所有钢材常见缺陷及原因Word下载.docx
《所有钢材常见缺陷及原因Word下载.docx》由会员分享,可在线阅读,更多相关《所有钢材常见缺陷及原因Word下载.docx(12页珍藏版)》请在冰豆网上搜索。
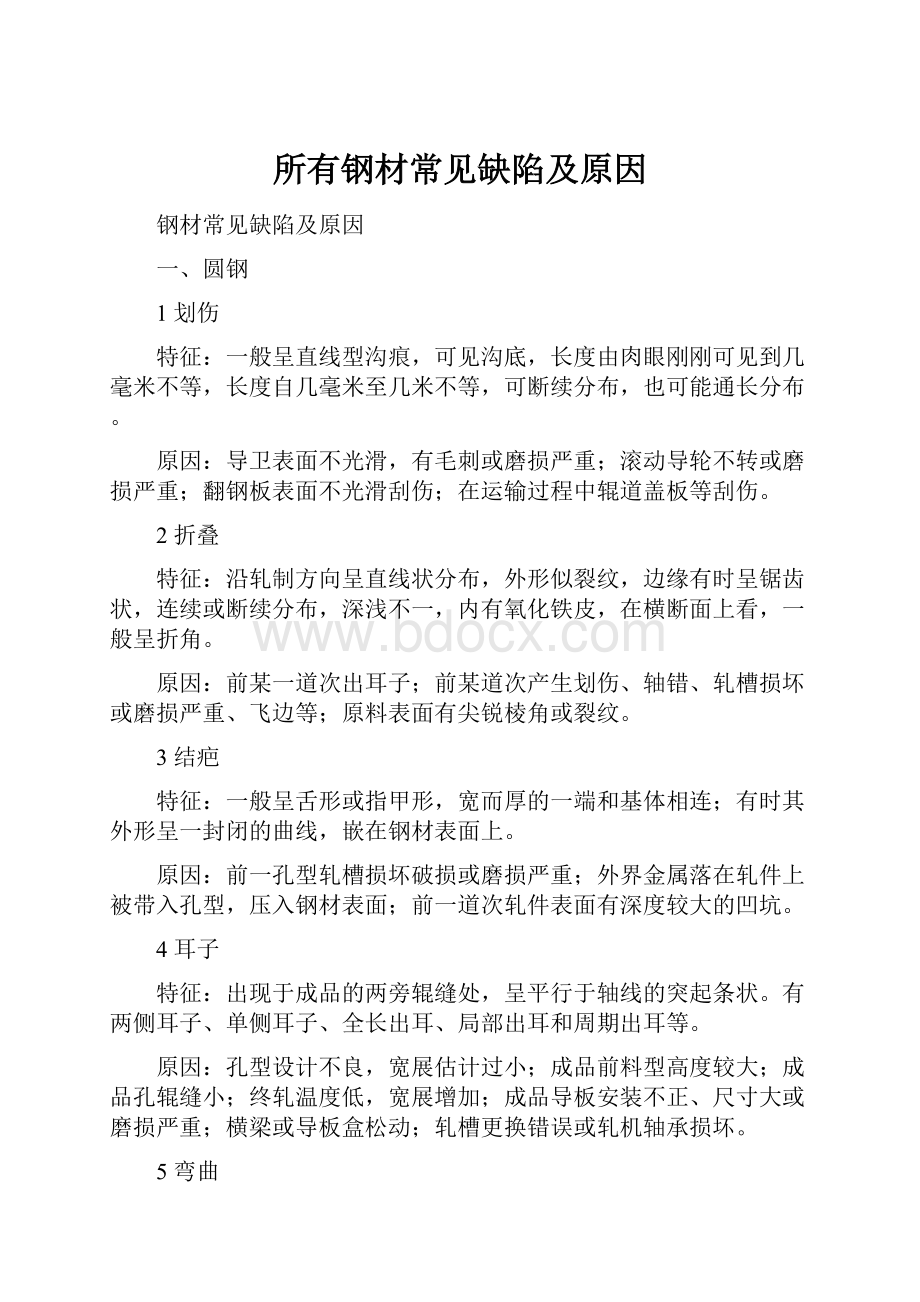
轧槽更换错误或轧机轴承损坏。
5弯曲
有头部弯曲、局部弯曲、全长弯曲等。
出口导卫安装过高或过低;
温度不均;
上下辊径差过大;
冷床不平,成品在冷床上排列不齐,移动速度不一致,翻钢设备不良;
冷却水分布不均匀,成品冷却不均;
精整操作不良。
6翘皮
呈鱼鳞状或分层翘起的薄皮,大部分是生根的,也有不生根的。
导卫装置加工或安装不良,围盘有尖锐棱角,刮伤了轧件表面,再轧后,引起翘皮;
输送辊道表面粗糙,刮起伤了轧件表面,再轧后造成翘皮;
轧件带有薄耳子;
轧槽磨损严重,轧件在孔型内打滑;
连铸坯内部有较大的皮下气泡,轧后破裂形成翘皮。
7表面夹杂
一般呈点状、条状或块状分布,其颜色有暗红、暗黄、灰白等,机械地粘结在成品表面上,不易剥落,且有一定的深度。
连铸坯表面带有非金属夹杂物;
在加热过程中,炉内耐火砖、煤灰、煤渣等杂物粘附在原材料表面上,轧制时未能剥落;
在轧制过程中,非金属夹杂物被带入孔型,被压入金属表面。
8裂纹
裂纹在钢材表面上,一般呈直线状,有的呈Y形,其方向多与轧制向一致,但也有横向或其他方向的。
加热不均,轧制时各部分延伸不一致;
轧制时,钢温过低,塑性变差;
高碳钢和合金钢材冷却不当;
连铸坯表面有裂缝未清除;
连铸坯内有缩孔、夹杂、皮下气泡、柱状晶间裂缝。
9过烧
在钢材表面上形成横向开裂,或呈龟裂状,裂口呈现肉眼可见的粗糙粒状组织,金相组织表现为晶界被氧化。
钢坯加热温度过高或在高温区停留时间过长;
钢中硫、铜等杂质含量过高,在钢中形成低熔点合金,使钢在加热时产生晶界融化,轧制时形成裂纹。
10麻面(麻点)
钢材表面有成片的凹凸不平的粗糙面,局部的、连续的或周期性的出现在钢材表面上。
轧辊冷却不良,钢温过低,造成孔型严重磨损,或轧槽粘有氧化铁皮;
轧辊材质不良,硬度不均匀或硬度过低,使轧槽很快磨损;
轧槽使用时间过长,磨损严重;
除鳞不良,氧化铁皮被压入轧件表面,以后脱落形成麻面。
11凹坑
成片孔型有凸块或粘附氧化铁皮,特别是冷却水中断时,引起孔型发热,更易粘附氧化铁皮,当轧件通过后,在轧件表面形成周期性的凹坑;
成品孔前某孔型嵌入氧化铁皮造成的凹坑,在轧件进入下几道孔型时得不到加工或加工不够,凹坑仍遗留在钢材表面上;
