储罐施工方案.docx
《储罐施工方案.docx》由会员分享,可在线阅读,更多相关《储罐施工方案.docx(41页珍藏版)》请在冰豆网上搜索。
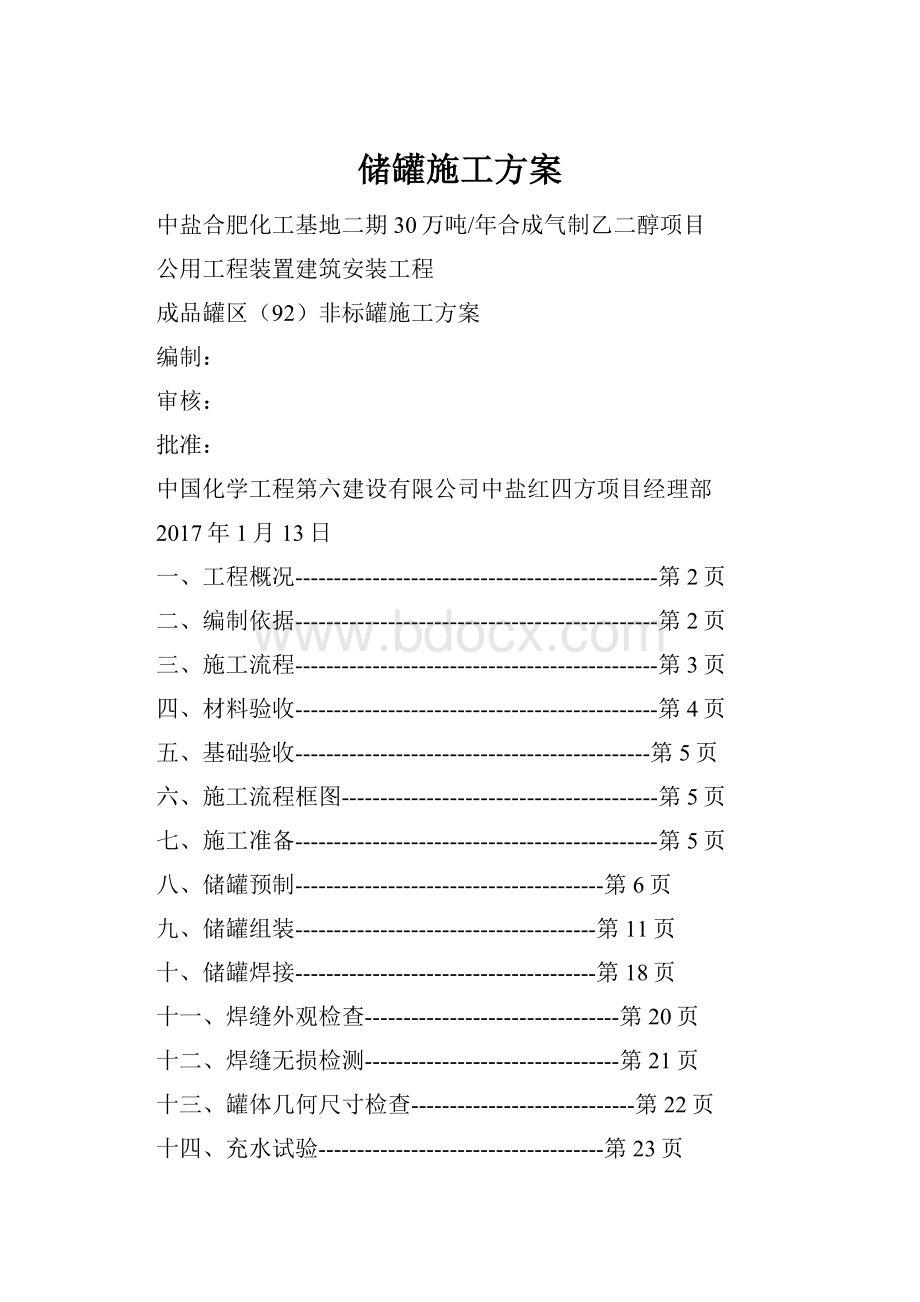
储罐施工方案
中盐合肥化工基地二期30万吨/年合成气制乙二醇项目
公用工程装置建筑安装工程
成品罐区(92)非标罐施工方案
编制:
审核:
批准:
中国化学工程第六建设有限公司中盐红四方项目经理部
2017年1月13日
一、工程概况-----------------------------------------------第2页
二、编制依据-----------------------------------------------第2页
三、施工流程-----------------------------------------------第3页
四、材料验收-----------------------------------------------第4页
五、基础验收----------------------------------------------第5页
六、施工流程框图-----------------------------------------第5页
七、施工准备-----------------------------------------------第5页
八、储罐预制----------------------------------------第6页
九、储罐组装---------------------------------------第11页
十、储罐焊接---------------------------------------第18页
十一、焊缝外观检查---------------------------------第20页
十二、焊缝无损检测---------------------------------第21页
十三、罐体几何尺寸检查-----------------------------第22页
十四、充水试验-------------------------------------第23页
十五、劳动力、工机具、设备配备计划-----------------第23页
十六、施工进度计划---------------------------------第27页
十七、质量目标及质量保证措施-----------------------第27页
十八、安全管理与安全保障---------------------------第30页
一、工程概况
1.简述
工程名称:
中盐合肥化工基地二期30万吨/年合成气制乙二醇项目公用工程装置建筑安装工程
工程地点:
安徽省合肥循环经济示范园(合肥市肥东县撮镇东十公里)
非标设备明细表:
名称
代号
规格/直径*高度
容积/m3
重量/㎏
材质
优级品乙二醇成品储罐
T-9201A
DN30000*16500
/
/
S30408
合格乙二醇储罐
T-9202
DN11500*13774
1000
39400
S30408
轻馏分储罐
T-9203
DN11500*13778
1000
42750
Q245R
重馏分储罐
T-9204
