新能源和高效节能Word文档下载推荐.docx
《新能源和高效节能Word文档下载推荐.docx》由会员分享,可在线阅读,更多相关《新能源和高效节能Word文档下载推荐.docx(39页珍藏版)》请在冰豆网上搜索。
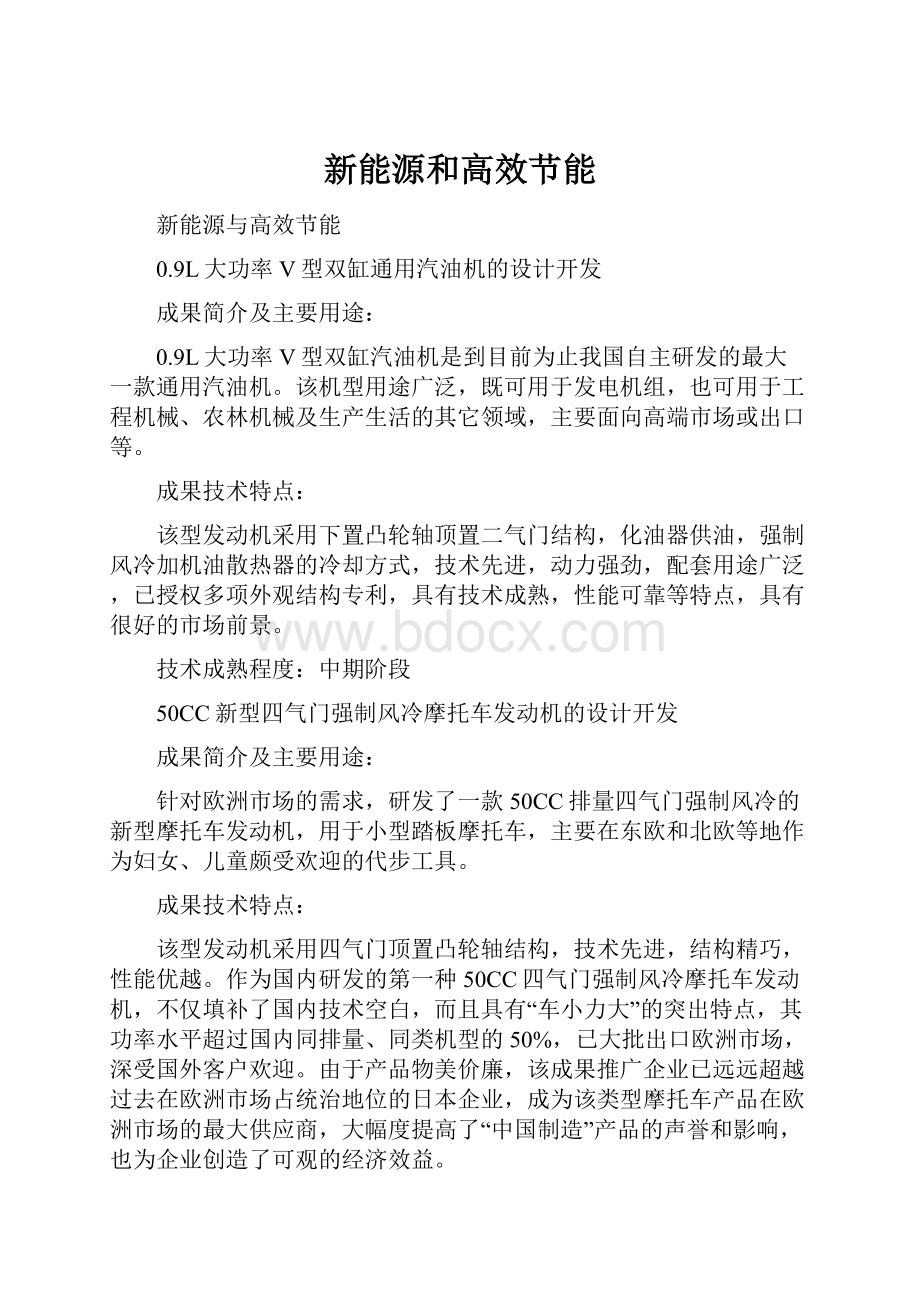
新型高效摩托车发动机燃烧技术的研究
本成果为摩托车发动机排放性能的提高提供了一种低成本解决方案。
在本项目科研成果的基础上,共发表科技论文2篇;
申请专利3项,其中发明专利1项,实用新型专利2项。
本项目成果已部分或全部应用到浙江春风公司2006年后生产的CF250T系列摩托车产品上,在持续地创造效益。
以2007年度计,浙江春风控股集团有限公司本年度生产172MM系列发动机约3万台,其中约1.2万台发动机外销,售价3700元/台,创造产值0.44亿元;
剩余部分自行配装CF250T系列摩托车,该部分产量2007年约为1.8万辆,售价1.1万元/台(本产品主要出口欧洲市场),创造产值1.98亿元。
合计由本项目衍生出的产值约2亿元,直接利润约5000万元。
本项目采用先进的虚拟设计技术及深入的CAE分析和试验测试手段,开发了一种可靠、高效而又成本低廉的摩托车发动机燃烧技术解决方案。
由于是从改善发动机缸内可燃混合气的燃烧过程入手来进行性能优化,因此有可能少量改动发动机的一些零部件和结构,低成本地达成预定的节能净化技术目标。
实际试验及生产证明,在不采用燃油电喷技术,不适应排放催化转化器,不过多增加生产成本的前提下,通过采用新型挤流燃烧系统、内部EGR等新技术,发动机装车后的排放性能很好地达到了国家当前的排放法规要求,实测百公里燃油消耗量不仅全部符合国家相应燃油消耗量限值,而且整体油耗水平低于国家限值超过5.8%,且整车加速性、最高车速等性能指标基本维持原车的水平。
由于未采用成本高昂的燃油电喷、排放催化转化等常规解决方案,对发动机的改动也不大,因此很好地控制了新产品的生产成本,既收到了很好的节能环保等社会效益,也为企业创造了可观的经济效益。
专业级450CC越野摩托赛车发动机的设计开发
新型450CC发动机主要用于专业级越野摩托赛车,是目前国际越野车比赛的主流赛车,通常代表着一个国家或一个企业在摩托车技术领域的最高水平。
该450CC四气门单缸四冲程水冷发动机是我国第一台大排量专业级越野摩托赛车发动机,填补了我国在这一领域的空白。
该机型主要针对欧美市场,属于高技术难度、高附加值、高成本的摩托车尖端产品,除用于竞赛、训练外,还可用于休闲、娱乐及军警用途等。
该型发动机采用顶置凸轮轴四气门结构,技术先进,结构精巧,性能优越。
作为国内自主研发的第一台大排量专业级越野竞技摩托车发动机,不仅填补了国内技术空白,而且具有强化程度高、质量轻、技术复杂、新材料新工艺集中等特点。
发动机采用水冷、电喷技术,排放水平达到欧三标准,采用了铝合金锻造活塞、钛合金气门、全铝合金陶瓷气缸等许多国内未采用过的新技术,各项主要性能指标达到或超过了国外先进国家的同类产品,拥有光明的细分市场前景,目前已批量生产并出口国际市场。
