答案精密加工课后习题黄Word格式.docx
《答案精密加工课后习题黄Word格式.docx》由会员分享,可在线阅读,更多相关《答案精密加工课后习题黄Word格式.docx(29页珍藏版)》请在冰豆网上搜索。
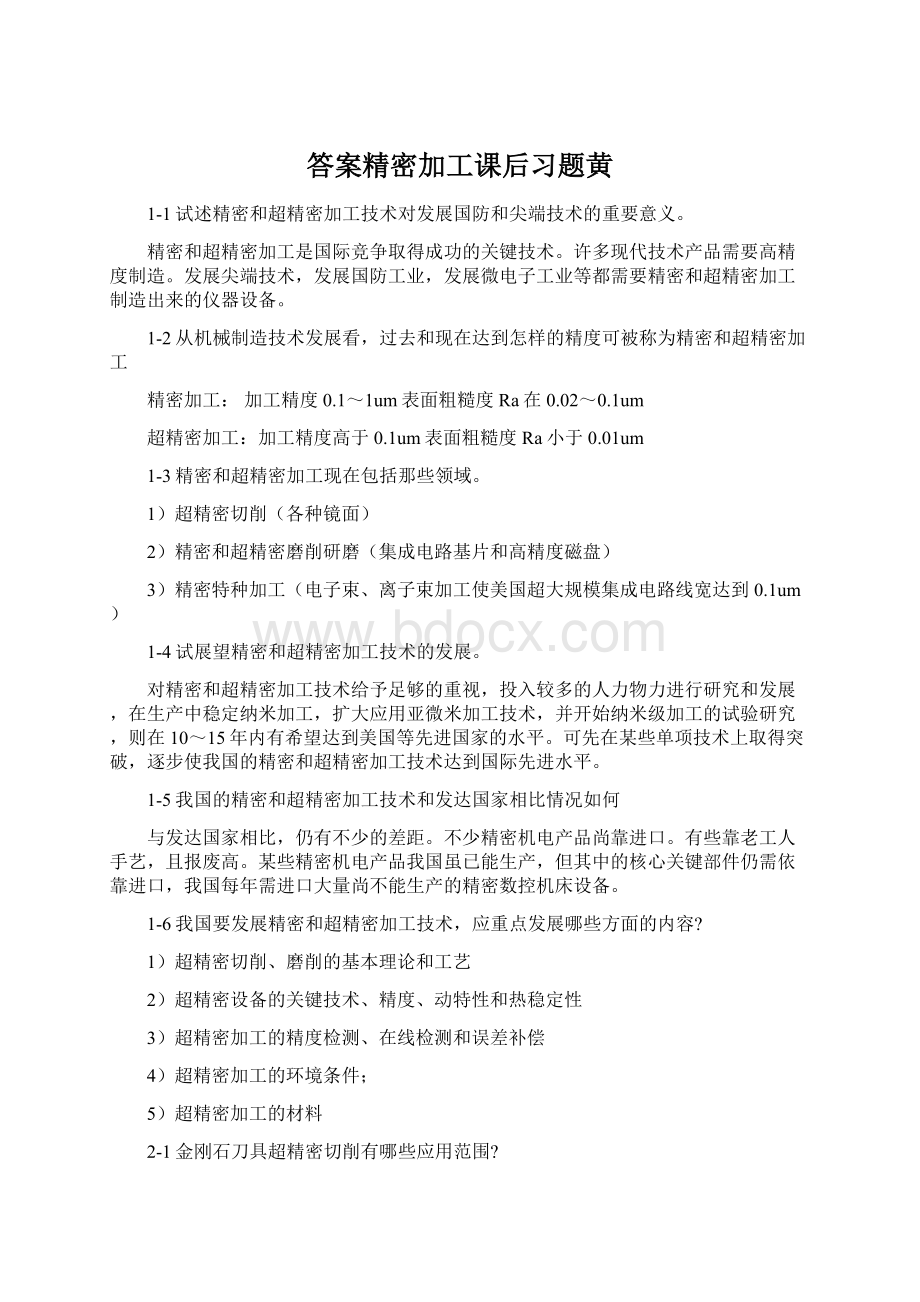
根据所使用的超精密机床的动特性和切削系统的动特性选取,即选择振动最小的转速。
2-3试述超精密切削时积削瘤的生成规律和它对切削过程和加工表面粗糙度的影响
金刚石刀具精密切削有色金属,不用切削液,在所有进行实验的切削参数下都产生积削瘤。
切削速度v较低时,积削瘤高度h0最高,当v>
314m/min时,积削瘤较小且趋于稳定
进给量f很小时,积削瘤高度h0较大,在f=5um/r时h0值最小,f值再增大时,h0值稍有增加,
背吃刀量ap<
25um时,积削瘤的高度h0变化不大,但在ap大于25um时,积削瘤的高度h0将随ap的值增加而增加。
2-4试述各工艺参数对超精密切削表面质量的影响
1)速度小表面粗糙,但使用切削液的情况下,切削速度的变化对加工表面的影响不大
2)进给量和修光刃,使用修光刃的刀具,f<
0.02mm/r时,进给量对表面粗糙度影响不大
3)切削刃形状,圆弧刃比直线刃更易对刀,更能得到高质量的表面。
4)背吃刀量减小时表面粗糙度加大,但在刀具切削刃钝圆半径rn足够小(0.05~0.1um)
2-5超精密切削时如何才能使加工表面成为优质的镜面?
1)进给量f=2.5um/r,背吃刀量ap=2um时,不同切削速度均能得到晶面
2)使用圆弧切削刃刀具,在进给量f<
5um/r时,均达到Rmax<
0.05um的镜面
3)采用经过精密研磨的单晶天然金刚石刀具。
2-6超精密切削时,金刚石刀具切削刃锋锐度对切削变形和加工表面质量的影响如何?
