水泥厂余热发电综合讲义Word下载.docx
《水泥厂余热发电综合讲义Word下载.docx》由会员分享,可在线阅读,更多相关《水泥厂余热发电综合讲义Word下载.docx(28页珍藏版)》请在冰豆网上搜索。
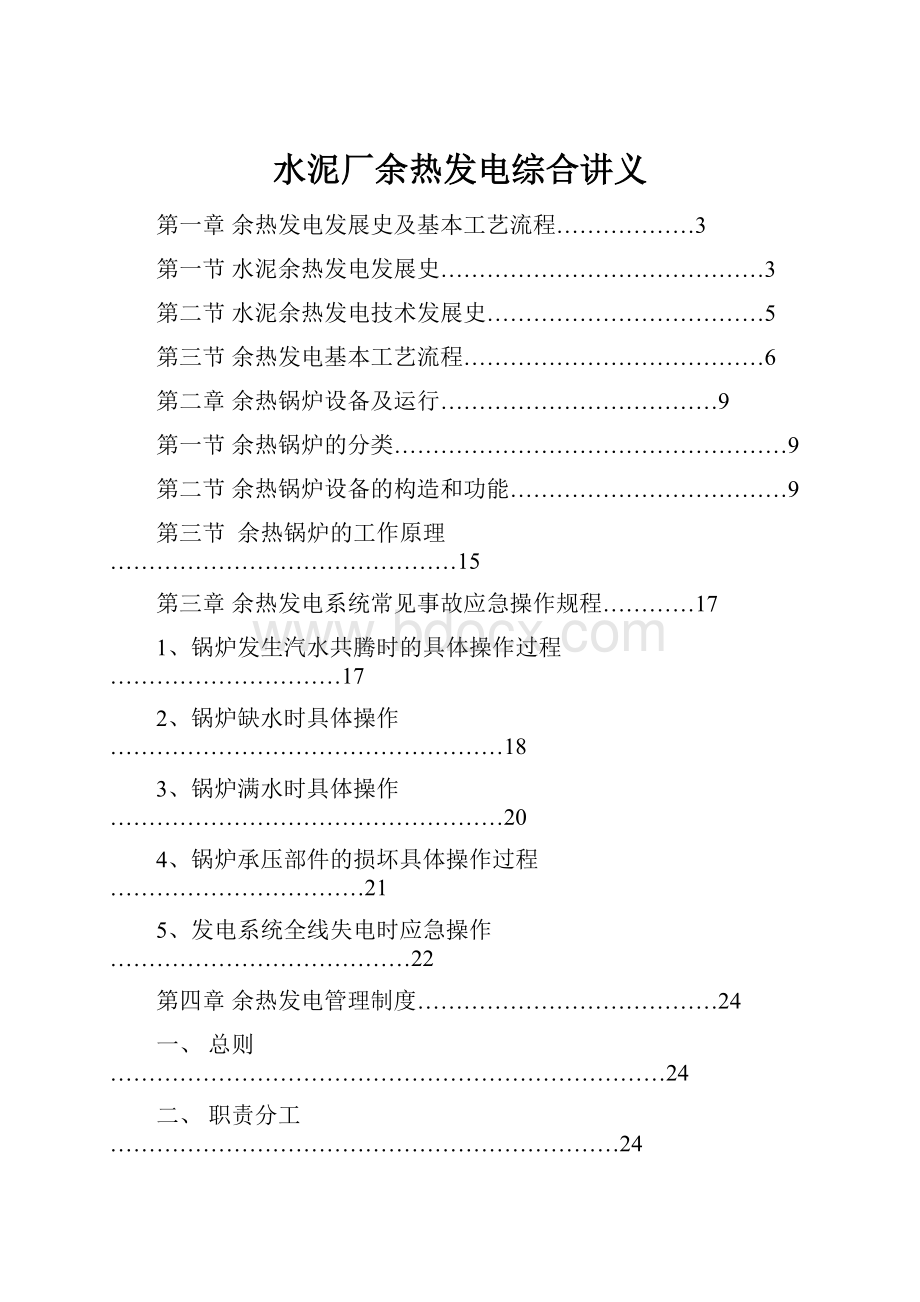
但我国水泥工业却“大而不强”,突出问题是耗能高、污染重。
在工业生产中使用的各种炉窑,都耗用大量的燃料,但它们的热效率都很低,一般只有30%左右,大部分热量都被高温烟气、炉渣和高温产品带走。
随着工业的发展,科学技术水平的不断提高,余热利用对节约能源、改善劳动条件、增加生产、降低生产成本等方面起着越来越重要的作用,已成为工业生产不可分割的组成部分。
在近几十年中,世界各国对余热利用进行了一些研究工作,但发展一直不快,其原因除了对余热利用重视不够之外,更主要的是没有掌握好它的规律。
60年代以来,世界各国余热利用技术发展很快。
我国目前余热利用的现状,与世界先进水平相比还有很大的差距,大部分余热尚未被利用。
在当前能源供应紧张的形势下,大力开展回收余热的工作已显得极为重要。
我国在水泥工业生产中,利用水泥回转窑尾部的余热进行发电,对降低生产成本,节约能源方面已积累了不少经验。
在新建的水泥厂中均已考虑到对余热的利用,进行统一规划,收到的效益十分可观。
在能源消耗方面,我国一吨水泥的平均综合煤耗约为159kg(标准煤),而国际先进水平约为110kg,仅此一项,我国水泥工业每年多消耗的煤炭约为5000万吨。
与此同时,由于节能技术、装备水平的限制和节能意识的影响,在水泥生产过程中,仍有大量的中、低温废气余热资源未能被充分利用,能源浪费现象仍然十分突出。
在新型干法水泥企业,由窑头熟料冷却机和窑尾预热器排出的350℃以下的废气,其热能大约为水泥熟料烧成系统热耗能的30%,造成巨大的能源浪费,在我国能源日益紧张、环境负荷不断加重的情况下,迫切需要改变这一状况,切实提高能源的综合利用效率,开发利用水泥生产过程中的废气余热资源,实现变废为宝将受到各方面的高度重视。
纯低温余热发电技术,即是在新型干法生产线生产过程中,通过余热回收装置——余热锅炉将窑头、窑尾排出大量低品的废气余热进行回收换热,产生过热蒸汽推动汽轮机实现热能——机械能的转换,再带动发电机转化成电能,并供给水泥生产过程中的用电负荷。
从而不仅大大提高了水泥生产过程中能源的利用水平,对于保护环境,提高企业的经济效益,提高产品的市场竞争力,起到巨大的促进作用。
同时该项技术的开发应用,完全符合我国的可持续发展战略。
从国家的产业政策来看,早在此1996年国力院曾以国发【1996】36号文批转国家经贸委等部门《关于进一步开发资源综合利用意见》的通知,《通知》明确指出:
“凡利用余热、余压、城市垃圾和煤矸石等低热值燃料及煤层气,生产电力、热力的企业,其单机容量在500kw以上,符合并网条件的,电力部门都应允许并网……,单机容量在(含12MW)以下的综合利用电厂,不参加电网调峰……”。
