#2机组改造培训资料1Word下载.docx
《#2机组改造培训资料1Word下载.docx》由会员分享,可在线阅读,更多相关《#2机组改造培训资料1Word下载.docx(84页珍藏版)》请在冰豆网上搜索。
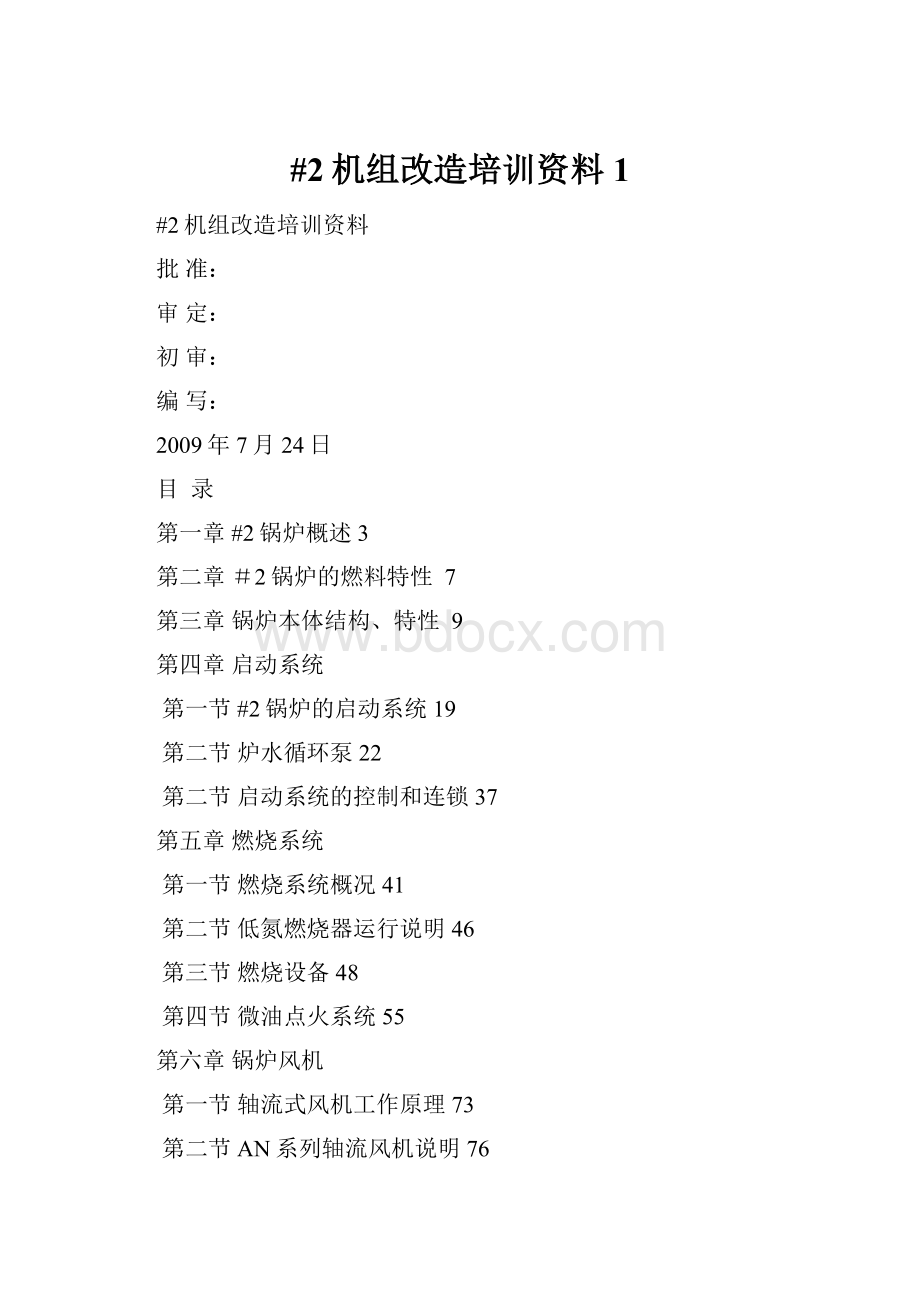
5.5内螺纹鳍片管,上辐射为¢25×
6鳍片管组成模式水冷壁。
锅炉采用悬吊结构,本体成为一个大吊笼向下膨胀,除回转式空气预热器外,其余重量均悬吊在K1、K2、K3、K4钢筋水泥柱支撑的4根炉顶大板梁上。
锅炉本体采用水泥平台与钢板网平台间隔布置,自12M以上设立五层水泥板平台,每层相距7.2M,中间每隔3.6M布置一层钢板网平台。
锅炉设有4级过热器,过热器系统按蒸汽流向可分为:
顶棚和包墙过热器、低温过热器、屏式过热器及高温过热器;
锅炉再热器系统由低温再热器和高温再热器两级组成;
锅炉布置有1级省煤器。
按烟气流向,炉顶和水平烟道顺次布置屏式过热器、高温过热器和高温再热器,竖井烟道顺次布置低温再热器、低温过热器和省煤器。
锅炉在低温过热器和屏过热器、屏式过热器和高温过热器之间,各设置1级过热喷水减温器;
在低温再热器进出口各设1级再热喷水减温器。
一次汽的调温主要靠煤、水比调节并设有两级喷水减温。
二次汽的调温原设计为烟气再循环主调,辅助于喷水微调,但后来烟气再循环拆除。
现在再热器调温靠喷水调节,在再热器中间集箱连接管上设有喷水点作为汽温调节,在低再入口设有事故喷水装置。
一次汽的汽水系统分左右二个独立回路,中间始终不相交叉混合,借助燃烧与给水的调整,控制左右二个回路的热偏差。
而二次汽系统开始也分左右二路进入低温再热器,在中间集箱后左右二路相互交叉,最后在高温再热器出口集箱再进行一次奇偶数的混合,使左右汽温获得均匀一致。
制粉系统采用钢球磨中间储藏干燥剂送粉,燃烧器呈四角切圆布置共8组,每组有4排一次风管和5排二次风管。
炉内负压燃烧、固态排渣,采用链条刮板式捞渣机,出口有碎渣机。
尾部受热面采用旋转的容克式回转空气预热器,每炉两台,并列布置直接支撑于基础上。
锅炉配有4套中间储仓式乏气送粉制粉系统,配有4台DZM380/650型钢球磨煤机、4台SW-CB轴向封闭三型粗粉分离器、4台细粉分离器和4台6-30-NO191/2型排粉机,每套制粉系统带1层8只煤粉喷燃器,制粉系统采用钢球磨中间储藏干燥剂送粉。
锅炉采用直流燃烧器,双炉膛共8组燃烧器,每组燃烧器有4层一次粉喷嘴和5层二次风喷嘴,一二次风喷嘴相间布置,均等配风。
锅炉风烟系统由送风系统和对流烟道组成。
配有两台轴流式送风机、两台轴流式引风机、两台风罩回转式空气预热器。
二、主要特点
**#2锅炉属国产的早期产品,它基于前两台配30万千瓦机组的锅炉,即一台为望亭电厂1000T/H燃油炉和**电厂原#1机组935T/H燃煤锅炉。
而#1锅炉为刚刚改造完成的锅炉,改造后达到预期的效果。
