级进模例题1Word格式文档下载.docx
《级进模例题1Word格式文档下载.docx》由会员分享,可在线阅读,更多相关《级进模例题1Word格式文档下载.docx(27页珍藏版)》请在冰豆网上搜索。
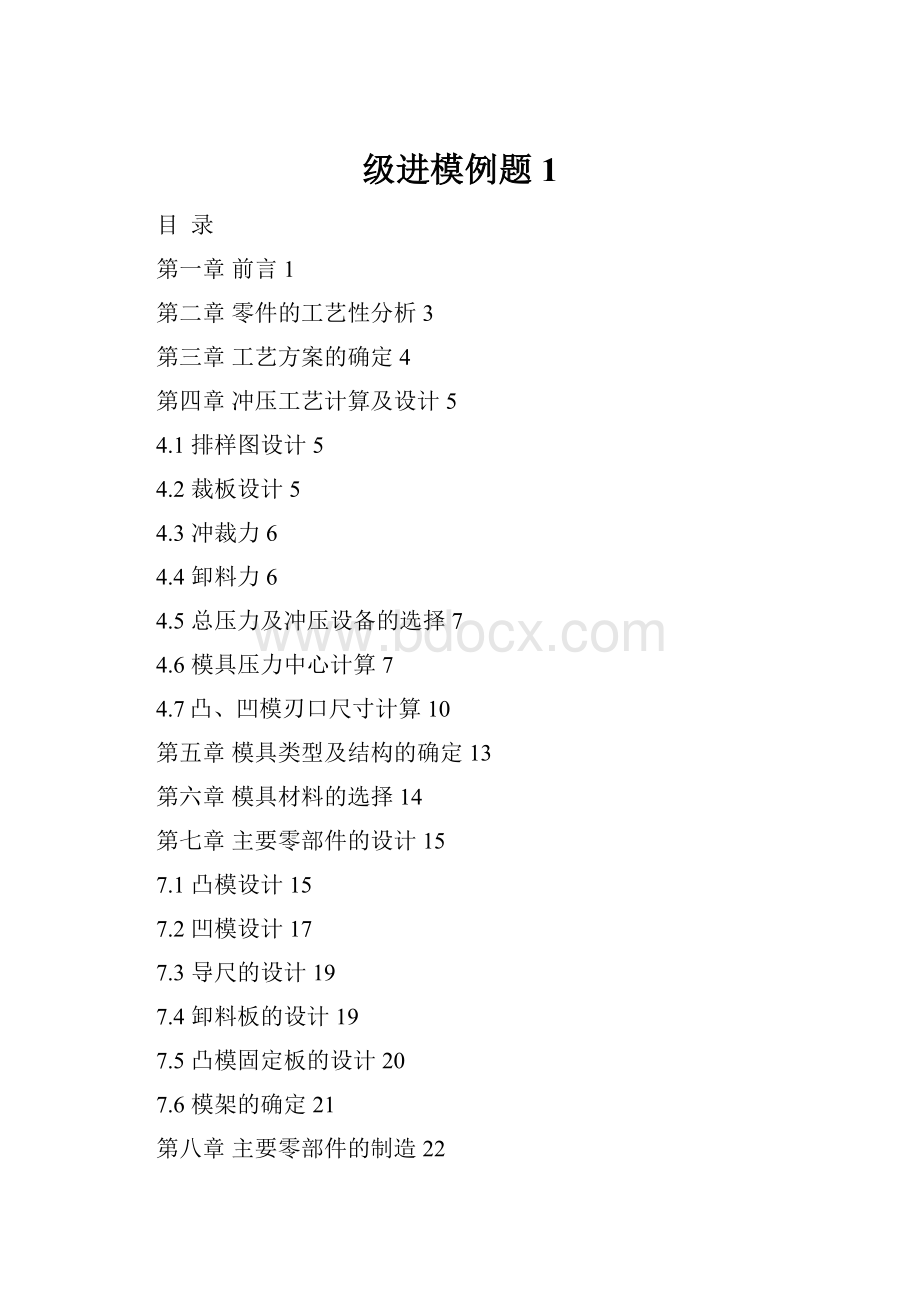
生产批量:
大批量
材料:
10
料厚:
2.0mm
工件简图,如图2.1所示:
图2.1
此工件为冲裁件,由冲空和落料两道工序组成。
外形为落料件,要冲的孔共有1个,都是φ8的孔,,工件的精度要求不高,模具的设计与制造要考虑的是结构合理、制造加工方便经济。
第三章工艺方案的确定
此工件所需的基本冲压工序为冲孔、落料。
可以拟出如下几种工艺方案:
方案一:
先落料,再冲孔的单工序冲裁;
方案二:
冲孔、落料复合模冲裁;
方案三:
冲孔、落料级进模冲裁;
采用方案一,用单工序冲裁模冲裁,冲压精度一般,生产率低,要求不严格,工件尺寸的积累误差大;
采用方案二,用冲孔、落料复合模进行冲裁,冲压成品件表面平直,精度也较高,但因工件结构较复杂,加工制造相对困难,模具成本较高,并且冲压后成品件留在模具上,在清理模具上的物料的时会影响冲压速度,增加操作危险性,而且本产品的精度要求并不需要很高,且生产通用性差,结构复杂,制造难度大。
方案三,用冲孔、落料的进模冲裁,在级进模上所产生的冲压制件和废料,多数都取下漏方式排出,不要对模具进行清理,从而大大提高了生产效率,从安全生产的角度看,送料时一般不需人手进入危险工作,因而大大提高了安全性,而且可保证工件尺寸精度的要求。
故该制件的生产采用冲孔,落的级进模。
模具简图,如图3.1所示
图3.1
第四章冲压工艺计算及设计
4.1排样图设计
根据已确定的冲裁工艺方案和模具类型,考虑的工件结构特点,排样方案设计为有废料排样。
采用如图4.1所示的排样方法,可显著的减少废料,冲裁方式采用隔位冲压。
图4.1
4.2裁板设计
因采用隔位冲压,为增加搭边的刚性,这里的搭边值可适当增加;
查表得
=2,a=1.8.
条料宽度B根据以下公式(4-1)计算:
B=[D+2(a1+△)+C1]
式中D为工件横向最大尺寸=40mm,a1为横搭边值,其值见表2-10.△为条料宽度公差=0.5C1为最小双面导料间隙,则B=[40+2(2+0.5)+0.2]=45.2;
材料利用率的计算:
(一)一个步距的材料利用率
=﹙A/sB﹚×
100%=﹙663.3/22.8×
45.2﹚×
100%=64.3%
A—一个步距内工件的有效面积﹙由Ug造型可得为663.3﹚
s—送料步距
B—材料宽度
(二)条料的材料利用率
=﹙nA÷
LB﹚×
100%=[﹙47×
663.3﹚÷
﹙1000×
45.2﹚]=69%
n—一根条料能冲出的工件数目﹙1000÷
21=47﹚
