焙烧资料Word格式.docx
《焙烧资料Word格式.docx》由会员分享,可在线阅读,更多相关《焙烧资料Word格式.docx(22页珍藏版)》请在冰豆网上搜索。
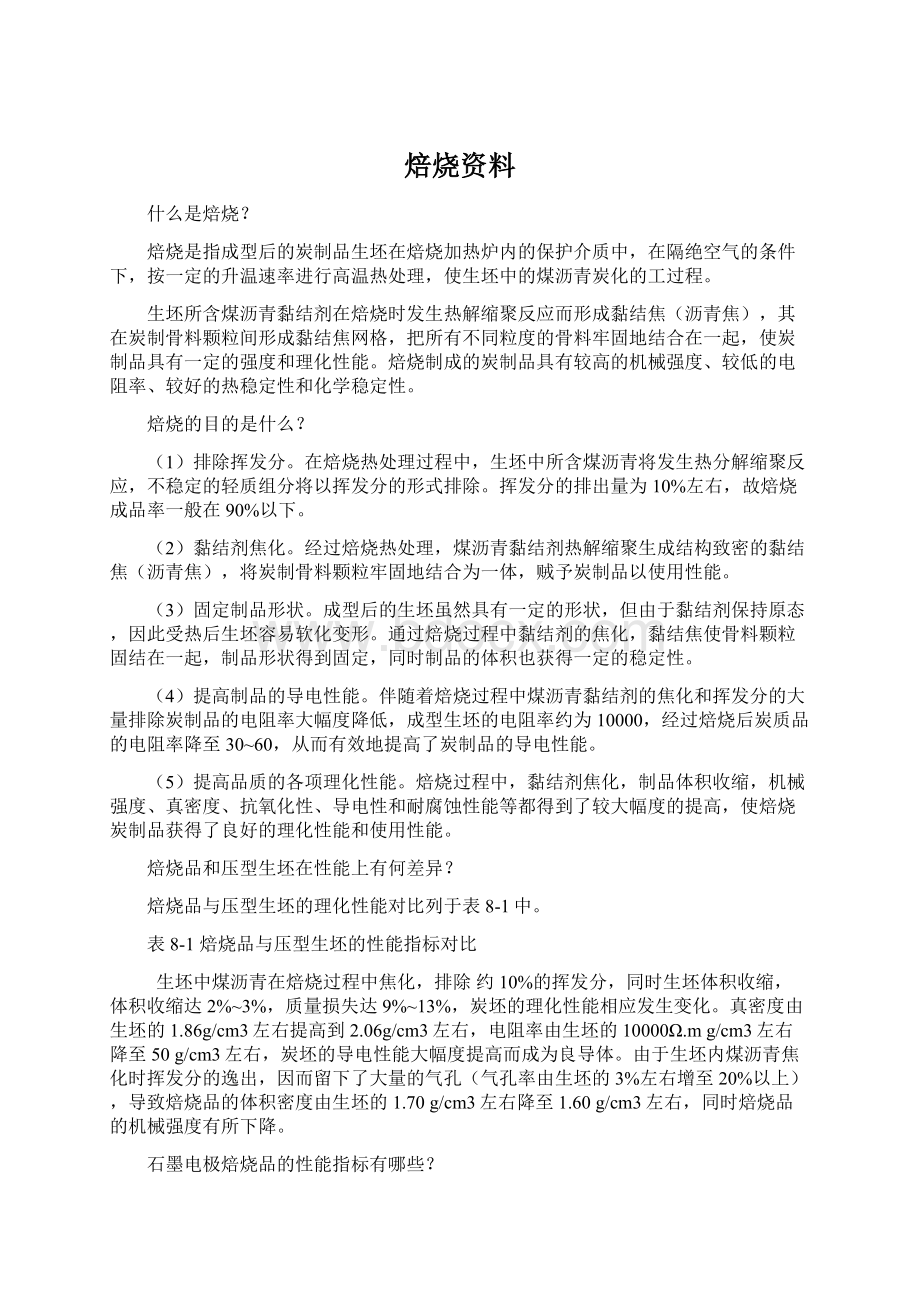
真密度由生坯的1.86g/cm3左右提高到2.06g/cm3左右,电阻率由生坯的10000Ω.mg/cm3左右降至50g/cm3左右,炭坯的导电性能大幅度提高而成为良导体。
由于生坯内煤沥青焦化时挥发分的逸出,因而留下了大量的气孔(气孔率由生坯的3%左右增至20%以上),导致焙烧品的体积密度由生坯的1.70g/cm3左右降至1.60g/cm3左右,同时焙烧品的机械强度有所下降。
石墨电极焙烧品的性能指标有哪些?
