102机体齿飞面孔双卧多轴组合机床及CAD设计毕业设计Word格式.docx
《102机体齿飞面孔双卧多轴组合机床及CAD设计毕业设计Word格式.docx》由会员分享,可在线阅读,更多相关《102机体齿飞面孔双卧多轴组合机床及CAD设计毕业设计Word格式.docx(39页珍藏版)》请在冰豆网上搜索。
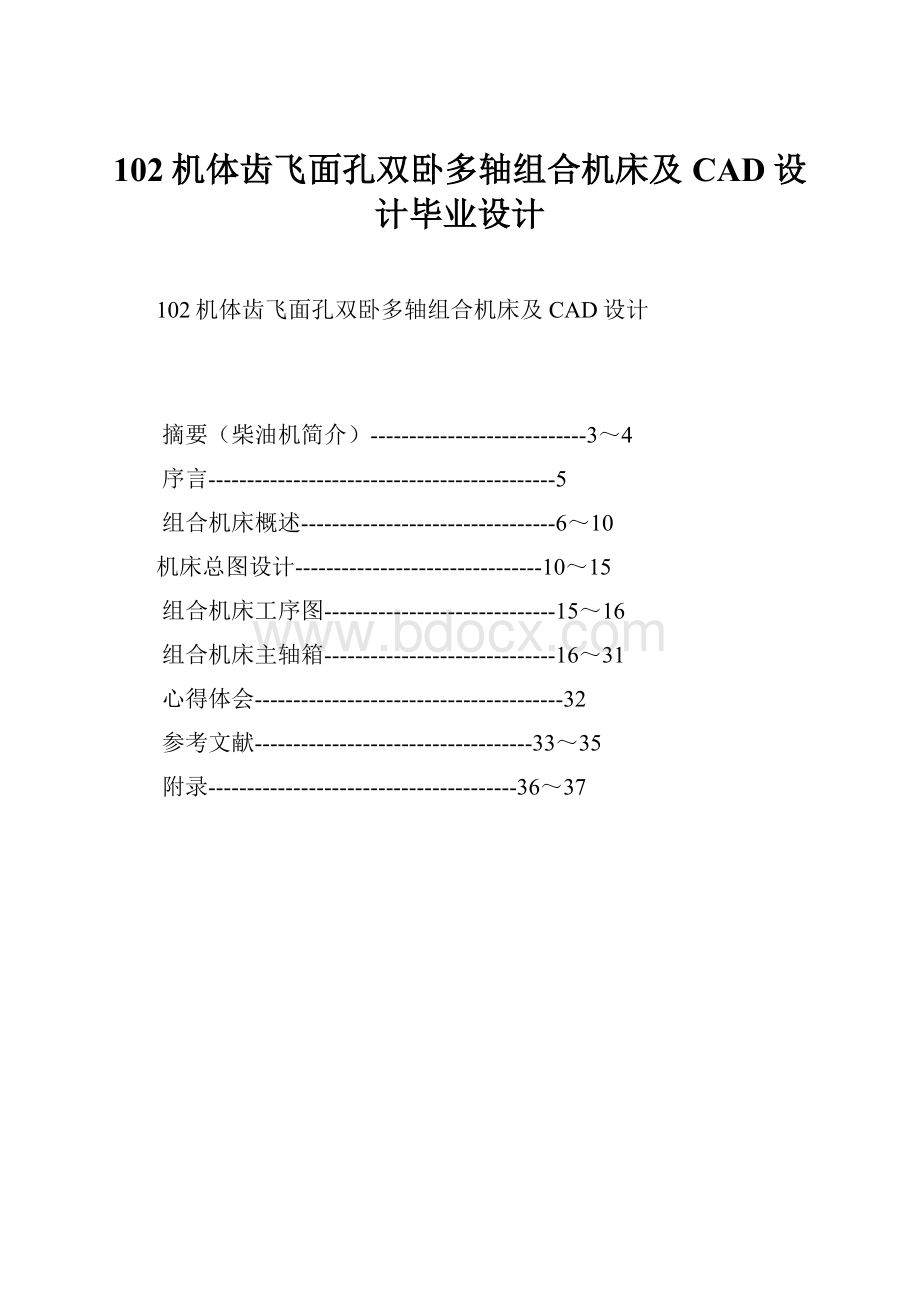
5-Ф12.5深30;
4-Ф6.7深20;
所有孔表面粗糙度12.5。
我在本次课题中承担的主要设计是:
1齿飞面双卧多轴组合机床总图(0号加长图纸)
2机体齿飞面工序图(1号图纸)
3齿飞面专机主轴箱飞面总图(0号图纸)
4齿飞面专机飞面前盖补充加工图(1号图纸)
序言
毕业设计的目的和意义:
毕业设计和毕业论文是我们学生完成学业的重要环节。
我们通过毕业论文的设计,综合性地运用几年内所学知识去分析、解决问题,在做毕业设计的过程中,所学知识得到梳理和运用,它既是一次对我们所学知识的检查,又是一次我们把所学知识运用到实践中的锻炼。
不少学生在做完毕业设计后,感到自己的实践动手、动笔能力得到锻炼,增强了即将跨入社会去竞争,去创造自信心的能力。
组合机床设计概述
组合机床是用按系列化标准设计的通用部件和被加工零件的形状及工艺要求设计的专用部件组成的专用机床。
一、设计特点:
组合机床上的通用部件和标准件约占全机床零部件总量的70%~80%。
因此在设计组合机床时,应首先根据被加工零件的工序图和加工示意图,正确地选择组合机床的通用零部件。
组合机床通用零部件包括:
侧底座、底座(中间底座和立柱底座)、立柱、动力箱、动力滑台、各种工艺切削头、移动工作台和回转工作台等。
这些通用零部件的绝大多数已有国家或行业标准,并按标准所规定的名义尺寸、形状和技术要求等,选用通用零部件,组成不同型式的组合机床,以满足生产需要。
其次根据被加工零件的工序图、加工示意图和联系尺寸图,设计组合机床非标准专用零部件、刀具、量具及辅具等。
最后将组合机床的联系尺寸图进一步完善为装配图。
由于组合机床的大部分零部件是按标准选用,只有少量专用零部件是自行设计,因而,可以大大减少设计工作量,提高设计效率,缩短制造周期,降低成本,并能确保机床工作的可靠性,从而,促进整个机械加工工艺水平的提高。
1、组合机床有重新改装的优越性,其通用零,部件可以多次重复利用。
2、组合机床是按具体加工对象专门设计的,因而可以按照最合理的工艺过程进行加工。
3、在组合机床上可以同时从几个方向采用多把刀具对几个工件进行加工,它是实现集中工序的最好途径,是提高生产效率的有效设备。
4、组合机床常常是用多轴对箱体零件一个面上的许多孔同时进行加工,这样就能比较好的保证各孔之间的精度要求,是提高产品质量;
减少了工序之间的搬运,改善劳动条件;
也减少了机床占地面积。
5、由于组合机床大多数零,部件是同类的通用部件,这就简化了机床的维护和修理,必要时可以更换整个部件,以提高机床的维修速度。