L—一根条料的长度
A—一个工件的有效面积
4.3冲裁力
根据公式F=Ltδb计算冲裁力
F=Ltδb=133.8×
2×
325=86970﹙N﹚
L—冲裁件轮廓的总长度﹙由Ug造型可得为133.8mm﹚
t—板料厚度﹙mm﹚
δb——材料的抗拉强度﹙Mpa﹚
4.4卸料力
FQ1=K1×
F=0.05×
86970=4348.5﹙N﹚
K1—卸料力系数查表2-15得0.05
F—冲裁力
4.5总压力及冲压设备的选择
由于是刚性卸料顺出键的模具,所以总冲压力F0=F+FQ1=86970+4348.5=91318.5﹙N﹚
FQ1=卸料力
冲压设备的选择,冲压生产中常用的冲压设备种类很多,选用冲压设备时主要应考虑下进回表:
1、压设备的类型和工作形式是否适合于应完成的工序;
是否符合安全生产和环保要求;
2、冲压设备的压力和功率是否满足应完成工序的需要
3、冲压设备的装模高度,工作尺寸,行程等是否适合应完成工序所用的模具。
4、冲压设备的行程次数是否满足生产率的要求等。
根据模具的形状尺寸及制件精度,这里选用开式可倾工作台压力机,其主要参数见表1
表1开式可倾工作台压力机主要参数
标称压力
最大闭合高度
/mm
工作台尺寸(左右X前后)
工作台孔尺寸直径/mm
模柄孔尺寸(直径X深度)/mm
/KN
/tf
180
360X240
130
30X50
100
4.6模具压力中心计算
冲裁力合力的作用线与凹模平面的交点称为冲裁的压力中心。
如果压力中心偏离压力机滑块中心线,工作中滑块和模具都将承受偏载,偏离越多,偏载越大。
结果,将加速压力机和模具导向件的磨损,也会破坏冲裁间隙的均匀性,降低模具寿命。
因此,模具设计应力求压力中心与压力机滑块的中心线重合。
计算压力中心时,如图4.2所示:
在图4.2中将XOY坐标建立在图的对称中心线上,在图中将冲裁线按几何图分成
~
共4组线段,每组线段都要计算出线段的总长度,及其中心坐标。
(1)各几何线段长度及中心坐标:
、、图4.2
4.8凸、凹模刃口尺寸计算
1、凸、凹模的加工方法
凸、凹模的加工方法一般有两种,一种是凸、凹模分开加工,另一种是凸、凹模配合加工。
凸、凹模分开加工时,是指凸模与凹模分别按图加工尺寸要求加工。
凸、凹模具有互换性,当制件形状复杂或凸、凹模,配合间隙较小时,采用分开加工法比较困难。
此时,可采用配合加工法,即无加工凸模(或凹模),这种加工法容易保证凸凹模间的间隙。
本文所定的工件形状较为复杂。
凸、凹模采用配合加工法较为适宜。
但对于工件上一些通孔及形状规则的孔采用分开加工法比较适宜。
2、凸、凹模间隙
已知工件材料为10,材料厚度t=2.0mm。
查表得Zmax=0.18mm,Zmin=0.13mm
3、冲孔
以凸模为基准,凸模在实际工作中磨损后会逐渐减小,为了使模具具有一定使用寿命,应加上一个被磨量△。
