660MW超临界机组防止受热面氧化皮脱落技术措施文档格式.docx
《660MW超临界机组防止受热面氧化皮脱落技术措施文档格式.docx》由会员分享,可在线阅读,更多相关《660MW超临界机组防止受热面氧化皮脱落技术措施文档格式.docx(24页珍藏版)》请在冰豆网上搜索。
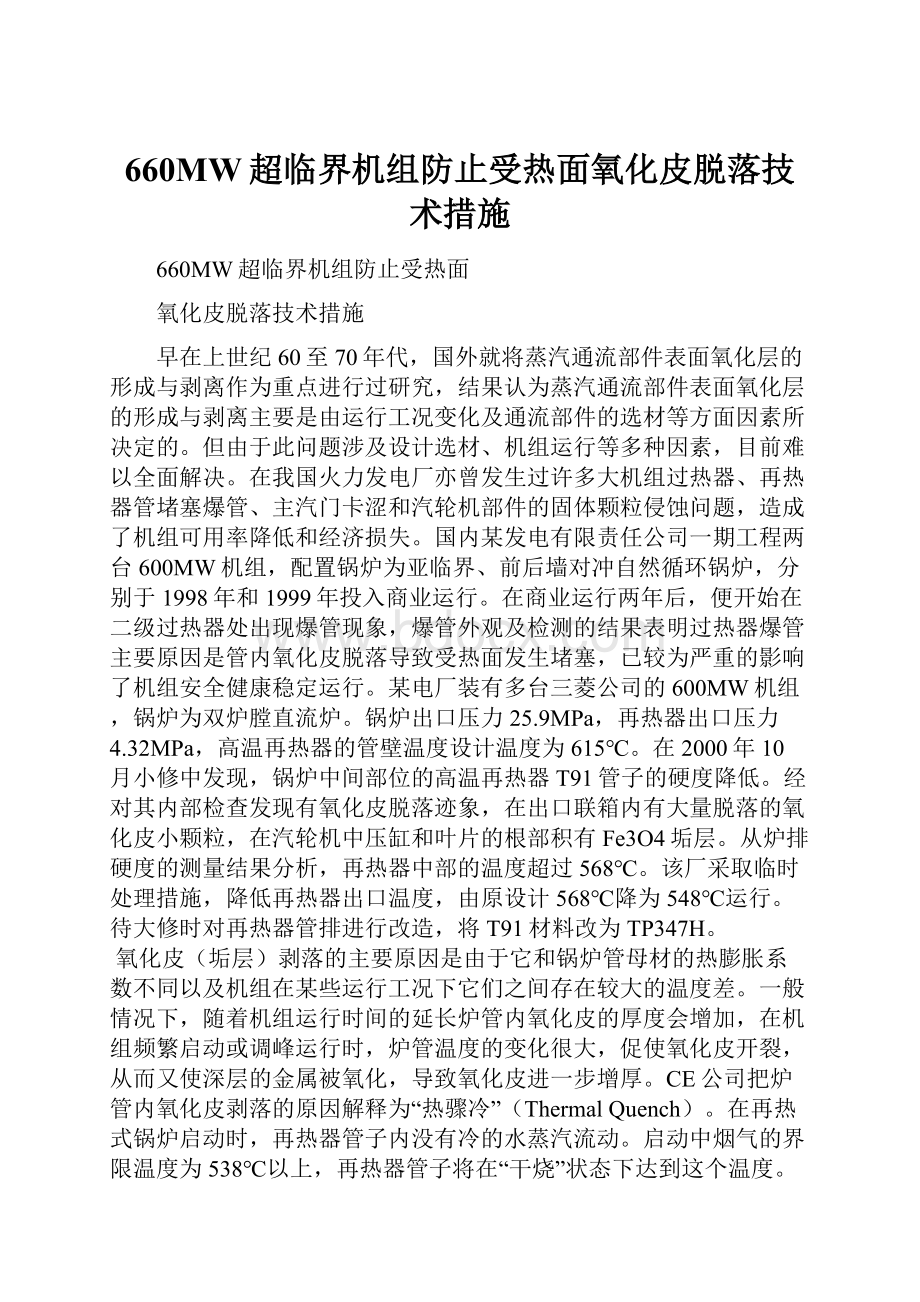
末级过热器
末级再热器
低温再热器
1
外径×
壁厚
mm
Φ41.3×
5.50
Φ47.6×
7.00
Φ38.1×
8.00
Φ63.5×
4.50
4.0
7
6.50
Φ60.3×
12
7.50
4.00
2
节
横向节距
2688(平均)
896
224
560
168
112
距
纵向节距
54
76.2
73
127
90
3
管子所用材质
SA-213T23
12Cr1MoVG
SA-210C
SA-213T91
15CrMoG
SA-213TP347H
4
相应材质的重量
t
80
96
225
1100
100
35
200
106
194
6
14
10
31
68
5
平均烟气流速
m/s
—
9.87
12.51
10.65
12.18
9.86
最高设计压力
MPa
28.24
27.68
27.08
5.17
32.54
运行压力
26.4
26.06
25.73
4.45
4.55
28.87
8
出口工质温度
℃
481
515
571
569
480
328
9
最高计算
工质温度
504
550
589
600
529
出口金属壁温
516
559
591
628
572
371
11
最高金属壁温
606
608
629
并联管数
根
6×
8×
20×
21
82×
13
33×
20
110×
167×
材质适用
温度界限
SA-210C:
454℃,15CrMoG:
550℃,12Cr1MoVG:
580℃,SA-213T23:
593℃,SA-213T91:
650℃,SA-213TP347H:
704℃
附件2各受热面管材分段示意图
分隔屏过热器
后屏过热器
高温过热器
高温再热器
通过以上数据分析可知:
上海原设计锅炉(比如国华太仓发电公司)末级过热器与TP347接口管段T23材质最高适用温度593℃,而出口设计最高温度金属温度593℃,接口部位设计温度基本接近管子允许温度,这样长期运行,该区域管子势必产生过热(异常工况:
主汽温度升高时或风烟工况发生偏斜时),产生氧化皮脱落也是必然的。
江苏扬州二厂一期2×
600MW亚临界锅炉,因炉膛设容积热负荷设计偏高,受热面管材设计裕度偏低(高过的出口管段选用SA213T22/580℃,仅出口段中上部至联箱Ф50.8×
6.9mm管段选用SA213T91/650℃(有一根T22),若按国内经验考虑炉外测点测量偏低30℃~60℃,各工况的不仅最高壁温已超出,平均壁温亦在许用温度左右(CRT画面报警值564℃偏高),管壁超温现象较严重;
壁温最高点基本集中在中间偏两侧的管排。
在与美国B&
W的交涉中,其认为炉外测点测量偏低约15℃。
即使按此标准高过管壁亦已局部超温。
查相关资料,无论是ASME、CE或RILEY设计标准,SA一213T22钢材管子金属许可温度均为580℃,但B&
