FDM概述Word格式.docx
《FDM概述Word格式.docx》由会员分享,可在线阅读,更多相关《FDM概述Word格式.docx(11页珍藏版)》请在冰豆网上搜索。
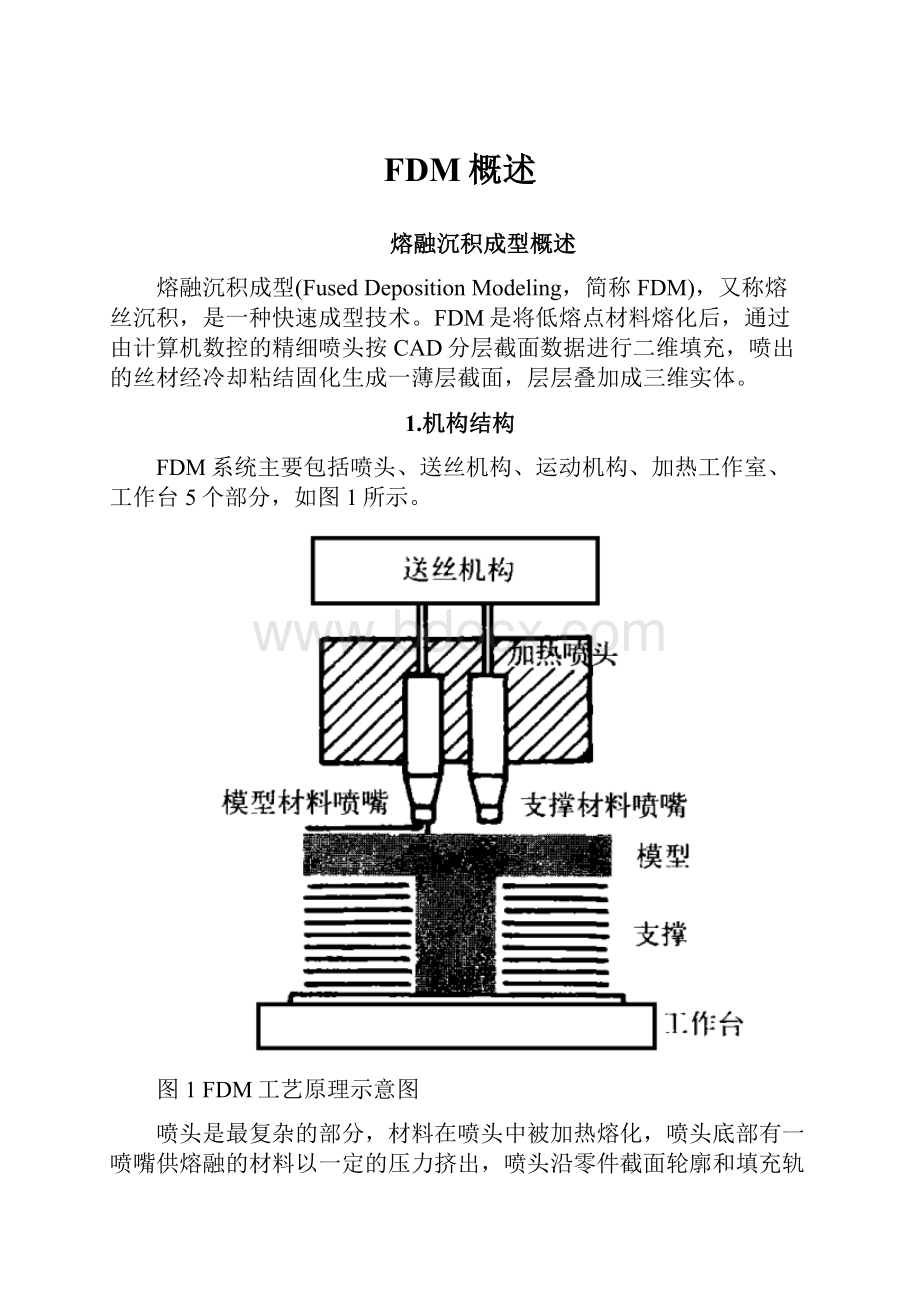
加热工作室用来给成型过程提供一个恒温环境。
熔融状态的丝挤出成型后如果骤然受到冷却,容易造成翘曲和开裂,适当的环境温度可最大限度地减小这种造型缺陷,提高成型质量和精度。
工作台主要由台面和泡沫垫板组成,每完成一层成型,工作台便下降一层高度[]。
2工艺参数控制
在使用FDM快速成型系统进行成型加工之前,必须考虑相关工艺参数的控制。
它们是分层厚度、喷嘴直径、喷头温度、环境温度、挤出速度、填充速度、理想轮廓线的补偿量以及延迟时间[]。
分层厚度是指将三维数据模型进行切片时层与层之间的高度,也是FDM系统在堆积填充实体时每层的厚度。
分层厚度较大时,原型表面会有明显的“台阶”,影响原型的表面质量和精度;
分层厚度较小时,原型精度会较高,但需要加工的层数增多,成型时间也就较长。
喷嘴直径直接影响喷丝的粗细,一般喷丝越细,原型精度越高,但每层的加工路径会更密更长,成型时间也就越长。
工艺过程中为了保证上下两层能够牢固地粘结,一般分层厚度需要小于喷嘴直径,例如喷嘴直径为0.15mm,分层厚度取0.1mm。
挤出速度是指喷丝在送丝机构的作用下,从喷嘴中挤出时的速度。
填充速度则是指喷头在运动机构的作用下,按轮廓路径和填充路径运动时的速度。
在保证运动机构运行平稳的前提下,填充速度越快,成型时间越短,效率越高。
另一方面,为了保证连续平稳地出丝,需要将挤出速度和填充速度进行合理匹配,使得喷丝从喷嘴挤出时的体积等于粘结时的体积(此时还需要考虑材料的收缩率)。
如果填充速度与挤出速度匹配后出丝太慢,则材料填充不足,出现断丝现象,难以成形;
相反,填充速度与挤出速度匹配后出丝太快,熔丝堆积在喷头上,使成型面材料分布不均匀,表面会有疙瘩,影响造型质量。
喷嘴温度是指系统工作时将喷嘴加热到的一定温度。
环境温度是指系统工作时原型周围环境的温度,通常是指工作室的温度。
喷嘴温度应在一定的范围内选择,使挤出的丝呈粘弹性流体状态,即保持材料粘性系数在一个适用的范围内。
环境温度则会影响成形零件的热应力大小,影响原型的表面质量。
研究表明,对改性聚丙稀这种材料,喷嘴温度应控制在230℃。
同时为了顺利成型,应该把工作室的温度设定为比挤出丝的熔点温度低1℃-2℃。
FDM成型过程中,由于喷丝具有一定的宽度,造成填充轮廓路径时的实际轮廓线超出理想轮廓线一些区域,因此,需要在生成轮廓路径时对理想轮廓线进行补偿。
该补偿值称为理想轮廓线的补偿量,它应当是挤出丝宽度的一半。
而工艺过程中挤出丝的形状、尺寸受到喷嘴孔直径、分层厚度、挤出速度、填充速度、喷嘴温度、成形室温度、材料粘性系数及材料收缩率等诸多因素的影响,因此,挤出丝的宽度并不是一个固定值,从而,理想轮廓线的补偿量需要根据实际情况进行设置调节,其补偿量设置正确与否,直接影响着原型制件尺寸精度和几何精度。
