装配钳工基础知识培训课件Word文件下载.docx
《装配钳工基础知识培训课件Word文件下载.docx》由会员分享,可在线阅读,更多相关《装配钳工基础知识培训课件Word文件下载.docx(27页珍藏版)》请在冰豆网上搜索。
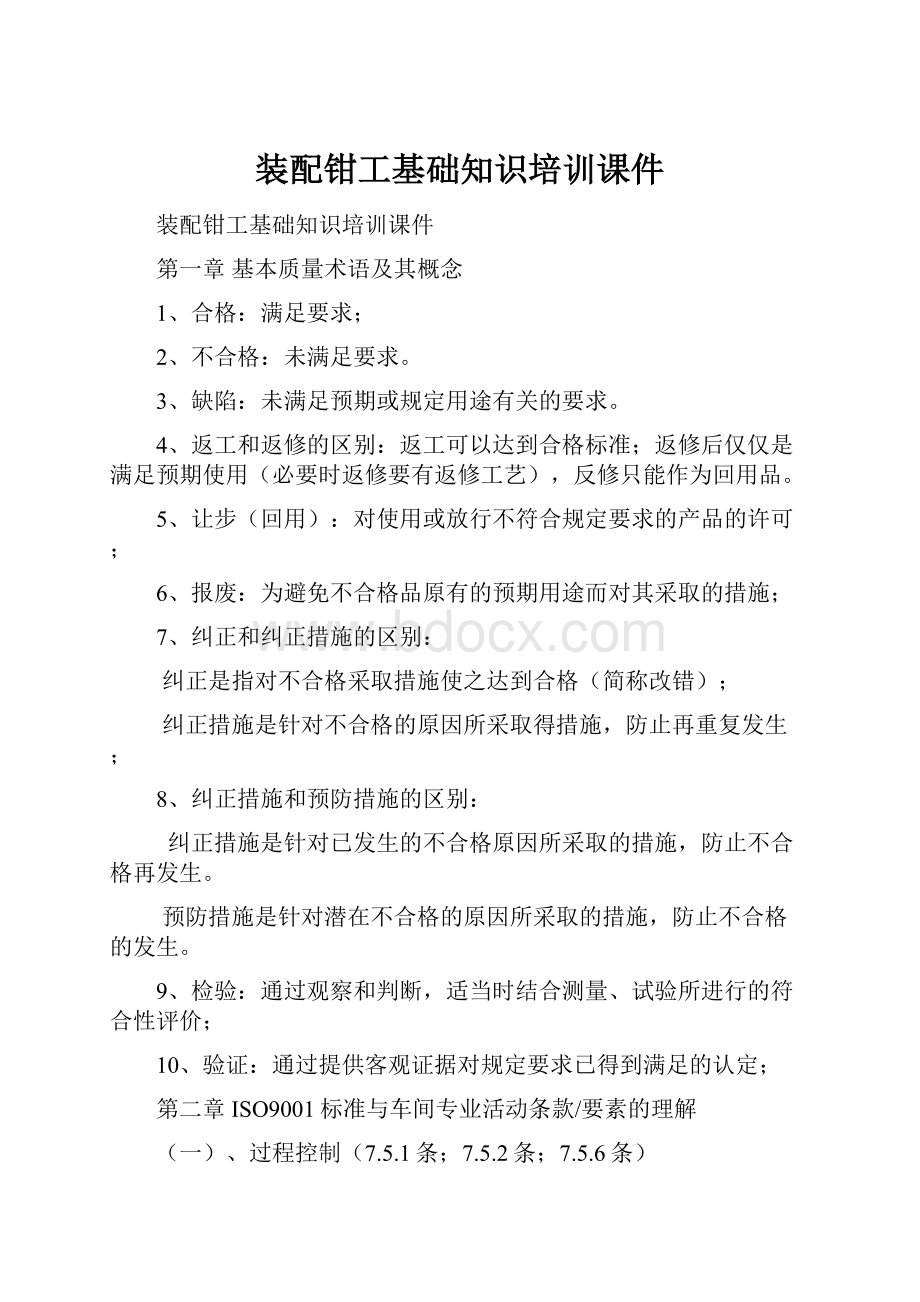
标识卡、流程卡、工序卡、派工单、标识牌、色标、符号标识、磕字头标识、专用器具或区域标识、不干胶标识、也可在零件直接标识等。
3、产品标识的内容:
名称或规格、图号、数量、工序等。
4、状态标识的划分:
待验(?
