挤压与拉拔Word格式.docx
《挤压与拉拔Word格式.docx》由会员分享,可在线阅读,更多相关《挤压与拉拔Word格式.docx(39页珍藏版)》请在冰豆网上搜索。
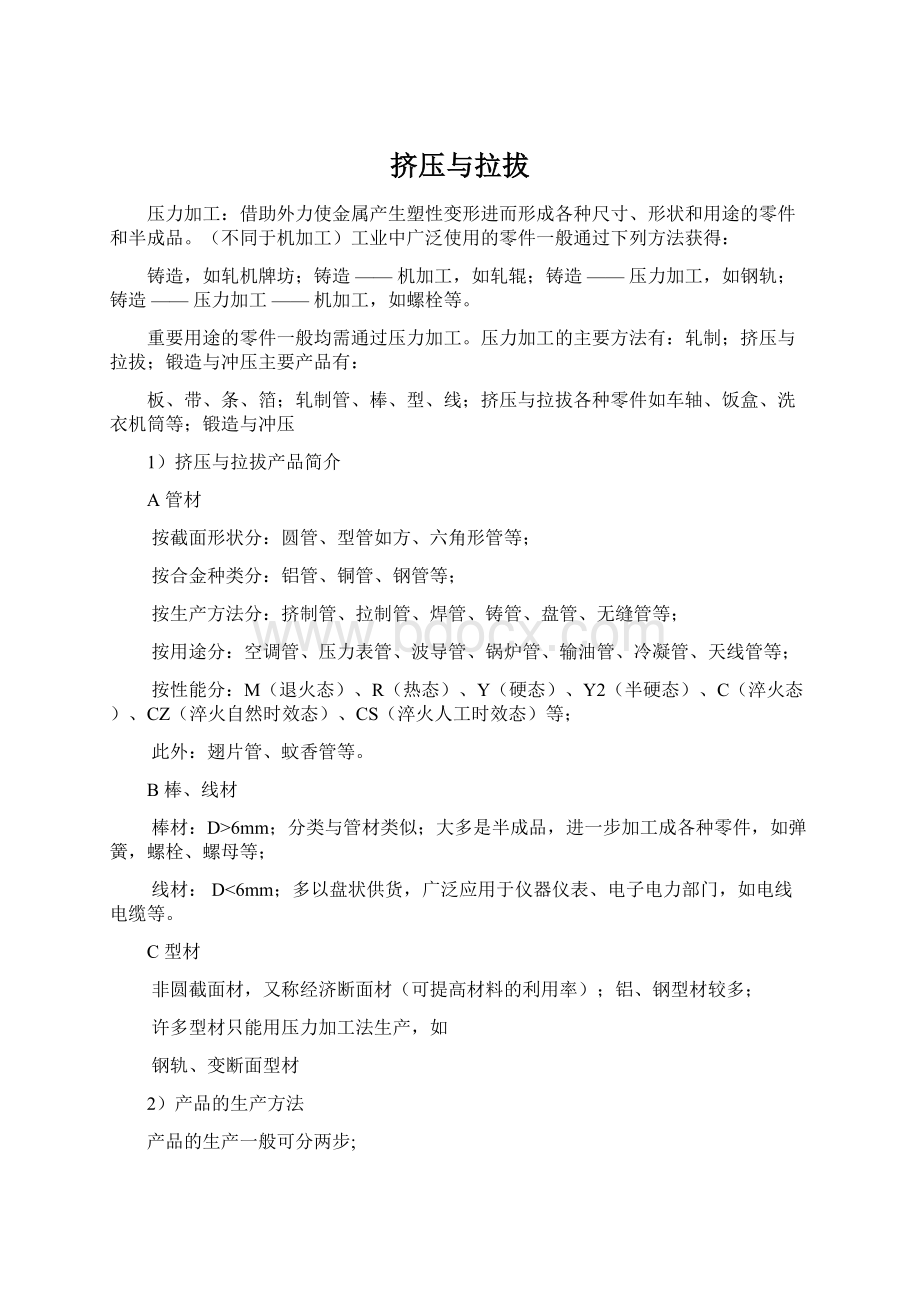
许多型材只能用压力加工法生产,如
钢轨、变断面型材
2)产品的生产方法
产品的生产一般可分两步;
坯料制取(开坯):
充分利用金属在高温时的塑性对其进行大变形量加工,如热挤、热轧、热锻。
制品的获得:
进行目的在于控制形状、尺寸精度、提高综合性能的各种冷加工,如冷轧、拉拔、冲压。
目前研究:
近终形成形技术、短流程生产技术
挤压:
生产灵活、产品质量好,适用于品种、规格多、产量小(有色金属)的场合,但成本高、成品率低;
斜轧穿孔:
生产率、成品率高;
成本低;
但制品形状尺寸精度差;
尺寸规格受限制;
多用于产量大的钢坯生产,有色金属厂基本没有;
铸造:
产品的尺寸规格少、质量差、性能低;
主要用于生产大尺寸、性能要求不高的产品如下水管;
轧管:
道次变形量大,几何损失少,适于难变形合金,能缩短工艺流程,也是提供长管坯的主要方法(使盘管生产得以实现),但形状、尺寸精度差;
拉拔:
是获得精确尺寸、优质表面和性能的主要方法;
焊管:
效率高、成本低,但性能、质量差。
先进工艺:
挤压——轧管——(圆盘)拉拔——联合拉拔
水平连铸管坯——行星轧制——拉拔
适用于多品种、多规格、复杂断面;
连铸连轧:
生产率、成品率高、能耗低(利用余热直接轧制);
但品种、规格单一;
型轧:
适于单一品种、大批量产品的生产。
发展方向:
中小棒材:
挤压(轧制)圆盘坯料后联合拉拔出成品;
多模、高速方向发展。
2基本概念
挤压:
对放在容器(挤压筒)内的坯料一端施以压力,使之从特定的空隙(模孔)中流出而成型的塑性加工方法。
欲完成挤压需有:
1)产生动力的装置:
挤压机
2)传递动力、容纳坯料控制制品尺寸和形状的工具:
轴、筒、模、穿孔针、垫片、模座、锁键
过程:
清理筒、装模、落锁键、送锭、放垫片、挤压、抬锁键、切压余、冷却(润滑)工具、重复下一次。
3基本方法
根据变形温度分:
热挤压、冷挤压和温挤压;
根据变形特征分:
正(向)挤压、反(向)挤压、连续挤压等。
方法有很多,但最基本的方法有以下两种:
1)正向挤压
制品流出的方向与挤压杆的运动方向相同。
特点:
1)存在较大的外摩擦(高温、高压),导致能耗大、变形不均匀(组织性能不均),制品表面质量好;
2)操作方便、适用范围广,是目前最广泛应用的方法。
2)反向挤压
制品流出的方向与挤压杆的运动方向相反。
1)变形局限在模孔附近,大部分坯料与挤压筒间没有相对运动,因此外摩擦小,能耗低、变形均匀(组织性能均匀);
2)操作不方便、制品的尺寸范围小;
3)制品表面质量差。
此外还有:
卧式挤压、立式挤压等。
注:
1)冷、热变形应以合金的再结晶温度界定,如Sn、Pb在室温变形也无硬化,属热变形;