#2炉与#1炉相比最大的不同点在于:
炉膛高度加高了2.81m,深度加深了0.42m,而尾部比原来加深了1m。
因为炉膛中间布置有一次上升全高度分隔管屏。
水冷壁采用内螺纹管膜式结构,且采用小管径一次上升的管圈,因此使得水动力特性对炉室燃烧工况的反映比较敏感,为使水冷壁安全运行,原设计水冷壁中采用了较高的重量流速,在100%负荷时,原设计流速为∮w=1927kg/m2.sec,双面水冷壁∮w=2050kg/m2F.sec。
锅炉的内螺纹管是老式内螺纹管,防止膜态沸腾的效果不佳,因此,该锅炉水冷壁壁温波动和传热恶化的现象十分明显,尤其在低负荷下,由于水冷壁管圈内加热水区段阻力与蒸发段阻力比变小,很容易产生水动力不稳的现象。
由于采用的小管径管屏,所以管屏的刚性较差,在外来的干扰下,容易发生振动和变形,影响机组安全运行。
由于管径小,热敏感性强造成局部水冷壁壁温高,很容易发生壁温腐蚀。
为解决热敏感性过强带来的热负荷不均的影响,用节流阀过分节流,结果使得通过阀心处的流速较高,压降过大,往往导致局部汽化、析盐,从而回影响锅炉正常运行。
本次改造以后,锅炉仍是一个独立的主体和双炉膛的布置和来自八个角的燃烧器的或切线的燃烧。
该锅炉采用低质量流量的垂直螺旋管,属于一次通过的亚临界型。
在考虑不导致改造装置的寿命和性能造成有害影响的基础上,在可能的场合,尽量保留现有的设备,所以对尾部新近更换过的设备尽量保留。
改造的锅炉对框架或基础无变化、外形和尺寸实际上也无变化。
三、主要技术规范:
锅炉容量及主要技术参数:
序号
参数名称
单位
原设计值
实际运行值
1
额定蒸发量
T/h
1000
2
主汽压力
Mpa
16.67
16.3
3
主汽温度
℃
555
545
4
再热蒸汽流量
830
5
再热器进/出口压力
3.43/3.24
3.34/3.3
6
再热器进/出口温度
325/555
342/545
7
给水温度
265
264
8
热风温度
320
327
9
炉室出口温度
1201
10
炉室容积热负荷
103W/m3
173.9
11
排烟温度
130
150-180
12
排烟热损失q2
%
6.68
7.0-8.3(试验值)
13
机械未完全燃烧热损失q4
2.0
0.4-0.6(试验值)
14
灰渣物理热损失q6
0.5
0.25-0.35(试验值)
15
散热损失q5
0.3
0.35
16
锅炉效率
90.52
90.3-91.0(试验值)
四、锅炉给水及蒸汽品质要求
1.锅炉给水质量要求
名称
符号
数据
计量单位
硬度
≈0
μmol/L
硅酸根
SiO2
20
μg/L
氧
O2
铁
Fe
铜
Cu
导电度25℃
<
μs/cm
联胺
N2H2
10~30
钠
Na
PH值
8.8~9.3
总盐量
