为Ф97+0.036mm,外圆面凹槽主要安放滑块与插八片。
侧面上的凹槽,通过调整螺钉的拧合顶住连杆上的锥螺钉来固定调整盘的位置。
图3.5 滑块
滑块如图3.5所示在整个装置运动过程中启到了很关键的作用。
它主要用来卡住拨盘,保证拨盘的位置,后面的凹槽直接与滑动盘连接,靠滑动盘来带动滑块的移动,以此来控制偏心轴对工件进行加工操作。
它的长度是从主盘,拨盘,调整盘等主要的零件的宽度来确定它的大小。
图3.6 偏心轴
偏心轴如图3.6所示用连接主盘、滚丝轮和盖板,起到了定位的作用。
底部圆柱与主盘相连,尺寸为Ф45-0.015-0.025mm,中间与滚丝轮相连得到尺寸为Ф37-0.01mm,上面与盖板相连确定尺寸为Ф28-0.015-0.025mm,下面的凹槽靠圆柱销连接来定位拨盘的安装位置,圆柱销也限制了偏心轴的转向角度。
偏心轴在装置中起到定位的作用,在整个装置运动过程中,滚丝轮依靠偏心轴来达到中心轴的偏移,对工件进行加工。
第4章主要零件的加工工艺规程
4.1主盘加工工艺
4.1.1零件的主要功用和技术要求
主盘如图4.1所示是管螺纹滚压装置中最主要的一个零件,它是连接各个组件的核心零件。
直接关系着偏心轴的位置及滚丝轮的放置角度。
所以它所要求的精度非常高,尤其和连杆连接的孔。
要求热处理HRC60-64,Ф45+0.015的中心线的距离向尾柄方向渐增,增量为0.15/10mm。
图4.1 主盘
4.1.2选择毛坯
考虑到加工过程中受到载荷不大,因此选用圆钢,零件所要求的配合精度很高所以选用材料为gSiCr,加工过后的零件要进行热处理,以此保证零件的稳固性,工作的可靠性。
主盘的直径上的总余量为5mm,宽度余量为6mm,进给量为0.1mm/r,滚压速度为72~78m/min。
所以选择毛坯尺寸为Ф185×
48。
4.1.3工艺分析
滚压装置的主盘三个倾斜面,三个通孔与工艺通孔都有一定的位置关系。
(1)以Ф180±
0.10mm为中心,包括Ф112
mm的小外圆,Ф60+0.022mm内孔和Ф46mm的通孔以及Ф60+0.022mm的内圆倒角。
(2)以Ф112
mm为中心的,包括Ф180±
0.10mm及Ф180±
0.10mm倒角,Ф46mm内孔倒角。
(3)以Ф12+0.019mm工艺通孔定位6个Ф4±
0.01mm通孔,3个M10×
1.5mm螺纹孔和宽10深8+0.30mm的圆弧槽,它们都垂直于Ф180±
0.10mm平面,根据工艺通孔定位三个倾斜面R52+0.5mm,Ф45+0.015mm通孔,确定它们与平面的角度为1º
45'。
4.1.4基准的选择
定位基面的选择是拟定零件的机械加工路线,确定加工方案中首先要做的重要工作。
基面选择得正确、合理与否,将直接影响工件的加工质量和生产率。
在选择定位基面时,需要同时考虑以下三个问题:
(1)以哪一个表面作为加工时的精基面或统一基准,才能保证加工精度,使整个机械加工工艺过程顺利地进行。
(2)为加工上述精基面或统一基准,应采用哪一个表面作为粗基面?
(3)是否有个别工序为了特殊的加工要求,需要采用统一基准以外的精基面?