6、组合机床的通用部件可以组织专门工厂集中生产,这样可以采用专用高效设备进行加工,有利于提高通用部件的性能,降低制造成本。
二、设计方法和步骤
通用机床及通用机械设备的设计方法是理论分析计算和试验研究相结合的设计方法。
首先根据理论分析计算和局部实验确定机床的结构尺寸,制造样机,再对样机进行整机和局部薄弱环节的各种实验,最后补充修改定型。
组合机床是专用的机械加工设备,不存在先制造样机,再批量生产的问题。
因此组合机床的设计方法应当是:
根据类比及理论分析计算和局部实验,正确选择通用零件部件,确定专用零件部件的结构尺寸,设计出满足一定工艺要求的专用机床。
三、组合机床的通用部件
1、通用部件简介
⑴、通用部件的分类
①、动力部件
动力部件是通用部件中最基本的部件。
第一种动力部件是传递切削主运动的部件,包括动力箱和完成各种专能工艺的切削(单轴头),如铣削头、镗削头、钻削头、镗孔车端面头等。
第二种是传递进给运动的部件,包括有液压滑台和机械滑台。
第三种是转塔动力部件,包括工作台和单轴转塔头。
②、输送部件
输送部件主要用作夹具和工件的移动或转位。
例如:
多工位组合机床的移动工作台,回转工作台及回转鼓轮等。
③、支承部件
支承部件是组合机床的基础部件。
组合机床的其他部件都安装在支承部件上。
它包括中间底座、侧底座、立柱、立柱底座等。
组合机床各部件之间的相对位置精度、机床的刚度等主要靠支承部件保证。
④、控制部件
控制部件是控制组合机床按规定程序运动的一些部件,包括液压元件、电气挡板及操纵台等。
⑤、辅助部件
除上述部件以外的其他部件,例如:
冷却与润滑装置,气动或液压夹具装置和机械搬手等。
⑵、动力滑台及动力箱
滑台与滑座配套组成一个独立的动力部件——动力滑台。
滑台在滑座导轨上移动,实现机床的进给运动。
滑台上可以安装各种功用的单轴工艺切削头或安装动力箱和主轴箱。
此外,滑台还可以用作夹具和工件的输送部件。
滑台的主要参数规定为台面宽度尺寸。
组合机床各种通用部件的品种、规格及其配套关系也以滑台宽度尺寸为标准,其理由是:
①、直接反映在滑台上安装工艺切削头的能力,间接反映铣刀最大直径等。
在安装主轴箱时,可以反映出被加工零件加工位置的分布面积等。
②、滑台台面宽度是一个主要结合尺寸,结合面尺寸的标准化能使组合机床各部件外型协调。
③、滑台台面宽度作为通用部件配套标准,使机床受力合理,提高组合机床的刚度。
四、组合机床的支承部件
1、组合机床支承部件的作用与类型
支承部件主要用来安装其他工作部件。
因此,支承部件要求具有足够的刚性,以保证各部件之间能长期保持其正确的相对位置。
它是决定机床能否长期保持精度的重要条件之一。
组合机床床身采用组合方式,例如卧式床身系由滑座、侧底座及中间底座组合而成。
其优点是加工和装配工艺性好;
同时,安装、调试与运输也都比较方便。
其缺点是削弱了床身的刚性,这一弊病通常是用加强部件之间连接部件的刚度来补偿。
