精脱硫转化部分Word文件下载.docx
《精脱硫转化部分Word文件下载.docx》由会员分享,可在线阅读,更多相关《精脱硫转化部分Word文件下载.docx(25页珍藏版)》请在冰豆网上搜索。
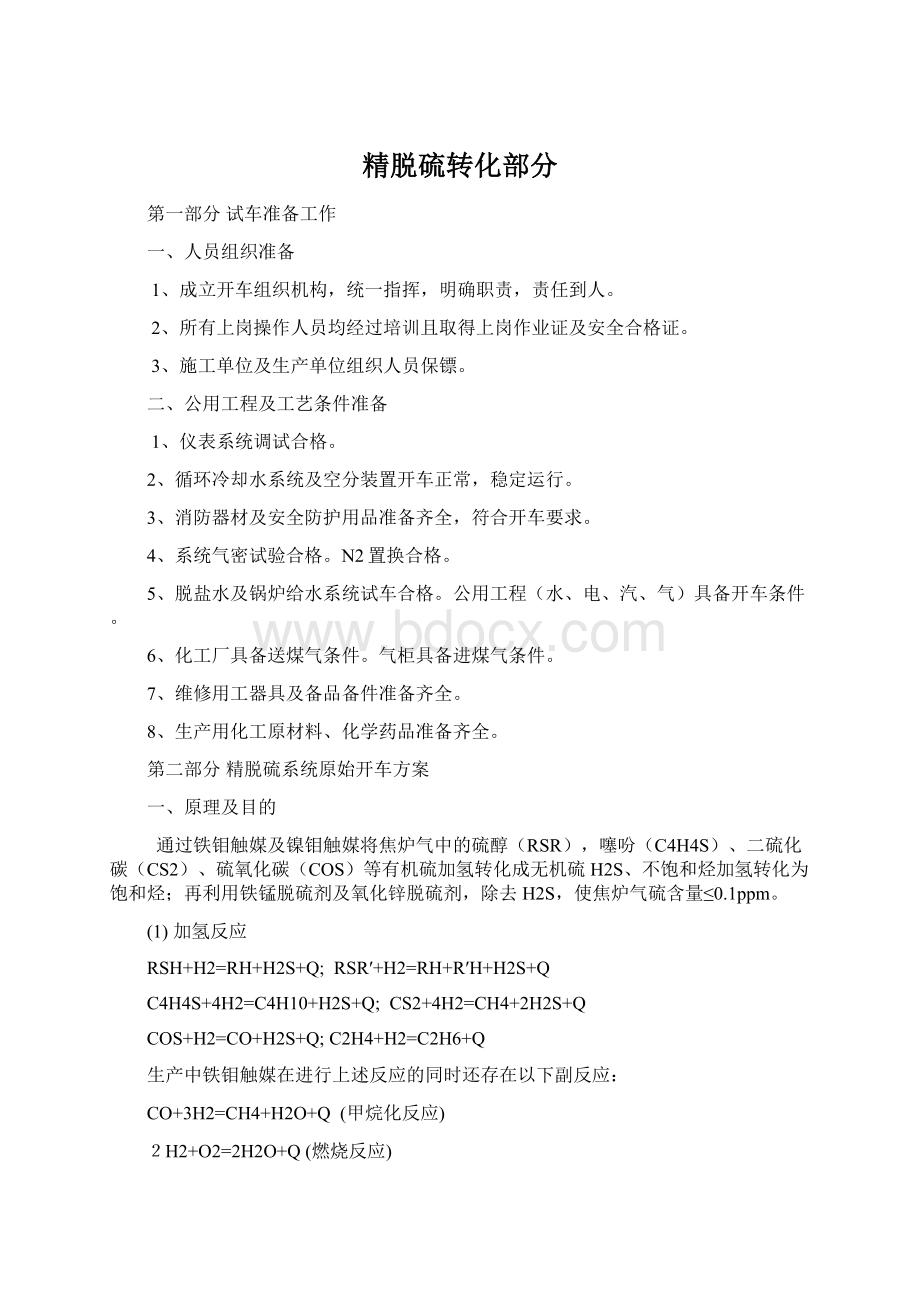
ZnO+H2S=ZnS+H2O
二、升温
(一)升温方块流程
脱硫转化系统升温用N2作为载体。
脱硫装置与转化系统串联进行升温。
流程如下:
D106a
D106b
E101壳程
E104壳程
焦炉气来自压缩
D101a
阿a阿a
D102
D101b
B101a盘管盘管
E102壳程
D105b阿
D103aA3a
D104
E104管程式
D103b
333a
O2
H101壳程
B102
H101管程
B101b中间煤气盘管
E103壳程
E103管程
E102管程
E105管程
E101管程
E108管程
E107管程
F102
E106管程
去压缩工序
F203
F105
(二)升温过程控制
1、依升温流程,启动C201、C202,建立N2循环流程。
2、升温速率及系统压力控制
(1)开工加热炉B101a、B101b升温速率控制
开工加热炉点火开车依开车方案进行(见开工加热炉B101ab操作规程)。
N2流量依空分送来的气量,通过精脱硫煤气调节阀FRCA102控制稳定。
B101a升温速率控制
从C201来的N2温度约90~100℃,在B101a内被加热升温,升温速率控制在20~50℃/h。
通过B101a第一组盘管后温度计TI-126及第二组盘管后温度计TI-166观察温度;
用HIC102a调节进B101a的燃料气量来控制升温速率。
B102升温速率控制
经过加热升温脱硫催化剂后,温度降低的N2进入B101b中间盘管继续加热,同时联压机C202送出的N2沿O2管线进入B101b上层盘管与下层盘管加热,观察进入B102前后温度TI-116、TI-117及TI-112、TI-115,通过HIC102b调节进B101b燃料气量,控制其升温速率为20~50℃/h。
压力控制
升温阶段系统压力可控制在0.3~0.5MPa。
(三)系统升温、恒温,脱除催化剂吸附水
1、空分N2量约2500~3000Nm3/h,通过煤气流量调节阀FRCA102控制稳定其流量;
通过HIC101b调节燃气量,控制B101a盘管出口气温度TI-166(TI-176)≯首先加热催化剂床层温度50℃,调节床层升温速率为20~50℃/h,通过升温管线对串联的脱硫转化系统进行升温。
2、当首先加热的D101ab床层温度升到120℃时,打开D102升温线阀门,同时关小D101ab升温线阀,关闭D101ab出口阀,用其放空阀控制压力为0.3~0.5MPa,120℃恒温2~3小时。
D102催化剂则成为首先加热对象。
3、当D102床层温度达120℃时,打开并联的D103ab升温线阀,同时关小D102升温线阀,关闭D102出口阀,用其放空阀控制压力为0.3~0.5MPa,120℃恒温2~3小时。
并联的D103ab催化剂则成为首先加热对象。
4、当D103ab温度达120℃时,打开D104升温线阀,同时关小并联的D103ab升温线阀。