黄色)、已验:
1)合格(√绿色);
2)不合格(×
黑色):
返工(
黑色)、返修(
黑色)、让步回用(
黑色)、报废(×
×
黑色)、待处理(D黑色、首检(☆或首√绿色)。
5、对可追溯性标识的要求:
必须单件和唯一性识别、并记录纳入档案。
6、按《产品标识和可追溯性控制程序》的规定实施产品标识、状态标识、可追溯性标识。
7、对合同要求的可追溯性要求的产品应按批次建立随工流程卡,记录投料、加工、装配、调试、检验的数量、质量、操作者和检验员。
其产品批次标记与原始记录保持一致,要能追溯产品交付前和交付后的情况。
(三)、产品防护(7.5.5条款)
1、本区域应开展定置管理,有区域定置图及工具箱定置图,现场定置管理规范,物品摆放流转有序。
2、应对本区域产品的搬运、装卸、贮存、加工交付等,采取适宜的防护措施和配置资源,以减少和杜绝工业七害(锈蚀、毛刺、磕碰、铁屑、污尘、损坏、渗漏)
3、对本区域的产品中转库或存放区应按《产品搬运、贮存、防护和交付控制程序》和有关仓储管理的规定进行管理(摆放、标识、环境条件、保质期、进出库手续、维护保养、不合格品隔离、定期检查等)。
(四)、产品监视和测量(8.2.4条款)
1、应明确本区域所负责的产品检验和自检的范围和项目。
2、凡本区域所承担的放行或完工检验工作,必须严格按《产品监视和测量控制程序》、《三自一控管理标准》《过程检验控制管理标准》和相关文件的规定进行检验,应有必备检验依据文件和准确的检测手段,并保持符合接收准则的证据和记录有权放行的人员。
3、应按《三自一控管理标准》的规定开展“三自一控”活动。
4、应严格执行“首检”、“巡检”和“完工检验”制度并保存记录。
(五)、不合格品控制(8.3条款):
1、不合格控制的简要流程:
判断(识别)标识记录隔离报告
评审/批准处置再次验证原因分析纠正措施。
2、建立了本区域的不合格品台帐,对不合格品通知单、评审处置单等记录保持完整。
3、严格按《不合格品控制程序》的规定对不合格品进行了评审和正确处置,评审单签批手续齐全符合规定,流向清楚,返工和返修进行了二次检验。
4、现场的不合格品按规定进行了标识和隔离。
5、关重原材料不合格让步回用必须严格按照规定审批,并经授权人审批认可。
(六)、测量设备(7.6条款)
1、现场使用(包括工具站和工具箱内)的计量器具完好并带有效期之内的标识,使用和摆放正确。
2、按照周期检定计划的要求,及时将本区域的测量器具送检。
3、按照《监视和测量控制程序》和《计量器具管理制度》的规定对本车间的量具进行管理。
第三章有关现场质量管理的基本概念:
(一)、有关现场管理的基础知识
1、现场质量管理:
是对生产现场进行的质量管理。
2、现场质量管理的主要内容:
1)过程质量控制(预防控制质量异常波动、质量控制点等)
2)开展5S活动做好定置管理。
3)建立健全质量信息系统。
4)质量改进和QC小组活动等。
3、现场质量管理的任务是:
质量缺陷的预防、质量维持、质量改进、质量验证。
4、定置管理:
使人与物在现场中的结合关系和状态达到最佳科学化、规范化和标准化的管理方法。
5、生产5S活动:
整理、整顿、清理、清洁、素养。
6、三按:
按图纸、按标准、按工艺。
7、三自一控:
自检、自分、自盖工号、控制自检正确率。
8、三检:
按生产过程分:
首检、巡检、完工检;
按检验执行人分为:
自检、专检、互检。
9、文件的三性:
正确性、完整性、统一性。
10、三分析、三不放过:
1)原因未分析清不放过;
2)危害性和责任未分析清不放过;
3)措施未分析落实不放过。
11、检验员的5大职能:
鉴别、把关、预防、报告、监督
12、四新:
新工艺、新技术、新材料、新设备
13、质量的五不准:
1)不合格产品不准出厂销售;
2)不合格原材料、零部件不准投产;
3)淘汰产品不准生产销售;
4)无标准产品和未经检验产品不准出厂和销售;
5)不准弄虚作假以次充好。
14、工业七害:
磕碰、锈蚀、毛刺、铁屑、污尘、损坏、渗漏。
15、PDCA循环:
P——计划;
D——实施;
C——检查;
A——总结。
16、工序:
产品形成的过程顺序。
17、工步:
同一生产工序分解的每个加工单元过程。
18、工位——是指以生产作业的工序流程划分的一个定点单元生产区域。
工位不同于工步,也不同于工序,即在一个工位可能存在多个工步,也可能在一个工序中存在多个工位。
19、工艺:
产品制造的最佳方法。
20、工序能力:
是指在工序制造过程中,通过对人、机、料、法、环、测量6大因素的控制,工序所达到的水平能力。
21、特殊过程:
不能验证或不能经济地进行验证的工序。
如:
焊接、热处理、锻造、铸造、涂渡、塑压、粘结、涂装等。
目前我公司的特殊过程是:
焊接、和涂装二个工序。
22、关键过程:
对形成产品质量起决定作用过程,一般包括形成关键、重要特性的过程;
加工难度大、质量不稳定、易造成重大经济损失的过程等。
23、质控点:
对需重点控制的工序/过程所实施的强化质量控制。
质控点设立的三个原则:
关键特性、易反馈、不易加工的工序过程。
24、质控点所使用的文件有:
作业指导书、控制图、记录表和设备日检点表。
注:
对产品的关键过程要进行三定(定人、定机、定工艺)关键工序的操作人员要经过技能培训并持证上岗,要设立质控点。
25、QC小组:
员工围绕着企业的方针、目标或技术质量问题,运用质量管理的理论和方法,开展质量改进和质量攻关的小组。
26、QC小组的特点:
1)广泛的群众性;
2)组织的灵活性;
3)明显的自主性;
4)高度的民主性;
5)明确的目的性;
6)严密的科学性。
27、QC小组活动的过程:
1)选择课题;
2)现状调查;
3)设定目标;
4)分析原因;
5)确定要因;
6)制定对策;
7)实施对策;
8)检查效果
9)巩固措施;
10)总结和下步目标或计划。
28、QC小组的类型:
1)管理型;
2)现场型;
3)攻关型;
4)服务型;
5)创新型
第四章有关过程检验的基本知识及要求
1检验员的5大职能:
鉴别、把关、报告、预防、监督(产品、工序、储存、工艺纪律、不合格品处置)
2检验人员的5项基本素质要求
1)良好的思想/意识素质和职业道德;
2)了解本岗位的职责范围及工作内容;
3)了解相关的检验标准/程序/法律法规等检验依据;
4)良好的身体素质;
5)有一定的沟通和协调能力。
2检验员的6项业务技能要求
1)熟悉相关的检验标准/程序/计划/方法等;
2)熟悉技术和产品实现的过程;
3)熟练使用相关的检测设备/量具;
4)一定的检验经验和熟练的检验技能;
5)一定的文化水平和数据分析能力;
6)对检验数据/信息能做出正确分析结论。
3检验工作的6个步骤/程序
1)明确检验要求及检验依据;