mg/L
2.蒸汽品质要求
钠<10μg/L
二氧化硅<20μg/L
电导率25℃<0.20μS/cm
铁≤10μg/L
铜≤5μg/L
3.自然环境条件
锅炉0.00m海拔高度:
102.5m
绝对最高气温:
+42.6℃
绝对最低气温:
-18.8℃
年平均气温:
14.9℃
历年平均大气压力:
1006.7hpa
年最大降雨量:
1323.6mm
年最小降雨量:
373.9mm
年平均降雨量:
754.6mm
年平均相对湿度:
67%
最大风速(瞬时):
39.7m/s
年平均风速:
3.2m/s
基本风压:
0.44KN/m2
夏季主导风向:
NE频率9%;
冬季主导风向:
NE频率14%
抗地震烈度为6度,按7度设防
最大冻土深度:
14cm
基本雪载:
0.245KN/m2
五、钢结构
现有#2锅炉混凝土框架,平台布置基本不变,只是由业主方设计院根据巴布科克能源公司提供的荷载进行混凝土梁柱和基础的较核,必要时加固梁柱。
巴布科克能源公司会根据压力部件的增减变化导致的荷载变化情况较核所有相关钢结构杆件,包含顶板范围内的大板梁、主梁、次梁,顶部的吊杆过渡梁,原有的管道支架,更换后的平台扶梯支撑件等。
根据荷载较核情况,以及现场观察原有钢结构杆件的变形情况,对其进行必要的更换或加固。
对于新增的压力部件,在需要处增加相应的悬吊、支撑杆件,并对承受该杆件的主钢结构件同样进行较核及必要的加固。
由于门孔和各操作件的位置基本不变,平台扶梯在满足锅炉改造后的运行维护、检修需要的前提下布置也基本不变。
但原钢平台各部件大部分均已变形老化,所以此次对所有原钢结构平台的支撑、平台框架、栏杆、格栅板、踢脚版均重新更换,并根据新的承载能力要求重新计算这些部件的大小、规格。
原混凝土屋顶也已经破损、老化,需要拆除。
此次将重新设计新的钢结构彩板轻型屋盖代替。
生根在混凝土结构上的钢结构件,需根据荷载计算的结果,提供荷载、接口尺寸供业主设计院进行局部和整体的较核。
同时积极配合业主设计院进行必要的修改设计。
所有钢结构设计均遵循各相关国家规范和招标文件中的各项详细要求。
第二章#2锅炉的燃料特性
一.煤质资料表:
项目
单位
设计煤种
校核煤种(Ⅰ)
校核煤种(Ⅱ)
工
业
分
析
收到基低位发热量Qnet,ar
MJ/Kg
18.34
16.30
19.97
全水分Mar
%
7.3
9.36
6.5
内在水分Mad
0.94
1.50
0.70
收到基灰分Aar
35.73
39.51
32.01
干燥无灰基挥发分Vdaf
33.08
28.50
35.05
炉灰可燃物CR
元
素
收到基碳含量Car
47.51
42.79
51.51
收到基氢含量Har
3.10
2.95
3.35
收到基氧含量Oar
4.85
3.57
5.31
收到基氮含量Nar
0.75
0.67
0.85