关闭D103ab出口阀,用其放空阀控制压力为0.3~0.5MPa,120℃恒温2~3小时。
D104催化剂则成为首先加热对象。
5、当D104床层温度达120℃时,打开关联的D105ab升温线阀,同时关小D104升温线阀,并关闭D104出口阀,用其放空阀控制压力为0.3~0.5MPa,120℃恒温2~3小时。
并联的D105ab成为首先加热对象。
6、当D105ab床层温度达120℃时,关小D105ab升温线阀,关闭D105ab出口阀,用其放空阀控制压力为0.3~0.5MPa,120℃恒温2~3小时。
同时,打开B101a后煤气正路阀,加热N2沿主流程CG-0112线进到D101ab前,通过大旁路CG-0136隔离脱硫装置后,进入E103壳程,对转化系统继续进行升温。
7、当D105ab恒温2~3小时后,(D105前面的催化剂120℃恒温均已大于2~3小时),再将D101ab到D105ab及转化系统串联,继续以30~50℃/h速率升温。
脱硫装置大旁路阀可用于调节转化系统温度。
8、当D105ab升温到220℃时,按
(2)~(7)方式操作,220℃各槽依次切除恒温4~5小时。
三、加氢催化剂的硫化
1、硫化条件及合格标准
(1)系统N2置换合格
(2)硫化剂为高硫焦炉气或焦炉气+CS2。
本工艺采用焦炉气+CS2。
气体中含S量:
0.5~1.5%(vol),O2≤0.2%(vol%)
(3)空速为200~500h-1(空速:
气体标准m3气/m3催化剂·
h)。
(4)压力:
控制系统压力≤0.5MPa
(5)硫化合格标准:
加氢槽进出口气体中硫含量相等时,则加氢催化剂硫化结束。
2、硫化
加氢催化剂硫化时,特别是采用CS2,反应剧烈,要一槽一槽地进行。
铁钼预加氢、铁钼加氢及铁钼加氢催化剂串联硫化。
将C201加压后的N2流程改走N2管道,即加压后的N2直接进入B101a盘管内加热后,沿升温线并联进入脱S各槽保温保压。
注:
铁钼预加氢槽D101ab两槽,开车时只硫化一槽,另一槽隔离,待开车过程中加入少许含硫煤气逐渐硫化。
启动备用煤气压缩机C201加压含硫焦炉气。
焦炉气沿主流程与N2混合进入B101a盘管内加热,加热温度未达220℃前煤气在B101a后放空。
煤气温度达220℃后沿主煤气流程线CG-0112进入D101a或b、D102,从D102出来的N2+煤气沿旁路进入D104,对三个槽的加氢催化剂串联硫化,同时关闭D102、D104并联的N2阀。
硫化初始,控制焦炉气+N2中H2S较低含量,随着硫化反应的进行,逐渐减小N2量,加大焦炉气量,控制混合气量≥3000Nm3/h。
因焦炉煤气含硫高,所以不可以进入D103ab与D105ab。
D103ab用过热蒸汽继续升温,D105ab则切除用N2保温保压。
向串联的铁钼预加氢槽D101a或b、铁钼加氢槽D102及镍钼加氢槽D104内导入含硫焦炉气,通过D104后的放空阀放空,在低压下进行硫化反应,压力控制在0.3MPa。
导入焦炉气后,调节B101a燃气量控制铁钼预加氢槽D101a或b床层温度为200~220℃,恒温1h以上,待催化剂床层温度均匀后,用N2将CS2加压通过硫化线加入D101a或b。
控制升温速率30~50℃/h,升温到250℃,恒温12~24h或更长时间进行等温硫化。