延迟时间包括出丝延迟时间和断丝延迟时间。
当送丝机构开始送丝时,喷嘴不会立即出丝,而有一定的滞后,把这段滞后时间称为出丝延迟时间。
同样当送丝机构停止送丝时,喷嘴也不会立即断丝,把这段滞后时间称为断丝延迟时间。
在工艺过程中,需要合理地设置延迟时间参数,否则会出现拉丝太细,粘结不牢或未能粘结,甚至断丝缺丝的现象;
或者出现堆丝、积瘤等现象,严重影响原型的质量和精度。
3工艺特点
与其他工艺相比,FDM工艺具有以下优势:
(1)不采用激光系统,使用和维护简单,从而把维护成本降到了最低水平。
多用于概念设计的FDM成型机对原型精度和物理化学特性要求不高,便宜的价格是其推广开来的决定性因素。
(2)成型材料广泛,热塑性材料均可应用。
一般采用低熔点丝状材料,大多为高分子材料如ABS、PLA、PC、PPSF以及尼龙丝和蜡丝等。
其ABS原型强度可以达到注塑零件的三分之一,PC,PC/ABS,PPSF等材料,强度己经接近或超过普通注塑零件,可在某些特定场合(试用,维修,暂时替换等)下直接使用。
虽然直接金属零件成型的材料性能更好,但在塑料零件领域,FDM工艺是一种非常适宜的快速制造方式。
随着材料性能和工艺水平的进一步提高,会有更多的FDM原型在各种场合直接使用。
(3)环境友好,制件过程中无化学变化,也不会产生颗粒状粉尘。
与其他使用粉末和液态材料的工艺相比,FDM使用的塑料丝材更加清洁,易于更换、保存,不会在设备中或附近形成粉末或液体污染。
(4)设备体积小巧,易于搬运,适用于办公环境。
(5)原材料利用率高,且废旧材料可进行回收再加工,并实现循环使用。
(6)后处理简单。
仅需要几分钟到一刻钟的时间剥离支撑后,原型即可使用。
而现在应用较多的SL,SLS,3DP等工艺均存在清理残余液体和粉末的步骤,并且需要进行后固化处理,需要额外的辅助设备。
这些额外的后处理工序一是容易造成粉末或液体污染,二是增加了几个小时的时间,不能在成型完成后立刻使用。
(7)成型速度较快。
一般来讲,FDM工艺相对于SL,SLS,3DP工艺来说,速度是比较慢的,但是其也有一定的优势。
当对原型强度要求不高时,可通过减小原型密实程度的方法提高FDM成型速度。
通过试验,具有某些结构特点的模型,最高成型速度己经可以达到60cm3/h。
通过软件优化及技术进步,预计可以达到200cm3/h的高速度。
同样其缺点也是显而易见,主要有以下几点:
(1)由于喷头的运动是机械运动,速度有一定限制,所以成型时间较长;
(2)与光固化成型工艺以及三维打印工艺相比,成型精度较低,表面有明显的台阶效应;
(3)成型过程中需要加支撑结构,支撑结构手动剥除困难,同时影响制件表面质量。
4产品发展及技术研究现状
(1)产品发展
FDM工艺由美国学者ScottCrump博士于1988年率先研制成功。
现今FDM产品制造系统应用最为广泛的主要是Stratasys公司,Stratasys公司于1993年开发出第一台FDM-1650机型后,先后推出了FDM-2000、FDM-3000和FDM-5000机型。