我国石墨电极焙烧品质量标准(YB/T099—2005)对石墨电极焙烧品的质量评价共限定了5项理化指标(见表8-2),表中B-IE代表浸渍石墨电极焙烧品,B-RP代表普通功率石墨电极焙烧品,B-HP代表高功率石墨电极焙烧品,B-UHP代表超高功率石墨电极焙烧品。
对于石墨电极焙烧品,电阻率、耐压强度、体积密度和硫含量作为质量考核指标。
直径550~700mm石墨电极焙烧品的理化指标由供需双方协议。
表8-2石墨电极焙烧品的理化性能指标
焙烧过程中煤沥青的炭化机理是怎样的?
焙烧就是炭生坯中煤沥青炭化形成黏结焦的过程。
在此过程中由稠环芳烃分子混合物构成的煤沥青将会发生分解、环化、芳构化、缩聚直至成焦等一系列反应。
煤沥青的热解缩小聚从300℃开始,前期以热分解反应为主,而后期以热缩聚反应为主,随着缩合环数增多,稠环芳烃的热稳定性增大,400℃进行中间相炭化阶段,450~500℃半焦形成,至此炭材料的基本结构雏形已形成,700~750℃形成黏结焦,750℃以后就是结构重排和深度焦化过程。
由于煤沥青组成结构的复杂性,从而导至其炭化过程也相当复杂。
煤沥青在炭坯中的焙烧炭化成焦与煤沥青单独炭化有所差异,主要在于焙烧时煤沥青的热解缩聚是在固体炭质物料颗粒表面(包括气孔)进行的,实质上是固体炭质物料与煤沥青的共炭化过程,并且由于焙烧时生坯埋在填充料中,煤沥青的炭化环境也发生了变化,这两方面都利于促进煤沥青的缩聚反应和提高煤沥青的结焦值。
焙烧热处理过程可分为哪几个阶段?
根据黏结剂煤沥青在焙烧过程中发的物理化学变化,可将焙烧热处理过程分为如下5个阶段:
(1)煤沥青软化—生坯发生塑性变化低温预热阶段。
当生坯实质受热达到100~230℃时,煤沥青程熔融状态,生坯开始软化,生坯体内的应松弛,导至生坯体积稍的膨胀,但煤沥青挥发分排出不多,生坯处于塑性阶段。
此阶段主要对炭坯起预热作用。
由于生坯体内的温度差和压力差的作用,部分煤沥青轻质组分产生迁移而扩散和流动,故此阶段升温速度要快。
(2)煤沥青热分解—炭坯挥发分大量排除阶段。
生坯实质受热温度继续升至230~400℃时,煤沥青分解速率逐渐加快,尤其在350~400℃温度范围内,煤沥青剧烈分解,挥发分大量排出。
为了控制煤沥青挥发分的排出不致过分激烈,此阶段升温速度必须放慢,即应均匀缓慢地升温。
否则,升温过快,就会造成挥发分急剧排出,使炭坯产生裂纹。
(3)煤沥青热缩聚和半焦形成阶段。
当生坯实质受热温度升至400~500℃时,煤沥青分解挥发速度减缓,进入以缩聚反应为主的阶段,煤沥青在高温下热解缩聚形成半焦,此时挥发分排出量有所减少,生坯体积由膨胀转为收缩。
此阶段升温不能过快,因为还有少量挥发分继续排出,而且此时焙烧品的机械强度和热导率都比较低,过快地升温会导致焙烧品开裂。
中温焦化阶段对提高煤沥青结焦值和改善炭制品性能起着很能作用,尤其是煤沥青形成半焦以前应严格控制升温速度,缓慢升温。
(4)煤沥青高温焦化阶段。
当生坯实质受热温度达到500~700℃时,煤沥青生成的半焦进一步转变成黏结焦(沥青焦),煤沥青分解排出的挥发化进一步减少,炭坯继续收缩,由于煤沥青黏结剂已转变成黏结焦,炭坯体的导热率也有所提高,因此此阶段升温速度可以适当加快。
(5)焙烧制品性能完善阶段。
当生坯实质受热温度达到700~1000℃时,煤沥青的焦化过程基本完成,炭坯真密度增加的同时继续发生收缩。
为了使焦化程度更加完善及进一步提高焙烧品的性能指标,还需要将炭坯加热到900~1000℃。
在高温炭化阶段升温速度可以快一些,当温度升高到最高温度后要保持15~30h,使炉内各个部位的温度都接近指定的温度,以缩小炉室各部位之间的温差,保证整炉制品质量的均匀。
焙烧最终温度是如何确定的?