2)冷、热挤压是挤压的两大分支,冶金工业中主要应用热挤压,常称挤压;
机械工业主要应用冷挤压。
4基本特点
1)优点
A可最大限度提高材料的变形能力,因此可加工脆性材料;
一次可进行大变形
B可提高材料的焊合性,因此可生产复合材料;
粉末挤压;
舌模挤压
C材料与工具的密合性高,因此可生产复杂断面制品;
选择坯料自由度大
D生产灵活(只需更换筒、模即可生产不同的制品),制品性能高。
2)缺点
A工具消耗大,产品成本高
工作条件:
高温、高压、高摩擦,工具消耗大,原料成本高,占制品成本35%以上
B生产率低
挤压速度低、辅助工序多
C成品率低
固有的几何损失多(压余、实心头、切头尾),不能通过增大锭重来减少
D制品组织性能不均匀。
二、挤压时金属流动的规律
挤压时金属的流动规律,即筒内各部分金属体积的相互转移规律对制品的组织、性能、表面质量以及工具设计有重要影响。
因此研究挤压时金属的流动规律以及影响因素,可改善挤压过程、提高制品的性能和质量。
挤压时金属的流动规律十分复杂,且随挤压方法以及工艺条件的变化而变化,现以生产中广泛使用的简单挤压(单孔模正挤圆棒)过程为例进行分析。
1、简单挤压时金属流动的规律
按流动特性和挤压力的变化规律,可将挤压过程分为:
填充挤压阶段:
金属在挤压杆(力)的作用下首先充满挤压筒和模孔(金属主要径向流动),挤压力急剧升高;
基本挤压阶段:
又称层流挤压阶段,金属不发生紊乱流动,即锭外(内)层金属出模后仍在外(内)层,挤压力稳中有降;
终了挤压阶段:
又称紊流挤压阶段,金属发生紊乱流动,即外层进入内层,挤压力上升。
1)填充挤压阶段
挤压时,为便于将锭坯放入筒中,常使锭坯的外径小于筒内径1-15mm,因此在挤压力的作用下,锭坯首先径向流动充满挤压筒,同时有少量金属流入模孔。
杆、垫片、锭坯开始接触到锭坯充满挤压筒的阶段称为填充挤压阶段。
A必要性
a操作要求;
b实心锭挤管,否则穿孔针弯曲导致管材偏心;
c制品要求横向性能,如航空用型材必须有一定的镦粗变形(25-30%)
B应力分析
作用于坯料上的外力:
挤压力P;
模端面反力N;
摩擦力T
应力状态类似于自由体镦粗,为三向压应力,即L、
R、θ,且均可看成是主应力,但由于挤压模孔的存在,导致分布不均匀,体现在:
径向上:
中心小,两边大,差异由前向后逐渐减小。
轴向上:
对着模孔部分:
由前向后增大
对着模壁部分:
由前向后减小
C变形(应变)分析
应变状态:
一向压缩(轴向)、二向延伸(径向、周向)
变形过程:
开始出鼓形,断面首先充满挤压筒;
继续加
力,断面充满挤压筒;
最后,断面充满挤
压筒。
D坯料端面变形分析
填充挤压时,部分金属会流入模孔,但此部分金属并不是发生塑性变形后流入模孔的,而是被剪出的,其组织是铸态组织,必须切下(棒材头)。
原因:
轴向应力L在径向上的分布是不均匀的,且在模孔周围最大,这种应力突变会产生很大的切应力,当此切应力达到材料的剪切极限时,对着模孔部分的金属便沿模孔被剪出。
E填充阶段应注意的问题
