人造板思考题答案整理Word下载.docx
《人造板思考题答案整理Word下载.docx》由会员分享,可在线阅读,更多相关《人造板思考题答案整理Word下载.docx(6页珍藏版)》请在冰豆网上搜索。
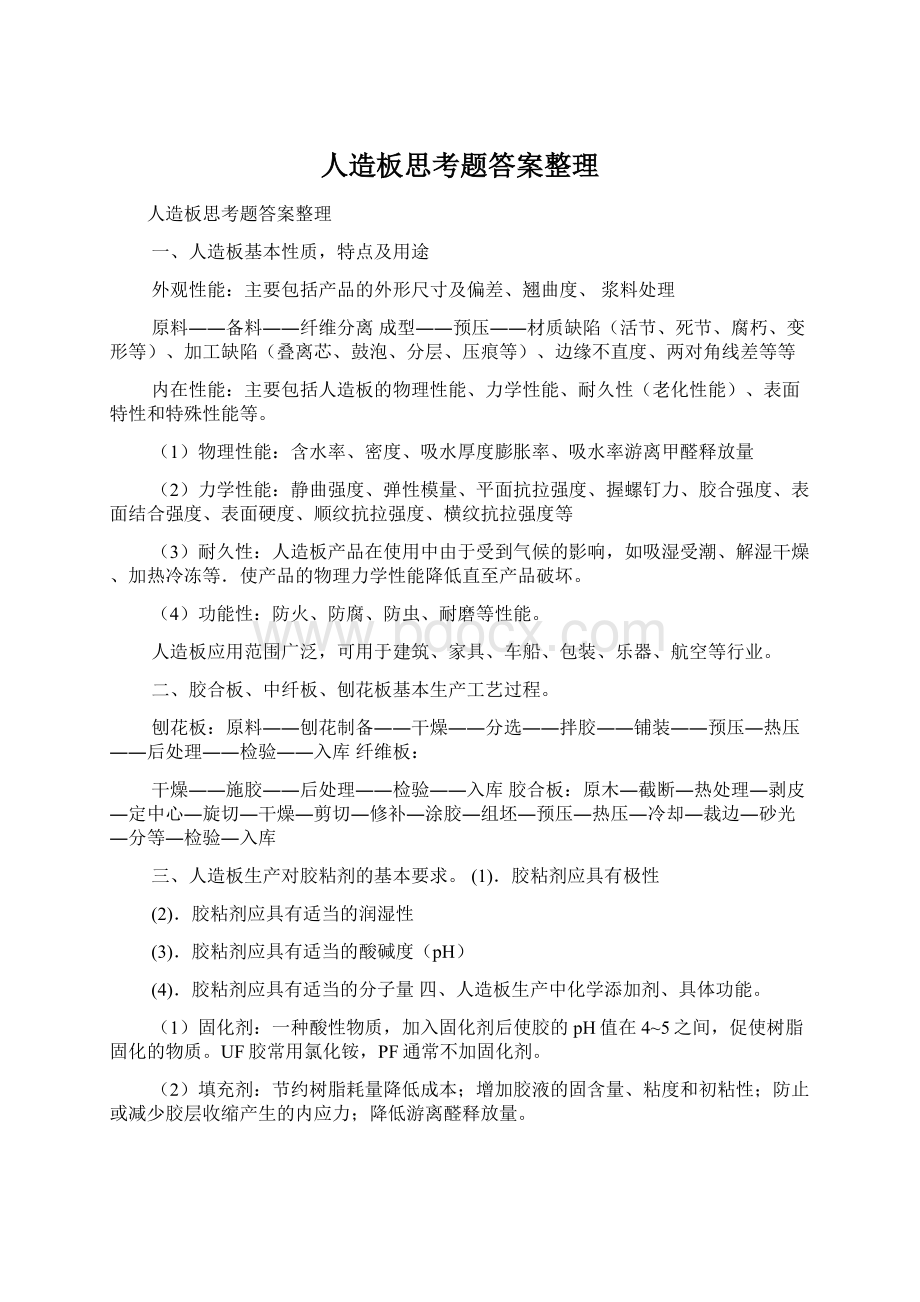
UF胶常用氯化铵,PF通常不加固化剂。
(2)填充剂:
节约树脂耗量降低成本;
增加胶液的固含量、粘度和初粘性;
防止或减少胶层收缩产生的内应力;
降低游离醛释放量。
(3)防水剂:
提高板制品的耐水性,改善尺寸稳定性,堵塞了刨花之间与纤维之间的空隙;
增大了水与刨花或纤维之间的接触角;
部分遮盖了物料表面的极性官能团,降低了吸附作用。
(4)阻燃剂:
一定程度上降低烟的产生,减轻明火燃烧和火焰的蔓延,但一般防火剂不能对上述三种情况同时制
止。
(5)防腐剂
防止、抑制或中止危害木质基材的细菌、微生物及昆虫的侵害。
要求对各种真菌、细菌和昆虫有杀伤力,但在处理过程中,对人、畜和环境无污染;
化学稳定性好,不易挥发,不会遇水流失;
与胶粘剂有好的协效性,不影响胶合强度和表面装饰五、木段旋切的工作原理与受力分析
旋切:
木段作定轴回转运动,旋刀作直线进给运动时,旋刀刀刃基本平行于木材纤维,而又垂直木材纤维长度方向向上的切削。
单板厚度:
等于木段回转一圈时,刀架的进刀量。
为了旋得平整、厚度均匀的带状单板,在旋切时,应保证最佳的旋切条件。
切削条件:
旋刀的位置(h―旋刀刀刃和通过卡轴中心水平面之间的垂直距离);
压尺相对旋刀的位置。
这些条件是根据木材的树种、木段直径、旋切单板厚度、木材水热处理和机床(旋切机)精度等来确定。
(1)旋刀作用力
P1:
旋刀前面对已旋出单板的劈力。
P2:
旋刀对木段上单板切削力。
P3:
旋刀后面对木段的压力。
在P1作用下,单板由原来自然状态变到反向弯曲状态,使单板内部产生应力。
由于木材横纹抗拉强度较低,结果在单板背面产生了大量超前裂缝,单板的背面(松面)高低不平,单板的正面(紧面)仅有凹陷。
降低了单板质量。
为了消除这些缺陷,应该正确地使用压尺。
切削力P2将木段旋切成单板
压木段力P3要保持正常旋切,旋刀后面对木段的压力必须存在,应尽量使其值稳定。
(2)压尺的作用力
应该使压尺的作用防止由于旋刀作用力P1所引起的劈裂现象。
由于单板被压缩,其横纹抗拉强度有所增加,这对减少单板背面的裂缝是有益的。
压榨力同单板的压榨程度有关,压榨力P0越大则压榨程度也越大主要角度参数:
旋刀研磨角(β):
旋刀的前面与后面
之间的夹角。
旋刀对着木段的一个面是后面(即旋刀的斜面)。
β值的大小,β值一般采用18~23°
。
为了要旋得优质单板,尽可能减少β值。
当其他条件相同,旋切硬、厚单板、节多的木材时,应当采用较大的β值后角(α):
旋刀的后面与旋刀刀刃处旋切曲线的切线CP之间的夹角。
切削角(δ):
切线CP与旋刀前面之间夹角,即旋刀的研磨角和后角之和
为了提高稳定旋切质量和旋刀正常使寿命,采用研磨微楔角的旋刀。
其研磨角β可为19°
,但其微楔角可为单面或双面,其值约为25~30°
后角大小的确定:
旋切时β值不变。
