提高垃圾焚烧发电厂热效率地措施Word格式文档下载.docx
《提高垃圾焚烧发电厂热效率地措施Word格式文档下载.docx》由会员分享,可在线阅读,更多相关《提高垃圾焚烧发电厂热效率地措施Word格式文档下载.docx(15页珍藏版)》请在冰豆网上搜索。
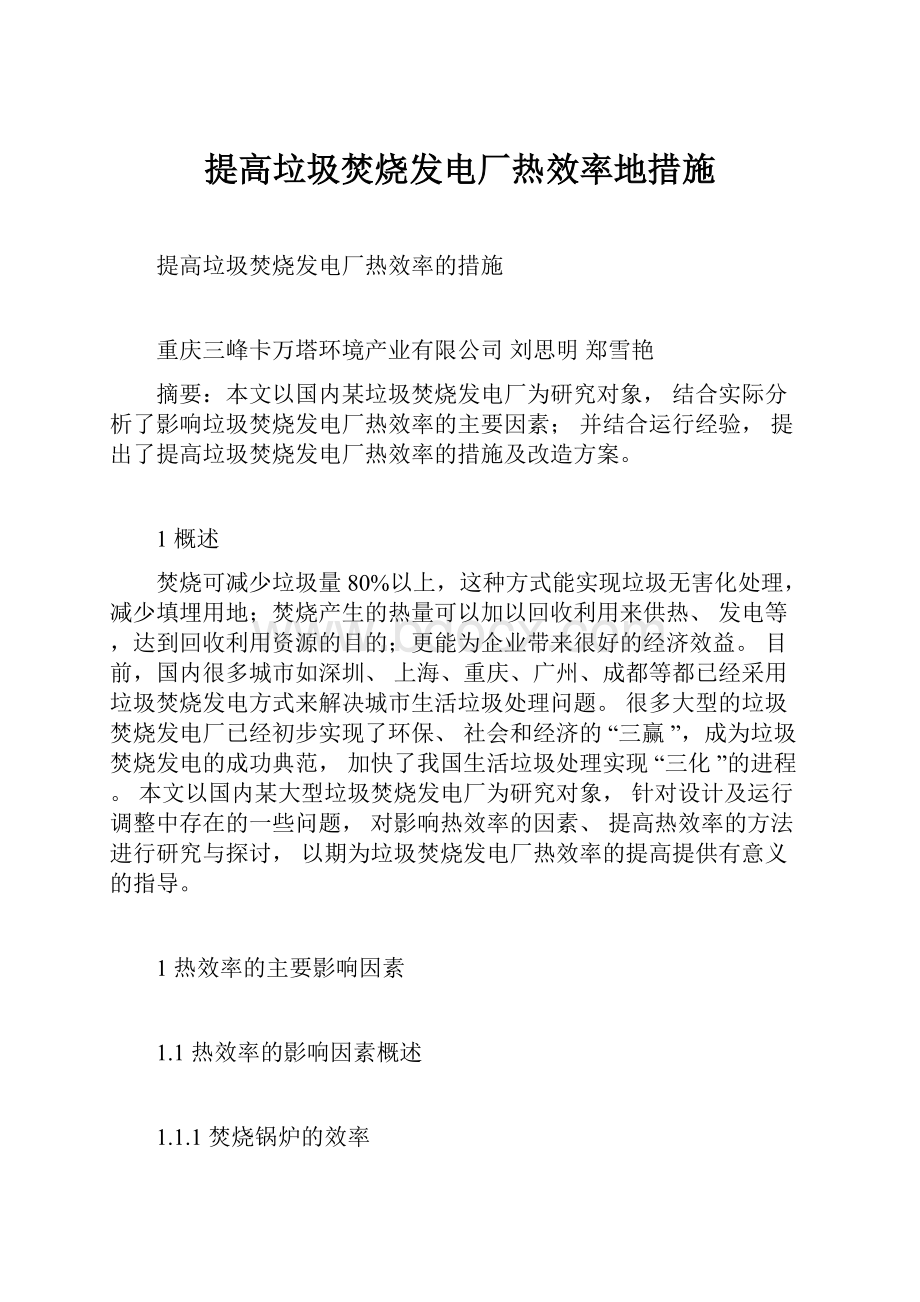
现代火电厂
垃圾化学能→烟气热能(
1a)
90
98
烟气热能→蒸汽热能(
1b)
88
93
锅炉效率(1
1a1b)
79
91
造成垃圾焚烧锅炉效率低下的原因有:
1)城市生活垃圾的高水分、低热值;
2)焚烧锅炉热功率相对较小,蒸发量一般不会超过100t/h,出于经济原因,能量
回收措施有局限性;
3)垃圾焚烧后烟气中含灰尘及各种复杂成份,带来燃烧室
内热回收的局限性。
4)为了确保烟气净化处理系统的进口烟气温度满足要求,
设计时考虑垃圾焚烧锅炉排烟温度一般为220℃左右,大大高于火电厂锅炉排烟
温度。
也就是说为了环保效益牺牲了垃圾焚烧锅炉的经济效益。
1.1.2蒸汽参数的影响
垃圾焚烧锅炉生产的蒸汽其参数偏低,原因如下:
1)焚烧锅炉的热功率较
小,在同容量的小型火电厂中也同样不会应用高压蒸汽参数;
2)焚烧锅炉燃烧
气体中含有的氯化物盐类会引起过热器的高温腐蚀。
在欧洲与美国,过热器管材
应用低合金钢与高镍合金,蒸汽参数一般不超过4.5MPa,450℃。
1.1.3给水回热系统热效率的影响
汽轮机组的给水回热系统既是汽轮机热力系统的基础,该系统的性能直接影
响到机组的安全和经济性,对全厂的热经济性也起着决定性的作用。
因此,在实
际的运行过程中,要保证该系统处于良好的工作状态。
1.1.4厂用电率的影响
垃圾焚烧发电由于其特殊性,厂用电率较高,约为17%~25%,其原因为:
1)垃圾焚烧发电厂容量小、蒸汽参数低;
2)系统复杂,辅机数量及耗电量增加。
垃圾输送储存及炉排驱动系统能耗较大;
同时,因垃圾焚烧产生的烟气中有害成
分较多,需要有烟气净化处理系统等,增加了辅机,并导致引风机功率增加。
同样,我们对上述两个发电厂进行比较,结果如表2所示,蒸汽热能转换为
发电电能的效率用2表示;
发电电能转换为供电电能的效率用3,3=1-厂用电
率;
发电效率发12;
供电效率供123。
表2现代垃圾电厂与现代火电厂全厂效率的比较
能量转换
符号
现代垃圾焚烧发电厂
现代火力发电厂
化学能→蒸汽热能
1
蒸汽热能→发电电能
28
45
2
发电电能→供电电能
3
发电效率
发
供电效率
供
7895
2241
1739
1.2垃圾焚烧发电厂热效率的主要影响因素
根据上述分析,针对锅炉热效率不高的实际,通过对某垃圾焚烧发电厂实际
运行情况的认真分析与探讨,并结合锅炉实际运行中出现的问题和取得的经验,
总结出了影响该焚烧发电厂热效率的几点原因:
(1)垃圾的混合均匀程度、给料速度、炉排运动速度;
(2)一次风的分配;
(3)排烟温度高,排烟热损失大;
(4)传热较差或长期运行导致传热恶化特别是蒸发管束的积灰;
(5)炉膛负压过大导致的漏风以及保温状况;
(6)给水回热循环的热效率;
(7)厂用电率。
2提高垃圾焚烧发电厂锅炉热效率的措施
针对前面分析的影响锅炉热效率的因素,结合实际运行中取得的经验与存