炭坯中黏结剂煤沥青的焦化650~700℃已基本完成,但加到700℃以上,焙烧品的真密度进一步提高,焙烧品的体积收缩仍在进行,同时机械强度、导电性和导热性继续有所提高,800℃后体积收缩基本稳定下来。
因此,为了保证后序工序的成品率,焙烧最终温度定为不低于800℃(炭坯实际受热温度),这样焙烧品在石墨化炉内就能顺利地进行高温热处理。
但由于焙烧炉温度场的不均匀,炉内各部位温差较大,因此,目前工业生产中最终焙烧温度(炭坯实际受热温度)一般控制900~1000℃(此时火道温度达到1100~1300℃)。
焙烧曲线的制定依据是什么?
(1)根据炭坯在焙烧过程中各温度阶段的物理化学变化制定焙烧曲线。
焙烧曲线应该与煤沥青挥发分的排出速率和煤沥青焦化的物理化学变化相适应,这是制定焙烧曲线的理论根据。
生坯在焙烧过程中最重要的变化是煤沥青的热解缩聚和形态的变化,从而引起一系列炭坯理化性能的变化。
弄清煤沥青在焙烧过程中的变化规律,对于合理地制定焙烧温度曲线至关重要。
一般来说,低温软化阶段升温速率要快。
中温挥发分大量排除阶段升温速率要慢,高温阶段可加快升温速率,这样有利于提高焙烧品质量和成品率。
(2)根据炭坯的种类和规格制定焙烧曲线。
不需要石墨化的炭制品(如预焙阳极和炭块等)焙烧温度应高一些(1300℃左右),需要石墨化的制品焙烧温度可稍低些(1200℃左右),而炭电阻棒等电阻率要求大的制品,则焙烧温度为1000℃即可。
大规模制品截面大,焙烧时内外温差大,易产生裂纹废品,升温速率应放慢,因此焙烧曲线要长些,小规格制品焙烧曲线则相反。
(3)根据焙烧炉炉形结构和尺寸制定焙烧曲线。
不同结构和尺寸焙烧炉的温度场有其相应的特点,为了使炉室内各部位温差尽可能缩小,制定焙烧曲线时必须考虑炉形结构和尺寸。
例如,对于大尺寸炉箱的环式焙烧炉,为减少各部位的温差,升温速率应适当放慢,焙烧最终温度适当提高或保温时间适当延长;
对于安装高温搅拌风机的隧道窑或车底式炉,由于各部位温差较小,因此可采有更为经济的焙烧曲线。
使用容器焙烧可缩短焙烧升温时间。
同一炉室炭坯合理搭配时(如下层装大规格生坯,上层装小规格生坯),焙烧曲线可适当短些。
反之,同一炉室上下均为大规格生坯,焙烧曲线应长些。
(4)根据生坯的压型方式和生坯性能制定焙烧曲线。
对于模压成型、振动成型和等静压成型的生坯,由于体积密度相对挤压成型要高一些,因此焙烧曲线应适当缩短。
对于同规格制品,生坯体积密度大的升温速率应慢些,体积密度小的升温速率可快些。
黏结剂用量大的制品升温速率可快些,以防止生坯的软化变形,黏结剂用量小的制品升温速率可慢些,以减少裂纹废品的产生。
生坯中骨料的煅烧程度不好,焙烧曲线要相对长些。
高软化温度煤沥青开始分解及排出挥发分的热失重曲线与中温沥青不同,故采用高软化温度煤沥青制备的生坯焙烧升温曲线应采用中温沥青时有所区别。
(5)根据填充料的种类制定焙烧曲线。
用烘干后的冶金焦和河沙分别做填充料焙烧炭坯,由于河沙堆积密度大且热导率高,因此要采用升温较慢的焙烧曲线,否则会影响焙烧成品率。
为什么制定焙烧曲线一定要遵循“两头快,中间慢”的原则?