当改变α值时,δ相应改变。
α值过大,在单板离开木段的瞬间,单板伸直,原料的弹塑性和外力作用频率是磨浆过程的两个主要因素:
磨浆时的单位压力和浆料浓度,也都直接影响浆料质量和磨浆速度
纤维分离目的:
提高纤维比表面积(单位重量的纤维所占反向弯曲变形大,单板背面易产生裂缝;
同时刀架易震动,单板成为瓦楞板。
α值过小,旋刀后面和木段表面的接触面积增大,产生较大的压力,导致木段劈裂或弯曲,小径级木段更易弯曲,单板厚度不均匀。
后角的大小实质:
反映了旋刀的后面与木段表面的接触面的大小,表示木段对旋刀支撑力的大小。
支撑力小则旋刀在旋切时稳定性能差,将会发生震动。
支撑力大,旋刀对木段推力大,使木段弯曲变形,旋切质量变差。
后角大小的变化:
为了保证正常的旋切条件,要求α值必须随着木段直径变小而减小。
一般在旋切过程中后角的变化范围在1~3°
之间较好;
木段直径大时,后角可为3~4°
,直径小时可为1°
六、纤维分离的原理。
磨浆理论:
磨浆过程中,木片或纤维在磨盘之间受到各种变动载荷作用,这种作用力以很快的速度从零到最大值交替变换着。
另外木片或纤维在磨浆条件下的应变性能又与它们本身的弹塑性有很大关系。
纤维分离的速度取决于两个基本因素:
原料受力变形后的弹性恢复速度、对原料的相邻两次作用力的时间间隔
有的总表面积),以增加纤维与纤维之间的结合力。
随着比表面积的增加,纤维表面上的游离羟基增加,这是形成纤维间各种结合力(胶化学结合、氢键、木素缩合)的内在条件。
软化目的:
木质原料软化处理目的是将原料进行软化,降低原料的硬度,增加可塑性,使其在人造板原料加工过程中,确保工艺所要求的尺寸、形状和质量以及减少制造能耗。
木段软化处理方法:
水煮、水与空气同时加热、蒸汽热处理。
七、纤维、刨花形态对板材性能的影响。
纤维形态:
一般长度大,长宽比大,细胞壁薄的纤维具有较好的交织能力
刨花形态:
刨花的几何形状(长、宽、厚对其表面积)对刨花板质量有较大影响,其中影响最大的是厚度。
一般刨花越薄,板的强度越高,但是过薄的刨花容易碎裂,很难保证刨花板的表面质量和强度要求。
刨花的长度对板的强度也有着影响,最适宜的长度取决于刨花本身的强度和刨花之间的接触面积,刨花过长会造成分布和施胶不均。
刨花的宽度对表面积和施胶量的影响比长度大,但是比厚度
小。
一般来说,薄刨花比厚刨花生产的刨花板静曲强度大,长刨花比短刨花生产的刨花板强度大。
选定刨花的尺寸时,还需要考虑形状系数,形状系数包括长细比,宽细比
,长宽比。
经验认为长细比为100~200,宽细比大于10,合调制成胶粘剂(Glue)
调胶目的:
较快的固化速度以提高生产率;
较高的胶合强度和耐水、耐老化性能;
较好的可操作性和一定活性期(3~4h);
胶粘剂调制工艺流程
而长宽比可根据种类与性质而定。
这样制得的板子,用胶量少,密度底,强度较高。
形状系数小,加压时边部容易溃散,裁边尺寸大,否则,板的边部强度很低。
形状系数大,给施胶和成型带来一定困难。
八、影响单板、纤维和刨花干燥的因素
影响单板干燥的因素:
a.干燥介质的影响:
热空气温度、热空气相对湿度、热空气风速、热空气喷射方式,b.单板本身条件的影响:
树种、含水率;
单板厚度;
影响纤维和刨花的因素:
a.干燥介质参数的影响:
介质温度;
介质相对湿度;
介质流速
b.物料本身条件的影响:
树种与初含水率;
物料形态c.干燥设备工作状态的影响:
输送浓度和充实系数、干燥辊筒安装角度和转速、物料在干燥机内的停留时间九、单板加工的内容、单板拼接方式
干燥后的单板加工包括单板分选、单板修补和单板胶拼,完成加工后的单板将被送入单板仓库贮存和调配使用。
单板拼接包括单板纵向接长、单板胶拼等内容十、胶粘剂调制的目的、要求、调胶工艺。
166
胶粘剂调制:
在树脂(Resin)中加入固化剂或其他添加剂(包括填料、缓冲剂、防水剂、防火剂和防腐剂等),混
调胶操作在混合器中进行。
混合器中的搅拌器转速140~150r/m,依次加入各组分,每次搅拌5~10min,加完所有组分后再搅拌15~20min即可。
十一、单板、纤维与刨花施胶类型、优缺点
单板施胶类型:
干法施胶:
胶膜法:
胶料分布均匀,胶合质量好,但胶模成本高,粉状上胶法:
均匀散落在大幅面基材表面;
液体施胶法:
辊筒施胶法:
结构简单,便于维护,但工艺性能差,不易控制。
淋胶:
高效率的施胶方法,挤胶:
节省胶料,但胶孔易堵塞,喷胶:
效率高,胶损小,但胶量控制较难。
纤维施胶类型:
热磨机磨室内胶:
混合均匀,但易引起部分胶提前固化;
纤维干燥后在拌胶机内施胶:
纤维易结团;
纤维干燥前在管道内施胶:
均匀混合,板面不出现胶斑;
纤维干燥后对含水率要求较低,工艺易掌握,节省能源,减少干燥过程着火可能性;
省去结构复杂的拌胶机。
刨花施胶类型:
摩擦法:
适用于细小刨花的拌胶;
涂布法:
用施胶辊将胶液涂在刨花表面。
适用于高粘度的胶液;
喷雾法气流式喷雾头:
适合喷胶量较低时使用。
操作比较方便,雾化胶滴较小,能处理含有少量固体的液体,但对密封要求较高,否则易污染环境;
离心式喷雾头:
适合于处
理含较多细小固形物的胶粘剂;
压力式喷雾头:
该喷头能耗低,生产能力大,能将高粘度胶液雾化,对环境污染小。
率;
影响板的变形,胶层的分解。
(2)热压压力作用:
使板坯中木材-胶层-木材紧密结合,目前生产中广泛采用。
十二、胶合板组坯应注意事项。
目前我国仍以手工组坯为主组坯注意事项:
零片施胶后要根据单板吸水后膨胀规律预留缝隙;
组坯时芯板与表板纹理应相互垂直,并做到“一边一头齐”;
窄芯板要放在板坯中间位置;
芯板不应露在外边太长,掌握陈化时间,防止局部胶干
十三、纤维与刨花铺装工艺的主要区别
刨花――铺装工艺要求:
铺装均匀稳定;
板坯结构对称;
分层施胶与铺装。
铺装方法:
间歇式铺装(将称量好的刨花,一块一块地铺成板坯)、连续铺装(刨花不间断铺撒,形成连续板坯)
纤维――成型工艺要求:
板坯密度均匀稳定,厚薄一致,具有一定的密实度,保证足够的厚度和尺寸规格,以满足产品质量要求。
根据铺装头的成型原理,铺装机分为机械成型、气流成型、机械气流成型和定向成型等几类。
十四、热压三要素在板坯热压中的作用及其对产品物理力学性能的影响。
热压压力、热压温度和热压时间称为热压工艺三要素。
实际热压过程是板坯状态(木材原料、胶粘剂、含水率等)与热压要素综合作用的结果。
