青岛科技大学硫磺车间实习报告文档格式.docx
《青岛科技大学硫磺车间实习报告文档格式.docx》由会员分享,可在线阅读,更多相关《青岛科技大学硫磺车间实习报告文档格式.docx(42页珍藏版)》请在冰豆网上搜索。
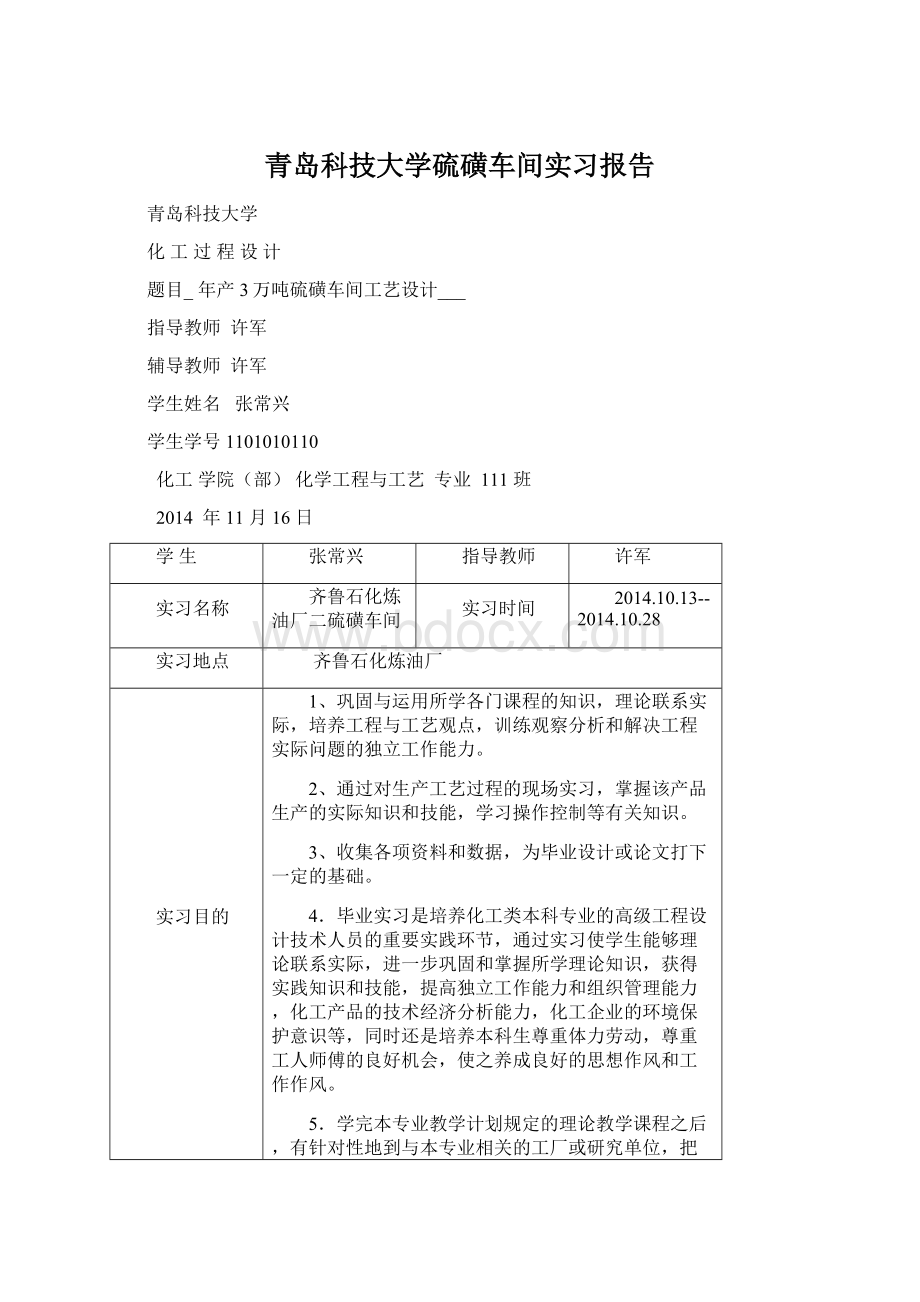
合理化建议,可以为企业生产提供先进的生产工艺,推进企业自身的技术改造。
酸性气脱硫工作在炼油厂是必须的,壳牌公司Caroline天然气加工厂克劳斯装置的脱硫率可达到98%甚至更高,我国的同类工作同世界先进水平仍有差距,因此国内企业应参照先进的生产工艺推动我国企业自身的技术改造。
本设计,除了设计说明书,还叙述了生产的工艺流程、物料衡算、部分环节的热量衡算以及设备的选型,此外,还附加了装置流程图,车间平面布置图,以供参阅。
该设计参考了大量文献,应用多种计算工具,历时六周,由于时间原因和自身能力有限所造成的不足之处,敬请指教,以求完善。
1.概述
1.1设计任务
一、设计项目:
年产3wt硫磺回收装置及尾气处理
二、生产方法:
克劳斯工艺制硫方法
三、数据来源:
齐鲁石化胜利炼油厂第二硫磺车间部分现场数据
四、设计阶段:
初步设计
五、设计内容:
1、方案设计:
确定生产工艺路线和进行流程设计,绘制流程草图。
2、物料横算
设计依据:
(1)生产规模:
3.75吨/小时
(2)生产时间:
8000小时/年
(3)原料组成:
H2S79.97%,烃类4.0%,CO2:
16.03%
3、热量衡算
4、吸收塔工艺设计与风机的设备选型以及转化炉的设备构造图
5、非工艺部分
6、绘制控制点的工艺流程图和平面图
1.2企业介绍
1.2.1齐鲁石化简介
中国石化集团齐鲁石化公司胜利炼油厂是全国颇具规模的炼油企业之一,于1966年4月动工建设,1967年10月投入生产,现已成为加工能力10500kt/a,占地面积587公顷的现代化石油加工企业。
该厂拥有生产装置和辅助生产装置60余套,拥有相应配套的科学研究、开发设计、计算机应用、环境保护等设施,是全国最具影响力的含硫原油加工以及沥青、硫磺生产和加氢工艺技术应用基地之一,生产的39种石油产品畅销全国27个省市,部分产品已进入国际市场。
胜利炼油厂坚持依靠科技求发展。
该厂VRDS-FCC组合工艺曾获联合国科技创新发明奖;
石油苯、-10号军用柴油等产品曾获国家金奖;
100号甲级道路沥青、1号喷气燃料、石油甲苯等产品曾获国家银奖;
硫磺、90号车用汽油等18种产品曾获省(部)优名牌产品称号;
汽油全部实现了高标号无铅系列化生产,其中97号无铅汽油填补了国内空白;
1999年开发投产的高等级道路沥青,技术指标达到或超过了国外同类产品水平,从而标志着胜利炼油厂的沥青产品实现了系列化。
按照“质量第一,用户至上”的原则,胜利炼油厂建立了从原材料进厂、生产过程控制、新产品开发、标准化管理、产品出厂控制到售后服务的全过程质量控制保证体系。