焙烧曲线的制定一定要遵循“两头快,中间慢”的原则。
这是因为焙烧各个阶段的加热速度决定着炭坯所发生的物理化学变化过程,应保证炭坯中的反应进程按黏结剂煤沥青的热解缩聚规律进行,即在煤沥青软化阶段不使炭坯变形,在煤沥青热解缩聚生成黏结焦阶段不使炭坯弯曲、变形和开裂,并且应得到最大的结焦残炭量和整体烧结强度。
生坯温度200℃以前,生坯没有明显的物理化学变化,加热速度可以适当加快,否则,低黏度的煤沥青发生物理迁移,就会产生空头变形废品。
炭坯温度达到700℃以后,煤沥青黏结剂的焦化过程基本结束,升温速率可以加快。
而焙烧的关键阶段,特别是炭坯温度200~500℃之间时,煤沥青剧烈分解,导至挥发分大量逸出,升温速率应特别予以控制,缓慢升温,否则容易产生大量废品。
如何确定焙烧曲线中不同阶段的升温速率?
当生坯实质受热温度达到100~250℃时,煤沥青处于熔融软化状态,煤沥青产生迁移而扩散和流动,炭坯开始变软并且体积膨胀。
若此阶段时间短,则炭坯产生变形就少;
反之,炭坯在软化阶段停留时间长,产生变形废品就多。
故此阶段升温速度要快,升温速率应高4℃/h。
焙烧温度升高250℃以后,煤沥青开始热解逸出挥发分并发生热解缩聚反应,在此阶段升温必须缓慢,同时缓慢升温,也有利于煤沥青结焦值的提高。
否则,升温过快。
会造成挥发分急剧排出,使炭坯产生裂纹,并导至炭坯体积密度偏低。
为了提高煤沥青的结焦值和保证炭制品制量,在生坯实际受热热温度为300~500度温度区间内,焙烧升温速率应低2℃/h。
当炭坯实际受热温度达成500~700℃时,进入煤沥青高温焦化阶段,炭制品结构已经形成并逐渐稳定,因此,此阶段升温速率可以适当加快,升温速率为4℃/h左右。
当炭坯实际受热温度达到700~1000℃时,目的是使焦化程度更加完善及进一步提高焙烧品的性能指标,此阶段升温速率可明显加快,达到6~12℃/h。
一般来说,焙烧生坯实际温度230~450℃温区时最关键,这一温区的升温速率必须放慢;
20~230℃温区的升温速率可230~450℃温区快1倍,既不会增加加废品,又可降低生坯膨胀量,使生坯变形减少,同时减轻填充料在生坯表面的焦结程度;
450~650℃温区的升温速率可比230~450℃温区2倍;
650~850℃温区的升温速率可450~650℃温区再增加1倍。
例如,直径为500mm的电极生坯,焙烧过程中,230~450℃温区的升温速率为1.3~1.5℃/h,450~650℃温区的升温速率为2.3~2.8℃/h,650~850℃温区的升温速率为4.8~5.6℃/h。
焙烧过程中煤沥青的物理迁移是如何进行的?
当生坯的焙烧温度达到150~300℃时,黏结剂煤沥青的黏度急剧下降,而此时煤沥青的热解缩聚反应尚未开始,煤沥青由玻璃态急剧转变成液态,呈很好的夜体流变状态,并且煤沥青体积增大。
在重力作用下,液态沥青沿着固体炭质物料的空隙向下流动,从而产生物理迁移现象,此时炭坯呈软化态。
影响煤沥青迁移的因素有两个:
一个是重力因素,在焙烧过程中煤沥青黏结剂由于重力作用沿炭坯体高度方向由上往下迁移;
另一个因素是温度梯度,它会引起煤沥青向低温方向迁移。
碳坯体积在焙烧炉中的受热状态正是存在由上端的高温到下端的低温的的温度梯度,热流从炉室上部到下部,因此,在此温区内停留时间过长,必然导致煤沥青迁移量增多,从而影响炭坯体上端的密实程度。
因为煤沥青的体胀系数大于焙烧品的体胀系数,所以煤沥青就有向外流动的趋势。
在焙烧升温过程中,热流由外向内传递,炭坯体外部首先软化,从炭坯体内部煤沥青析出的挥发分就由内部向外部扩散,从而使过剩沥青形成向外的推力,向外迁移的煤沥青被填充料吸附。
这也是填充料黏结在焙烧品表面的原因。
焙烧时煤沥青的迁移分纵向迁移和横向迁移。
在正常升温条件下,纵向迁移可使焙烧品上端与下端的体积密度相差0.01~0.03g/cm3,个别大规格产品可能会出现空头现象;
横向迁移可使焙烧品径向内外体积体积密度相差0.01g/cm3。
焙烧炭坯内部发生的迁移现象不是糊料的整体迁移,而是煤沥青的选择性迁移,其中煤沥青较轻质组分优先发生迁移。
如何防止焙烧过程中煤沥青产生迁移?