通用部件支承既可以用于配置卧式又可以用于配置立式机床,如果需要还可配置复合式机床。
2、组合机床卧式床身
机床床身可安装液压动力滑台及机械动力滑台。
滑座安装在侧底座上,侧底座与中间底座用螺丝钉及销子联结成一体。
滑座与侧底座之间有一个5毫米厚的调整垫。
采用调整垫对机床的制造和维修都方便。
因为当滑台导轨磨损后,或重新组装机床时,只须取下滑座将导轨面重新修刮,并更换(修磨)调整垫,使之恢复应有的高度即可。
而且滑座可以使用较好的材料(一般导轨面应用耐磨性较好的铸铁),而侧底座则可使用较次的材料。
侧底座的顶面除具有与滑座结合的平面外,周围有收集冷却液或润滑油的槽,用管子将油液引回储存箱中,侧底座的另一侧面有电气壁龛,以供安装电器元件用。
一般电器龛与冷却液储存箱不应靠近,以防电气元件潮湿。
为了便于支承元件的运输,应设有起吊孔或起吊螺丝孔。
五、组合机床的发展趋势
1、提高通用部件的水平
衡量通用部件技术水平的主要标准是:
品种齐全,动、静态性能参数先进,工艺性好,精度高和精度保持性好。
目前应注意开发适应强力铣削的大功率动力滑台,高精度镗削头和高精度滑台,以及适应中、小批生产的快调、速换动力部件和支承部件。
机械驱动的动力部件具有性能稳定,工作可靠等优点。
目前,机械驱动的动力部件应用了交流变频快调速电机和直流伺服电机等,使机械驱动的动力部件增添了新的竞争能力。
动力部件采用镶刚导轨(硬度可达HRC58~60)、滚动丝杠、静压导轨、静压主轴、齿形皮带等新结构。
支承部件采用焊接结构等。
由于提高了部件的精度和动、静态性能,因而使被加工的工件精度明显提高,表面粗糙度减小。
2、发展适应、小批生产的组合机床
在机械制造工业中,中、小批生产约占80%。
在某些中批生产的企业中,如机床、阀门行业等,其关键工序采用组合机床。
其中机床厂用组合机床加工主轴变速箱孔系,产品质量稳定,生产效率高,技术经济效果显著。
发展具有可调、快调、装配灵活、适应多品种加工特点的组合机床十分迫切。
转塔主轴箱式组合机床,可换主轴箱式组合机床以及自动换刀式数控组合机床可用于中、小批生产。
但这类机床结构复杂,成本较高。
带转塔式主轴箱的组合机床,由于转搭不能制造的太大,安装的主轴箱数量有限,因此只适应工序不多,形状不太复杂的零件。
本机床设计成卧式多轴组合机床,以适应中大批量生产加工的需要。
机床总图设计
一、机床联系尺寸图
机床联系尺寸图是决定各种部件的轮廓尺寸及相互间联系关系的,是开展各专用部件设计和确定机床最大占地面积的指导图纸。
组合机床是由一些通用部件和专用部件组成的。
为了使所设计的组合机床既能满足预期的性能要求,又能做到配置上匀称合理,符合多快好省的精神,必须对所设计的组合机床各个部件之间的关系进行全面的分析研究。
这是通过绘制机床联系尺寸图来达到的。
机床的总体联系尺寸图是在被加工零件工序图和加工示意图之后。
根据初步选定的通用部件(动力部件及其配套的滑座、床身等)以及确定的专用部件的结构原理绘制而成的。