有明显的影响,用rn=0.6um的金刚石车刀,只能在较小的进给量和背吃刀量的条件下(ap=1~2um,f<
2.5um/r)可切出可切出Rmax=0.056um;
更锋锐的刀具(rn=0.3um),可以在较宽的切削条件下切出Rmax=0.056um的表面。
2-7超精密切削时极限最小切削厚度是多少?
hDmin=rn[1-(Fp+uFf)/sqrt((Ff2+Fp2)(1+u2))]
2-8试述超精密切削用金刚石刀具的磨损和破损特点。
属于机械磨损,本质是微观解理的积累。
当作用应力相同时,(110)面破损的机率最大,(111)面次之,(100)面产生破损的机率最小。
2-9金刚石刀具晶面选择对切削变形和加工表面质量的影响如何?
直接影响切削变形和加工表面质量,用100晶面做金刚石刀具的前面和后面,可使切削变形减小,并可减小后面与加工表面间的摩擦
2-10工件材料的晶体方向对切削变形和加工表面质量的影响如何?
单晶体材料有很高的各向异性,不同晶向的切削变形和切削力都不相同。
不同晶向的加工表面粗糙度都不相同。
相同晶面的切削,晶面方向发生变化,切削变形和加工表面粗糙度也不相同
2-11脆性材料用超精密切削如何加工出优质表面?
需要实现塑性切削,要求金刚石刀具很锋锐并有合理的切削角度,通过改变切削力作用方向来改变切削区的变形方向,使崩碎可能性小,其次,切削厚度极小,小于某临界值后,可实现塑性切削,能切出极好的优质表面。
2-12超精密切削对刀具有哪些要求?
为什么单晶金刚石是被公认为理想的、不能代替的超精密切削的刀具材料?
1)硬度高、耐磨性高和弹性模量高,保证寿命长和耐用度高
2)切削刃钝圆及其锋锐,及半径rn极小,可实现超薄切削
3)切削无缺陷
4)和工件材料的抗粘结性好、化学亲和性小、摩擦因数低。
使加工表面完整。
天然单晶金刚石有以上一系列优异的特性
2-13单晶金刚石有哪几个重要晶面?