2)策划选择/确定检验方法;
3)检验准备(软、硬件);
4)观察、判断、测量、试验等检验实施;
5)比较、分析、判定;
6)标识、记录、报告和处置。
4中级机械检查工(包括机加、机钳)应知:
1)受检零件加工设备的名称、型号、规格、性能、机构及传动系统的知识。
2)常用精密量具、复杂工具、检测设备、检查夹具(包括组合夹具)的名称、规格、构造、用途及调整维护保养方法。
3)根据工件精度合理选用量具、仪器及相互配合使用的方法。
4)常用金属材料的种类、牌号、性能和用途。
5)机械制图的公差配合、表面粗糙度、形状和位置公差的标准及应用。
6)常用的数学计算知识。
7)齿轮、凸轮的原理和主要尺寸的计算及检查方法。
8)静、动平衡试验检查方法。
9)一般工件的加工工艺过程;
工序间加工余量的相互关系和工件的技术条件。
10)较复杂工件根据设计、装配要求合理选择测量基准及在夹具上的安装和检查。
11)编制检查工艺规程的基本知识。
12)工件的加工方法和质量的关系;
根据技术要求分析零件精度和装配间隙等对产品质量的影响;
一般工件产生废品的原因和防止方法。
13)热处理常识(退火、正火、淬火、回火、调质、渗碳和渗氮等的作用和目的)。
14)液压传动的基本原理。
15)生产技术管理知识。
5中级机械检查工(包括机加、机钳)应会:
1)使用精密量具、复杂工具、夹具和仪器检查各种复杂工件。
2)看懂复杂零件图、装配图、并了解各部件的相互关系和作用。
3)确定复杂工件的检查程序。
4)各种旋转运动机件的静、动平衡的检查。
5)检查轴类、箱体类及各种螺纹、齿轮、凸轮的主要尺寸。
6)产品总装试车后进行各项性能和精度检查。
7)看懂一般液压机床传动系统图。
8)掌握涂色厚度,检查配合件的接触面。
9)根据公差配合的种类,检查配合件的间隙。
6中级机械检查工(包括机加、机钳)工作实例:
1)检查细长轴的直线度和圆度。
2)按图纸检查四拐曲轴。
3)按图纸检查箱体类工件尺寸精度。
4)按部件装配图的技术要求检查床头箱、主轴箱和溜板箱等同类型部件的装配质量。
5)按图纸技术要求检查机床导轨的各项精度。
6)相应复杂精度的工件检查。
7过程检验的职责:
1)按文件执行首件检验、巡回检验和完工检验;
2)鉴别是否合格;
3)记录问题和工艺纪律执行情况;
4)放行合格产品、拒收不合格产品。
8首件检验:
对生产开始和工艺要素变化后的首件产品质量进行的检验。
9首件检验的范围:
1)刚上班/换班/调换操作者后批量加工的第一件产品;
2)调整或更换设备、工装、量具后批量加工的第一件产品;
3)改变工艺参数或操作方法后批量加工的第一件产品;
4)改变原材料/毛坯/半成品后批量加工的第一件产品;
10首件检验的作用:
预防的作用,防止批量不合格品产生。
11首件检验的要求:
首件检验应按照检验依据文件的规定进行检验,检验合格后应在零件上做出首件合格标识,并向报验者出具《首件自检、专检记录表》/《装配线首件检验记录》,该记录单一式两份,检验员和操作者各持一份,以作为首检合格的证据。
只有首检合格后方可进行批量加工。
首件检验适用于所有的生产过程。
12巡回检验:
巡检是检验人员对自己所分管区域(或工序)进行的定期或随机的流动性巡回检查、测量或监督。
13巡回检验的范围:
除成品检验之外的所有制造加工、装配工序。
14巡回检验的要求:
正常情况下,检验员在当班应至少对自己所分管的区域或工序巡检一次,以便及早发现潜在的工序质量问题,巡检应依据文件的规定和质量波动的状况有针对性的进行检验,当巡检发现异常问题应及时向所在车间质量/技术科长报告,以便及时采取纠正措施。
巡回检验应保持记录《工序巡检记录表》/《部装巡检记录表》/《在线检测巡检记录表》以便追溯,巡回检验适用于所有的生产过程。
15工序完工检验:
检验员对零件加工工序完工转序前所进行的放行检验。
15.1工序完工检验对操作者的要求:
各加工工序完工后操作者首先要进行自检、自分、自盖工号(或做标记)方可报验。
15.2工序完工检验对检验员的要求:
在操作者自检、自分报验的基础之上按照图纸、工艺、标准、程序、检验指导书等检验依据的规定进行检验,检验合格做出标识和检验记录登记以便追溯;
16常用三种检验方法
1)测量装置检验法;
2)感官/经验检验法;
3)试验/使用/在线验证法。
17制造过程中返工/返修的检验
所有返工/返修后的产品必须经过重新检验,并做好检验记录。
其中,返工后的产品必须完全达到原合格标准的规定,而返修后产品则要达到让步接收(回用)评审处置方案(或措施)的规定,并对返修后的产品作出标识。
返工或返修达不符合要求作报废处理,由检验员做出标识,责任生产单位负责隔离并按照《不合格品控制程序》规定处理。
18与制造部相关的2012年公司质量目标
1)产品出厂交付合格率100%;
交付时无反馈台数÷
交付总台数,每季度1次;
2)成品一次交验合格率≥90%;
交验合格数÷
交验成品数,每月1次;
3)零部件一次交验合格率≥95%;
交验零部件数,每月1次;
4)产品检验正确率≥98%;
检验正确数÷
检验总数,每月1次;
5)计量器具周检率100%;
实际检定量具÷
计划周检量具;
每季度1次;
6)产品平均首次无故障工作时间≥350小时;
首次出现故障时间之和÷
交付三包期内总台数,每季度1次;
7)产品早期故障率≤5%;
三包期内出现故障的台数÷
交付后三包期内的台数,每季度1次;
8)生产设备完好率100%;
检查完好台数÷
检查总数,每月1次;
9)培训计划完成率100%;
实际完成数÷
计划培训数,每半年1次;
10)质量体系认证审核重要不符合项为0;
认证后根据外审提出的不符合项,由体系办进行检查考核。
11)质量体系认证审核一般不符合项≤3项;
第五章有关金属材料基本知识
(一)金属材料的性能
1、强度:
金属材料抵抗塑性变形(永久变形)和断裂的能力称之为强度,抵抗能力越大,则强度越高。
测定强度高低的方法通常采用试验法,其中拉伸试验应用最普遍。
1.1、强度应力曲线图(见P6页图1-3)
1.2、表示强度的3个常用概念及符号:
1)弹性极限σe:
在弹性变形内所承受的最大拉伸应力;
2)屈服极限σs:
产生屈服时所承受的最大拉伸应力;
3)强度极限σb:
被拉断前使能承受最大拉伸的应力;
4)应力用符号σ表示,其单位为Pa(帕)或MPa(兆帕)。
1Pa=1N/㎡,1MPa=106Pa
2、硬度:
硬度是指金属材料抵抗局部变形,特别是局部塑性变形、压痕或划痕的能力,是衡量材料软硬的判据,也可以从一定程度上反映材料的综合力学性能。
材料的硬度可通过硬度试验来测定。
常用的硬度试验方法有布氏测试法、洛氏测试法、维氏测试法和里氏测试法,其中前两种方法应用最广泛。