a尽量减小变形量(锭坯与挤压筒的间隙),否则易造成:
制品性能不均匀;
棒材头大,即切头大;
低塑性材料易出现表面裂纹。
此阶段的变形量用填充挤压系数表征,定义填充挤压系数为:
b锭坯的长度与直径比小于3-4,即L/D<
3-4。
否则变形不均出现鼓形,甚至失稳弯曲,导致封闭在模、筒交界处的空气压入表面微裂纹中,出模后若焊合则形成气泡,若未焊合则出现起皮缺陷。
c锭坯梯温加热,即坯料获得长度上的原始温度梯度,变形抗力低的高温端靠近模孔,填充挤压时坯料由前向后依次变形,从而将空气排除。
2)基本挤压阶段
金属从模孔中流出到锭坯长度等于变形区高度的阶段,又称平流挤压阶段。
A挤压比
挤压时的变形量常用挤压比表征,定义挤压比为:
挤压比的大小由被挤压材料的塑性决定,可查表。
挤压比λ的选择与合金种类、挤压方法、产品性能、挤压机能力、挤压筒内径及锭坯长度等因素有关。
如果λ值选用过大,挤压机会因挤压力过大而发生“闷车”,使挤压过程不能正常进行,甚至损坏工具,影响生产率。
如果λ值选用过小,挤压设备的能力不能得到充分利用,也不利于获得组织和性能均匀的制品。
挤压比λ一般应满足下列要求:
一次挤压的棒、型材≥8~12
轧制、拉拔、锻造用毛坯≥5
二次挤压用毛坯不限。
外力:
挤压力P;
筒、模的反力N;
筒、模、垫片与坯料间的摩擦力T。
应力状态:
为三向压应力,即L、r、θ,且可近似看成是轴对称,即r=θ。
实际上,在区有:
轴向应力分布规律:
轴向上:
由前向后逐渐增大;
径向上:
由中心向边部逐渐增大。
二向压缩(径向、周向)、一向延伸(轴向)
变形规律(应变分布):
可由此阶段坐标网格变化分析。
a纵向网格在进、出模孔发生方向相反的两次弯曲,弯曲程度由内向外逐渐增大,说明变形是不均匀的。
分别连接两次弯曲的弯折点可得两个曲面,一般将此两曲面与模孔锥面或死区界面所围成的区域叫变形区压缩锥,或简称变形区。
b在变形区中,横向网格的中心朝前,且越接近模孔弯曲越大,说明中心质点的流速大于外层质点的流速,且差异越接近模孔越大。
这是因为:
外摩擦影响:
外层大,中心小;
断面温度分布:
一般外层低,中心高;
模孔的存在使中心质点的流动阻力小于外层质点。
c制品的网格也有畸变,表现在:
①横向线的弯曲程度以及弯曲顶点的间距由前向后逐渐增大,说明变形(延伸变形和剪切变形)由前向后逐渐增大。
②中心网格变成近似矩形,外层网格变成平行四边形,说明外层质点不仅承受了纵向延伸,还承受了附加的剪切变形,且剪切变形由中心向外层逐渐增大。
变形规律总结:
后端大,前端小;
变形差异:
由前向后逐渐增加;
流动速度:
中心大,外层小;
总体看流动平稳(层流)。
D挤压筒内金属分区
①前端难变形区又称死区,位于筒、模交界处的环形区域,是由于筒、模的摩擦和冷却,使此部分金属不易变形形成的。
死区在基本挤压阶段基本不参与流动。
死区的顶部能阻碍锭坯的表面缺陷进入变形区而流入制品,因此能提高制品的表面质量。
影响死区大小的因素:
模角、摩擦、挤压温度等,随这些参数的增大,死区增大,如平模挤压时死区大。
②后端难变形区位于垫片端面附近,是由于筒、垫片的摩擦和冷却,使此部分金属不易变形形成的,在基本挤压末期,此区域逐渐变成一小楔形区。
③在变形区中,有一个剧烈滑移区,处于死区和快速流动区之间。
变形越不均匀,此区越大,因此随挤压过程的进行,此区不断扩大。
剧烈滑移会导致晶粒过渡破碎,易导致制品表面出现微裂纹和组织粗大(粗晶环),导致制品性能下降。
3)终了挤压阶段:
筒内锭坯长度减小到接近变形区高度时的流动阶段。
主要特征:
A挤压力升高;
(死区参与流动、温度低)
B金属径向流速增加,金属回流(紊流)(维持体积不变规律)。
实际生产中,在此阶段停止挤压(留压余)。
2、正挤管材时金属流动的特点
1)金属流动比挤压棒材时均匀。
主要是由于穿孔针的摩擦和冷却,使内部质点的流动阻力增大;
2)穿孔时强烈的内摩擦易导致制品内表面出现裂纹,因此一般润滑穿孔针。
3、反挤压时金属流动的特点
1)变形区小且集中在模孔附近,金属流动均匀;
2)死区小,制品表面质量差;
3)挤压力小且在基本挤压阶段不变。
4、影响挤压时金属流动规律的因素
1)摩擦与润滑挤压时的摩擦有:
筒、模、垫片穿孔针与坯料间的摩擦,一般主要指筒、坯料间的摩擦。
润滑时摩擦力小,金属流动均匀;
2)金属强度强度高流动均匀。
(强度高,摩擦小;
变形热大,温度分布均匀);
3)温度有坯料温度和工具预热温度。
坯料温度高,流动不均匀。
(温度高,强度低,变形不均匀;
温度高,出炉后冷却使锭温度梯度大,变形不均匀;
一般温度高导热性能下降,锭温度梯度大,变形不均匀);
工具预热温度高,流动均匀。
(使锭温度分布均匀)
4)工具结构与形状指与坯料接触的筒、模、垫片和穿孔针,筒、穿孔针的结构和形状基本不变,为圆柱形,故只分析模和垫片。
模主要有平模(ɑ=90
)和锥模(ɑ<
90),模角越大,流动越不均匀,平模挤压时流动最不均匀(死区大,摩擦大;
弯曲(剪切)变形大)。
垫片主要有平、凸、凹三种,凹垫片流动均匀,但仅在挤压初期有作用,同时由于加工、切压余困难,实际中除了在半连续挤压中外,还是采用平垫片。
5)变形程度及速度
随变形程度的增大,外层质点向中心流动的阻力增加,导致坯料中心质点与外层质点的流速差增加,变形不均匀。
但当变形程度增加到一定程度时,剪切变形深入到内部,变形向均匀方向转化。
实践表明:
当变形程度为60%时,变形最不均匀;
当变形程度>
85-90%时,变形均匀,性能均匀;
当变形程度<
6%时,变形较均匀,但性能低。
挤压速度:
三个方面,流动不均匀、加工硬化、变形热
三、挤制品的组织、性能和主要缺陷
1、挤制品的组织
1)挤制品组织的不均匀性
A特征一般情况,前端、中心晶粒粗大,后端、边部晶粒细小。
B原因
a变形特点决定的挤压时变形的分布规律是前端、中心变形小,后端、外层变形大,导致晶粒的破碎程度由前向后、由里向外逐渐增大;