在的问题,共同探讨出了如下的解决办法。
2.1蒸发管束的积灰
积灰速度太快,过热器温度升高,蒸发量下降,排烟温度升高,热损失增加,厂用电增加,对系统影响很大。
前期与后期运行参数的变化较大就说明了上述问题。
锅炉受热面不足是导致锅炉蒸汽产量下降的主要原因。
锅炉产量降低,并造成锅炉出力与汽轮机能力不匹配,致使整个蒸汽发电系统效率降低。
积灰问题的存在,影响余热锅炉效率,导致装置能耗升高,经济效益下降。
造成上述问题的主要原因:
一是光管的换热系数相对较低,传热效果差;
二是受热面顺列布置,设计意图是减少积灰,为了加强传热,保护过热器而把管束节距又设计的太小,这本身就是矛盾的,实际运行中由于垃圾所含灰分较多、管束节距小且受热容易积灰,致使换热更加的恶化。
通过在该电厂的现场调查及与该电厂的技术人员交流发现,锅炉系统的对流受热面中,蒸发器的积灰最为严重。
蒸发器是余热锅炉重要的受热面,蒸发器起着保护过热器,调节烟温的重要作用。
但在实际运行中普遍存在以下问题:
因吹灰而带来的管子破损,由于余热锅炉具有大量的换热管束,而烟气中含有较多量的灰份,随着运行时间的推移导致管子严重积灰,影响了传热及烟气的流动。
为了提高锅炉的热效率,我们建议取掉部分蒸发器换热管,增大管子节距。
改造前一级蒸发管束原设为错列布置,结构如图1所示,节距为110mm,管净距
为72mm,管子规格为Φ38×
4.5,材质为20G,管排数为118排,每排3根管子。
改造后的一级蒸发管束改为顺列布置,结构如图2所示,节距改为220mm,管净距增至182mm,管排数减至59排。
图1改造前的一级蒸发器管束结构示意图
图2改造后的一级蒸发器管束结构示意图
经过计算,垃圾热值为7000kJ/kg、工质进出口温度不变的条件下,改造后
一级蒸发管束进出口烟气温度由原来647℃/599℃变成647℃/628℃,一级蒸发
管束的出口烟温比原设计提高了29℃。
主要原因有二:
一是原设计的一级蒸发器管圈数为4圈,而现有的蒸发器管圈数为3圈,换热面积减少了1/4;
二是本次改造使得蒸发器换热面积又减少了1/2。
因此,相对于原设计,换热面积减少
了5/8。
在高过进口蒸汽温度不变的情况下,主蒸汽温度由原来的400℃变为405℃。
在实际运行中,我们可以通过调节减温水量来调节主蒸汽的温度。
因此,不会影响电厂的正常运行。
同时对受热面必须及时吹灰,保持受热面外壁清洁,还要保证软化除氧水及蒸汽的品质,防止出现汽水管道结垢现象。
2.2一次风的分配
炉排面的下部设有一次风室供应垃圾燃烧所需空气并且对炉排片的进行冷
却,为了对垃圾起到良好的干燥及助燃效果,一次风空气进入焚烧炉之前,先通过蒸汽式空气预热器加热到220℃,然后从炉排下部分段送风。
垃圾在炉排上的燃烧分为三个阶段:
干燥段、燃烧段、燃尽段。
所研究垃圾发电厂每列炉排下布
置有四个风室,分别对炉排的四个部分供应一次风。
用一次风风量调节阀的开度控制每段风的风量。
改造前的一次风管结构尺寸如图3所示,经过风管的阻力计算我们发现只有5%~10%的风量进入第一风室,对垃圾进行干燥。
而有接近70%的风量进入第二风室,进入第三风室的占15%左右,进入第四风室的占10%左右。