硫化初期,配入CS2后,分析入口气中H2S≤10g/Nm3,即用未经湿法脱硫的焦炉气。
硫化主期,需逐步增加CS2量,分析入口气H2S≤10~20mg/Nm3。
CS2加入量通过流量计及分析数据控制初始加入量30L/h,缓慢增加。
250℃恒温12~24h后,逐步关放空阀,将压力以0.2~0.5MPa/h的速率提高到1.0~1.2MPa,继续硫化。
压力达到需求后,稳定1小时,以20℃/h升温速率,控制催化剂床层温度<350~380℃,恒温恒压12~24h。
注意:
升压时不允许同时升温;
同样,升温时不允许同时升压。
B101a出口焦炉气温度根据催化剂床层温度调节。
使用CS2硫化时反应剧烈,放热量大,要控制D101a或b进口焦炉气温度为280~300℃(如果使用高硫焦炉煤气硫化,则控制D101a或b进口焦炉气温度为300~320℃)。
严格控制床层热点温度<450℃,若有超温趋势,立即降低入口气温度,必要时打开冷激线CG-0200进D101ab的阀门冷激降温(D106ab出口煤气→各加氢槽),均设有冷激线。
当D101ab进出口硫含量基本相等时,则铁钼预加氢催化剂硫化基本结束。
然后通过调节B101a出口焦炉气温度逐渐提高床层温度至380~400℃,但最高不得超过450℃,恒温2h。
分析D101ab进出口气体硫含量不变停止加入CS2,则铁钼预加氢催化剂硫化结束。
铁钼预加氢催化剂硫化时,串联的铁钼加氢及镍钼加氢催化剂同时在硫化。
D101a或b硫化结束,切除D101a或b保温保压,按照同样的程序对铁钼及镍钼加氢催化剂D102、D104进行串联硫化。
D102、D104串联硫化时,将焦炉气温度及床层温度降到250℃,加热焦炉气沿升温线进入D102内,再开始向D102内配入CS2,以防温升太快。
3、放硫
放硫即将硫化过程中吸附在催化剂床层中的硫充分释放出来。
D104硫化结束后,将D101a或b、D102、D104串联起来,控制床层温度为380℃左右,将系统压力逐渐降至0.1~0.2MPa,将焦炉气切换为湿法脱硫后的合格低硫(S≤20mg/m3)焦炉气吹扫硫化后的催化剂。
吹扫催化剂要有足够时间释放床层中的H2S,分析进出口H2S含量不变,则放硫结束。
放硫结束后,将系统压力逐步提高到0.5MPa,关闭进出口阀及放空阀,保温保压。
四个加氢槽的催化剂串联硫化时,硫化过程是按前后顺序一槽一槽地进行。
硫化反应首先在第一槽进行,当第一槽中催化剂吸附硫较多时,开始有H2S穿透,第二槽催化剂开始有较强的硫化反应。
串联硫化的温度最高点在首先硫化的第一槽即铁钼预加氢槽,控制好其床层温度非常重要。
串联硫化时,热量及焦炉气利用充分。
第二槽开始硫化时,要先配入含S浓度较低的焦炉气,将入口气温度控制在250~280℃左右才可进行。
4、附:
加氢催化剂升温硫化表
加氢催化剂硫化项目分析表
加氢催化剂升温硫化及放硫曲线
温度范围
升温升压
速率
时间
(h)
介质
流量
压力MPa
说明
常温-120℃
20℃/h
5-6
N2
3000-4000
0.3-0.5
驱赶水
120℃
恒温
2-3
220℃
30-50℃/h
4-5
1
未脱硫焦炉气
小气量
≤0.5MPa
开始硫化
250℃