三个100、110、111
2-14试述金刚石晶体的各向异性和不同晶面研磨时的好磨难磨方向。
各项异性:
对称轴不同,与4次对称轴垂直的是100面,与3次对称轴垂直的是111晶面晶面,与2次轴对称的是110晶面。
网面最小单元不同,100是正方形,110为矩形,111为三角形,网面密度100:
110:
111为1:
1.414:
2.308
网面距不同:
100与110为均匀分布,分别为D/4=0.089mm,sqrt
(2)D/4=0.126mm,111为宽窄交替宽为sqrt(3)D/4=0.154mm,窄为sqrt(3)D/12=0.1051mm
解理现象:
111面的面网宽面距比100和110都大,最易解理。
好磨难磨方向可用图表示:
100磨削率:
111磨削率:
110磨削率=5.8:
1:
12.8
2-15金刚石晶体有哪些定向方法?
1)人工目测定向2)X射线定向3)激光定向
2-16试述金刚石晶体的激光定向原理和方法。
利用金刚石在不同晶面方向上,晶体结构不同,对激光反射形成的衍射图像不同而进行。
2-17如何根据金刚石微观破损强度来选择金刚石刀具的晶面?
在外力作用下,110面最易破损,111面次之,100面最不易破损,因此金刚石刀具的前面和后面应选择最不易破损的100面。
2-18比较直线修光刃和圆弧修光刃金刚石刀具的优缺点。
直线修光刃制造容易,可减少残留面积,减小加工表面粗糙度,长度通常取0.05~0.20mm。
缺点是加长修光刃的长度对表面加工质量效果不大,对刀不易
圆弧刃容易对刀,半径可取R=2~5mm。
可加工高质量的超光滑表面,缺点是刀具制造复杂
2-19试述金刚石刀具的前面应选哪个晶面
选用100面,111面硬度高,而微观破损强度并不高,研磨加工困难。
选用100面的原因:
1)100面耐磨性高于110面,刀具使用寿命长
2)100面微观破损强度高于110面,产生崩刃的机会小
3)100面与有色金属之间的摩擦因数低于110晶面,使切削变形小,使加工表面的变形和残留应力小。
有利于提高表面质量。
2-20试述金刚石刀具的金刚石固定方法。
1)机械加固
2)用粉末冶金法固定
3)使用粘结或钎焊固定
2-21试述单晶金刚石刀具的研磨加工方法
有粗研和精研
粗研后的金刚石不能有大划痕、刀具切削刃不能有崩刃或其他缺陷,粗研与研磨方向、研磨速度和压力、使用的金刚石微粉的粒度等有关。
精研加工是制造精密金刚石刀具的关键工序,与磨料粒度、研磨盘质量、研磨方向、精抛这些因素有关。
2-22单晶金刚石刀具质量的好坏如何评定
1)能否加工出高质量的超光滑表面(Ra=0.005~0.02um)
2)能否有较长的切削时间保持切削刃锋锐(一般要求切削长度数百千米),切出极高质量的加工表面。
3-1何谓固结磨料加工?
何谓游离磨料加工?
它们各有何特点?
适用于什么场合?
固结磨料加工,使用固结磨具和涂覆磨具进行加工。
将磨粒或微粉与结合剂粘合在一起,形成一定的形状并具有一定强度,再采用烧结、粘接、涂覆等方法形成砂轮、砂条、油石、砂带等磨具。
固结磨具用于精密砂轮磨削、油石研磨、精密研磨、精密超精加工,涂覆磨具用于精密砂带磨削、砂带研磨。
游离磨料加工,加工时磨粒或微粉不是固结在一起,而是成游离状态,用于研磨和抛光。
3-2试述超硬磨料磨具(金刚石砂轮、立方氮化硼砂轮)的特点。
超硬磨料磨具为什么会成为精密加工和超精密加工的主要工具之一?
1)磨具在形状和尺寸上易于保持,使用寿命高,磨削精度高。
2)磨料本身磨损少,可较长时间保持切削性,修整次数少,易于保持精度。
3)磨削时,一般工件温度较低,因此可以减小内应力、裂纹和烧伤等缺陷。
精密加工和超精密加工要求能加工出质量高的表面。
金刚石和立方氮化硼硬度高、耐磨性好。
3-3在表示普通磨料磨具和超硬磨料磨具的技术性能时,有哪些技术性能的表示方法相同?