W设计标准为602℃,可见美国B&
W在高过受热面选材方面裕量很小甚至无裕量),锅炉投产以来#1锅炉过热器T91因氧化皮脱落爆管一次,超温停炉一次;
#2锅炉T91管材因氧化皮脱落爆管6次,其原因均为与T91与接口T22(设计裕度偏低后全部改为T91)管材氧化皮脱落引起管道堵塞T91管段超温所致。
为了避免设计裕度过低导致管材长期处于超温运行而出现氧化皮脱落堵塞管子而爆管,在投运超临界机组的电厂利用机组大修或中修,建议将末过上采用SA213T23改为SA-213T91提高该区域金属壁温裕度,在建或准备建的电厂可依据定电公司锅炉受热面选取,在招标文件中就要要求锅炉厂将末过材质定位在SA-213T91和TP347H上,提高设计裕度避免机组投运后因燃烧工况变化引起受热面超温导致氧化皮产生和脱落。
二、SA213-T91钢的现场焊接采取措施防止根部焊缝和母材的过烧
超临界机组的工作压力和温度很高,ALSTOM公司大量选用SA335-T91管子作为过热器系统和再热器系统用管。
SA213T91钢是一种改良型的9Cr-1Mo钢,在原9Cr-1Mo马氏体钢中加入V、Nb等合金元素,具有良好的抗高温氧化和抗蠕变性能,AC1为830-850℃,AC3为900-940℃。
在550-650℃的许用应力明显高于10CrMo910、X20CrMoV121钢;
与10CrMo910钢相比,在同等的温度、压力条件下,管子壁厚可减小50%,推荐使用温度为650℃以下。
SA213-T91钢种可采用钨极氩弧焊、焊条电弧焊方法进行焊接。
预热温度和层间温度应在180-250℃之间,不要超过350℃,在焊后热处理之前,必须将整个材料的温度降至180℃以下,以保证马氏体的充分转换。
SA213-T91的合金成分相当高,如果采用和低合金钢相同的焊接工艺,焊缝根部就会过烧,因此,氩弧焊打底时,焊缝根部必须充混合气体——N2(88%)+H2(12%)进行保护,才能使打底焊缝的根部得到良好的保护,防止根部焊缝和母材的过烧,获得良好的根部焊缝的成形和符合要求的机械性能。
现场焊接工艺保证可降低锅炉投运后管材蒸汽高温腐蚀和氧化腐蚀几率。
1、充气方法
结合外高桥工程,经过现场实践和效果,焊缝根部充混合气体进行保护方法,作具体介绍:
如图三在焊口两端的两根管子内都不塞入可溶纸,一根管子远离焊口的密封盖1处充入混合气体,另一根管子远离焊口的密封盖2一端作为混合气体出气口,这样混合气体充气长度变成44米,因此充气前先用耐高温铝箔纸密封整个焊缝,使混合气体只能流向密封盖2处的出气口,提高了混合气体的充气速度,也降低了混合气体的消耗量,实际焊接时的混合气体充气流量为10-12L/min,当混合气体充满44米长的管子内部时,将耐高温铝箔纸由仰焊位置至平焊位置撕去二分之一,先进行二分之一焊缝的氩弧焊打底,氩弧焊枪的氩气流量为9-10L/min,然后再进行另外二分之一焊缝的氩弧焊打底,打底封口时,气体可以从密封盖2的出气口流出,封口处一直保持稳定的气体流量和压力,既满足了气保护的要求,又解决了平焊位置封口难的矛盾,可操作性比较强,无论是目视检查还是射线探伤检查都符合规范要求,取得了良好的效果。
