热处理分厂实习报告Word文档格式.docx
《热处理分厂实习报告Word文档格式.docx》由会员分享,可在线阅读,更多相关《热处理分厂实习报告Word文档格式.docx(17页珍藏版)》请在冰豆网上搜索。
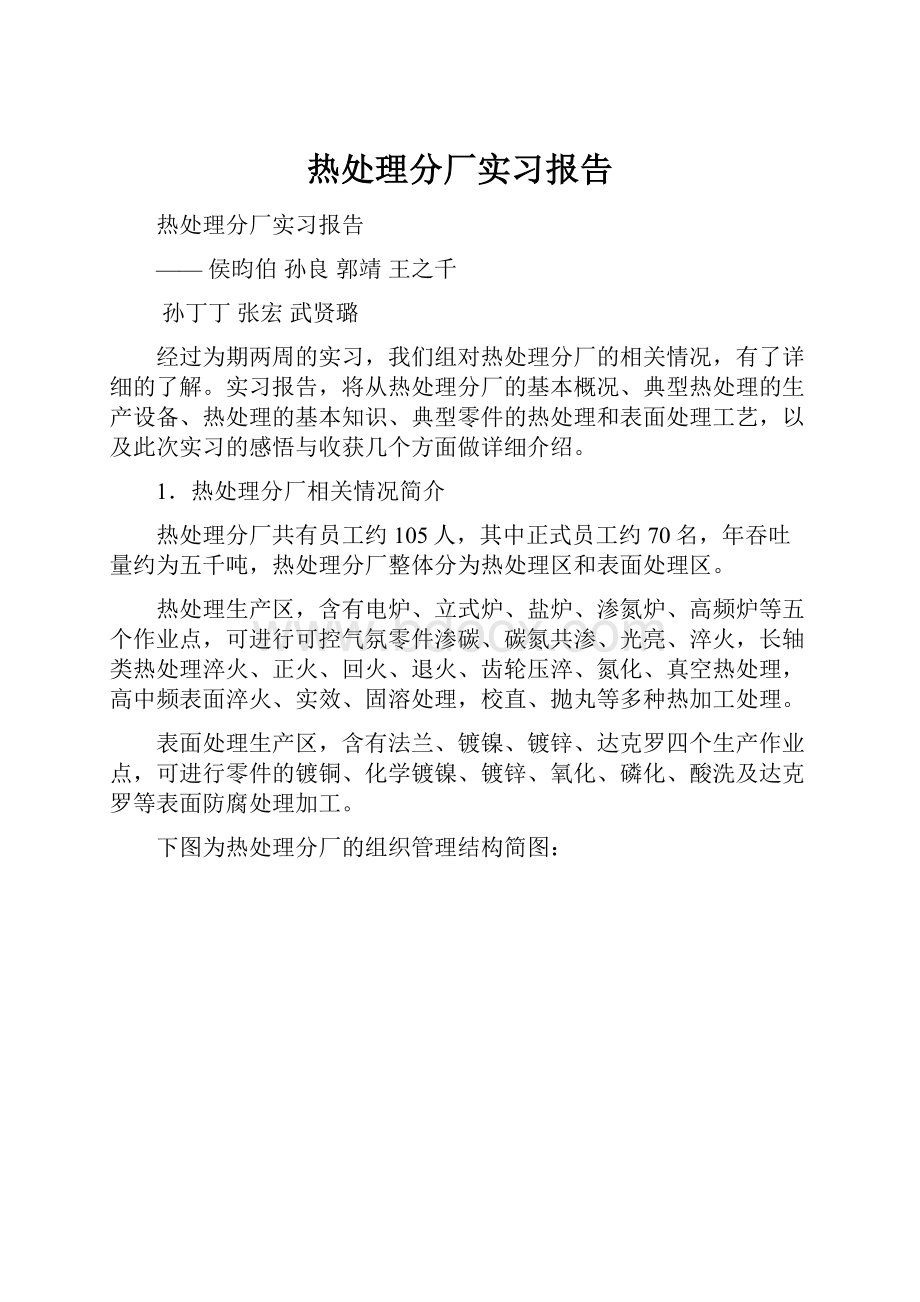
2-80mm/s
内无极调速
工件旋转速度范围:
20—150r/min
冷却方式:
喷液
2.2多用箱式炉
主要技术参数:
型号:
VKEs3-60/65/110CN;
电容量:
180KVA;
工作尺寸:
1100×
600×
650mm;
工作高度:
1400mm
自重:
15000kg
最高使用温度:
950°
C
主要用途:
主要进行渗碳、氢化、油浴淬火等。
它的前室可防止装料时氧气渗入炉内并可保护热处理工件在前中冷却和油浴淬火过程中不致氧化。
炉外有火幕,可大大减少渗入炉内的氧气量,同时防止在前室内形成炉气和空气的爆炸性混合物。
前室中任何可能残存的氧气彻底清除后,才可将工件送入,确保加热室中的炉气组分不因工件的送入而受影响。
前室为双壁结构,用油冷却。
前室可设计为两层,以便将处理后的工件在保护气体中在前室上层进行冷却。
同时可在下层像加热炉装入新料。
前室设有压力释放安全阀,防止前室压力过高。
2.3可控气氛井式炉
加热功率:
110KW额定温度:
700°
主要作用:
气体渗碳、渗氮、氮碳共渗或碳氮共渗、保护气氛下得淬火回火退火。
2.4转底式炉
型号:
RDEs-230功率:
117KW
进料口尺寸:
300mm(W*H)工作高度:
1300mm
12000kg最高工作温度:
AICHELIN转底炉是一种适用于大批量连续生产的热处理设备。
工件装在可转动的炉底上,装料和出料正常为同一炉门。
转底炉的显著特点是:
占地面积小,由于是圆形炉膛,顶部设有风扇,其炉温均匀性好;
炉底由氮化硅砌成,坚固耐用;
整体炉子结构简单,工作期间故障率低,操作简单,维修费用低。
如与等温淬火槽配合并配爱协林的机械手可实现轴承、离合器片等零件的贝氏等温淬火并组成自动化程序很高的自动生产线。
安全装置
·
高压超温保护
低温保护装置,用以在炉温不足750℃时,爆炸性气体不得进入炉内。
氮气自动冲入装置,在突然停电、断气故障发生,氮气自动冲入炉内,防止爆炸混合物的形成,同时炉内件受到中性气体的保护。
炉门火幕防止开门时氧气进入
火幕点火器装置失效,有关装置发出报警信号并使炉们关闭。
2.5盐浴炉
用熔融盐液作为加热介质、将工件浸入盐液内加热。
盐浴炉的加热速度快,温度均匀。
工件始终处于盐液内加热,工件出炉时表面又附有一层盐膜,所以能防止工件表面氧化和脱碳。
盐浴炉可用于碳钢、合金钢、工具钢、模具钢和铝合金等的淬火、退火、回火、氰化、时效等热处理加热,也可用于钢材精密锻造时少氧化加热。
2.6低温回火炉
VKHLE3-60/65/110CN
55KVA
650mm
2000kg
500°
金属机件的回火、正火,退火,淬火用
2.7高温回火炉
KEs3-60/65/110CN
70KVA
2600kg
2.8真空回火炉
由真空炉、高真空抽气机组、储气罐等组成。
真空的主要参数:
WZC-60
