洗发水瓶盖的热流道注塑模设计Word文档格式.docx
《洗发水瓶盖的热流道注塑模设计Word文档格式.docx》由会员分享,可在线阅读,更多相关《洗发水瓶盖的热流道注塑模设计Word文档格式.docx(29页珍藏版)》请在冰豆网上搜索。
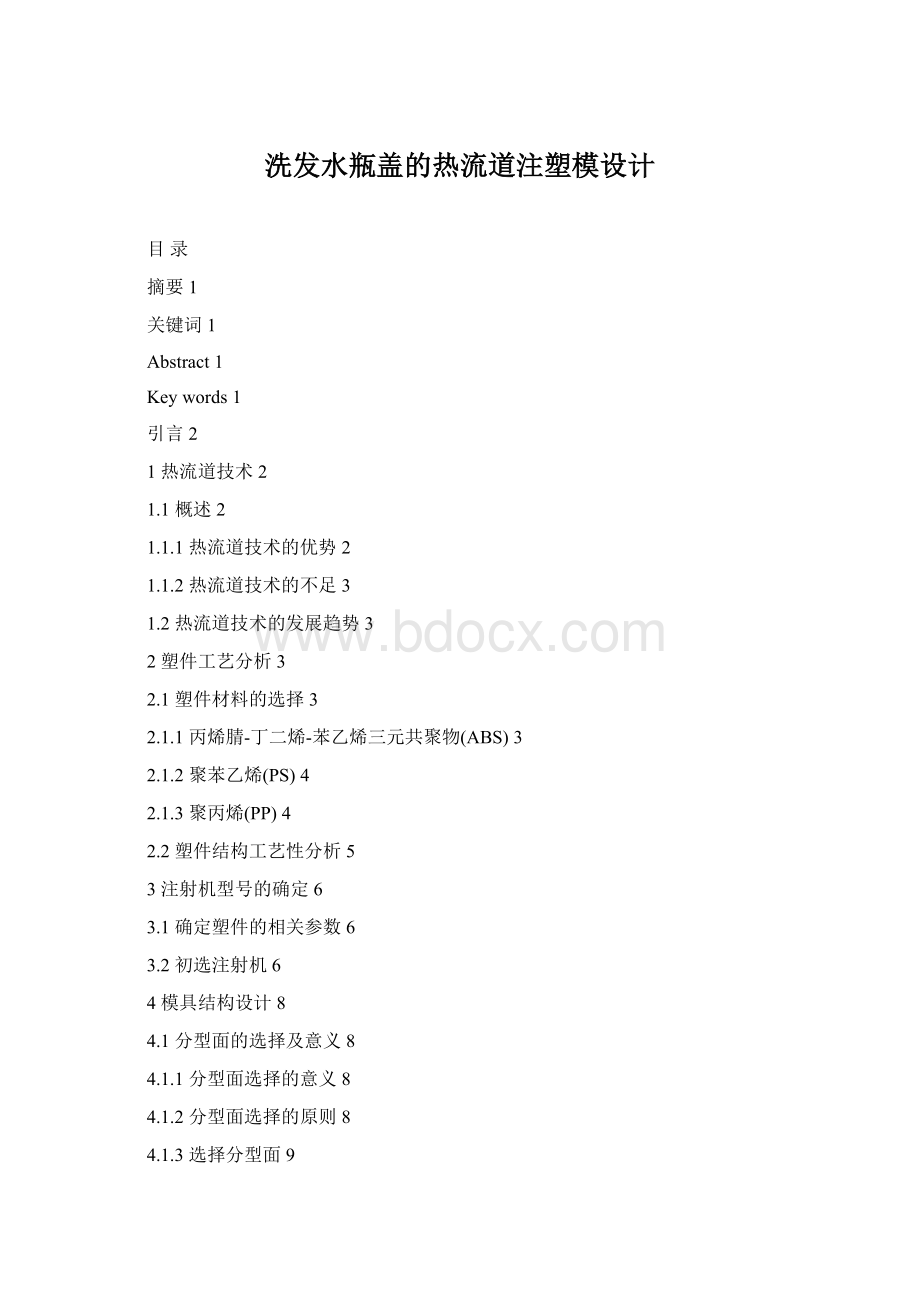
4.5.2脱模力的计算17
4.5.3脱模机构设计17
4.6导向机构的设计18
4.6.1导柱导向机构19
4.6.2导柱的数量和布置19
4.7温度调节系统的设计20
4.7.1冷却系统设计原则20
4.7.2冷却系统的结构设计20
4.7.3加热板加热形式选择21
5结论21
参考文献22
附录23
致谢26
机械电子工程专业学生闫思倍
指导老师张东方
摘要:
针对塑件的质量要求比较高,此次模具设计引入了热流道技术。
设计过程包括设计准备、塑件设计、模具设计、装配图及零件图的绘制和毕业设计论文的完成等六个环节。
其中,塑件设计和模具设计是重要环节。
因此,本文主要叙述了设计方案的确定、塑件设计及模架的调用及注塑机的选择、热流道系统的设计、脱模推出机构的设计等等。
这一系列的设计环节都离不开CAD技术的应用,这样将有助于切入问题的核心,避免不必要错误的造成。
关键词:
热流道;
塑件设计;
模具设计;
装配;
CAD
ShampooLidofHotRunnerInjectionMoldDesign
StudentmajoringinMechanicalandElectronicEngineeringYanSibei
TutorZhangDongfang
Abstract:
Fortheplasticpartsofthehigherqualityrequirementsofthemolddesignandtheintroductionofhotrunnertechnology.Thedesignprocessincludessixaspectsofdesignpreparation,plasticpartdesign,molddesign,assemblydrawingandpartsdiagramdrawingandcompletionofthegraduatedesignthesis.Amongthem,thedesignofplasticpartsandmolddesignistheimportantpart.Therefore,thisarticledescribesthedeterminationofthedesign,thedesignofplasticpartsandmoldbasecallsandinjectionmoldingmachineofchoice,hotrunnersystemdesign,moldreleaseejectionmechanismdesign.ThisseriesofdesignaspectscannotbeseparatedfromtheapplicationofCADtechnology,cutintothecoreoftheproblem,thiswillhelptoavoidunnecessaryerrorcaused.
Keywords:
Hotrunner;
plasticpartdesign;
molddesign;
Assembly;
CAD
引言
热流道注塑成型作为传统注塑成型一个重要发展方向,其最大特点在于浇注系统内的塑料不会凝固,也不会随制件脱模,整个注塑过程可实现自动化,从而大大提高了材料利用率;
