无机材料工艺学考试重点Word文档下载推荐.docx
《无机材料工艺学考试重点Word文档下载推荐.docx》由会员分享,可在线阅读,更多相关《无机材料工艺学考试重点Word文档下载推荐.docx(28页珍藏版)》请在冰豆网上搜索。
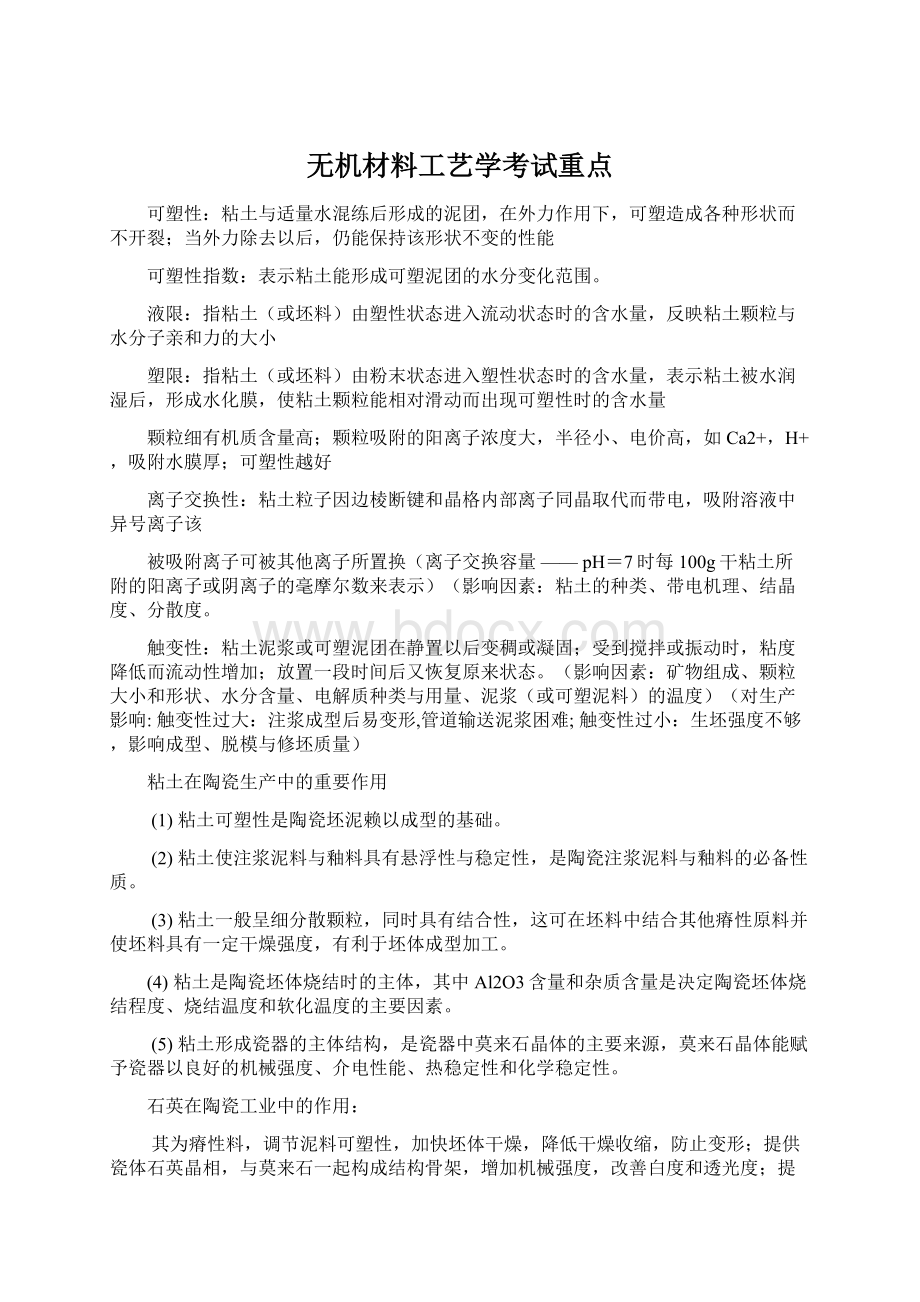
一般颗粒的形状有三种:
a:
近似于球形的粒形b:
近似于盘形的针状c:
近似于棒形的针状颗粒形状对成型,烧结和使用性能有一定的影响,球粒状最好。
呈鳞片状或针状的常需预烧,破坏其晶体结构或通过机械粉碎改变其颗粒形状。
4)活性。
衡量原料化学反应能力及速度的指标。
原料化学活性越好,烧结温度越低。
陶瓷的分类
陶瓷分类一(按性能分为普通陶瓷和特种陶瓷):
普通陶瓷:
采用粘土类及其它天然矿物原料制得,也称传统硅酸盐陶瓷。
特种陶瓷:
(氧化物,非氧化物,金属陶瓷等)采用化工或合成原料,组成范围超出硅酸盐材料范畴。
又分为结构陶瓷和功能陶瓷。
结构陶瓷定义:
定义1:
是一种坚硬耐磨,且具有耐高温,耐腐蚀,抗压,不老化等结构性能的陶瓷材料。
定义2:
是一类在1000℃高温下抗形变和断裂优于金属的陶瓷材料。
功能陶瓷定义:
功能陶瓷是指以电,磁,光,声,热,力,化学和生物等信息的检测,转换,耦合,传输及存储等功能为主要特征的陶瓷材料
陶瓷分类二:
(按烧结程度分类)
(1)瓷器—瓷质制品:
日用细瓷、玻化砖、卫生陶瓷等。
坯体致密,吸水率低,烧成收缩率大,烧成过程中易变形,较难生产大规格产品,制品可有釉或无釉。
(2)陶器——陶质制品:
釉面砖(内墙砖)、日用精陶等。
断面粗糙无关,不透明,敲击之声音粗哑,有的无釉,有的施釉。
坯体吸水率高,有利于施工时采用水泥砂浆铺贴,但坯体防污能力差,通常在制品使用面施釉以保证使用面不吸水和易清洁的要求,同时也起着装饰产品作用。
(3)炻器——炻质制品,也称半瓷,是介于陶器和瓷器之间的一类产品。
1)坯体烧结程度较低,吸水率较高,烧成收缩率较小,2)易制成形状较复杂或大规格制品;
3)大部分制品表面施釉;
陶瓷坯、釉料组成表示方法
1.化学组成表示法(氧化物质量分数表示法):
以SiO2、Al2O3、Fe2O3、CaO、MgO、K2O、Na2O、灼烧减量等的含量以质量分数来表示。
特点:
准确反映坯(釉)料的化学组成;
根据其含量,推断坯、釉基本性能,如:
坯料烧成温度、收缩、产品色泽等or釉料熔融温度、热膨胀系数等。
缺点:
不清楚坯料的化学成分来源于何原料。
2.实验式表示法or坯、釉式表示法:
根据化学组成表示法,分别将各氧化物质量百分数除以其摩尔质量,得各氧化物的摩尔数,冠于各氧化物分子式前。
按碱性氧化物(R2O+RO)·
中性氧化(R2O3)·
酸性氧化物(RO2)的顺序排列,并把其中一种系数调整为1。
各类氧化物的组成一目了然,除能估计有害杂质与降低熔融温度对坯体,釉料的影响外,还能表明高温性能,是普通陶瓷坯、釉料组成常用的表示方法。
一些陶瓷原料也可用此方法列出其坯式,反映其组成。