工件未标注公差,按ITA13级查表,得φ80-0.22,400+0.39,210+0.33磨损系数查表得,X=0.75。
工作零件刃口尺寸的计算:
(1)冲孔凸模刃口尺寸dp=(dmin+X△)
(4-6)
=(7.78+0.75×
0.22)0-0.02=7.9450-0.02
dp—冲孔凸模刃口尺寸
dmin—冲孔件最小极限尺寸
X—磨损补偿系数
δp—凸模尺寸下偏差上偏差为零
δp=0.4(Zmax-Zmin)=0.4×
(0.18-0.13)=0.02
(2)冲孔凹模刃口尺寸
=(dp+Z
)
=(7.945+0.13)0+0.03
=8.0750+0.03
dd—冲孔凹模刃口尺寸
δd—凹模尺寸上偏差,下偏差为零
δd=0.6(Zmax-Zmin)=0.6×
(0.18-0.13)=0.03
(3)落料凹模刃口尺寸Dd=(Dmax-X△)
落料凸模刃口尺寸Dp=(Dd-Zmin)
Dmax—落料件最大极限尺寸
X—磨损补偿系数
δd—凹模尺寸上偏差,下偏差为零
所以当Dmax=40.39时,Dd=(Dmax-X△)
=(40.39-0.75×
0.39)0+0.03=40.09750+0.03
Dp=(Dd-Zmin)
=(40.0975-0.13)0-0.02
=39.96750-0.02
当Dmax=21.33时,Dd=(Dmax-X△)
=(21.33-0.75×
0.33)0+0.03=21.08250+0.03
=(21.0825-0.13)0-0.02
=20.95250-0.02
第五章模具类型及结构的确定
典型的冲裁模类型有三种:
1.单工序冲裁模:
这种模具结构简单,制造周期短,成本较低。
但模具本身无导向,需依靠压力机滑块进行导向,安装模具时调整冲裁间隙较困难,且不易均匀。
因此冲出的工件精度较差,模具寿命较低,而且使用不够安全。
这种模具适于工件质量要求不高、批量较小的单工序冲裁。
2.复合冲裁模:
复合冲裁模具是在压力机滑块一次行程中,在模具同一工位同时完成冲孔和落料。
其基本结构形式有两种:
落料凹模装在下模时成为顺装复合模;
装在上模时成为倒装复合模。
复合模属于复杂模具,制造难度较大。
3.级进冲裁模:
级进冲裁模是在压力机滑块的一次行程、在模具不同工位分别进行工件的内形和外形冲裁,而在最后工位才制成工件。
级进冲裁模的设计十分灵活,采用不同的排样形式、卸料方式、定距方法及导向方式,同一个工件的级进冲裁模可设计成多种结构形式。
模具根据工件图的工艺分析,采用冲孔,落料级进模。
根据工件窄长的特点和排样方案,采用纵向送料方式,模架选用中间导柱。
模具上模部分由垫板、凸模固定板,各个凸模和卸料板等组成。
模具下模部分由导尺、凹模等组成。