30℃/h
12-24h
等温硫化
0.5MPa/h
焦炉气+CS2
1.0-1.2MPa
硫化初期
恒压
硫化主期
350-380℃
380-400℃
2
硫化末期
0.1-0.2MPa
放硫
充分
硫化
合格的湿法脱硫气
0.5MPa
保温保压
1、升温还原曲线按厂家提供的方案执行。
2、D101ab铁钼预加氢催化剂硫化时间约为70~80小时。
3、精脱硫系统加氢催化剂全部硫化结束约130~150小时。
加氢催化剂硫化过程分析一览表
序号
位号
取样地点
分析项目
分析频次
CO
CO2
H2
CH4
S
每小时分析一次S,其余依工艺要求分析。
S-101
D106ab前
S-102
D101a后
3
S-103
D101b后
4
S-104
D102后
5
S-105
D104后
四、铁锰脱硫剂还原
加氢催化剂硫化结束后,铁锰脱硫剂开始进行升温还原。
升温可以用N2作介质,也可以用过热蒸汽作介质。
本装置用N2作升温介质。
(一)升温还原过程控制
1、升温流程(以N2作为升温介质)
N2→C201→N2路线→B101a盘管内升温→升温管线进入D103ab→放空
2、配焦炉气还原铁锰脱硫催化剂
(1)还原流程
焦炉气→C201→焦炉气主线→CG-0107→CG-0108(B101a旁路,即焦炉气不经加热)→D101ab前→CG-0140管线(还原线路)并联进入D103ab→放空
(2)还原过程控制
D103ab催化剂床层温度用N2维持220℃,D103ab出口放空,控制系统尽可能低压力,一般控制为0.1~0.2MPa。
系统配H2。
通过FRCA102阀调节焦炉气量,打开还原线路DN25旁路阀,控制焦炉气量FI-104,焦炉气与N2混合并联进入D103ab,严格控制起始浓度CO+H2≤0.5%。
即N2量控制3000Nm3/h,焦炉气量FI-104为30Nm3/h。
配氢时,控制焦炉气压力大于N2压力0.1-0.2MPa。
配H2后每小时分析一次进出口CO、H2浓度,以观察还原进行程度。
控制床层温升10℃/h,床层温度控制在250~350℃,若还原激烈,温升过快,可通过MS-0109管线阀门加入过热蒸汽调节降温或者调节B101a出口N2温度,以控制温升。
根据床层温度及进出口H2浓度变化情况,逐步提高H2浓度,通过提H2浓度,控制床层温度≥350℃,但最高不超过400℃。
提高氢量时不允许同时提高温度,提高温度时不允许同时提高氢量。
当床层热点下移,温度在350℃,H2浓度在20%左右,进出口H2浓度消耗无明显变化时,恒温10~16h,然后逐渐减小蒸汽量至全停蒸汽,同时减小N2量控制混合气量中H2浓度为20℅,提高H2浓度1h后无明显温升,无反应水析出,无H2耗,则还原结束。
铁锰催化剂升温还原,也可全部采用过热蒸汽作载体配焦炉气进行。
过热蒸汽温度TI-1302控制在300~340℃为宜(此温度由电厂来的蒸汽决定)。
不允许带水,升温速率控制为20~30℃/h。
(二)附:
铁锰催化剂还原
铁锰还原项目分析
升温速度控制表(升温曲线,以热点为准)
温度℃
速率℃/h
压力
常-120
20
0.8
出水、升温
120
恒
8
120-270
10
1.0
蒸气
升温
270
蒸气+焦炉气