为区别坯、釉组成,以R2O3的物质的量为基础,将其调为1,得坯式。
以碱R2OandRO为基础,其物质的量之和为1,得坯、釉式。
根据A12O3和SiO2前面的系数值区别是坯式或釉式:
坯式中A12O3和SiO2的系数较大;
釉式中A12O3和SiO2的系数都很小。
3.矿物组成(或示性组成)表示法:
将各天然原料中的同类矿物含量合并,换算成粘土、长石、石英三种纯矿物的质量百分比含量表示其组成。
可大致反映坯料性能。
因同类型矿物在坯体中所起作用基本相同,而粘土,长石,石英所起作用各不相同。
长石质瓷坯料组成
矿物组成为:
40-60%高岭土,20~30%长石,25~40%石英。
(高岭土含量高,长石含量少)瓷体由石英-方石英-莫来石-玻璃相组成。
玻璃相50~60%,莫来石10~20%,残余石英8~12%,半安定方石英6~10%。
烧成范围宽(1150-1450℃),烧成温度高(1350~1450℃),硬度高(莫氏硬度为7)。
绢云母质瓷坯料组成
瓷坯的组成范围:
瓷石70~30%,高岭石30~70%。
烧成温度随瓷坯中瓷石和高岭石的用量比不同在1250~1450℃范围内波动。
瓷质由石英-方石英-莫来石-玻璃相构成。
除具有长石质瓷的一般特点外,还具有透明度高,还原气氛下烧成时呈白里泛青的特色。
骨灰瓷坯料组成
磷酸盐-高岭土-石英-长石系统瓷,以磷酸钙为熔剂,磷酸盐通过骨灰引入。
磷酸钙作助熔剂,但它本身的熔点并不低(1734℃),它的助熔作用是它与其它组元共熔而引起,共熔后液相温度降低,液相大量产生,因而起助熔作用。
骨灰最好以50%为宜,过多则瓷质发黄,可塑性差,不易成型,因此配料中需要一定量的高可塑性粘土。
坯体主要由钙长石,β-Ca3(PO4)2,方石英,莫来石和玻璃相组成。
滑石瓷坯料组成
日用滑石瓷是滑石-粘土-长石三组分瓷,属于MgO-Al2O3-SiO2系统瓷。
配方组成为70~80%滑石,5~10%粘土,<
5~10%长石.烧成范围窄(理论范围为30~40℃,实际应控制在10~20℃),一般烧成温度为1320℃,要求窑内温差小,窑内温度分布均匀。
控制泥浆的上述性能的途径:
(1)加入电解质加入电解质解凝剂可增强泥浆的流动性。
(2)泥浆温度:
泥浆温度↑,粘度↓,滤动性↑,脱水速度↑,吸浆时间↓,坯体强度↑。
温度过高则起泡,影响质量及石膏模使用次数。
(3)调整工艺:
搅拌→泥浆保持悬浮状态,减少分层。
陈腐→水分分布均匀,排出泥浆空气,流动性和可注性↑,坯体强度↑。
可塑泥团的成型性能
可塑泥团的特点:
有良好的加工性,易于形成各种形状而不开裂,可钻孔和切割,干燥后要有较高的生坯强度。
有各向同性的均匀结构,不会因颗粒定向排列使坯体收缩不均,导致坯体变形和开裂。
(1)可塑泥团流变特性:
由固相、液相和少量气相组成的弹塑性系统。
含水量低,固体含量大→很高屈服值:
成形后能克服自重影响而不变形。
(2)影响泥团可塑性的因素:
A)矿物种类。
。
可塑性好的泥团需具备以下条件:
1)颗粒较细;
2)矿物解理明显或解理完全,最好呈片状结构;