料框尺寸:
660×
900×
450mm
最高温度:
1320°
极限真空度:
3.3x10-3Pa
3相100KW
总功率:
<
150KW
12T
适用于软磁材料、硅钢片、电工纯铁、铜合金等材料的光亮退火;
高速钢、模具钢、工具钢、合金钢、钛合金等淬火后光亮回火;
消除锻件、焊接件、冷冲压件、工件淬火后残余内应力,防止工件变形开裂。
2.9各种井式炉
热处理厂里有很多井式炉。
有井式回火炉、井式淬火炉、井式退火炉等。
主要作用是气体渗碳、气体渗氮(或氮碳共渗)、碳氮共渗、保护气氛下的淬火、回火、退火。
2.10台车炉和日本炉
厂子里还有几台台车炉和两台日本炉。
台车炉是箱式电炉。
日本炉基本是出于淘汰的阶段。
两者的作用都是进行淬火。
台车炉主要是对毛坯进行淬火,而日本炉主要是为成品进行淬火、渗碳、氢化等。
2.11强扭机
S68-003A
主要作用是对扭力轴进行预扭力。
以上就是热处理分厂的主要设备。
3.典型零件的热处理工艺
3.1热处理基础知识回顾
金属材料的热处理,是金属材料在固态下,通过适当的方式进行加热、保温和冷却,改变材料内部机构,从来改善材料性能的一种工艺方法。
热处理,分为普通热处理(退火、正火、淬火、回火),表面热处理(表面淬火:
感应加热淬火、火焰加热淬火;
化学热处理:
渗碳、渗氮、渗金属)和其他热处理(形变热处理、超细化热处理、真空热处理)。
3.1.1退火
退火,是将钢加热到预定温度,保温一定时间后,缓慢冷却(通常随炉冷却),获得接近平衡组织的热处理工艺。
退火目的是,降低硬度,改善切削加工性能;
消除残余应力,稳定尺寸,减少变形与开裂倾向;
细化晶粒,调整组织,消除组织缺陷。
3.1.1.1完全退火:
将钢加热到Ac3温度以上30~50度,保温一定时间后,随炉冷却到500度,再出炉空冷。
适用于,亚共析钢和铸件、锻件以及焊接件,使加工过程中,造成的粗大不均匀组织细化,降低硬度,提高塑性,改善加工性能,消除应力。
组织变化:
奥氏体变成铁素体和珠光体
3.1.1.2球化退火:
将钢加热到Ac1以上10~30度,保温较长时间后以及其缓慢的速度,冷却到600度以下,再出炉空冷。
适用于,共析钢和过共析钢以及合金工具钢的退火,降低材料硬度,改善切削加工性能,并减小最终淬火变形和开裂。
网状二次渗碳体和珠光体中的片状渗碳体球化
3.1.1.3扩散退火(均匀化退火):
在1050~1150度,长时间保温(10~15h)后,随炉缓冷。
适用于,合金钢大型铸、锻件,目的是消除其化学成分的偏析和组织的不均匀。
3.1.1.4去应力退火:
在500~600度,充分保温后缓慢冷却到200度,出炉空冷。
适用于,铸、锻、焊件及经过切削加工的零件,目的是为了消除毛坯和零件中的残余应力。
3.1.2正火
正火,是将钢加热到亚共析钢或共析和过共析钢以上30~50度,保温适当时间后,在静止空气中冷却的热处理工艺
正火的目的是,对普通碳素钢、合金钢和力学性能要求不高的结构件,可作为最终热处理;
对低碳素钢用来调整硬度,避免切削加工中的粘刀现象,改善切削加工性能;
对共析、过共析钢用来消除网状二次渗碳体,为球化退火做好组织上的准备。
3.1.3淬火
