工艺技术炼钢原理与工艺.docx
《工艺技术炼钢原理与工艺.docx》由会员分享,可在线阅读,更多相关《工艺技术炼钢原理与工艺.docx(68页珍藏版)》请在冰豆网上搜索。
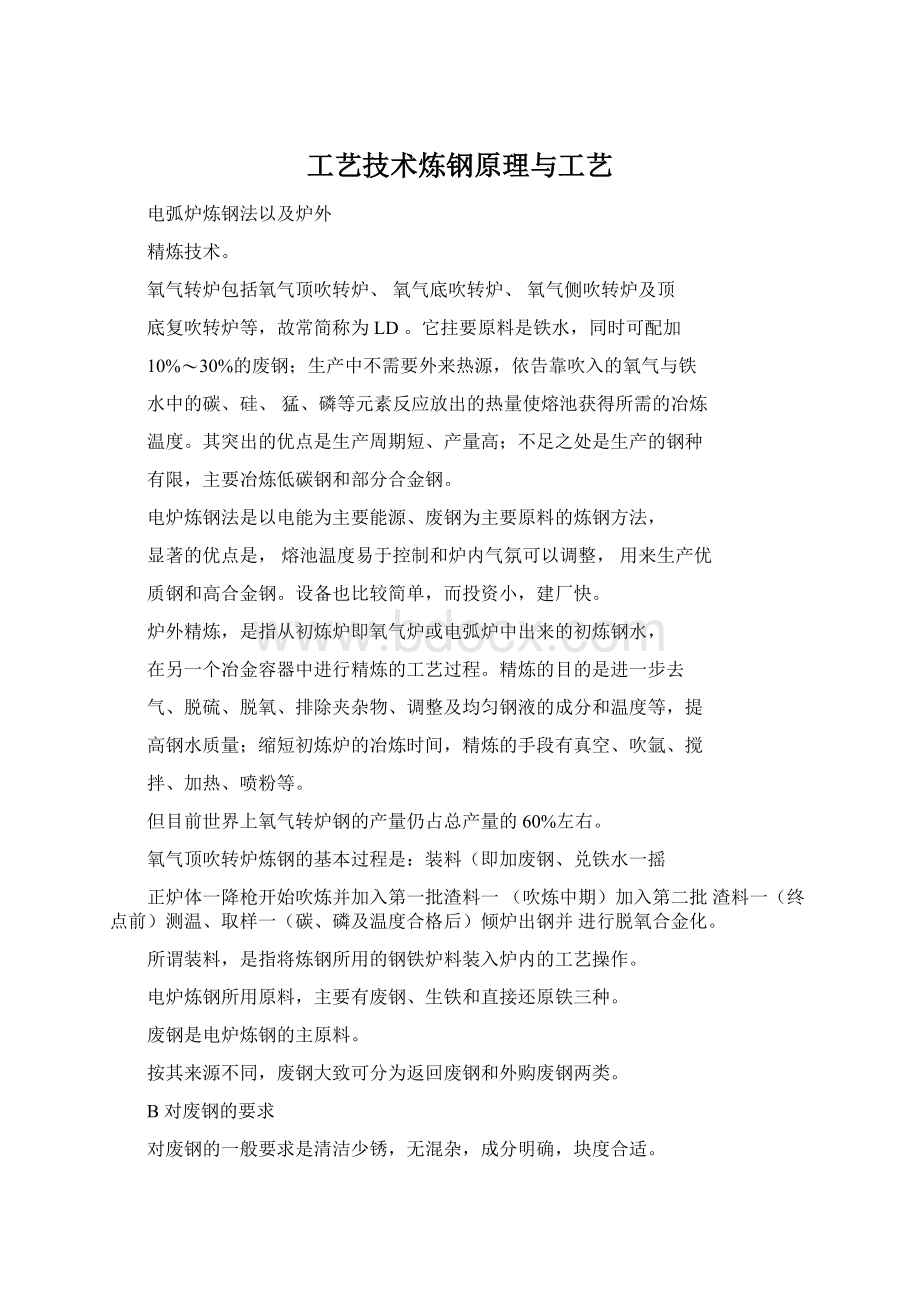
工艺技术炼钢原理与工艺
电弧炉炼钢法以及炉外
精炼技术。
氧气转炉包括氧气顶吹转炉、氧气底吹转炉、氧气侧吹转炉及顶
底复吹转炉等,故常简称为LD。
它拄要原料是铁水,同时可配加
10%〜30%的废钢;生产中不需要外来热源,依告靠吹入的氧气与铁
水中的碳、硅、猛、磷等元素反应放出的热量使熔池获得所需的冶炼
温度。
其突出的优点是生产周期短、产量高;不足之处是生产的钢种
有限,主要冶炼低碳钢和部分合金钢。
电炉炼钢法是以电能为主要能源、废钢为主要原料的炼钢方法,
显著的优点是,熔池温度易于控制和炉内气氛可以调整,用来生产优
质钢和高合金钢。
设备也比较简单,而投资小,建厂快。
炉外精炼,是指从初炼炉即氧气炉或电弧炉中出来的初炼钢水,
在另一个冶金容器中进行精炼的工艺过程。
精炼的目的是进一步去
气、脱硫、脱氧、排除夹杂物、调整及均匀钢液的成分和温度等,提
高钢水质量;缩短初炼炉的冶炼时间,精炼的手段有真空、吹氩、搅
拌、加热、喷粉等。
但目前世界上氧气转炉钢的产量仍占总产量的60%左右。
氧气顶吹转炉炼钢的基本过程是:
装料(即加废钢、兑铁水一摇
正炉体一降枪开始吹炼并加入第一批渣料一(吹炼中期)加入第二批渣料一(终点前)测温、取样一(碳、磷及温度合格后)倾炉出钢并进行脱氧合金化。
所谓装料,是指将炼钢所用的钢铁炉料装入炉内的工艺操作。
电炉炼钢所用原料,主要有废钢、生铁和直接还原铁三种。
废钢是电炉炼钢的主原料。
按其来源不同,废钢大致可分为返回废钢和外购废钢两类。
B对废钢的要求
对废钢的一般要求是清洁少锈,无混杂,成分明确,块度合适。
在电弧炉炼钢中,生铁一般是用来提高炉料的配碳量的。
转炉炼钢的原料主要是铁水,其次还配用部分废钢。
1.2.1.1铁水
铁水是氧气顶吹转炉的主原料,一般占装入量的70%以上。
铁水
的物理热和化学热是氧气顶吹转炉炼钢过程中的唯一热源。
A、对铁水温度的要求
较高的铁水温度,不仅能保证转炉炼顺利进行,同时还能增加放
心钢的配加量,降低转炉的生产成本。
希望铁水的温度尽量高些,入
炉时仍在1250〜1300Co
1、兑入转炉时的铁水温度相对稳定。
2、铁水的成分应该合适而稳定。
3、铁水中的硅,是转炉炼钢的主要发热元素之一。
铁水含硅量
以0.5%〜0.8%为宜。
4、对于含硅量过高的铁水应进行预脱硅处理,以改善转炉的脱
磷条件,并减少渣量。
5、铁水的含猛量
(1)铁水中的猛是一种有益元素;
(2)铁水的
含猛量多低于0.3%。
6、铁水的含磷量
(1)磷会使钢产生“冷脆”,是钢中的有害元
素之一。
