丰田精益管理模式的成功密码.ppt
《丰田精益管理模式的成功密码.ppt》由会员分享,可在线阅读,更多相关《丰田精益管理模式的成功密码.ppt(99页珍藏版)》请在冰豆网上搜索。
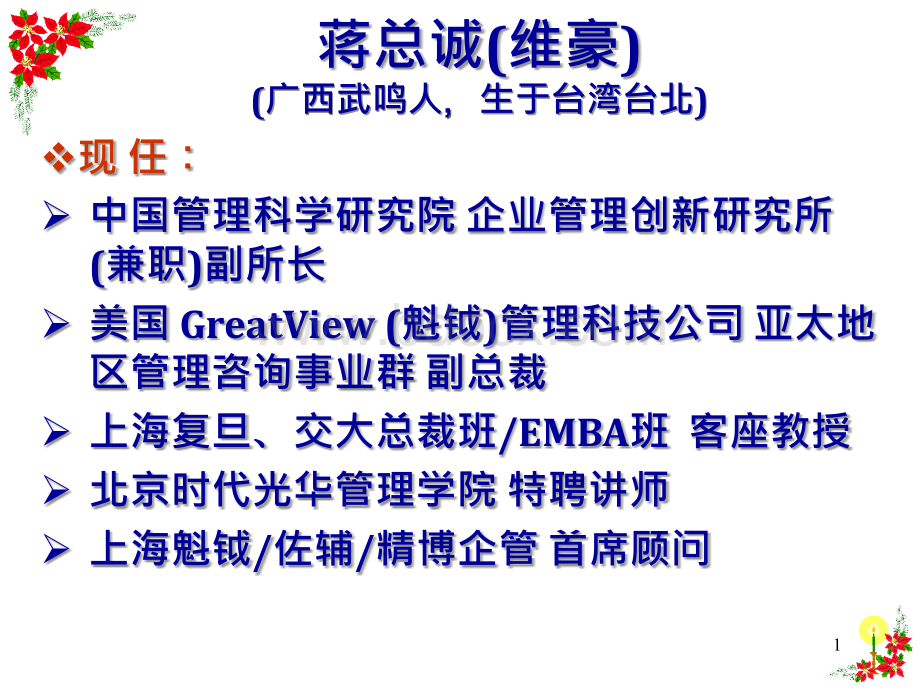
1蒋总诚(维豪)(广西武鸣人广西武鸣人,生于台湾台北生于台湾台北)中国管理科学研究院企业管理创新研究所(兼职)副所长美国GreatView(魁钺)管理科技公司亚太地区管理咨询事业群副总裁上海复旦、交大总裁班/EMBA班客座教授北京时代光华管理学院特聘讲师上海魁钺/佐辅/精博企管首席顾问v现任:
2蒋总诚(维豪)(台湾)丰年公司果糖事业部部长(台湾)太尊企管顾问公司总经理(台湾)奇盟化工公司总经理(台湾)奇孚压克力制品公司总经理v学历:
(台湾)文化大学多国籍企业管理研究所(台湾)中原大学化学工程学系v经历:
3蒋总诚(维豪)东芝电脑、SONY索广映像、日立空调、ABB电机、ABB自动化、FESTO自动化组件、上海福兴工业、英业达集团、万向集团、Adidas服饰、杭州秋水伊人、太原钢铁、上海汇众汽车、上海通用汽车v项目专长:
策略规划(BSP)、方针展开(POD)、流程再造(BPM)、精益生产(TPS)、ERP实施监理。
v项目经验:
4主讲人主讲人:
蒋维豪蒋维豪破译破译破译破译丰田精益化管理模式丰田精益化管理模式丰田精益化管理模式丰田精益化管理模式的成功密码的成功密码的成功密码的成功密码(精益思想精益思想精益思想精益思想的的的的因果逻辑论因果逻辑论因果逻辑论因果逻辑论)本教材的智慧财产权属于蒋维豪所有本教材的智慧财产权属于蒋维豪所有破译丰田密码破译丰田密码克隆精益基因克隆精益基因成本减半成本减半利润倍增利润倍增不是梦不是梦!