收到基全硫含量St,ar
0.76
1.15
0.47
可磨系数Kkm
1.4
灰熔点t1
>1350
灰熔点t2
>1450
灰熔点t3
>1500
二.设计煤煤灰成分:
校核煤种1
校核煤种2
会
成
份
61.07
\
Fe2O3
3.02
Al2O3
28.8
TiO2
1.00
CaO
1.81
MgO
0.63
K2O
1.05
Na2O
0.37
P2O5
其它
三、燃油特性
目前,#2锅炉燃用原油,2007年,姚电公司计划完成#2锅炉燃油系统改造,改造后锅炉将燃用#0轻柴油。
锅炉设计时,应按锅炉燃用#0轻柴油考虑。
下列数据是姚电公司拟采用的#0轻柴油的技术特性。
设计油种:
#0轻柴油
运动粘度(20℃时)3.0~8.0mm2/s
硫含量≤0.2%
水份痕迹
机械杂质无
凝固点≯0℃
闭口闪点不低于65℃
灰份≤0.02%
低位发热值Qnet.ar约41800kJ/kg
第三章锅炉本体结构
一、锅炉总体布置情况见下图:
图11025t/h亚临界压力直流锅炉
1-前屏过热器;
2-后屏过热器;
3-高温过热器;
4-低温再热器;
5-高温过热器;
6-低温过热器;
7-省煤器;
8-空气预热器
二、炉膛
改造后:
拆除分隔墙,设置较大口径的管子,因为分隔墙的管子为双面受热结构,其需要更高的质量流量以使管子得到足够的冷却,而更高的质量流量使得分隔墙对炉堂中的热偏差更敏感,所以只有采用较高的本森负荷才能维持动态稳定性,而分隔墙中又无法布置中间联箱,中间联箱功能就是降低温差,使温度分布更均匀。
但分隔墙中无法布置中间联箱,对分隔墙的运行表现相对于外墙大打折扣。
所以本次决定取消分隔墙管。
其他四周部分维持原外形结果,但管子形式采用西门子的专利技术的螺旋槽管。
下炉膛及折焰角区域均采用优化的内螺纹管,上炉膛采用光管,本森负荷30%,增加中间联箱;
炉膛四周设计1014根管子,下炉膛管子为33.7x5.12mm,质量流速为720kg/m2s,上炉膛管子为28.58x4.5mm,质量流速为1000kg/m2s,材料为15CrMo。
改造后的垂直管结构新炉膛设计呈现出下列优点:
有较低的炉膛压力损失,允许达到1025te/小时高压蒸汽的产出能力;
正向的流动响应特征;
消除了不可接受的温度差;
关于荷载范围和荷载改变的充分的操作灵活性;
滑动的压力操作和较低的加热比例;
通过在炉膛出口设置分隔屏,使得炉膛出口气体温度基本不变;
容易的管子布置和安装;
在“本生(Benson)”负荷以上运行时,在管子内部发生了全部蒸发和部分过热。
炉膛壁利用了一些不同的管子尺寸,实现了需要的静态和动态稳定性。
在30%BMCR以下的负荷(例如,在开车和停车期间)时,此炉膛壁与分离器开车系统一起,形成一个循环系统的一部分。
这就保证了在炉膛壁中的流量不降低到低于30%的BMCR流量以下。