引人注目的是1998年Stratasys公司推出的FDM-Quantum机型,最大造型体积为600mm×
500mm×
600mm。
由于采用了挤出头磁浮定系统,可在同一时间独立控制两个挤出头,因此其造型速度为过去的5倍。
1999年Stratasys公司开发出水溶性支撑材料,有效地解决了复杂、小型孔洞中的支撑材料难以去除或无法去除的难题,并在FDM-3000得到应用,另外从FDM-2000开始的决速成型机上,采用了两个喷头,其中一个喷头用于涂覆成型材料,另一个喷头用于涂覆支撑材料,加快了造型速度。
目前stratasys公司的主要产品有:
适合办公室使用的FDMVantage系列产品以及在此基础上开发的可成型材料更多的FDMTitan系列产品,另外还有成型空间更大且成型速度更快的FDMMaxum系列产品,还有适合成型小零件的紧凑型prodigyplus成型机[]。
stratasys公司1998年与MedModeler公司合作开发了专用于一些医院和医学研究单位的MedMedeler机型,并于1999年推出可使用聚脂热塑性塑料的Genisys型改进机型GenisysXs。
该公司自2002年起在年即设备销售台数上超过美国3DSystems公司,成为世界上最大的RP设备销售商,目前Stratasys公司每年销售的RP设备占到全球销售总量的一半左右。
(2)技术研究
在国内,上海富力奇公司的TSJ系列快速成型机采用了螺杆式单喷头,清华大学的MEM一250型快速成型机采用了螺杆式喷头,华中科技大学和四川大学正在研究开发以粒料、粉料为原料的螺杆式双喷头。
其中,北京殷华公司通过对熔融挤压喷头进行改进,提高了喷头可靠性并在此基础上新推出了MEM20O小型设备,MEM350型工业设备以及基于光固化工艺的AURO一350型设备。
此外,殷华公司近几年推出了专门用于人体组织工程支架的快速成形设备MedtisS。
该型设备以清华大学激光快速成形中心发明的低温冷冻成形(LDM)工艺为基础,最多可同时装备4个喷头。
该设备成形材料广泛,可成形PLLA、PLGA、PU等多种人体组织工程用高分子材料。
成形的支架孔隙率高,贯通性好,在组织工程中有良好的应用前景[]。
在系统方面,丹麦科技大学(TechniealUniversityofDenmark)的BelliniAnna将一个微型挤出器安装在一个精确定位系统上,它能直接使用颗粒状原料,从而扩大了FDM工艺的使用范围。
提高FDM制件的性能,达到使用FDM工艺制造特殊原型和熔融沉积快速成型精度及工艺研究快速制造的目的。
目前,该系统和使用该系统的制件已经制作出来,但是一些工艺参数(如颗粒度等)还需要进一步优化。
王伊卿、方勇等对两种典型结构溶融沉积快速成型喷头中材料的压力场和速度场进行了有限元分析和实验验证,得出导致断丝的几个重要因素,并设计了一体化的喷头,保证出丝顺畅[]。