《国家发展改革委办公厅关于组织申报节能、节水、资源综合利用重大项目和示范项目以及现役火电厂脱硫设施设备选项目的通知》(发改办环资【2004】906号),明确重点支持钢铁、有色石油石化、化工、建材等高耗能行业节能技术改造,水泥中、低温余热利用就列入其中。
可见,利用水泥余热进行发电,国家在政策和法规上是扶持和大力提倡的,该技术的开发应用完全符合国家的产业政策。
新型干法水泥生产技术在我国经历了一个逐步完善提升的发展过程。
近年来,新型干法水泥生产技术在应用中不断提升,尤其是海螺集团,在工艺系统优化、自动控制、投资成本、生产规模、劳动生产率和环境保护等生产技术和装备方面,已赶上甚至领先国际先进水平,只是在可燃废料替代率和生产用电自供率方面,与发达国家相比,还存在一定的差距。
近两年来,我国经济发展水平持续高扬,电力需求增长迅猛,电力供应紧张,国家对工业企业节能提出了更高的要求,尤其是对高耗能产业,要求最大限度地回收利用余热,降低能耗,节约能源,实现经济可持续发展战略。
因此,随着水泥市场竞争的日益激烈与残酷,充分利用窑系统排放废气进行余热发电,提高工厂生产用电自供率降低水泥生产成本,提高产品的竞争力,从而占领和扩大水泥市场份额,保持企业可持续发展,是大型水泥企业当前及今后可供选择的技术之一。
第2节水泥余热发电技术发展史
1、水泥熟料生产过程的热能利用
众所周知,水泥厂是耗能大户,在其熟料形成及粉磨的生产过程中要消耗大量的能源,同时也产生大量的含有相当多热能的废气,这些废气除一部分用来原料烘干、原煤烘干外,其余全部排放到大气之中。
随着时代的发展和技术的进步,在现代的大型水泥生产企业中,一般都采用带四级或五级悬浮预热器的窑外分解新型干法生产工艺来生产水泥熟料。
就能源利用率而言是大大的提高了,但是,仍然不可避免地有大量的能源流失。
我们来看水泥生产的三个主要工艺过程的能源消耗分配情况,生料粉磨占总能源的3.4%,熟料煅烧占总能源的92.6%,熟料粉磨占总能源的4.0%被废气带走,在带走的废气中的热能,除一小部分在原料烘干中加以利用外,其余大部分排入大气之中。
也就是说,在熟料生产过程中,通过窑头燃烧喷的40%煤粉和在分解炉中喷的60%煤粉,全部燃烧所产生的热量为100%,则用于熟料煅烧热量仅占60%,其余的40%的热能随废气排到大气中;
所以,在水泥厂的生产过程中排放废气中余热未回收之前,可以这样说,水泥厂既是能源耗大户,又是能源浪费大户。
2、纯低温余热发电技术
新型干法水泥生产线配套应用的纯低温余热发电技术,是在不提高水泥生产过程中能耗指标前提下,完全利用水泥煅烧过程中产生的余热进行回收,最大限度的提高水泥生产过程中热能的利用率,与此同时,配置纯低温余热发电系统,将对原有水泥工艺系统不产生影响,当两个系统接口设计合理,将融合成为一个更优的大系统。
因此纯低温余热发电技术在新型干法水泥生产线配套应用,具有十分广阔的推广应用前景。
第3节余热发电基本工艺流程
1、水泥余热发电的工艺流程
从余热发电的工艺流程图我们可以看出,整个系统设置是:
一台PH锅炉,一台AQC锅炉,一台闪蒸器及锅炉给水系统,一套汽轮机发电机及其冷却水系统,水泥工艺线的设备不作大的改动。