同时,由于具有高难度、高利润特点,该产品的成功推出也为生产企业创造了良好的经济效益。
稠油炼制减压分离过程大型化关键集成技术及应用
天津大学与中国石油化工股份有限公司齐鲁分公司胜利炼油厂共同开发了稠油炼制减压分离过程大型化关键集成技术,并成功地在胜利炼油厂第三常减压装置减压塔扩能项目中得到应用。
通过近三年的运行,各项工艺参数稳定,运行良好。
2007年4月7日,该项目通过了中国石油和化学工业协会组织的科技成果鉴定,与会专家一致认为该项目达到了国际先进水平。
该项目针对稠油炼制减压蒸馏大型化过程中的技术难题和设备要求,综合应用现代计算传递学理论及技术,进行了集成创新,开发出600万吨/年稠油炼制减压蒸馏大型化集成技术。
该项目自主开发、研制和应用了TUPAC规整填料、悬挂式槽式液体分布器、槽盘式气液分布器、通透式填料支撑结构等新型塔内件及技术,提出了全塔可视化设计新方法,建立了大型蒸馏装置设计、诊断和技术改造的工程学基础和方法,申请了三项发明专利和一项实用新型专利(实用新型专利已授权),具有自主知识产权。
稠油炼制减压分离过程大型化关键集成技术在中国石油化工股份有限公司齐鲁分公司胜利炼油厂第三常减压装置减压塔扩能项目中获得了成功应用。
该技术实施后,实现单套装置稠油炼制达到600万吨,成为国内规模最大的稠油炼制蒸馏装置之一;
实现了减压塔进料段的雾沫夹带达到千分之一以下,加氢裂化料中Fe离子浓度降到0.3ppm以下;
各侧线的产品质量均达到了质量控制指标,完全满足加氢裂化原料要求;
减压塔拔出率54.73%,超过设计值(52.15%)2.58个百分点。
天津大学稠油炼制减压分离过程关键集成技术的应用,使齐鲁分公司的资产和设施得到充分有效的利用,取得了巨大的经济效益。
该项目采用了先进适用技术改造传统产业,适合国内同类企业大范围推广。
方案采用了天津大学自主开发、研制和应用了TUPAC规整填料、悬挂式槽式液体分布器、槽盘式气液分布器、通透式填料支撑结构等新型塔内件及技术,提出了全塔可视化设计新方法,建立了大型蒸馏装置设计、诊断和技术改造的工程学基础和方法,申请了三项发明专利和一项实用新型专利(实用新型专利已授权),具有自主知识产权。
天津大学关键集成技术实施后,实现单套装置稠油炼制达到600万吨,成为国内规模最大的稠油炼制蒸馏装置之一;
大型润滑油型减压蒸馏塔内件集成技术的开发与应用
常减压蒸馏是原油加工的第一道工序,原油通过常减压蒸馏分离成各种油品和下游加工装置的原料。
炼油企业常减压装置因其加工量大、产品品种多、分离精度高以及对下游生产装置影响面广等因素,在炼油企业占据核心地位。
受中国石化股份公司上海高桥分公司及中国石化工程建设公司的委托,天津大学对高桥分公司800万吨/年润滑油型常减压蒸馏装置内件进行设计、制造。
该项目创新性地综合应用现代传质理论、流体力学与计算流体力学和系统分析优化等化工过程领域的最新研究成果和方法,针对炼油厂润滑油型减压蒸馏过程,深入探讨了大型装置的运行特点和设备要求,开发了大型蒸馏塔内件集成新技术。