粗基准的选择。
对于零件而言,尽可能选择不加工表面为粗基准。
而对有若干个不加工表面的工件,则应以与加工表面要求相对位置精度较高的不加工表面作粗基准。
所以选择Ф180±
0.10mm定为粗基准。
精基准的选择。
主要应该考虑基准重合的问题。
当设计基准与工序基准不重合时,应该进行尺寸换算。
所以选择Ф12+0.019mm工艺通孔作为精基准。
4.1.5工艺规程设计
工艺路线的拟定是制定工艺规程的工体布局,包含确定加工方法,划分加工阶段、决定工序的集中于分散、加工顺序的安排以及安排热处理、检验和其他的辅助加工。
它影响着加工质量和加工质量的高低,影响工人的劳动强度,设备的投资和生产成本等。
工艺路线方案:
工序1:
粗车、半精车大外圆端面,粗车半精车Ф180mm外圆,钻、扩Ф46mm,倒内外角;
工序2:
车60孔,粗车、半精车小外圆端面,粗车、半精车Ф112mm外圆,倒角;
工序3:
钻,扩,铰Ф12mm孔;
工序4:
铣宽10mm深8mm的圆弧槽;
工序5:
钻、铰6-Ф4mm的孔;
工序6:
钻、攻3-M39mm螺纹;
工序7:
分别粗铣、半精铣三个R52mm倾斜面,倒角;
工序8:
钻、扩3-Ф45mm的倾斜孔,倒角;
工序9:
热处理;
工序10:
分别磨三个R52mm倾斜面,磨3-Ф45倾斜孔;
工序11:
磨小外圆端面,磨Ф60mm内孔;
工序12:
终检
4.1.6加工余量,工序尺寸及其公差的确定。
确定加工余量的方法有三种:
经验估计法、查表法和分析计算法,在实际生产中广泛应用查表法。
滚压装置主盘的加工主要是车削和磨削,根据查表可知:
粗车外圆(长度≤200)的加工余量一般为1.5~3㎜;
精车外圆(长度≤200)的加工余量一般为0.8~2㎜;
磨削外圆的加工余量一般为0.1~0.5㎜,各个尺寸如表4.2所示。
表4.2 主要尺寸加工余量,工序尺寸及其公差
加工表面
工序双边余量
工序尺寸及公差
表面粗糙度
粗
精
磨
毛坯
Ф180端面
1.5
1
0.5
47
45.5
44.5
6.3
1.6
Ф180外圆面
185
181
180±
0.10
Ф112端面
0.9
43
42.1+0.2
42
3.2
0.8
Ф112外圆面
116
113.5
112.5+0.2
112
0.4
Ф60内圆面
2.3(钻)
1.3
(车)
0.3(磨)
46
59.7
60+0.022
Ф45内圆面
1.3(扩)
25
44.7+0.15
45+0.015
R52端面
0.3
0.2
1.3+0.2
1.5+0.02
Ф12通孔
11
(钻)
0.85
(扩)
0.15(铰)
11.85
12+0.019
Ф4通孔
3.9(钻)
0.1
(精铰)
3.9
4±
0.01(精铰)
4.1.7确定切削用量及基本工时
工序1:
粗车、半精车大外圆端面,粗车半精车Ф180mm外圆,钻、扩Ф46mm,倒内外角。
(一)粗车大外圆端面
(1)选择刀具
选用93偏头端面车刀,参看《机械制造工艺设计简明手册》车床选用C365L转塔式车床,中心高度210mm。
选择车刀几何形状,前刀面形状为平面带倒棱型,前角=10º
,后角=8º
,主偏角93º
,副偏角k=10º
,刀尖角圆弧半径0.5mm,刃倾角=-10º
。
(2)确定切削用量
1)确定背吃刀量a(即切深a)
粗车的余量为4.5mm由于刀杆截面取最大吃刀深度为6mm所以一次走刀完成即a=4.5mm。
2)确定进给量
查《切削用量简明手册》:
加工材料45钢、车刀刀杆尺寸为16~25、工件直径100mm、切削深度a=4.5mm,则进给量为0.7~1.0。
再根据C365L车床及《机械制造工艺设计简明手册》表4-2-3查取横向进给量取f=0.73mm/r。
3)选择磨钝标准及耐用度
根据《切削用量简明手册》表1.9,取车刀后面最大磨损量为0.8~1.0。
焊接车刀耐用度T=60mm。
4)确定切削速度V
根据《切削用量简明手册》表1.11当用YG6硬质合金车刀加工HT200(182~199HBS),a=4.5mm,f=0.73mm/r,查出V=1.05m/s。
由于实际情况,在车削过程使用条件的改变,根据《切削用量简明手册》表1.28,查得切削速度的修正系数为:
K=1.0,K=1.0,K=0.73,K=(190/HBS)1.25=1.0,KSV=0.85,Kkv=1.0。
则
V=VKKKKKSVKkv
=44m/min
n=140r/min
按C365L车床转速(《机械制造工艺设计简明手册》表4.2-2)选择与140r/min相近似的机床转速n=136r/min,则实际切削速度V=42.7m/min。
5)校验机床功率
车削时功率P可由《切削用量简明手册》表1.25查得:
在上述各条件下切削功率P=1.7~2.0,取2.0。
由于实车削时功率P可由《切削用量简明手册》表1.25查得:
由于实际车削过程使用条件改变,根据《切削用量简明手册》表1.29-2,切削功率修正系数为:
际车削过程使用条件改变,根据《切削用量简明手册》表1.29-2,切削功率修正系数为:
Kkrpc=KkrFc=0.89,Kropc=KroFc=1.0。
则:
P=P×
Kkrpc×
Krop=1.87KW
根据C365L车床当n=136r/min时,车床主轴允许功率PE=7.36KW。
因P<
PEX,故所选的切削用量可在C365L上加工。
6)校验机床进给机构强度
车削时的进给力Ff可由《切削用量手册》查表得Ff=1140N。
由于实际车削过程使用条件的改变,根据《切削用量简明手册》查得车削过程的修正系数:
Kkrf=1.17,Krof=1.0,K=0.75,则
F
=1000N
根据C365L车床说明书(《切削用量简明手册》),进给机构的进给力Fmax=4100N(横向进给)因Ff<
Fmax,,所选的f=0.73进给量可用。
综上,此工步的切削用量为:
a=4.5mm,f=0.73mm,n=136r/min,V=42.7m/min。
(3)计算基本工时:
按《机械制造工艺设计简明手册》公式计算:
L=+L1+L2+L3,由于车削实际端面d1=0,L1=4,L2=2,L3=0,则
L=1002+4+2+0=61mm.