1、含中低温余热废气的工艺流程
1.1PH锅炉部分:
在预热器的废气出口的总管上开孔,用管道将开口处与PH锅炉的入口进行连接;
管道的入口处设置一台挡板(编号490),在预热器的废气的总管开孔下部设置一台挡板(编号491),PH锅炉废气的出口用管道连接至窑尾风机入口。
一台档板设置在废气管道中间(旁路档板编号492)。
当PH锅炉具备升温条件时,打开491,打开490挡板,关闭492。
这样,预热器出口的350℃的废气被引入PH锅炉,先通过炉内的过热器、蒸发器后,尚有250℃左右的废气由窑尾风机抽出,一部分用来烘干生料与煤,另一部分经过增湿塔及窑尾电收尘后排入大气之中。
1.2AQC锅炉部分:
在熟料冷却机的中部左右处开口,用管道把开口处与AQC锅炉前端的沉降室入口连接。
在沉降室入口前设置一台挡板(编号390),沉降室出口用管道连接至AQC锅炉入口,锅炉出口处设置一台档板(编号391),用管道连接至篦冷机到电收尘入口间管道上,篦冷机尾部与电收尘的管道上设置一台档板(旁路档板编号392)。
当AQC锅炉具备升温条件时,打开391,打开390挡板,同时关闭392挡板,篦冷机内的360℃的废气被引入AQC锅炉,先后通过炉内的过热器、蒸发器及省煤器,出口废气温度为90℃左右,由窑头风机抽出排入大气。
2、锅炉水的工艺流程
余热电站的热力循环是基本的蒸汽动力循环,既汽、水之间的往复循环过程。
蒸汽进入汽轮机做功后,经凝汽器冷却成凝结水,凝结水经凝结水泵升至常压与闪蒸器出水汇合,通过锅炉给水泵升压进入AQC锅炉省煤器进行加热,经省煤器加热后的高温水分三路分别送到AQC炉汽包,PH炉汽包和闪蒸器内。
进入两炉汽包内的水在锅炉内循环受热,最终产生一定压力的过热蒸汽作为主蒸汽送入汽轮机做功,进入闪蒸器内的高温水通过闪蒸原理产生一定压力的饱和蒸汽送入汽轮机后级起辅助做功作用。
做过功后的乏汽经过凝汽器冷凝后形成凝结水重新参与热力循环。
生产过程中的消耗掉的水由纯水装置制取出的纯水经补给水泵打入凝汽器下方的热井内。
锅炉水是整个余热发电炉机内部的循环水。
这样锅炉水经历了一个水蒸汽水的工艺过程。
3、蒸汽的工艺流程
3.1进入AQC锅炉汽包的水,由汽包底部的管道引入锅炉的蒸发器,蒸发出的饱和蒸汽再进入锅炉的汽包,经过汽水分离后送入锅炉的过热器,成为350℃过热蒸汽进入蒸汽主管道。
3.2进入PH锅炉汽包的水,由汽包底部的管道引入锅炉循环泵,通过强制循环,将汽包内的水送入蒸发器,蒸发出的饱和蒸汽再进入锅炉汽包,经汽水分离后送入锅炉的过热器,成为330℃过热蒸汽进入蒸汽主管道。
3.3AQC锅炉的350℃过热蒸汽与PH锅炉的330℃过热蒸汽并汽后,进入主蒸汽母管,通过主蒸汽切断阀和调节阀,进入汽轮机做功。
3.4闪蒸器将AQC锅炉的省煤器送来的热水,闪蒸成饱和蒸汽,进入汽轮机的末级辅助做功。
主蒸汽进入汽轮机做功后,乏汽进入凝汽器冷凝成水,并进入凝汽器的热井。
水蒸汽水的工艺过程中,将损失一部分水,根据凝汽器热水井的水位,由纯水泵将纯水箱内的纯水打入热水井进行补充。
二、热力系统