可以检验机床各部件相对位置尺寸联系是否满足加工要求,通用部件的选用是否合适;
并进一步开展多轴箱夹具等转用部件的设计提供依据。
1、机床装料高度的确定:
在确定机床装料高度时,要考虑车间运送工件滚道高度、工件最低孔的位置、主轴箱最低主轴高度和通过部件高度尺寸的限制。
根据具体情况为便于操作和省力,在此本组合机床装料高度选择1060mm。
2、夹具轮廓的尺寸确定
夹具是用于定位和夹紧工件,工件的轮廓尺寸和形状是确定夹具尺寸的依据,在加工示意图中对工件和钻模板的距离,以及导套的尺寸,有了一定的规定。
所以确定夹具长度尺寸时主要在于合理的选择钻模板的高度。
对于高度不大钻模板其厚度可取150-200毫米。
当高度较高,为了保证足够的刚度和稳定性其厚度可取250-300毫米机床取270毫米。
在知道工件的长宽高尺寸、钻模板长宽高尺寸以及初极限和定位夹紧机构后确定夹具底座的总长尺寸。
为了补偿铸件的铸造误差,应比上述三项尺寸的总和稍大一些。
3、中间底座尺寸确定
在加工示意图中,已经确定了工件端面至主轴箱端面在加工的距离。
根据选的动力部件极其配套部件(滑座,床身等)的位置关系动力头的前备量等因素,就可以确定中间底座长度尺寸(L)
计算公式
式中L1─动力头的支承凸台尺寸
L3─是滑座前端面到床身端面的距离,它们却可以从动力部件的联系尺寸查得(见《组合机床通用部件图册》)
L2─动力头的支承凸台端面到滑座端面在加工完了时的距离,它由动力头支承凸台端面到滑座端面的最小尺寸(4和5号动力头滑台为50mm)和动力头的向前备量组成,并具有一定的调节范围(75~80mm)所以L=540mm
在确定中间底座高度尺寸时应考虑铁屑的贮存及排除,电气接线盒的安排,以及冷却液的贮存对于本机床(铸铁件的机床)为了使冷却液有足够的沉淀时间,容量取10-15分钟冷却棒的流量。
装料高度为1060mm时,床身和中间底座中间结合面的高度,无论那一型号的床身都是同意的,定为540mm。
所以中间底座的高度应为540mm。
当算出L值后,还必须检查是否合适,当机床无冷却液时,а=10~15mm,
有冷却液时,还考虑铁屑贮存及排除,对于本机床是加工铸铁的机床,为了使
冷却液有足够的沉淀空间,容量还应大一些,一般取10~15分钟及泵的流量。
4、主轴箱轮廓尺寸确定
标准主轴箱的厚度由箱体、前盖和后盖三层尺寸构成。
主轴箱体厚为180毫米。
前盖有两种尺寸,卧式厚为55毫米;
立式厚为70毫米。
后盖厚有90毫米和50毫米两种尺寸,通常采用90毫米的后盖。
因此,主轴箱总厚度卧式主轴箱通常为325毫米;
立式主轴箱通常为340毫米。
我主要设计的本专机飞面卧式主轴箱。
主轴箱及前、后盖均采用灰铸铁HT250。
下面设计主轴箱的宽度、高度和最低主轴高度。
主轴箱的宽度B和高度H可按下式来确定:
B=b2+2b1H=h1+h+h2
式中:
b1——最边缘主轴中心至主轴箱外壁的距离(mm);
