车螺纹时相关工艺知识内螺纹Word格式文档下载.docx
《车螺纹时相关工艺知识内螺纹Word格式文档下载.docx》由会员分享,可在线阅读,更多相关《车螺纹时相关工艺知识内螺纹Word格式文档下载.docx(16页珍藏版)》请在冰豆网上搜索。
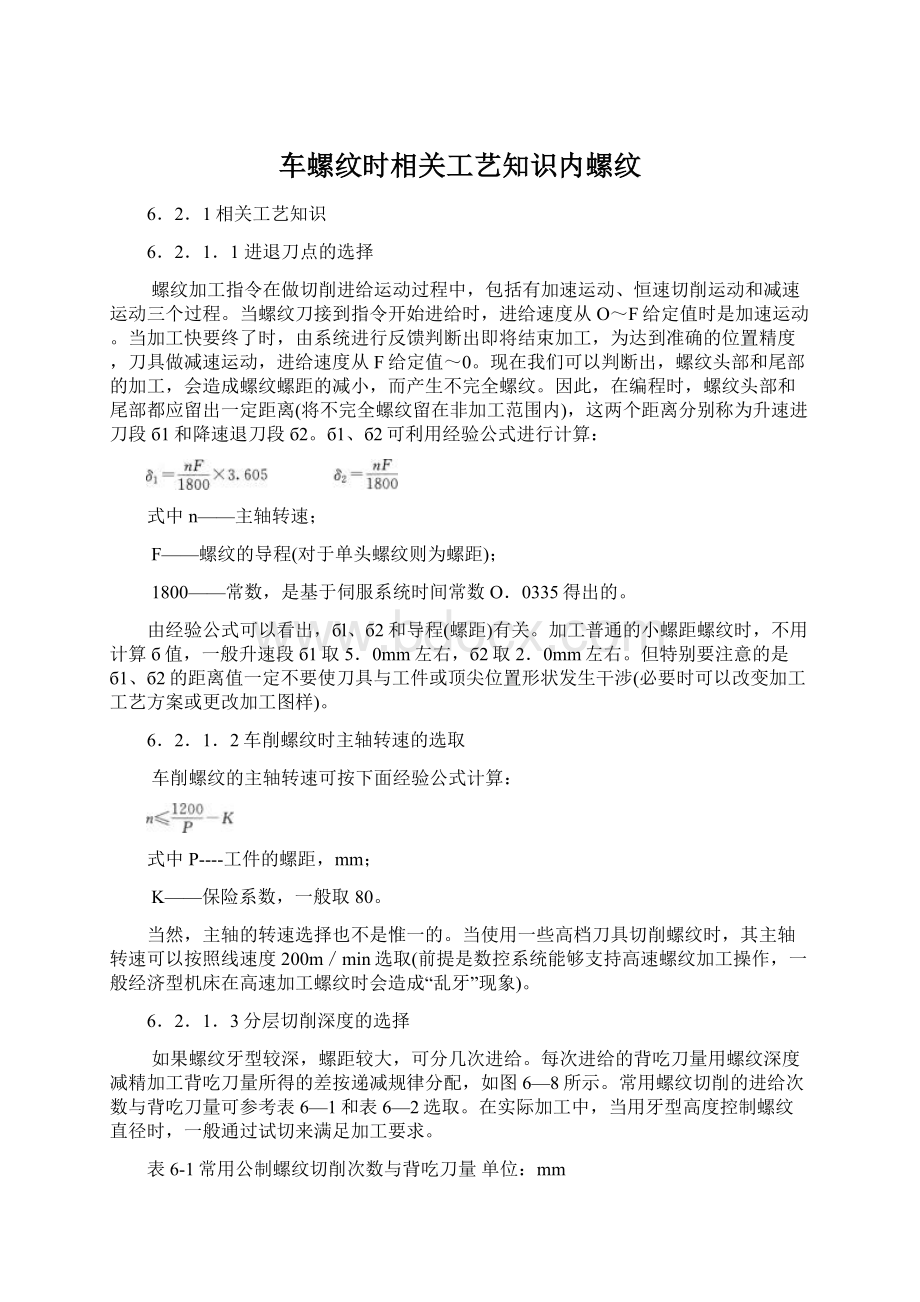
0.7
O.8
O.9
1.O
1.2
第2次
0.4
O.6
0.6
O.7
第3次
O.2
第4次
O.16
O.4
背吃刀量
第5次
0.1
及切削次数
第6次
0.15
第7次
0.2
第8次
0.3
第9次
说明:
当然,螺纹切削的进给次数与背吃刀量也需根据不同的加工材质和刀具质量自定选取,但一定要遵循逐渐递减的原则。
6.2.1.4螺纹车刀的装夹方法
车削螺纹时,为了保证齿形正确,对安装螺纹车刀提出了较严格的要求。
(1)刀尖高装夹螺纹车刀时,刀尖位置一般应与车床主轴轴线等高。
特别是内螺纹车刀的刀尖高必须严格保证,以免出现“扎刀”、“阻刀”、“让刀”及螺纹面不光等现象。
表11-2常用英制螺纹切削次数与背吃刀量单位:
in
英制螺纹
牙/in
24牙
18牙
16牙
14牙
12牙
10牙
8牙
O.678
O.904
1.016
1.162
1.355
1.626
2.033
O.3
O.5
O.11
O.14
背吃刀量
O.13
O.21
O.17
当高速车削螺纹时,为防止振动和“扎刀”,其硬质合金车刀的刀尖应略高于车床主轴轴线0.1~O.3mm。
(2)牙型半角装夹螺纹车刀时,要求它的刀尖齿形对称并垂直于工件轴线[如图6—11(c)所示],即螺纹车刀两侧刀刃相对于牙型对称中心线的牙型半角应各等于牙型角的一半(锯齿型螺纹和其他不存在牙型半角的非标准螺纹无此项要求)。
它通过牙型对称中心线与车床主轴轴线处于垂直位置的要求来安装螺纹刀。
图6—11外螺纹刀安装
图6—12内螺纹刀的安装
如果外螺纹刀装歪,如图6—11(b)所示,所车螺纹就会产生牙型歪斜等质量异常现象,而影响正常旋合。
外螺纹车刀装刀时可按照图6一11(a)所示,用样板校对刀型与工件垂直的对刀方法安装、锁紧螺纹刀。
内螺纹车刀装刀时可按照图6—12所示,用样板校对刀型与工件端面平行的方法安装内螺纹刀。
(3)刀头伸出长度刀头一般不要伸出过长,约为刀杆厚度的1~1.5倍。
内螺纹车刀的刀头加上刀杆后的径向长度应比螺纹底孔直径小3~5mm,以免退刀时碰伤牙顶。
6.2。
1.5内螺纹孔径的计算
由于国家标准规定螺纹孔径有很大的公差,内螺纹小径的基本尺寸与外螺纹小径的基本尺寸相同,为了计算方便,可用近似公式:
d1=d一(1~1.1)P
式中d1——内螺纹小径尺寸;
d——内螺纹大径尺寸;
P——螺距。
当用丝锥攻制内螺纹或高速切削塑性金属内螺纹时,螺纹孔径加工尺寸推荐:
d1=d—P
当车削脆性金属(铸铁等),或低速车削内螺纹(尤其是细牙螺纹)时,螺纹孔径推荐:
d1=d一1.1P