整个热力系统设计力求经济、高效、安全,系统工艺流程是由两台高效余热锅炉AQC、PH锅炉,一台闪蒸器和一套汽轮发电机组组成,辅之以冷却水系统、纯水制取系统、锅炉给水系统及锅炉粉尘输送系统。
余热锅炉内进行热交换产生压力、温度、额定蒸发量的过热蒸汽通过汽轮机,进行能量转换,拖动发电机向电网输送电力。
1、采用凝汽式混汽汽轮机。
凝汽式是指做过功的蒸汽充分冷凝成凝结水,重新进入系统循环,减少系统补充水量。
混汽式是指汽轮机除主蒸汽外,另有一路低压饱和蒸汽导入汽轮机做功,从而提高汽轮机的相对效率,提高发电机输出功率。
2、设置具有专利技术、高热效率的余热PH锅炉,采用特殊设计的机械振打装置进行受热面除灰,保证锅炉很高的传热效率。
3、应用热水闪蒸技术(高压热水进入低压空间瞬间汽化现象),设置一台闪蒸器,一方面将闪蒸出的饱和蒸汽导入汽轮机做功,进一步提高汽轮机的做功功率;
另一方面形成锅炉给水系统循环,可以有效的控制AQC炉省煤器段出口水温,保证锅炉给水情况稳定。
4、由于PH出口废气还要用于原料和煤烘干,所以PH锅炉无省煤器,只设蒸发器和过热器,控制出炉烟温在250℃左右,仍可满足水泥生产线工艺需要。
5、采用热水闪蒸自除氧结合化学除氧的办法进行除氧,不另设除氧器,减少了工艺设备,简化了工艺流程。
6、热力泵均采用一用一备双系列。
在运行泵出现故障时,备用泵自动投入使用,保证了发电系统安全、稳定运行。
第2章余热锅炉设备及运行
第1节余热锅炉的分类
余热锅炉是利用工业窑炉的废烟气,生产热水和蒸汽的设备。
因为各种工业窑炉的形式不同,故在工业窑炉烟道中配套安装的余热锅炉种类繁多,结构复杂,余热锅炉分为如下几类:
(1)按受热方式分:
有水管式余热锅炉和烟道式余热锅炉。
水管式余热锅炉:
指烟气在管外对流冲刷加热管内的水。
烟道式余热锅炉:
指烟气在烟管内,通过加热管外的水。
(2)按循环方式分:
有自然循环余热锅炉和强制循环余热锅炉。
(3)按布置方式分:
有立式余热锅炉和卧式余热锅炉。
(4)按压力分:
有低压余热锅炉和中压余热锅炉。
(5)按锅炉蒸发量分:
有大型余热锅炉、中型余热锅炉和小型余热锅炉。
按以上分类方式,我公司锅炉的特点为:
AQC:
小型、低压、立式、自然循环、水管式锅炉;
PH:
小型、低压卧式、强制循环、水管式锅炉。
余热锅炉吸收的热源及条件特殊,所以余热锅炉必须具有耐高温、耐磨损、耐腐蚀,并且有良好的除渣、除灰装置。
余热锅炉不仅具有普通锅炉的工作条件,还有其特殊性,所以在设计制造过程时还应考虑到防止磨损、防止堵灰、防止腐蚀和防止漏风等特殊工艺要求。
用于发电的余热锅炉一般都采用水管式锅炉。
第二节余热锅炉设备的构造和功能
1、余热锅炉设备的组成
余热锅炉是利用工业窑炉的余热来生产热水和蒸汽的设备。
与工业锅炉、电站锅炉相比较,它省去了燃料输送、煤粉的制备和燃烧设备,因而它的结构大大的简化了。
余热锅炉的汽水系统与工业锅炉、电站锅炉基本相似,它是由汽包、过热器、防灰管(蒸发器),对流管束和省煤器组成。
构成了由水变过热蒸汽的三个阶段:
水的加热、饱和水的蒸发、饱和蒸汽的过热。
余热锅炉辅助设备有:
链板除灰机、锅炉给水系统、。