T=61×
1÷
(0.73×
136)=0.61min
(二)半精车大外圆端面
(1)选择刀具:
与粗车100左端面同一把。
(a)确定背吃刀量
加工余量为z=1.1,可一次走刀完成,asp=1.1。
(b)确定进给量:
由《机械制造工艺设计简明手册》表3—14表面粗糙度Ra3.2,铸铁,副偏角10,刀尖半径0.5,则进给量为0.1~0.25mm/r,再根据《机械制造工艺设计简明手册》表4.2—3查取横向进量f=0.24mm/r。
(c)确定切削速度V
根据《切削用量手册》表1.11查取:
V
=2.02(由182~199HBS、asp=1.1、f=0.24mm/r、车刀为YG硬质合金)由于实际车削过程使用条件的改变,查取切削速度修正系数:
=V
60
V=V
KKKKKSVKkv
=75.2m/min
n=266r/min
按C365L车床转速(《机械制造工艺设计简明手册》表4.2-2)选择与266r/min相近似的机床转速n=322r/min,则实际切削速度V=n/1000=3.1490322/1000=91.0m/min。
a=1.1mm,f=0.24,n=322r/min,V=91.0m/min。
(3)计算基本工时
L=(d-d1)/2+L1+L2+L3(其中d=90,d1=45,L1=4,L2=L3=0)
=(90-45)/2+4+0+0=26.5mm
T=L×
i/(f×
n)=26.5×
1/(0.24×
322)=0.34min。
(三)粗车Ф180mm外圆
与粗车左端面同一把。
粗车外圆,加工余量为1.5+1=2.5mm,两次走刀,则asp=2.5/2×
2=0.825mm。
(b)确定进给量
由《切削用量简明手册》加工材料gSiCr,刀杆尺寸16~25,工件直径为100mm,则f=0.8~1.2。
再由《简明手册》表4.2—3查取f=0.76。
(c)选择刀具磨钝标准及耐用度
由《切削用量简明手册》表1.9查取后刀面磨损最大限度为0.8~1.0,焊接耐用度T=60mm。
(d)确定切削速度V
根据《切削用量简明手册》表1.11查取:
=1.33(由182~199HBS、asp=2.1、f=0.76mm/r、车刀为YG硬质合金),由于实际车削过程使用条件的改变,查取切削速度修正系数:
K=1.0,K=1.0,K=0.73,K=(190/HBS)1.25=1.0,KSV=0.85,Kkv=1.0。
KKKKKSVKkv
=49.5m/min
n=157.6r/min
按C365L车床转速(《机械制造工艺设计简明手册》表4.2-2)选择与157.5r/min相近似的机床转速n=183r/min,则实际切削速度V=n/1000=3.14100183/1000=57.5m/min。
a=2.1mm,f=0.76,n=183r/min,V=57.5m/min。
(3)计算基本工时
T=(L+L1+L2+L3)×
n)其中L=9,L1=3,L2=3,L3=0,i=2
按C365L车床转速(《机械制造工艺设计简明手册》表4.2-2)选择与157.5r/min相近似的机床转速n=183r/min,则实际切削速度V=n/1000=3.1490183/1000=51.7m/min。
a=2.1mm,f=0.76mm/r,n=183r/min,V=51.7m/min。
T=(L+L1