第二章输油泵Word文档格式.docx
《第二章输油泵Word文档格式.docx》由会员分享,可在线阅读,更多相关《第二章输油泵Word文档格式.docx(17页珍藏版)》请在冰豆网上搜索。
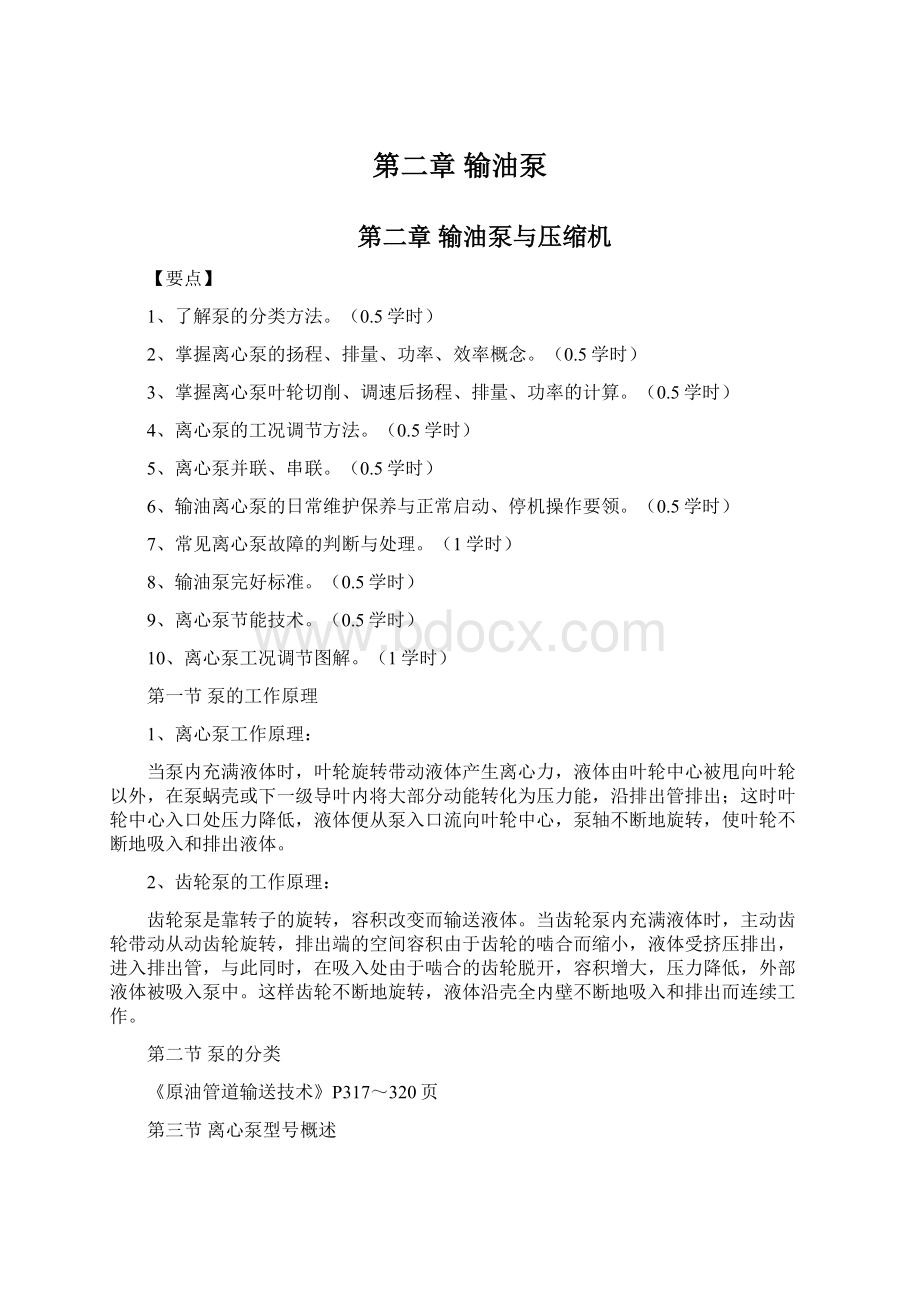
K:
水平中开结构
S:
双吸式
500:
额定流量500m3/h
90:
3.4BA-12A
4:
吸入口径4英寸,100mm
BA:
单级单吸悬臂式水泵
12:
比转速除10,即比转速120左右
叶轮更换不同外径或叶轮首次切削。
2B-6A
2:
吸入口径2英寸,50mm
B:
6:
比转速除10,即比转速60左右
4.150S-78A
150:
吸入口径150mm
78:
扬程m
单级双吸式离心水泵
5.D155-30×
3
D:
多级单吸离心水泵
155:
排量155m3/h
30:
单级扬程30m
3:
三级叶轮
6.4/3D-AH(渣浆泵)
入口直径4英寸
3:
出口直径3英寸
D型托架
AH:
重型渣浆泵
7.IS80-65-160A
IS:
单级单吸IS型离心水泵
80:
吸入口经mm
65:
排除口径mm
160:
叶轮名义直径mm
叶轮首次切削
8.KDA260-85×
8
水平中开结构
多级泵
涡壳式
260:
排量260m3/h
85:
单级扬程85m
8:
叶轮级数
9.KDY250-114×
6
DY:
多级离心输油泵
250:
排量250m3/h
114:
单级扬程114m
第四节离心泵的性能参数
1、流量
泵的流量是指单位时间内泵排出口所输出的流体量。
铭牌表示的通常是体积流量,工艺计算中常采用质量流量。
2、扬程
泵的扬程是指单位质量液体流过泵所获得的能量增量。
铭牌上的扬程是用水试验并按标准状况给出的。
在输送介质粘度不大于水时,恒转速下泵扬程与液体重度无关。
3、功率
泵的有效功率公式:
Ne=QHγ
式中:
Ne——泵的有效功率,W
Q——体积流量,m3/s
H——扬程,m
γ——液体重度,γ=ρg,N/m3
4、效率
1)容积损失
容积损失是由于泵的泄露造成的。
离心泵运转过程中,有一部分获得能量的高压液体,通过叶轮与泵壳之间的间隙回流至吸入口,因此造成泵排出的实际流量要比理论排出流量低,其比值称为容积效率。
容积损失包括环流损失、多级泵级间泄漏、平衡装置及盘根漏损。
环流损失是由于叶轮出口压力大于入口压力,使高压液体通过叶轮与泵壳承磨环的间隙漏回到叶轮入口,形成环流损失。
漏失的大小取决于叶轮口环的直径、间隙大小和压差。
平衡装置的漏损主要是液体通过泵的平衡孔、平衡盘、平衡管等回流到低压区形成的损失。
η容=(Q-q)/Q
2)水力损失