5生产运营管理是一个有效的生产运作系统整合为PQCDSM运营目标以实现的一系列活动和过程。
把人力设备物料章法(资源)信息改进控制策划驱动评价6产量/Productivity质量/Quality成本/Cost速度/Delivery弹性/Flexibility安全/Safety士氣/Morale产量质量速度成本产量质量生产运营管理必须兼顾的目标覆盖面愈放愈大产量7在多重目标间顾此失彼的情况下,所衍生出来的问题愈来愈复杂,也愈来愈可怕8为了兼顾多重目标的同步实现,手段必须快速调整和变化手段战略/方针管理产品选择/设计资源配置管理厂房/设备布局制程设计工作设计供应链管理生产计划管理质量管理成本控制环安卫管理目的高效实现:
产量/品质/成本/需求响应速度/安全/环保等等的顾客期望要求执行与控制结果产量(P)质量(Q)成本(C)交期(D)弹性(F)安全(S)士气(M)分析与改进9所以:
管理者面对手段的精炼与快速变革压力也愈来愈大焦头烂额之后,不禁让人怀疑:
到底存不存在能够兼顾多重目标同时实现的方法?
10同样的问题,存在各种不同的解决方法!
不同的方法,当然必须付出不同的代价!
11精益(Lean)生产系统=丰田生产系统丰田汽车是当今世上最赚钱的汽车厂(2005年净赚100亿美金)丰田公司赚钱的绝活是:
排除浪费!
寻找最有效、最便宜的管理方法,要向丰田公司学习!
寻找最便宜的管理方法要向丰田公司学习12丰田之屋:
精益生产的核心架构自自自自働働働働化化化化使问题易于浮现,使问题易于浮现,出现出现问题自动问题自动停止生产停止生产安灯安灯(Andon)人机分离人机分离防止错误防止错误就地品管就地品管解决问题的根本原因解决问题的根本原因即时生产即时生产即时生产即时生产(JIT)(JIT)在正确时间里生产正在正确时间里生产正确数量的正确产品确数量的正确产品花时间花时间提前作提前作规划规划连续畅流式流水线连续畅流式流水线后拉式后拉式Kanban系统系统快速切换快速切换后勤整合后勤整合丰田模式的长期理念丰田模式的长期理念5S及目及目视化管理视化管理稳定且标准化的流程稳定且标准化的流程平衡化平衡化/平准化生产平准化生产员工与团队员工与团队挑选挑选人才人才目标目标共有共有廪议决策廪议决策交叉训练交叉训练持续改善持续改善持续改善持续改善减少浪费减少浪费关注浪费关注浪费现地现物现地现物解决问题解决问题五个五个Why透过杜绝透过杜绝一切一切浪费以精简生产流程,达成下列目标:
浪费以精简生产流程,达成下列目标:
最佳品质、最低成本、最短前置期、最佳安全性、最高员工士气最佳品质、最低成本、最短前置期、最佳安全性、最高员工士气(P、Q、C、D、S、M)131.等待的浪费2.库存的浪费3.搬运的浪费4.制造不良品的浪费5.加工作业的浪费6.动作的浪费7.制造过多(过早)的浪费尽一切可能,排除一切浪费!
8.14破译丰田密码克隆精益基因破译丰田精益化管理模式的成功密码主讲人主讲人:
蒋维豪蒋维豪精益系列课程之一第二讲:
第二讲:
第二讲:
第二讲:
浅说浅说浅说浅说八八八八大浪费大浪费大浪费大浪费15库存的浪费v零部件、原材辅料、在制品、半成品、成品的库存是所有浪费的首恶,因为:
过度的库存会严重积压流动资金;产生不必要的入库、出库、登帐、盘点、防护、寻找、搬运等管理成本浪费;不必要的库房空间、料架、堆高机、自动搬运系统等投资浪费;使用时的重新整理,价值衰减,或因订单或设计变更而变成呆料废料;库存拥有成本:
15%25%.16为什么需要/会有这么多的库存?