有哪些技术性能的表示方法不同?
为什么?
相同:
磨料的主要物理性能、磨料粒度、磨具强度,不同:
组织和浓度、硬度
普通磨具中磨料的含量用组织,反映磨料、结合剂、气孔三者之间体积的比例关系。
超硬磨具中磨料含量用浓度,表示每1cm3体积中所含超硬磨料重量。
普通磨具的硬度是指磨粒在外力作用下,自表面脱落的难易程度。
超硬磨具没有硬度项
3-4为什么在超硬磨料磨具的结构中一般由磨料层、过渡层和基体三个部分组成?
过渡层起什么作用?
普通磨料磨具的结构为什么与超硬磨料磨具的结构不同?
由于金刚石、立方氮化硼的价格高、具有很好的耐磨性能,用它们制造的固结磨具与普通磨料固结磨具不同,除超硬磨料层外,还有过渡层和基体。
过渡层用于连接基体和超硬磨料层,由结合剂构成,有时也可省去。
3-5涂覆磨具在制造技术上的质量关键是哪些?
粘接剂、涂覆方法
3-6试述近年来涂覆磨具在精密和超精密加工中所占的地位。
涂覆磨具是将磨料用粘接剂均匀地涂覆在纸、布或其他符合材料基底上的磨具。
应用比较广泛,产品有干磨砂布、耐水砂纸、刚纸磨片、环状砂带、卷状砂带。
3-7试述涂覆磨具制造中三种涂覆方法的特点和应用场合
1)重力落砂法,用于砂布、砂纸
2)涂覆法,用于小量生产纸质材料基底的砂带
3)静电植砂法,广泛采用。
3-8试从系统工程的角度分析精密磨削的技术关键
精密磨削是指加工精度为1~0.1um、表面粗糙度达到Ra0.2~0.025um的磨削方法,又称为小粗糙度磨削,多用于机床主轴、轴承、液压导轨、量规等的精密加工。
3-9试分析砂轮修整对精密磨削质量的影响。
砂轮修整是精密磨削的关键之一,通过砂轮修整,可以提高磨料的使用寿命,形成等高性很好的微刃。
使砂轮表面更平整,从而提高精密磨削质量。
3-10精密磨削能获得高精度和小表面粗糙度表面的主要原因何在?
精密磨削的磨粒具有微刃性和等高性,磨削后,被加工表面留下大量极微细的磨削痕迹,残留高度极小,加上无火花磨削阶段的作用,获得高精度和小表面粗糙度表面。
3-11试分析超硬磨料砂轮的各种修整方法的机理、特点和应用范围
1)车削法用单粒天然金刚石笔、聚晶金刚石笔、修整片等车削金刚石砂轮达到修整目的。
2)磨削法用普通磨料砂轮或砂块与超硬磨料砂轮对磨进行修整。
修整陶瓷、金属结合剂金刚石砂轮等各种超硬磨料砂轮
3)滚压挤压法用碳化硅、刚玉、硬质合金或钢铁等制成的修整轮,与超硬磨料砂轮在一定压力下进行自由对滚,使结合剂破裂形成容削空间,并使超硬磨粒表面崩碎形成微刃。
多用于修锐
4)喷射法气压喷砂法:
将碳化硅、刚玉磨粒从高速喷嘴喷射到传动的砂轮表面上,去除部分结合剂,使超硬磨粒突出。
液压喷砂法,用高压泵打出流量为20L/min、压力为150Pa的冷却液,进入喷嘴的漩涡室时,形成低压,从边孔中吸入碳化硅或刚玉等磨粒及空气,与冷却液形成混合液,并以高速喷嘴喷射到转动的砂轮上。
5)电加工法电解修锐法利用电化学腐蚀作用蚀除金属结合剂多用于金属结合剂砂轮的修锐
电火花修整法其原理是电火花放电加工,适用于各种金属结合剂砂轮,若在结合剂中加入石墨粉,也可用于树脂、陶瓷结合剂砂轮
6)超声波振动修整法用受激振动的簧片或超声波振动头驱动的幅板作为修整器,并在砂轮和修整器间放入混油磨料,通过游离磨料撞击砂轮的结合剂使超硬磨粒突出结合剂。
主要用于修锐
3-12试分析普通磨料砂轮和超硬磨料砂轮在修整机理上的不同。
修整是整形和修锐的总称。
普通砂轮的整机和修锐一般是合为一步进行的,而超硬磨料砂轮的整形和修锐一般是分为先后两步进行,有时,整形和修锐采用不同的方法。
3-13在超硬磨料砂轮磨削时如何选用磨削液?