6.2.1.6车削螺纹时常见故障分析
车削螺纹时,由于各种原因,造成加工时在某一环节出现问题,引起车削螺纹时产生故障,影响正常生产,这时应及时加以解决。
车削螺纹时常见故障及解决方法如下。
(1)车刀安装得过高或过低过高,则吃刀到一定深度时,车刀的后刀面顶住工件,增大摩擦力,甚至把工件顶弯;
过低,则切屑不易排出,车刀径向力的方向是工件中心,致使吃刀深度不断自动趋向加深,从而把工件抬起,出现啃刀。
此时,应及时调整车刀高度,使其刀尖与工件的轴线等高。
在粗车和半精车时,刀尖位置比工件的中心高出1%D左右(D表示被加工工件直径)。
(2)工件装夹不牢工件夹装时伸出过长或本身的刚性不能承受车削时的切削力,因而产生过大的挠度,改变了车刀与工件的中心高度(工件被抬高了),形成切削深度突增,出现啃刀。
此时应把工件装夹牢固,可使用尾座顶尖等,以增加工件刚性。
(3)牙形不正确车刀在安装时不正确,没有采用螺纹样板对刀,刀尖产生倾斜,造成螺纹的半角误差。
另外,车刀刃磨时刀尖角测量有误差,产生不正确牙形,或是车刀磨损,引起切削力增大,顶弯工件,出现啃刀。
此时应对车刀加以修磨,或更换新的刀片。
(4)刀片与螺距不符采用定螺距刀片加工螺纹时,刀片加工范围与工件实际螺距不符,也会造成牙型不正确甚至发生撞刀事故。
(5)切削线速度过高进给伺服系统无法快速地响应,造成乱牙现象发生。
因此,一定要了解机床的加工性能,而不能盲目地追求“高速、高效’,加工。
(6)螺纹表面粗糙原因是车刀刃口磨得不光洁,切削液不适当,切削参数和工件材料不匹配,以及系统刚性不足切削过程产生振动等造成的。
应正确修整砂轮或用油石精研刀具(或更换刀片);
选择适当切削速度和切削液;
调整车床滚珠丝杠间隙,保证各导轨间隙的准确性,防止切削时产生振动。
另外,在高速切削螺纹时,切屑厚度太小或切屑斜方向排出等原因造成拉毛已加工表面。
一般在高速切削螺纹时,最后一刀切削厚度要大于O.1mm,切屑要垂直于轴心线方向排出。
对于刀杆刚性不够,切削时引起振动造成的螺纹表面粗糙,可以减小刀杆伸出量,稍降低切削速度。
6.2.2数控车床加工操作实例
在数控车床上加工如图6—13所示零件。
6.2.2.1零件图工艺分析
(1)技术要求分析
此零件图为内、外螺纹配合件,包括外圆柱阶梯面、外螺纹、外退屑槽加工;
内圆柱阶梯面、内螺纹和内倒角等加工,并配合手工截断、车端面、倒角等操作保证零件尺寸精度。
图6一13加工操作实例零件图
零件材料为LYl2硬铝合金,内、外圆柱面粗糙度要求Ra1.6μm,其余各处要求均为Ra3.2μm,内螺纹件要求内螺纹孔与外圆柱面有同轴度要求;
内、外圆柱Φ30处为配合位置设计,尺寸精度要求分别为Φ30和,精度要求较高。
两配合件间隙为O.1mm,配合处偏差范围为O.07~O.13mm。
无热处理和硬度要求。
(2)确定装夹方案、定位基准和刀位点
a.装夹方案原料为毛坯棒料,可采用三爪自定心卡盘装夹定位。
外螺纹轴工件,伸出卡盘端面50mm。