淬火,是将钢加热到Ac3或Ac1以上30~50度,经过保温后,在冷却介质中迅速冷却的热处理工艺
淬火,可以得到马氏体和贝氏体组织,以提高钢的力学性能,各种工具、模具、量具和轴承需要经过淬火来提高强度和耐磨性。
淬火是强化钢件最主要和最常用的热处理工艺。
冷却介质:
1.水:
廉价、冷却能力强,在500~650度时冷却能力强,对保证工件淬硬有力,在200~300度时,冷却速度大,容易使工件严重变形和开裂。
适用于,过冷奥氏体稳定性较差的碳素钢
2.盐(碱)水
冷却能力比水强,淬火后工件硬度高而均匀,低温冷却速度大,变形开裂更明显,盐水对工件有锈蚀作用,淬火后需要清洗。
盐碱在工件表面析出、爆裂,破坏起隔热作用的蒸汽膜,冷却速度快,同时也能是氧化皮剥落,工件表面更光滑。
适用于,形状简单、淬硬层要求较深、硬度高而均匀、表面要求光洁、变形要求不严的碳钢零件。
3.油(主要是矿物油,常用的是10号机油)
油的粘度大,流动性差,冷却能力低,对于200~300度时马氏体的转变有利,可以有效减少变形开裂,在500~650度时冷却能力差,容易造成碳素钢中奥氏体分解而淬不硬。
适用于,过冷奥氏体比较稳定的合金钢淬火。
3.1.4表面淬火
表面淬火,是将淬火零件表层金属迅速加热至相变温度以上,而心部未被加热,然后迅速冷却,使零件表面获得马氏体而西部仍未原始组织的热处理工艺。
适用于,承受弯曲、扭转等交变载荷及冲击载荷并在摩擦条件下工作的零件,如齿轮、轴等,不但要求表面高硬度、高强度、耐磨性和疲劳强度,还要求心部有足够塑性和韧性的零件。
3.1.5回火
回火,是将经过淬火的零件重新加热到低于Ac1的某一温度,适当保温后,冷却到室温的热处理工艺。
回火的目的是,消除或降低应力,降低脆性,防止变形和开裂;
稳定组织,稳定尺寸和形状,保证零件使用精度和性能;
通过不同回火方法,调整零件的强度、硬度,获得所需要的任性和塑性。
3.1.5.1低温回火(150~250):
得到回火马氏体,降低钢的淬火应力和减小脆性,并保持高硬度和高耐磨性。
适用于,刃具、量具、磨具、滚动轴承及渗碳、表面淬火零件。
3.1.5.2中温回火(350~500):
得到回火托氏体,获得高的弹性极限和屈服强度,并具有一定的韧性和抗疲劳能力。
适用于,各种弹簧钢和锻模等。
3.1.5.3高温回火(500~650):
得到回火索氏体,获得高强度的同时,还有较好的塑性和韧性。
适用于,受交变载荷和冲击的连杆、曲轴、齿轮和机床主轴等,也常作为精密零件和模具、量具的预备热处理。
3.1.6化学热处理
化学热处理,是将工件置于一定温度的活性介质中保温,使一种或几种元素深入表层,以改变其化学成分、组织和性能的热处理工艺。
3.1.6.1渗碳
应用于,表层要求高硬度、耐磨性及疲劳强度,而心部要求一定强度和高韧性的零件,如:
汽车主轴和变速箱齿轮等。
渗碳材料,需要经淬火、低温回火来满足性能。
分气体渗碳和固体渗碳。
3.1.6.2渗氮
应用于,要求表面高硬度、耐磨性、疲劳强度和抗蚀性零件(比渗碳更硬)。
渗氮层很薄、很脆,要求有较高强度的心部组织,渗氮前需调质处理。
应用最广泛为气体渗氮(氨气)。
3.1.6.3碳氮共渗
应用于,碳素钢、合金钢、工具钢、模具钢、铸铁等材料。