轧制时落入的硬质金属物压入轧件表面,剥落后形成凹坑;
冷却回炉再度加热,易造成过厚的氧化铁皮,轧制时压入钢材表面,冷却后脱落造成凹坑。
12缩孔
钢材断面有分层或孔洞,有时某部位呈现鼓形。
连铸坯的缩孔深度超过规定的数值,或钢坯的残余缩孔未完全切除。
13辊印
钢材表面呈连续性或周期性的凸起或凹下的印痕。
周期性的凸起印痕又叫凸块,连续性的印痕又叫轧痕。
成品孔或成品前孔磨损严重,孔型内有砂眼,或辊环崩缺;
轧辊加工不良,留有刀痕,或轧槽表面粘有氧化铁皮。
14碳化物网状级别高
轧制碳含量较高的碳素体工具钢、合金工具钢、铬轴承钢时,其显微组织的碳化物网状级别超过国家标准。
终轧温度过高,适当降低终轧温度;
轧后冷却速度太慢;
轧后热处理不当。
15脱碳
轧制含碳量大于0.4%的钢时,由于钢坯原始脱碳层深度过大,加热温度过高或在高温区停留时间过长,会产生脱碳过多现象,使钢材表面脱碳层深度超过允许标准。
钢材表面脱碳将大大降低表面硬度和耐磨性。
16脆断
成品在冷状态矫直过程中,产生的直线或折线形裂缝,其裂缝内无氧化铁皮。
严重时,钢材产生脆裂,
矫直压力过大,或矫直次数过多,钢材产生加工硬化,造成机械性脆断;
钢中磷含量较高,冷脆性增加,矫直时易脆断;
矫直温度不当。
17力学性能
常有屈服强度、抗拉强度、延伸率、冲击功、硬度、淬透性等力学性能达不到国标标准。
成分不合、成分偏析、冷却方式、加热制度等。
二、型钢
1结巴
型钢表面上的疤状金属薄块。
其大小、深浅不等,外形极不规则,常呈指甲状、鱼鳞状、块状、舌头状无规律地分布在钢材表面上,结疤下常有非金属夹杂物。
由于钢坯未清理,使原有的结疤轧后仍残留在钢材表面上。
2表面夹杂
暴露在钢材表面上的非金属物质称为表面夹杂,一般呈点状、块状和条状分布,其颜色有暗红、淡黄、灰白等,机械的粘结在型钢表面上,夹杂脱落后出现一定深度的凹坑,其大小、形状无一定规律。
钢坯带来的表面非金属夹杂物;
在加热或轧制过程中,偶然有非金属夹杂韧(如加热炉的耐火材料及炉渣等),炉附在钢坯表面上,轧制时被压入钢材,冷却经矫直后部分脱落。
3分层
此缺陷在型钢的锯切断面上呈黑线或黑带状,严重的分离成两层或多层,分层处伴随有夹杂物。
钢坯的皮下气泡,严重疏松,在轧制时未焊合,严重的夹杂物也会造成分层;
钢坯的化学成份偏析严重,当轧制较薄规格时,也可能形成分层。
4气泡
型钢表面呈现的一种无规律分布的圆形凸起称为凸包,凸起部分的外缘比较圆滑,凸包破裂后成鸡爪形裂口或舌形结疤,叫气泡。