水力损失是由于流体流过叶轮、泵壳时,由于流速大小和方向改变(形成漩涡),且发生冲击而产生的能量损失。
所以泵的实际压头要比泵理论上所能提供的压头低,其比值称为水力损失。
η水=(HT-hT)/HT
水力损失包括吸入室损失、叶轮入口处的冲击损失、叶轮流道内的摩擦损失、液体流出叶轮时的冲击损失、排出蜗壳室扩散部分的冲击损失等。
3)机械损失
泵在运转时,在轴承、轴封装置等机械部件接触处由于机械摩擦而消耗部分能量,故泵的轴功率大于泵的理论功率。
理论功率与轴功率之比称为机械效率。
η机=(N轴-N损)/N轴
盘面损失:
叶轮在充满液体的泵壳内高速旋转时,叶轮盖板与液体产生的摩擦损失。
随叶轮级数的增加而成倍增加,与叶轮直径、转速、液体性质有关。
泵的总效率等于上述三种效率的乘积。
η=η容·
η水·
η机
或η=Ne/N轴
5、最小汽蚀余量及允许吸上真空高度
1)汽蚀
离心泵入口处压力低,溶解在液体中的气体在泵叶轮入口压力低到其气化压力时就会逸出,进入叶轮后液体压力又会高于其气化压力,因此气泡溃灭时,液体质点冲击叶轮金属表面,产生机械撞击破坏,即剥蚀,同时由于气泡中还夹杂有一些活泼性气体(如氧等),对金属又兼有化学腐蚀作用,加快了金属的损失。
这种剥蚀与腐蚀合称汽蚀。
汽蚀会在泵一级叶轮入口处造成密集的坑洞甚至沟槽,严重影响泵的性能甚至运行安全。
2)最小汽蚀余量
为避免汽蚀发生,要求泵一级入口处液体高出饱和蒸汽压一个最小余量,称泵的最小汽蚀余量。
泵入口处的绝对压力与汽蚀余量关系:
△h=Pr/ρg+V2/2g-Pv/ρg
3)允许汽蚀余量
为保证泵操作时不发生汽蚀,应使泵所需要的汽蚀余量比泵的最小汽蚀余量大一裕量,一般为0.3米液柱。
因此允许汽蚀余量:
△h=△hmin+0.3
4)最大吸上真空高度Hs
当泵在大气压下作用于吸入池液面时,在泵一级入吸上真空度增加到泵发生汽蚀时的吸上真空度即泵的最大吸上真空高度。
对于大气压Pa为760mmHg,抽20℃清水时,泵最大吸上真空高度Hs与允许汽蚀余量之间关系:
Hs=(Pa-Pv)/ρg+V2/2g-△h
5)允许吸上真空高度
为保证泵操作时不发生汽蚀,把最大吸上真空高减去0.3米液柱,即为允许吸上真空高度。
Hs=Hs·
max-0.3
6)比转数
两台离心泵在效率相同的情况下,要使两台泵相似,必须具备以下条件:
a)几何相似泵内液体流道部分所有对应的尺寸成比例,所有对应叶片角相等(甚至表面粗糙度相同)
b)运动相似泵内液体流道部分对应的液流方向一致。
流速大小成比例。
c)动力相似泵内液体流道部分的雷诺数相同或处于阻力平方区
对于水泵主要是前两个条件。
两台相似泵的性能曲线是否相似,可用比转数ns衡量。
ns=3.65