b2——工件上要加工的在宽度方向上相隔最远的两孔距离;
h——工件上要加工的在高度方向上相隔最远的两孔距离;
h1——最低主轴中心至主轴箱底平面的距离,即最低主轴高度;
h2——最低边主轴中心至主轴箱外壁的距离。
b2和h是已知的尺寸,但如果确定了b1、h1和h2的尺寸,那同时主轴箱的宽度B和高度H就可以算出来了,随后根据标准箱宽×
高的标准尺寸系列,选用合适的尺寸B×
H。
主轴箱最低主轴高度h1,我们不能孤立地任意确定,必须考虑到它与工件最低孔的位置、机床配置型式、装料高度和动力部件、滑座、床身的关系,一般应大于85~120mm。
∴取h1为88mm
B=b2+2b1=530+2×
30=610mmH=h1+h+h2=184.5+88+258=503.5mm
根据上述计算结果,按主轴箱轮廓尺寸系列标准,同时为了保证主轴箱内有足够的安排传动齿轮,主轴箱的轮廓尺寸定为
B×
H=630×
630mm
所以可以确定主轴箱的宽度和高度=630×
5、最大行程的确定
动力部件的工作循环是指:
加工时动力部件从原始位置开始运动到加工终了位置又返回到原始位置的运动过程。
⑴、工作进给长度L1的确定
工作进给长度L1等于加工部位长度L(多轴加工时应按最长孔计算)与刀具切入L1和切出长度L2之和。
切入长度L1应根据工件端面的误差情况在5~10毫米内选择,误差大时选大值。
再采用一般简单刀具时,切出长度L2可见《非标准设备设计》P198表8.21推荐值选取。
钻:
LⅠ=L+L1+L2=30=5+(1/3)d+(3---8)=40
⑵、快速退回长度的确定
快速退回长度等于快速引进与工作长度之和。
快速引进是指动力部件把多轴箱连同刀具从原始位置快速送到工作进给开始位置,其长度按具体情况确定。
通常,在采用固定式夹具的钻扩、铰孔组合机床上、快速退回行程须保证所有刀具均退至夹具导套内而不影响工件装卸。
L快=LⅠ+L快=40+60=100毫米
①、动力部件总行程长度,除应保证要求的工作循环工作行程外,还要考虑装卸和调整刀具方便。
即考虑前、后备量。
前备量是指考虑刀具磨损或补偿制造,安装误差动力部件尚可向前调节的距离。
后备量是指考虑刀具从接杆中或接杆连同刀具一起从主轴孔中取出所需要的轴向距离。
即:
刀具能够退离夹具导套外端面的距离应大于接杆插入主轴孔内的长度。
因此,动力部件的总行程为快退行程长度与前、后备量之和。
依此作为选择标准动力滑台的依据。
结合上面的考虑取前备量L前=30mm,好备量L后=270mm
L总=L前+L快退+L后=30+100+270=400mm
二、主轴的计算
1、主轴箱齿面被加工孔的计算
a:
由加工示意图和加工工序图可知:
s=f=0.124mm/r
n=426.7r/min
每分钟进给量Vf=n·
f=426.7×
0.124=52.9108mm/min
V=n∏d/1000=(426.7×
3.14×
8.5)/1000=11.38m/min
MKP=10×