该技术在结构上采用了天津大学ZUPAC规整填料、槽盘式气液分布器、多级组合槽式液体分布器、具有捕液吸能作用的双切向挡板进料分布器、埋藏梁支撑及桁架梁支撑等多项专利和专有技术,使该装置于二零零二年一次开车成功,提高了润滑油基础油料收率和拔出率,各侧线产品质量合格并降低了能耗,设计工艺完全满足了润滑油生产的需要,各项技术指标均达到或超过了设计要求。
该集成技术显著提高了蒸馏强度,达到了3.31t/m2•h,使单套润滑油型原油蒸馏装置生产能力由过去的250万吨/年,突破了当时国内500万吨/年的最大处理能力,首次达到800万吨/年的规模,减压蒸馏塔直径达到10.2米,为我国目前最大减压蒸馏塔和世界上目前最大润滑油型减压蒸馏塔之一。
该项目自应用以来,共加工原油1174.6万吨,获得经济效益1亿多元。
为提高企业的竞争能力和经济效益,我国各大炼油厂均有或拟建设减压蒸馏装置。
该装置生产能力达到800万吨/年,可使炼油厂的资产和设施得到充分有效的利用,因此具有广阔的应用前景。
方案采用了天津大学ZUPAC规整填料、槽盘式气液分布器、多级组合槽式液体分布器、具有捕液吸能作用的双切向挡板进料分布器、埋藏梁支撑及桁架梁支撑等专利和专有技术,结合现代流体力学传质理论、流体力学与计算流体力学和系统分析优化等化工过程领域的最新研究成果和方法,对炼油厂大型减压蒸馏过程实施了系统集成开发及应用。
整体装置一次开车成功,提高了润滑油基础油料收率和拔出率,各侧线质量任务达到合格指标,同时降低了能耗,设计工艺完全满足了润滑油生产的需要。
天津大学流线型、低压降组合式规整填料的设计,显著增加了炼油强度,达到了3.31t/m2•h,使上海高桥大型减压蒸馏实际能力破了500万吨/年当时国内最大处理能力,首次达到了800万吨/年的规模。
精馏装置直径达到10.2米,为我国目前最大塔器。
该项目的成功应用,为我国自主研制更大规模的减压蒸馏成套装置提供了基础。
大型乙烯装置汽油急冷关键技术
天津大学精馏技术国家工程研究中心、中国石化齐鲁股份有限公司烯烃厂、中国石化工程建设公司经过共同合作和刻苦攻关,应用现代传质理论、计算流体力学、系统分析优化等基本理论和方法,针对大型乙烯装置汽油分馏急冷系统工程放大难题,进行了关键技术创新,实现了系统集成。
开发出了高效三溢流塔盘、低液面梯度、气液均匀分布、抗堵塞和内件集成等多项关键新技术。
建立了大型乙烯装置汽油分馏急冷塔的工程学方法,形成了中国具有自主知识产权的汽油分馏急冷技术品牌。
课题组在攻关过程中集成了国内自主研发的新技术和质量可靠的设备,打破了大型汽油分馏急冷塔分离段长期以来使用填料的技术格局,创造性地开发和首次使用了导向三溢流复合塔盘技术、变截面变孔径管式预分布技术、组合桁架支撑技术、多进口环形折返进料分布技术,解决了大型汽油分馏急冷装置气液分布、结焦堵塞和长周期稳定运行的工程难题,首次将大型板式塔/填料塔组合集成技术成功应用于国内最大的乙烯装置—齐鲁84万吨/年乙烯汽油分馏急冷塔中。