n——泵轴转速,r/min
Q——额定体积流量,对于双吸式叶轮为Q/2,m3/s
H——额定扬程,对于多级泵应为H/i(i为级数),m液柱。
根据比转数,离心泵可分为:
低比转数泵:
ns=20~80
中比转数泵:
ns=80~150
高比转数泵:
ns=150~300
比转速可反映叶轮的形状:
低比转速泵(一定转速下流量小,扬程高)的叶轮外径大,内径小,出口宽度窄小;
高比转速泵叶轮外径小,内径大,出口宽度大。
比转速低于50的离心泵,由于其流道窄,盘面损失过大,泵的效率低,加工困难,不多采用。
不同比转速离心泵的叶轮简图如下:
不同比转速离心泵的工作特性曲线图如下:
第五节离心泵工况调节
一、泵的设计(额定)流量
泵的设计流量是泵设计时首先要确定的主要参数之一。
其它通用部件的设计都与它密切相关、协调一致。
泵在设计流量点工作时,液体在叶轮内及涡室内的流动速度以及流出叶轮的速度协调一致。
涡室可以保证液体在叶轮周围作匀速运动,叶轮周围液体流速和压力分布均匀,水力撞击损失小,效率高,叶轮径向力平衡,运转平稳。
反之,过多地偏离设计流量运行,涡室与叶轮的合理匹配就要丧失,导致液体在涡室内的流动速度与液体流出叶轮的速度在大小与方向上不一致,使水力撞击损失增加,效率下降。
另外,叶轮径向力的平衡被破坏,振动增加,运转平稳性下降。
泵运行中异常声音可分:
汽蚀异音松动异音小流量异音滚动异音
二、离心泵的最小输量与经济运行范围
泵样本或使用说明书对泵的最小操作流量作出的规定,其比例通常为泵额定流量的一半,也有将泵的最小流量规定为额定流量的30%。
这是因为当离心泵在接近出口阀全关状态下工作时,由于介质在泵内滞留时间增长,涡流及环流量增加,泵体内温升将随之增加。
同时由于出口节流大,泵体内流体流动状况与设计相差较远,泵的振动及噪音均会提高,加上发热量大,泵口环易咬合,发生机械故障的概率增加,不利于泵长周期运行。
经验表明,离心泵在下列范围内运行比较经济合理:
1、比转速ns<
100的离心泵:
Qmax=1.2Qd时,Hmin=0.9Hd
Qmin=0.6Qd时,Hmax=1.1Hd
2、比转速ns>
Qmax=1.2Qd时,Hmin=0.8Hd
Qmin=0.6Qd时,Hmax=1.15Hd
Qd、Hd:
设计工作点流量与扬程。
(备注:
讲课时根据泵特性曲线标示出高效区域比较清晰)
三、离心泵工况调节方法与特点
一)改变管路系统特性的调节方法:
1、节流法
即改变泵出口阀开度,从而改变管路系统的摩阻大小,此法调节比较灵活,应用广泛,但节流损失较大。
离心泵节能首先就是要降低或避免出口阀的节流损失。
2、旁路循环法
此法能耗浪费大,且回流温度高时,易发生汽蚀,通常较少利用。