DN6550*7458
200
13930
Q245R
杂醇油储罐
T-9205
DN11500*13578
1000
42800
Q245R
粗DMC储罐
T-9206A
DN11500*13574
1000
38250
S30408
粗DMC储罐
T-9206B
DN11500*13574
1000
38250
S30408
DMO重组分储罐
T-9207A
DN4200*12102
100
19650
S30408
DMO重组分储罐
T-9207B
DN4200*12102
100
19650
S30408
DMC储罐
T-9208A
DN21000*19344
5000
145115
S30408
DMC储罐
T-9208B
DN21000*19344
5000
145115
S30408
高纯DMC储罐
T-9209A
DN8200*12129
500
25200
S30408
高纯DMC储罐
T-9209B
DN8200*12129
500
25200
S30408
成品甲醇储罐
T-9210
DN21000*19344
5000
129755
S30408
二、编制依据
1、设计施工图;
2、合同、招标文件;
3、GB50128-2014《立式圆筒形钢制焊接储罐施工规范》;
4、GB50341-2014《立式圆筒形钢制焊接油罐设计规范》;
5、HGT20584-2011《钢制化工容器制造技术要求》;
6、NB/T47003.1-2009《钢制焊接常压容器》;
7、HGT20583-2011《钢制化工容器结构设计规定》;
8、NB/T47015-2011《压力容器焊接规程》
9、TSGR0004-2009《固定式压力容器安全技术监察规程》;
10、JBT4736-2002《补强圈》;
11、GB/T5117-2012《非合金钢及细晶粒钢焊条》;
12、GB/T5118-2012《热强钢焊条》;
13、GB/T983-2012《不锈钢焊条》;
14SH3505-1999《石油化工施工安全技术规程》;
15GB50484-2008《石油化工建设工程施工安全技术规范》;
16JGJ80-2011《建筑施工高处作业安全技术规范》;
3、施工流程
底板组装时肯定不焊接,底板组装完毕焊接中幅板,缘板外侧400mm左右也是要提前焊接,底板试漏我先做中幅板,主体完成后再做没做的部分边缘板,后面的总体试验就括边缘板及边缘板与中幅板焊缝的真空试验。
罐内立柱多倒链提升倒装法施工总体程序见下图
四、材料验收
4.1钢板与型材
4.2焊条、焊丝、焊剂及保护气体等焊接材料应具有质量合格证明书,除应符合现行行业标准NB/T47018的规定外,还应符合下列规定:
(1)焊条应符合现行国家标准GB/T5117、GB/T5118、GB/T983的规定;
(2)焊丝应符合现行国家标准GB/T10045、GB/T17493、GB/T17853的规定;
(3)气体保护焊焊丝应符合现行国家标准GB/T8110的有关规定。
五、基础验收
5.1储罐安装前,必须对基础进行验收,要有基础施工记录和验收资料,并应对基础进行复验,合格后方可安装。
5.2基础中心标高允许偏差为±20mm
