RG031211电弧炉炼钢基本操作工艺规程Word格式.docx
《RG031211电弧炉炼钢基本操作工艺规程Word格式.docx》由会员分享,可在线阅读,更多相关《RG031211电弧炉炼钢基本操作工艺规程Word格式.docx(6页珍藏版)》请在冰豆网上搜索。
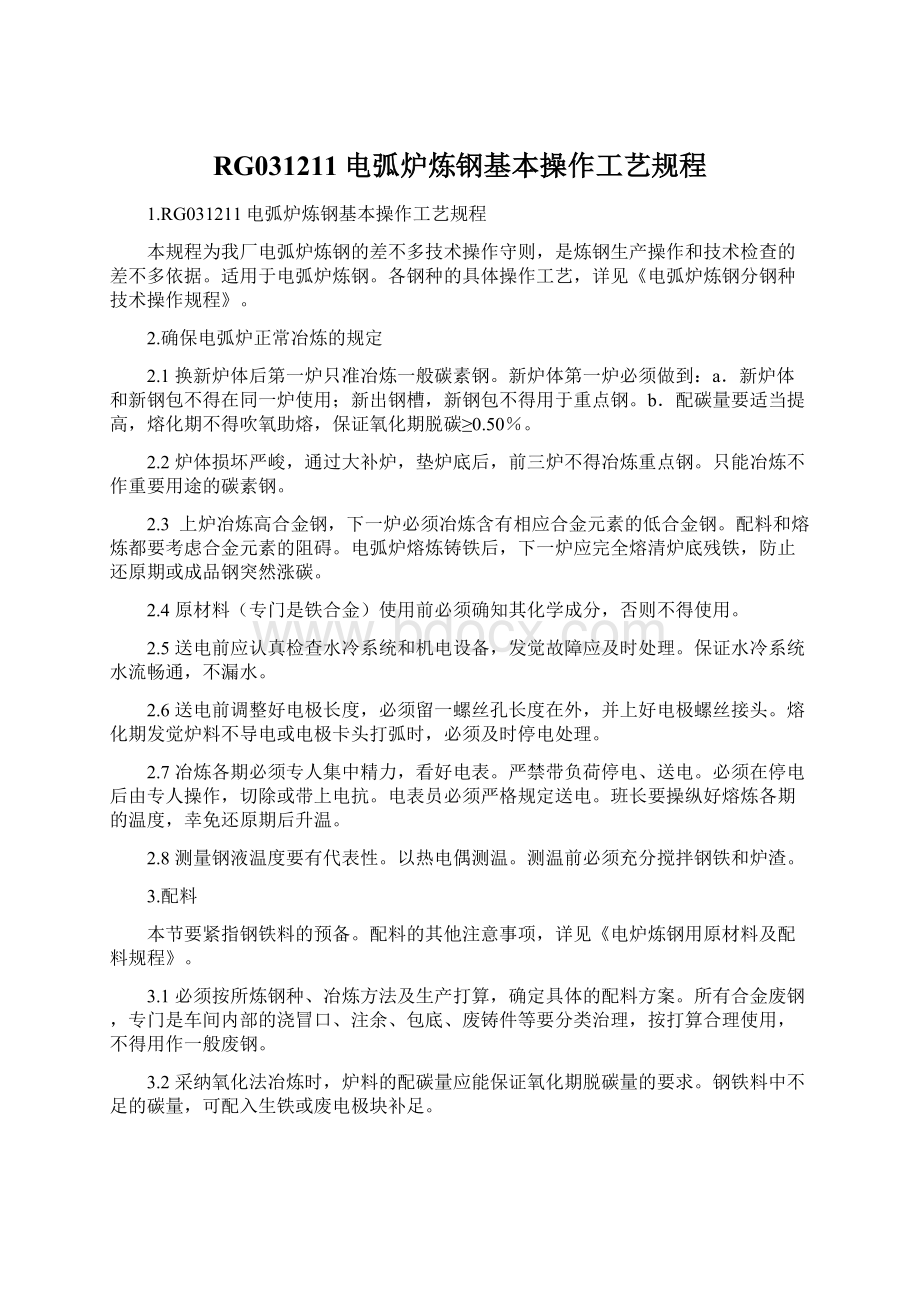
2.6送电前调整好电极长度,必须留一螺丝孔长度在外,并上好电极螺丝接头。
熔化期发觉炉料不导电或电极卡头打弧时,必须及时停电处理。
2.7冶炼各期必须专人集中精力,看好电表。
严禁带负荷停电、送电。
必须在停电后由专人操作,切除或带上电抗。
电表员必须严格规定送电。
班长要操纵好熔炼各期的温度,幸免还原期后升温。
2.8测量钢液温度要有代表性。
以热电偶测温。
测温前必须充分搅拌钢铁和炉渣。
3.配料
本节要紧指钢铁料的预备。
配料的其他注意事项,详见《电炉炼钢用原材料及配料规程》。
3.1必须按所炼钢种、冶炼方法及生产打算,确定具体的配料方案。
所有合金废钢,专门是车间内部的浇冒口、注余、包底、废铸件等要分类治理,按打算合理使用,不得用作一般废钢。
3.2采纳氧化法冶炼时,炉料的配碳量应能保证氧化期脱碳量的要求。
钢铁料中不足的碳量,可配入生铁或废电极块补足。
3.3废钢中不得混入有色金属,如:
铜、铅、锡、锌、铝等,专门是巴氏轴承合金,一经发觉,必须赶忙检出送交废品库集中处理。
废钢中不得混入封闭容器及易燃爆物品。
浇道上的耐火砖及废铸件上的砂子必须清除洁净,确保炉料良好导电。
3.4炉料应大小块度搭配,尽量减少装料次数,加速熔化。
3.5炉料必须准确称量,依照生产打算要求,配好料。
配料单上必须准确填写熔炼炉号、钢号、料斗号和炉料重量。
如配合金废钢和生铁必须清晰写明。
配料员必须在料单上签名。
4.补炉
炉体耐火内衬的好坏直截了当阻碍炼钢质量。
加强炉体爱护、延长炉体寿命,是电炉炼钢的重要环节。
4.1上一炉出钢前应预备下一炉的补炉材料。
一样采纳卤水镁砂,即原装镁砂或加工镁砂(粒度≤8㎜)加卤水8–12%(密度≥1.3g/㎝3),拌和平均。
炉体腐蚀严峻时,可在冷态下,用碾制的沥青镁砂贴补。
配制方法为70%沥青镁砂+30%镁砂粉,外加5–10%卤粉在轮碾机中碾匀后,适当加水碾制而成。
4.2出完钢炉体回正后,将炉门坎清理到适当高度,认真检查炉坡、渣线,清除残渣。
炉料要趁高温,做到快速、薄补,以便烧结。