3)颗粒表面水膜较厚。
蒙脱石具备上述三条件,可塑性强。
叶腊石及滑石呈片状,但水膜薄,可塑性不高。
迪开石颗粒较粗石英不呈片状,且吸附水膜薄,可塑性低。
粘土中所含矿物的可塑性:
迪开石<
隧石<
伊利石<
绿脱石<
锂蒙脱石<
高岭石<
蒙脱石。
高岭土<
膨润土。
原因可由两者矿物结构差异说明
蒙脱石:
复网层结构。
每个晶层的两端为硅氧四面体层,中间为AlO4(OH)2八面体层(也叫水铝石层)。
晶层之间氧层与氧层的联系力很小(分子间作用力),水容易进入进入晶层之间,引起c轴膨胀。
有良好的片状解理,且晶粒细小,易发生同晶取代,质地不纯,熔点较低,可塑性强。
高岭石:
单网层结构。
每个晶层是由一层硅氧四面体和一层AlO2(OH)4八面体通过共用的氧原子联系在一起,相邻两层通过八面体的OH与四面体的氧以氢键相联。
水分子不易,可塑性差。
B)固相颗粒大小和形状
颗粒越粗,呈现最大塑性时所需的水分越少,最大可塑性越低。
粒径↓每个颗粒表面形成水膜需水分↑,颗粒堆积而成的毛细管半径↓,毛细管力↑,可塑性↑。
C)吸附阳离子的种类
粘土中阳离子交换的能力、阳离子的大小和半径,影响粘土胶团间的吸引力,从而影响粘土的可塑性。
1)阳离子交换能力强则可塑性高,阴离子交换能力小,对可塑性影响小;
2)阳离子价数高,泥团可塑性越大;
对泥团可塑性影响大小:
三价>
二价>
一价;
3)同价阳离子,半径愈大,可塑性越大。
粘土吸附不同阳离子时,其可塑性的强弱顺序为:
H+>
Al3+>
Ba2+>
Ca2+>
Mg2+>
NH4+>
K+>
Na+>
Li+吸附Li+的粘土塑性低。
D)液相的数量和性质
水分是泥团出现可塑性的必要条件,水分适当才能达到最大可塑性。
屈服值:
随含水量增加而减小。
最大变形量:
随含水量的增加而加大。
可塑性表示:
屈服值与最大变形量乘积。
改变泥团含水量可改变一个流变特性,但同时会降低另一个特性。
可塑成型时的最佳水分是可塑性最大时的含水量,亦称可塑水分。
(3)可塑泥团的颗粒取向
影响泥浆流变性能的因素
1泥浆的浓度:
泥浆浓度增大,要获得同一剪切速率所需的应力也增大。
2固相颗粒大小:
泥浆的颗粒分布范围和大小颗粒之比影响泥浆的粘度。
颗粒分布范围广,最小与最大颗粒粒径之比必小,中间颗粒较多,空隙体积大,吸引水分进入,泥浆粘度增大。
3电解质的加入:
含电解质的泥浆都会出现触变滞后环,随着泥浆解凝程度的不同,泥浆的屈服值和滞后环的面积都会变化。
4陈腐:
新调制的泥浆和解凝程度不够的泥浆,流变性不稳定,在陈放过程中粘度和屈服值会逐渐加大,需一段时间才能稳定。
5有机物质:
粘土中常含天然有机物质(也叫腐殖质)。
腐殖质会降低粘土泥浆的粘度,增加其流动性。
6可溶性盐类:
粘土中的可溶性盐(碱金属,碱土金属的氯化物,硫酸盐等)会提高泥浆的粘度。
微量Ca2+和Mg2+取代被粘土颗粒吸附的Na+,可使ζ电位变小而导致粘度增大。
泥浆中可溶性盐增多是,即使添加解凝剂,粘度也难以下降。
注浆过程的物理化学变化(掌握)