凹模采用整件凹模结构,板料采用手工送料,依靠凹模两侧设置的导料板导向,首次冲孔工序,通过导料阶段进行定位,完成后向前移动,通过一个空步,进行第二道落料工序。
模具采用弹性卸料装置,在冲压时卸料板可压紧条料,这样冲出的工件表面平整,毛利少或远毛利。
工件和废料则直接从压力机工作占孔中漏下,不需对模具进行清理,节省了时间,提高了生产率,同时保证安全。
第六章模具材料的选择
模具材料是模具的制造基础,合理选择模具材料,正确实施模具热处理工艺是保证模具寿命,提高模具质量和使用效能的关键。
冷冲模是在常温下对材料进行压力加工或其他加工所使用的模具。
在使用中受到压缩、拉伸、弯曲、冲击、摩擦等机械力的作用。
正常失效形式主要是磨损、脆断、弯曲、啃伤等,因此要求冷作模具刚应有在相应的热处理后,具有较高的变形抗力、断裂抗力、耐磨损、抗疲劳等能力,以保证模具的精度和寿命。
目前我国常用冲模材料有T8、T10、CrWMn,9Mn2V,GCr15,Cr12,CrMoV钢及硬质合金等。
T8、T10属于碳素工具钢,这类钢价格低廉、供应方便、切削性能好,淬火后有较高的硬度和耐磨性,但其淬透性较差、淬火时必须急冷、变形开裂倾向大、回火稳定性差、耐热性低,一般只能在250°
C以下用于制造尺寸较小、形状简单、负荷较小的冲压模具。
CrWMn钢具有较好的淬透性,淬火后保留较多的残余奥氏体,因而淬火变形很小。
钨形成的碳化物硬度很高,耐磨性好,钨还能细化晶粒,提高韧性。
但此钢只适合与制造要求变形小、形状复杂的各种中、小型冲模。
9Mn2V钢具有淬透性好与碳素工具钢,碳化物不均匀性与淬火开裂倾向小于CrWMn钢,淬火变形也比较小,有较高的硬度和耐磨性。
加入锰可提高钢的淬透性,加入钒有利于细化晶粒,提高韧性。
Cr12钢是一种应用广泛的冷作模具钢,淬火加热时碳化物大量溶入奥氏体,淬火后得到高硬度马氏体;
回火时马氏替析出大量弥散分布的碳化物。
由于其硬度很高,因而提高了钢的耐磨性,Cr又使等温转变曲线右移,从而增加了刚的淬透性。
马氏替相变点低,淬火后模具刚中有大量的残留奥氏体,减少了模具淬火时的变形量,由于Cr12刚具有高硬度和良好的耐磨性,所以在冷作模具中已得到广泛应用。
所以这里的外形凸模材料选用Cr12钢
。
第七章主要零部件的设计
7.1凸模设计
1、外形凸模的设计。
外形凸模材料选用Cr12钢。
根据制件的形状,把外形凸模设计成直通式凸模,如图7.1所示。
图7.1
固定方式采用螺钉紧固的方法,用2个m8的螺钉吊装在垫板上,与凸模固定板的配合安Hb/m5。
2个螺钉孔布置,如图7.2所示,螺钉孔位置的选择应满足下式:
凸模最小壁厚m>
1.5t。
图7.2
外形凸模的高度:
L
=
+
—(0.2~1)+
×
90%(7-1)
=102.9mm
这里取103mm
2、圆凸模的设计
3个φ8mm的圆形凸模设计可查ISO8021:
1986进行选取。
因其直径较小易损坏按常拆结构设计,与凸模固定板采用(H6/m5)的配合。
7.2凹模设计
1、凹模刃口形式的确定
凹模的刃口形式主要有直壁式锥形两种,漏料孔根据刃口的形状可分为柱行和锥行两种,这里采用直壁式,如图7.2所示。
各冲裁的凹模刃口部分均采用电火花线切割机床加工,刃口部分深度h,根据材料厚度1.2mm,h一般取5~10mm,这里定为5mm。
落料部分可采用电火花成型加工机床进行扩孔加工。
2、凹模外形的确定。
凹模外形尺寸是否合理,将直接影响到凹模的强度,刚度和耐用度。
所以要经过一定计算来确定。
外形尺寸计算如下:
凹模厚度H:
=
(7-2)
=38mm取整数40mm。
式中F—冲裁力(N)K
—凹模材料修正系数,合金工具钢取K
=1碳素工具钢取K
=1.3
K
—凹模刃口同边长度修正系数
查表2-18,凹模刃口长度修正系数K
=1.25
根据计算的凹模高度尺寸,查表得,取凹模标准尺寸为200mm×
160mm×
40mm。
凹模材料选Cr12钢,用螺钉和销钉直接固定在下模座下。
各螺钉和销钉孔布置如图7.3所示。
图7.3
7.3导尺的设计
导尺也叫导料板,其主要用来对板料进行导向,导尺工作的侧壁设计为平直的。
导尺的内侧与条料接触,外侧与凹模齐平,这样就确定了导尺的宽度。
条料的宽度为109mm,凹模宽度是160mm,导尺与条料之间的间隙一般伪0.03~0.2mm,这里选为0.2mm,则导尺宽度为(160-109-0.2)/2=25.5mm。
导尺厚度查表为6mm。
导尺用销钉和螺钉固定在凹模上。
导尺材料采用45钢,调质处理硬度到40~45HRC。
导尺长度为160mm,入口处设计成15°
如图7.4所示。
图7.4
7.4卸料板的设计
本模具的卸料板不仅要有卸料作用,还要有压料和用外形凸模导向,对小凸模起保护的作用,故采用台阶式弹压卸料板。
其外形尺寸与凹模的边界尺寸相同,为200mmX160mm。
卸料板台阶部分厚度:
H=H-t+Kt(7-3)
式中k——系数,当料厚t>
1mm时,k取0.1。
t——材料厚度,t=1.2mm.
H——导尺厚度,H=12mm.
则h=6-1.2+0.1x1.2
=4.8+0.12
=4.92mm
所以台阶厚度h=4.92+6=10.92mm,取整为11mm。
卸料板总厚度则定为25mm。
因卸料板要对小凸模起保护作用,故凸模与卸料板的间隙应选择小一点,取双面间隙为0.2mm。
卸料板上设置4个M10的卸料螺钉,卸料螺钉在上模座的台阶孔中定位,卸料螺钉工作时的行程为4.2mm,上模座在螺钉尾部应留有足够的行程空间。
橡胶分为两块,两个卸料螺钉安装一块。
橡胶的厚度务必一致,不然会造成受力不均匀,运动产生歪斜,影响模具的正常工作。
卸料材料采用45钢,热处理HRC40~45.