余热锅炉附件有:
安全阀、汽水管线阀门、自动控制装置及热工仪表。
2、汽包的构造及作用
汽包是一个椭圆形密闭的容器,起着汇集炉水和饱和蒸汽的作用。
在汽包内装有给水装置、汽水分离装置、加药装置和连续排污装置。
余热锅炉基本上采用低、中压型,因此一般不设分段蒸发装置。
汽包外设有水位计、安全阀和压力表。
(一)汽包的作用
1、容水
汽包内存有一定量的水,当负荷升降时,使各受热面有足够的水量,以满足蒸发的需要。
2、容汽
汽包中储存一定的汽、水量,因而汽包具有一定的储热能力。
在运行情况变化时,可减缓气压变化的速度,对锅炉运行调节有利。
例如,当外界负荷增加时,气压要下降。
汽包具有的储热就要释放出来,产生更多的蒸汽,使气压下降的速度减缓;
相反,当外界负荷降低时,水和金属就会吸收热量,使产生的蒸汽量减少,使气压上升的速度减缓。
3、汽水分离
汽包内有一定的汽空间高度,使离开水面的汽水混合物在汽空间内分离,水珠落入水中,不含水的饱和蒸汽进入过热器。
(2)汽包内的蒸汽净化装置
为了保护过热器,避免在管壁内凝结盐类和其它沉积物,要求进入过热器内的是干饱和蒸汽。
因此就必须在汽包内进行净化、汽水分离。
1、汽水挡板
当汽水混合物进入汽包时,首先碰到汽水挡板,使汽水混合物改变流动方向,不能直接冲击水面,水珠由于受碰撞、转变和惯性的作用落入水中。
2、水下孔板
为了防止经过汽水挡板的饱和蒸汽直接冲出水面,保持水表面的平稳,让蒸汽通过设在水下的多孔板上的小孔,改变流量,降低流速,离开水面进入汽空间,使饱和蒸汽所带的水分滞留在水中,可以避免汽水混合物冲击水面溅起大量的水珠。
3、钢丝网分离器
钢丝网分离器是设置在汽包内顶部饱和蒸汽出口处的一种装置,由多层钢丝网组合而成。
蒸汽通过多层钢丝网迂回上升,蒸汽中的水珠因改变流动方向和降低流速而落入水中,并可以使蒸汽以比较均匀的流速离开汽包进入饱和蒸汽引出管。
4、给水槽
为了防止给水进入汽包内直接冲击水位平面,保持水面的稳定,故在水位平面下装配一个溢水槽。
槽内有一根无缝钢管,管的下端钻有8-10个小孔,孔的数量根据给水管截面的水量决定。
给水通过小孔射向水槽的底部,槽内水满后稳定均匀地溢出,起到稳定水位表面的作用。
5、连续排污装置
连续排污管安装在炉水含盐浓度最大的部位,即汽包水位-100mm左右,连续不断地排除炉水中溶解盐,使炉水含盐量控制在水质标准允许的范围内。
6、加药装置
为了消除炉水中的残留硬度,利用加药装置通过汽包内的加药管向锅炉内直接加药,进行锅炉内处理,以保持炉水碱度和磷酸根数量的正常,防止炉管的苛性脆化,使炉管内形成一层碱膜防止结垢。
7、旋风式汽水分离器
当汽水混合物沿切线方向进入旋风分离器作旋转运动,受离心力作用,水珠落水中,蒸汽通过分离器上的百叶窗得到进一步的分离,进入汽空间。
旋风分离器分左旋式和右旋式,又分内置式和外置式。
余热锅炉一般皆采用内置式。
三、省煤器
省煤器是安装在余热锅炉尾部的受热面,用锅炉排出的烟气加热给水的设备,其作用:
(1)降低排烟温度,提高锅炉热效率。
余热锅炉省煤器回收利用排烟余热,可以节省大量的燃料。
