瓶盖注塑模说明书.docx
《瓶盖注塑模说明书.docx》由会员分享,可在线阅读,更多相关《瓶盖注塑模说明书.docx(18页珍藏版)》请在冰豆网上搜索。
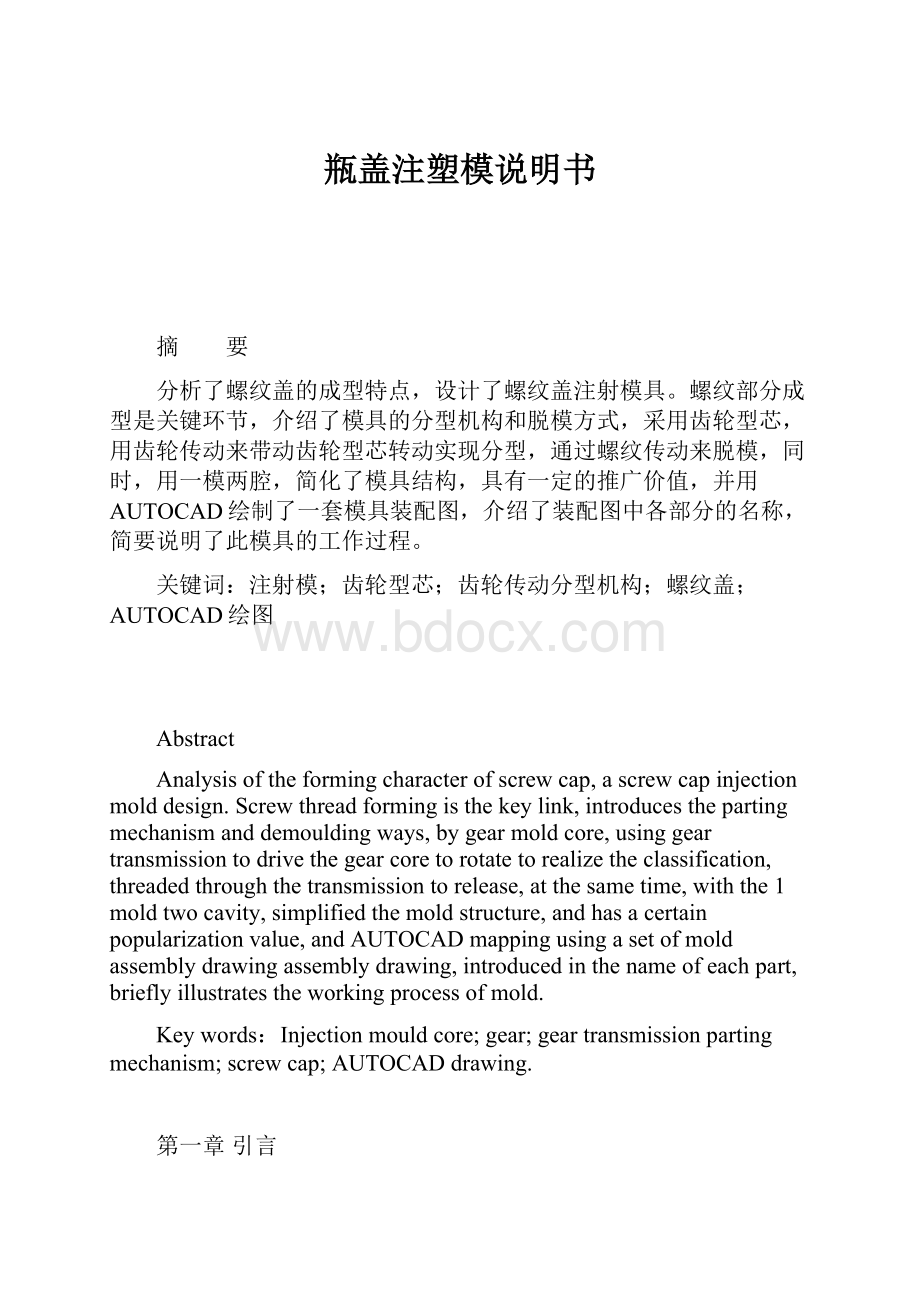
瓶盖注塑模说明书
摘 要
分析了螺纹盖的成型特点,设计了螺纹盖注射模具。
螺纹部分成型是关键环节,介绍了模具的分型机构和脱模方式,采用齿轮型芯,用齿轮传动来带动齿轮型芯转动实现分型,通过螺纹传动来脱模,同时,用一模两腔,简化了模具结构,具有一定的推广价值,并用AUTOCAD绘制了一套模具装配图,介绍了装配图中各部分的名称,简要说明了此模具的工作过程。
关键词:
注射模;齿轮型芯;齿轮传动分型机构;螺纹盖;AUTOCAD绘图
Abstract
Analysisoftheformingcharacterofscrewcap,ascrewcapinjectionmolddesign.Screwthreadformingisthekeylink,introducesthepartingmechanismanddemouldingways,bygearmoldcore,usinggeartransmissiontodrivethegearcoretorotatetorealizetheclassification,threadedthroughthetransmissiontorelease,atthesametime,withthe1moldtwocavity,simplifiedthemoldstructure,andhasacertainpopularizationvalue,andAUTOCADmappingusingasetofmoldassemblydrawingassemblydrawing,introducedinthenameofeachpart,brieflyillustratestheworkingprocessofmold.
Keywords:
Injectionmouldcore;gear;geartransmissionpartingmechanism;screwcap;AUTOCADdrawing.
第一章引言
1.1塑料注射模具的简介
塑件形状也越来越复杂,因此,对注射模结构的设计也要求越来越高。
本章主要对注射模装备图的绘制,通过对绘制注射模去了解注射模,了解模具结构及工作原理。
同时也是对工程制图的更深运用学注塑模具是塑料工业中增长最快的工业门类之一,因此,研究注塑模具对了解塑料产品的生产过程和提高产品质量有很大意义。
注射成型较压缩成型和压注成型具有周期短、塑件质量好、劳动强度低、模具寿命长、操作安全和劳动环境改善等诸多优越性。
但是,注射成型产品尺寸精度要求越来越高习。
1.2塑件及塑件材料的特点
图1螺纹盖三维零件图
塑件如图1所示,材料为ABS,密度为1.05g/cm
,收缩率0.4-0.7,取0.5。
ABS是由丙烯腈、丁二烯和苯乙烯三种化学单体合成。
