斜联结管数控加工和工艺.docx
《斜联结管数控加工和工艺.docx》由会员分享,可在线阅读,更多相关《斜联结管数控加工和工艺.docx(16页珍藏版)》请在冰豆网上搜索。
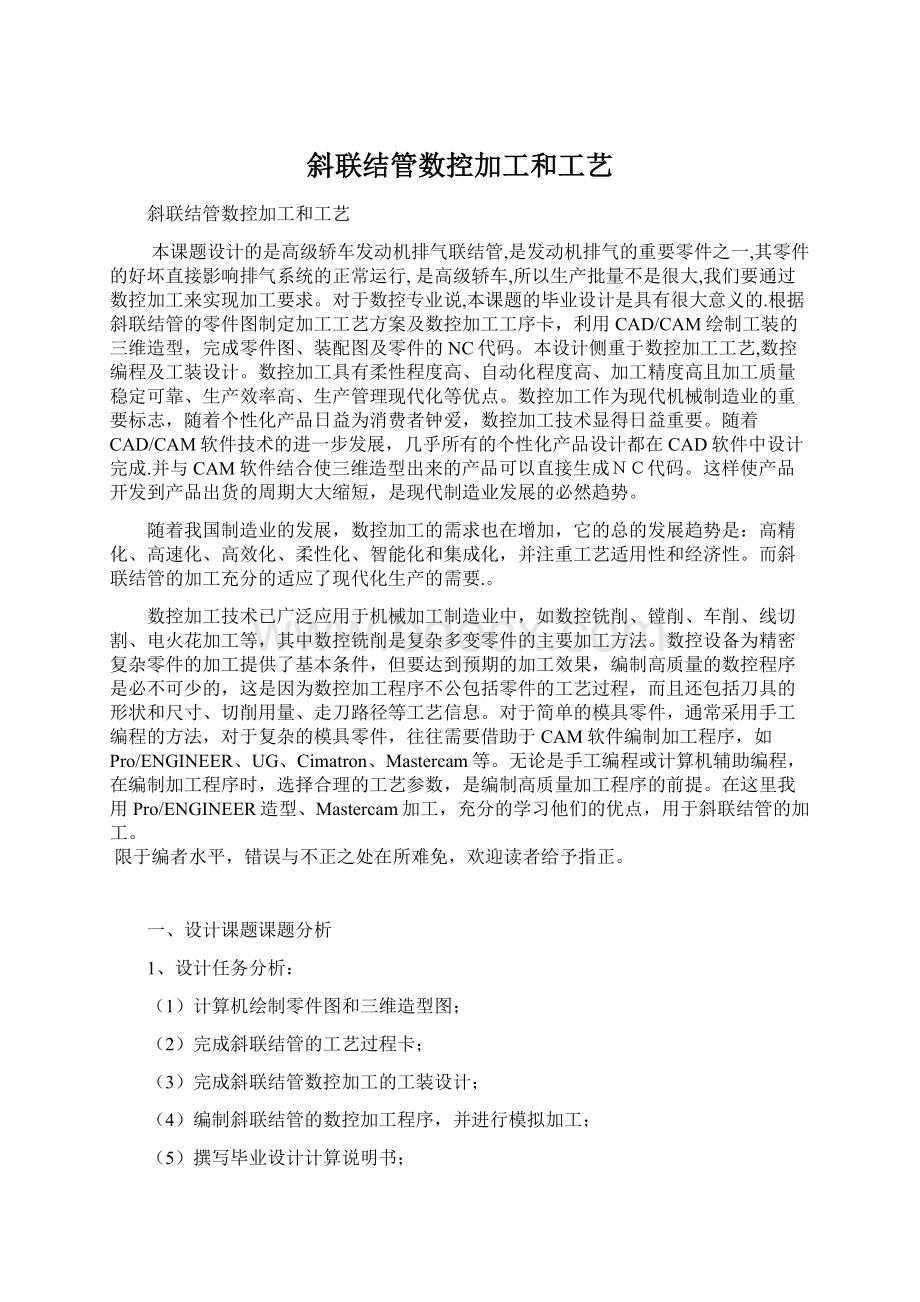
斜联结管数控加工和工艺
斜联结管数控加工和工艺
本课题设计的是高级轿车发动机排气联结管,是发动机排气的重要零件之一,其零件的好坏直接影响排气系统的正常运行,是高级轿车,所以生产批量不是很大,我们要通过数控加工来实现加工要求。
对于数控专业说,本课题的毕业设计是具有很大意义的.根据斜联结管的零件图制定加工工艺方案及数控加工工序卡,利用CAD/CAM绘制工装的三维造型,完成零件图、装配图及零件的NC代码。
本设计侧重于数控加工工艺,数控编程及工装设计。
数控加工具有柔性程度高、自动化程度高、加工精度高且加工质量稳定可靠、生产效率高、生产管理现代化等优点。
数控加工作为现代机械制造业的重要标志,随着个性化产品日益为消费者钟爱,数控加工技术显得日益重要。
随着CAD/CAM软件技术的进一步发展,几乎所有的个性化产品设计都在CAD软件中设计完成.并与CAM软件结合使三维造型出来的产品可以直接生成NC代码。
这样使产品开发到产品出货的周期大大缩短,是现代制造业发展的必然趋势。
随着我国制造业的发展,数控加工的需求也在增加,它的总的发展趋势是:
高精化、高速化、高效化、柔性化、智能化和集成化,并注重工艺适用性和经济性。
而斜联结管的加工充分的适应了现代化生产的需要.。
数控加工技术已广泛应用于机械加工制造业中,如数控铣削、镗削、车削、线切割、电火花加工等,其中数控铣削是复杂多变零件的主要加工方法。
数控设备为精密复杂零件的加工提供了基本条件,但要达到预期的加工效果,编制高质量的数控程序是必不可少的,这是因为数控加工程序不公包括零件的工艺过程,而且还包括刀具的形状和尺寸、切削用量、走刀路径等工艺信息。
对于简单的模具零件,通常采用手工编程的方法,对于复杂的模具零件,往往需要借助于CAM软件编制加工程序,如Pro/ENGINEER、UG、Cimatron、Mastercam等。
无论是手工编程或计算机辅助编程,在编制加工程序时,选择合理的工艺参数,是编制高质量加工程序的前提。
在这里我用Pro/ENGINEER造型、Mastercam加工,充分的学习他们的优点,用于斜联结管的加工。
限于编者水平,错误与不正之处在所难免,欢迎读者给予指正。
一、设计课题课题分析
1、设计任务分析:
(1)计算机绘制零件图和三维造型图;
(2)完成斜联结管的工艺过程卡;
(3)完成斜联结管数控加工的工装设计;
(4)编制斜联结管的数控加工程序,并进行模拟加工;
(5)撰写毕业设计计算说明书;
(6)参加毕业设计答辩。
二、工件的结构分析
1、斜联结管是一个弯管,就是周围分布着有规律的六根肋板,还有一个75度直径为38的孔。