碳氮共渗后,不需要在进行其他热处理。
分为中温碳氮共渗(820~860)和低温碳氮共渗(500~570)。
3.2扭力轴的热处理工艺简介
棒料、镦粗、校直、冷压花键、淬火加高温回火、校直、二次回火(重量在30t以上的车需要此步骤)、喷砂、表面精磨、滚压表面、预扭、磷化处理、喷砂、挂胶(水陆两栖车辆需要此步骤)。
4.典型零件的磷化处理及表面处理工艺
4.1扭力轴的磷化工艺
由于扭力轴工作环境负荷大而且摩擦力也很大。
磷化主要是用来加工扭力轴使其产生磷化膜,在后续加工中易于涂漆,并能加漆牢固,工件在使用中不容易生锈和氧化,给基体金属提供保护,提供清洁表面。
(磷化膜只有在无油污和无锈层的金属工件表面才能生长,因此,经过磷化处理的金属工件,可以提供清洁、均匀、无油脂和无锈蚀的表面。
),且在金属冷加工工艺中起减摩润滑使用。
扭力轴在表面处理之前先需要锻造,挤压以及热处理等工序。
这些工序分别在七车厂,十三车厂,机加工厂及热处理厂完成。
在经过表面处理后就可以投入使用了。
4.1.1按磷化处理分类
4.1.1.1按温度分类
高温型:
80—90℃处理时间为10-20分钟,形成磷化膜厚达10-30g/m2,溶液游离酸度与总酸度的比值为1:
(7-8)
优点:
膜抗蚀力强,结合力好。
缺点:
加温时间长,溶液挥发量大,能耗大,磷化沉积多,游离酸度不稳定,结晶粗细不均匀,已较少应用。
中温型:
50-75℃,处理时间5-15分钟,磷化膜厚度为1-7g/m2,溶液游离酸度与总酸度的比值为1:
(10-15)
游离酸度稳定,易掌握,磷化时间短,生产效率高,耐蚀性与高温磷化膜基本相同,目前应用较多。
低温型:
30-50℃节省能源,使用方便。
常温型:
10-40℃常(低)温磷化(除加氧化剂外,还加促进剂),时间10-40分钟,溶液游离酸度与总酸度比值为1:
(20-30),膜厚为0.2-7g/m2。
不需加热,药品消耗少,溶液稳定。
处理时间长,溶液配制较繁。
4.1.1.2按磷化液成分分类
(1)锌系磷化
(2)锌钙系磷化
(3)铁系磷化
(4)锰系磷化
(5)复合磷化磷化液由锌、铁、钙、镍、锰等元素组成。
4.1.1.3按磷化处理方法分类
(1)化学磷化
将工件浸入磷化液中,依靠化学反应来实现磷化,目前应用广泛。
(2)电化学磷化
在磷化液中,工件接正极,钢铁接负极进行磷化。
4.1.1.4按磷化膜质量分类
(1)重量级(厚膜磷化)膜重7.5g/m2以上。
(2)次重量级(中膜磷化)膜重4.6-7.5g/m2。
(3)轻量级(薄膜磷化)膜重1.1-4.5g/m2。
(4)次轻量级(特薄膜磷化)膜重0.2-1.0g/m2。
4.1.1.5按施工方法分类
(1)浸渍磷化
适用于高、中、低温磷化特点:
设备简单,仅需加热槽和相应加热设备,最好用不锈钢或橡胶衬里的槽子,不锈钢加热管道应放在槽两侧。
(2)喷淋磷化
适用于中、低温磷化工艺,可处理大面积工件,如汽车、冰箱、洗衣机壳体。
特点:
处理时间短,成膜反应速度快,生产效率高,且这种方法获得的磷化膜结晶致密、均匀、膜薄、耐蚀性好。
(3)刷涂磷化
上述两种方法无法实施时,采用本法,在常温下操作,易涂刷,可除锈蚀,磷化后工件自然干燥,防锈性能好,但磷化效果不如前两种。