图7.5
7.5凸模固定板的设计
凸模固定板的外形尺寸与凹模一致,为200mm×
160mm。
各凸模孔可采用线切割机床加工,3个圆柱凸模的沉孔可用普通铣床,装上镗刀进行镗孔,镗孔的深度应小于圆柱凸模台阶部分的高度约0.3mm左右,装配时用平面磨床对其进行磨削,这样能够保证装配后圆柱凸模不会上下位移,减少冲击,延长使用寿命。
固定板用螺钉吊装在上模座上。
材料采用45刚,调质热处理HRC40~45。
7.6模架的确定
模架的类型有很多种,按导柱不同的位置可分为四种模架:
中间导柱模架、后侧导柱模架、对角导柱模架、四导柱模架。
根据前面确定的模具类型和卸料、出料形式,采用对角导柱模架,依据凹模尺寸,查国标GB2852.1—81和GB2852.1—81确定上下模座,查国标GB2861.1—81和GB2861.6—81确定导柱和导套。
第八章主要零部件的制造
模具的加工方法有很多。
一般有机械加工、数控机床加工、精密机械加工、电火花加工。
但目前国内外的线切割机床占加工机床的六成以上。
电火花线切割加工在模具制造中应用最为广泛。
8.1凹模
凹模总体的制造工艺过程为:
锻造——热处理(退火)——机械加工——热处理(淬火+回火)——线切割——热处理(回火)。
凹模采用Cr12钢。
由于Cr12型高碳高铬冷作模具刚结晶过程中析出的碳化物极其稳定,以常规热处理方法无法细化。
在较大规格钢材中残留有明显的带状或网状碳化物,而且钢材规格越大,碳化物不均匀度越严重。
碳化物严重偏析,不仅易产生淬火变形及开裂,而且会使热处理后的力学性能变坏,尤其是横向性能下降更多,严重影响模具使用寿命。
因此对Cr12钢必须进行锻造以改善碳化物的不均匀性,保证模具的强度、韧性及使用寿命。
锻造实际操作时一定要严格按照锻造工艺规范,其关键在于毛坯加热温度及保温时间。
温度低、时间短、透烧不足或变形抗力太大,会产生锻件内裂或裂纹:
而加热温度过高,会使毛坯过热或过烧,导致锻打碎而报废;
保温时间长,会造成晶粒长大及表面严重蜕碳。
加热时要先预热,再逐渐升温,注意工件放置的位置要适当,切应注意翻料,以使加热均匀。
锻打时坚持多向墩拔,反复墩粗、拔长,将网状碳化物和共晶碳化物打碎,消除碳化物的不均匀性。
锻后应注意暖冷并及时退火。
锻后一般退火:
加热温度为850~970℃,保温4~5h,炉冷至500℃以下出炉空冷,退火后硬度≤229HBS,为粒状珠光体碳化物。
锻后进行机械加工。
这里的加工主要是对凹模外行尺寸及各螺纹孔的加工。
外形可用刨床对其进行粗加工,然后用磨床进行半精加工。
在电火花线切割加工之前还应进行热处理,即淬火和回火。
淬火:
加热温度为950~980℃,抽冷,硬度≥60HRC。
回火:
一般回火温度为180~200℃,这里为了防止电火花线切割裂纹和磨削裂纹,提高Cr12钢模具的韧性,建议采取400℃回火。
回火后硬度为58~60HRC。
电火花线切割加工,凹模加工是去除内腔,所以线切割前须先打好钼丝孔,钼丝孔打在中心线O上,走丝路线如图8.1中虚线所示。
编程采用3B格式,由于凹模型腔比较复杂,所以采用自动编程。
线切割结束后还要进行低温回火热处理,以消除加工产生的内应力。
图8.1
8.2外型凸模
凸模制造工艺与凹模基本相同,只是电火花线切割加工部分不同。
凸模走丝路线如图8.2所示,
图8.2
异型凸模线切割程序
N1:
B0B3900B3900GYL2;
N2:
B0B3900B7800GXSR1;
N3:
B5100B0B5100GXL3;
N4:
B0B5200B5200GYL4;
N5:
B5000B0B5000GXL1;
N6:
B0B3000B3000GYL4;
N7:
B8200B0B8200GXL1;
N8:
B0B24200B24200GYL2;
N9:
B008200B0B8200GXL3;
N10:
N11:
B5000B0B5000GXL3;
N12:
N13:
B5100B0B5100GXL1;
N14:
B0B3900B3900GYL4DD;
方孔凸模线切割程序:
1.B4900B0B4900GXL3
2.B4100B4100B4100GYL2
3.B1083B0B1083GXL3
4.B4100B4100B4100GYL3
5.B4100B4100B4100GYL4
6.B1083B0B1083GXL1
7.B4100B4100B4100GXL1
8.B4900B0B4900GXL1DD
第九章模具装配
此模具是一副弹压卸料板级进模,采用配合加工法保证装配精度。
选取凹模为装配准件,先装下模部分,后装上模部分。
9.1复检模具零件
按零件图要求,并结合级进模装配是具体工艺要求检验已制作完成的全部模具零件(模具装配时需配做完成的加工内容不在检验项目之中)。
9.2左、右导料板的补充加工
1.对按装配图的位置要求划出导料板的基准线。
将左、右导料板放在凹模面上,与凹模边缘齐,然后用平行夹板夹住凹模和左、右导板,用
mm的钻头钻通导料板,并在凹模上钻7mm的深度。
2.将导料板和凹模拆开用
mm的钻头钻通导料板
的孔,并两面倒角。
用
的螺钉连接导料板和凹模,不要旋紧。
用铜棒轻击导料板,调整左、右导料板的位置,保证左右导料板内侧边缘与落料型孔边缘等距,且间距为109mm
9.3下模座的补充加工
1.在凹模上划出装配螺钉的位置,根据凹模外形在下模座上划出凹模外形轮廓线,保证凹模工作时的压力中心在下模座的中心,按线找正凹模位置,用平行夹板夹紧凹模和下模座。
mm的钻头通过凹模螺钉孔在下模座钻出锥窝。
2.做记号后拆开凹模和下模座。
mm的钻头在下模座上钻
的螺钉过孔,在底面用
mm的钻头扩孔,在用
mm钻头磨成的平钻钻孔,保证沉孔深10mm左右。
3.用
的螺钉连接凹模和下模座,按线找正凹模位置,旋紧螺钉。
mm的钻头钻出凹模销孔,通过凹模销孔向下模座钻锥窝,通过凹模型腔孔在下末座上用划针划出漏料孔轮廓线。
将凹模和下模座拆开,用
mm的钻头钻圆柱销预孔,然后用绞刀至
mm,并将下模座上各孔倒角。
4.下模座上的漏料孔可按轮廓线钻削、铣削,也可采用线切割机床加工。
9.4下模部分的组装
将导料板、凹模、下模座按装配图的位置找正,打入适当过盈的圆柱销,再用螺钉紧固。
把始用挡料装置和承料板用螺钉固定在导料板上,把固定挡料销装入预定孔内。
9.5组装凸模组件
1.将落料凸模和冲孔小凸模分别压入土模固定板中,压入时要用90度角尺检测凸模和不固定板的垂直度。
每压入一个都要以凹模为基准,在凸模压入固定板后用透光法检测并修整与凹模的间隙至要求。
2.磨平凸模尾端与凸模固定板齐平,翻面磨平凸模刃口。
磨削刃口时应以等高垫块,套上卸料板,以防磨削刃口时小凸模折断。
9.6凸模固定板的补充加工
1.将已加工好螺钉过孔和销孔的垫板放在凸模固定板上,找正相互位置后用平行夹板夹紧,用
12mm、
8.5mm、
8mm的钻头分别通过垫板在凸模固