需求实现周期长供方所要求的移交批量大害怕人算不如天算的事情(停工待料、设备故障、批量返工、脱销断货)会发生,所以多准备一点余量/缓冲/安全库存去化速度太慢/不稳定/不确定人算不如天算(预测/计划失误、订单取消、货品滞销),所以留下这些库存17面对库存的典型传统思维小媳妇思维面对/妥协/迁就/承受按现状做好库存管理周期时间太长:
提前采购/投产更早准备更多库存恶性循环移动批量太大:
批量经济/自我安慰;增加储存空间/提高搬运效率自动仓储系统干扰变数太多:
采取应变措施陷入救火漩涡;快速变更计划MRP需求波动无常:
需求臆测/增加缓冲/风险转嫁;卖不出去折价抛售/认赔了事18订单变更订单变更质量质量不良不良物料未到物料未到设备故障设备故障库存水平技能不足技能不足人手人手不够不够堆积的库存最容易掩盖管理问题、隐藏管理失误,是改革的最大障碍。
强迫降低库存,让管理问题水落石出!
丰田面对库存的精益思维19精益模式面对库存的对策缩短周期:
ECRS/JIT/后拉式KB系统降低批量:
单件流/快速切换/混合装载控制变量:
源流管理/事前管理持续改进;计划简化/精准化/冻结概念强化设计:
产品企划、设计与市场验证需求明晰化提高产品的市场命中率调节波动:
信息采集自动化/需求预测合理化(摆脱牛鞭效应)/订单需求平准化:
20企业各种资源彼此等来等去,就是一种浪费!
企业资源包括:
资金、厂房空间、机器设备、原材辅料、人员、信息这就是等待的浪费!
21等待产生的原因F淡旺季变化淡旺季变化淡季资源闲置淡季资源闲置F接接单不力不力订单不足不足资源源闲置置F被动接单被动接单单量波动大,来单时间不一定单量波动大,来单时间不一定排程困难排程困难忙闲不均忙闲不均F订单排程不良订单排程不良排程像蛇吞蛋排程像蛇吞蛋忙闲不均忙闲不均F外部干扰外部干扰+内部失调内部失调干扰计划排程干扰计划排程+计划计划逻辑不当逻辑不当变来变去变来变去等来等去等来等去F离岛式的车间布局离岛式的车间布局搬来搬去搬来搬去等来等去等来等去F现场管理不当现场管理不当生产线不安定生产线不安定等来等去等来等去F流线设计不当流线设计不当生产线不平衡生产线不平衡等来等去等来等去22搬运的浪费物品的取放、堆积、排列、移动、整列等等搬运的动作都是不能产生价值的动作;搬运的动作会直接造成时间、空间、容器、载具、输送带、人力等等,以及间接造成库存、管理上的浪费;更糟糕的是:
搬运过程经常发生物品的损伤,也会产生许多质量性连锁浪费。
搬运产生的原因:
离岛式车间、离散式工序、多余库存、返工重做、计划变更优先考虑如何免除搬运?
非搬不可时,才去考虑如何搬运才有效率?
23制造不良品的浪费当不良品产生时:
原材辅料、人工、设备、能源、管理费用白白浪费;返工修补时:
额外的修复、选别、检验等成本还要再花一次;或者:
报废;若订单交期可能因此而延误,则所采取的:
紧急换线、紧急调货、加班、海运变空运等等的救火成本;假如不良品未被发现而继续向后流出24产生更可怕的一人错误百人忙的连锁效应日常管销/制造成本救火、防火、多余监督、过度控制、多余检验、投诉处理、退货维修、商誉损失、顾客流失等效应连锁扩大成本!
重工、返修、报废成本正常成本更多的返工成本更多的救火成本更多的防火成本一人错误百人忙的成本暴增曲线1:
30:
600:
900025制造过多/过早的浪费?