使长流程流道成为可能,保证多型腔注塑生产的一致性,提高了制件的精度,浇注系统更人性化,通过温度控制可实现充模过程的平衡。
本设计通过对实体塑件进行分析、测量,建立可供加工生产的三维模型,并对塑件结构进行工艺性分析,确定其所选用的材料,然后根据塑件的材料特性及结构特征选择相应的注射机。
其次就是模具的结构设计,包括分型面的选择、型腔的确定、模架的选取、热流道系统的设计以及后续的脱模机构、导向机构和温度调节系统的控制等。
在设计过程中,使用先进的三维软件UG进行辅助设计,使设计的模具达到最佳效果。
1热流道技术
1.1概述
热流道注塑成型于20世纪50年代问世,经历了一段较长时间的推广以后,其市场占有率逐年上升,80年代中期,美国的热流道模具占注塑模具总数的15%~17%,欧洲为12%~15%,日本约为10%。
但到了90年代,美国生产的塑料注塑模具中热流道模具占40%以上,在大型制品的注射模具中则占90%以上。
由于快速自动化注塑成型工艺的发展,热流道注塑模具正在我国逐渐推广使用,在70年代,我国已经有热流道技术的应用,从90年代开始,已相继创建了不少热流道装备的经营企业。
热流道系统工作原理是在塑料模具流道附近或中心设有加热棒和加热圈,从注塑机喷嘴出口到浇口的整个流道都处于高温状态,使流道中的塑料保持熔融,从而均匀充满型腔,停机后一般不需要打开流道取出凝料,再开机时只需加热流道到所需温度即可。
因此,热流道工艺有时称为热集流管系统,或者称为无流道模塑。
通过热流板、热嘴、及其控制系统的功能,让模具在成形时能节省流道的塑料、减少流道压力、加快生产速度、做出高难度产品。
热流道系统作为模具系统的一个常用部件,能够有效地提高塑料制品的质量、提高生产效率、降低生产成本,并使资本的投入得到更高的回报。
在模具产业中,热流道模具所占的比例越来越大,已逐渐取代传统式模具的地位。
1.1.1热流道技术的优势
1)缩短制件成型周期,提高生产效率;
2)节省塑料原料;
3)降低废品率,提高产品质量;
4)消除后续工序,有利于生产自动化。
1.1.2热流道技术的不足
1)模具成本上升;
2)热流道模具制作工艺设备要求高;
3)操作维修复杂。
1.2热流道技术的发展趋势
总之,热流道技术的发展是利远大于弊。
在国外已运用了数十年,由于其多方面的技术优势与用途,因此在射出成形塑料模具的使用率与普及率已大幅度的提升。
且在“分秒必争”且环保意识观念增强的时代,热流道技术可说已成为“射出成型产业”及“塑料模具产业”不可或缺的热门产品。
热流道不但可提高生产速度、减少废料并能进一步的提升模具价值[1]。
在现今以质量、生产力、提倡环保及节省人力资源的情况中,冷流道模具无论在设计和生产上,都缺乏竞争力,而应用热流道系统再搭配CAD实用技术与模流分析,将极大的提高产品生产效率和改善相关的问题,如果在产品设计初期能综合利用CAD技术来设计和进行模流分析,将有助于直接进入问题的核心,及时发现不必要的错误,缩短产品开发时间,进而避免由此造成更多的资源浪费。
2塑件工艺分析
2.1塑件材料的选择
2.1.1丙烯腈-丁二烯-苯乙烯三元共聚物(ABS)
ABS具有良好的综合物理力学性能,耐热,耐磨,耐油,尺寸稳定,加工性能优良,具有三种单体所赋予的优点,其中丙烯腈赋予材料良好的刚性,硬度,耐油性耐寒性,苯乙烯赋予材料刚性,硬度,光泽性和良好的加工流动性,改变三组分比例可以调节材料性能。
ABS为无定型聚合物,无明显熔点,在160°
C-190°