每种单体都具有不同特性,丙烯腈有高强度、热稳定性及化学稳定性;丁二烯具有坚韧性、
抗冲击特性;苯乙烯具有易加工、高光洁度及高强度。
ABS具有如下特性:
⑴综合性能较好,冲击强度较高,化学稳定性,电性能良好;
⑵与372有机玻璃的熔接性良好,制成双色塑件,且可表面镀铬,喷漆处理;
⑶有高抗冲、高耐热、阻燃、增强、透明等级别;
⑷流动性比HIPS差一点,比PMMA、PC等好,柔韧性好,适于制作一般机械零件,减磨耐磨零件。
ABS成型的工艺条件见下表:
预热温度
80~85ºC
注射温度
20~90ºC
料筒前段温度
150~170ºC
预热时间
2~3h
高压时间
0~5s
料筒中段温度
165~180ºC
喷嘴温度
170~180ºC
冷却时间
2~120s
料筒后段温度
180~200ºC
模具温度
50~80ºC
总周期
5~220s
1.3成型方法
主要依靠注射成型机和注射模具来完成。
ABS塑料的成型加工性能良好,选用螺杆式注塑机进行注塑成型。
1.4模具分析
该注射模采用的是一模两腔的模外手工脱螺纹,模具体积小,模架简单,避免了自动脱螺纹。
但由于开模后需人工为其脱螺纹,造成了人力资源的提高,另外手工脱螺纹时需把螺纹型芯卸下来,所以型芯需备双份,以防机器的暂停。
第2章塑料制品设计与模具的选择
2.1塑料制品的设计
2.1.1塑件材料的选择
如图2—1所示,该塑件是一个连接螺帽,塑件为圆柱形薄壁塑件,生产批量很大。
要求其化学稳定性好,熔点高,故选用丁腈橡胶,玻纤增强,成型工艺性很好,可以注射成型。
2.1.2丁腈橡胶性能分析
干燥处理:
如果储存适当则不需要干燥处理;
熔化温度:
220~275℃,注意不要超过275℃;
模具温度:
40~80℃,建议使用50℃。
结晶程度主要由模具温度决定;
注射压力:
可大到1800bar。
注射速度:
通常,使用高速注塑可以使内部压力减小到最小,如果制品表面出现了缺陷,那么应使用较高温度下的低速注塑;
流道和浇口:
对于冷流道,典型的流道直径范围是4~7mm。
建议使用通体为圆形的注入口和流道。
所有类型的浇口都可以使用。
典型的浇口直径范围是1~1.5mm,但也可以使用小到0.7mm的浇口。
对于边缘浇口,最小的浇口深度应为壁厚的一半;最小的浇口宽度应至少为壁厚的两倍[5]。
2.1.3丁腈橡胶的成型条件
表2—1丁腈橡胶参数
项目数值
注射成型机类型螺杆式
密度0.96—1.02
计算收缩率1.02—1.025
预热和干燥温度t(℃)80—100
时间r(h)2—3
料筒温度t(℃)后段150—170
中段165—180
前段180—200
成型温度t(℃)200—210
模具温度t(℃)50—70
注射压力p(MPa)70—140
2.2注塑机的选择
2.2.1制品的几何属性
制品的壁厚对其质量有很大的影响,壁厚过小难以满足使用强度和刚度的要求,对于大型复杂难以充满型腔制品的内部易产生气泡,外部易产生凹陷等缺陷,同时还会增加生产成本。
本设计的制品壁厚为1.75㎜,属于中型塑件壁厚。
2.2.2分型面的选择
本塑件分型面位置如图2—2所示。