(1)温度的作用:
使胶粘剂固化,形成胶合强度;
增加木材塑性,促使木材密实;
蒸发板坯水分,降低板材含水
胶料部分渗入木材细胞中为胶合创造必要的条件。
在胶合过程中既有利于浸润,使胶层均匀、致密,也使得被胶合的表面尽量的靠紧,,减少了胶合界面上的薄弱点;
影响板密度及厚度。
(3)热压时间作用:
对刨花板的厚度控制,表面质量,以及胶合的耐久性和预固化;
影响板的密度,抗弯强度,和抗拉强度。
预固化层
十五、常见人造板产品的热压曲线1)板坯热压过程时间―温度特性曲线直接影响到加压时间和生产率。
T1(A阶段):
热压板的板坯表层温度迅速上升,芯层温度几乎没有变化。
T2(B阶段):
板坯芯层温度迅速上升。
热量以对流的形式由表层向芯层传递,直至芯层水分开始蒸发。
T3(C阶段):
芯层温度缓慢上升。
T4:
芯层保持恒温。
大量水分开始蒸发,传递至芯层的大部分热量被用于蒸发水分,因而芯层保持恒温。
T5(D阶段):
芯层温度缓慢上升接近热压板温度,直至热压结束。
2)压力曲线
T1:
板坯送入压机的时间板坯没有受到压力。
(受热不受
压)T2:
热压板从开始闭合到全部闭合上,板坯仍未受到压力。
(受热不受压)T3:
上下热压板都压紧板坯后,压力升到工作压力Pmax。
(受热受压但压力未达到最大值)T4:
压力保持时间(加压间),板坯被压紧,胶粘剂固化。
(受热保压,芯层温度升高)
T5:
胶粘剂固化后,压力下降到零。
(受热受压,大量排湿)
T6:
热压板完全张开的时间。
(大量排湿)T7:
卸板时间。
十六、刨花板的端面密度梯度、形成的原因。
闭合时间T3,对刨花板厚度上密度有影响。
在大多数热压条件下,密度形成一个梯度,板坯的表面比较密实,密度较大。
图示不同压力和闭合时间对刨花板厚度上密度的影响闭合时间短(初压力高),表层的密度大,芯层的密度小。
由于密度
和强度有关系,刨花板l的抗弯强度高。
板3虽然平面抗拉强度增加,但其抗弯强度大大低于板l。
十七、人造板表面预固化层的形成原因避免表面预固化层的措施对于在热压过程中,当板坯在压板尚未闭合时,已受到热的作用,表层物料的水分开始蒸发,部分胶粘剂缩聚固化,形成密度较低的疏松的预固化层。
一般采用砂光处理将表面预固化层清除十八、热压后的人造板进行冷却的目的。
借助冷却处理,可以使上述矛盾得到缓解。
钝化板材表芯层的温度梯度和含水率梯度,缓解以至消除板内的残余热压应力,使板材内部的温湿度与所置大气环境的温湿度趋于平衡,最大限度地避免板材翘曲变形。
冷却还有利于降低板材的游离甲醛散发量。
十九、降低人造板甲醛散发量的原理和处理方法①从胶黏剂入手:
1)不用胶或改用其他环保胶替代2)降低甲醛与尿素摩尔比3)UF制胶中增加尿素的投料次数4)加入甲醛捕捉剂5)适当增加固化剂用量②从制板工艺入手:
1)适当调整热压工艺参数、温度、压力、时间2)适当提高板坯含水率
③从后期处理入手:
1)尿素溶液喷洒2)氨处理3)进行人造板表面装饰(涂料、贴板)
二十、人造板生产过程质量控制的目的。
产品质量是影响一个组织业绩的主要因素,顾客对质量越来越高的期望已成为世界性的趋势,不断改进质量对于获