该厂于1998年通过了ISO9002国际质量体系贯标认证和ISO10012计量检测体系贯标认证;
2001年3月被中国实验室国家认可委员会等机构评定为“沥青产品检验实验室”。
齐鲁石化坚持科技创新,1996年以来,累计完成科研课题950项,成果鉴定169项,获得专利授权93项,16项科技成果获国家级奖励。
先后与美国、德国、英国、日本、意大利、荷兰、韩国等多家国外公司进行了成功合作。
公司凭籍自身丰富的工程建设经验,依托雄厚的技术实力和可靠的服务质量,在国内树立了良好的企业形象,形成了可研、设计、采购、施工和开车服务管理等系统的服务网络。
自主开发的硫磺回收技术及催化剂、炼厂气等温绝热加氢技术、轻烃醚化技术等填补了国内空白。
为全国“科技进步百强企业”。
在中国石油和化学工业协会、中国化工企业管理协会、中国化工情报信息协会联合发布的2003年中国化工企业500强排行榜中,齐鲁分公司、齐鲁股份有限公司分别名列第7位和第27位。
1.2.2车间简介
胜利炼油厂南生产区加工的为含硫量较高的胜利原油。
为了变废为宝,改善环境,造福人类,1971年5月由北京石油设计院设计的我国第一套自行设计的炼厂气制硫装置在胜利炼油厂建成投产,即现在的第一硫磺回收装置。
原设计规模为5500吨/年,采用分硫法,1972年改为部分燃烧法,高温掺合式的二级转化克劳斯工艺流程。
改造后的产品质量一直比较稳定,1979年被化工部和山东省评为优质产品。
随着生产发展的需要,通过挖潜改造,1975年将燃烧炉、废热锅炉更新,装置的生产规模增加到7500吨/年。
1981年对生产工艺进一步完善,将一级冷却器由立式改为卧式并增加一个大捕集器。
1982年催化剂由福建漳浦产的天然铝钒土改为由齐鲁石化公司研究院、胜利炼油厂和山东铝厂共同研制的LS-801催化剂,该催化剂为人工合成的的活性氧化铝型硫磺回收催化剂,具有强度大、磨损小、活性高、稳定性好、对有机硫水解能力强等优点。
装置总硫转化率可达96%左右,从而减少了排放废气中的硫含量。
该装置采用部分燃烧法工艺,二级转化,用高温掺合法控制转化器入口温度,因此较易控制。
另外1984年选用LS-811催化剂,转化率进一步提高,生产更加稳定。
表1-1装置情况一览表
原计划规模
5000t/a
现实际能力
7500-10000t/a
设计单位
北京石油设计院
投产日期
1971年5月
装置建设日期
1969-1970
占地面积
70×
80m2
投资
定员/现有人员
60/
1.2.3酸气来源
本装置酸性气来源分三路:
北区改扩建、新建装置的混合酸性气;
新建装置的含硫污水汽提单元的含氨酸性气和二化甲醇装置的甲醇酸性气。
三种酸性气组成如表1-2。
表1-2原料组成
名称
组成
体积%
公斤分子/时
公斤/时
混
合
酸
性
气
H2S
CO2
C1
C2
C3
C4
C5
H2
H2O
合计
91.95
0.56
0.64
0.13
0.11
0.29
4.41
2.22
100
204.06
1.69
2.14
0.43