5.3支撑罐臂的基础表面,有环梁时,每10m弧长内任意两点的高差不得大于6㎜,且整个圆周长度内意两点的高差不得大于12㎜;无环梁时,每3m弧长内任意两点的高差不得大于6㎜,且整个圆周长度内意两点的高差不得大于12㎜。
5.4沥青砂表面应平整密实,无突出的隆起、凹陷及贯穿裂纹。
沥青砂表面凹凸度按下列方法检查:
当储罐直径小于25m时,可从基础中心向周边拉线测量,基础表面每100m2范围内测量点不应少于10点(小于100m2的基础按100m2计算),基础表面凹凸度不应大于25mm。
5.5验收完毕应办理基础中间交接手续。
六、施工方法
1、储罐拟采用电动倒链倒装法施工。
罐底板焊接采用手工电弧焊接,壁板焊接采用自动焊焊接。
2、现场进行下料、安装。
3、板材下料碳钢板采用机械加工或火焰切割下料,不锈钢钢板采用机械或等离子切割下料。
七、施工前准备
7.1施工准备:
(1)根据设备图纸合理绘制排版图,编制详细的材料、配件预算进行施工材料准备。
(2)提前准备好储罐加工场地:
安装好卷板机、剪板机、电焊机、空压机等机械设备。
(3)搭设好预制钢平台,所用计量器具应全部调校合格并在有效期内。
(4)组织施工作业人员认真熟悉施工图样,进行详细的技术交底,了解施工方法、技术要求。
7.2储罐制作一般要求
(1)必须根据绘制好的排版图进行放样和下料。
(2)材料放样应采用1:
1实样放样,放样时应根据工艺要求预留焊接缩和加工裕量。
(3)储罐预制和安装检验用样板,应符合下列规定:
①当曲率半径小于或等于12.5m时,弧形样板的弦长不应小于1.5m;曲率半径大于12.5m时,弧形样板的弦长不应小于2m。
②直线样板的长度不应小于1m。
③测量焊缝棱角度的弧形样板,其弦长不应小于m。
(4)储罐的预制方法不能损伤母材或降低母材性能。
(5)板材边缘加工面应平滑,不得有夹渣、分层、裂纹及熔渣等缺陷,去除火焰切割坡口产生的表面硬化层。
(6)纵向焊缝及环向焊缝严格按照图纸要求施工。
(7)不锈钢储罐预制还应符合以下要求:
①不锈钢材料不应与碳素钢及存放过氯化物的材料接触。
②不锈钢板材不应做硬印标记或刻画标识,应采用易擦洗的颜料做标记。
③不锈钢钢板及构件的吊装应采用吊装带,运输胎具上应采取防护措施。
④不锈钢钢板及构件不得用铁锤直接敲击,其表面不应有划痕、撞伤、电弧擦伤、腐蚀,并保持光滑。
⑤不锈钢构件不应采用热煨成型。
⑥不锈钢构件打磨应采用不锈钢专用砂轮片或磨带。
(8)所有的构件预制完成后及时用油漆作出清晰的编号标识。
八、储罐预制
8.1罐底板预制
8.1.1底板预制前,应根据图样要求及材料规格绘制排版图,并应符合下列规定:
(1)底板的排版直径,应按设计直径放大0.1%-0.15%。
(2)罐底环形边缘板沿罐底半径方向的最小尺寸不应小于700mm;边缘板最小直角边尺寸不应小于700mm如下图。
1-边缘板;2-环形边缘板;3-边缘板
(3)罐底环形边缘板的对接接头应应采用不等间隙,采用焊条电弧焊时,外侧间隙e1应为6mm-7mm,内侧间隙e2应为8mm-12mm如下图。
(4)罐底中幅板的宽度不应小于1000mm,长度不应小于2000mm;与罐底环形边缘板连接的不规则中幅板最小边尺寸不应小于700mm。
(5)底板任意相邻焊缝之间的距离,不应小于300mm。
罐底环形边缘板的尺寸测量部位
罐底环形边缘板的尺寸允许偏差(mm)
≥
8.2罐壁板预制