该汽油分馏急冷塔直径为9.2米,是我国目前自行设计和制造的最大直径的板式分馏急冷塔;
是集成技术应用于大型乙烯急冷系统国产化装置的成功范例。
中国石化齐鲁股份有限公司烯烃厂装置建成后,乙烯装置生产能力从48万吨/年大幅度提高到84万吨/年,汽油分馏急冷塔的主要控制指标均达到或优于设计值:
全塔压降为0.01165MPa(小于设计值的0.013MPa);
塔釜温度平均为197oC(达到了设计值);
进料流量5656607Kg/h,达到设计负荷(年开工时间按8000小时计),产品质量全部合格。
利用急冷油余热产生稀释蒸汽的换热器,换热效率提高,每小时节省中压蒸汽15吨。
该塔操作正常并具有15%的上限裕量,完全满足乙烯生产要求。
该项成果应用后,经济和社会效益显著,技术达到国际先进水平。
(1)基于现代传质理论、计算流体力学、系统分析优化等基本理论和方法,通过模拟计算、实验研究建立了大型乙烯装置汽油分馏急冷技术的工程学方法。
(2)汽油分馏急冷塔首次采用通透性桁架支撑梁,改善了塔内的气液流动、消除死角、抗堵塞;
分离段打破了长期以来使用填料的技术格局,首次使用导向三溢流塔盘,塔盘上的高效浮阀在没有中油循环下不仅提高了塔盘传热效率,同样提高了传质分馏能力,保证了汽油、柴油的产品质量;
首次将环形折返流气液分离分布器引入汽油分馏急冷塔,改善了进料气液分布;
创新性将原填料技术优良的变截面管式预分布器作为汽油回流分布器,解决了大直径塔盘液体分布不均的难题,也使板式塔首次成功应用于国内最大的乙烯装置(84万吨/年)汽油分馏急冷塔成为可能。
(3)开发出大型乙烯装置汽油分馏急冷关键集成技术和设备,它的设计采用高效喷射导向三溢流塔及垂直格栅填料,同时应用了大量促进塔盘和填料性能发挥的塔内件集成技术,包括变孔径/变截面管式预分布器、溢流式槽式液体分布器、环形折返流气液分离分布器、桁架式支撑梁等,攻克了大型急冷装置的工程放大过程带来的生产强度高、液面梯度大、气液分布不均、易堵塞等难点问题,解决了长期以来束缚我国乙烯发展的一个重要难题,并形成中国具有自主知识产权的汽油分馏急冷技术品牌。
新型填料集成技术在催化分馏和吸收稳定系统中的开发应用
化裂化(FCC)是我国炼油厂最重要的二次加工手段,主要产品是干气、汽油、柴油和液化气。
分馏系统的任务是将反应器顶的气态产物,按沸点范围分割成富气、汽油、轻柴油、重柴油、回炼油和油浆等馏份。
大庆炼化公司林源炼化厂催化分馏装置始建于1971年,当时处理量不到20万吨/年。
1993年和1997年先后进行了两次改扩建后设计规模要达到50万吨/年。
这两次改扩建的设计中主分馏塔塔盘为复合型,吸收、解吸、再吸收、稳定塔均为浮阀型塔盘。
但在实际运行中发现,由于主分馏塔塔径只有2.8m,在原有的设计基础上无法满足50万吨/年处理量的要求,实际生产能力只能达到45万吨/年。
除此之外,原装置在实际生产过程中暴露出的其它技术问题还有:
主分馏塔侧线不能生产合格的-25#柴油;