对于弯管的数控铣削加工必须满足以下要求:
(1)、斜联结管加工前要先用车床做,图1、然后在钻床上加工,再要在数控铣床上前把肋板加工出来,加工肋板时必须要利用分度头来保证肋板分布时的加工。
图1
(2)、斜联结管的孔加工时需要保证加工孔的轴心线与主轴的同轴度,保证同轴度需要夹具体来保证斜联结管的底面与底板成15度,由于这个孔精度要达到H9,所以造成了难度,我们现在是以四个一起加工,来提高效率、图2。
图2
三、三维建模
我们这个斜联结管加工必须要用软件造型,我们这个课程设计说白了老师就给了我们一张二维的图纸,上面尺寸也不是全,所以需要我们自己去设计,我先用Pro/ENGINEER把图用三维造出来,这样看上去非常直观,对这个零件可谓是心领神会,图3、
图3
但是把这个图转换到Mastercam加工时却不能加工,原因是在转换中有些数据丢失,无法加工,所以我有在这软件中造型,并且进行加工,编程等。
图4
图4
四、数控铣削加工工艺分析
数控铣床加工的零件主要有;
1、曲线轮廓类零件
曲线轮廓类零件指要求有内、外复杂曲线轮廓的零件,特别是由数学表达式等给出其轮廓为非圆曲线或列表曲线的零件。
2、空间曲面类零件。
空间曲面类零件指由数学模型设计出的,并具有三维空间曲面的零件。
3、复杂零件
复杂零件指形状复杂,尺寸繁多,划线与检测均较困难,在普通铣床上加工又难以观察和控制的零件。
4、高精度零件
高精度零件指尺寸精度、形位精度和表面粗糙度等较高的零件。
如发动机缸体上的多组高精度孔或型面。
5、一致性要求好的零件
在批量生产中,由于数控铣床本身的定位精度和重复定位精度都较高,能够避免在普通铣床加工中,因人为因素而造成的多种误差。
故数控铣床容易保证成批零件的一致性,使其加工精度得到提高,质量更加稳定。
同时,因数控铣床加工的自动化程度高,还可以大大提高作者的体力劳动强度,显著提高其生产效率。
该零件为中小批量生产,我们是用棒料加工,我们是先在车床上把棒料的长度和底面圆的直径控制好,再到钻床上把3个直径为6的孔打好,再加上一个直径12的通孔,为下面做准备,然后到数控铣床上加工肋板,肋板的加工在这里就不详细的介绍了,我们这里特别介绍直径38H9的孔,这个孔精度要求有点高,而且表面粗糙度值为Ra1.6,有为了提高产量还有加工的效率,我们特地设计一次性加工四个的夹具来满足加工的效率,把四个的精度全做到,这要有一定的技术。
这个Φ38H9的孔加工,我们是把它固定在斜度为15度的夹具体上,图五、然后把夹具体放在底板上,用这个Φ80图柱用来定位,用3个Φ6的孔用来夹紧加定位来确保Φ的精度。
五、工艺工序安排
1、以下我们对些零件进行工艺安排:
下料→车削→车削→钻孔→铣削→钻孔→去毛刺→检验→油封
下料:
Φ96x62
车削:
车左端面及外圆Φ90。
粗台阶、Φ80。
车削:
粗车右端面至56。
钻孔:
钻孔3个Φ6深8孔。