铁水的含磷量小于0.15%〜0.20%。
7、铁水的含硫量
(1)硫会使钢产生“热脆”现象,也是钢中的
有害元素,铁水含硫量低于0.04%〜0.05%。
铁水含硫高时,对其进行预脱硫处理是经济有效的脱硫方法。
铁水的成分也应相对稳定,以方便冶炼操作和生产调度。
还希望兑入转炉的铁水尽量少带渣。
1.2.1.2废钢
废钢是转炉的另一种金属炉料,作为冷却剂使用的。
转炉的装入制度,包括装入量、废钢比及装料顺序三个问题。
1.2.2.1装入量的确定
转炉的装入量是指每炉装入铁水和废钢两种金属炉料的总量。
目
前控制氧气顶吹转炉装入量的方法有以下三种。
(1)定量装入法。
所谓定量装入,是指在整个炉役期内,每炉
的装入量保持不变的装料方法。
优点是:
生产组织简单,便于实现吹炼过程的计算机自动控制,
定量装入法适合于大型转炉。
(2)定深装入法。
所谓定深装入,是指在一个炉役期间,随着
炉衬的侵蚀炉子实际容积不断扩大而逐渐增加装入量以保证溶池深
度不变的装料方法。
优点是:
氧枪操作稳定,有利于提高供氧强度并减轻喷溅;又能充分发挥炉子的生产能力。
但是装入量和出钢量生产组织难度大。
(3)分阶段定量装入法。
该法是根据炉衬的侵蚀规律和炉膛的
扩大程度,将一个炉役期划分成3〜5个阶段,每个阶段实行定量装
入,装入量逐段递增。
因此中小转炉炼钢厂普遍采用。
1.2.2.2废钢比
废钢的加入量占金属装入量的百分比称为废钢比。
提高废钢比,
可以减少铁水的用量,从而有助于降低转炉的生产成本;同时可减少
石灰的用量和渣量,有利于减轻吹炼中的喷溅,提高冶炼收得率;还
可以缩短吹炼时间、减少氧气消耗和增加产量。
废钢比大多波动在
10%〜30%之间。
氧气顶吹转炉的装料顺序,一般情况下是先加废钢后兑铁水,以
避免废钢表面有水或炉内渣未倒净装料时引起爆炸。
炉役后期,可先
兑铁水后加废钢。
炼钢的主要任务之一,就是要将金属炉料中的杂质元素如碳、磷
等降低到钢种规格所要求的程度。
炼钢生产首先要有一个氧化过程。
供入炉内的氧,可以三种不同的形态存在,即生态、溶于钢液和溶解
在渣中。
溶池内的氧主要来源于直接吹氧、加矿分解和炉气传氧三个方
面。
直接吹入氧气是炼钢生产中向熔池供氧的最主要方法。
要求氧气
的含氧量不得低于98.5%,水分不能超过3g/m3,而且具有一定的压力。
转炉炼钢采用高压氧气经水冷氧枪从溶池上方垂直向下吹入的方式供氧;氧枪的喷头是拉瓦尔型的,工作氧压0.5〜I.IMPa,氧气流股的出口速度高达450〜500m/s,即属于超音速射流,以使得氧气流股有足够的动能去冲击、搅拌熔池,改善脱碳反应的动力学条件,
加速反应的进行。
2.1.2加入铁矿石和氧化铁皮
而在氧气顶吹转炉炼钢中,铁矿石和氧化铁皮则多是作为冷动剂
或造渣剂使用的。
炼钢对铁矿石的要求是,含铁要高、有害杂质要低,一般成分为:
在氧化精炼过程中,炼钢炉内具备了炉气向熔池传氧的条件,气
相中的氧会不断传入溶渣和钢液。
杂质元素,是指钢液中除铁以外的其他各种元素如硅、猛、碳、
磷等。
它们的氧化方式有两种:
直接氧化和间接氧化。
所谓直接氧化,是指吹入熔池的氧气直接与钢液中杂质元素作用
而发生的氧化反应。
杂质元素的直接氧化反应发生在溶池中氧气射流的作用区,或氧
射流破碎成小气泡被卷入金属内部时。
所谓间接氧化,是指吹入溶池的氧气先将钢液中的铁元素氧化成
氧化亚铁(FeO),并按分配定律部分地扩散进入钢液,然后溶解到
钢液中的氧再与其中的杂质元素作用而发生的氧化反应。
杂质元素的间接氧化反应发生在熔池中氧气射流用区以外的其
也区域。
间接氧化是指钢中的[O]或渣中的(FeO)与钢液中的杂质元素间发生的氧化反应。
在氧气射流的作用区及其附近区域,大量进行的是铁元素的氧化反应,而不是杂质元素的直接氧化反应。
氧气转炉炼钢的供氧方式,主要是直接向溶池吹氧气。
所谓供氧
强度,是指单位时间内向每金吨金属供给的标准状态氧气量的多少。
供氧时间,主要与转炉的容量的大小有关,而且随着转炉容量增
大供氧时间增加;通常情况下,容量小于50吨的转炉取12〜16分钟;
50吨转炉取16〜18分钟;容量大于120吨的转炉则取18〜20分钟。
缩短吹氧时间可以提高供氧强度,从而可强化转炉的吹炼过程,
提高生产率。
枪位,通常定义为氧枪喷头至平静熔池液面的距离。
枪位的高低
是转炉吹炼过程中的一个重要参数,控制好枪位是供氧制度的核心内
容,是转炉炼钢的关键所在。
转炉炼钢中,高压、超音速的氧气射流连续不断地冲击熔池,在
熔池的中央冲出一个“凹坑”,该坑的深度常被叫做氧气射流的冲击
深度,坑日的面积被称为氧气射流的冲击面积;与此同时,到达抗底
后的氧气射流形成反射流股,通过与钢液间的摩擦力引起熔池内的钢
液进行环流运动。
钢液的环流运动极大地改善了炉内化学反应的动力
学条件,对加速治炼过程具有重要意义。
吹炼过程中,采用低枪位或高氧压的吹氧操作称为“硬吹”。
硬
吹时,氧气射流与熔池间炼时的枪位较低或氧压较高,氧气射流与熔
池接触时的速度较快、断面积较小,因而熔池的中央被冲出一个面积
较小而深度较大的作用区。
作用区内的温度高达2200〜2700C,而
且钢液被粉碎成细小的液滴,从坑的内壁的切线方向溅出,形成很强
的反射流股,从而带动钢液进行剧烈的循环流动,几乎使整个熔池都
得到了强有力的搅拌。
采用高枪位或低氧压的吹氧操作称为“软吹”。
软吹时,氧气射
流与熔池间的作用吹炼时的枪位较高或氧压较低,与熔池接触时氧气
射流的速度较慢、断面积较大,因而其冲击溶度较小而冲击面积较大;
同时所产生的钢液中因此而形成的环流也就相对较弱,即氧气射流对
熔池的搅拌效果较差。
转炉的吹氧操作可有以下三种类型。
(1)恒氧压变枪位操作。
所谓恒氧压变枪位操作,是指在一炉