(2)由于省煤器出口水的温度提高,减小进入汽包给水与炉管内饱和水的温差,汽包的热应力降低,保证了锅炉的安全运行。
(3)省煤器常见的故障
1、氧腐蚀
现代工业窑炉中,较多采用小型和中型余热锅炉。
这种类型的锅炉大多从事附属工作,在水处理方面往往被忽视,得不到应有的重视,尤其给水除氧问题一直解决不彻底,一些中小型余热锅炉不设除氧器,因此省煤器内部氧蚀较普遍。
为了防止氧腐蚀,省煤器在设计过程中已经考虑到水在管内的流速,水流速太慢,水中的气泡容易滞留在钢管壁上增加腐蚀的机会。
2、外表面的腐蚀
中、低压余热锅炉的给水温度一般在40℃~60℃,余热锅炉烟气温度波动幅度很大,在尾部受热面很容易产生露点温度,生成一些水珠凝结在管的外壁上,这些水珠吸收烟气中的二氧化碳,形成一层硫酸和亚硫酸,腐蚀钢管的外部。
为了防止产生露点温度,现代中压余热锅炉给水温度设计为104℃以上,锅炉排烟温度设计在160℃以上。
冶金窑炉产生的烟气含腐蚀气体对管外部的腐蚀更为严重,因此在锅炉设计时都有特殊的防腐蚀措施。
四、防灰管(蒸发器)
防灰管一般装置在余热锅炉的最前端,有的亦称水冷屏,是余热锅炉主要的蒸发受热面。
水泥窑尾废烟气中粉尘浓度很高,粉尘中含有钾、钠等微量元素,当温度达到900℃左右时,很容易粘贴在炉管表面。
当水从汽包中顺下降管进入防灰管内,低温的水与管外高温的灰相互传热,形成的温差较大,高温灰便急剧冷却,再落入烟道内。
同时管内的水吸收烟气中的热量,蒸发形成的汽水混合物顺上升管进入汽包,形成自然循环系统。
五、过热器
(1)过热器的作用
过热器是将饱和蒸汽过热到额定过热温度的热交换器,在发电锅炉中是不可缺少的组成部分。
采用过热器能够使饱和蒸汽至所需要的温度,可以提高汽轮机的工作效率,减少汽轮机的蒸汽消耗量,减少蒸汽输送过程中凝结损失,消除对汽轮机叶片的腐蚀。
(2)过热器的结构
过热器有多种结构形式,按传热方式可将过热器分为对流式和辐射式两种。
而余热锅炉是利用工业窑炉的热烟气加热水或汽的设备,故余热锅炉只有对流式过热器。
对流式过热器是由许多根并列的蛇形管和联箱所构成。
蛇形管与联箱之间采用焊接连接。
联箱布置在炉外不受热。
蒸汽在蛇形管内流动,蛇形管外受到为烟气的冲刷,烟气将热量传给蛇形管,蒸汽则从管壁上将热量带走,从而使蒸汽受到加热,温度升高。
对流式过热器按管子的放置方向,可分为立式布置和卧式布置两种。
由于立式布置的过热器支吊比较方便,积灰可能性小,故得到广泛采用。
对流式过热器按烟气与蒸汽的流动方向可分为顺流、逆流及混流式等。
六减温器
汽轮机对蒸汽温度要求比较严格,如果过热蒸汽温度超过规定值,就会对汽轮机各部件产生极大的损害。
一般余热锅炉的烟气温度参数极不稳定,为防止因蒸汽温度过高而产生的损害,必须对蒸汽温度进行调节。
(1)调节过热器温度的方法
1、改变烟气温度
及时联系窑炉操作人员,减弱或增强燃烧来调节蒸汽温度。
这种方法直接影响窑炉燃烧的稳定性,影响窑的产品产量和质量,故不提倡采用这种办法。
2、表面式减温器
表面式减温器是一个圆形的热交换器,在筒内设有U形管两端与管板连接。
