冲压模具变压器铁芯片模具Word格式.docx
《冲压模具变压器铁芯片模具Word格式.docx》由会员分享,可在线阅读,更多相关《冲压模具变压器铁芯片模具Word格式.docx(26页珍藏版)》请在冰豆网上搜索。
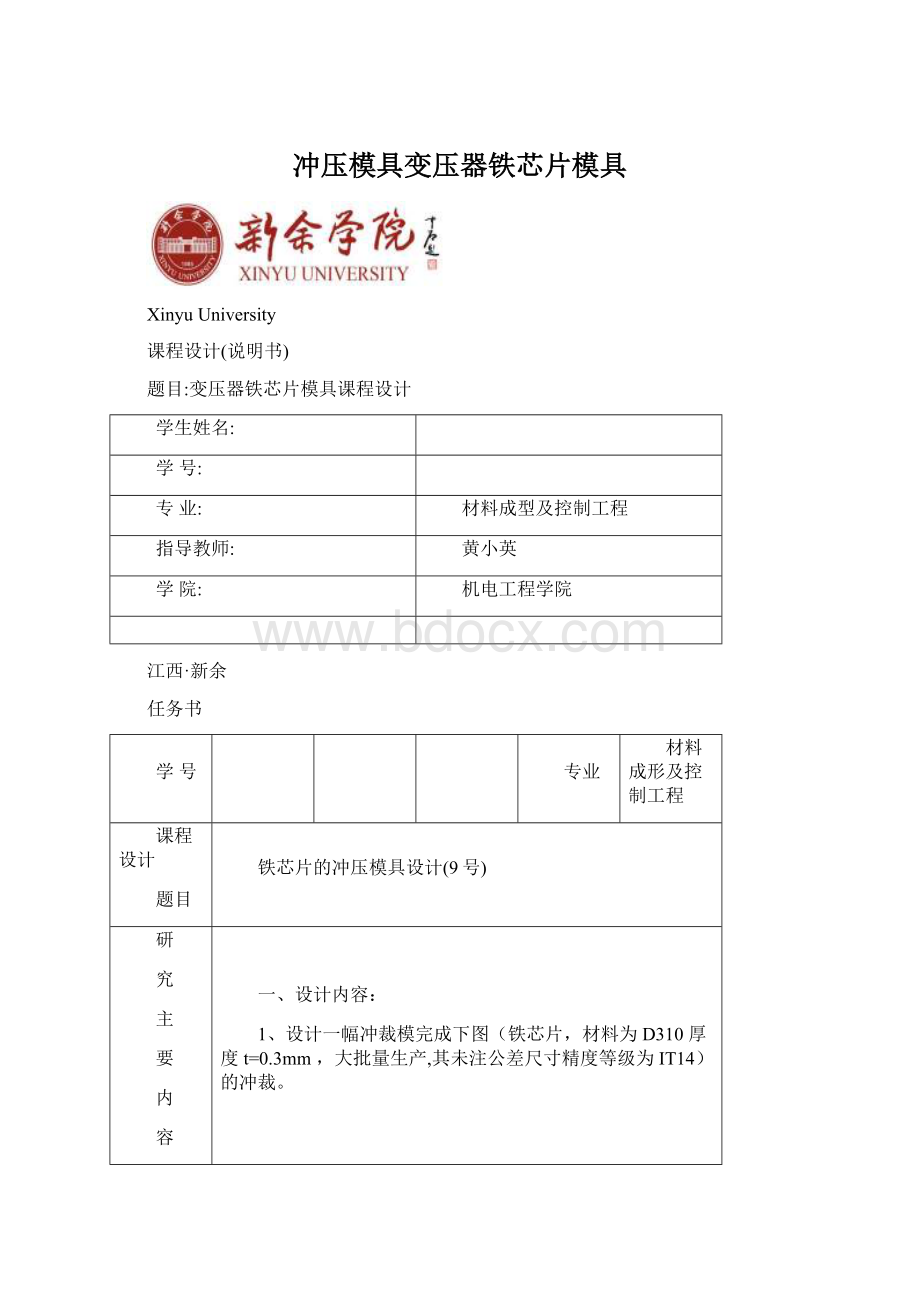
第二阶段(2016年12月25日)完成模具的总体结构设计;
第三阶段(2016年12月26日)完成模具的有关计算及相关零部件的选择设计;
第四阶段(2016年12月27日)完成模具的总装配图绘制;
第五阶段(2013年12月28日)完成模具设计说明书,并进行答辩。
毕业设计
(论文)工作
指导小组
(或教研室)
审核意见
毕业设计(论文)工作指导小
组组长(或教研室主任)签名:
年月日
签
名
学生签名:
年月日
指导教师签名:
目录
1绪论1
1.1冷冲压模具概述和发展1
1.2当前模具的技术水平1
1.3研究意义及当前国内外发展状况1
2冲压件工艺分析3
2.1工件材料分析3
2.2工件结构形状分析4
2.3尺寸精度4
3冲压工艺方案确定5
3.1冲裁工艺方案的确定5
3.2冲裁工艺方法的选择5
4模具总体结构7
4.1模具类型的选择7
4.2定位方式的选择7
4.3送料方式的确定7
5工艺参数计算9
5.1排样方式的选择9
5.2冲压力的计算12
6刃口尺寸的计算17
6.1冲裁间隙的确定17
6.2刃口尺寸的计算及依据与法则18
7主要零部件设计23
7.1凹模设计23
7.2凸模的设计25
7.3卸料装置的设计27
7.4凸模固定板的设计28
7.5导向零件及模架的选用的设计29
7.6模柄的选用29
8冲压设备的校核与选定31
8.1冲压设备的校核31
8.2压力机的选择31
9结论与展望33
9.1结论33
9.2展望33
参考文献35
致谢37
附录39
1绪论
1.1冷冲压模具概述和发展
冲压模具的定义是,冲压加工过程中,对材料加工使其成为半成品(或零件)的一种特殊工艺装备。
这是种特殊的工艺装备,与冲压件有精密相连的关系,但两者并没有通用性,在冲压生产的工艺装备中是必不可少,其功能、作用、手法这种种的东西注定冲压模具是技术密集、高附加值型产品。
因此冲压成形加工有着许多优点,包括低耗、高效、低成本、质量稳定、高一致性,可加工薄壁、复杂零件,板材有良好的冲压成形性能,但是模具成本高,所以冲压成形适宜批量生产。
冲压加工在制造业中很常用,采用模具生产的制件生产效率高,质量好,切削少,节约能源和材料,成本底等等的优点。
模具成形已经成为当代工业生产的重要手段,成为多种成型工艺中最具潜力的发展方向。
模具是机械、电子等行业的基础工业,它对国民经济和社会的发展起着越来越大的作用。
一个国家模具生产能力的强弱、水平的高低,直接影响着许多工业部门的新产品开发和旧产品更新,影响着产品质量和经济效益的提高。
我国为了优先发展模具工业,制定了一系列优惠政策,并把它放在国民经济发展十分重要的战略地位。
1.2当前模具的技术水平
近年企业加大了在技术进步方面的投资力度,将其看做企业发展的重要动力。
直至现在这些企业已普及了二维CAD,并陆续开始使用UG、Pro/E、SolidEdge、Solidworks、Optris和MAGMASOFT等软件,并成功应用于冲压模的设计中。