汽、柴油重叠严重,汽油质量也经常不合格,产品时常变色;
主分馏塔塔板压降过大,能耗高,气压机效率低;
各塔的原内件设计存在技术缺陷,使塔操作不稳定,非计划停车次数多;
“干气不干”,干气中C3以上含量过高,甚至达到10%以上;
液化气C5含量高;
汽油中液化气含量高;
稳定吸收系统能耗高;
再吸收塔带液严重。
对催化裂化系统的改造主要包括了主分馏塔改造和吸收稳定系统改造两个方面。
从行业的技术发展上看,国内对主分馏塔的设计均使用了板式塔的设计,本次改造前林源分馏装置也不例外,改造前采用了条形浮阀上开两个固舌的复合型塔盘。
天津大学精馏技术国家工程研究中心针对林源炼油厂主分馏塔的技术问题,并根据改造前标定数据得出结论:
在分馏塔不增加塔高塔径条件下,若不改填料,不但处理量不能进一步提高,更不能应用现在的粗汽油回炼技术。
对此,天津大学首次在国内提出了全填料设计的新思想,采用了天津大学双向波纹填料、不同型号的波纹填料、格栅填料等新型填料技术完全取代板式塔结构以提高分馏效率和处理能力。
同时,由于填料塔效率与液体均匀分布度密切相关,改造中还需要设计结构合理的液体分布器,本项目采用了高弹性液体分布器技术进行彻底改造。
另一方面,为提高催化吸收稳定装置分离效率、受林源炼油厂委托,天津大学对吸收稳定装置的吸收塔、解吸塔、稳定塔及再吸收塔进行技术改造:
采用了天津大学新型高效规整填料及塔内件技术改造吸收稳定装置各塔,其中解吸塔改为双股进料,并对整体工艺实施了先进的流程模拟技术。
通过以上技术改造,在不变更原主分馏塔塔高及塔径情况下,使改造后的生产能力由40万吨/年增加到65万吨/年,同时很好解决了其它上述各个技术问题,并可根据不同操作方案方便地采出0#柴油和-25#柴油,特别是将干气中C3含量降至1%以下,取得了巨大的经济效益。
(1)天津大学首次在国内提出了全填料设计的新思想,采用了天津大学双向波纹填料、不同型号的波纹填料、格栅填料等新型填料技术完全取代板式塔结构以提高分馏效率和处理能力。
(2)采用本方案,在不变更原主分馏塔塔高及塔径情况下,使改造后的生产能力由40万吨/年增加到65万吨/年,同时很好解决了其它上述各个技术问题,并可根据不同操作方案方便地采出0#柴油和-25#柴油,特别是将干气中C3含量降至1%以下,取得了巨大的经济效益。
软包装大容量高功率超级电容器
超级电容器是介于传统电容器和二次电池之间一种新型储能器件,具有高能量密度和高功率密度的优点,还有免维护、充放电效率高、循环寿命长(可达105次以上)、使用温度范围宽、对环境友好等优点,可以被用作UPS的后备电源,小型储能装置、移动通信和混合电动车的启动与后备电源、燃料电池电动车或混合电动车的能量回收系统,将来还将与太阳能电池、风力发电系统等联合用于大型的储能装置。
本产品是涂布法制备活性炭电极,采用卷绕方式制作电芯,单体电容器产品的电压可以达到2.5~2.7V,最高可达3.0V,能量密度为6~8Wh/kg;