在材料方面,新加坡国立大学(NationalUniversityofSingaPore)的DietmarW等人研制了一种新型PCL材料用于组织工程中,并通过数据说明了支架的多孔性和抗压性之间存在极大的关系[]。
EricJ,Vamsik等通过对ABS材料的改性处理,使材料表面具有亲水性和生物相容性,从而使得FDM工艺能够运用到生物领域,制备具有生物相容性的活性制件[],拓展了FDM工艺的应用范围。
S.Kannan,,Dr.D.Senthilkumaran等在利用FDM进行成型时,对传统ABS材料添加镍涂层,并与未添加涂层的制件比较,发现添加了涂层的制件在机械性能上远远优于未添加涂层的制件[]。
在工艺方面,西安交通大学把FDM工艺中材料挤出过程改为由空气压缩机提供的压力挤出。
结果表明,以气压作为挤压动力有效可行,系统工艺简单,成形材料选择范围广泛,可完成传统FDM的快速设计任务,还可完成制造人工生物活性骨的模型加工[]。
JorgeMireles、Ho-ChanKim等利用FDM成型工艺进行低熔点金属合金的成型,制备了金属实体零件,同时验证单层的导电性,他们还对制件过程中的参数选择做了简单介绍[]。
OlafDiegel、SaratSingamneni等提出了一种新的弯曲层溶融沉积制造方案,并利用其进行具有导电性的聚合物的打印,甚至将FDM工艺推广到电子电路的制造中[]。
穆存远、李楠等针对快速成型时采用逐层叠加制造的基本思想,对成型时的台阶效应引起的正偏差进行了分析计算,得出了影响该误差的因素及其误差曲线图,提出了减小误差的方法[]。
在实验方面,印第安科技大学(IndianInstituteofTeehnology)的K.Thrimurthulu等人以成型件的成型时间和表面粗糙度为测试对象,通过遗传算法求出最优的成型方向,并通过实验验证了其合理性,该算法可以用来获取任意成型件的最优成型方向。
新加坡国立大学(NationalUniversityofSingpore)的DietmarW等人用FDM制作组织工程中的细胞支架并研究其机械性能及机体对于支架的反应、接纳程度,实验结果证明在3-4周的时间里,新的组织可以在FDM制造的支架下生长。
大连理工大学的郭东明教授人也进行了FDM工艺参数优化设计,先是提出丝宽理论模型,然后通过正交试验得到影响试件尺寸精度及表面粗糙度的显著因素及水平,并进行参数优化,大幅度提高成型件的成型精度[,,]。
朱传敏、许田贵等对溶融沉积制造的填充方式进行了研究,针对四多边形截面凸分解得到的子区,应用一种偏置与直线复合算法,对多边形轮廊进行填充,并成功应用在实例中[]。
在应用方面,澳大利亚Swinburne大学的MasoodS.H.教授等人使用FDM工艺直接喷射金属制作注塑模嵌件。
目前,他们正在对这种新工艺,以及使用这种注塑模制作出来的塑料件进行研究。
清华大学的颜永年教授等人利用喷射/挤出沉积成形方法制作了骨模型和耳状软骨,并在狗和兔子上进行了实验。