图2—2分型面
分型面的选择应注意以下几点:
1.不影响塑件外观,尤其是对外观有明确要求的制品;
2.有利于保证塑件的精度要求;
3.有利于模具加工,特别是型腔的加工;
4.有利于浇注系统、排气系统、冷却系统的设计;
5.便于制件的脱模,尽量使塑件开模时留在动模一边.
6.分型面应有利于侧向抽心;
7.分型面应取塑件尺寸最大处;
8.拔模斜度小或塑件较高时,为了便于脱模,可将分型面选在塑件的中间部位。
2.2.3注射机的选用
注射模是安装在注射机上使用的工艺装备,因此设计注射模是应该详细了解注射机的技术规范,才能设计出符合求的模具。
1.注射机的选用原则
(1)计算塑件及浇道凝料的总容量(体积或重量)应小于注射机额定容量(体积或容量)的0.8倍;
(2)模具成型时需用的注射压力应小于所选用注射机的最大注射压力;
(3)模具型腔注射时所产生的压力必须要小于注射机的锁模力;
(4)模具的闭模高度应在注射机最大,最小闭合高度之间;
(5)模具脱模取出朔件所需的距离应小于所选注射机的开模行程;
(6)模具的外形尺寸及安装尺寸必须与所选注射机模板适应,既模具最大外形尺寸安装时应不受拉杆间距的影响,模具安装用的定位环尺寸应与机床定位孔直径相配合;模具的模板各安装孔应与注射机固定模板的安装孔相对应、机床喷嘴孔径和球面半径应与模具进料孔相对应,注射机的开模行程应满足脱件条件[6]。
2.有关制品的计算
制件的参数
由于本塑件的结构复杂,为了避免计算误差过大,此次设计采用Solidworks自带计算功能:
本课题的塑件体积为V=25999.55立方毫米;密度ρ=0.98g/㎝³;
质量
=25.48g;表面积=13537.95
。
流道凝料的质量为
=0.6n
=0.6×2×25.48=30.576g(2-1)
注射量
m=
+
=25.48+30.576=50.056g(2-2)
3.选择注塑机
注塑成型机按结构形式可分为立式、卧式、和直角式三类。
为方便零件成型开模后自动脱落,本设计选卧式注塑机。
通过分析,根据每一周期的注射量的计算值,选用SZ-60/40卧式注塑机其规格如下
表2—2注射机主要技术参数
名称参数
理论注射容量(
)60
螺杆直径(mm)30
注射压力(MPa)180
注射速率(g/s)70
塑化能力(g/s)35
螺杆转速(r/min)0~200
喷嘴球半径(mm)10
喷嘴伸出量(mm)20
锁模力(kN)400
拉杆内间距(mm)220×300
开模行程(mm)250
最大模厚(mm)250
最小模厚(mm)150
模具定位孔直径(mm)80
模具定位孔深度(mm)10
顶出行程(mm)70
顶出力(KN)12
机器质量(T)3
由注塑机料筒塑化速率确定模具的型腔数n
=2.3(2-3)
式中k-注射机最大注射量的利用系数,M—注射机的额定塑化量,t—成型周期。
(因为本设计的零件体积比较,所以成型周期可以根据各种情况缩短一点,在此取300s)。
因此本设计选择一模两腔形式。
第三章具结构分析
2.1上模结构分析
2.1.1浇注系统