目前,风量调节板一直处于全开状态,对风量起不到控制作用。
考虑到垃圾含水量高、发热值低的特点,干燥段的风量远远没有达到要求。
在这种情况下垃圾得不到充分的干燥,就在炉排的推动下进入燃烧段燃烧。
由于含水量较高,垃圾不能得到充分的燃烧,会生成更多的一氧化碳,甚至会导致炉膛内充满浓烟,增大
不完全燃烧损失。
另外,根据研究二噁英的生成与燃料在燃烧时产生CO量的多少有着密切的关系,因此我们在设计时,考虑了足够的过量空气系数和特殊的一、
二次风进风方式及合理配比,保证燃料的完全燃烧,尽量避免CO的生成。
针对以上情况,为了使垃圾得到更好的燃烧,我们采取以下措施:
对一次风管进行改造,增大第一风室风管的进口尺寸和第一风室的风管直径,使改造后进入第一风室的风量可以达到30%,利用风量调节阀控制流量;
同时,增大第三风室的风管进口尺寸,使更多的一次风进入该尾部燃烧段,有利于垃圾充分燃烧。
改造后的一次风管结构尺寸如图4所示,这样进入第二风室和燃尽段的风量就相
应减少,风量的分配更加合理。
垃圾得到充分的干燥,有利于充分燃烧。
因此,
燃尽段需要的风量就相应减少。
图3改造前一次风管结构示意图
图4改造后一次风管结构示意图
2.3排烟损失
排烟热损失是烟气离开锅炉末级受热面带走的部分热量,是锅炉最主要的
热损人。
该值可按排烟温度焓与冷空气焓差来求得。
Q1K(HpyHlk)100
式中:
k为燃烧产物修正值;
Hpy为排烟焓值,Hlk为冷空气焓值(包括空
气过剩系数的大小)。
从上式可以看出,排烟热损失的大小主要取决于排烟温度和过量空气系数的大小。
1)排烟温度的高低,是锅炉的基本设计参数之一。
设计锅炉时,首先要对该参数进行科学选定。
锅炉排烟温度的合理选定,直接影响到锅炉机组的经济性
和其尾部受热面工作的安全性。
选择并在实际操作中达到较低的排烟温度,
可以较明显降低锅炉的排烟热损失,有利于提高锅炉的热效率,节约能源及降低锅炉的运行费用。
研究结果表明,在锅炉的过剩空气系数一定,其排烟温度每升高或降低15℃左右时,排烟热损失就会升高或降低1%左右。
因此,锅炉在运行
中,应尽量降低其排烟温度。
当然,排烟温度的高低同时也受锅炉出力和尾部受热面的影响。
2)过量空气系数
锅炉运行中炉膛及烟风道不同程度的漏风现象,以及送引风配风不合理等都会造成空气过剩系数偏大,不仅增大了排烟热损失,造成炉膛温度降低,也增大了其它热损失。
2.4炉膛压力及保温因素
当炉膛微正压运行时工况比较合理,可有效避免冷风侵入炉膛。
但是这样会使现场脏乱甚至会出现漏气、冒火等危险,因此锅炉大多采用微负压运行。
综合
考虑可取炉膛负压为-5mmWG,可以有较小的上下波动,一般控制在
20~50Pa。
实际运行过程应避免负压过大导致的严重漏风以及正压运行导致的现场脏
乱。
根据已有的研究成果,对于电站锅炉,一般漏风系数每增加0.1~0.2,排烟
温度将升高3~8℃,锅炉效率降低0.2%~0.3%;
漏风系数每增加0.1,将使送、
引风机电耗增加2kW/MW电功率。
因此要在运行过程中,要严格控制负压。
此因素多为检修造成,当锅炉某处位于保温层内部件出现故障时,检修必须拆下保温层进行,维修完成后保温层不能及时修复,导致锅炉散热热损失增大。
汽包、联箱、管道、构架、炉墙和其他附件等的温度高于周围空气的温度,应