内螺纹套工件,伸出卡盘端面40mm。
b.设定程序原点以工件右端面与轴线交点处建立工件坐标系(采用试切对刀法建立)。
c.换刀点设置在工件坐标系X200.OZ100.0处。
d.加工起点设置外螺纹轴工件粗、精加工设定在X42.0Z2.O处;
退屑槽设定在X30.0Z2.O处;
外螺纹设定在X22.OZ5.O处。
内螺纹套工件外圆粗、精加工加工设定在X42.0Z2.0处;
镗内孔粗、精加工设定在X16.OZ2.O处;
内倒角加工设定在X17.0Z2.O处;
内螺纹加工设定在X17.0Z2.O处。
(3)刀具选择、加工方案制定和切削用量确定分别见表6—3和表6—4。
表6-3a外螺纹轴工件刀具选择
实训课题
内、外螺纹车削训练
零件名称
内、外螺纹
零件图号
图6-12
配合件
序号
刀具号
刀具名称
规格
数量
加工表面
备注
1
T0101
93。
外圆车刀
20mmX20ram
端面、外圆
粗、精车
2
T0303
60。
外螺纹车刀
外螺纹
3
T0404
切槽车刀(刀宽4mm)
20mmX20mm
退屑槽
精车
4
切断刀(刀宽4mm)
切断棒材
手动
5
T0202
45。
倒角
表6一3b内螺纹套工件刀具选择
图6—12
刀具号
备注。
93~外圆车刀
20mmX20mm
镗孔车刀
12mmX150mm
×
15mm
内孔圆
内螺纹车刀
150mmX16mm
32mmXl5mm
内槽车刀
(刀宽3mm)
150mmX16mmX
35mmX15mm
内倒角
(替换内槽7/)
切断车刀(刀宽4mm)
6
(替换镗孔刀)
表6一4a外螺纹轴加工方案制定和切削用量
材料
LYl2
系统
FANUC
工序号
01外螺纹轴
切削用量
操作序号
工步内容(走刀路线)
G功能
T刀具
主轴转速s
/(r/min)
进给速度F/(mm/r)
切削深度/mm
主程序
夹住棒料一头,留出长度大约50mm(手动操作),调用主程序001131加工
(1)
粗外圆柱阶梯面
G71
600
O.15
(2)
精外圆柱阶梯面
1000
O.05
0.Z5
(3)
切退刀槽
G01
450
(4)
车外螺纹
G76
400
螺距:
2.O
自动递减
(5)
切断
手控
(6)
调头车端面
800
(7)
调头车倒角
表6一4b内螺纹套加工方案制定和切削用量
02内螺纹套
主轴转速s
/(r/min)
进给速度F
/(mm/r)
切削深度/mm
Φ16毛坯孔采用手动钻孔方式加工。
通过夹住棒料一头,留出长度大约50mm(手动操作),调用主程序00009加工
粗车外圆表面
G90
O.25
粗镗内孔表面
O.1
精镗内孔表面
G70
内倒角加工
内螺纹加工
G92
2.0
逐渐递减
精车外圆表面
0.08
(8)
(4)数值计算
a.设定程序原点外螺纹件以工件右端面与轴线的交点为程序原点,建立工件坐标系。
内螺纹套件以工件左端面与轴线的交点为程序原点,建立工件坐标系。
b.计算基点位置坐标值图中各基点坐标值可通过标注尺寸识读或换算出来(略)。