铣削;铣外形的6个分布均匀的肋板及顶面。
钻削:
钻Φ37.5、扩孔Φ37.85、铰孔Φ38H9。
钳工:
去毛刺。
检:
检验。
油封:
清理、油封、入库。
六、切削用量的确定
正确地确定切削用量,对保证加工质量、提高生产率、获得良好的经济效益,都有着重要的意义。
在确定切削用量时,应综合考虑零件的生产纲领、加工精度、和表面粗糙度、材料、刀具的材料及耐用度等方面因素。
单件小批量生产时,为了简化工艺文件,常不具体规定切削用量,而由操作者根据实际情况,凭经验确定合理的切用量。
成批及大量生产时,特别是组合机床、自动机床及多刀加工工序的切削用量,应科学地、严格地确定,确定的一般原则为:
粗加工时,由于要求的加工精度较低、表面粗糙度较大,切削用量的确定应该尽可能保证较高的金属切除北和必要的刀具耐用度,以达到较高的生产率。
提高切削速度、增大进给量和切削深度,都能提高金属切除率,但在这三个要素中,切削速度对刀具耐用度影响最大,其次是进给量,影响最小的是切削深度。
所以在确定粗加工切削用量时,应优先考虑采用大的切削深度,其次考虑采用较大的进给量,最后根据刀具的耐用度要求,确定合理的切削速度。
具体数据的确定可参阅有关手册。
半精加工、精加工时,确定切削用量首先要考虑的问题是保证加工精度和表面质量同时也要兼顾必要的刀具耐用度和生产率。
半精加工、精加工时的切削深度一般根据粗加工后留下的加工余量来确定,而进给量主要根据表面粗糙度来确定。
为了减少工艺系统的弹性变形和已加工表面的残留面积高度,半精加工和精加工时一般多采用较小的切削深度和进给量。
在切削深度和进给量确定之后,再确定合理的切削速度。
在采用组合机床、自动机床等多刀具同时加工的工序时,其加工精度、生产率和刀具的寿命与切削用量的关系很大,为保证机床正常工作,不经常换刀,其切削用量要比采用一般机床加工时低一些。
以下是Φ38H9切削加工:
曲面挖槽粗加工生成一系列平面铣削,是一种最常用的曲面粗加工方法。
它还可以使刀具从零件毛坯外开始加工,防止刀具直接埋入工件材料。
调出图形文件:
曲面挖槽粗加工、图六。
图六、曲面挖槽粗加工零件图
选择“刀具路径→曲面加工→粗加工(如图所示、图七)→挖槽粗加工→实体”命令,设曲面/实体/CAD为设实体图素为然后按执行:
图七图八
选取要加工面1、2如图所示、图九。
选取14.0的平刀。
这里我们用平头端铣刀替代球
图九
头刀来粗加工面,可以加快除去毛坯材料。
在弹出的“曲面粗加工”视窗口选择“曲面加工参数”选项卡,设置选给下刀位置为2.0,参考高度为10.0,加工预留量为1.0,如图十所示。
图十、曲面加工参数
在“刀具包含”中单击“选择”中。
在“挖槽粗加工参数‘选项卡中,选择等距环切削方式,并且精修量,为0.2,’选中“精修切削范围的轮廓”。
如图十一所示。
选中“螺旋式下刀”并单击,在弹出的对话框中选择“螺旋式下刀”选项卡,参数设置如图十二所示。
