数控技术专业毕业论文车床手柄座加工工艺及关键工序工装设计.docx
《数控技术专业毕业论文车床手柄座加工工艺及关键工序工装设计.docx》由会员分享,可在线阅读,更多相关《数控技术专业毕业论文车床手柄座加工工艺及关键工序工装设计.docx(20页珍藏版)》请在冰豆网上搜索。
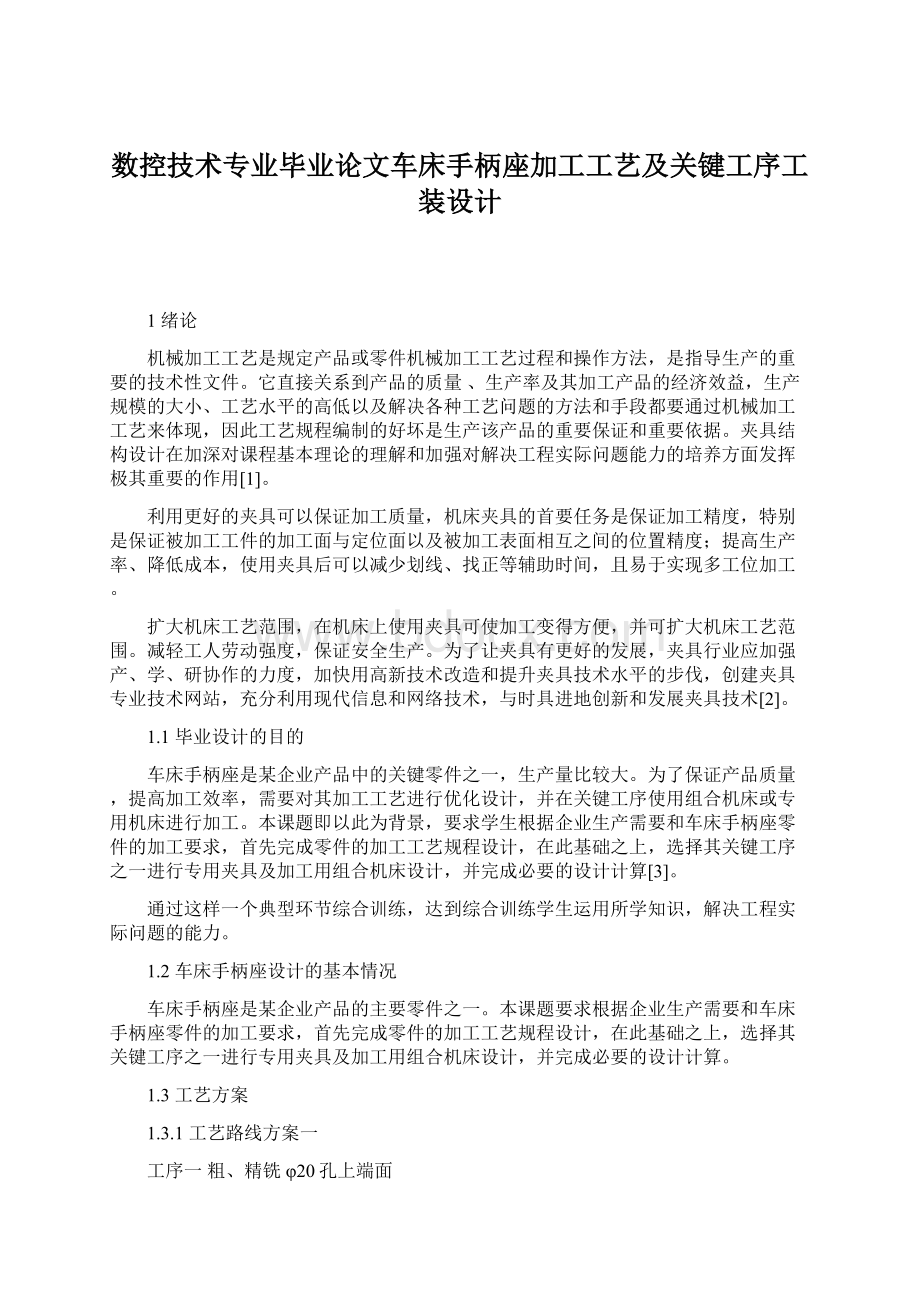
数控技术专业毕业论文车床手柄座加工工艺及关键工序工装设计
1绪论
机械加工工艺是规定产品或零件机械加工工艺过程和操作方法,是指导生产的重要的技术性文件。
它直接关系到产品的质量、生产率及其加工产品的经济效益,生产规模的大小、工艺水平的高低以及解决各种工艺问题的方法和手段都要通过机械加工工艺来体现,因此工艺规程编制的好坏是生产该产品的重要保证和重要依据。
夹具结构设计在加深对课程基本理论的理解和加强对解决工程实际问题能力的培养方面发挥极其重要的作用[1]。
利用更好的夹具可以保证加工质量,机床夹具的首要任务是保证加工精度,特别是保证被加工工件的加工面与定位面以及被加工表面相互之间的位置精度;提高生产率、降低成本,使用夹具后可以减少划线、找正等辅助时间,且易于实现多工位加工。
扩大机床工艺范围,在机床上使用夹具可使加工变得方便,并可扩大机床工艺范围。
减轻工人劳动强度,保证安全生产。
为了让夹具有更好的发展,夹具行业应加强产、学、研协作的力度,加快用高新技术改造和提升夹具技术水平的步伐,创建夹具专业技术网站,充分利用现代信息和网络技术,与时具进地创新和发展夹具技术[2]。
1.1毕业设计的目的
车床手柄座是某企业产品中的关键零件之一,生产量比较大。
为了保证产品质量,提高加工效率,需要对其加工工艺进行优化设计,并在关键工序使用组合机床或专用机床进行加工。
本课题即以此为背景,要求学生根据企业生产需要和车床手柄座零件的加工要求,首先完成零件的加工工艺规程设计,在此基础之上,选择其关键工序之一进行专用夹具及加工用组合机床设计,并完成必要的设计计算[3]。
通过这样一个典型环节综合训练,达到综合训练学生运用所学知识,解决工程实际问题的能力。
1.2车床手柄座设计的基本情况
车床手柄座是某企业产品的主要零件之一。
本课题要求根据企业生产需要和车床手柄座零件的加工要求,首先完成零件的加工工艺规程设计,在此基础之上,选择其关键工序之一进行专用夹具及加工用组合机床设计,并完成必要的设计计算。
1.3工艺方案
1.3.1工艺路线方案一
工序一粗、精铣φ20孔上端面
工序二钻、扩、铰、精铰φ20、φ50孔
工序三粗、精铣φ50孔上端面
工序四粗、精铣φ50、φ20孔下端面
工序五切断
工序六钻φ4孔(装配时钻铰锥孔)
工序七钻一个φ4孔,攻M6螺纹
工序八铣47°凸台
工序九检查
上面工序加工效率较高,但同时钻三个孔,对设备有一定要求。
且看另一个方案。
1.3.2工艺路线方案二