二)改变泵特性P439
1、改变泵转数
Q2/Q1=n2/n1,H2/H1=(n2/n1)2,N2/N1=(n2/n1)3
离心泵转速变化程度与泵的效率的关系:
通常泵转速变化在额定转速的20%以内时,泵效率不变;
而当降低转速超过20%额定转速时,泵效率略有下降。
相反。
提高转速20%时,泵效率会略有上升,但超过额定转速调节的情况较少。
2、切削叶轮,改变叶轮直径
对于中、高比转数泵:
Q2/Q1=D2/D1,
H2/H1=(D2/D1)2,
N2/N1=(D2/D1)3
对于低比转数泵:
Q2/Q1=(D2/D1)2,
H2/H1=(D2/D1)3,
N2/N1=(D2/D1)4
但是叶轮切削也不是任意的,切削达到一定程度后,泵的效率就要明显下降。
为了使叶轮切削后泵的效率不降低或少量降低,要规定出最大允许车削量。
最大允许车削量与比转速ns大小有关,比转速越大,允许车削量越小,如下图:
ns
60
120
200
300
*350(仅供参考)
(D-D’)/D
0.2
0.15
0.11
0.09
0.07
3、对多级泵可调整叶轮级数,降低泵的总扬程,从而改变泵特性。
如果多级泵在基本稳定的流量下长期工作且扬程偏高量超过单级叶轮的扬程,可以用减少叶轮的办法降低泵的总扬程。
第一级叶轮不能拆除,因为有的多级泵一级叶轮与其它级叶轮尺寸不同,另外,拆除一级叶轮,吸入段阻力会增加,在吸入管路汽蚀余量较低的情况下,有可能出现汽蚀现象。
四、离心泵(风机)调速方式大致分为类:
一)、在驱动机与工作机之间联轴器处安装调速装置,如液力偶合器,(滑差变送器)等。
其中液力偶合器使用较多,它的适用功率范围较宽。
偶合器的效率等于输出功率与输入功率之比值。
η=MTnT/MBnB=nT/nB=i
忽略主、从动轴承、轴封等阻力转矩,涡轮转矩MT与泵轮转矩MB相等,其效率等于转速比i。
偶合器的滑差S指泵轮与涡轮转速之差对泵轮转速之比。
S=(nB-nT)/nB=1-i=1-η
由此可见,偶合器的效率等于其转速比i,提高偶合器转速比时,其效率也增加,而滑差S减小。
二)、改变驱动机转速,如气轮机、电机调速。
异步电动机由于结构简单、运行可靠,在工业领域广泛应用,但其调速性能很差。
通常异步电机调速方法可分类如下:
1、在定子方面采取措施:
1)变更加到定子绕组上的电压数值;
2)改变定子绕组的磁极对数;
3)变更加到定子绕组上的电源频率。
2、在转子方面采取措施:
1)变更转子电路中的电阻数值;
2)在转子电路端上串联一个或几个附加电气元件,称为串级联接调速。
还有用电磁偶合的方法来实现调速的。
五、变频调速
异步电动机的变频调速是通过改变定子的供电电源频率来改变旋转磁场的同步转速,从而改变转子的转速的。