U形管内通水,蒸汽通过管外和管体内部。
蒸汽通过筒体与U行管外空间,与U形管内的水进行热交换,达到减温目的。
这种减温方法分为给水减温系统和炉水减温系统两种。
通常广泛采用的是给水减温系统,给水减温方法是利用锅炉给水进入减温器U形管内与蒸汽进行热交换后回到给水箱,形成一个独立的循环系统,达到蒸汽温度调节的目的。
七对流管束
对流管束是余热锅炉的主要受热面。
它采用上、下两集箱连接。
下集箱内下降管与汽包连接;
上集箱上升管与汽包连接,构成两组或更多组的循环系统。
对流管束有顺排和叉排两种型式。
顺排对流管束磨损度较轻,不易积灰,受热面布置受到限制。
叉排对流管束容易积灰,磨损严重,而且容易堵灰,清除灰尘困难,受热面布置多,传热效果好。
为了提高锅炉效率,多采用叉排式。
第三节余热锅炉的工作原理
1、余热锅炉的水循环
水和汽的混合物在锅炉内密闭的回路中不断地流动就叫水循环。
锅炉水循环分两种:
一种是自然循环,一种是强制循环。
在余热锅炉中较广泛采用自然循环。
自然循环是锅炉密闭的循环回路中因工质密度差而形成的水循环称自然水循环。
炉水受热后产生的汽水混合物密度变小,沿上升管上升进入汽包。
新进入汽包的水温度低,密度大,便顺下降管进入下集箱受热后进入上升管上升至汽包。
这样水在炉管内不断地流动、不断地吸收受热面金属壁的热量同时冷却金属壁,使金属壁不会超温,保证水的正常循环。
从汽包沿两侧下降管到防灰管下集箱,再经过防灰管受热上升回汽包,为一个循环系统。
强制循环锅炉中水或水蒸汽不仅以水与水蒸汽的密度差为动力,而且需要一定的泵功来在加热管道中循环,所以称之为强制循环锅炉。
第三章余热发电系统常见事故应急操作规程
1.锅炉发生汽水共腾时的具体操作过程
1.1.汽水共腾的现象
1.1.1.蒸汽和炉水的含盐量增大
1.1.2.过热蒸汽温度下降
1.1.3.汽包水位发生剧烈波动,汽包水位计模糊不清
1.1.4.严重时,蒸汽管道内发生水冲击
1.1.5.汽轮机热效率下降
1.2.汽水共腾的原因
1.2.1.炉水水质电导率不合格
1.2.2过路入口风温和风量波动较大,造成符合波动剧烈
1.2.3锅炉汽包内的汽水分离装置有缺陷或水位过高
1.3汽水共腾的处理方法
1.3.1适当降低锅炉蒸发量,并保持锅炉稳定运行
1.3.2全开锅炉连续排污阀必要时开启事故放水阀或其它排污阀,同时增加给水量
1.3.3停止向锅炉汽包内加药
1.3.4尽量维持汽包低水位
1.3.5开启过热器和蒸汽管道上的所有疏水阀
1.3.6通知现场人员对排污水进行检测,并采取一定措施改善水质
1.3.7锅炉炉水质量未改善之前,不允许增加锅炉负荷
1.3.8待故障消除后应冲洗水位计
2锅炉缺水时具体操作
锅炉缺水分为轻微缺水和严重缺水两种。
轻微缺水:
当锅炉水位降至最低允许水位以下或水位计不能直接看到
水位,但用叫水操作能使水位出现。
(“叫水”操作:
先开启水位计底部排泄阀,再关闭汽连管旋塞,
保持水连管旋塞开度,然后缓慢关闭排泄阀,观察水位计内是否有
水位出现。
有水位出现后,打开汽连管旋塞。
)
严重缺水:
当锅炉水位计看不见水位,而且