出钢口有坎时,必须打平,以利出钢时钢流顺畅。
依照装入量大小,注意垫好炉门坎。
超装量大时,要专门注意爱护门框水箱脚。
4.3炉底局部起坑时,应迅速扒净残钢残渣,用沥青镁砂填平。
如凹坑较深时,可用沥青镁砂砖填入坑底,用沥青镁砂充填间隙,找平,面上撒一层沥青粉。
4.4间隙开炉前冷补炉时,应先清除炉底、炉坡、渣线处的残渣,用卤水镁砂认真补修,炉墙损坏处一并修补。
炉体状况不行时,不冶炼合金钢和重要产品用钢。
5.装料
5.1装料前,炼钢班长在生产现场对比配料单检查炉料,核对重量,以免装错料。
5.2装料时,先在炉底垫石灰1–2%(占炉料重量)。
炉底上涨时可不垫石灰,在熔化期酌情加入,以利提早形成炉渣,早期脱磷。
5.3装料、压料要有专人指挥行车,防止碰撞炉墙。
当料堆高时,不得强行开进炉体,应设法拉平或压平。
装料后要检查炉料是否接触炉门框水箱和水冷炉盖,如有应及时排除。
超装量大时,加最后一、二次料前,应加堵炉门坎,防止跑钢。
6.熔化
熔化期占全炉冶炼时刻一半以上,耗电量占全炉的60–70%。
因此,抓紧熔化期操作,合理吹氧助熔,加速炉料熔化。
做到早期脱磷,为氧化期制造良好条件,对增加产量、保证质量、降低电耗都有重大意义。
6.1熔化期采纳最大功率供电。
无大塌料时,应尽早切除电抗。
6.2熔化期炉底形成熔池,炉料发红,可吹氧助熔,切割废钢,破坏炉料搭桥,加速熔化。
助熔的氧气压力0.5Mpa左右,氧焰不得触及炉底,炉坡和炉墙,不得用吹氧管推料。
吹氧人员必须集中精力,注意安全。
6.3熔化末期,依照配碳量和含磷量高低,可加入不超过炉料重量的1.5%的碎矿石成氧化铁皮放初期渣,并补充适量的石灰、萤石,造好流淌性良好的熔化渣,以利脱磷。
熔化期石灰总量(包括垫炉底的石灰)为炉料重量的2–4%。
6.4冶炼含镍、钼的钢号,可按规格中、下限加入镍、钼(应考虑废钢中的合金元素)。
6.5当炉料熔化90%左右时,可取参考样分析C、P,依照化验结果或火花判定,决定是否需要扒渣增碳,以保证氧化期的脱碳量,取样分析C、P、S、Cr、Ni、Cu等元素。
脱碳量以此样为准。
7.氧化期
氧化期的任务是通过氧化脱碳,熔池沸腾,从而脱磷去气体(N、H)和夹杂物,同时提高钢液温度,达到或略高于出钢温度。
7.1矿石氧化法和吹氧氧化法
7.1.1规定铸造用钢或其他重要钢号氧化期的脱碳量必须≥0.30%。
化验碳不能满足脱碳量要求时,应扒渣增碳,取样分析合格后,再开始氧化。