旋转磁场同步转速:
n1=60f/P
异步电机的转速公式:
n=60f(1-s)/P
式中 f——频率 Hz
P——磁极对数
S——转差率
电机变频调速的优点:
①变频调速范围大,调速的平滑性能好,并有足够的机械特性。
调节效率高,接近于理想的调节和变速;
②改造设备时,不涉及电动机及所驱动的泵或风机本身,停机改造时间短,影响生产少;
③变频装置一旦故障,可退出运行,改为工频供电机泵的节流调节,不影响泵的连续运行;
④安装地点不限于在电动机轴端和设备附近,处理与集中操作便利。
但变频调速造价高。
第六节离心泵工况图解
1.离心泵特性曲线《原油管道输送技术》P324~326页
案例:
外输泵提量如电流接近极限,是开出口还是关循环?
2.输油泵与管道系统工况调节图解《原油管道输送技术》P120~129页
2.1泵出口节流
2.2改变泵站工作特性P127
2.3离心泵串联P81
2.4离心泵并联P81
2.5旁路调节P438
2.6机泵调速P439
(可根据情况推倒比转数变化)
2.7密闭输油管道中间泵站入口压力图解P123
2.8典型分支管路、交汇管路工况图解P435
经验小结:
采用节流法时实际过泵流量远小于旁路循环法,根据离心泵的N-Q特性曲线,通常离心泵输量增加,其轴功率也相应增加,即电机负荷相应增加,电机电流也相应增加。
节流时管道压力降低、输量减少,泵压上升,电机负荷下降电流减小。
旁路循环时,泵后管道压力降低,输量减小,泵压降低,但过泵流量增加,电机负荷上升,电机电流增加。
第七节离心泵完好标准
7.1运转正常,效能良好
a.压力、流量平稳,出力能满足正常生产需要,或达到铭牌能力的90%以上。
b.润滑、冷却系统畅通,油环、轴承箱、液面管等齐全好用。
润滑油(脂)选用符合规定。
轴承温度符合设计规定;
c.运转平稳无杂音,和振动符合标准规定;
d.轴封无明显泄漏;
e.填料密封泄漏:
轻质油不超过20滴/min;
重质油不超过10滴/min。
f.机械密封泄漏:
轻质油不超过10滴/min;
重质油不超过5滴/min。
7.2内部机件无损,质量符合要求:
主要机件材质的选用,转子径向,轴向跳动量和各部安装配合,磨损极限,均应符合规程规定。
7.3主体整洁,零附件齐全好用:
a.压力表应定期校验,齐全准确。
控制及自起动联锁系统灵敏可靠。
安全护罩,对轮螺丝,锁片等齐全好用;
b.主体完整,稳钉,挡水盘等齐全好用;
c.基础,泵座坚固完整,地脚螺栓及各部连接螺栓应满扣,齐整、紧固:
d.进出口阀及润滑、冷却的管线,安装合理,横平竖直,不堵不漏。
逆止阀灵活好用;
e.泵阵整洁,保温,油漆完整美观:
f.附机达到完好.