0.36
0.96
14.66
7.36
332.09
10338.04
74.36
34.24
12.90
15.84
24.94
69.12
29.32
132.40
10731.16
1.3生产原理与工艺流程简述
1.3.1生产原理
1.3.1.1制硫工艺原理
酸性气体中的H2S的含量不同,故燃烧时放出的热量不同,根据酸性气中H2S的含量,对于不同浓度的气体,分别采用部分燃烧法、分流法、直接氧化法三中方法来回收硫磺。
本装置采用部分燃烧法回收硫磺。
一.部分燃烧法
酸性气中的H2S含量大于50%时,一般采用部分燃烧法。
将全部酸性气体引进燃烧炉,所配风量是按烃类完全燃烧和H2S的1/3完全燃烧生成SO2来计算的。
对H2S来说,反应结果炉内约有65%的H2S反应生成气体硫,而余下的35%H2S中1/3反应生成SO2、2/3保持不变。
余下没有反应的H2S、SO2在转化器内,在催化剂作用下发生反应,进一步生成气体硫。
二.分流法
酸性气中H2S含量在15-50%之间时,一般采用分流法。
即将1/3酸性气体引入燃烧炉,所配空气量为烃类完全燃烧生成SO2来计算的。
对于H2S来说,反应结果在炉内没有气体硫生成,只有SO2生成。
2/3酸性气体在一级转化器前与燃烧炉内生成的SO2汇合,同时进入转化器,在催化剂作用下,H2S与SO2反应生成气体硫。
三.直接氧化法
酸性气体中的H2S浓度低于15%时,一般采用直接氧化法。
将酸气与空气事先预热到一定温度,再引进燃烧炉、转化器发应,所需要配风量为酸性气体中的烃类完全燃烧和1/3H2S完全燃烧生成SO2来计算的,反应结果在燃烧炉或转化器内都生成气体硫。
本装置制硫的基本工艺是采用部分燃烧法,使酸性气在燃烧炉燃烧,其中的NH3和烃类组分被完全氧化分解,而H2S不完全燃烧,约有65%直接转化成元素硫,其余的H2S又有1/3转化为SO2,H2S和SO2在催化剂条件下发生低温克劳斯(Claus)反应,制硫转化率达97%以上,残余H2S及SO2和未捕集下的S经加氢还原并吸收再生利用,使装置收率达到99.9%以上。
克劳斯工艺的实质是部分氧化还原反应,其化学反应式为:
2H2S+3O2=2H2O+2SO2+Q
(1)
2H2S+SO2=3/xSX+2H2O+Q
(2)
(1)与
(2)又可写为:
2H2S+O2=2/xSX+2H2O+Q(3)
基于以上反应,在酸性燃烧炉内约有60~65%的H2S转化为元素硫。
在酸气燃烧炉内,还同时发生氨及烃类燃烧反应:
4NH3+3O2→N2+6H2O+Q(4)
CH4+2O2→CO2+2H2O+Q(5)
H2S+CO2→COS+H2O+Q(6)
2H2S+CO2→CS2+2H3O+Q(7)
在转化器中H2S与SO2在催化剂作用下继续发生低温Claus反应,如式
(2),同时还发生NH3有机硫的水解反应。
COS+H2O→H2S+CO2-Q(8)
CS2+2H2O→2H2S+CO2-Q(9)