7.1.2依照化验结果,成分合适,温度1560–1580℃,方许加矿石或吹氧。
应分批加矿,勤搅拌、勤调渣,做到高温氧化,活跃沸腾,自动流渣,平均升温。
脱碳速度不宜过快,禁止低温加矿,以防发喷跑钢。
保持氧化期渣许多于3%。
7.1.3含磷量较高时,可采纳矿石氧化法或综合氧化法:
前期加矿石氧化,换渣去磷后吹氧去碳,或边加矿边吹氧。
钢液含磷较低时,可采取全部吹氧脱碳法。
7.1.4吹氧脱碳时,吹氧管插入熔池深度为150–200㎜。
保持与水平成30°
左右的倾角,并左右摆动,以利平均脱碳,防止局部过热,炉底如无冷钢凝聚,则严禁吹炉底。
吹氧压力0.8–1.2Mpa。
7.1.5加完矿或吹完氧5分钟后,搅拌取样分析碳、锰、磷及相应的合金元素,并调整锰量:
中碳钢≥0.20%Mn,低碳钢≥0.30%Mn。
7.1.6从加完最后一批矿或吹完氧到扒氧化渣这一段时刻为纯沸腾时刻,规定:
末批加矿石时≥10分钟,吹氧时≥5分钟。
7.2返回吹氧法
7.2.1为了回收废钢中的合金元素,不加矿石氧化。
直截了当吹氧去碳,经预脱氧后,依照含磷量高低确定采纳单渣法、部分单渣法或双渣法进行冶炼。
7.2.2炉料由电炉返回钢和清洁废钢组成,配入合金元素不得超过规定上限。
含钼钢种,包括炉料中的Mo,用Fe-Mo将Mo加到规格中限。
7.2.3熔化末期可吹氧助熔,如磷高也可加入1.0-1.5%的矿石(占料重),熔清后取样全分析,温度、成分合适,即可吹氧脱碳,要求脱碳量≥0.15%。
吹氧脱碳后,取样分析,然后加1-2kg/t硅铁粉或硅钙粉进行预脱氧,待炉渣流淌性良好,渣色变亮可扒除大部分渣,造新渣进行还原。
其他同氧化法。
7.3还原前扒渣及增碳的规定
7.3.1扒渣条件:
⑴扒渣碳规定≤操纵下限,冶炼合金钢时,应考虑铁合金的增碳量。
冶炼低碳钢时,扒渣碳不得低于0.05%(分钢种规程有规定者除外)。
⑵扒渣磷规定≤0.020%,含磷量上限≤0.030%的钢种,扒渣磷规定≤0.010%。
⑶扒渣温度应不低于出钢温度。
7.3.2扒渣时,可先带电扒渣,不得使钢液暴露。
等到化验结果合乎扒渣条件,方可停电和升起电极迅速扒渣,应可能扒净氧化渣。
不氧化法和返回吹氧法采纳单渣冶炼的钢种,还原前先调整好炉渣流淌性,但不得过稀,以免还原期增碳。
7.3.3纯沸腾时刻,温度和磷均合乎要求,而碳比规定高0.03-0.05%时,可作如下处理:
⑴吹氧或加矿去碳,取样分析,纯沸腾时刻≥5分钟,可不等化验结果扒渣还原。