开始还原
270-400
15
13
还原
400
焦炉气
彻底还原
累计
60
注:
升温还原曲线以厂家提供的方案为准。
铁锰还原过程分析项目
每半小时分析一次CO、O2、H2,其余依要求分析。
D103a后
S-106
D103b后
五、氧化锌脱硫剂
氧化锌脱硫剂不需要还原操作。
在加氢催化剂硫化及铁锰脱硫剂还原期间,将其切除用N2保温保压。
待加氢催化剂硫化及铁锰脱硫剂还原结束后,氧化锌槽串入升温流程,用N2升温,以50℃/h速率升温,温度升到320~350℃,恒温4小时。
六、精脱硫全系统开车
1、氧化锌320~350℃恒温四小时,至此,精脱硫催化剂的升温硫化还原结束。
2、将焦炉气按主流程加入精脱硫系统,逐步将N2减小直至关闭。
焦炉气通过B101a加热(逐渐关闭旁路),将各催化剂床层温度控制在300~400℃。
3、分析焦炉气中S≤0.1ppm,精脱硫系统开车正常。
准备将合格焦炉气导入转化系统。
4、精脱硫系统运行正常后,视催化剂床层温度,逐渐打开B101a旁路,将B101a燃气量逐渐关小,随着转化系统的开车及热量的供给,开工加热炉B101a逐渐全部退出系统。
七、精脱硫转化系统安全技术方案
(一)精脱硫加氢催化剂硫化安全技术方案
1、精脱硫系统N2置换。
(1)置换流程:
用升温流程对精脱硫系统进行N2置换。
(2)应开的阀门:
依置换流程路线,阀门开关情况:
C201到D105ab所有主线阀门均应打开。
每个导淋、放空阀需逐个打开放空,以置换死角。
D101ab、D102、D104四个加氢槽硫化副线阀门打开。
D103ab铁锰槽还原副线阀打开。
D106至D101ab、D102、D104的冷激副线阀门打开。
升温炉B101b副线阀门打开。
C201出口N2阀门及N2主脱硫系统九个槽(包括CS2)的N2管线上的盲板均要抽去,阀门均要打开。
(3)N2置换合格标准
置换时依流程合理设置若干个排放点,逐段管道、逐台设备从前到后依次进行置换,合格后进行下一步置换,直至每个系统合格为止。
置换方法及合格标准:
用N2重复升压泄压,直至系统各个排气分析合格,关闭排放阀,分析气体氧含量均小于0.5℅(包括放空管道)为合格。
2、加热炉系统置换
(1)燃气管线置换
打开C201二段出口燃料气阀门,将N2导入B101a、B101b炉膛内,从进炉前燃气管放空处分析,O2≤0.5℅,燃气管线置换合格。
(2)加热炉膛置换
加热炉膛与大气相通,开车前用蒸汽置换炉膛,分析CO+H2<0.5℅为合格。
3、CS2的安全操作:
(1)CS2性质
CS2为无色透明液体,有刺激性气味。
易挥发。
不溶于水。
受热分解产生有毒的氧化硫烟气。
其沸点:
46.3℃,相对密度:
1.26,较水重。
具有爆炸性,其蒸气与空气混合形成浓度范围广阔(1-60%vol)的爆炸性气体,高速冲击、流动、激荡后可因静电火花放电引起爆炸。
极度易燃,闪点很低:
-30℃,适明火或氧化剂易引起燃烧、爆炸,产生有毒烟气。
(2)CS2的安全操作
CS2贮槽内预先旋转适量水。
卸压时,将CS2导管插入水下,将CS2导入水面下与空气隔离。
CS2贮槽周围要设置隔离区。
CS2贮槽周围要配备干粉CO2、泡沫灭火器及沙土等。
CS2着火用其无效时,可用水灭。