2.1、布氏硬度:
用布氏测试法测定的硬度。
用HBS或HBW表示。
2.2、洛氏硬度:
用洛氏测试法测出的硬度值,用HRC表示。
3、塑性:
塑性是指金属材料断裂前发生不可逆永久变形的能力。
塑性好的金属材料便于进行压力加工成形。
判断金属材料塑性好坏的主要判据是断后伸长率σ和断面收缩率ψ。
断后伸长率是试样被拉断后,标距的伸长量同原始标距的百分比,即σ=
ⅹ100%
式中lk---试样被拉断后的长度(mm);
lo---试样的原始标距长度(mm)。
4、韧性:
韧性是指金属材料在断裂前吸收变形能量的能力。
韧性主要反映了金属抵抗冲击力而不断裂的能力。
韧性好的金属抗冲击的能力强。
韧性的判据是通过冲击试验确定的。
最常用的冲击试验是摆锤式一次性冲击试验。
5、疲劳强度:
许多零件工作时其内部都存在着变应力(即随时间变化的应力)。
如果这种变应力作周期性变化,则称之为循环应力或交变应力。
零件在交变应力下工作时,尽管有时交变应力值远远低于抗拉强度,但经过一定的应力循环次数后也会在一处或几处产生局部永久性积累损伤,导致零件产生裂纹或突然发生断裂。
这个过程称为金属疲劳(疲劳破坏)。
据统计,大部分零件的损坏都是由于金属疲劳造成的。
(二)常用热处理
1、退火:
退火是指将钢件加热至临界温度(可查有关资料)以上30~50℃,保温一段时间后再缓慢冷却(常随炉冷却)的工艺,多用来消除铸件、锻件、焊接件的内应力,降低其硬度以易于切削加工,细化晶粒、改善内部组织,增加零件的韧性。
2、正火:
正火是指将钢件加热到临界温度以上,保温一段时间后放入空气中冷却的工艺,多用来处理低碳钢、中碳钢和表面渗碳零件,使其组织细化,增加强度和韧性,减少内应力,改善其切削性能。
3、淬火:
淬火是指将钢件加热至临界温度以上,保温一段时间后放入淬火介质(又称淬火剂)中急剧冷却的工艺,用来提高钢的硬度和强度以及疲劳强度。
常用的淬火剂有水、盐水、机油等。
要注意,因淬火时工件内部会产生较大的内应力,工件回变脆,故淬火后必须回火。
4、回火:
回火是指将淬硬的工件加热至临界点以下某一温度,保温一段时间后让工件在空气或油中冷却的工艺,分为低温回火、中温回火和高温回火三种情况。
回火的目的是消除工件淬火后的脆性和内应力,提高钢的塑性和韧性。
5、调质:
调质是指将工件淬火后又高温回火的热处理工艺过程,其目的是提高工件的综合力学性能。
重要零件一般都需要经过调质。
6、表面淬火:
为了使某些零件(如齿轮)满足即耐磨又耐冲击的工作要求,应使其工作面表层有较高的硬度、强度和耐磨性而心部仍保持原有的强度和韧性,可采用某些加热方式使工件的表面迅速达到淬火高温而心部温度还很低时对其进行淬火,这种工艺称为表面淬火。
7、渗碳:
为了增加零件表层的含碳量和一定的碳浓度梯度,将工件在渗碳介质中加热并保温,使碳原子渗入工件表层的化学热处理工艺称为渗碳。
渗碳可以使得零件表面的硬度高、强度高、耐磨性好而保持心部原有的韧性和强度,多用在受冲击载荷的低碳钢、低碳合金钢或中碳钢零件中。
8、渗氮:
渗氮也是一种化学热处理工艺,其工艺方法与渗碳类似。
由于氮的特殊作用,使得工件表面的硬度更高,耐磨性与耐蚀性好。
渗氮多用于耐磨性零件(钢件或铸铁件),特别适用于在潮湿或燃烧气体介质中工作的零件。
9、时效:
时效是指先将钢件加热至不大于120-130℃的温度,长时间保温后再让其随炉或在空气中冷却的工艺,用来消除或减小工件的微观应力,防止其变形和开裂,稳定工件的形状和尺寸。
(三)机械工程常用材料(见P12页图1-9)
1、铸铁:
(见P13-14页的文字内容)
1)灰口铸铁(断口呈灰色):
灰铸铁、球墨铸铁、蠕墨铸铁、可鍛铸铁;
2)白口铸铁(断口呈亮白色),硬度高、脆性大、难加工,作为炼钢毛坯;
2、工业用钢:
工业用钢的4种分类法(见P14页中2.1)-2.4)条
1)按用途分为:
结构钢、工具钢、专门用途钢及特殊性能钢;
2)按含碳量多少分为:
低碳钢(含C≤0.25%)、中碳钢(含C=0.25%-0.60%)、高碳钢(含C≥0.60%);
3)按含有害杂质元素(硫S、磷P)的多少分为:
普通钢、优质钢、高级优质钢;
4)按合金元素含量多少分为:
非合金钢、低合金钢、合金钢;
2.1、非合金钢(碳素钢)的牌号及说明(见P15表1-3)
1)碳素结构钢:
Q235A;
2)优质碳素结构钢:
35、45
3)碳素工具钢:
T8、T12A
4)铸造碳钢:
ZG200-400
2.2、合金钢(见P15-P16表1-4)
1)合金结构钢:
60Si2Wn
2)合金工具钢:
9Mn2VW18Cr4V
3)特殊性能钢:
0Cr18Ni9
2.3、结构钢(见P16页中第1条)
1)碳素结构钢(见P16页中第1)条)
Q235A;
Q235B;
Q235C;
Q235D;
Q215A;
Q215B;
Q195
2)低合金高强度结构钢(见P17页中第2)条)
Q295;
Q345;
460;
3)优质碳素结构(见P17中第3)条,P17-P18页中表1-6)
08F、15、20、25、35、40、45、50Mn、65、65Mn
4)合金结构钢(见P18页中部分内容,P19页表1-7和表1-8)
合金渗碳钢:
20Cr、20CrMnTi、18Cr2Ni4WA;
合金调质钢:
40Cr、35CrMo、40CrNiMoA
5)铸钢(见P20页表1-9)
ZG200-400、ZG230-450、ZG270-500、ZG310-570
2.4、工具钢(见P19页上两行)
1)碳素工具钢(见P20页中两段)
T7T7AT8T8AT8MnT8MnAT9T9AT10T10AT11T11AT2T12A等
2)合金工具钢(见P20页中第2)条)
9SiCrCr29Cr2
3)高速工具钢(又称为:
锋钢、白钢)(见P21页表1-10)
W18Cr4VW6Mo5Cr4V2W6Mo5Cr4V2A
3、硬质合金(见P21-22中划线内容及表1-11)
1)钨钴合金:
YG3YG3XYG6YG6XYG8YG8CYG15YG6A
2)钨钴鈦合金:
YT5YT14YT15YT30
3)通用合金(万能合金):
YW1YW2
第六章形位公差基本概念
符号
⊥
0.01
∥
0.1
A面
◎
φ0.1
A
↗
A-B
含义
垂直度
≤0.01
以A面为基准
平行度≤0.1
同轴度
≤0.1
以A为基准
对称度≤0.1
位置度≤0.1
以A-B为基准
跳动度≤0.1
2、以下形位公差符号的含义
第七章机械制图基本概念
1、机械制图中有6个基本视图;
他们之间保持三个相等关系;
优先选用3种视图
——6个基本视图是:
主视图、俯视图、左视图、右视图、仰视图、后视图;
——他们之间保持着“长对正、高平齐、