4.1.2扭力轴磷化工艺流程
扭力轴分为正反(左右)。
车型的不同对应不同的扭力轴,比如有502,534,5008型。
这些都是用于不同的装甲车辆上的。
磷化工序由于扭力轴精度的不同,其工序顺序也不同。
对于扭力轴或者精度高的工件在加工之前是不能过酸,而比较粗糙或者毛坯件必须过酸才可以继续加工。
磷化的基本工艺顺序主要是:
除油—酸洗—磷化—皂化—侵油
1、去油过程
主要用脱脂王剂在80-90℃的温度下搅拌完成,时间大约20分钟,不过根据工件的不同时间略有差异。
2、酸洗过程
使用工业水和稀盐酸(3:
1弱酸)去锈,直到肉眼看不到锈为止,但酸洗结束后必须水洗才可以进行下一道工序。
3、磷化过程:
磷化有两个槽,一种是清槽,一种是浊槽。
清槽主要处理没有过酸的工件(高精度,扭力轴),浊槽则处理过酸的工件。
磷化过程大约需要15分钟左右。
水洗后进行皂化过程。
4、皂化过程
作用是封孔,填充工件上的沙眼使工件工作时不暴露在空气中,防止生锈。
皂化完成后吹干工件,侵油经检查员检查合格后送往一分厂进行涂漆即可投入使用。
5、涂胶
当然有时工件也需要涂胶。
这主要是用于装甲车辆上防海水腐蚀,防雷达侦查。
4.2表面处理工艺
4.2.1镀镍
镀镍的工艺流程:
装挂工件→电解除油→流动冷水洗→酸洗→流动冷水洗→镀镍→退蜡→热水洗→烘干→浸油
说明:
①镀镍槽分为A、B、C三个槽。
其中A槽中主要是用来镀镍的溶液;
B槽中是光亮剂;
C槽中是化学反应剂,使所镀的镍更好的结合在工件表面。
②退蜡的目的是之前工件不需镀镍的局部表面涂上了蜡,镀镍结束后需要退蜡。
③浸油的目的是为了填堵砂眼,有防锈的作用。
④镀镍需要镀1~3道,整个工艺流程需要2个小时左右。
⑤镀镍工件防海水,不防淡水,即在海水里面不容易生锈。
⑥镀镍工件不容易折断。
⑦镀镍槽中的溶液,活少时20天一换,或多时1周一换,换一次溶液可加一千个螺母、螺栓工件。
⑧电解除油,流动冷水洗,酸洗,流动冷水洗,这几个工序需要重复进行直至油锈除尽。
所存在的问题:
①缺少烘干机。
②缺少退镍工序。
之前工厂用硝酸退镍,由于处理过程中有大量黄烟,极度影响工作环境因此取消了。
需退镍时,工件被送到专门退镍厂处理,浪费时间且加大成本。
③技术设备落后,设备更新速度慢,效益低。
④工人缺少专业知识,且工作效率低。
4.2.2镀锌
镀锌的工艺流程:
①不需钝化:
装挂工件→电解除油→流动冷水洗→强酸洗→流动冷水洗→弱酸浸蚀→流动冷水洗→碱性镀锌或钾盐镀锌→热水洗→出光→热水槽→压缩空气吹干
②需要钝化:
装挂工件→电解除油→流动冷水洗→酸洗→流动冷水洗→弱酸浸蚀→流动冷水洗→碱性镀锌或钾盐镀锌→热水洗→出光→热水槽→钝化→流动冷水洗→压缩空气吹干
①利用钾盐镀槽镀出的工件比碱性镀槽镀出的工件色泽更为光亮。
②光化主要用于加工白色工件(“白件”),使其变色并且产生一层保护膜。
③钝化主要用于加工彩色工件,相对于白件,钝化处理后的工件较防锈防腐。
④光化结束后用热水清洗,钝化结束后用冷水清洗。
⑤镀锌整个工艺流程需要2个小时左右。
⑥若所镀的工件较小,如螺栓螺母,则可用滚镀镀锌。