工序一粗、精铣φ20孔上端面
工序二粗、精铣φ20孔下端面
工序三钻、扩、铰、精铰φ20孔
工序四钻、扩、铰、精铰φ50孔
工序五粗、精铣φ50孔上端面
工序六粗、精铣φ50孔下端面
工序七切断
工序八钻φ4孔(装配时钻铰锥孔)
工序九钻一个φ4孔,攻M6螺纹
工序十铣47°凸台
工序十一检查
上面工序可以适合大多数生产,但效率较低。
综合考虑以上步骤,得到我的工艺路线。
1.3.3方案一与方案二比较
虽然工序仍然是十一步,但是效率大大提高了。
工序一和工序二比起工艺路线方案二快了一倍(实际铣削只有两次,而且刀具不用调整)。
多次加工φ50、φ20孔是精度要求所致。
1.3.4工艺路线方案三
工序一铣φ45mm凸台端面
工序二钻,扩,铰φ25H8mm内孔
工序三钻,粗铰,精铰φ10H7mm孔
工序四钻,铰φ13mm孔
工序五钻φ8.5mm底孔
工序六钻,粗铰,精铰φ14H7mm孔
工序七钻φ5mm圆锥孔
工序八钻槽底通孔φ5.5mm
工序九拉键槽6H9mm
工序十钻底孔,攻螺纹M10mm
工序十一检查。
2零件分析
2.1零件的工艺分析
粗基准的选择。
对于零件而言,尽可能选择不加工表面为粗基准。
而对有若干个不加工表面的工件,则应以与加工表面要求相对位置精度较高的不加工表面作粗基准。
根据这个基准选择原则,现选取φ20孔的不加工外轮廓表面作为粗基准,利用一组共两块V形块支承这两个φ32作主要定位面,限制5个自由度,再以一个销钉限制最后1个自由度,达到完全定位,然后进行铣削。
精基准的选择。
主要应该考虑基准重合的问题。
当设计基准与工序基准不重合时,应该进行尺寸换算,这在以后还要专门计算,此处不再重复。
2.2零件的加工工序
(1)铣,半精铣φ45mm凸台端面
(2)铣,半精铣大端面
(3)钻,扩,铰φ25H8mm内孔
(4)钻,粗铰,精铰φ10H7mm孔
(5)铣槽mm
(6)钻粗铰精铰φ14H7mm孔
(7)钻底孔,攻螺纹M10mm
(8)钻φ5mm圆锥孔
(9)拉键槽φ6H9mm
(10)钻槽底通孔φ5.5mm
2.3粗加工零件时切削用量的选择原则
粗加工时加工精度与表面粗糙度要求不高,毛坯切削余量较大。
因此,选择粗加工的切削用量时,要尽可能保证较高的单位时间金属切削量(金属切除率)及必要的刀具耐用度,以提高生产效率和降低加工成本[4]。
金属切除率可以用下式计算:
Zw=V.f.ap.1000(2.1)
式中:
Zw单位时间内的金属切除量(mm/s)
V切削速度(m/s)
f进给量(mm/r)
ap切削深度(mm)
提高切削速度、增大进给量和切削深度,都能提高金属切除率。
但是,在这三个因素中,影响刀具耐用度最大的是切削速度,其次是进给量,影响最小的是切削深度。
所以粗加工切削用量的选择原则是:
首先考虑选择一个尽可能大的切削深度(ap),其次选择一个较大的进给量度f,最后确定一个合适的切削速度V。