D1.9f0.8HB0.6=10×
8.51.9×
0.1240.8×
2400.6=2942.80(N·
mm)
Ne=MKPV/(9470·
∏·
D)=(2942.80×
11.38)/(9740×
8.5)=0.129(kw)
P=26Df0.8HB0.6=26×
8.5×
2400.6=1114.95(N)
b:
8—φ6.7深20s=f=0.16mm/rn=640r/min
f=640×
0.16=102.4mm/min
V=n∏d/1000=640×
6.7/1000=13.4643m/min
MKP=10×
2D1.9f0.8HB0.6=10×
6.71.9×
2400.6×
0.160.8=2295.96(N·
D)=2295.96×
13.4643/(9740×
6.7)=0.151(kw)
6.7×
0.160.8×
2400.6=1077.63(N)
齿面主轴箱所需要动力验算:
∑P=1114.95×
2+1077.63×
8=10850.94(N)
∑N=0.129×
2+0.151×
8=1.466(kw)
∑MKP=294.280×
2+229.596×
8=2425.328(N·
根据这个计算认为选择Y132S-4135
(2)N=5.5kwn=1440r/mm合适的.
2、飞面被加工孔的计算
已知5-φ12.5深30根据加工示意图和工序图可知:
n=460r/mins=f=0.1mm/r
f=460×
0.1=46(mm/min)
∴V=∏nd/1000=(3014×
460×
12.5)/1000=18.055m/min
∴MKP=10×
12.51.9×
0.10.8×
2400.6=5155.32(N·
Ne=MKPV/9470·
D=(5155.32×
18.055)/(9740×
12.5)=0.243(kw)
12.5×
0.10.8=1380.42(N)
已知:
钻4—φ6.7深20
根据加工示意图和工序图可知:
s=f=0.16mm/rn=640r/min
0.16=102.4(mm/min)
Ne=MV/9470·
D=2295.96×
13.4643/9740×
6.7=0.151(kw)
以上的计算公式见《毕业指导设计书》
二、液压动力滑台
1、液压滑台的结构
液压滑台是由滑台、滑座和油缸三部分组成。
油缸固定在滑座上,活塞杆则固定在滑台下面。
当压力油进入油缸的后腔或前腔时候,便可实现滑台沿滑座的导轨向前或向后移动。
控制滑台各种运动的液压系统装置,则可根据滑台动作程序另外配置。
液压滑台可实现典型的自动工作循环。
液压滑台既可用于配置卧式机床又可配置立式机床。
2、液压滑台的选择
根据以上的计算,在此选择4号动力头、以及与之相应的4号滑台和4号侧底座。
组合机床工序图
一、被加工零件工序图的作用及内容
被加工零件工序图是根据选定的工艺方案,表示组合机床完成的工艺内容、加工部位尺寸、精度、表面粗糙度及技术要求、加工用定位基准、夹紧部位及被加工零件的材料、硬度、重量和在本道工序加工前毛坯或半成品情况的图纸。