C度具有充分的流动性,且热稳定性好在高于285℃时才出现分解现象,因此加工温度范围较宽。
ABS熔体具有明显的非牛顿性,提高成型压力可以使熔体粘度明显减小。
粘度随温度升高也会明显下降。
ABS吸湿性稍大于聚苯乙烯,吸水率在0.2%—0.45%之间,但由于熔体粘度不高,对于要求不高的制品,可以不经干燥,但干燥可使制品具有良好的表面光泽并可改善内在质量,在80-90℃以下干燥2-3个小时,可以满足各种成型要求。
ABS具有较小的成型收缩率,收缩率变化最大范围约为0.3%-0.8%。
在多数情况下,其变化不小于该范围。
注塑是ABS塑料最重要的成型方法,可以采用柱塞式注塑机,但更常用螺杆式注塑机,后者更适于形状复杂制品,大型制品成型。
主要用途:
汽车(仪表板,工具舱门,车轮盖,反光镜盒等),电冰箱,大强度工具(头发烘干机,搅拌器,食品加工机,割草机等),电话机壳体,打字机键盘,娱乐用车辆如高尔夫球手推车以及喷气式雪撬车等[4]。
2.1.2聚苯乙烯(PS)
聚苯乙烯是无色无味的透明刚硬固体,制品掷地时有金属般鸣响,聚苯乙烯透光率不低于80%,折射率较大,在1.5%-1.6%之间,具有特殊光亮,在热塑性塑料中属于典型的硬而脆材料,拉伸,弯曲等常规力学性能高于聚苯烃,拉伸时无明显屈服现象。
聚苯乙烯分子链虽是刚性链,但由于是无定型结构,超过玻璃花温度即开始软化,软化点为95℃左右,许多力学性能都受到温度升高的明显影响,最高连续实用温度仅60~80℃,120℃时开始成为熔体,180℃时开始具有流动性,其热稳定性较好,超过300℃才开始分解,因此聚苯乙烯具有较高的成型加工区间,但储存容易泛黄,泛黄的原因之一是单体纯度不够,特别是在含微量元素时,二是聚合物在空气中缓慢老化引起发黄,聚苯乙烯较轻,密度在1.04-1.05之间。
加工工艺性:
吸湿性很小,加工前一般不需要与专门的干燥工序,成型温度范围较宽。
收缩率及其变化范围都很小,一般在0.2%—0.8%,有利于成型尺寸精度较高和尺寸稳定性的制品。
聚苯乙烯制品容易产生内应力,并且在空气中缓慢老化引起发黄,很明显不适合选用。
2.1.3聚丙烯(PP)
聚丙烯无色、无味、无毒的。
外观似聚苯乙烯,但比聚苯乙烯更透明、更轻。
密度为0.90—0.91g/cm3。
它不吸水、光泽好、易着色。
聚丙烯具有聚乙烯的所有优良性能,如卓越的介电性能,耐水性、化学性能稳定,宜于成形加工等;
还具有聚乙烯所没有的许多性能,可制作铰链,有教高的抗弯曲疲劳强度。
可用于各种机械零件如法兰、接头、泵叶轮、汽车零件;
可作为各种酸碱等的输送管道,化工容器和其他设备的衬里,表面涂层;
可制造盖和本体合一的箱壳,各种绝缘零件,并用于医药工业中。
成形特点:
成形收缩范围及收缩率大,易发生缩孔,凹痕、变形、方向性强,流动性极好,易于成形;
热容量大,注射成形必须设计能充分进行冷却的冷却回路;
注意控制成形温度。
料温低时方向性明显,尤其是低温、高压时更明显。
聚丙烯成形的适宜模温为80度左右,不可低于50度,否则会造成成形塑件表面光泽差,产生熔接痕等缺陷。
温度过高会产生翘曲或变形。
如表2-1,三种材料性能参数:
表2-1三种材料性能参数表
性质材料
ABS
PS
PP
密度(g/cm3)
1.05
1.04-1.06
0.90-0.91
收缩率(%)
0.3-0.8
0.2-0.8
1.0-2.5
熔点(°
C)
130-160
131-165
220-275
热变形温度(°
65-98
65-90
102
模具温度(°
60-80
40-60