多产生于型钢的角部及腿尖。
钢坯有皮下气泡,轧制时未焊合。
5裂纹
顺轧制方向出现在型钢表面上的线形开裂,一般呈直线形,有时呈“Y”形,多为通长出现,有时局部出现。
钢坯有裂缝或皮下气泡、非金属夹杂物,经轧制破裂暴露;
加热温度不均匀,温度过低,轧件在轧制时各部延伸与宽展不一致;
加热速度过快、炉尾温度过高或轧制后冷却不当,易形成裂纹,此种情况多发生在高碳钢和低合金钢上。
6尺寸超差
尺寸超差是指型钢截面几何尺寸不符标准规定要求的统称。
这类缺陷名目繁多,大部以产生部位以及其超差程度加以命名。
例工、槽、角钢的腿长、腿短、腰厚、腰薄及一腿长,一腿短。
对工字钢成品孔腿长往往表现在开口腿上,主要由于腰部压下量不够,角钢和槽钢成品孔压下量的大小,直接影响腿长和腿短;
切深孔切人太深,造成腿长无法消除;
轧辊不水平或有轴向串动,咬入不正,成品孔夹板上偏等都会造成一腿长,一腿短等;
腰的厚、薄主要是成品孔及成品前孔压下量不合理所造成。
7划伤
一般呈直线或弧形的沟槽,其深度不等,通长可见沟底,长度自几毫米到几米,连续或断续地分布于钢材的局部或全长,多为单条,有时出现多条。
导卫板安装不当,对轧件压力过大,将轧件表面划伤;
导卫板加工不良,口边不圆滑,或磨损严重,粘有氧化铁皮,将轧件表面划伤;
孔型侧壁磨损严重,当轧件接触时产生弧形划伤;
钢材在运输过程中与表面粗糙的辊道、盖板、移钢机、活动挡板等接触划伤。
8缺肉
型钢其一侧面沿轧制方向全长或周期性的缺少金属称缺肉,缺陷处没有成品孔轧槽的热轧印迹,色暗、表面较粗糙。
孔型设计不良,轧辊车削不正确及轧机调整不当,使轧件进入成品孔时由于金属量不足,造成孔型充填不满;
轧槽错牙或入口导板安装不当,造成轧件某一面缺少金属,再轧时孔型充填不满;
前、后孔磨损程度不一样;
轧件弯、扭造成进孔不正;
对于工、槽钢,钢坯不清理,往往出现结疤掉到闭口腿内,在轧制过程中便会出现周期性的腿尖缺肉。
9耳子
在型钢表面上与L型开口处相对应的地方,出现顺轧制方向延伸的凸起部分称为耳子。
有单边的,也有双边的,有时耳子产生在型钢的全长,也有局部或断续的,方、圆钢产生较多。
轧机调整不当或孔型磨损严重,使成品前孔来料过大或成品孔压下量过大,产生过充满,多产生双边耳子;
进入成品孔前因事故造成温度过低,进入成品孔时延伸降低,宽展过大,多产生双边耳子;
成品孔入口夹板向孔型一侧偏或松动。
金属挤人孔型一侧辊缝里,产生单面耳子;
成品入口夹板间隙过大或松动,进钢不稳,易产生双面断续耳子。