另外一方面,许多教育教研机构在模具技术的研究和开发也大力支持。
社会方方面面下的支持下,模具CAD/CAE/CAM技术方面明显有了极大的发展。
1.3研究意义及当前国内外发展状况
变压器铁芯片的冲裁工艺应用范围十分广泛,应用于国民经济的各个部门中,几乎都有冲压加工产品。
如汽车,飞机,拖拉机,电器,电机,仪表,铁道,邮电,化工以及轻工日用产品中均占有相当大的比重。
冲压工艺具有:
1)生产率高;
2)精度高,质量稳定;
3)材料利用率高;
4)操作简便等优点。
特别适宜于大批量生产和自动化。
我国的模具工业的发展,日益受到人们的重视和关注,在电子、汽车、电机、电器、仪表、家电和通信等产品中,60%-80%的零部件都要依靠模具成型(形)。
用模具生产制件所具备的高精度、高复杂程度、高一致性、高生产率和代耗率,是其它加工制造方法所不能比拟的。
近几年,我国模具工业一直以每年15%左右的增长速度发展,2003年,我国模具总产值超过400亿元人民币。
现代模具制造的必然趋势,就是机械加工尽可能地取代人工加工,这些设备大部分所用的程序基本上都是应用CAD、CAE、CAM系统产生的,操作人员工作按照规定的程序装夹工作,配备刀具和操作,机台就拿自动地完成加工任务,并将理想的模具零件制造出来或为下一加工工序完成规定的部分。
随着计算机软件的发展和进步,CAD、CAE、CAM技术也日臻成熟,其现代模具中的应用将越来越广泛。
可以预料不久的将来,模具制造业将从机械制造业中分离出来,而独立成为国民经济中不可缺少的支柱产业,与此同时,也进一步促进了模具制造技术向集成化、智能化、益人化、高效化方向发展
2冲压工件分析
本设计主要完成变压器铁芯片的冲压工艺及其模具设计,变压器铁芯片如图2-1所示。
图2-1铁芯片
工件名称:
铁芯片;
工件简图:
如图2-1;
生产批量:
大量;
材料:
D310;
材料厚度:
0.3mm;
精度等级:
IT14。
工件表面质量:
工件表面无毛刺、压痕、拉裂、油污等不良现象
2.1工件材料分析
材料名称:
硅钢;
材料牌号:
材料状态:
已退火;
2.2工件结构形状分析
变压器铁芯片结构相对简单,其上有两个直径Φ3mm的孔,工件轮廓由直线和直线垂直,呈山字形,且孔与边缘之间的最小距离也满足符合冲裁时的要求。
2.3尺寸精度
该冲裁件属结构简单的板状制品,冲裁件在形状上为对称结构,材料为D310。
属于电工用硅钢,具有良好的冲压性能。
零件图上所有的尺寸均未标注公差,可按IT14确定冲裁尺寸公差,查表可得各尺寸公差为48
6
12
36
30
3
24
,Ø
3
,冲裁件的尺寸公差为3mm大于孔的最小冲孔尺寸。
该冲裁件表面质量要求较小,普通冲裁件断面粗糙度Ra12.5--50μm如表2-1所示。
表2-1常见零件公差等级表
尺寸/mm
/μm
/mm
≤3
>3~6
>6~10
>10~18
>18~30
>30~50
>50~80
>80~120
>120~180
4
5
6
7
8
10
12
9
11
13
15
18
16
19
22
25
21
30
35
40
14
27