丰田的痛苦经验:
1948年的大争议事件大争议事件坚定了及时生产的信念JIT(Justintime)及时生产观念就是:
只有在顾客需要的时候,才生产顾客所需质量和数量的产品!
正确的时间(顾客需要的)、正确的数量(顾客需要的)、正确的产品(顾客需要的)!
违反这个原则就会产生:
多余的库存、多余的搬运、多余的等待等等各种浪费!
26多余加工作业的浪费v加工的浪费主要是指在设计开发阶段就已被内建进去的不必要加工作业而言;v例如:
零件部件数量设计过多(增加管理环节、增加工序)、规格公差要求过度(加严检查、增加工序)、余量放置过多(切掉、铣掉)、技术交代不足(挖孔:
定寸、划线)等原因所造成的各种浪费性加工作业;v加工浪费是七大浪费中较难观察发现的一种,因为它看似必要却又实无必要,除非具备向设计/技术部门追溯和衔接的能力,否则是察觉不出来的。
27动作的浪费不产生价值的、违反动作经济原则的、有方法可以免除的动作就是浪费动作!
执行生产作业时,诸如:
拆箱、拆包、取放、换手、反转、对准、弯腰、转身等等都是比较容易被发现的无价值动作;不产生价值的动作都会造成人力、体力、设备效率、时间等浪费;排除动作浪费可以降低劳动强度、提高士气、缩短交期、降低成本、创造效益。
28所有这些浪费都是来自于:
忽视员工智慧潜能的浪费!
许多管理者可能是碍于自己的管理能力、或者只是为了贪图管理上的方便,他们通常只会要求员工的顺从、只在乎员工的劳动力,往往忽略了员工的智慧;所以有人说:
管理上的七大浪费,追根究底就是来自于管理者无视于或不懂得运用员工的智慧和潜能以改善这些浪费;这就是第八大浪费!
也是最严重、最无知的浪费!
29八大浪费结构图本身多余、及作业内产生的搬运、行走、等待、在手量、储存量、产生不良多余动作多余动作加工作业加工作业本身多余、及作业内产生的搬运、行走、等待、在手量、储存量、产生不良多余动作多余动作加工作业加工作业等待等待等待等待搬运搬运搬运搬运储存储存储存储存不良不良不良不良等待等待等待等待搬运搬运搬运搬运储存储存储存储存不良不良不良不良等待等待等待等待搬运搬运搬运搬运储存储存储存储存不良不良不良不良采购采购/制造:
过多制造:
过多/过早过早激活人员的动力和潜能激活人员的动力和潜能提案提案/小集团改善活动小集团改善活动30丰田成功密码
(一):
离岛式车间集结式流水线流线化1234561011131819打破现制打破现制打破现制打破现制,重新串联成集结式流水线重新串联成集结式流水线重新串联成集结式流水线重新串联成集结式流水线1247368591310111215141620171918投投单单生生产产产产品品交交付付(A车间)(B车间)(C车间)(D车间)31丰田成功密码
(二):
降低移动批量单件流动化转换成转换成转换成转换成(中转库存中转库存400个,成品库存个,成品库存100个个)裁剪裁剪冲压冲压加工加工抛光抛光1分钟分钟1分钟分钟1分钟分钟1分钟分钟+100分钟分钟=104分钟分钟100(周期时间缩短成周期时间缩短成104分钟,中转库存分钟,中转库存4个,成品库存个,成品库存100个个)裁裁剪剪100冲冲压压0100加加工工0100抛抛光光0100100分钟分钟100分钟分钟100分钟分钟100分钟分钟+=400分钟分钟100(单件流)09-1209-1232工序集结后的现场照片33单件流动生产方式3435.服裝行業培訓專題服裝行業培訓專題服裝行業培訓專題服裝行業培訓專題服裝製造業精益生服裝製造業精益生服裝製造業精益生服裝製造業精益生產管理產管理產管理產管理服裝行業精益生產培訓教材服裝