钢的吹炼过程中氧气的压力保持不变,而通过改变枪位来调节氧气射
流对熔池的冲击深度和冲击面积,以控制冶炼过程顺利进行的吹氧方
法。
恒氧压变枪位的吹氧操作能根据一炉钢冶炼中各阶段的特点灵
活地控制炉内的反应,吹炼平稳、金属损失少,去磷和去硫效果好。
目前国内各厂普遍采用这种吹氧操作。
恒枪位变氧压操作。
所谓恒枪位变氧压操作,是指在一炉钢的吹
炼过程,喷枪的高度,即枪位保持不变,仅靠调节氧气的压力来控制
冶炼过程的吹氧方法。
变枪位变氧压操作。
变枪位变氧压操作是在炼钢中同时改变枪位
和氧压的供氧方法。
目前国内普遍采用的是分阶段恒氧压变枪位操作,低枪位吹炼
时,钢液的环流强,几乎整个熔池都能得到良好的搅拌;高枪位吹炼
时,钢液的环流弱,氧气射流对熔池的搅拌效果差。
氧气顶吹转炉内的传氧方式有两种:
直接传氧和间接传氧。
直接传氧,是指吹入熔池的氧气被钢液直接吸收的传氧方式。
硬吹时,转炉内的传氧方式主要是直接传氧。
其传氧的途径有以
下两个;
(1)通过金属液滴直接传氧。
A、硬吹时,氧气射流强烈冲击熔池而溅起来的那些金属液滴被
气相中的氧气氧化,其表面形成一层富氧的FeO渣膜。
这种带有FeO
渣膜的金属滴很快落入熔池,并随其中的钢液一起进行环流而成为氧
的主要传递者。
B、通过乳浊液直接传氧
高压氧气射流自上而下吹入熔池,在将熔池出一凹坑的同时,射
流的末端也被碎裂成许多小气泡。
这些小氧气泡与被氧气射流击碎的
金属液和熔渣一起形成了三相乳浊液,其中的金属液滴可将小气泡中
的氧直接吸收。
由于熔池的乳化,极大地增加了钢液、熔渣、氧气三者之间的接
触面积,据估算低枪位吹氧时,氧气射流大量地直接向熔池传氧,因
而杂质元素的氧化速度较快;但是,渣中的(FeO)低而化渣能力差
些。
所谓间接传氧,是指吹入炉内的氧气经熔液传入钢液的传氧方
式。
软吹时,接传氧作用则会明显加强。
转炉炼钢中采用高枪位吹氧时,氧气射流的间接传氧作用得以加
强,使得渣中的(FeO)含量较高而化渣能力较强;
枪位控制:
转炉炼钢中枪位控制的基本原则是,根据吹炼中出现
的具体情况及时进行相应的调整,力争做到毁不出现“喷溅”,又不
产生“返干”,使冶炼过程顺利到达终点。
A、一炉钢吹炼过程中枪位的变化:
枪位的变化规律通常是:
高
—低—高—低。
吹炼前期,最佳的枪位应该是,使炉内的熔渣适当泡沫化即乳浊
液涨至炉口附近而又不喷出。
吹炼中期的枪位也不宜过低。
合适的枪
位是使渣中的(2FeO)保才!
在10%〜15%的范围内。
吹炼后期:
该阶段应先适当提枪化渣,而接近终点时再适当降枪,
以加强对熔池的搅拌,均匀钢液的成份和温度。
2.3.4复吹转炉的底部供气制度
顶底复合吹炼技术是近年来氧气转炉炼钢技术的重要发展。
氧气转炉的顶底复合吹炼法,可以通过选择不同的底吹气体的种
类和数量及顶枪的供氧制度,得到冶炼不同原料和钢种的最佳复合吹