⑵扒渣后不加Fe-Mn,造稀薄渣后吹氧去碳至规定要求。
7.3.4扒渣后如碳过低,可在裸露的钢液面上加干燥的炭粉增碳,增碳量≯0.10%,炭粉回收率按40-60%运算,加入后应充分搅拌,也可在稀薄渣下加干燥生铁增碳。
8.还原期
还原期的要紧任务是脱氧、脱硫、调整钢液成分和温度。
还原期是保证钢液质量的要紧环节。
8.1扒渣后如需增碳,应迅速加炭粉增碳,然后加稀薄渣料:
石灰20-50kg/t,萤石4-5kg/t,火砖块4-5kg/t。
还原期总渣量为料重的3-5%。
8.2调整Mn至规格下限。
薄渣形成后,有预脱氧要求的钢种,插铝0.5kg/t,随后加入扩散脱氧剂。
一样采纳硅铁粉白渣法还原。
硅铁粉总用量3-6kg/t,硅的回收率为40-60%,第一批硅铁粉用量≤2.5kg/t,加完后酌量加入炭粉,紧闭炉门和炉盖加料孔,保持炉内正压,加完后隔5-7分钟,搅拌钢液和炉渣,可适量加石灰,再加第二批硅铁粉,用量≤2.0kg/t,以后各批硅铁粉用量<1.0kg/t,并酌量加炭粉。
8.3加完第二批硅铁粉后5-7分钟,在白渣下充分搅拌,取样分析C、Mn、Si、P、S及所需的合金元素,同时测温,酌量加入Si、C粉,再通过5分钟后,搅拌取全分析样及渣样,一样要求(FeO)<0.8%。
同时取圆杯样检查脱氧收缩情形。
8.4铬钼及铬钼钒等合金铸钢,在出钢前加入预热的钛铁,不计烧损加Ti0.05%。
8.5整个还原期切实操纵好温度、还原气氛和化学成分,C、Mn、Si及合金元素的化验试样必须许多于2个,出钢前30分钟内,必须要有C的分析结果。
出钢前10分钟,必须要有测温数据。
出钢温度一样要求:
低碳钢1610-1630℃,中碳钢1600-1620℃。
如铸件浇注箱数较多,则应适当提高出钢温度。
8.6如含碳量偏低,可加入干燥的低磷生铁增碳。
生铁增碳量不超过0.06%,加入生铁到出钢要有一定的熔化时刻,并加强搅拌。
加入生铁量达15kg/t小时,经15分钟后,生铁全熔方许出钢。
合金钢炉后不得用炭粉增碳,45钢及以下的碳素钢,炉后炭粉增碳量不得超过0.03%。
8.7整个还原期应在弱电石渣或白渣下精炼,注意保持炉内的还原气氛和炉渣的流淌性。
出钢时必须是流淌性良好的白渣,不得在黄渣或弱电石渣下出钢。
8.8依照还原试样化验结果,调整钢液成分,原则上C、S必须进入规格方许出钢,如C比操纵下限低0.03%以内,可在补加高碳料(高碳铁合金或增碳生铁)后,确有把握的情形下出钢。