7.4技术资料齐全准确,应具有:
a.设备档案,并符合总公司设备管理制度要求,
b.定期状态监测记录(主要设备):
c.设备结构图及易损配件图。
第八节离心泵节能技术
一.离心泵调速
(前面已述)
二.提高离心泵加工、检修质量
1.提高泵的机械效率
1)减少轴封及轴承摩擦损失。
尽量采用机械密封而不采用填料密封。
对于滑动轴承,轴承与轴径的接触间隙要符合要求,同时要保证轴径光度,改善润滑,以降低损耗。
填料密封要压紧适度,以减少摩擦损耗。
2)减少圆盘摩擦损失,即减少叶轮外表面与液体间的摩擦损失,它占机械损失的主要部分。
比转数越低时,盘面损失功率比例越大,因此要提高叶轮盖板、泵体内壁的光度。
2.提高泵的容积效率。
容积效率与泵的结构形式及比转数有关。
对于吸入口径相同的情况下,比转数大的泵容积效率较高。
在设计及检修过程中提高容积效率的措施是采取增大口环阻力的结构形式,如迷宫式口环、锯齿状口环等。
另外在不影响安全运行前提下,尽量减小口环间隙。
3.减少泵的水力损失
水力损失与泵的几何形状、壁面粗糙度及介质粘度有关。
经验表明:
铸铁泵壳内壁涂漆(工况允许时)后效率提高2~3%。
泵体内壁及叶轮盖板研磨后,泵效率可提高2~4%。
三.提高离心泵原动机运行效率
通常电动机负载率70~100%效率较高,尤其以75%左右时效率最高。
因此要尽量合理匹配离心泵的电动机。
GB11057-89《离心式、混流式、轴流式水泵运行管理》规定:
对于泵的常用工况,其驱动电机的负载率不得小于40%或超载运行。
1980年的《炼油厂机泵调整座谈纪要》规定:
电机负载率在50~70%时应通过经济比较后决定是否更换,在更换前要测定、比较,确定节约有功、无功的效果。
设备回收期不宜超过两年。
第九节通风机、鼓风机、压缩机、真空泵(课时不足时略)
一、分类
气体输送机械与液体输送机械大体相同,但气体具有压缩性,在输送过程中,压力发生变化时其体积和温度将发生变化。
气体压力变化程度,常用压缩比来表示。
压缩比为气体排出与吸入压力的比值。
气体输送机械按其终压(出口压力)或压缩比大小可分为以下四类:
1、通风机终压不大于1500mmH2O(表压),压缩比为1~1.15
2、鼓风机终压0.15~3kgf/cm2(表压),压缩比小于4
3、压缩机终压3kgf/cm2以上(表压),压缩比大于4
4、真空泵使设备产生真空,出口压力为1kgf/cm2(表压),其压缩比由真空度决定。
二、通风机
通风机主要有离心式和轴流式两种类型。
轴流式通风机所产生的风压很小,只作通风换气之用。
离心式通风机按产生的风压大小分:
低压离心通风机风压≤100mmH2O(表压)
中压离心通风机风压100~300mmH2O(表压)
高压离心通风机风压300~1500mmH2O(表压)
离心式通风机的叶片数较离心泵多,而且不限于后弯叶片,也有前弯叶片。
在中、低压离心通风机中,多采用前弯叶片,有利于提高风速,从而减少通风机截面积,设备尺寸较小,但效率较低。
这是因为动能加大,而且叶轮出口速度变化比较剧烈的缘故。
三、鼓风机(blower)
常见的鼓风机有离心鼓风机和旋转鼓风机两种。
1、离心鼓风机又称涡轮鼓风机或透平鼓风机,其基本结构和操作与离心通风机相似,只是离心通风机只有一个叶轮,仅能产生低于0.15kgf/cm2的风压,而离心鼓风机一般是由几个叶轮串联组成的多级离心鼓风机,其出口压力一般不超过3kgf/cm2。
2、旋转鼓风机生产中应用较多的是罗茨鼓风机。