通过一段高温反应和两级催化反应,H2S转化率可达97%以上。
1.3.1.2尾气处理工艺原理
含有一定量H2S、SO2、Sx的制硫尾气在催化剂的作用下,进行加氢反应:
SO2+3H2→H2S+2H2O(10)
Sx+xH2→xH2S(11)
加氢尾气中的H2S由MDEA吸收,净化尾气经焚烧炉焚烧后排大气,吸收了H2S的MDEA经解析得到再生酸气返回制硫部分处理。
1.3.2工艺流程简述
1.3.2.1制硫部分
来自重油加氢脱硫装置,重整装置、二催化脱硫装置、一加氢脱硫装置、二加氢脱硫装置就双塔汽提的混合酸性气与尾气处理部分、返回酸性气混合后进入混合酸性气分液罐(D—101A);
重油双塔汽提装置的含氨酸性气与三常含氨酸性气混合后进入含氨酸性气缓冲罐(D—101B),两路酸性气经缓冲罐脱水后分别进入制硫燃烧炉(F—101),经燃烧,将酸性气中的氨和烃类等有机物全部分解。
在炉内约65%(V)的H2S进行高温克劳斯反应转化为硫,余下的H2S中有1/3转化为SO2,燃烧时所需空气由离心鼓风机(K—101A、B、C)供给。
进炉的空气量按比例控制调节。
自F—101排出的高温过程气(约1322℃),一小部分通过高温掺合阀调节第一级转化器(R—101)的入口温度,其余部分进入制硫余热锅炉(ER—101)冷却至350℃,同时ER—101壳程产生3.7MPa(g)的饱和蒸汽,经蒸汽过热器(E—203)过热至450℃出装置并入整齐管网。
从ER—101出来的过程气进入一级冷凝冷却器(E—101),过程气被冷却至170℃,E—101壳程产生0.3MPa(g)的饱和蒸汽。
在E—101末端,冷凝下来的
液体硫磺与过程气分离,自底部流出进入液硫脱气池;
顶部出来的过程气经高温掺合阀调节至250℃进入一级转化器(R—101),在催化剂的作用下进行反应。
反应后的气体温度为319℃,先经过过程气换热器(E—104)管程与进二级转化器(R—102)的冷气流换热,温度降至248℃后进入二级冷凝冷却器(E—102)被冷却至170℃。
E—102冷凝下来的液体硫磺,在末端与过程气分离,自底部流出进入液硫脱气池,顶部出来的过程气经E—104壳程与一级转化器的高温气流换热后,温度由170℃升至224℃进入二级转化器(R—102),过程气在催化剂作用下继续进行反应,反应后的过程气进入三级冷凝冷却器(E—103),温度从242℃被冷却至130℃。
在E—103末端,被冷凝下来的液体硫磺与过程气分离,自底部流出进入液硫脱气池;
顶部出来的过程气经尾气分液罐(D—104)分液后,进入尾气处理部分。
图1-1制硫部分流程图
1.3.2.2尾气处理部分
制硫部分排出的硫磺尾气经过混氢,进入尾气加热器(E—201),与尾气焚烧炉(F—201)出口的高温烟气换热,温度升至300℃后进入加氢反应器(R—201),在LS—951催化剂的作用下进行加氢、水解反应,使尾气中的二氧化硫、元素硫、有机硫还原、水解为H2S。