这种焊缝根部混合气体充气方法在SA213-T91焊口的组合焊接中得到了推广,焊工一致认可。
2、氩弧焊打底
氩弧焊打底前应检查焊口的清洁度,对口间隙为2.8mm-3.2mm之间,点焊固定。
然后贴上焊口一半的铝箔纸,应对根部进行充氢氮混合气。
焊缝根部的焊接方法为内加丝焊法,即对于管子处于水平位置的焊口,由仰焊位置起弧,焊丝由平焊位置通过对口间隙径向穿过管子,送至仰焊位置的管子内壁处,焊工的视线顺着焊丝透过焊缝的对口间隙进行观察,观察焊口坡口内壁边缘及焊丝的熔化情况,如有内咬边、未焊透、生焊丝等缺陷,应及时改变焊枪的角度及加丝的速度;
如还有问题,应将缺陷处的焊缝打磨掉,然后继续施焊,焊口点焊处应打磨掉,焊好一半后撕去铝箔纸,再去焊另外一半,以确保内壁焊缝的正常成形。
3、氩弧焊盖面
由于打底焊缝的厚度在2-2.5mm,氩弧焊盖面时,存在打底焊缝的二次熔化,所以焊缝根部必须保持混合气体的充分保护,以免根部过烧。
为确保层间熔合良好,盖面前先用锋钢锯条清理焊缝表面的氧化硅,因为C9MVIG焊丝焊接后焊缝表面产生的氧化硅比较多,另外如焊缝两侧熔合线处有尖角或沟槽存在,必须打磨至圆滑,再用钢丝刷清理打底焊缝的表面,直至焊缝表面呈现明亮的金属光泽。
在盖面过程中应严格控制焊缝的层间温度,不得大于300℃,温度控制好,铁水流动性能好,外表光滑无缺陷,甚至会有金属光泽出现。
如果层间温度过高,熔化的钢水的流动性将明显降低,甚至无法流动,此时若继续焊接,焊缝的层间温度会越来越高,焊接操作越来越困难,焊缝的厚度会越来越厚,容易引起夹渣,焊缝成型差,咬边多,一出现上述焊接症状,必须立即停止焊接,将层间温度降下来,并将焊缝修整至正常的厚度,再继续进行焊接。
焊接结束后,必须立即进行表面清理,将二氧化硅等杂物清理清楚,并检查焊缝是否存在表面缺陷,如咬边、表面脱节、弧坑等,如有应及时修补,消除缺陷。
4、热处理
在焊后热处理之前,必须将整个材料的温度降至180℃以下,以保证马氏体的充分转换。
热处理采用电加热的方法,热处理时升降温度速率控制在每小时200度,加热至740-770度,恒温30分钟。
5、无损探伤
无损探伤必须在热处理完成以后进行,特别是象T91这样的高合金钢,易产生延迟裂纹,而且在没有进行热处理前,先进行无损探伤,必然要和T91管子接触,焊缝在外力的作用下,较易产生裂纹,甚至导致焊缝折断。
即使无损探伤检查结果是合格的,也不能保证在随后进行的热处理过程中,焊缝不会产生任何影响质量的缺陷。
6、返修
焊口经无损探伤,主要存在根部生焊丝、内凹、层间未熔合等缺陷,都属于手工操作方面的问题,随着焊工对T91母材和焊接材料的焊接特性的熟悉和掌握,以上缺陷出现的概率都明显降低。
缺陷去除的方法为使用角向磨进行机械打磨,直至找到缺陷,然后将开挖处修磨成圆弧形,不得有尖角、尖沟、尖槽存在,因为这些结构的存在易产生层间未熔合。
补焊前必须进行预热,温度为200-250℃,然后利用图三所示的方法对焊缝根部充混合气体,气体保护到位后,即可进行补焊,然后重做热处理、硬度检查和无损探伤。
如果焊口存在的缺陷长度超过焊口周长的四分之一,则必须将焊缝割除,重新焊接,所有的工艺程序与要求和焊接一个焊口完全一样。
三、锅炉酸洗过程控制避免受热面欠洗或过洗