其风量变动范围大,可自2至500m3/min,出口表压在0.8kgf/cm2以内,在表压0.4kgf/cm2附近效率最高。
罗茨鼓风机兼有往复式和离心式的一些特点。
与往复式一样,在转速一定时,风压改变,风量可基本不变,风量与转速成正比。
另外,与离心式一样,转速高,无阀门,重量较轻,结构简单,排气均匀。
缺点是制造和安装不易,效率较低。
其出口应安装稳压罐与安全阀。
流量用旁路调节,操作时温度不能超过85℃,否则会引起转子受热膨胀而发生碰撞。
四、压缩机(Compressor)
化工生产中使用的压缩机(Compressor)主要有往复压缩机与离心压缩机两种。
由于离心压缩机的基本结构和操作原理与离心鼓风机完全相同,故下面着重介绍往复压缩机。
往复压缩机的构造、工作原理与往复泵相近。
主要部件有气缸、活塞、吸气阀和排气阀。
依靠活塞的往复运动,循环地进行吸气,压缩及排气过程。
一,往复压缩机的工作过程
1.理想压缩循环
在理想情况下,气缸排气终了时,活塞与气缸盖之间没有空隙(即余隙)以及各种能量损失。
往复压缩机在理想情况下的压缩过程可用图2-26来说明。
当活塞由左往右运动时,吸气阀A打开,气体在pl压力下吸入缸内,如图2-26中4-1线所示。
当活塞开始向左移动时,吸气阀A关闭,气体在气缸中被压缩,如图中1-2(或1-2’;
1-2”)线所示。
当气缸中气体的压力大于排气阀B外的气体压力时,排气阀被顶开,气体在P2压力下排出气缸,如图中2-3(或2’-3;
2”-3)。
3-4线表示排气终了和吸气初气缸内压力的变化,由4点开始又重复以上循环。
由压力p1升高到p2可依三种不同的过程进行压缩,即绝热过程、等温过程和多变过程,分别用图中1-2’、1-2”和1—2线表示。
等温与绝热过程只是两种极端情况,实际压缩过程与多变过程比较接近,多变压缩功为
压缩所消耗的功可用图2-26中的面积表示。
如等温压缩耗功面积为1-2”-3-4;
绝热压缩耗功面积为1-2’-3-4;
多变压缩耗功面积为1-2-3-4。
由图2-26可知,绝热压缩耗功最多,等温压缩耗功最少.
多变压缩时,气体排出口绝对温度为:
T1——入口温度,K;
T2——出口温度,K;
m——多变指数。
2、有余隙压缩循环
往复式压缩机排气终了时,活塞与汽缸盖之间必须留出很小的空隙,称为余隙。
有余隙的压缩循环与理想压缩循环的区别在于排气终了残留在余隙体积中的高压气体在活塞反向运动时,将再膨胀。
采用多级压缩可降低压缩气体所消耗的功。
3、往复式压缩机排气量的调节
1)调节转速
2)旁路调节在旁路装调节阀,如果旁路的截面积足够,调节阀全开时,排气压力和进气压力相等,无气体排出。
如果调节阀部分开启,即可均匀调节。
一般压缩机多采用此法。
3)改变汽缸余隙容积显然,余隙容积增大,余隙内残存气体膨胀后所占容积将增大,吸入气体必然减少,供气量随之下降。
反之供气量上升,所以能起到调节流量作用。
多在大型压缩机中采用。
五、真空泵(vacuumpump)
从真空容器中抽气并加压排向大气的压缩机称为真空泵(vacuumpump)。
真空泵的型式很多,现将化工厂中常用的几种,简单介绍如下。
一、往复真空泵
往复真空泵的基本结构和操作原理与往复压缩机相同,只是真空泵在低压下操作,气缸内外压差很小,所用阀门必须更加轻巧,启闭方便。
另外,当所需达到的真空度较高时,如95%的真空度,则压缩比约为20。
这样高的压缩比,余隙中残余