同时采用优选的电解液,保证了产品的高功率特性,功率密度大于3000W/kg。
化学活化制备超级电容器用电极性炭
超级电容器是介于传统电容器和二次电池之间一种新型储能器件,具有高能量密度和高功率密度的优点,被用作UPS的后备电源,小型储能装置、移动通信和混合电动车的启动与后备电源、燃料电池电动车或混合电动车的能量回收系统,将来还将与太阳能电池、风力发电系统等联合用于大型的储能装置。
但目前为止,国产活性炭一直未能取得实质性突破,市场均为国外厂家占有。
本技术的以石油焦等为原料选用化学活化法,采用优化的活化工艺制备电极用活性炭。
比表面积1500~2000m2/g,1~4nm的微孔和中孔大于50%,工作电压2.7~3.0V,比电容100~120F/g。
低成本液浸聚光光伏组件及系统
条形平面镜线性聚光光伏电热联产系统是天津大学自主研发的新型光伏系统,目标获得太阳能综合利用效率70%以上,太阳能发电成本低至每度电0.8-1.0元,冷却光伏电池的回收热量根据品位高低为建筑提供生活用热水及供暖。
自主研发的条形平面镜二维自动跟踪聚光器成本低,宜加工,可将直射阳光时刻汇聚在焦直线上;
利用液体直接浸没的方式制作新型聚光接收器,将汇聚阳光进行光电转化,循环液体带走副产热量,并提高电池工作效率。
天津大学在长期的科研工作中,开发了低成本、模块化的二维跟踪条形平面镜聚光器和高效液浸光电池冷却技术,实现了很好的效果,并建立了多处示范工程。
相关技术已申请专利10余项,其中3项已获授权。
以研发的条形平面镜线性聚光器为基础,通过液体直接浸没的强化散热途径,采用国际上的聚光电池,建立以72m2为基本单元的20-30倍聚光光伏电热联产系统,实现系统电热综合利用效率70%。
单元模块化的设计利于大规模的电场建设,副产热可用于降低建筑能耗。
70%的电热综合利用效率可同时解决建筑的电力和热需求,从城市和荒漠两个应用领域解决我国能源短期与环境污染问题。
本技术基于国内具有自主知识产权的关键技术,结合国际先进技术产品,实现国内与国际的接轨,突破聚光光伏技术发展的瓶颈,促进CPV在国内的快速发展,并同时形成具有我国自己的知识产权的技术产品,推动我国相关技术领域的快速发展。
研制的条形平面镜聚光器在集光比为1:
20的情况下,集光系统的综合造价仅为287元/m2。
该新技术比国际领先水平的系统综合成本低9倍,国际领先水平的系统综合成本为317美元/平米。
利用液体直接浸没的方式完成电池的高效散热,将太阳能电池片直接置于流动的液体中,电池表面的散热系数为2000W/m2K左右,电池温度大幅度降低,系统效率较大提高。
72m2的单元模块可产生14.4kWp的电力,热量为36kWp。
条形平面镜线聚焦自动跟踪系统的初始投资为400元/平方米,考虑电池成本为平板电池的3-4倍,每个单元的投资成本约10万元左右。
对比而言,如果采用晶硅平板光伏系统,若售价35元/W,对应成本50.4万元。
每度电成本价格仅为现有光伏发电成本的1/8-1/10。