由于超硬磨料砂轮组织紧密、气孔少、磨削过程中易被堵塞,故要求磨削液有良好的润滑性、冷却性、清洗性和渗透性。
金刚石砂轮磨削时常用油性液和水溶性液为磨削液,视具体情况而定,如磨削硬质合金时普通采用煤油,但不宜使用乳化液;
树脂结合剂砂轮不宜食用苏打水。
立方氮化硼砂轮磨削时采用油性液为磨削液,一般不用水溶性液,因为在高温下立方氮化硼磨粒和水会起化学反应,称水解作用,会加剧砂轮磨损。
可加极压添加剂以减弱水解作用。
3-14超精密磨削的含义是什么?
镜面磨削的含义是什么?
加工精度达到或高于0.1um,表面粗糙度小于Ra0.025um,是一种亚微米级的加工方法。
镜面磨削一般是指加工表面粗糙度达到Ra0.02~0.01um,表面光泽如镜的磨削方法。
3-15试从系统工程的角度来分析超精密磨削能达到高质量的原因。
影响超精密磨削的因素很多,各因素之间又相互关连,所以超精密磨削是一个系统工程,超精密磨削需要一个高稳定性的工艺系统,对力、热、振动、材料组织、工作环境的温度和净化等都有很高的要求,并有较强的抗击来自系统内外的各种干扰能力,有了高稳定性,才能保证加工质量的要求。
所以超精密磨削是一个高精度、高稳定性的系统。
3-16试分析超硬微粉砂轮超精密磨削的特点。
1)磨料粒度细,可同时获得极小的表面粗糙度和很高的几何尺寸和形状精度
2)加工效率高
3)需要进行在线修整
4)需要有微进给装置的超精密磨床上进行,设备价格高
3-17试比较精密砂轮磨削和精密砂带磨削的机理、特点和应用场合
精密砂轮磨削的机理:
1)微刃的微切削作用形成小粗糙度表面2)微刃的等高切削作用使加工表面残留高度极小。
3)微刃的滑挤、摩擦、抛光作用减小表面粗糙度
特点是残留高度小,表面精度高。
应用于机床主轴、轴承、液压滑阀、滚动导轨、量规等的精密加工
精密砂带磨削时弹性变形区的面积大,使磨粒承受的载荷大大减小,载荷值均匀,有减震作用。
砂带的粒度均匀、等高性好、磨粒尖刃向上,有方向性,且切削刃间隔长,切削不易堵塞,有较好的切削性
砂带磨削特点:
1)弹性磨削2)冷态磨削3)磨削效率高4)砂带制作比砂轮简单方便。
砂带可加工外圆、內圆、平面和成形表面。
磨削头架可安装在卧式车床、立式车床、龙门刨床等机床上进行加工,很强的适应性。
不仅可以加工各种金属材料,而且可加工木材、塑料、石材、水泥制品、橡胶等非金属材料以及单晶硅、陶瓷和宝石等硬脆材料。
3-18比较闭式砂带磨削和开式砂带磨削的特点和应用场合
闭式砂带磨削特点是效率高、噪声大、易发热。
可用于粗、半精和精加工
开式砂带磨削特点是磨削质量高,磨削效果好,但效果不如闭式砂带磨削,多用于精密和超精密磨削。
3-19论述接触轮外缘截面形状及其结构对砂带磨削的影响
接触轮外圆截面形状有平滑形用于细粒度砂带精磨、精密和超精密磨及研抛,填充形用于粗磨,齿形又有锯齿形用于粗磨和精磨,锯齿形用于粗磨
3-20分析接触轮外缘材料的种类及其硬度对砂带磨削的影响。
接触轮外缘材料种类很多,有钢、橡胶、胶木、帆布、充气橡胶等,硬度从硬到软,在砂带磨削的用途由重负荷磨削到轻负荷磨削,到精密抛光
3-21如何处理砂带磨削时的冷润与除尘问题?