浇注系统包括主流道的选择,分流道截面形状及尺寸确定,浇口位置的选择,浇口形式及浇口截面尺寸的确定等几个方面的内容。
浇注系统配件主要有:
主流道,分流道,浇口,冷料穴,唧嘴,热唧嘴,热流道板,钩针,法兰,水口边,拉料杆,机械手,阻水,塞打螺丝等。
主流道可理解为塑料熔体从注射喷嘴开始到分流道为止的流动通道。
它与注塑机喷嘴在同一轴线上。
从减少压力和热量损失的角度来看,圆柱形是最佳截面形状。
分流道可以理解为从主流道末端开始到浇口为止的塑料熔体流动的通道。
圆柱形具有最大体积和最小表面积的特点,故分流道的截面形状应以圆形截面为最佳。
型腔体积形状相同,分流道最好采用等截面和等距离,另外,还要通过改变流道长度来调节阻力大小,保证型腔同时填充。
浇口可以理解为熔融塑料进入型腔的最后一道“门”,其主要功能有两个:
1.对塑料熔体流入型腔起控制作用;2.在注塑压力消失后封锁型腔,防止尚未冷却固化的塑料倒流。
浇口类型取决于制品外观要求、尺寸和形状的制约以及所用塑料种类等因素。
图2流道示意图
2.1.2冷却系统
模具的温度对塑料熔体充满、流动、固化成型、生产效率及制品形状与尺寸精度都有重要影响。
在模具中设置温度调节系统的目的就是要通过控制模温,使注射成型具有较好制品质量和较高生产效率。
冷却主要要注意冷却性与均匀性两个原则。
常用冷却介质有常温水、冷水、温水,还可利用模具材料的热导性能,如散热效果好的铍铜等。
冷却过程的三个环节:
1.高温塑料熔体注入模腔,经过冷却固化才能得到所需制品。
成型周期中一半以上时间用于对制品的冷却,可见其对提高生产效率的重要性。
2.由于制品形状复杂、壁厚不均、充模顺序不同等因素,使塑料在固化过程中不同位置温度不一样,这种热交换产生的应力会直接影响制品尺寸精度及外观。
冷却系统的设计理念就是保持与塑料特性、制品质量相适应的温度,最大限度消除或减少这种应力,改善塑料的物理性能,得到高质量制品。
3.冷却系统以冷却水道(运水)为主。
其工作目的不仅仅使模具冷却,而且要把成型过程中塑料熔体带给模具的高温不断散发掉,使模具保持恒定温度,控制塑料熔体的冷却速度。
【注:
冷却速度太快会影响填充;太慢会因温度过高引起制品产生缺陷和使成型周期加长。
】
2.1.3型腔
型腔也称母模,该结构安装在定模板上,并与型芯配合,注射成型时,型腔成型塑件的外壁形状。
其结构形式如图3。
图3型腔
根据塑件成型的需要和加工装配的工艺要求,凹模又有整体式和组合式两类。
其工作尺寸属包容尺寸,在使用过程中凹模的磨损会使包容尺寸逐渐变大。
因此,为了使得模具的磨损留有修模的余地,以及装配的需要,在设计模具时,包容尺寸尽量取下限尺寸,尺寸公差取上偏差。
2.2下模
2.2.1型芯
型芯也称公模,该结构安装在动模板上并与型腔配合,注射成型时,型腔成型塑件的外壁形状。
其结构形式如图4。
图4型芯
型芯是成型塑件内表面的成型零件,其工作尺寸属被包容尺寸,又分为整体式型芯、组合式型芯及小型芯的固定式型芯三种。