40-80
注射压力(MPa)
60-100
68.6-137.2
塑化形式
螺杆柱塞式
拉伸强度(MPa)
33-49
35-63
37
拉伸弹性模量(MPa)
2000
2800-3500
—
弯曲强度(MPa)
80
61-98
67.5
缺口冲击强度(KJ/m2)
11-20
0.25-0.40
78
介电常数(KV/mm)
2.4-5.0
2.7
24
喷嘴温度(°
220-240
160-170
240-250
2.2塑件结构工艺性分析
由于设计的洗发水瓶盖整体体积较小,外形规则,与其他制件的配合比较容易,下面从以下几点去分析塑件。
1)塑件壁厚
塑料制件的壁厚是最重要的结构要素。
制件的壁厚太大,则塑料在模腔中需要冷却的时间较长,产品的生产周期也会随着延长;
制件的壁厚太薄,制件的刚性较差且不耐压,在脱模过程中容易发生变形。
另外,壁厚太薄,流动阻力加大,造成塑料的填充不满,成型比较困难。
此外,制件的壁厚原则上要求一致,因为壁厚不均匀,在成型时会出现收缩不均匀,产成缩孔,以致发生变形或开裂。
2)拔模斜度
为了制件可以顺利从模腔中脱出,在平行于开模方向的制件表面上,必须设计一定的拔模斜度。
在不影响尺寸精度的情况下,制件的内外表面都应该设计拔模斜度。
设计之前,对制件定义的拔模角度为3°
,但是在实际制件的设计中发现,如果拔模角度太大,所设计的制件会出现局部壁厚过薄,影响制件的注塑生产质量,所以必须降低拔模斜度。
由于制件的壁厚相对比较薄,不能设计太大的拔模角度,根据设计当中出现的情况,所以对于这个制件设计了1°
的拔模斜度,得出的设计效果符合产品要求[11]。
3)制件的尺寸与精度
不同塑料材料有其固定的标准收缩率,收缩率小的材料,产品的尺寸误差就很小,容易保证尺寸精度。
ABS塑料材料的收缩率为0.5%,所以制件的尺寸精度可以得到保证。
经过对材料和制品进行分析,该塑件是一个洗发水瓶盖,属于小型复杂零件,分上下盖两部分,可以开合,外观要求光滑,ABS符合制品的质量和使用要求,它成型性能较好,可以注塑成型,伸缩率较低。
如图2-1所示,塑件壁厚为0.8mm,生产批量大。
另外,在设计时ABS塑料要求模具分型面、配合面的精度要高,以免溢料。
图2-1三维零件工程图
塑料ABS的一些注塑工艺参数见表2-2。
表2-2ABS注塑工艺参数
注射机类型
螺杆式
保压力(MPa)
30~70
螺杆转速(r/min)
20~60
注射时间(s)
3~5
喷嘴形式
直通式
保压时间(s)
15~30
喷嘴温度(℃)
180~260
冷却时间(s)
10~30
模具温度(℃)
40~85
成型周期(s)
60~100
3注射机型号的确定
3.1确定塑件的相关参数
通过三维软件建模分析计算得:
塑件体积:
V=15.437cm3
塑件质量:
M=16.2g
浇注系统凝料体积估算:
由于本模具采用热流道系统(无凝料系统)所以不必考虑浇注系统的体积。
3.2初选注射机
注射模是安装在注射机上的,因此在设计注射模具时应该对注射机有关技术规范进行必要的了解,以便设计出符合要求的模具,同时选定合适的注射机型号。
如果两者不相匹配,则模具无法使用,为此,必须对两者之间有关的数据进行校核,并通过校核来设计模具与选择注射机型号。
1)公称体积:
该模具采用一模四腔,所以一次注入模具型腔塑料的总体积:
要与注塑机理论注射量的0.8倍相匹配,
依据公式(Vg=V÷
0.8),则有:
这样才能满足实际注塑的需要,则注塑机的理论注射量为77.185cm3,