(1)物理脱水
推动力:
毛细管力,取决于毛细管半径和水的表面张力。
毛细管越细,水的表面张力越大则脱水的推动力越大。
阻力:
模型内表面形成一层坯体后,水分必先通过坯层的毛细孔,然后再进入模型的毛细管中,脱水阻力来自模型和坯体两方面。
注浆前期,模型阻力起主要作用,注浆后期,坯体厚度增加所产生的阻力起主导作用。
坯体中塑性原料多,胶体粒径小的泥浆脱水阻力大。
模型中形成的坯体密度大则阻力也大。
石膏模型产生阻力的大小取决于毛细管的大小和分布,这又与制造模型时水和熟石膏的比例有关。
(2)化学凝聚
泥浆与石膏模接触时,会溶解一定数量的CaSO4,溶解的CaSO4和泥浆中Na-粘土和硅酸钠发生离子交换反应:
Na-粘土+CaSO4+Na2SiO3→Ca-粘土+CaSiO3↓+Na2SO4此反应使靠近石膏表面的一层Na-粘土变为Ca-粘土,泥浆由悬浮状态转变为聚沉。
因此,石膏起絮凝剂的作用,促使泥浆絮凝硬化,缩短成坯时间。
反应产物CaSiO3溶解度很小,促使反应向右进行。
水溶性产物Na2SO4被吸入模型的毛细管中,烘干模型时,Na2SO4以白色晶体析出。
由于石膏中CaSO4的溶解与反应,模型的毛细管增大,表面出现麻点,力学强度下降。
粉体的成型机理
5.1.2.1粉体的成形性能
(1)粒度和粒度分布:
粒度:
粉料颗粒的大小,用颗粒半径或直径表示。
粒度分布是不同大小颗粒所占的百分比。
很粗或很细的粉料在一定压力下被压紧成型的能力差。
(2)粉料的堆积特性:
大小不同的球体堆积,小球体填塞在空隙中,要得到大的堆积密度需粗、中、细三级颗粒配合使用。
(3)粉料的拱桥效应:
拱桥效应使粉料自由堆积的空隙率远大于理论计算值。
拱桥效应:
表面粗糙,非球形的实际粉料中颗粒互相交错咬合,形成拱桥形空间,增大孔隙率。
(4)流动性:
粉料的分散程度高,有一定流动性。
粉体堆积到一定高度后会向四周流动,保持圆锥体,偏角α不变。
α角反映粉料的流动性。
一般粉料的α角(20~40°
),表面光滑的球形粉料,α角小,流动性好。
生产中,粉料流动性决定其在模型中的充填速度和充填程度。
流动性差的粉料在短时间内难以填满模具,影响压机的产量和坯体质量。
可向粉料中加入润滑剂来提高其流动性
5.1.2.1干压成型工艺原理
(1)密度的变化:
压制成型过程中,压力增加,松散粉料迅速成坯体,坯体密度急剧增加(颗粒滑移,重排,排出空气)压力继续增加,密度缓慢增加(接触点局部变形和断裂)压力超过粉料的极限变形应力后密度迅速增大(再次引起颗粒重排和滑移)。
坯体孔隙率V公式:
孔隙率与其它参数的关系:
装模时孔隙率V0小则成型后坯体的孔隙率也越小,密度大。
孔隙率减小与p成指数关系。
延时可降低坯体气孔率,增加密度,但生产效率降低。
加润滑剂,减小内摩擦力η,提高密度。
坯体形状,尺寸及粉料性质都会影响坯体的密度。
(2)强度变化:
随成型压力增加,坯体强度分阶段以不同速度增大:
1)压力较低时,强度增加不大。
(粉料颗粒位移而填充空隙,颗粒间接触面积仍小)2)成型压力增大后,强度直线提高。