超临界及超超临界机组受热面管材基本上采用耐高温优质钢材,其性能应属于不锈钢材。
不锈钢的抗腐蚀性能主要由于表面覆盖着一层极薄的(约1nm)致密的钝化膜,这层膜把腐蚀介质隔离,是不锈钢防护的基本屏障。
不锈钢钝化具有动态特征,不应看作腐蚀完全停止,而是形成扩散的阻挡层,使阳极反应大大降低。
通常在有还原剂(如氯离子)情况下倾向于破坏膜,而在氧化剂(如空气)存在时能保持或修复膜。
不锈钢管材放置于空气中会形成氧化膜,但这种膜的保护性不够完善。
通常先要进行彻底清洗,包括碱洗和酸洗,再用氧化剂钝化,才能保征钝化膜的完整性与稳定性。
酸洗的目的之一是为钝化处理创造条件,保证形成优质的钝化膜。
因为通过酸洗使不锈钢表面平均有10um厚一层表面被腐蚀掉,酸液的化学活性使得缺陷部位的溶解率比表面上其它部位高,因此酸洗可使整个表面趋于均匀平衡,一些原来容易造成腐蚀的隐患被清除掉了。
但更重要的是,通过酸洗钝化,使铁与铁的氧化物比铬与铬的氧化物优先溶解,去掉了贫铬层,造成铬在不锈钢表面富集,这种富铬钝化膜的电位可达+1.0V(SCE),接近贵金属的电位,提高了抗腐蚀的稳定性。
不同的钝化处理也会影响膜的成份与结构,从而影响不锈钢表面氧化性,如通过电化学改性处理,可使钝化膜具有多层结构,在阻挡层形成CrO3或Cr2O3,或形成玻璃态的氧化膜,使不锈钢发挥最大的耐腐蚀性。
锅炉本体基建完成后,其首要工作完成锅炉酸洗。
为了使酸洗工作安全顺利达到预期酸洗效果,在酸洗前一定要通过电科院做小样酸洗试验,通过多种小样试验结论,最终确定最佳酸洗工艺。
如果小样试验结论不准确,必然导致锅炉欠洗或过洗。
锅炉欠洗因管子内部毛刺不能彻底清除,在锅炉存水后就会发生局部电化学腐蚀或点蚀,在高温下形成不稳定氧化皮,锅炉快速升温和冷却因膨胀系数不同产生应力导致氧化皮脱落;
锈蚀层不能彻底清除同样在机组投运后,因锅炉受热面温度快速变化导致其锈蚀层脱落。
过洗导致管材壁厚减薄,承压能力降低而爆管(神头二厂捷克500MW机组发生过锅炉过洗导致水冷壁大面积爆管事故)。
目前,华能电厂直流锅炉酸洗采用德国氢氟酸化学清洗技术。
在许多电厂清洗结束后检查,清洗非常成功,由此可见其技术的先进性。
德国的直流锅炉常规开路酸洗工艺,在某些地方不同于我国的传统做法。
下面就该清洗方案进行简要论述(以300MW直流炉为例),建议国华公司在建600MW及以上超临界(超超临界)机组锅炉酸洗采取该方案。
1、直流锅炉清洗范围:
整个化学清洗分为水冲洗和酸洗两部分。
水冲洗范围:
凝汽器、凝结水管道、低压水管道及加热器水侧、除氧器、高加水侧。
酸洗范围:
高压给水管道、省煤器、汽水分离器、过热器及相应的各联箱和联络管、再热器、减温器及高压旁路站。
2、清洗工艺说明
1)清洗步骤
(1)冲洗凝结水及给水系统,冲洗水分别由临时系统和启动分离器底部排除。
(2)冲洗省煤器至再热器部分,冲洗水分别由启动分离器、主蒸汽管道、再热管道排放。
(3)润湿剂浸泡:
利用给水泵和加药泵将稀释后的润湿剂注入整个系统,浸泡4~8h。
(4)水冲洗:
利用给水泵和3台凝泵冲洗省煤器至再热器的整个系统。
冲洗水分别由启动分离器、主汽管道、再热管道排放。
(5)酸处理:
利用给水泵和临时加药泵将氢氟酸和缓蚀剂注入系统。
维持氢氟酸浓度为1%,缓蚀剂浓度为0.15%。
酸液分别从启动分离器、主汽管道、再热管道排放。
排放合格后,酸液浸泡2h。
(6)冲洗及钝化:
浸泡结束后利用给水泵和凝泵分段冲洗整个系统,冲洗合格后,利用给水泵向整个系统注入钝化液。
监测排放水合格后,钝化结束。
2)清洗流量的控制
为使酸洗时流速达到或接近0.2m/s,冲洗流速达到或接近1m/s,各部位的清洗流速如下。
省煤器和蒸发器:
酸洗流量为200t/h;
冲洗流量为560t/h。
过热器:
冲洗流量为1350t/h。
再热器:
酸洗流量为500t/h;
酸洗流量由电动给水泵提供动力,冲洗省煤器至蒸发器部分时由电动给水泵提供动力,冲洗过热器和再热器时由给水泵和凝泵并联运行来提供动力。
3)各步骤控制标准
(1)除盐水冲洗流量为560t/h、1350t/h;
浊度为只进行监测,但不作为控制标准;
温度为常温。
(2)润湿剂处理加药流量为200t/h;
润湿剂(外供)浓度为0.05%;
温度为30~60℃;
浸泡时间为12h。
(3)除盐水冲洗温度为常温;
流量为560t/h、1350t/h;
浊度为只作监测,但不作为控制标准;
(4)酸洗氢氟酸入口浓度为1%~1.2%;
缓蚀剂浓度为0.15%;
温度为55~60℃;
开路清洗排放标准为全铁小于2g/L转为浸泡;
加酸流量为200t/h、500t/h;
浸泡时间为2h。
(5)除盐水冲洗流量为560t/h、1350t/h;
温度为常温;
电导为冲洗水出入口电导差小于10μS/cm。
(6)钝化温度为常温;
流量为560t/h;
钝化液浓度为H2O2=0.1%(1g/L) pH>10;
排放时间为排放口浓度合格后0.5h,钝化结束。
3、清洗过程及结果
整个清洗过程依照上述控制标准执行。
实际过程及主要数据如下:
(1)除盐水冲洗:
该阶段利用除盐水冲洗整个系统。
冲洗给水管道至启动分离器时最大流量为540~560t/h;
冲洗过热器时最大流量约为900t/h;
冲洗再热器最大流量约为1300t/h。
3个排放口冲洗合格时浊度最低值为0.1NTU。
该过程共耗水约2600t。
(2)润湿剂处理:
加入润湿剂时的流量实际约为300t/h,水温40~50℃。
利用给水泵和高压加药泵调整润湿剂浓度约为0.06%。
整个系统一次注满,排放水含有润湿剂时(目测,搅拌后有泡沫),停止加入。
该阶段共耗水540t,润湿剂约400kg。
(3)除盐水冲洗:
经13h的系统浸泡后利用除盐水冲洗整个系统。
实际过程的流量类似于上述的第
(1)步。
排放水由锈黄色转为透明,合格时浊度最低值为0.1NTU。
该过程共耗水1800t。
(4)酸洗:
自省煤器至启动分离器,加酸流量为195t/h,温度为70℃,入口酸浓度为0.9%~1.15%,酸洗合格后排放口氢氟酸浓度为0.8%,全铁为1.85g/L,其中全铁最高峰值为9.3g/L,开路酸洗时间为40min。
清洗过热器时,加酸流量为500t/h,温度为70℃,入口酸浓度为1%~1.1%,酸洗合格后排放口氢氟酸浓度为0.9%,全铁为1.8g/L,其中全铁的高峰值为11.5g/L,开路排放时间为50min。
再热器阶段的数据如下:
加酸流量500t/h,入口酸浓度1.1%,合格后排放口氢氟酸浓度0.8%,全铁为1.5g/L,其中全铁峰值为8.5g/L,开路排放时间为70min,共耗水约900t/h,氢氟酸(40%)消耗18t,缓蚀剂700kg。
(5)除盐水冲洗及钝化:
浸泡2h后,用除盐水分段冲洗整个系统,实际流量同上述的第
(1)步。
3个阶段冲洗合格后,排放口电导率最低值为11μS/cm,排放口PH由1.5最终升高并稳定为6.5左右。
测定电导率合格后加入双氧水和氨水,实际过程PH为9.5~9.8,H2O2含量约为0.15%~0.2%。
该阶段共耗时3h30min。
钝化冲洗1h。
除盐水冲洗阶段,由于除盐水供应不足,系统维持压力停止约3h。
消耗除盐水1900t,消耗H2O2740kg,消耗NH3·
H2O400kg。
清洗后检查:
金属表面光滑,钝化膜完整呈钢灰色,个别部位颜色较深,呈灰黑色。
清洗过程中挂片的腐蚀速率为0.15g/(m2·
h)。
清洗评定级别为优。
4、就德国氢氟酸化学清洗技术问题进行论证
前面所述的内容包含了化学清洗的3个基本过程,即水冲洗过程、化学溶解过程、腐蚀电化学过程。
腐蚀电化学过程包括金属腐蚀过程和钝化过程。
冲洗过程用除盐水冲洗清除系统内的污物;
化学溶解过程即清洗剂对各种垢的溶解,此过程不存在电子的得失问题。
关于氢氟酸对铁氧化物的络合溶解理论国内外文献报导不少。
对于清洗过程中,酸对金属基体的腐蚀是通过加入缓蚀剂来保护金属的,国内氢氟酸缓蚀剂已完全能满足要求。
下面就酸洗后的冲洗和钝化作一分析。
酸洗结束至钝化阶段,金属腐蚀体系的溶液中离子成份的变化影响了腐蚀过程的最终产物,及铁钝化膜的形成。
当除盐水冲洗结束后,pH逐渐上升接近中性,同时电导率值逐渐下降到10μS/cm。
电导率下降即实际溶液中离子浓度的下降。
开始冲洗时,腐蚀体系成份是金属离子、氢离子、氟铁络合离子及常见的中性盐。
此时金属铁的电位主要由下列过程控制:
阳极反应:
Fe→Fe2++2e
阴极反应:
2H++2e→H2↑
根据混合电位理论,铁的电位由上述两过程耦合后确定。
该电位值随冲洗过程中pH的升高而稍有下降。
当冲洗水接近中性时,体系成分大大简化,电导率已降到10μS/cm,因此,可视为Fe—H2O体系。
开始加入钝化剂H2O2和NH3·
H2O时,体系的电位和pH将发生变化,阴极过程将变为:
H2O2+2H++2e→2H2O,虽然系统始终有背压存在,空气中的氧仍会不断补充到冲洗水中,在不加入H2O2时,原有溶氧逐步被消耗,因而不足以使铁电位发生显著变化。
在上述阴极过程的作用下,铁的电位升高,阳极过程最终产物由Fe2+变为成膜的Fe2O3或Fe3O4。
铁电位的高低受H2O2加入量的影响,当H2O2的浓度不均时,钝化后的钢表面有Fe2O3或黑色的Fe3O4,当膜脱落时,钢表面呈现金属本色。
需注意的是,这种钝化方式是采用H2O2作为钝化剂的,并必需满足低电导率的条件。
这是因为高电导率时,体系中的离子浓度高,将从以下2个方面改变腐蚀体系:
第一:
离子成分将改变阴极过程和阳极过程,有的直接参与反应,直接影响钝化结果,例如氯离子将促进点蚀,而氟离子的存在会使得钝化膜疏松;
第二:
离子