确保这些元件处于良好的保温状态,减少散热损失。
2.5强化燃烧,减少不完全燃烧损失
不完全燃烧损失包括机械不完全燃烧损失和化学不完全燃烧损失。
其中化学
不完全燃烧损失是由于炉温低、送风量不足和混合不良等导致烟气成分中一些可
燃气体(如CO,H2,CH4等)未燃烧所引起的热损失;
机械不完全燃烧损失是由
于垃圾中未燃或未完全燃烧的固定碳引起的,由飞灰不完全燃烧热损失和炉渣不
完全燃烧热损失两部分组成。
其中化学不完全燃烧损失
Q2KWr(VCOQCOVH2QH2VCH4QCH4)
式中Wr为送入炉内的垃圾量,VCO、VH2、VCH4⋯为1kg垃圾产生的烟气所含未燃烧可燃气体体积。
QCO、QH2、QCH4为各组分对应的热值。
机械不完全燃烧损失
Ay
Clz
Q332700Wr100
1Clz
式中Clz为炉渣中含碳百分比,
Ay100
为1kg垃圾中所包含灰分。
空气过剩系数对化学不完全燃烧热损失影响很大,空气过剩系数过小,将使燃烧因氧量不足而增大化学不完全燃烧热损失,过大则会降低炉膛温度,也会使化学不完全燃烧热损失增大。
因此在锅炉运行中,对风量进行调节,以保持合适的空气过剩系数,保持较高的炉膛温度,使燃料与空气充分混合,延长烟气停留时间,促进烟气中可燃物燃尽。
燃料的灰分越少,挥发分越多,则机械不完全燃烧热损失就越小;
炉渣含碳
量偏大,使炉渣不完全燃烧热损失大幅度增大,应根据锅炉负荷情况合理调整给
料速度、炉排速度和料层厚度,使垃圾能得以燃尽。
另外,如果前后拱上吊渣现
象比较严重,会影响炉膛内热辐射,这也是造成炉膛温度降低,灰渣含碳量偏高
的主要因素,应利用检修期间及时除焦渣。
焚烧炉在正常运行时,燃烧室内的火焰应在上炉排燃烧区横向分布均匀,下炉排燃烬区无明显红火;
炉排上料层厚度呈阶梯递减分布,平均厚度应在300mm~500mm之间;
上下炉排运动均匀,下炉排较上炉排稍慢;
火焰不得冲刷四周水冷壁管和对流管束,也不能伸入冷灰斗内;
锅炉两侧的烟气温度应均匀,
过热器两侧的烟气温差,一般不超过30~40℃;
燃烧室负压应保持为30~50pa,
不允许正压运行;
炉膛出口氧量值在7%~8%,一次风机出口风温达到设计值
220℃,二次风机出口风温达到设计值166℃;
排烟温度控制在220℃~240℃,
一炉膛烟气温度应保证烟气在850℃持续2秒的条件范围。
电厂实际运行时,操
作人员要严格按照规程操作,并及时调节工况,是垃圾处于良好的燃烧状态。
3汽轮发电机组给水回热系统
给水回热系统是汽轮机组的主要组成部分,采用给水回热后,汽轮机抽汽的热量被用于提高给水温度,使排气量及其对冷源的放热量大为减少。
因此,在蒸汽初、终参数相同的情况下,给水回热循环的热效率比朗肯循环的有显著提高。
在其它条件不变的情况下,给水温度越高,回热级数越多,则回热循环的热效率就越高。
但过分提高给水温度,使蒸汽的做功量减少,给水回热的经济效益反而降低。
因此当回热级数一定时,给水温度有一最佳值,此时回热循环的热效率最高。
同样,当给水温度一定时,回热级数越多,回热循环的热效率最高。
但是,随着回热级数的增多,热效率的相对增益逐渐减小,而加热器等设备投资及维护费用将随之增加。