33
39
46
54
63
36
43
52
62
74
87
100
48
58
70
84
120
140
160
60
75
90
110
130
190
220
250
0.10
0.12
0.15
0.18
0.21
0.25
0.30
0.35
0.40
0.14
0.22
0.27
0.33
0.39
0.46
0.54
0.63
0.36
0.43
0.52
0.62
0.74
0.87
1.00
3冲压工艺方案确定
3.1冲裁工艺方案的确定
冲裁工艺方案的影响因素可分为制件的尺寸精度、技术要求、外观质量要求、工件材料力学性能及生产批量方面,从上述分析,可见本制件的工艺方案有以下三种:
方案一:
先落料,后冲孔。
采用单工序模生产。
方案二:
落料-冲孔复合冲压,采用复合模生产。
方案三:
冲孔-落料连续冲压,采用级进模生产。
分析:
模具结构简单、但需两道工序两副模具,生产率较低,难以满足该零件的年产量要求。
只需一副模具,冲压件的形位精度和尺寸精度较高,生产率高。
但材料利用率不高、冲压后成品件留在模具上,在清理模具上的物料时会影响冲压速度,操作安全不能保证。
也只需要一副模具,生产率较复合模高,操作方便,材料能合理利用,工件精度也能满足要求。
模具制造、安装稍复杂。
通过对上述三种方案的分析比较,该件的冲压生产采用方案三为佳。
3.2冲裁工艺方法的选择
本制件包含两道工序:
冲孔级落料。
模具类型通常有三种常用的模具可供选择,1)
采用两套模具,分别是冲孔模与落料模具。
这种单工工序
模制造方便,成本低,但无法达到本制件的精度要求。
(2)
级进模,把两道工序合并在一副模具中完成,可以减少模
具和设备数量,提高生产效率并容易实现自动化。
(3)
复合模,能够在一套模具中同时完成两道工序,但是复合
模结构复杂,制造成本高。
根据上述条件可以采用级进模具或者复合模具进行成型。
因为单工序模具无法达到产品的精度要求。
本制件属于小型制件,一采用成本较低,安全,自动化较高的级进模进行生产。
4模具总体结构
4.1送料方式的确定
由于零件尺寸较小,采用横向手动送料方式,即由左向右送料。
4.2模架结构和导向装置的选择
本模具采用导正销精定位,挡料销粗定位,导料板纵向定位。
(1)导料板的选用
选用分离式的导料板,外形尺寸纵向长度由凹模长度决定。
(2)侧刃的选择
由于制件两道工序之间的距离相对较大,步距与两个制件的距离一致,即为54mm.采用双侧刃,提高制件的精度。
侧刃的制造公差按h6确定,带侧刃的模具,一般都在侧刃孔旁的导料板上装有挡块,以减轻导料板挡料台阶的磨损。
(3)卸料装置的选用
对于本冲裁,落料级进模,已选用最简单的卸料装置,即弹压卸料装置,弹压卸料板既起卸料作用也起压料作用,所以冲件直平度较高,结构简便易于制造。
节约成本。
在冲裁前将板料压平,防止冲裁件翘曲。
(4)模架的结构形式
模架是模具的主体结构,他是连接冷冲模具工作零件的部件,所以选用模架相当重要,根据落料模的要求,搜作用的冲裁力较大,故选用导柱在两侧的中间导柱的模座结构,次结构比较平稳。
冲模的主要零件都是通过螺钉、销钉连接到模架上,构成一幅完整的冲模结构方可使用。