整体式型芯将成型的型芯与动模板做成一体,不仅结构牢固,还可省去动模垫板,但是由于不便于加工,故只适用于开关简单且型芯高度较小的单型腔模具。
组合式型芯又分整体装配式和镶件组合式。
小型芯的固定通常将成型塑件的小型芯称为小型芯,一般是单独制造多面手以嵌入的方式固定。
在使用过程中型芯的磨损会使被包容尺寸变小。
因此,为了使得模具的磨损留有修模的余地,以及装配的需要,在设计模具时,被包容尺寸尽量取上限尺寸,尺寸公差取下偏差。
此型芯含有螺纹,具有很大的加工难度,故采用小型芯固定式凸模,型芯在开模后可与动模板脱离,从而可实现模外手工脱螺纹。
因型芯需从模具中脱离出来,所以,每个型腔需配备两个型芯。
2.2.2导向与定位机构
注射模的导向机构主要有导柱导向和锥面定位两种类型。
导柱导向机构用于动、定模之间的开合模导向和脱模机构的运动导向。
锥面定位机构用于动、定模之间的精密对中定位。
导柱:
国家标准规定了两种结构形式,分为带头导柱和有肩导柱,大型而长的导柱应开设油槽,内存润滑剂,以减小导柱导向的摩擦。
若导柱需要支撑模板的重量,特别对于大型、精密的模具,导柱的直径需要进行强度校核。
导套:
导套分为直导套和带头导套,直导套装入模板后,应有防止被拔出的结构,带头导柱轴向固定容易。
设计导柱和导套需要注意的事项有:
1)合理布置导柱的位置,导柱中心至模具外缘至少应有一个导柱直径的厚度;导柱不应设在矩形模具四角的危险断面上。
通常设在长边离中心线的1/3处最为安全。
导柱布置方式常采用等径不对称布置,或不等直径对称布置。
2)导柱工作部分长度应比型芯端面高出6~8mm,以确保其导向与引导作用。
3)导柱工作部分的配合精度采用H7/f7,低精度时可采取更低的配合要求;导柱固定部分配合精度采用H7/k6;导套外径的配合精度采取H7/k6。
配合长度通常取配合直径的1.5~2倍,其余部分可以扩孔,以减小摩擦,降低加工难度。
4)导柱可以设置在动模或定模,设在动模一边可以保护型芯不受损坏,设在定模一边有利于塑件脱模。
5)导柱设在动模一侧可以保护型芯不受损伤,而设在定模一侧则便于顺利脱模取出塑件。
6)一般导柱滑动部分的配合形式按H8/f8,导柱和导套固定部分配合按H7/k6,导套外径的配合按H7/k6。
7)除了动模、定模之间设导柱、导套外,一般还在动模座板与推板之间设置导柱和导套。
8)导柱的直径应根据模具大小而决定,可参考标准模架数据选取。
第四章注塑模脱模系统设计
塑件脱模的机构设计在注射成型的每一循环中,塑件必须由模具型腔中脱出,脱出塑件的机构称为脱模机构或顶出机。
2.7.1概述
在注塑模中,将冷却固化后的塑料制品及浇注系统凝料从模具中安全无损坏地推出的机构称为脱模系统,也叫推出系统或顶出系统。
2.7.2设计原则
1.模具打开时,制品必须留在有脱模机构的半模上由于注射机的顶棍安装在动模一侧,所以注塑模的脱模系统一般在动模。
这种模具结构简单,动作稳定可靠。
2.防止塑件在推出时变形或损坏正确分析制品对型芯的包紧力和对模腔的粘附力的大小及其所在部位,有针对性的分析选择合适的推出方式,,使脱模力施于制品对模具包紧力最大,以及能够承受脱模力的部位。