(颗粒位移和填充空隙继续进行,且颗粒发生弹性-塑性变形或开裂,接触面积大增)3)压力继续增大,强度变化较平坦。
(坯体密度和孔隙变化不明显)
(3)坯体中压力的分布:
压制成型时,坯体中的压力分布不均,导致坯体各部分密度有差别。
坯体中离开加压面的距离越大,受到的压力越小。
原因:
1)颗粒移动和重排时,颗粒间产生内摩擦力。
2)颗粒与模具间产生外摩擦力。
两种摩擦力妨碍压力的传递。
H/D比值越大,坯体中压力分布不均现象越严重。
因此,高而细的产品不适合压制法成型。
坯砖四周的中心部位比四周的压力稍小,沿坯砖中心线上越趋近中心受到的压力也越小。
(4)影响坯体密度的因素:
1)成型压力
净压力:
粉料相对位移所需克服的摩擦力+粉料颗粒变形所需力)
消耗压力:
克服粉料颗粒对模壁摩擦所耗的力。
压制过程的总压力(成型压力)=净压力+消耗压力
成型压力与粉料组成和性质有关,还与模壁和粉料的摩擦力和摩擦面积有关。
2)加压方式
单面加压:
坯体在上方及近模处密度最大,下方近模壁处和中心部位密度最小。
双面加压:
上下同时受压,压力梯度的有效传递距离变短,由摩擦力带来的能量损失减小,密度相对均匀,H/D越小密度均匀性越好。
坯体的中心部位密度较低。
3)加压速度
除压时可稍快加压(坯体疏松,空气易排出)
高压使颗粒紧密靠拢后需缓慢加压,以免密实坯体残余空气无法排出。
H/D比值大时or粉粒较细流动性较低时,需慢加压,延迟持压时间。
可多次加压or多次换向加压or加压时振动粉料来提高压力的均匀性。
(一轻,二重,慢提起)
4)可塑性及添加剂的选用
保证生坯强度的前提下,少用或不用可塑粘土(降低干压坯体的收缩率)
加入一定种类和数量的添加剂来提高坯体的密度和强度,减少密度分布不均的现象(减少颗粒间及颗粒与模壁间的摩擦)如CMC,甘油等。
5.2.2基本注浆方法(掌握)
(1)单面注浆(空心注浆)。
注浆过程:
泥浆注满石膏模后放置一定时间,待模型内壁粘附一定厚度坯体后将余浆倒出,之后带模干燥,注件干燥收缩脱模后就可取出。
单面注浆特点:
采用的石膏模没有型芯。
坯体外形取决于模型的工作面。
坯体厚度较均匀,厚度取决于吸浆时间,并与模型的温度,湿度及泥浆性质有关。
适合成型小件,薄壁产品。
(2)双面注浆(实心注浆)。
泥浆注入模型和模芯的空穴中,泥浆被模型和模芯的工作面两面吸水,泥浆中水分不断被吸收而形成坯泥,因注入的泥浆会不断减少,需陆续补充泥浆,直到空穴中泥浆全部变成坯。
双面注浆特点:
坯体厚度由模型和模芯之间的空穴尺寸决定。
无多余泥浆倒出。
坯体的形成过程被缩短。
模型复杂。
注件均匀性不理想,远离模面处的致密度小。
泥浆注入模型后需振荡几下,使气泡逸出,得到致密坯体。
需预留出气口。
适合于坯体的内外表面形状,花纹不同,大型壁薄的产品。
空心注浆和实心注浆对泥浆性能要求也不同:
空心注浆要求泥浆的比重小些,防止注浆后坯体内表面有泥缕和不光滑的现象。
要求泥浆具有较高的稳定性,触变性不能太大,粒度要细一些。
实心注浆常用较浓的泥浆来缩短吸浆时间。