选用较大的ap和f以后,刀具耐用度显然也会下降,但要比V对刀具耐用度的影响小得多,因此,使V、f、ap的乘积尽可能大,从而保证较高的金属切除率。
此外,增大ap可使走刀次数减少,增大f又有利于断屑。
因此,根据以上原则选择粗加工切削用量对提高生产效率,减少刀具消耗,降低加工成本是比较有利的[5]。
2.3.1切削深度的选择
粗加工时切削深度应根据工件的加工余量和由机床、夹具、刀具和工件组成的工艺系统的刚性来确定。
在保留半精加工、精加工必要余量的前提下,应当尽量将粗加工余量一次切除。
只有当总加工余量很大,一次不能切完时,应考虑分多次走刀[6]。
2.3.2进给量的选择
粗加工时限制进给量提高的因素主要是切削力。
因此,进给量应根据工艺系统的刚性和强度来确定。
选择进给量时应考虑到机床进给机构的强度、刀杆尺寸、刀片厚度、工件的直径和长度等。
在工艺系统的刚性和强度好的情况下,可选用大一些的进给量;在刚性和强度较差的情况下,应适当减小进给量[7]。
2.3.3切削速度的选择
粗加工时,切削速度主要受刀具耐用度和机床功率的限制。
切削深度、进给量和切削速度三者决定了切削功率,在确定切削速度时必须考虑到机床的许用功率。
如超过了机床的许用功率,则应适当降低切削速度[8]。
2.4精加工零件时切削用量的选择原则
精加工时加工精度和表面质量要求较粗加工高,加工余量小且均匀。
因此,选择精加工的切削用量时应先考虑如何保证加工质量,并在此基础上尽量提高生产效率。
2.4.1切削深度的选择
精加工时的切削深度应根据粗加工留下的余量确定。
通常希望精加工余量不要留得太大,否则,当背吃刀量较大时,切削力显著增加,影响加工质量[9]。
2.4.2进给量的选择
精加工时限制进给量提高的主要因素是表面粗糙度。
进给量增大时,虽有利于断屑,但残留面积高度增大,切削力增大,表面质量下降。
2.4.3切削速度的选择
切削速度提高时,切削变形减小,切削力有所下降,而且不会产生积屑瘤和鳞刺。
一般选用切削性能高的刀具材料和合理的几何参数,尽可能提高切削速度。
只有当切削速度受到工艺条件限制而不能提高时,才选用低速,以避开积屑瘤产生的范围。
由此可见,精加工时选用较小的背吃刀量ap和进给量f,并在保证合理刀具耐用度的前提下,选取尽可能高的切削速度V,以保证加工精度和表面质量,同时满足生产率的要求[10]。
3工艺规程设计
3.1制定工艺路线
制定工艺路线得出发点,应当是使零件的几何形状、尺寸精度及位置精度等技术要求能得到合理的保证,在生产纲领已确定的情况下,可以考虑采用万能性机床配以专用工卡具,并尽量使工序集中来提高生产率。
除此之外,还应当考虑经济效果,以便使生产成本尽量下降[11]。
3.2机床夹具设计的作用及要求
夹具是卡紧工件用的。
比如机床加工时,主轴有几千转的转速,工件必须要固定好,否则工件飞出伤人后果严重。