10扭转
型钢绕其轴线扭成螺旋状称为扭转。
卫板安装不良,使轧件出孔时受到力偶的作用产生扭转;
两侧延伸不一致,主要是压下不均或辊子有轴向串动;
方、圆钢由于入口夹板安装不正确,使钢料进孔不正,造成延伸不一致;
轧辊安装不正确,上、下轧辊轴线不在同一垂直平面内,即上、下辊成水平投影交叉,使轧件扭转;
矫直机调整不当。
11弯曲
型钢沿垂直或水平方向呈现不平直的现象称为弯曲,一般为镰刀形或波浪形,仅只头部的弯曲叫弯头。
轧机调整不当,轧辊倾斜或跳动,上、下辊径差大,造成速度差大;
出口卫板安装不正确,卫板梁过低或过高;
轧件温度不均匀,使金属延伸不一致;
冷床拉钢车不同步或滑轨不光滑;
运输辊道速度过快,容易把钢材头部撞弯;
矫直温度过高,冷却后容易产生弯曲;
成品捆扎长短不齐较大。
在运输中装卸不当;
堆垛时不按规定进行;
锯片用的太老,也容易产生弯头。
12形状不正
型钢断面几何形状歪斜不正,这类缺陷对不同品种各异,名称繁多。
如工槽钢的内并外斜,弯腰挠度,角钢顶角大、小腿不平等。
矫直辊孔型设计不合理;
矫直机调整操作不当;
矫直辊磨损严重;
轧辊磨损或成品孔出口卫板安装不良。
三、宽厚板
1裂纹
钢板表面呈现的形状不同,深浅不等,方向任意的裂口称为裂缝(裂纹)。
板坯上的纵裂缝清理不净或漏清理,经轧制残留在钢板上。
2氧化铁皮压入
钢板表面压入的氧化铁皮,呈灰黑色或红棕色,分布面积有大有小,有呈块状,也有呈条状或点状的.其压入深度有深有浅。
(1)氧化铁皮的压入生成取决于加热条件,加热时间愈长,加热温度愈高,氧化性气氛愈强,生成氧化铁皮就愈多,而且不容易脱落;
高压水压力不足、高压水嘴堵塞、立辊侧压小、轧制去鳞不尽;
含合金元素Ni含量较高。
3厚薄不均
钢板各部分厚度不一致称厚薄不均,局部钢板厚度超过规定的允许偏差。
辊缝的调整和辊型的配置不当;
轧辊和轧辊两侧轴瓦磨损不一样;
板坯加热温度不均。
4折叠
钢板表面有局部互相折合的双层金属称折叠。
其外形与裂纹相似,深浅不一,在横截面上一般呈现锐角,多在钢板的边部或角部出现。
轧件刮伤,轧制时产生折叠,多出现在钢板的下表面;
立辊挤压过大,辊环啃伤轧件下表面;
加热炉滑道磨损,推钢时使板坯下表面产生划伤;
钢坯表面存在凸台,横轧时产生压折。
5麻点
钢板表面呈现局部或连续的凹坑叫麻点,其大小不同,深度不等。
加热过程中,板坯氧化严重,轧制时铁皮压人表面,脱落后形成细小的口坑。
6瓢曲
钢板在纵横方向同时出现同一方向的翘曲,严重者呈船形。