触变性可稍大,粒度可粗些。
采用基本注浆法成型,石膏模的干燥程度要适中,模型各个部位的干燥程度一致,表面要清洁以免出现开裂,变形等缺陷;
浇注过急会出现气孔和针眼;
脱模过早,原料过细会引起坯体变形和塌落。
热压铸成型(掌握)
热压铸成型过程:
将含有石蜡的浆料在一定温度和压力下注入金属模中,待坯体冷却凝固后再行脱模的成型方法。
热压铸成型包括制备蜡浆,坯体浇注,排蜡。
蜡浆由陶瓷粉料,塑化剂(常用石蜡,熔点55~60℃,150℃挥发),表面活性剂组成。
粉料在配浆前进行预烧的目的是什么?
1)降低制品的烧成收缩。
预烧温度根据原料的性质而定。
滑石预烧温度1300℃,工业氧化铝为1300~1400℃。
2)减少塑化剂的用量。
5.2.2可塑法成型
1用模具或刀具等运动所造成的压力,剪切力或挤压力等外力对可塑性的坯料进行加工,迫使坯料在外力作用下发生可塑变形而制作坯体的成型方法。
2可塑法成型的特点:
传统陶瓷和特种陶瓷普遍采用的成型方法。
适合成型具有回转中心的圆形产品如管,棒等。
结合剂用量少于注浆成型。
要求坯料具有较高的屈服值和较大的延伸变形量(屈服值至到破裂点这一段)。
5.2.2.2滚压成形(掌握)
1滚压成型是在旋压成型的基础上发展起来的一种可塑成型方法。
滚压成型过程:
把扁平形的刀改为滚压头。
盛放泥料的石膏模型和滚压头分别绕自己的轴线以一定速度同方向旋转,滚压头在转动的同时,逐渐靠近石膏模型,并对泥料进行滚压成型。
2滚压成型特点:
泥料在滚压头作用下均匀展开,受力由小到大比较均匀。
滚头和泥料的接触面积大,受压时间长,坯体致密均匀,强度较大。
靠滚压头使坯体表面光滑,勿需加水,减少了坯体的变形。
滚压成型坯体质量好,生产效率高,滚压机和其它设备配合可组成生产流水线,在日用陶瓷生产中已逐步取代了旋坯成型。
3阳模成型:
滚压头决定坯体的外表形状和大小。
适于成型扁平状,宽口器皿和坯体内表面有花纹的产品。
石膏模转速(主轴转速)不能太快,以免坯料被甩掉。
要求坯料水分少,可塑性好。
带模干燥,坯体有模型支撑,脱模较困难但变形较小。
4阴模成型:
滚压头形成坯体内表面。
适于成型口径较小而深的制品。
成型时为防止坯体变形,常将带坯的模型倒装放置,之后脱模干燥。
5滚压成型主要控制因素:
1)对泥料的要求:
要求泥料具有一定的可塑性,并有较大的延伸变形量。
可塑性太低,滚压时坯体易开裂,可塑性过高,水分又比较多,容易粘滚头。
2)滚压头的温度:
为使坯体表面光滑,泥料不沾滚头,可将滚头加热,称为热滚压。
温度为100~130℃。
不同坯料,合适的滚头温度不一样。
热滚压对泥料可塑性要求不严,使用范围广。
冷滚压要求泥料可塑性较高,水分少。
3)主轴转速和滚头转速:
主轴转速快可提高产量。
阳模成型主轴转速过大,泥料易脱离模型。
阴模成型时,主轴转速可适当增大,太小容易粘滚头。
产品直径大,主轴转速应稍小;
直径小,可适当提高主轴转速。
5.2.3压制法成型(掌握)
压制成型的特点:
生产过程简单。
坯收缩小,致密度高,产品尺寸精确。