它不能用用户提供的产品图纸代替,而须在原零件图纸基础上,突出本机床或自动线的加工内容,加上必要的说明而绘制的,它是组合机床设计的主要依据,也是制造、使用、检验和调整机床的重要技术文件。
我设计的工序图上表示出:
1、被加工零件的形状和轮廓尺寸及与本机床设计有关的部位的结构形状及尺寸。
2、加工用定位基准、夹紧部位及夹紧方向。
以便以此进行夹具的定位支承(包括辅助定位支承)、限位、夹紧的设计。
3、本工序图加工部位的尺寸、精度、表面粗糙度、形状位置尺寸精度及技术要求,还包括本道工序对前道工序提出的要求(主要指定位基准)。
4、必要的文字说明。
如被加工零件编号、名称、材料、硬度、重量及加工部位的余量等均在图上均表示出来了。
本工序图保证的尺寸、角度等,均用了方框表示出来。
组合机床主轴箱
一、主轴箱的概念及其作用
主轴箱是组合机床的重要组成部分。
它是选用通用零件,按专用要求进行设计的,在组合机床设计过程过中,是工作量较大的部件之一。
主轴箱是组合机床的主要部件之一。
其主要作用是,根据被设计零件的加工要求,安排好各主轴的位置,并将动力和运动由电机或动力部件传给各工作主轴,使之得到要求的转速和转向。
主轴箱用于布置(按所要求的坐标位置)机床工作主轴及其传动零件和相应的附加机构的。
它通过按一定速比排布传动齿轮,把动力从动力部件——电动机、动力箱、主轴箱等传递给各工作主轴,使之获得所要求的转速和转向等。
二、主轴箱的分类
主轴箱按其结构大小,可分为大型主轴箱和小型主轴箱两大类。
大型又分为通用(亦称标准)主轴箱和专用主轴箱两种。
专用主轴箱根据加工零件特点,及其加工工艺要求进行设计,由大量的专用零件组成。
其结构与设计方法与通用机床类似。
三、确定主轴箱设计的原始依据图
主轴箱设计的原始依据图,要包括下述的全部或部分内容:
1、所有主轴的位置关系及尺寸;
2、要求的主轴转速和转向;
3、主轴的工序内容和主轴外伸部分尺寸;
4、主轴箱的外形尺寸以及与其他相关部件的联系尺寸;
5、动力部件;
6、工艺上的要求;
7、其他要求;
四、齿飞面专机飞面主轴箱设计
1、主轴结构型式选择、直径及动力计算
⑴、确定主轴型式
主轴的型式和直径,主要取决于刀具的进给抗力和切削扭矩或主轴结构上的需要.通常,钻孔时采用前支承有止推轴承的主轴;
钻孔以外的其他工序,主轴前支承有没有止推轴承都可以,这要视具体情况而定。
设计时,尽可能不选用15毫米直径的主轴和滚针主轴,因为这种主轴的精度低,既不利于制造装配,也不便于使用和维修。
⑵、主轴直径和齿轮模数的初步确定
①、主轴直径的确定(飞面)
主轴直径按加工示意图所示主轴类型、及外审尺寸初步确定。
主轴直径通常根据扭距的计算,采用经验公式d=B(MKP/100)1/4,式中MKP扭距(N·
mm),B为刚性系数,刚性主轴取〔Ψ〕=1度时,取5.2具体见附录
A:
n=460r/min