考虑到该洗发水瓶盖注射模为一模四腔,由于塑件要求的注射量较小,但是产品覆盖面积比较大,模具体积比较大。
因此初步选定注射机理论注射容量为2000cm3,符合生产要求。
2)注射压力:
参照表2-1ABS主要技术参数,ABS的注射压力为60-100Mpa,这里取P0=100Mpa,注射压力安全系数k1=1.25~1.4,取1.3,所以:
3)锁模力计算:
塑件在分型面上的投影面积A1,则A1=3500mm2。
一模四腔,所以总投影面积:
模具型腔内的胀力为F1,则
(由于塑件壁厚较薄,且模具采用热流道系统,参照表3-1模内的平均压力,所以p取34.3MPa。
)
表3-1模内的平均压力
制品特点
模内平均压力/MPa
举例
容易成型制品
24.5
PE、PP、PS等壁厚均匀的日用品
一般制品
29.4
在高温下,成型壁厚较薄的制品
中等粘度和精度要求高
34.3
ABS、PMMA等有精度要求的工程结构件
高进度、高粘度、难充模的制品
39.2
用于机械零件上高精度的齿轮或凹轮
根据F1,计算出理论胀力为(k2=1.1~1.2,取k2=1.2):
由此得出:
F锁=4000KN〉576.24KN(校核通过)
综合以上三点再结合塑件高度,注射机选用SZ-2000/4000型号,下表3-2表示注射机主要技术参数。
表3-2SZ-2000/4000主要参数
结构类型
卧式
螺杆直径/mm
90
理论注射量/cm3
注射压力/MPa
130
注射速率/(g/s)
430
塑化能力/(g/s)
75
螺杆转速/(r/min)
10~140
锁模力/kN
4000
拉杆间距/mm
750×
750
移模行程/mm
最大模具厚度/mm
770
最小模具厚度/mm
380
模具定位孔直径/mm
250(深25)
喷嘴球半径/mm
20
喷嘴孔直径/mm
4
锁模形式
双曲肘
4模具结构设计
4.1分型面的选择及意义
4.1.1分型面选择的意义
定模与动模相接触的面称为分型面,它是用于将冷却凝固的制件从模腔里面取出的接触面。
分型面的选择的好坏对制件的质量、模具结构及其制造、生产操作的难易等都有很大的影响。
按分型面的形状来分,有平面分型面、斜分型面、阶梯分型面和曲面型分型面。
如图4-1:
a.平面分型面;
b.斜分型面;
c.阶梯分型面;
d.曲面分型面
图4-1分型面的几种形式
4.1.2分型面选择的原则
对大多数制品来说,其分型面都在很显而易见的部位,即正好在或者是靠近一个容器的缘口或在一个工业制品的基座面。
但是,在另一些制品中,分型面并不那么一目了然,而需进行大量周密的思考[5]。
选择分型面总的原则是保证塑件质量,且便于制品脱模和简化模具结构,下面列出分型面选择应考虑的基本原则:
1)分型面的方向尽量采用与注塑机开模方向垂直的方向;
2)分型面一般开设在产品的最大截面处;
3)尽量使塑件留在动模一侧;
4)有利于保证塑件的尺寸精度和外观质量等;
5)有利于成型零件的加工与制造;
6)应有利于排气。
4.1.3选择分型面
制件的开模方向是垂直向上,而且设置了1°
的脱模斜度。
分型面的形状为平面分型面,选择在瓶盖处,如图4-2所示。
这样有利于制件的脱模而且不会影响制件的外观质量,还可以利用其间隙和型芯、推杆等间隙排气。
图4-2分型面的选择
4.2确定型腔数目和排列方式
4.2.1确定型腔数量
考虑到该塑件的精度要求不高,还是大批量生产可以采用一模多腔。
根据塑料制品的结构,初步确定采用一模四腔的模具形式。
4.2.2确定型腔排列方式