8.9出钢口及出钢槽应经常注意爱护,保持形状,大小正常,烘烤干燥。
出钢前5分钟打开出钢口,清扫出钢槽。
8.10出钢前5分钟内不许加炭粉。
出钢前3分钟内,插铝终脱氧,插铝后不得加入Fe-Si粉。
插铝后经充分搅拌,提升电极停电出钢。
终脱氧插铝量规定规定如下:
低碳铸钢1.0kg/t,中碳铸钢及Q235A2钢锭0.8kg/t,铬钼及铬钼钒铸钢0.3kg/t。
出钢槽随钢流加Ca-Si合金粒1.0kg/t。
8.11出钢应做到:
⑴钢流不冲刷塞杆及包壁;
⑵先出渣后出钢,渣钢混出,以利混渣脱硫。
浇注组必须有专人指挥行车降落和移动钢包,与倾炉紧密配合。
出完钢,钢液冷静许多于5分钟后浇注。
9.加入铁合金的一样规定
9.1铬铁:
在稀薄渣下,按运算加到规格下限或比下限少0.10-0.20%,以便还原期调整含碳量:
出钢前补加Cr≥0.20%时,Fe-Cr加入后≥10分钟方可出钢,补加Cr<0.20%时,Fe-Cr加入后≥7分钟方可出钢。
铬的回收率按95%运算。
9.2锰铁:
可在扒渣后随稀薄渣料加入或在薄渣形成后加入。
出钢前调整Mn,加入锰铁到出钢的时刻要求与铬铁相同。
锰的回收率按95-98%运算。
9.3硅铁:
冶炼含硅合金钢时,于出钢前加入烘烤过的Fe-Si块。
一样钢加入少量Fe-Si时,于出钢前5分钟加入,加入后要充分搅拌,防止Fe-Si块裹入渣中。
硅的回收率按94-97%运算。
9.4钼铁:
在熔化末期按规格中下限加入,还原期尽量不调整钼,加入Fe-Mo距出钢时刻应≥15分钟。
钼的回收率按95-98%运算。
9.5钒铁:
必须在还原期脱氧良好的白渣下,距出钢前5-8分钟加入,补加的Fe-V不许用粉末,Fe-V加入后应赶忙加一批硅铁粉或硅钙粉,以保证钒的回收率。
钒的回收率按85-95%考虑。
9.6钛铁:
在出钢前3分钟内良好的白渣下加入。
9.7硅钙合金(粒状或小块状):
出钢时随钢流加入出钢槽中。
Ca-Si粒的块度应为5-15㎜,Ca-Si合金中的Si的回收率按60-70%估量。
9.8稀土硅铁:
出钢时先出钢水,稀土硅铁加入钢包中,钢水出完后才能大量出渣。
如稀土硅铁的钢号出钢温度比不加稀土的钢号提高20-30℃,以防产生稀土类夹杂,同时要专门注意其增Si量。
9.9金属铈与稀土合金:
在良好的白渣下部分随钢流加入钢包,先出钢水,待稀土全熔后,方可大量出渣。
亦可在出完钢后,用钟罩将稀土插入钢包。
进行稀土处理时出钢温度相应提高20-30℃,以防产生稀土类夹杂。