贮槽内剩余的CS2要妥善保存,定期检查。
4、倒换盲板的操作
(1)依工艺系统将盲板编号登记造册。
(2)需要倒换盲板的设备、管道置换合格。
(3)关闭紧邻盲板的阀门。
(4)依工艺要求倒换盲板。
5、事故状态的操作
(1)设备或管道有较大的焦炉气泄漏,立即关闭焦炉气进界区总阀XV-101及压缩机C201出口缓冲罐出口阀,必要时停煤压机C201及F202,以防着火爆炸。
(2)加氢催化剂硫化过程中出现超温,降低加热炉出口温度,或打开冷激线降温,或减小焦炉气量,必要时切断焦炉气,以防超温烧损催化剂。
(3)铁锰催化还原过程中出现超温,降低加热炉出口温度,或减小气量,或打开蒸汽阀加蒸汽,降低床层温度,必要时切断焦炉气,以防超温烧损催化剂。
(二)精脱硫铁锰催化剂还原安全技术方案
1、升温速率严格按供货商提供的升温速率控制,一般控制为20~40℃/h。
2、当床层温度达250~350℃时,要密切注意,有可能出现温度飞升现象,此时要立即减少配氢量,放慢升温速率,同时加大蒸汽量,增大放空量,及时移走反应热。
3、严格要求焦炉气中O2≤0.5%,否则催化剂床层会出现超温而损坏。
八、精脱硫催化剂硫化还原简略计算
(一)硫化
1、要求:
(1)空速为200~500h-1
(2)气体中S含量为0.5~1.5℅(vol)
(3)气体中O2<0.2℅(v)
(4)空分N2量≥3000~4000Nm3/h
2、加氢催化剂相关计算
(1)升温
铁钼预加氢催化剂:
催化剂体积v=8m3×
2台
通过催化剂床层气量Q=(200~500)×
8×
2=3200~8000Nm3/h
因空分只能提供约4000Nm3/hN2,所以FRCA102控制氮气量为4000Nm3/h。
每台催化剂通过的气量Q单=4000/2=2000Nm3/h,空速==250h-1。
催化剂为常温20~30℃,加热后的N2温度≯床层温度50℃,即开始时加热后的N2温度为80~90℃,并以30~50℃/h速率升温,约5小时升到120℃。
铁钼加氢催化剂
催化剂体积v=12m3
通过催化剂床层气量Q=4000Nm3/h,空速=4000/12=330h-
N2通过D101ab降温后,串联进入D102,对D102催化剂加热升温。
镍钼加氢催化剂
催化剂体积v=13m3
通过催化剂床层气量Q=4000Nm3/h,空速=300h-
从D102出来的N2串联进入D105内,对D105内催化剂加热升温。
升温速率控制
升温速率为30~50℃/h。
用调节阀FRCA102控制载热介质N2流量,稳定为4000Nm3/h。
通过HIC102ab调节燃料气量FI-122,控制出口N2温度≯床层温度50℃,控制升温速率。
FI-122正常生产时为1500Nm3/h。
(2)硫化
焦炉气量及硫含量
将未经湿法脱硫的焦炉气引入精脱硫系统。
其硫含量约≤7g/Nm3。
通过FRCA102控制焦炉气量4000Nm3/h。
则硫化初期,用含硫焦炉气即可。
焦炉气中配入CS2,控制焦炉气中H2S含量为10~20g/Nm3。
随着硫化的进行,要求焦炉气中H2S含量为10~20g/Nm3。
仅靠焦炉气中的H2S,其浓度不够,需向焦炉气中配入CS2,以提高H2S浓度至10~20g/Nm3。
焦