3.力求良好的塑件外观在选择顶出位置时,应尽量设在塑件的内部或对塑件外观影响不大的部位。
4.结构合理,工作稳定可靠脱模机构应推出可靠,运动灵活,制造方便,更换容易且具有足够的强度和刚度。
5.位置合理,推出安全模具的推杆要设置于制品包紧力最大的地方,且不能和冷却系统、侧向抽芯机构、支撑柱、螺钉等发生干涉。
中间保持钢厚3~5㎜。
6.推出行程合理,制品可自由下落脱模系统必须将制品完全推出,完全推出是指制品在重力作用下可自由落下。
推出行程取决于制品的形状。
对于锥度很小或没有锥度的制品,推出行程等于后模型芯的最大高度加5~10㎜的安全距离,对于锥度很大的制品,推出行程可以小些,一般取后模型芯高度的1/2~2/3之间即可[15]。
2.7.3脱模机构的选择
本模具选择了推杆脱模机构,推杆脱模机构是最简单、最常用的一种形式,具有制造简单、更换方便、推出效果好等特点。
推杆直接与塑件接触,开模后将塑件推出。
推杆的截面形状;可分为圆形,方形或椭圆形等其它形状,根据塑件的推出部位而定,最常用的截面形状为圆形;推杆又分为普通推杆和成型推杆两种,前者只是起到将塑件推出的作用,后者不仅如此还能参与局部成型,所以,推杆的使用是非常灵活的。
推杆设计原则如下:
1.推杆应设在推出阻力的最大处。
2.推杆直径不宜过细。
3.推杆应设在塑件的内表面上,推杆的端面一般比型腔的平面高出0.05~0.1mm,以免在塑件留下凸台。
4.推杆与模具的配合间隙可以起排气作用,间隙值应小于塑料的溢出间隙值。
5.在保证塑件的质量和顺利推出的情况下,推杆数量不宜过多,推杆应布置均匀,使塑件受力平衡,推杆的布置应避开冷却水道和侧抽芯[16]。
2.7.4推杆的设计
1.推杆大小设计的一般原则
本设计采用的是扁形推杆推出。
(1)因为下列理由,推杆外径尽量取较大值;
①防止因承受注射压力而弯曲;
②防止因推出阻力而弯曲、磨损,甚至断裂;
③防止制品推出时变形,顶白。
(2)在不影响制品推出和位置足够时,应尽量采用相同型号及相同大小的推杆,以方便推杆采购和模具上推杆孔的加工。
(3)推出零件和模具型芯的配合为间隙配合,配合公差为H7/f7,配合长度10~20㎜。
2.推杆的固定形式
推杆的固定形式有多种,但最常用的是推杆在固定板中的形式,此外还有螺钉紧固等形式。
3.推出机构的复位
脱模机构完成塑件的顶出后,为进行下一个循环必须回复到初始位置,目前常用的复位形式主要有复位杆复位和弹簧复位。
本设计采用弹簧复位机构,弹簧复位机构是一种最简单的复位方式。
复位弹簧的作用是在注射机的顶棍退回后,模具的定模板、动模板合模之前,就将推杆板推回原位。
推出时弹簧被压缩,而合模时弹簧的回力就将推出机构复位[17]。
4.推杆的尺寸计算
脱模力的计算
F=
=211N(2-11)
式中:
S—制品的壁厚,m,E—塑料的弹性模量,MPa,Q—塑料成型的平均收缩率,%,l—制品对型芯的包容长度,m,f—制品与型芯之间的静摩擦系数,常取0.1—0.2,
—塑料的泊松比,
—系数,