对坯料的可塑性要求不高。
对形状复杂的制品难以成型,多用来成型扁平状制品。
等静压工艺的发展使许多复杂形状的制品也可以压制成型。
(1)干压成型:
粉料中加入少量结合剂,先经造粒,然后将造粒后的粉料置于钢模中,在压力机上加压形成一定形状的坯体。
插模:
模框固定在压机底座,上模芯直接进入模腔,下模完成装料,出模等动作。
盖模:
下模模宽可上下移动,上模芯尺寸大于下模腔,压制过程中上模芯下降,推压在下模框上,使上模芯得以将压力施加于粉料上。
插模精度高,易排气,成品质量好,目前国内大多数墙地砖生产厂家都采用插模。
(2)等静压成型
等静压成型的理论基础:
帕斯卡原理即加在密闭液体上的压强能够大小不变地被液体向各个方向传递。
等静压成型的特点:
多方向加压,多面受压,有利于粉料压实到相当的密度,提高了压制效率。
生坯密度高,各个方向都密实均匀。
生坯中很少出现应力的现象。
生坯强度高,内部结构均匀,无颗粒取向排列。
粉料含水率低(1~3%),使用粘合剂和润滑剂少,可减少干燥和烧成收缩。
对制品尺寸限制不大。
不消耗石膏模,半成品不经干燥工序,直接入窑烧成,简化了生产工序,提高了产品品质。
一次烧成:
成型、干燥或施釉后的生坯,在陶瓷窑内一次烧成陶瓷产品的工艺路线。
工艺流程简化;
劳动生产率高;
成本低,占地少;
节约能源。
二次烧成:
即先素烧后施釉。
避免气泡、针孔、吸釉、干釉等釉面缺陷,提高坯体强度和密度,增加釉面的白度和光泽度,提高釉面质量,提高产品合格率。
陶瓷胎体的显微结构(重点)
1显微结构指利用各种显微镜才能观察到材料的组织结构,是组成、工艺、过程等因素的反映,是决定材料性能的基础。
2显微结构的组成:
陶瓷坯体的显微结构:
晶相、玻璃相、气相构成。
晶相:
研究种类,数量,形态,晶粒的大小、分布和取向,晶体缺陷。
玻璃相:
研究含量、分布、应力分布等。
气孔:
研究大小、多少、分布、位置等及微裂纹的大小、形状分布等。
3显微结构的组成——晶相:
长石质瓷的晶相:
莫来石,残余石英,半安定方石英。
总量占45~60%。
滑石质瓷的晶相:
原顽火辉石,斜顽火辉石。
骨灰瓷的晶相:
—Ca3(PO4)2,Ca—长石。
特种瓷的晶相:
晶相所占的比例大。
如:
刚玉瓷中刚玉晶相>
95%。
晶相的作用:
提高材料力学性能、热性能、电绝缘性能等。
4显微结构的组成——玻璃相:
坯料组分或杂质所形成的低共熔固体物质。
组成:
与坯料配方有关,特别是与熔剂性原料的种类有关。
具有不均匀性。
作用:
普通陶瓷的玻璃相为连续相,分布在晶相周围,粘接晶粒,填充空隙,促进坯体致密,提高胎体的透明度,降低坯体的烧结温度。
注意:
玻璃相结构疏松,强度比晶相低,膨胀系数大,高温下易软化变形,因此过多会降低制品强度及热震性→高温易变形。
5显微结构的组成——气孔:
普通陶瓷存在少量的气孔。
气孔率在0.5%~22%。
气孔分布在玻璃相的连续基质中。
气孔会明显影响材料性能,降低坯体机械强度、介电强度、透光性、白度等,降低化学稳定性、抗冻性,增大介电损耗和吸湿