图十一、曲面加工参数
单击“确定”“确定”。
系统计算出刀具加工轨迹,如图十三所示。
可以看出开始刀具从定义的切削范围外下刀,然后在等Z值高度一层层加工,每层间下降的距离不大于设定的最大Z轴进给量2.0。
虽然这是一种挖槽曲面粗加工方法,但它也能粗加工零件外表面的凸起部分。
本例中采用等距切削方式,这种方式能够更多地切除毛坯材料,更有效地完成粗加工。
图十三,曲面挖槽粗加工刀具路径
工件设定如图十四所示。
我们所选的是圆柱
图十四、参数设定
实体切削仿真结果如图十五所示:
图十五、实体仿真
流线曲面精加工
流线曲面精加工,可以沿着曲面流线方向生成光滑和流线型的刀具路径,它种曲面平行精度加工不同,后者以一定的角度加工,并不沿着曲面流线加工,因此可能会有许多空切削。
曲面流线精加工可以精确控制工件的残脊加工高度,因此可以产生一精确,平滑的刀具路径。
这种加工方法是早期单一曲面加工方法的改良。
选择“刀具路径曲面精加工流线加工”命令。
弹出“曲面精加工”对话框,选取12.0的球刀,在“击曲面加工参数”选项卡中,参数设置如图十六所示。
图十六、曲面加工参数、选项卡
在“曲面流线精加工参数”选项卡中,在“截断方向的控制”项中,设定残脊高度为0.04,参数设置如图十七。
确定。
图十七、曲面流线精加工参数、选项卡
结果流线曲面精加工刀具路径如图十八所示。
图十八、流线精加工刀具路径
七、夹具体的设计
为了保证工件的加工要求,必须使工件在机床上处于准确的位置,夹具就是用来实现这一要求的。
1、定位方式的选择
根基准统一的原则,我们采用设计基准来作为我们的定位基准,即采取一面二孔的形式进行定位。
2、夹紧方式的选择
夹紧方式的确定,起初我考虑各种各样的方案,但是都没有成形,最后我考虑用3个螺纹孔来夹紧。
我的夹具设计的主要元件如图十九所示:
图十九、夹具体
八、数控加工
为了提高效率,我采用Mastercam自动编程软件进行加工,加工程序如下:
%
O0000/*程序名
N100G21/*采用公制单位
N102G0G17G40G49G80G90/*刀具半径补偿取消、绝对坐标编程
N104T1M6/*换到1号刀位
N106G0G90X-2.521Y2.275A0.S1637M3/*主轴正转快速到一点
N108G43H1Z70.809/*给1号刀具长度补偿
……………………
……………………
N4112G28X0.Y0.A0./*返回到原点参考点
N4114M01/*程序选择停止
N4116T2M6/*换到2号刀位
N4118G0G90X-12.715Y3.457A0.S1273M3/*主轴正转快速到一点
N4120G43H2Z50./*给2号刀具长度正补偿
……………………
……………………
N9026M5/*程序停止
N9028G91G28Z0./*增量坐标编程
N9030G28X0.Y0.A0./*参考点返回
N9032M30/*程序结束