b温度分布规律决定的坯料的温度分布规律一般是前端、中心高,后端、外层低,即前端、中心在高温下变形,而后端、外层在低温下变形;
注:
挤压软铝合金时,坯料、筒间温差不大,热量不易散失,温度分布规律与上述相反。
c合金在相变温度下变形,会引起组织不均。
如HPb59-1,在720℃以上为均匀的相,若在挤压过程中温度低于720℃,则会析出相,导致组织不均。
2)挤制品的层状组织
A特征断口呈现出与木质折断后相似的形貌,分层的断口凸凹不平并带有裂纹;
分层面近似平行于轴线;
一般出现在前端。
B原因
a根本原因是坯料中存在有大量的气孔、缩孔或在晶界上分布有未溶解的第二相或杂质等,在挤压时被拉长,从而出现层状组织;
b与变形特点有关挤压初期流动平稳,形成的杂质膜不易破坏,后期变形逐渐紊乱,杂质膜破坏,层状组织不明显。
c与铸造条件有关冷却速度大,柱状晶明显,缺陷、夹杂物易集中分布,层状组织明显;
反之不明显。
d与合金成分有关出现层状组织的合金不多,在铜合金中主要是含Al的青铜QAl10-3-1.5和QAl10-4-4以及含Pb的黄铜HPb59-1;
铝合金中主要是LD2和LD4,而LY11、LY12、LC4中较少、主要是由于这些合金中易出现氧化物夹杂。
C对性能的影响对纵向性能影响不大,使横向性能显著下降。
有层状组织的衬套,承受的内压降低30%。
D防止措施
a主要从铸锭着手,如降低冷却强度以缩小柱状晶区,分散杂质;
b增大变形程度,以增加紊流区,进而破坏杂质膜。
3)挤制品的粗晶组织
某些合金在挤压时或在随后的热处理时,会形成异常粗大的晶粒组织,这种组织称为粗晶粒或粗晶组织。
易出现粗晶组织的主要是某些铝合金,如纯铝、软铝在挤压后即出现;
而锻铝、硬铝在挤压后的淬火时出现。
A分布规律由前端外层向后端外层逐渐扩大,严重时可扩展至整个断面,象带锥度的圆管,又称粗晶环。
B形成机理出现粗晶组织的根本原因是在挤压时或在挤压后的淬火时发生了集聚再结晶,因此凡是能降低再结晶温度、促进再结晶过程的因素均易导致粗晶环。
a与变形特点有关
对于纯铝、软铝合金而言,挤压速度快,变形热大,制品出模后温度应较高,因此外层、后端优先发生再结晶和集聚再结晶,形成粗晶组织。
b与合金成分有关
易出现粗晶环的合金中均含有Mn、Cr等过渡族元素,这些元素的特点是:
溶入基体中能提高再结晶温度,以第二相如MnAl6、CrAl7在晶界析出时能阻碍晶粒长大。
挤压时,由于中心质点流动速度快,导致边部产生拉副应力,促进Mn、Cr元素的析出,降低再结晶温度,但因析出的第二相能阻碍晶粒长大,因此含这些元素的合金在挤压后是一次再结晶组织,不出现粗晶组织。
挤压后淬火时,为了得到均匀的单相固溶体组织,加热温度高、时间长,在这种条件下,析出的第二相重新溶入基体,阻碍晶粒长大的作用消失,因此一次再结晶后的晶粒吞并周围的晶粒并迅速长大,形成粗晶组织。
1)有关粗晶形成机理还有待进一步研究;
2)粗晶组织降低性能,应尽量避免,生产中应检查。
2、挤制品的性能
1)挤制品性能的不均性