(1)各圈壁板的纵缝应向同一方向逐圈错开,相邻圈板纵缝间距应为板长的1/3,且不得小于300mm。
(2)底圈壁板纵向焊缝与罐底边缘板的对接焊缝之间的距离不得小于300mm。
(3)开孔与罐壁纵、环焊缝中心及罐壁最下端角焊缝边缘板的距离应符合下列规定:
①罐壁厚度大于12mm,且接管与罐壁板焊后不进行消除应力热处理时,开孔接管或补强板外缘与罐壁纵、环焊缝之间的距离,应大于较大焊脚尺寸的8倍,且不应小于250mm。
②任意厚度罐壁与接管进行焊后热处理或厚度不大于12mm的罐壁与接管焊后不进行热处理时,开孔接管或补强板外缘与罐壁纵焊缝之间的距离不应小于150mm;与罐壁环焊缝之间的距离,不应小于壁板厚度的2.5倍,且不应小于75mm。
③壁板的最低屈服强度小于或等于390MPa时,开孔应符合设计规定。
(4)罐壁上连接件的垫板周边焊缝与罐壁纵焊缝或接管、补强板的边缘角焊缝之间的距离,不应小于150mm;与罐壁环焊缝之间的距离,不应小于75mm;如不可避免与罐壁焊缝交叉时,被覆盖焊缝应磨平并经射线或超声检测合格,垫板角焊缝在罐壁对接焊缝两侧边缘应至少留20mm不焊。
(5)两开孔之间的距离应符合下列规定:
①两开孔至少有一个补强板时,其最近角焊缝边缘之间的距离,不应小于较大焊脚尺寸的8倍且不小于150mm;
②两开孔均无补强板时,角焊缝边缘之间的距离不得小于75mm。
(6)包边角钢对接接头与壁板纵向焊缝之间的距离不得小于300mm。
(1)
(2)壁板滚制后,应立置在平台上用样板检查,垂直方向用直线样板检查,其间隙不应大于2mm;水平方向上用弧形样板检查,其间隙不应大于4mm。
(3)因壁板长度过大,滚板时必须在滚床进板侧设一平胎架,出板侧设一曲率胎架。
壁板滚制必须严格控制弧度,特别是壁板端部的弧度。
测量壁板的滚制弧度必须在专用平台上检查测量,垂直方向用长度不小于1m的直线样板检查,其间隙不得大于2mm;水平方向上用2m长弧形样板检查,其间隙不得大于4mm。
(1)罐壁钢板的最低标准屈服强度小于或等于390MPa、板厚大于32mm且接管公称直径大于300mm;
8.3固定顶板预制
(1)顶板任意相邻焊缝的间距大于200㎜;
(2)单块顶板本身的拼接,应采用对接。
8.4构件预制
应预留调整量。
(1)补强板的材质应与开孔处壁板的材质相同。
:
垂直方向上用直线样板检查,其间隙不应大于2mm,水平方向用弧形样板检查,其间隙不应大于4mm。
(3)拼接补强板的对接焊缝应采用全熔焊透焊缝。
(4)补强板应有信号孔。
整块钢板制造的补强板应有一个信号孔;拼接的补强板,每一拼接段上应有一个信号孔。
信号孔应为M6-M10,位于开孔水平中心线上的螺孔。
(1)中间加强圈的预制先在钢制平台上安装好各种工卡具,做好胎具并控制好胎具弧度的准确性,将角钢放置于胎具上进行煨弧;
(2)中间加强圈内弧必须准确,其曲率同相应壁板的外圆半径相同,这样与罐壁组焊在一起,起到调整罐壁椭圆度的作用。
因此,为保证其安装精度,煨弧后用弧形样板进行检查,其误差不得大于2mm;放在平台上检查,其翘曲变形不得超过构件长度的0.1%,且不得大于6mm,有超差的必须进行调整修补;
(3)盘梯等构件均在预制厂进行预制,量油管和导向管在施工现场预制。