在大于30%BMCR负荷时,炉膛壁提供了过热蒸汽,该过热蒸气通过分离器到炉顶和其后进行过热的各级装置。
在炉膛壁中蒸汽的产生基本上是由吸收燃烧过程中的辐射热而实现的。
锅炉的燃烧及炉膛出口烟气温度场的分别较改造前没有发生较大改变,但水冷壁运行安全性得到了很大提高。
喷燃器改造后,各喷嘴区域热负荷均匀性有了较大改善,炉内不结焦;
由于喷燃器带偏置侧二次风,有效抑制了还原性气氛的形成,防止水冷壁高温腐蚀产生。
锅炉在多次启停及长时间低负荷运行期间,均未发生水冷壁泄漏。
三、水冷壁
水冷壁的功能是使来自省煤器和下降管的锅炉给水产生需要数量的饱和或过热蒸汽,也是本次需要改造的重点。
1、流量特性
改造前水冷壁管高质量流速呈负流量响应特性,温度最高的管子所需的冷却水流量本应最大,而实际流量最小;
而温度最低的管子所需的冷却水流量本应最小,而实际流量却最大,这就导致了金属温度升高并产生热应力。
改造后水冷壁管低质量流速呈正流量响应特性,需要冷却流量高的管子的实际流量也相对较高,这就限制金属温度和热应力。
由于水冷壁采用了低质量流速、正流量响应内螺纹管,使水冷壁具有了自补偿特性,能有效地消除由于热偏差引起的水动力恶化,解决水冷壁管间温度偏差大的问题,确保了水冷壁水动力稳定和不发生DNB,杜绝了水冷壁管经常超温、泄漏和爆管的隐患,并防止水冷壁高温腐蚀。
2、结构上改造
改造后取消双面水冷壁,拆除原水冷壁管屏,重新安装,改造后水冷壁进、出口集箱材质SA106C/15CrMo,水冷壁管屏材质15CrMo;
中间集箱及连接管材质SA106C,水冷壁进、出口导管及进口分配器材质SA106C;
包括水冷壁悬吊装置,连接管、进口分配器支吊装置;
炉底挡火板及密封板,重新设计安装。
起:
水冷壁进口分配器(包括分配器)
止:
水冷壁出口联箱(包括联箱)
a)全部水冷壁管屏(包括第一悬吊管)及其联箱;
水冷壁悬吊装置及附件。
b)连接管、支吊装置及其附件等。
c)水冷壁进口分配器及其支吊装置、附件等。
d)放水管道,放气一次门前管路,取样一次门前管路及,支吊装置及附件。
一次门后由电厂采购。
f)水冷壁冷灰斗及水封槽插板
四、过热器系统
原过热器的蒸汽流程:
炉顶过热器——大直径下降管至分配器——水平烟道和后烟井四周包覆管——大直径下降管——低温过热器——后烟井受热面悬吊管——第Ⅰ级喷水减温器——屏式过热器——第Ⅱ级喷水减温器——高温过热器——至汽机高压缸。
主蒸汽的参数为:
P=170kg/cm2;
t=555℃。
改造后过热器的蒸汽流程:
炉顶过热器——大直径下降管至分配器——水平烟道和后烟井四周包覆管——大直径下降管——低温过热器——后烟井受热面悬吊管——第Ⅰ级喷水减温器——前屏过热器——后屏式过热器——第Ⅱ级喷水减温器——高温过热器——至汽机高压缸。
顶棚过热器因为考虑到现锅炉的漏风较大,所以本次顶棚过热器将重新设计为膜式壁形式。