颜永年教授还于2005年正式提出生物制造工程的概念,于2008年提出低温工程与绿色制造,目前他们的研究工作在国际上处于领先水平[]。
5应用方向
作为一种全新的制造技术,快速成型能够迅速将设计思想转化成新产品,一经问世便得到了广泛的应用,涉及的行业包括建筑、汽车、教育科研、医疗、航空、消费品、工业等。
近年来,FDM工艺发展极为迅速,目前已占全球RP总份额的30%左右[]。
FDM主要的应用可以归纳为以下两个方面:
(1)设计验证
现代产品的设计与制造大多是在基于CAD/CAM技术上的数控加工,显著提高了产品开发的效率与质量,但产品的CAD设计模型总是不能在CAM辅助制造之前尽善尽美。
利用快速成型技术进行产品模型制造是三维立体模型实现的最直接方式,它提高了设计速度和信息反馈速度,使设计者能及时对产品的设计思路、产品结构以及产品外观进行修正。
针对产品中重要的零部件,在进行量产前,为降低一定的生产风险,往往需要进行手板的验证,对于形状复杂,曲面众多的部件,传统手板加工方法往往很难加工,利用RP技术可以快速方便地制造出实体,缩短新产品设计周期,降低生产成本以及生产风险。
Mizuno是世界上最大的综合性体育用品制造公司。
1997年1月,Mizuno美国公司开发一套新的高尔夫球杆,这通常需要13个月的时间。
FDM的应用大大缩短了这个过程,设计出的新高尔夫球头用FDM制作后,可以迅速地得到反馈意见并进行修改,大大加快了造型阶段的设计验证,一旦设计定型,FDM最后制造出的ABS原型就可以作为加工基准在CNC机床上进行钢制母模的加工。
新的高尔夫球杆整个开发周期在7个月内就全部完成,缩短了40%的时间。
现在,FDM快速成型技术已成为Mizuno美国公司在产品开发过程中起决定性作用的组成部分。
(2)模具制造
RP技术在典型的铸造工艺(如失蜡铸造,直接模壳铸造)中为单件小批量铸造产品的制造带来了显著的经济效益。
在失蜡铸造中,快速成型技术为精密消失型的制作提供了更快速、精度更高、结构更复杂的保障,并且降低成本,缩短周期。
FDM在快速经济制模领域中可用间接法得到注塑模和铸造模。
首先用FDM制造母模,然后浇注硅橡胶、环氧树脂、聚氨酯等材料或低熔点合金材料,固化后取出母模即可得到软性的注塑模或低熔点合金铸造模。
这种模具的寿命通常只有数件至数百件。
如果利用母模或这种模具浇注(涂覆)石膏、陶瓷、金属构成硬模具,其寿命可达数千件。
用铸造石蜡为原料,可直接得到用于熔模铸造的母模。
6主要问题与发展方向
成型精度是快速成型技术中的关键问题,也是快速成型技术发展的一个瓶颈。
快速成型技术由数据处理、成型过程和后处理三部分组成,所以可以推断快速成型误差由原理性误差、成型过程产生的误差和后处理产生的误差组成。
目前快速成型技术领域存在以下主要问题[]:
(1)材料方面的问题,RP成型方法的核心是材料的堆积过程,材料的成型性能一般不太理想,大多数堆积过程伴随有材料的相变和温度的不稳定,残余应力难于消除,致使成型件不能满足需求,要借助于后处理才能达到产品要求。