c.螺纹的计算
①轴螺纹的计算
根据公式d=D一1.3P:
=20一1.3×
2=17.4mm
轴螺纹底径坐标尺寸(螺纹加工最后一刀尺寸)为X17.4Z一23.O。
②套螺纹的计算
根据公式d1=d—P=20—2=18mm
套螺纹孔底径坐标尺寸为X18.Oz一33.5
(5)工艺路线的确定
a.螺纹轴的加工
①用G71复合固定循环指令粗车外圆表面(精加工余量O.5mm)。
②用G70精加工循环指令精车内圆表面。
精车轨迹为:
G00移刀至X0Z2.O—G01工进移刀至X0ZO一工进切削端面并倒角C2.O至X19.8Z0一工进切削外圆面至X19.8Z一25.O一工进车端面台至X30.OZ一25.O一工进车外圆阶台轴至X30.0Z一30.1一工进车端面台并倒角CO.5至X39.OZ一30.1一工进车外圆阶台轴至X39.0Z一41.0。
③切退屑槽。
轨迹为:
快速移刀至X30.OZ2.0一快速移刀至X30.OZ一25.O一工进移刀至X20.0z一25.0一工进切削至X16.0Z一25.O一刀具在槽底停2转(G04U2.O)一工进返回至X20.0Z一25.O。
④切外螺纹。
用G76复合螺纹切削循环指令切削外螺纹。
螺纹底径至X17.4Z一23.O;
精加工重复次数(m:
3次);
刀尖角度(a:
60。
);
最小切削深度(Δdmin:
0.1mm);
精加工余量(d:
0.2mm);
锥螺纹的半径差(i:
0);
螺纹的牙高(k:
1.3mm);
第一次车削深度(Δd:
O.5mm)。
⑤手动切断工件一工件调头装夹(工件表面应包一层铜皮),用划针或百分表校正工件后夹紧一车端面至规定尺寸并倒角0.5mm。
b.螺纹套的加工
①手动钻毛坯孔一钻中心孔Φ3.0一用Φ10钻头钻孔,深34mm一用Φ16钻头扩孔,深34mm一用Φ16平头钻平孔底面。
②用G90单一固定循环指令粗车外圆表面(精加工余量0.5mm)。
③用G71复合固定循环指令粗镗内孔表面(精加工余量0.5mm)。
④用G70精加工循环指令精镗内孔表面。
G00移刀至X32.OZ2.0一G01工进移刀至X32.OZO一工进切削倒角至X30.OZ一1.O一工进切削内圆孔至X30.OZ一5.0一工进车内端面台并倒角C2.0至X30.OZ一5.O一工进车削螺纹孔径至X18.0Z一33.5。
⑤车孔径内倒角。
G00移刀至X17.OZ2.O—G01工进移刀至X17.OZ一33.0一工进切槽至X22.OZ一33.O一刀具在槽底停2转(G04U2.O)一工退返回至X17.cZ一33.0一Z正向工进移刀至X17.OZ一31.O—X向工进进刀至X18.0Z一31.O一工进车削倒内角C2.0至X22.0Z一33.0一刀具在槽底停2转(G04U2.O)一X向工退至(X17.cZ一33.0)一Z向工退至X17.OZ2.O。
⑥车内螺纹。
用G92螺纹循环切削指令切削内螺纹(精车时,采用螺纹轴配合车削)。
⑦精加工外圆表面。