湿磨要选择磨削液,磨削液选择要考虑加工表面粗糙度和被加工材料,考虑砂带粘结剂的种类,考虑基底材料,干磨要选用干磨剂
除尘处理:
设吸尘和集尘装置。
可用封闭罩或吸尘管等结构将磨削液、切削、磨粒等汇集于集尘箱,通过过滤回收,磨削液再用。
4-1试述精密和超精密机床的国内外发展概况
第二次世界大战前后精密机床的发展已逐渐完善成熟,主轴回转精度在1um以下,主轴振摆在0.4~0.5um,直线度可达<
1um/100mm。
20世纪50年代末期,美国首先发展了金刚石刀具超精密切削技术
20世纪80年代,超精密切削技术已应用到民用产品。
现在,美国的DTM-3和LODTM大型机床是公认水平最高的、达到当前技术最前沿的大型超精密机床。
我国虽已取得不小的成绩,但与国外相比仍有不少差距。
4-2试述我国发展超精密机床概况
20世纪60年代开始发展精密机床。
1987年北京密云机床研究所研制成功加工球面的JSC-027型超精密车床。
最大加工直径400mm。
1998年北京机床研究所制成的加工直径800mm的NAM-800型CNC超精密金刚石车床和SQUARE-200型超精密铣床,主轴回转精度达0.05um.。
现在在研究加工直径为1m以上的立式超精密机床。
4-3以美国为例,说明精密机床的发展过程
1962年,美国联合碳化物公司研制成功半球车床,是最早期的使用金刚石刀具实现超精密镜面切削的车床
1968年,发展了Moore车床,主轴回转精度0.05um
70年代,Pneumo公司生产了MSG-325型超精密车床,机床空气主轴的径向圆跳动和轴向跳动均<
=0.05um
1983年,LLL研制成功大型超精密金刚石车床DTM-3,可加工最大零件直径为2100mm
1984年,大型光学金刚石车床LODTM,研制成功
2000年,生产了五轴联动500FG超精密机床。
回转误差小于等于0.025um
4-4能代表超精密机床最高水平的是那几台超精密机床
1号机床、Moore车床、Ex-Cell-O公司的2m镜面立式车床、美国PneumoMSG-325超精密车床、DTM-3大型超精密车床、LODTM大型光学金刚石车床、Cranfield公司的OAGM2500大型超精密机床、Moore公司的500FG超精密机床、TOYOTA公司的AHN10型高效专用车削、磨削超精密车床。
4-5试述美国LLL实验室生产的DTM-3大型精密车床的主要技术性能
1)检测系统长距离测定用分辨率为2.5nm的He-Ne激光干涉仪,短距离测定用分辨率为0.625nm的差动式电容微测仪。
2)主轴和导轨主轴采用油静压径向轴承,空气静压推力轴承,主轴刚度>
500N/um,x向采用平面液体润滑导轨,z向采用平面空气静压导轨
3)导轨运动系统的驱动与控制x轴、z轴的驱动有DC电动机与静压轴承的φ50mm的摩擦驱动轮驱动,频带宽10Hz,最大送进量2.5mm/s.并有PZT(PbZrO-PbT)陶瓷压电元件驱动刀具的微位移机构(范围:
2.5um)进行误差修正。
4)恒温控制及底座在6m2空间内流体温度控制可达(20±
0.0006)℃,空气温度控制可达(20±
0.005)℃.机床底座为价5万美元的6.4m×
4.6m×
1.5m的花岗岩,膨胀系数低,对振动的衰减能力比钢高15倍
4-6试述美国LLL实验室生产的LODTM大型光学金刚石车床的主要技术性能