⑦电解除油,流动冷水洗,强酸洗,流动冷水洗,弱酸浸蚀,流动冷水洗,这几个工序需要重复直至油锈除尽。
⑧强酸浸蚀采用浓度为1:
1的盐酸溶液,在常温下进行30分钟以下,防止过腐蚀。
⑨弱酸浸蚀在50~100g/L的稀硫酸中,室温下进行0.5~1分钟,保证镀锌零件表面无氧化膜。
①缺少压缩空气吹干机。
②冬天输送液体时管道易冻坏。
③技术设备落后,设备更新速度慢,效益低。
④工人缺少专业知识,且工作效率低。
⑤工艺工程较为繁琐。
5.实习感悟
经过为期两周的生产实习,我们在这次实习过程中有了一些感悟和体会。
在九月十号,我们怀揣了兴奋与好奇的心情进入了北方车辆汽车厂开始了为期两周的生产实习。
初入工厂,我们对工厂的各个方面有了各种各样的好奇,同时产生了去探索、去学习、去收获的强烈兴趣。
开始的几天我们进行了入厂教育,北方车辆厂的各个部门的工作骨干们牺牲了自己工作的时间,为我们授课,用自己的亲身经历工作经验为我们传授知识,将复杂、拗口、难懂的要点讲的深入浅出、活灵活现。
在这个不同于大学上课的课堂上,我们也学到了不同于课堂的知识。
之后我们便进入了工厂开始实习,我们组分到了热处理分厂,进入热处理厂的第一感官就是“热”。
一路走过去,股股热浪迎面而来,吸入的空气不仅仅是热,还伴随着各种各样的气味。
这样的生产条件是我们从课本中无法体会到的。
作为未来的工程师,去体验一下一线的生产条件我觉得确实是很必要的,不去体验,不能知道一线工人的苦,也就不能从他们的角度对生产进行规划。
进入热处理分厂后,我们的生产实习基本上就是自主式的实习,没有了约束,我们可以对我们感兴趣的内容集中进行学习。
我们先后对热处理与表面处理的各个环节进行了探索与学习,在这里要说一句,我们所实习的分厂的工人们对我们的实习还是很支持的,有问必答,虽然有时候说出来的并不是我们想要的答案,但我们能感觉出来,他们已经尽力的用他们知道的知识和经验进行讲解了,虽然他们听不到,但我还是要在这里感谢他们一下。
没有他们的支持与理解,我们的实习举步维艰。
我们在实习过程中感觉到,实际学习到的有关工厂生产的知识和在一线的工人们真正的工作运用其实相差甚远,课本上一句话的内容可能需要工人们几年甚至十几年的揣摩才能达到熟练,而课本上好几页甚至一章节的内容有可能只是工人们一个非常简单的动作,而我们去询问工人们的时候,他们大多也不太明白,只知道需要这样做,原因没人和他们说过。
仔细去考虑,其实这个也不是生产与课本的脱节,只是不同人需要掌握的程度不一样,掌握的方面不一样,工人掌握每一个动作每一道工序的含义固然有好处,但对于生产就是一个熟练的过程,相信不会有哪个人去加工一个部件还要背一遍他的加工原理,只是按照自己熟悉的一个过程用最快的速度完成工序。
要真是那样,生产必然会变慢,效率会低下,这样就没有任何意义了。
而对于我们,去操作的机会很少,但去研究或者设计的工作会很多,那么这些课本的知识就显得举足轻重了。
同样,这也就显示出我们这些未来的设计者计划者到达工厂最前线实习的必要,也只有这样,才能很好的将理论与实际相结合。
相信这也是学校把我们送到工厂实习的目的和意义所在了吧!
虽然两周的实习时间不长,但给我们这些身处象牙塔的学子们确是上了很好的一课,使我们受益匪浅!