G00移刀至起刀点X42.Oz2.O—G00移刀至X30.OZ2.O—G01工进移刀至X30.0Z0一工进切削端面并倒角C0.5至X39.0ZO一工进车削外圆表面至X39.OZ一30.5。
⑧手动切断工件一工件调头装夹(工件表面应包一层铜皮),用划针或百分表校正工件后夹紧一车端面至规定尺寸并倒角CO.5。
(6)编程
a.外螺纹轴加工程序
程序内容说明
001131;
输入程序号
N1;
粗加工外圆表面
G99G97S600M03;
转进给方式加工,主轴正转
T0101;
调用1号刀,建立工件坐标系
G00X200.0Z100.O;
换刀点
X42.OZ2.O;
循环点(加工起刀点)
G71U1.5RO.5;
用G71复合固定循环指令粗车外圆表面
G71P10Q11UO.5WO.05FO.15;
N10GOOXOlG01Z0lX19.8C2.O;
Z一25.O;
X30.0CO.5;
Z一30.1;
X39.OCO.5;
N11Z一40.5;
G00X200.OZ100.O;
返回换刀点
M05;
主轴停
M00;
进给停,检测
N2;
精车外圆表面
G99G97S1000M03;
调1号刀,建立工件坐标系
G00X42.OX2.O;
G70P10Q11FO.08;
用G70精加工循环指令粗车外圆表面
MOO;
N3;
切退刀槽
G99G97S450M03;
T0404;
调4号刀,建立工件坐标系
GOOX30.OZ2.O;
循环点(加工起刀点)
快速移刀
G01X20.OFO.3;
工进移刀
X16.OFO.05;
工进切削
G04u2.0;
槽底停2转
工进返回
GOOX200.OZ100.O;
主轴停
N4;
切外螺纹
G99G97S400M03;
T0303;
调3号刀,建立工件坐标系
G00X22.0Z5.O;
G76P030060Q100R0.2;
用G76复合螺纹切削循环指令切削外螺纹
G76X17.4Z一23.0R0P1300Q500F2.O;
M30;
程序停止,返回程序头
%
b.内螺纹套加工程序
程序内容说明
001132;
G00X42.0Z2.O;
G90X39.5Z一30.5F0.15;
用G90单一固定循环指令粗车外圆表面
粗车内孔表面
T0202;
调2号刀,建立工件坐标系
G00X16.0Z2.O;
G71U1.0RO.5;
用G71复合固定循环指令粗车内圆表面
G71P10QllU—O.5W0.05F0.1;
N10G00X32.O;
G01ZO~X30.0Z一1.O;
Z一5.O;
X18.0C2.O;
NilZ一33.5;
精车内孔表面
G70P10Q11F0.05;
用G70精加工循环指令精车内圆表面
车孔径内倒角
G99G97s400M03;
X17.0Z2.O;
加工起刀点
G01Z一33.0F0.3;
X22.0F0.05;
21进切槽
G04U2.O;
G01X17.0F0.3;
工退返回
Z一31.0;
Z正向工进移刀
X18·
0F0.05;
X向工进进刀
X22.0