故本模具采用后侧导柱导套式中精度的中小型模架。
5工艺参数计算
5.1排样方式的选择
冲裁件在板料、带料或条料上的布置方法称为排样。
排样可以使使用的材料化学用品更少、从根本上让模具使用更长时间,排样的对不对很重要,将反应到材料的合理利用、冲件质量、生产率、模具结构与寿命。
排样的方法有:
直排、斜排、对直排、混合排,结合模具的各种物理方面性能及其不可改变的条件等全方位思考。
因此考虑以下三种方案:
有废料排样沿冲件外形冲裁,在冲件周边都留有搭边。
冲件尺寸完全由冲模来保证,因此冲件精度高,使用的时间更长,但是其性价比低。
见图5-1所示。
少废料排样因受剪切条料和定位误差的反应,冲件质量差,模具寿命较方案一低,但材料利用率稍高,冲模结构简单。
见图5-2所示。
无废料排样冲件的物理性能和使用时间都更低,但性价比最高。
见图5-3所示。
本模具采用少废料直对排方式排样:
见图5-3。
5.1.1搭边值的确定
根据零件形状和尺寸查表得,工件间的搭边值按矩形取=2mm。
制件间的搭边值a=1.8mm,制件与条料间搭边值a=1.5mm。
5.1.2材料利用率的计算
5.1.2.1直排的材料利用率计算
图5-1直排排样图
①
冲裁面积为:
A=993.87
②
步距S=36
③
条料宽度B=51
④
材料利用率n=A÷
BS=993.87÷
36×
51=0.5413
5.1.2.2横排的材料利用率计算
图5-2横排排样图
A=993.87
步距S=42
条料宽度B=63
42*63=0.7512
5.1.2.3对排的材料利用率计算
图5-3队排排样图
步距S=48
条料宽度B=45
48×
45=0.9203
表5-1排样比较方案
对3种排样方案比较:
排样方式
冲裁件面积
mm
步距
条料宽度
一个步距材料利用率
直排
993.87
51
54.13%
横排
42
75.12%
对排
45
92.03%
5.2冲压力的计算
5.2.1冲裁力的计算
1冲孔与落料的冲裁力
查附表知,τ=190Mpa,查表知Kx=0.055,Kt=0.063
F=KLtσb=1.3*(48*2+36*2+30*4+2*π*1.5*2)*0.3*190=22.75KN
其中冲孔F=KLtσb=1.3*2*π*1.5*2*0.3*190=1.4KN
落料冲裁力F2=22.75-1.4=21.35KN
卸料力Fx=Kx*F1=0.055*1.4=0.077KN
推件力Ft=n*Kt*F1=6*0.063*1.4=0.53KN
总冲压力F3=F+Fx+Ft=22.75+0.077+0.53=23.35KN
5.2.2初选压力机
5.2.2.1
根据计算总压力,查表可选用J23-160的压力机
表5-2压力机参数
公称压力(kN)
滑块行程(mm)
55
行程次数(次/min)
最大封闭高度(mm)
封闭高度调节量
滑块中心到床身距离(mm)
立柱间距离(mm)
工作台尺寸(mm)
前后
300
左右
450
工作台孔尺寸(mm
240
直径
210
垫板厚度(mm)
模柄尺寸(mm)
深度
床身最大倾角(°
)
5.2.5压力中心的确定
本制件冲裁时,模具中位置如图5-4
图5.4压力中心计算图
具体计算表如5-2-1所示。