a制品前端、内部强度低、塑性高;
后端、外层相反;
(纯铝、软铝分布规律相反)
b各向异性,纵向性能高于横向性能;
c性能差异随变形程度不同而不同。
当变形程度<
20%时,性能均匀但较低;
当变形程度为60%时,性能差异最大;
当变形程度>
80%时,性能均匀且较高。
因此挤压时变形程度应>
80%。
2)挤压效应
某些工业用铝合金,在经过同一热处理后(淬火、时效),挤制品与其它压力加工制品相比,在纵向上具有较高的强度和较低的塑性,这一现象叫挤压效应。
易出现挤压效应的合金:
锻铝、硬铝
A特征出现在制品内部(外部因粗晶环而消失);
组织是未再结晶的加工组织。
B形成机理
a与形成的织构有关挤压时,金属处于两压一拉的变形状态且流动平稳,晶粒皆沿挤压方向被拉长,形成较强的纵向织构,即大多数晶粒的某一晶向(111)均按挤压方向取向,导致纵向强度升高。
b与合金成分有关出现挤压效应的合金也都含Mn、Cr元素,由于挤压时中心质点流速快,因此内部产生压副应力,不利于Mn、Cr元素的析出,使再结晶温度升高,可认为挤压后制品内部是过饱和的、未再结晶的加工组织。
在挤压后的淬火加热时,内部过饱和的固溶体继续析出,析出的第二相弥散分布在晶界上,阻碍晶粒长大(阻碍再结晶过程),因此热处理后,制品的内部仍保留着未再结晶的加工组织,导致强度升高。
c与强烈的三向压应力状态有关挤压时强烈的三向压应力状态使晶界、晶内破坏较少,有利于缺陷的愈合,使强度升高。
注要得到类似的强化效应,关键不在于采用什么加工方法,而在于通过什么途径使合金在热变形以及随后的热处理过程中,仍然保留有未再结晶的加工组织。
粗晶与挤压效应总结:
均出现在含Mn、Cr元素的铝合金中;
粗晶出现在外层,
挤压效应出现在内层;
粗晶产生的根本原因是发生了集聚再结晶;
挤压效应产生的根本原因是未发生再结晶。
形成机理:
铸造时冷速快导致铸锭是过饱和组织;
3、挤制品的主要缺陷
1)挤制品裂纹
A特征出现在制品表面,外形大致相同,呈周期性分布,又称周期性裂纹。
裂纹一般出现在高温塑性差的合金中,如锡磷青铜、锡黄铜、硬铝等合金。
B形成原因
根本原因是变形不均所产生的轴向拉副应力作用结果
挤压时中心质点流速快,中心产生轴向拉副应力,当此力与基本应力叠加后的工作应力达到合金的强度极限时,就会产生裂纹。
由于在表面的拉副应力最大,故裂纹首先在表面产生。
裂纹的产生一方面在裂纹的尖角处产生应力集中,促进裂纹的扩展,另一方面也消除了此局部的拉副应力,因此当裂纹扩展到一定深度后不再向内扩展。
随着变形的进行,合金又会由于拉副应力的产生而形成裂纹,因而裂纹呈周期性分布。
C消除措施
a使变形均匀,消除轴向拉副应力,如润滑等;
b提高基本应力,如施加反压力、增加定径带长度、增加变形程度等(以能耗多为代价);
c保证合金的高温强度,制订合理的温度-速度规程,使合金处于高温塑性好的区域,如低温快速、高温慢速、等温挤压等。
2)挤压缩尾