1)多腔时,型腔在模板上通常采用圆形排列,H形排列,直线型排列以及复合排列一边构成平衡式浇注系统,保证制品的质量均一和稳定;
2)型腔布置和浇注口部位应力求对称,以便防止模具称便偏载而产生溢料现象;
3)圆形排列加工麻烦,除圆形制品和一些高精度制品外,在一般情况下常用H型排列和直线型排列,且尽量选用H型排列,因为该平衡性更好[12]。
4.2.3本设计的排列方案
根据设计需要和生产效率的要求可知,为满足塑件的使用要求,在同一次的注射成型中,一次成型塑件的个数为四个,也就是采用一模四腔的生产方式。
型腔排列的简单工程图4-3如下:
图4-3形腔排列图
4.3模架的选择与调入
4.3.1概述
在现代模具工业中,模具设计主要是对成型制件外形的凹、凸模(型腔、型芯)零件以及开模和脱模方式进行设计,而模具上的大部分零部件可以从专门厂家直接选购,对于一些特殊的,也可以要求厂家另外加工生产。
尤其是模架的选购,如果设计制造一套非标准模架,可能需要花费很多的时间、资金和人力,但是根据设计的参数,选择合适的厂家、选购合适的模架,则可降低模具生产的费用,也缩短了设计的周期。
总的来说,模具零件的选购大大节约了模具制造时间和费用。
现在,一般的模具厂家设计制造出一套中等复杂程度的注塑模具,可以在20天左右的时间里完成。
4.3.2选择模架
市场上,模架的种类有很多,不同厂家生产出来的模具也存在差异。
具体选哪种模架形式主要根据个人的爱好及所具有的加工设备而定。
1)根据整体嵌入式的外形尺寸,又考虑导柱、导套的布置等,再同时参考注射模架的选择方法,可确定自行定制的(即宽×
长=400×
450mm)模架结构。
2)定模板尺寸的确定
定模板要开框装入整体嵌入式型腔件,加上整体嵌入式型腔件上还要开设冷却水道,嵌入式型腔件高度为28mm,还有定模板上需要留出足够的距离引出水路,且也要有足够的强度,故定模板厚度取90mm。
3)流道固定板
该模具为热流道、一模四腔进浇,因此模架中设置一块热流道固定板,作用只是为了容纳热流道板,固定板的厚度与流道板的厚度相关,流道板的厚度是35。
4)动模板尺寸
具体选取方法与定模板相似,由于动模板下面是模脚,特别是注射时,要承受很大的注射压力,而且必须为动模侧的顶出机构及冷却水路留出导向空间,所以相对定模板来讲相对厚一些,故动模板厚度取100mm。
5)模脚尺寸
模脚高度=顶出行程+推板厚度+顶出固定板厚度+5mm=50+20+25+5=100mm,所以初定模脚为100mm。
经上述尺寸的计算,模架尺寸已经确定好。
其外形尺寸:
宽×
长×
高=400mm×
450mm×
400mm,如图4-4:
1.定模座板;
2.流道固定板;
3.定模板;
4.动模板;
5.模脚;
6.动模座板
图4-4模架
4.4热流道系统
4.4.1概述
热流道系统是相对于冷流道系统说的,热流道注塑模是无流道凝料注塑模中最常见的一种,是注塑成型技术发展的新阶段。
由于快速自动化注塑成型工艺的发展,热流道注塑模具正逐步推广使用,且应用的厂家越来越广泛,积累起来的技术成果也与日俱增[1]。
热流道注塑模与一般注塑模具(冷流道注塑模具)相比,具有以下几方面的优势:
1)由于有加热器,流道凝料不需脱模,整个注塑过程可实现自动化,从而大大提高了材料利用率;
2)对浇口系统的统一控制,使长流程流道成为可能,保证多型腔注塑生产的一致性,提高了制件的精度;
3)浇注系统更人性化,通过温度控制可实现充模过程的平衡;
4)减少进料系统压力损失,充分利用注塑压力,有利于保证制件质量;
5)与双分型面的三板模相比,流道更短;
6)