表5-2-1尺寸计算表
线段序号
线段长度L
线段重心坐标
L*X
L*Y
X
Y
1
-24
-864
2
-21
-126
108
-18
-540
-12
-144
-6
-180
216
180
144
540
126
24
864
3.14*3
-15
113.04
-141.3
-113.04
合计
306.84
-642.6
-2.09
综上表格可知道压力中心为(0.-2。
09)
6模具刃口尺寸的计算
6.1冲裁间隙的确定
根据经验值法,查表得到该冲裁模初始双面间隙
Zmin=0.03Zmax=0.05
6.2刃口尺寸的计算
本凹模按配制法进行计算,具体见图6-1所示。
(1)落料凹模刃口尺寸计算
图6-1落料凹模刃口尺寸计算图
查表确定所有尺寸的磨损系数为x=0.5.
即
A36=(Amax-xΔ)=(36-0.5*0.062)
=35.69
A48=(Amax-xΔ)=(48-0.5*0.62)
=47.69
A6=(Amax-xΔ)=(6-0.5*0.62)
=5.85
A24=(Amax-xΔ)=(24-0.5*0.52)
=23.74
B12=(Bmin+xΔ)=(11.57+0.5*0.43)
=11.785
B3=(Bmin+xΔ)=(2.75+0.5*0.25)
=2.87
C30=C±
δ=30±
0.13
C3=C±
δ=3±
0.75
(2)落料凸模刃口尺寸计算
图6-2落料凸模计算图
A36=(Amax+xΔ)=(36+0.5*0.062)
=45
A48=(Amax+xΔ)=(48+0.5*0.62)
=67
A6=(Amax+xΔ)=(6+0.5*0.62)
=6.31
A24=(Amax+xΔ)=(24+0.5*0.52)
=24.26
B12=(Bmin-xΔ)=(11.57-0.5*0.43)
=12
B3=(Bmin-xΔ)=(2.75-0.5*0.25)
=2.625
(3)冲孔凸模的刃口尺寸计算
图6-3冲孔凸模计算图
A36=35.69
A48=47.69
A6=5.85
A24=23.74
B12=11.785
B3=2.87
C30=30±
C3=3±
7主要零部件设计
7.1落料凹模外形的设计
1.凹模长度
L=1+s+2c=36+36+72=144mm
3.凹模的高度Ha=
=
=16
4.凹模壁厚c=32
5.凹模的宽度B=b+2c=48+72=120
6.外形尺寸为140*120*20
图7-1凹模零件图
7.2冲孔凸模的设计
冲孔凸模:
冲孔模直径为3mm,固定方法采用台阶式固定。
由于凸模要穿过凸模固定板、橡胶及卸料板,长度较大,易折断,因此上部直径取值较大,定为10mm进入卸料板的凸模直径为3mm,用卸料板进行保护。
考虑到孔径的大小和冲裁力的影响制造成台阶式的凸模保证其强度及刚性,装配修磨方便,最大直径的作用是形成台肩,以便固定,保证工作时凸模不被拉出。
与凸模固定板配合部分按过渡配合(H7/m6或H7/n6)制造。
如图7-2所示。
凸模长度
L1=h1+h2+h3+h=16+10+4+24=54mm
图7-2冲孔凸模
落料凸模:
凸模断面为48mm*36mm的矩形凸模制成长方体,其体积大小适中且卸料力小,宜采用压入固定在凸模固定板上。