=1+fsin
cos
1,
—模具型芯的脱模斜度。
推杆直径的计算
d=
0.002m(2-12)
式中:
—安全系数,常取
=1.5,L—推杆长度,m,F—脱模力,N,N—推杆数量,E—塑料的弹性模量,MPa。
2.7.5弹簧
弹簧的作用主要是缓冲,减振,储存能量。
在注塑模具中弹簧作用主要有以下几方面。
1.推杆固定板自动复位:
装在复位杆旁边,制品推出后,将推杆拉回原位,恢复型腔的状态。
它有先复位的功能。
2.定位:
用于侧向抽芯中的滑块定位,与当块一起使用。
3.活动板、流道推板等活动零件的辅助动力。
弹簧没有冲击力,且易疲劳失效,在模具中不允许单独使用。
合模,对模具进行预热一定的时间,再进行注塑,再冷却一段时间,然后开模,手工取出塑件。
开模的具体动作过程是:
开模时,定模扳与动模板的分离,在环形拉簧和卡环的作用下,螺纹型芯在开模时被带往动模,当推板碰到模外顶出机构时,推板、推杆、型芯停止动作,型芯被强行与动模板分离,即完成开模过程,然后用扳手卸掉螺纹型芯,完成脱模过程。
与此同时可装入另一个型芯,合模进行下一个循环。
结论
谢辞
经过一个多星期对收集与查询,又经过几天的总体构思,在脑中对串行通信设计有了一个总体的框架,对程序的流程图也有一个基本的结构,最后结合参考资料,结合自己对单片机知识的认识,又经过两天对程序的编写以及程序的改进,最后终于完成了本次课程设计各各项内容。
看着自己亲自通过自己的知识和努力设计的串行通信电路,心里是很欣慰的,因为我从这次课程设计不仅仅只是得到了一个自己的产品,还学到了很多,例如面对问题要保持冷静,特别是在程序的编写这一块,要找出程序的错误一定要有一个冷静的头脑,否则很难发现错误甚至是越改越错。
另外我还认识到与他人合作的重要性,虚心向别人学习,吸取别人编写程序的一些好的风格与特点再融入到自己的程序中,都是一些不错的方法。
在本次课程设计中,胡机秀老师认真指导我们课设。
虽然对某些软件仿真,操作环境还不是很熟悉。
但是在胡老师和同学们的帮助下,我开始慢慢熟悉了这些软件并懂得了如何去建立模型,设置参数,并且了解各个图形所代表的意思,并且得到了不错的结果。
而且胡老师严谨的态度,认真对待每一个同学的课设,以及在我的困难时期给我的帮助和理解,我感激不尽,且受益匪浅。
在此,我要对胡老师以及帮助过我的同学们表达最真挚的感谢。
参考文献
[1]《塑料模设计手册》编写组.塑料模设计手册.北京:
机械工业出版社,1994
[2]陈万林.实用塑料注射模设计与制造.北京:
机械工业出版社,2000.
[3]付宏生、刘京华.注塑制品与注塑模具设计.北京:
化学工业出版社,2006
[4]黄毅宏.模具制造工艺.北京:
机械工业出版社,999
[5]吴其晔.注射成型手册.北京:
化学工业出版社,2005
[6]叶久新、王群主编《塑料制品成型及模具设计》.湖南:
湖南科学技术出版社,2005
[7]模具实用技术丛书编委会.塑料模具设计制造与应用实例.北京:
机械工业出版社,2002
[8]宋长发.工程制图.北京:
国防工业出版社,2011