钢板两面冷却条件不一致,上下表面温差大;
钢板在中压水区域停留时间过长。
7镰刀弯
钢板两纵边向同一侧弯曲,形似镰刀,称镰刀弯。
轧辊车削不正确或辊缝调整不平行;
轧件两边温度不均,钢板延伸不一致;
用圆盘剪剪边时,两剪刃重合量不一致。
8切斜
钢板未切成直角,而切成平行四边形、梯形、无规则的四边形等,称切斜。
剪切机调整不当,钢板剪切时未摆正靠齐或操作人员误操作等,都会造成钢板切斜。
四、宽带、窄带
1辊印
是一组具有周期性,大小形状基本一致的凸口缺陷,并且外观形状不规则。
一方面由于辊子疲劳或硬度不够,使辊面一部分掉肉变凹,另一方面可能是辊子表面粘有异物,使表面部分呈凸出状轧钢或精整加工时压^钢板表面形成凸凹缺陷。
在钢板表面破皮处,有不规则的点状、块状或长条状的非金属夹杂物,其颜色般呈棕红色、黄褐色、灰白色或灰黑色。
板坯皮下夹杂轧后暴露,或板坯原有的表面夹杂轧后残留在钢板表面上;
加热炉耐火材料及泥沙等非金属物落在板坯表面上,轧制时压入板面。
3氧化铁皮压入
氧化铁皮一般粘附在钢板表面,分布于板面的局部和全部。
铁皮有的疏松易脱落,有的压入板面不易脱落。
根据其外观形状不同有:
红铁皮、线状铁皮、木纹状铁皮、流星状铁皮、纺锤状铁皮,拖曳状铁皮和散沙状铁皮等。
板坯加热制度不合理或加热操作不良时产生一次铁皮难以除尽,轧制时被压入到钢板表面上;
大立辊设定不合理,铁皮难以除掉;
由于高压除鳞水管的水压低,水口堵塞,水口角度不对及使用不当等原因,使钢板上的铁皮没有除尽,轧制后被压入钢板表面上。
钢板表面有无规律分布的圆形凸包,有时呈蚯蚓式的直线状,其外缘比较光滑,内有气体。
当气泡轧破后,呈现不规则的细裂纹。
某些气泡不凸起,经平整后,表面光亮,剪切断面呈分层状。
圆板坯上存在较多的气泡气囊类缺陷,经多道轧制没有焊合,残留在钢板上;
板坯在炉内时间长,气泡暴露。
5折叠
钢板局部性的折合称折叠。
沿轧制方向的直线状折叠称顺折,垂直于轧制方向的折叠称横折,边部折叠称折边。
折叠、折皱的区别主要在于缺陷的形状,程度不同而异,折边与折角根据角度大小不同相区别。
横向折叠多发生在薄规格的带钢中。
含碳量小于0.08的软钢种,因开平机没有安装张力辊易产生折皱。
扳坯缺陷清理的深宽比过大;
板坯温度不均匀或精轧轧辊辊型配置不合理及轧制负荷分配不合理等,轧制中的带钢不均匀变形成大波浪后被压合;
立辊辊环的挤压或轧件有严重刮伤以及由于粗轧来料有较大的镰刀弯,刮框后再次被轧制压合;