该电厂设有一级除氧抽汽,采用的除氧器类型为喷雾式中压除氧器,其余采用的是表面式加热器,设置了低压加热器和轴封加热器。
未设置高压加热器。
除氧器设计工作压力为0.27Mpa,工作温度为130℃。
在实际运行中发现,如果按照设计给水温度130℃运行,给水泵存在一定程度的气蚀现象,后来将除氧器工作温度定为105℃,对应的饱和压力为0.12Mpa,接近大气压力。
采用中压除氧器的目的是提高给水温度,更多的使用回热抽气量即二级调整抽汽量。
而目前二段抽汽的参数约为0.3Mpa左右,155℃,而中压除氧器给水温度在130℃的饱和压力为0.27Mpa,基本等于二段抽汽压力,使用二段抽汽来加热给水存在一定困难。
而目前除氧器工作温度在105℃,能够解决采用二段抽汽
来加热给水的问题,但由于除氧器运行温度比设计温度低25℃,势必造成二段回热抽气量减少,影响汽轮机发电机组效率;
由于除氧器工作压力降低了
0.15MPa,意味着给水泵灌注头降低了0.15MPa,势必加大给水泵气蚀的危险性。
针对上述情况,现对本系统进行如下改进,使得给水温度能够达到130℃运
行,从而提高给水回热系统的热效率。
1)更换给水泵,改进变频装置。
选用知名厂家给水泵,保证给水泵在除氧
器工作温度130℃情况下,稳定可靠的运行且不易气蚀。
由于目前给水泵变频器
只有5%变频幅度,节能效果不佳。
使用变频给水泵可以降低给水泵转速从而降
低给水泵出口压力,这样能在锅炉出力降低的情况下降低给水泵功率,便于滑压调节在负荷变低的情况下经济性得到改善。
2)对汽轮机二段抽汽口进行改进。
由于目前二段抽气口已经固定,只能通
过调整汽轮机抽气口内部隔板来实现二段抽汽压力在0.5Mpa,抽汽温度在180℃
左右。
4降低厂用电率的措施
垃圾发电厂厂用电量主要包含:
生活用电,生产用电。
生活用电主要包括照明、空调等耗电。
生产用电主要包含办公设施、生产照明、动力设备等耗电。
由于电厂就是一个产生电能的工厂,在一般情况下为自给自足,当厂内不产生电能的情况下由外接保安电源提供。
厂内的电力消耗主要在于动力设备的耗电,为此我们对机电装置进行改造,采用的节能型产品或先进产品。
对动力消耗大的设备采用变频调节,比如给水泵、引风机。
在减少动力设备耗电量的同时,建筑按照
节能设计规范,增加光照和通风,减少照明和空调设备的耗电量。
通过这些措施来降低厂用电率,节约电能。
5结论
针对某垃圾焚烧发电厂的具体情况,我们主要采取了以下措施:
取掉一级蒸
发器部分换热管,增大管子节距,变为原有的两倍;
改造一次风管,把进入干燥
段的风量调到30%左右;
维修完成后及时修复保温层,并加强散热元件的保温工
作;
严格控制排烟温度和炉膛负压;
强化燃烧,减少不完全燃烧损失;
提高给水
回热循环的热效率。
采取措施后蒸发器问题得到解决,避免了因积灰严重导致的
停炉;
一次风的分配更加适合垃圾低热值、高水分的特点,有利于垃圾的燃烧;
排烟损失和散热损失都得到了控制;
有效地控制了垃圾的燃烧状况,尽可能地使
垃圾完全燃烧;
避免了给水泵的气蚀,使得给水温度能够达到130℃。
建议先按以上方法进行改造,其次是及时准确的调整。
如果能做到以上几点,不仅能提高全厂运行的热效率,而且具有可观的经济效益,使每顿垃圾发电量也能得到提高。