由此可见,线性聚光液浸光伏电热联产系统具有很好的经济性,与同类产品相比具有很强的市场竞争力,在国家对可再生能源电力大力推广和支持的背景下,该技术产品将有很大的发展和盈利空间。
利用辐射板技术实现建筑物制冷与供暖工程
天津大学自主研发的与建筑一体化的太阳能冷热技术体系,采用一体化辐射板技术、超低温差辐射末端技术和高效多源热泵技术综合利用太阳能源、空气源和太空低温源,实现太阳能利用装置与建筑围护结构完美一体化;
可低成本提供供暖、制冷和供应热水。
该技术体系发挥了当前国内外太阳能利用技术的优点,而克服了其不足之处,在国内外处于领先水平;
已申请近20项相关发明专利,并建立了10余处示范工程。
该技术的推广使用将大大提高可再生能源的利用率,实现国家提倡的节能减排要求。
利用建筑外围墙体或屋顶安装的一体化辐射板对旧有建筑进行更新改造或与新建建筑的建造过程耦合起来,提高建筑外围护结构的保温隔热性能,达到三步节能设计标准。
有阳光照射的时候,利用太阳能通过带有选择性吸收涂层的辐射板提供供暖和生活用热水需求,没有阳光照射的时候,利用空气源和低温太空源实现被动式制冷,提供供冷需求。
通过显热储存系统短期调节自然条件对系统性能的影响,必要时,通过多源高效热泵系统长期调节自然条件下的系统运转情况。
通过一体化辐射板系统的安装,可在超低能耗的基础上,满足建筑制冷供暖和提供生活用热水的需求。
通过中试和实际项目示范,该技术产品低于国内外同类产品,而且与建筑结合后,制冷供暖成本低于传统空调制冷、集中供暖系统成本,具有很强的市场竞争力。
而且,可再生能源系统的使用,符合目前节能环保绿色可持续发展的方向。
在国家十一五科技支撑和天津市科委的资助下建立了10余处示范工程,示范建筑面积为1300m2至5056m2。
所有示范项目均已实现天津地区对制冷供暖的要求,即冬季室温不低于18℃,夏季室温不高于26℃,常年提供不低于50℃的生活用热水。
天津市建筑节能与环境检测中心在“三九”和“三伏”期间对部分示范项目进行了随机检测,冬季房间最高温度23.9℃,最低温度21.9℃;
夏季房间最低温度20.2℃,最高温度25℃,整栋建筑在生活用热水、制冷供暖上的年总耗电量低于30kWh/m2。
1、技术领先:
在全球首次实现太阳能源、空气源、太空低温源和地源等多种可再生能源综合利用,与建筑一体化,实现建筑物供暖和制冷,并提供生活用热水,一套系统多种用途,并且项目得到了国家十一五科技支撑计划和天津市重大科技计划的支持。
天津市节能中心对工程进行实际检测,在冬季供暖“三九”极端天气下,室温测量结果表明,最低温度为21.9℃,高于民用建筑18℃的国家供暖标准。
夏季制冷在“三伏”极端天气下,室温连续测量结果表明,平均最高温度为23.8℃,低于民用建筑26℃供冷标准。
2、经济、节能、环保:
对于新建建筑物,本系统初始投资与传统制冷供暖方式相差无几,因本系统采用太阳能、辐射能等等可再生能源综合利用系统,其后续运行费用很低。
整栋建筑在生活用热水、制冷供暖上的年总耗电量低于30kWh/m2,降低建筑对传统能源消耗的80%。
大大的