压型得到的生坯相当均质,而焙烧品各部位性质却相差较大,这是由于焙烧过程中煤沥青的物理迁移现象造成制品质量的不均匀,并且容易产生焙烧废品。
固体炭制物料粒度越大,其比表面积越小,物料与煤沥青的接触面积也就越小,因而造成粗颗粒配方的生坯焙烧时煤沥青容易发生迁移,即制品规格大,骨料颗粒大,煤沥青迁移容易。
例如,炭块焙烧中无烟煤粒度较大,与电极坯焙烧相比,其焙烧时煤沥青迁移程度大得多,因而易产生空头废品。
在相同的配料组成条件下,煤沥青用量过多,也易产生迁移;
煤沥青焙烧时结焦量低,也会导致空头。
要控制重力下黏结剂煤沥青的迁移,可采取如下措施:
(1)控制黏结剂煤沥青用量;
(2)对于大颗粒配方,采用高软化温度改质沥青,可使迁移现象显著降低;
(3)尽量缩短焙烧升温曲线的低温阶段,使生坯在煤沥青容易迁移的软化阶段停留时间缩短。
一般地,当焙烧温度达到100~250℃时,煤沥青处于低黏区,此时煤沥青最易迁移,在此低黏区停留时间越短,煤沥青迁移越少,焙烧变形废品率相应降低,即煤沥青的迁移量与生坯在100~250℃停留时间有关,焙烧时,在250℃以下维持时间过长,会增加煤沥青迁移的数量。
但在环式炉焙烧时,此段温区是靠余热自然升温的,无法控制其升温速率来缩短低黏区停留时间,适当减少预热炉室数目,可以在一定程度上加快升温速率。
减少预热炉室数目,即采取低温通煤气的措施,可以大大地减少生坯处在煤沥青迁移的临时温度带(100~250℃为迁移温度)的时间,而这个时间正是煤沥青产生剧烈迁移过程的时候。
装炉时生坯倾角越大,焙烧时煤沥青迁移现象越严重,但这方面的改善又受到装出炉操作的限制。
矩形截面的生坯焙烧变形率总是高于圆柱形截面生坯,这是由于两种截面的受力状态不同所致。
另外,生坯在焙烧炉室内装放不垂直,填充料在生坯周围密实程度不同,生坯焙烧时受力不均,煤沥青迁移也易造成制品变形。
生坯在焙烧过程中是处于非稳定的热场中,从黏度变化角度来看,煤沥青迁移与炭坯内温度梯度成正比,同时温度梯度也使焙烧品热收缩不均而产生内应力。
缩小焙烧炉内温差一直是一道工艺难题。
力求使焙烧炭坯处于均匀热场中,对于降低煤沥青迁移和焙烧废品率,提高焙烧品质量,都具有较大的意义。
焙烧升温曲线的类型有哪些?
带盖环式焙烧炉常用的焙烧升温曲线一般为280h、300h、320h、360h和400h。
预焙阳极的焙烧多采用敞开式环式焙烧炉,其焙烧升温曲线为本160~280h,预焙阳极的焙烧升温曲线要比石墨电极炭坯的焙烧曲线短。
例如30室环式焙烧炉的320h焙烧升温曲线(温度为炉盖下火焰温度)如下:
(1)130~350℃:
升温速率4.4℃/h,持续时间50h;
(2)350~400℃:
升温速率1.7℃/h,持续时间30h;
(3)400~500℃:
升温速率1.2℃,持续时间80h;
(4)500~700℃:
升温速率3.0℃/h,持续时间65h;
(5)700~800℃:
升温速率5.0℃/h,持续时间跨度20h;
(6)800~1000℃:
升温速率8.0℃/h,持续时间25h;
(7)1000~1250℃:
升温速率8.3℃/h,持续时间性30h;
(8)1250±
25:
保温,持续时间跨度20h。
焙烧曲线各阶段的温度误差范围是多少?