卷取机前的侧导板严重磨损出现淘槽,开口度过小,夹送辊缝呈楔形,易使带钢跑偏,在侧导板沟槽处的部位被夹送辊压;
因故没及时卷取,使卷取温度过低或卷取速度设定不合适;
钢卷卷边错动,或因钢卷松动,在用吊车上吊,下降落地时易产生折边(折角),此时,常发生在厚度较薄的钢卷上;
带钢开卷温度过高,或开卷时的张力及压紧辊的压力设定不合适。
6塔形
钢卷上下端下齐,一圈比一圈高称塔形。
卷边上下错动称卷边错动。
助卷辊间隙调整不当;
夹送辊辊缝呈楔形;
带钢进卷取机时对中不良;
卷取张力设定不舍适;
成形导板的间隙调整不当;
卷取机前的侧导板动作时间不同步;
卷筒与推卷器之间有间隙;
卷筒传动端磨损严重。
回转时有较大的离心差;
带钢有较大的镰刀弯或板形不好。
沿钢带长度方面的水平面上向一边弯曲。
板坯有镰刀弯或严重的厚度不均;
粗轧、精轧辊磨损不均,辊缝出现楔形;
轧件两侧温度不均或加热温度不均;
轧机调整不良,两边压下量不一致;
立辊的中心线有偏差;
轧辊发生轴向串动或两侧轴承磨损不均;
侧导板开口度过大,轧件跑偏或轧件对中不好。
8楔形
钢板一边厚,一边薄在钢板宽度方向的横断面上看,类似楔形。
楔形程度有大有小。
轧辊磨损严重;
辊缝调整不舍适;
轧件跑偏;
轧件温度不均。
9凸度
钢板中间厚,两边薄,从钢板宽度方向的横断面来看,类似弧形,弧形程度有大有小。
轧辊严重磨损;
轧辊的热膨胀的冷却不均;
辊型设计不合理;
轧制负荷分配不均,轧辊弹跳变形过大;
弯辊装置不好;
加热温度不均或轧件温度不均。
10瓢曲
钢板的纵横部分同时在同一个方向出现的翘曲称瓢曲。
轧件温度不均,轧制过程变形不均;
钢带在轧钢辊道上喷水冷却不均;
终轧压下率过小;
钢带在精整时,矫直机压下设定下良,开卷温度过高,压力辊、矫直辊磨损严重。
五、冷轧带钢
1边浪
在轧制过程中,工作辊弯辊力设定不合适引起带材边部变形过大引起。
2乳化液斑
吹扫不净,板面残存乳化液与铁粉等其他杂质混合。
3分层
原料夹带。
4窄尺
原料镰刀弯、窄尺或酸洗对中装置故障。
5卷曲错层
原料本身携带镰刀弯过大或生产线对中装置故障。
六、棒材
1性能不合
屈服强度、抗拉强度、屈屈比、强屈比等性能不符合国标。
主要是化学成分、尺寸、重量偏差及轧制过程控制不当。
2重量偏差不合
钢筋实际重量与理论重量超过允许偏差。
在组织生产中,刻意生产负偏差产品。
3尺寸及外形不合
特征:
主要表现为肋间距、横肋高及内径不合标准。
原因:
生产企业为节约成本,普遍按内径负偏差组织生产;
未能使用符合标准的轧辊及严格执行换辊换槽制度。