采用面积较大的推力轴承、7路高分辨率双频激光测量系统、使用He-Ne双频激光测量器、使用4路激光检测横梁上溜板的运动、使用3路激光检测刀架上下运动位置、使用在线测量和误差补偿以提高加工精度、发热部件用恒温水冷却,水温控制在(20±
0.0005)℃、大地基,地基周围有防振沟、用4个大空气弹簧支撑起来,有两个空气弹簧气室是连通的。
4-7试述美国Cranfield公司生产的OAGM2500大型超精密机床的必要性
三轴联动数控、x和y向导轨采用液体静压、z向的磨轴头和测量头采用空气轴承。
床身采用型钢焊接结构。
中间用人造花岗岩、精密数控驱动、采用分辨率为2.5nm的ZYGOAXIOM双频激光测量系统检测运动位置。
4-8举例说明发展高效专用多功能超精密机床的必要性
精密机床是实现精密加工的首要基础条件,发展高效专用多功能的超精密机床能促进国家的微电子和家电工业的发展。
日本研究超精密切削技术和研制超精密机床虽然起步较晚,但由于得到有关方面的重视和协同努力,发展很快,多功能和高效专用超精密机床在日本发展较好,促进了日本微电子和家电工业的发展,促进了经济的发展。
4-9为什么超精密机床大部分都采用空气轴承,它有哪些优缺点
由于超精密切削时切削力甚小,空气轴承能满足要求,故在超精密机床中得到广泛的应用。
优点:
回转精密高、高速转动时温升小热变形误差小
缺点:
刚度低、承受载荷小。
4-10空气主轴轴承有哪些常用的机构形式?
它有哪些优缺点?
1、圆柱径向轴承和端面止推空气静压轴承。
能自动调整定心。
采用多孔石墨的轴衬代替输入空气的小孔节流,效果好、使用多孔石墨在没有空气状态下轴如少量旋转,不会和轴套咬住使主轴损坏,缺点是这种多孔石墨要求组织均匀、各处透气率相同,制造技术难度大。
2、双半球空气轴承主轴。
气浮面是球面有自动调心作用,当轴承尺寸较大时,可以有较高的刚度和较大的承载能力。
3、前部用球形,后部用圆柱径向空气轴承的主轴。
一端是球形,起到径向和轴向推力轴承的作用,并有自动调心作用。
刚度和承载能力不高
4、立式空气轴承。
下止推面大于上止推面,以平衡主轴的重量,使上下止推面的空气间隙相等,处于最佳状态。
径向轴承制成圆弧面,可起到自动调心、提高精度的作用。
4-11超精密主轴有哪些驱动方式?
各自的优缺点是什么?
1、电动机通过带传动驱动机床主轴。
无极调速、减少振动。
超精密机床多数采用T形总布局,这种方式,十分不便。
2、电动机通过柔性联轴器驱动机床主轴。
主轴部件结构紧凑、无级调速、消除振动和回转误差。
主轴轴向长度较大,使整个机床的尺寸加大。
3、采用内装式同轴电动机驱动机床主轴。
消除电刷磨损对电动机的影响,回转精度高,主轴轴箱的轴向长度缩短,主轴箱成为一个独立的、很方便移动的部件。
主轴部件热变形,需要通恒温油(或水)冷却。
4-12超精密车床有哪几种总体布局?
1、十字形滑板工作台布局。
主轴箱位置固定,刀架在十字形滑板(或溜板)工作台上。
激光干涉测量系统的激光光路需要封闭结构,增加了工作台体积。
2、T形布局。
z向和x向运动相互独立,误差不累加,测量系统的安装简单,测量精度高。
3、R-θ布局。
可加工平面和各种凹凸非球曲面。
高精度的圆弧导轨制造不易,加工调整用极坐标不是直角坐标,用的不多。
4、偏心圆转角布局。
加工球面和平面时,完全不需要导轨的直线运动,故加工精度和表面质量高,机床结构简单紧凑。
5、立式结构布局。
加工工件直径较大并且重量较重。
4-13简述精密和超精密机床使用的床身和导轨材料,并说明各自的优缺点
1、优质耐磨铸铁。
工艺性好,耐