(1)低温送煤气阶段。
点火时允许温度波动±
50℃,但必须在30mih内调整正常,按一定速率升温,直至350℃止。
(2)中温阶段。
炉室温度为350~800℃,允许温度波动范围为±
30℃。
由于某种原因,温度拖后,未达到规定温度,低于800℃时,每班可带5℃。
(3)高温阶段。
炉室温度为800~1300℃时,允许温度波动范围为±
由于某种原因,温度拖后,未达到规定温度,温度在800~1000℃时,每班可带15℃,温度在1000℃以上,每班可带25℃。
1300℃时允许温度波动±
25℃,保温一段时间后降温。
(4)降温阶段。
炉温由高温冷却至800℃时,降温速率为30±
10℃/H,降至800℃以下切断煤气。
升温速率对焙烧传统产生什么影响?
焙烧升温速率影响到煤沥青的热解缩聚炭化进程和黏结剂的析焦量,也影响炭坯形态的变化,从而影响到焙烧品的理化性能指标。
升温速率慢时,煤沥青有足够的时间进行热解缩聚反应,其析焦量增多,成焦密度增大,有利于提高炭制品性能,从而防止炭坯产生裂纹。
相反,升温速率快时,大量煤沥青所含有机物分子来不及发生缩聚反应便挥发出来,带走了很多本来可生成沥青焦的炭,使煤沥青析焦量降低,同时煤沥青的挥发分剧烈排出,炭坯容量产生裂纹。
焙烧升温速率过快,煤沥青的热分解和挥发速率也加快,分解的挥发分增加,同时结焦残炭值下降,并导致焙烧品一系列理化性能降低,而且在焙烧过程中容易产生裂纹废品。
升温速率直接影响到焙烧炉的温度场分布,这是由于炭坯在焙烧炉内的受热温度和时间均滞后热气流,炉室内不同位置的炭坯都处在不均匀的温度场中,温度分布的不均匀决定了煤沥青同类热解缩聚反应的不同时性,导致炭坯体积发生不均匀收缩,内部产生内应力而出现裂纹。
放慢350~600℃阶段的升温速率,煤沥青有足够时间进行热解缩聚反应,可以提高煤沥青析焦量,同时还可以使焙烧体系内温度场较均匀,对炭坯焙烧质量的提高有利。
最佳升温速率应能保证生坯中煤沥青的热解缩聚在最利于成品率和产品质量条件下进行,即产生的弯曲、变形和裂纹的数量最少,并且能得到量大的结焦残炭值,从而使焙烧品有较高的体积密度、机械强度和较高的电阻率。
什么是加压焙烧,压力会对焙烧产生什么影响?
加压焙烧就是在压力下对炭制品进行焙烧热处理,加压焙烧可以提高黏结剂煤沥青的结焦残炭值,有利于提高焙烧品的密度和机械强度,同时也可以大大缩短焙烧周期。
加压焙烧的方式有:
气体加压焙烧、机械压力加压焙烧和重力加压焙烧(如在焙烧炉上部填充料加放一层耐火砖)。
在焙烧过程中,生坯内煤沥青黏结剂分解产生的挥发分气体不断地透过炭坯的气孔和填充料逸出,并汇入流过炉室的热气流中。
当对焙烧体系施加压力时,这些挥发分气体的逸出就会受到阻力,炭坯中热分解气体扩散出来的速率放慢,直接抑制了煤沥青的热分解反应,促进了煤沥青缩聚反应的进行,导致黏结剂结焦值增加,因此加压焙烧有利于提高黏结剂的结焦值,从而改善焙烧品的质量。
焙烧过程中炭制品收缩会产生什么影响?
焙烧过程中炭坯的外观尺寸在不断变化,最终表现为收缩。
这是由于煤沥青在焙烧过程中发生分解缩聚,从而导致焙烧后炭坯线性收缩1%~2%(其中长度方向收缩小于2%,直径方向收缩小于1%),体积收缩2%~3%。
焙烧过程中炭坯体的收缩对炭材料的结构和质量有直接的影响,而且生坯在焙烧过程中的不均匀收缩经常会导致内外缺陷,直至形成裂纹。
炭坯体的收缩是伴随着焙烧烧温度的升高而逐渐产生的,其收缩与煤沥青的用量和性质密切相关,炭坯体在焙烧过程中的收缩与煤沥青的用量呈线性关系,煤沥青用量越多,炭坯体体积收缩越大。
炭坯的收缩量还与焙烧最高高温度、糊料配方、成型压力以及焙烧工艺条件有关。
气氛会对焙烧产生会长影响?