管子规格及节距为:
φ51×
6,节距90mm,共188根;
炉顶过热器进口集箱、出口集箱规格为Φ323.9*44,材料为A106C。
五、屏式过热器
本次屏式过热器改造主要是在炉膛上部新增加了20片辐射过热器即前屏过热器,其目的是为了达到取消了分隔墙后仍可达到设计的炉膛出口烟温。
使得下游受热面的工艺参数没有改变,从而无需修改下游的压力部件。
前屏过热器总共20片,每片16只管子管子,外径44.5mm,壁厚7.0mm质量流速为1152Kg/m2s,材料为12Cr1MoV,外三圈为T91。
其他的受热面的更换是考虑到有些部件使用寿命已经已经到期,所以过时的构件将用由优质材料制作的新构件来替换。
同时,保留原来的布置和加热表面。
六、包覆管
由炉顶过热器出口集箱引左右二根¢325×
35大直径下降管至分配器,分配到后烟井的前、后墙二侧墙和水平烟道的底部为该部分的包墙管,轻形炉墙就敷设在管子一并悬吊在过热器上,可大大简化炉墙结构。
包墙管回路采取炉外一次下降,炉内一次上升,为保持具有一定上升流速,管径为¢38×
5.5,20A,节距很大,按照不同部位的热负荷通过计算,在水平烟道底部和二侧包墙管S=76,后烟井四周包墙管S=106,由管子焊扁钢组合为单根鳍片管出厂,在工地总装时和集箱一起拼焊成管屏,重量流速§
w=600~820,为使各回路有一定的重量流速,在后烟井二侧和后墙包墙管的进口处装有孔径为12.5节流圈.包墙管与炉室水冷壁一样,组成管屏总装时在工地装上刚性梁,刚性梁结构也与炉室相同,在包墙管各部设有不少人孔门,在门孔处系光管弯制,其管间空隙应以扁钢嵌焊,以免炉墙烧坏。
改造更新范围如下:
1)水平烟道两侧墙及进出口联箱,水平烟道底部及进出口联箱。
2)水平烟道两侧墙、尾部烟井四周包覆墙悬吊装置及其它附件。
3)包覆过热器管屏人孔门区域弯管及其部分直管段。
4)包覆过热器悬吊管
本次改造范围内未对包覆管进行更新。
七、低温过热器
由包墙管出来的蒸汽,其参数为P=184kg/cm2*,T=384℃,L=665.5kcal/kg,设计选择该点作为控制甲、乙炉膛热偏差的中间点讯号,汽温约微过热25℃左右,在锅炉启动阶段即该点接往启动分离器。
接往低温过热器也由左右二根¢325×
35大直径下降管一次引进低过进口集箱(¢325×
35,材料10CrMo910)。
低温过热器分上、下二组,布置中间留有800mm空挡供安装检修,并布有必要人孔门。
蛇行管规格为¢42×
35,材料为10CrMo910,双根套管错列布置,节距S1=160,S2=60,每组的上面二排和管子弯头上设有防磨罩,材料为Cr6SiMo,整个低温过热器蛇行管由管夹定位,并通过它悬吊在上部梁上所有管夹和连接板材料均为Cr6SiMo。