盘梯预制为两段,待量油管平台安装完后,实测其尺寸;量油管及导向管安装前提前进行预制,如其需要对接,则接口必须采用氩弧焊打底的焊接工艺。
九、储罐组装
9.1一般规定
①罐壁、罐底及附件不得作硬印标记;
②卡具应采用不锈钢材质,碳素钢工具卡不应与不锈钢罐接触及焊接;需要接触及焊接时在卡具上焊上不锈钢隔离垫板;
③在组装过程中应防止电弧擦伤等显现。
9.2罐底组装
(1)罐底板铺设前,要清除表面的泥土、油污。
(2)罐底板、底板与边缘板采用搭接接头,搭接宽度及搭接型式严格按照设计图纸施工。
(3)边缘板对接接头的垫板必须卧倒环墙内,避免应力集中。
焊缝尺寸按照蓝图施工。
板铺设时,按照排版图从中心向四周铺设。
垫板与相邻两块底板中的一块先点焊,底板与垫板应贴紧,其间隙不大于1㎜。
(4)中幅板焊接时,应先焊短焊缝,后焊长焊缝,第一层焊道应采用分段退焊或跳焊法。
搭接角焊缝至少焊两遍。
(5)底板焊接完后,检查凹凸度,凹凸变形的深度不应大于变形长度的2%,且不应大于50mm,并对所有焊缝进行真空试验,试验负压值应符合图纸要求。
9.2罐壁组装
9.2.1壁板采用倒装法组装。
组装前,应对预制成型的壁板几何尺寸进行检查,合格后方可组装;当壁板几何尺寸需要校正时,应防止出现锤痕。
(1)底圈壁板或倒装法施工顶圈壁板应符合下列规定:
①相邻两壁板上口水平的允许偏差不应大于2mm,在整个圆周上任意两点水平的允许偏差不应大于6mm;
②壁板的垂直度不应大于3mm;
③
(1)纵向焊缝:
采用焊条电弧焊,当壁板厚度小于或等于10mm时,错边量不应大于1mm;当壁板厚度大于10mm时,错边量不应大于板厚的0.1倍,且不应大于1.5mm;采用自动焊时,错边量均不应大于1mm。
(2)环向焊缝:
采用焊条电弧焊时,当上圈壁板厚度小于或等于8mm时任何一点的错边量均不应大于1.5mm;当商圈壁板厚度大于8mm时,任何一点的错边量均不应大于壁板厚度的0.2倍,且不应大于2mm;采用自动焊时,错边量不应大于1.5mm。
(3)罐壁组装的纵、环向间隙符合GB50128-2014中的规定,如下:
检查用样板符合
9.2.7倒装法施工程序及吊装计算
根据储罐的设计要求,并结合我公司多年来大型储罐的施工经验,本储罐的组装采用“均布立柱倒装法”,即利用均布在罐内的临时立柱(立柱结构见图2.5-1)作为吊装抱杆,立柱之间用架杆或型钢连接固定(示意图见图2.5-2),按倒装顺序,从组装底板、顶盖开始,采用立柱上挂电动葫芦(10t),由上而下逐带板提升,当提升到预定高度时,组焊下一带板。
如此反复,完成全部带板的组对焊接。
提升工艺参数和计算数值
10000m3的提升工艺参数和计算数值
当储罐第二层壁板提升到1.6米高度时,10吨电动葫芦受力最大(所有储罐都用电动葫芦提升,据储罐重量选择电动葫芦个数)。
胀圈和定位板重量:
G2=4T
实际提升最大重量:
G实=180*1.1+4=202T
每台电动葫芦提升重量:
G平均=202/28*1.05=7.58T
电动葫芦提升安全系数及不均匀性:
σ=1.25
每台电动葫芦提升最大重量:
G最大=σ*G平均=9.48T
电动葫芦额定起重载荷:
G额定=10T>9.48T
G额定>G最大
所以设置28台电动葫芦提升罐体符合10000m3储罐提升工艺要求。
电动葫芦提升和和调整(抱杆数量与电动葫芦数量一致,抱杆数量如下)