卡具设计要合理,即卡紧可靠,又要定位准确,较少误差,并保护好已加工好的表面。
才能保证工件质量。
夹具是机械加工不可缺少的部件,在机床技术向高速、高效、精密、复合、智能、环保方向发展的带动下,夹具技术正朝着高精、高效、模块、组合、通用、经济方向发展。
为保证工件的加工要求,必须使工件在机床上处于准确的位置,夹具就是用来实现这一要求的[12]。
3.3基本工序的设计
3.3.1工序Ⅰ切削用量及基本工时的确定
(1)铣Φ45端面
选择铣刀半径为25mm,齿数Z=6(见《工艺手册》表3.1-27)
mm/z(3.1)
mm,min(《切削》表3.7和《切削》表3.8)
m/min(《切削》表3.9)
r/m
按机床选取r/min
实际切削速度m/min(3.2)
mm/min(3.3)
铣床工作台进给量:
mm/min
基本工时:
min
(2)半精铣Φ45端面
加工余量为Z=1mm
切削速度为m/min
r/min
选用主轴为r/min
mm/min(3.4)
基本工时:
min
3.3.2工序Ⅱ切削用量及基本工时的确定
(1)粗铣大端面
进行两次铣削,第一次Z=2mm,第二次Z=1mm
m/min
r/min(3.5)
选用主轴为r/min
实际切削速度:
m/min(3.6)
工作台进给量:
mm/min
基本工时:
min
(2)半精铣大端面
切削速度:
m/min
r/min
选用主轴为r/min
工作台进给量:
m/min
基本工时:
min
3.3.3工序Ⅲ切削用量及基本工时的确定
(1)钻孔Φ23mm
选择Φ23mm高速钢锥柄标准麻花钻(见《工艺手册》表3.1-6)
mm/r(《切削》表2.7和《工艺》表4.2-16)
m/min(《切削》表2.15)硬度200-217
r/min(3.7)
按机床选取r/min(《工艺》表4.2-5)
实际切削速度:
m/min
基本工时:
min(《工艺》表6.2-5)
(2)扩孔mm
选择Φ24.8mm高速钢锥柄扩孔钻(《工艺》表3.1-8)
由《切削》表2.10得扩孔钻扩Φ24.8mm孔时的进给量
f=0.7mm/r~0.8mm/r,
由《工艺》表4.2-16取mm/r扩孔钻扩孔时的切削速度
由《切削》表2.15得m/min,故:
7m/min~4.7m/min
89r/min~60r/min
按机床选取r/min
m/min(3.8)
基本工时:
min
(3)铰mm孔
选择Φ25mm高速钢锥柄机用铰刀(《工艺》表3.1-17)
由《切削》表2.24得f=1.1mm/r~1.5mm/r,ap=0.15mm~0.25mm,
VC=4m/min~8m/min
由《工艺》表4.2-16得mm/r
51r/min~10r/min
按机床选取r/min
m/min
基本工时:
min
3.3.4工序Ⅳ切削用量及基本工时的确定
(1)钻Φ10孔
选择Φ9.8mm高速钢锥柄麻花