凸模用线切割机床加工制造。
尺寸67mm与5.44mm相交处为直角,但为延长凸模寿命,在线切割时应制成圆角5.0mm,如图7-3所示。
。
7-3落料凸模
7.3卸料装置的设计
对于本冲裁,落料级进模,已选用最简单的卸料装置,即弹压卸料装置,弹压卸料板既起卸料作用也起压料作用,所以冲件直平度较高,结构简便易于制造。
7.3.1卸料出件方式
弹压卸料装置弹压卸料装置是由卸料板、弹性元件(弹簧或橡胶)、卸料螺钉等零件组成。
弹压卸料既起卸料作用又起压料作用,所得冲裁零件质量较好,平直度较高。
因此,质量要求较高的冲裁件或薄板冲裁宜用弹压卸料装置。
弹压卸料板与凸模的单边间隙可根据冲裁板料厚度按下表选用。
在级进模中,特别小的冲孔凸模与卸料板的单边间隙可将表列数值适当加大。
当卸料板起导向作用时,卸料板与凸模按H7/h6配合制造,但其间隙应比凸、凹模间隙小。
此时。
凸模与固定板以H7/h6或H8/h7配合。
此外,在模具开启状态,卸料板应高出模具工作零件刃口mm5.0~3.0,以便顺利卸料。
7.4模架类型的选择
该模架选用对角导柱模架,导向装置安装在模具的对角线上,滑动平稳,导向准确可靠。
由标准(GB/T2851.5-1990)中选取,从而确定以下材和尺寸:
模架材料选取铸铁HT200,模架上模板的长度为250mm、宽度160mm、厚度45mm。
下模板的长度为250mm、宽度160mm、厚度50mm;
最大高度为200mm、最小高度为160mm。
模柄选取压入式模柄,压入模柄部位应与安装孔成H7/m6配合;
材料选取45钢,尺寸mm15030´
j。
螺钉选用标准件内六角螺钉,规格为M10;
导柱的直径为25mm,长度170mm;
导套的直径为38mm,长度85mm;
应按H6/h5配合;
柱间的距离150mm;
材料为20钢。
8铁芯片模具校核
8.1凹模强度校核
图8-1落料凹模
①正压力的校核
dmin≥
查参考文献可知
τ=300Mpa
σ=1400Mpa
即3≥
=1.7m
因为尺寸大于1.7mm,故满足强度要求
②弯曲应力的校核
Lmax≤95
=95×
=56mm
装模高度的校核
为了保证模具和压力机相适应,冲模的闭合高度H应介于压力机的最大装模高度Hmax和最小装模高度Hmin之间,其关系式为:
Hmin-H1+10mm≤H≤Hmax-H1-5mm
式中,H--冲模的闭模高度
Hmax--最大闭模高度
Hmin--最小闭模高度
H1--垫板高度
Hmax-H1--最大装模高度
Hmin-H1--最小装模高度
则Hmin-H1+10mm=130mm+10mm=140mm
Hmax-H1-5mm=190mm-5mm=185mm
H=H下模座+H上模座+H垫板+H凸模+H凹凸模=45+40+8+42+28-16=179mm
有此可知,Hmin≤H≤Hmax则所选则的压力机符合要求
9模具结构设计
模具的总装图和工作过程
模具的装配就是根据模具的结构特点和技术条件,以一定的装配顺序和方法,将符合图纸技术要求的零件,经协调加工,组装成满足使用要求的模具。
在装配过程中,既要保证配合零件的配合精度,又要保证零件之间的位置精度,对于具