顶圈壁板、承压板、附件等组装焊接完毕后,电动葫芦在控制柜控制下提升罐前,应先检查和调整各个电动葫芦的倒链松紧程度,尽量保证松紧一致。
提升罐体过程中,若发现有个别电动葫芦提升不均匀,应及时暂停提升,直至将提升不均匀的电动葫芦逐个调整至相同状态,再整体提升,保证提升安全和稳定性。
按上述方法可得出其他储罐立柱(抱杆)根数:
10000m3罐起升重量为180吨(钢板材料代用后),采用28根立柱均布进行吊装。
5000m3罐起升重量为112吨(钢板材料代用后),采用18根立柱均布进行吊装。
1000m3罐总重量为42吨,采用10根立柱均布进行吊装。
500m3罐总重量为25吨,采用6根立柱均布进行吊装。
200m3罐总重量为14吨,采用4根立柱均布进行吊装。
100m3罐总重量为19吨,采用4根立柱均布进行吊装。
提升架的稳定性:
提升架安装时必须垂直,平稳地固定在底板上,并使支架具有足够的稳定性。
9.2.8罐壁的焊接,应先焊纵焊缝,后焊环焊缝。
当焊完相邻两圈壁板的纵焊缝后,
再焊其间的环焊缝。
环向焊缝组对时,用角钢楔子把整个一圈环焊缝对口楔好。
在对中过程中,不点焊固定,整个一圈环焊缝都对好(内壁平齐),检查变形及装配质量,若发现变形要及时处理(否则焊后将难以矫正,且易产生较大应力),然后再在全外环上同时均匀点焊固定(定位焊缝厚度4~6mm,长度15~30mm,间距100~200mm),焊接第一层焊道采用分段退焊或跳焊法,顺序如下图。
顶圈壁板的内半径按下式计算:
Rb=(Ri+nα/2?
)cos?
---------------
(2)
式
(2)中Rb—顶圈壁板安装内半径(mm)
Ri—罐内半径
n—顶圈壁板立缝数量
α—每条立缝焊接收缩量(mm)
?
—基础坡度夹角。
沿着顶圈壁板安装圆周线,每隔1m在内侧焊上挡板,在安装圈外侧60mm处同样焊上挡板,作为组装卡具用限位。
9.3罐顶的组装
(1)
(2)罐顶支撑支柱的垂直度不应大于柱高的0.1%,且不应大于10mm。
(3)罐顶应按画好的等分线对称组装。
顶板搭接宽度允许偏差为±5mm。
9.4附件组装
(1)开孔接管的中心位置偏差,不应大于10mm;接管外伸长度的允许偏差为±5mm。
(2)开孔补强板的曲率,应与罐体曲率一致。
(3)开孔接管法兰的密封面不应有焊瘤和划痕,设计文件无要求时,法兰的密封面应与接管的轴线垂直,并保证法兰面垂直或水平,倾斜不应大于法兰外径的1%,且不应大于3mm,法兰的螺栓孔应在跨中安装。
十、储罐焊接
10.1一般规定
从事储罐焊接的焊工,必须按《特种设备焊接操作人员考试细则》TSGZ6002的规定考核合格,并应取得相应项目的资格后,方可在有效期间内担任合格项目范围内的焊接工作。
焊接前,报合格的焊接工艺评定。
(1)凡是定位焊接及工卡具的焊接,由合格焊工担任。
其焊接工艺应与正式焊接相同。
引弧不应在母材或完成的焊道上。
(2)焊接长度不应小于30㎜;焊接前应检查组装质量,清除坡口面,充分达到干净干燥无污染物。
(3)板厚大于6㎜的搭接角焊缝,应至少焊两遍。
(4)焊接材料设专人保管、烘干、发放,并作焊条烘干发放记录。
焊条、焊剂烘干使用要求如下表
(5)焊材选用:
碳钢焊条J427,焊剂F4A0-H08A焊丝HJ431-H08A;不锈钢焊条A102,焊剂F308-H08Cr21Ni10焊丝SJ601-H08Cr21Ni10;不锈钢与碳钢焊接焊条采用A302,焊接F309-H1Cr24Ni13焊丝H1Cr24Ni13。
焊条烘烤温度如下表:
序
号
焊材名称及牌号
烘干温度
℃
烘干时间
(h)
恒温温度
℃
1
A102
200
1
100~150
2
A302
200
1
100~150
3
J427
350
2
100~150
(6)施焊前应按工艺评定要求编制详细的焊接工艺指导书,焊接应严格按焊接工艺规范进行,不得随意变动焊接工艺参数,焊接前应根据焊接工艺评定编制焊接工艺卡并下发到施工人员手中,并对所有施焊的焊工进行技术交底。
(7)下列情况若无防护措施不得施焊:
风速大于8m/s时的手工电弧焊,和风速大于2m/s时的CO2气体保护焊;相对湿度大于90%;温度低于-10℃。
10.2焊接顺序
(1)罐底的焊接。
应采用收缩变形最小的焊接工艺及焊接顺序,且焊接顺序应符合下列规定:
①中幅板焊接时,先焊短焊缝,后焊长焊缝;初层焊道应采用分段退焊或跳焊法。
②罐底环形边缘板焊接,应先完成靠外缘至少300mm的焊缝,在罐底与罐壁连接的角焊缝焊完后且边缘板与中幅板之间的收缩缝焊接前,完成剩余边缘板的对接焊缝和中幅板的对接焊缝;环形边缘板对接焊缝的初层焊道应采用焊工均与分部、对称施焊的方法进行;边缘板与中幅板之间的收缩缝的初层焊道采用分段退焊或跳焊法。
③非环形边缘板的罐底不留收缩缝。
④罐壁与罐底连接的角焊缝,在底圈壁板纵焊缝焊接完毕后,由数个焊工均匀分部,分别从罐内、外沿同一方向分段焊接,先焊罐内角焊缝,后焊外侧角焊缝。
初层焊道采用分段退焊或跳焊法。
(2)罐壁的焊接顺序
①先焊纵向焊缝,后焊环向焊缝。
当焊完相邻两圈壁板的纵向焊缝后,再焊其间的环向焊缝;采用不对称坡口时,应先焊大坡口后焊小坡口。
②纵向焊缝采用气体保护焊时,自下向上焊接。
采用焊条电弧焊时,焊工均匀分部并沿同一方向施焊。
(3)固定顶板的焊接
①先焊内侧焊缝,后焊外侧焊缝。
径向的长焊缝采用隔缝对称施焊方法,并由中心向外分段退焊。
②顶板与包边角钢或抗拉环、抗压环焊接时,焊工对称均匀分部,并沿同一方向分段退焊。
十一、焊接外观检查
11.1焊缝外观检查前,将熔渣飞溅清理干净。
焊缝表面及热影响区不的有裂纹、气孔、加渣和弧坑等缺陷。
11.2焊缝表面质量应符合下列规定:
(1)焊缝表面及热影响区,不得有裂纹、气孔、夹渣弧坑和未满焊等缺陷。
(2)对接焊缝咬边深度不大于0.5mm,咬边连续长度不大于100mm;每条焊缝两侧咬边的总长度不超过焊缝总长度的10%。
(3)罐壁纵向对接焊缝不得有低于母材表面的凹陷;环向对接焊缝和罐底对接焊缝低于母材表面的凹陷深度不大于0.5mm,凹陷的连续长度不得大于100mm;凹陷的总长度不超过焊缝总长度的10%。
(4)焊缝宽度为坡口宽度两侧各增加1-2mm。
十二、焊缝无损检测
12.1从事焊缝无损检测人员,必须具有国家质量监督检验检疫总局颁发的与其工作范围相适应的资格证书。
12.2罐底焊缝检验应符合下列规定:
(1)所有焊缝应采用真空箱法进行严密性试验,试验负压值不得低于53kPa,无渗漏为合格。
(2)厚度大于或等于10mm的罐底边缘板,每条对接焊缝的外端300mm应进行射线检测