又称挤压缩孔,是出现在制品尾部的一种缺陷,是指挤压过程中,坯料表面的缺陷(氧化物、偏析瘤、杂质、油污等)进入制品内部或出现在制品的表明层,而形成的一种漏斗状、环状、半环状的疏松组织缺陷。
缩尾破坏组织的连续性和致密性,降低制品性能。
缩尾依其存在的部位可分为以下三种:
环形缩尾
中心缩尾
皮下缩尾
A环形缩尾
a特征分布在制品尾部中间部位,呈完整的圆环或部分圆环,一般在200-1000mm内。
b形成原因挤压末期发生紊乱流动,即外层金属发生回流,由于后端难变形区的存在,回流的金属沿难变形区界面流动,分布在制品的中间层。
由于外层金属含有氧化皮、油污等脏物,流入制品内部与基体金属不能焊合,形成环形缩尾。
环形缩尾是最常见的缩尾。
B中心缩尾
a特征分布在制品尾部中心部位,短而粗,呈漏斗状,一般留在压余内,只有在大规格制品、压余又薄时才能观察到。
b形成原因随着挤压过程的进行,后端难变形区逐渐变成一小楔形,回流的金属沿此界面流动,分布在制品的中心。
由于外层金属含有氧化皮、油污等脏物,流入制品内部与基体金属不能焊合,形成中心缩尾。
当回流的外层金属也不能补充中心金属的短缺时,形成缩孔。
C皮下缩尾
a特征分布在制品尾部周边部位,没有规律性。
b形成原因挤压末期,金属温降大、塑性低,导致剧烈滑移区与死区界面发生断裂(内摩擦转变为外摩擦),含有氧化皮、油污等脏物的外层金属沿此界面流出,同时,死区也不是完全的刚体,也会沿模孔一点一点的流出,包覆在由死区界面流出的脏金属上面,形成皮下缩尾。
D防止措施
a使挤压不处于末期如留压余(压余长度一般为锭径的10-30%)、半连续挤压;
b使变形均匀,金属不产生回流,主要措施是制订合理的工艺参数,如润滑、锥模挤压、低温挤压、提高工具表面光洁度等;
c提高坯料表面质量如机加工、加热时尽量减少氧化、热剥皮、脱皮挤压等。
四、挤压力
挤压力:
轴通过垫片作用在坯料上使之从模孔中流出的力,是指曲线上的最大力。
挤压力是制订工艺、选择设备、校核工具强度的依据。
影响因素:
有很多,如摩擦、金属性质、挤压温度、变形程度、模角等。
模角逐渐增大过程中,一方面弯曲变形增大,导致挤压力升高;
另一方面摩擦面减小,导致挤压力减小,结果存在一最佳模角,使挤压力最小。
挤压时最佳模角为45-60°
。
平模挤压时形成死区,模角取60°
五、挤压工具
1、挤压筒
作用:
容纳金属。
1)结构
一般由二层或三层过盈热装组成,分别称为内套、中套和外套,目的是:
a使筒壁中的应力分布均匀(降低筒壁中的应力峰值);
b筒磨损后只需更换内套,不必更换整个挤压筒,可节约材料。
各套之间的配合可以是圆柱形的(a)、带一定锥度的(b、c)或带止口的(d)。
圆柱形衬加工容易,但更换困难;
锥形衬加工困难,但更换容易;
带止口衬与圆柱形衬基本相同,只是热装时依靠止口自动找准。
内套两端面均做成锥面,有助于挤压时顺利将坯料、垫片推入挤压筒,更重要的是起定心作用,即使模子在模座靠近筒内衬套锥面后,能准确地位于挤压中心线上,因此,这个锥面又叫定心锥。
2)预热
目的:
a减