上部吊耳吊梁为12Cr1MoV,下部梁为12CrMo,进出口集箱都位于高温烟气中,烟温为480~580℃区域,对集箱与梁在安装中必须加敷耐热保温层,以防钢材烧坏变形。
整个低温过热器的金属重量约185T,上下二组共422排。
由低温过热器出口分二组出口集箱¢273×
36,10CrMo910,由它引出三排吊挂管,每排62根,管子规格为¢60×
7,材料为15CrMo,整个后烟井中省煤器、低温过热器、低温再热器的金属总重约600T,(不包括水、保温层等重量在内)都通过三排吊挂管悬吊于炉顶过渡梁上,因此对管材的钢种和焊接,要求严格检查,保证质量。
改造更新设备如下:
1)进口联箱更换。
2)出口联箱更换(炉内、炉外)。
3)尾部烟井悬吊管更换。
4)低温过热器出口联箱到新增前屏进口联箱导管部分保留再利用,原启动系统简化,在低过出口设计电动水压试验阀。
八、喷水减温器
设计采用两级减温,第Ⅰ级装在低温过热器和屏式过热器之间由甲、乙炉膛两个回路各一组,集箱规格为¢426×
36,材料为10CrMo910,进口蒸汽温度为415℃,第Ⅱ级装在屏式过热器和高温过热器之间,每个回路装二组,集箱规格为¢426×
45,12Cr1MoV,进口蒸汽温度为476℃,在额定参数下设计考虑每级喷水量为20T/H。
喷水与蒸汽直接混合,因此要求水质甚高。
喷嘴采用“文丘里”形式,采用锅炉给水作为喷水之源,水温265℃,为避免蒸汽和喷水二者较大温度差所引起热应力所产生的不良后果,喷水进口管座采用夹层套管,集详内置混合套筒,长度不小于3米,其喷水装置中由渐扩管、喉口、套环等组合,根据耐磨和温度情况选用12Cr1MoV合金材料制造,在喉口处蒸汽流速约为140M/S,在喉口上喷水孔为¢3mm,沿圆周方向均布,喷水速度约为2米/秒左右。
改造后设计采用两级减温,第Ⅰ级装在低温过热器和前屏式过热器之间由甲、乙炉膛两个回路各一组,集箱规格为¢426×
36,材料为10CrMo910,进口蒸汽温度为427℃,在额定参数下设计考虑喷水量为30T/H,高加全切工况下设计喷水量为90T/H;
第Ⅱ级装在后屏式过热器和高温过热器之间,每个回路装二组,集箱规格为¢426×
45,12Cr1MoV,进口蒸汽温度为484℃,在额定参数下设计考虑喷水量为20T/H。
两级喷水与蒸汽直接混合,喷嘴采用“笛”形喷咀形式,采用锅炉给水作为喷水之源。
过热器配置二级喷水减温装置,且左右能分别调节。
由于减温器筒体内装有套管,在制造、安装过程中必须清除杂质,严防铁屑等堵塞在内,危及安全运行。
在喷水减温管路中,对每一组减温器均装有Dg25的截止阀和喷水调节阀,根据蒸汽温度要求给定讯号自动调节喷水量,由流量计记录数值。
再热器采用烟气调温,喷水减温仅用作事故减温。
采用喷水减温时,其喷水后的蒸汽温度至少高于相应的饱和温度15℃。
喷水减温器的防护套筒始端与联箱可靠连接并保证套筒与联箱的相对膨胀。
九、高温