(2)成型精度与速度方面的问题,RP在数据处理和工艺过程中实际上是对材料的单元化,由于分层厚度不可能无限小,这就使成型件本身具有台阶效应。
工艺要求对材料逐层处理,而在堆积过程中伴随有物理和化学的变化,使得实际成型效率偏低。
就目前快速成型技术而言,精度和速度是一对矛盾体,往往难以调和。
(3)软件问题,快速成型技术的软件问题比较严重,软件系统不仅是离散/堆积的重要环节,也是影响成型速度、精度等方面的重要影响因素。
如今的快速成型软件大多是随机安装,无法进行二次开发,各公司的成型软件没有统一标准的数据格式,且功能较少,数据转换模型STL文件缺陷较多,不能精确描述CAD模型,这都影响了快速成型的成型精度和质量。
因此发展数据格式统一并使用曲面切片、不等厚分层等准确描述模型的方法的软件成为当务之急。
(4)价格和应用问题,快速成型技术是集材料学科、计算机技术、自动化及数控技术于一体的高科技技术,研究开发成本较高;
工艺一旦成熟,必然有专利保护问题,这就给设备本身的生产和技术服务带来经济上的代价,并限制了技术交流,有碍RP技术的推广应用。
虽然快速成型技术已在许多领域都已获得了广泛应用,但大多是作为原型件进行新产品开发及功能测试等,如何生产出能直接使用的零件是快速成型技术面临的一个重要问题。
随着快速成型技术的进一步推广应用,直接零件制造是快速成型技术发展的必然趋势。
快速原型技术经过近20年的发展,正朝着实用化、工业化、产业化方向迈进。
其未来发展趋势归纳如下[,,]:
(l)开发新型材料。
材料是快速成型技术的关键,因此,开发全新的RP新材料如复合材料、纳米材料、非均质材料、活性生物材料,是当前国内外RP成型材料研究的热点。
(2)开发功能强大标准化的成型软件和经济稳定的快速成型系统,提高快速成型的成型精度和表面质量。
(3)金属/模具直接成型,即直接制造金属/模具并应用于生产中。
(4)大型模具制造和微型制造,熔融沉积快速成型精度及工艺研究。
(5)反求技术。
反求技术常用于仿制、维修和新产品开发,可大大缩短产品开发周期,降低成本,同时也是人体器官成型的核心与基础,在快速成型领域其已成为研究热点。
(6)低温成型及生物工程。
低温成型成本低,制件方便,属于绿色制造。
由于只有在低温下,生物材料和细胞才可能保持其生物活性,因此开发低温下的成形制造新技术,将生物材料或细胞或它们的复合体喷射成形,对生物制造具有决定性的意义。
(7)研究具有特定电、磁学性能的梯度功能材料及纳米晶材料。
(8)生长成型。
伴随着生物工程、活性材料、基因工程、信息科学的发展,信息制造过程与物理制造过程相结合的生长成型方式将会产生,制造与生长将是同一概念。
以全息生长元为基础的智能材料自主生长方式是即M的新里程碑。
(9)远程制造。
随着网络技术的发展,设计和制造人员可以通过各种桌面系统直接控制制造过程,实现设计和制造过程统一协调和无人化,实现异地操作与数据交换。
用户可以通过网络将产品的CAD数据传给制造商,制造商可以根据要求快速地为用户制造各种制品,从而实现远程制造。
参考文献