在焙烧过程中,煤沥青热解产生的挥发分不断透过炭坯和填充料的间隙,随着热气体流入烟道而排出。
热解挥发分气体在热气流中的分压永远小于煤沥青的饱和蒸气压,这就造成了炭坯内外挥发分的浓度差,炭坯内外层和挥发分内外层都存在着挥发分的浓度梯度,从而使挥发分气体不断向外扩散,其扩散速度与挥发分浓度梯度成正比。
填充料中和焙烧室上部空间的挥发分浓度越低,挥发分从生坯中扩散出来的速度越大,这将促进煤沥青分解速率加快,导致煤沥青的析焦量减少。
相反,如果挥发分从生坯中扩散出来的速度较慢,则煤沥青的析焦量将增加。
焙烧体系中煤沥青挥发分浓度梯度与烟囱的抽力有关,烟囱的抽力越大,其浓度梯度越大。
填充料的透气度越大。
(其松装密度越小),煤沥青挥发分的浓度梯度也越大。
使用新冶金焦作填充料时,其对煤沥青挥发分的吸附能力强,造成生坯内外煤沥青挥发分浓度梯度较大,煤沥青分解排出的挥发分多,导致煤沥青析焦量下降。
而当填充料使用一次后,冶金焦表面生成了一种热解炭膜,并使其表面活性降低,导致它对煤沥青挥发分的吸收能力减小,这对提高煤沥青的析焦量有利。
增大气向外压力(加压焙烧),会使煤沥青的析焦量显著提高。
为了促进焙烧过程中煤沥青更多地向缩聚反应方向发展,提高煤沥青结焦残炭值,在保证热气体顺畅流动的前提下,应尽量减小负压。
焙烧时煤沥青散发的挥发分可作为燃料使用。
焙烧炉室的温度场是如何分布的?
由于焙烧炉结构的限制,焙烧炉室的结构方向和水平方向都存在着较大的温差,如环式焙烧炉炉室深度一般为3.6~4.5m,可装两层长度为1.5~1.8m的生坯,国内此炉型在加热过程中上下温差达200~300℃,当达到焙烧最高温度时,上层水平方向中心和周围的温度相差50℃,而下层水平方向温度差达到100℃左右。
国外结构先进的环式炉装一层生坯时,上下温差可降到50℃以内;
装两层生坯时,可降到100℃左右。
焙烧炉内上述温差不仅表现在焙烧升温结束时,而且在焙烧全过程都存在,升温速率越快,温度差值越大。
温差的存在造成焙烧炉室温度场分布很不均衡,这决定了各温升阶段炉室不同部位炭坯实际加热速率及最终热处理温度的不同,对焙烧炭制品质量的均匀性有一定的影响,一般可通过高温阶段保温来缩小温差带来的影响。
调整焙烧炉室负压的原则是什么?
焙烧炉室的负压增大或减小,都会改变炉室的升温条件。
如果点火炉室的负压过大,则容易灭火。
炉子的负压越高,送入的热空气越多,燃烧的煤气增多,热量加大,燃烧产物也多,升温加快,但需要按焙烧曲线升温。
如果负压过小或没有富余的负压可供调整,那么吸入的热空气太少,煤气燃烧不完全,不仅高温炉室温度升不上去,而且还易发生“串煤气”,破坏了加热系统的温度制度。
焙烧炉室负压调整的原则是:
在满足升温条件的前提下,负压应调整到最佳值。
调整负压主要靠调整排烟机的风门来进行,其次是盖好不用的二次空气孔盖上的看火孔盖,抹好炉边,防止漏气。
冷却阶段的降温速率和出炉炉温度是如何确定的?
焙烧停止加热后即进入冷却阶段,此时焙烧品逐渐降温,并在较低温度下卸出炉外,再在炉外继续冷却至室温。
冷却过程中,焙烧品产生收缩,由于于制品表层和内部存在着温差,其内外体积变化不同而产生热应力,从而导致裂纹的出现。
因此,必须对降温速率进行控制,避免快速降温。
环式焙烧炉从最高温度1200℃下降到80