反应后的高温气体,进入蒸汽发生器(E—202),产生0.3MPa(g)的饱和蒸汽,同时高温气体被冷却至170℃,再进入尾气急冷塔(C—201)下部。
尾气急冷塔使用的急冷水,用急冷水循环泵(P—201/A,B)自C—201底部抽出,经急冷水冷却器(A—204)冷却至40℃后返C—201循环作用。
MDEA贫液自D—206经贫胺液泵(P—202)抽出送至尾气吸收塔(C—202)上部,在塔内尾气与贫液逆流接触,其中的H2S被吸收。
自塔顶出来的净化气,进入尾气焚烧炉(F—201),在700℃高下,将净化气中残留的硫化物焚烧生成SO2。
焚烧后的高温烟气经过蒸汽过热器和尾气加热器回收热量后,烟气温度降至329℃,最后经烟囱(S—201)进入大气。
吸收H2S后的MDEA富液,由C—202塔底经富液泵(P—203/A,B)升压后,先经贫富液换热器(E—207A,B)换热,温度升至85℃进入溶剂再生塔(C—203)上部进行再生。
C—203热源由再生塔底重沸器(E—209)供给。
塔底贫液经E—207A,B温度由121℃降至79℃后再经贫液冷却器(E—208A,B)用循环水冷却至40℃后进入溶剂储罐(D—206A,B)储存,供C—202循环使用。
C—203顶气体经再生塔冷凝冷却器(A—205),温度见降至40℃进入再生塔顶回流罐(D—202)分液。
液相经再生塔顶回流泵(P—204A,B)打回C—203顶;
气体为解吸的酸性气,返回D—101A制硫。
图1-2尾气处理部分流程图
1.3.2.3液硫脱气成型部分
自E—101、102、103分出的液态硫进入液硫脱气池后,经注入氨气和氮气,用液硫脱气泵(P—102A,B)循环,将液硫中的H2S气体脱出,再用抽空器将H2S抽出送到尾气焚烧炉F—201焚烧后排烟囱。
经过脱气处理后的液硫中H2S含量小于10ppm(W),用液硫提升泵(P—103A,B)提升至硫磺成型机(MC—101A,B)造粒成型后,经自动称(W—101A,B)称重包装为50千克/袋规格的产品,自动输送码跺至硫磺库棚暂存,汽车外运出厂。
1.4操作规程
1.4.1开停工方案
一、开工前的准备
1.组织职工学习开工方案,熟悉开工程序及关键步骤的岗位操作方法。
2.检查动改技措项目是否完好,质量是否符合要求。
3.检查设备、管线的检测质量是否达到规定标准
4.检查各仪表是否达到投用条件。
5.检查开工安全环保落实情况。
6.确认催化剂的更换、装填质量。
7.准备好各种看板、图表。
二、开工程序步骤及相关内容
(一)装置吹扫、水洗、试压气密
1、尾气吹扫、气密(与硫磺装置吹扫同步)
2、主流程吹扫,气密
吹扫介质:
空气
吹扫流程:
机202→炉201→反201→换201→塔201→容208→尾气线→烟囱
↓
冷回流线机-201炉-202
3、再生酸气线先吹扫、气密
4、瓦斯线及氢气线:
与硫磺装置同步吹扫气密。
5、塔201冷却系统水冲洗。
(1)塔201冷却系统
(2)含硫污水线
(3)氨水线
第二加氢双塔给水→装置界区→泵201入口阀前拆法兰排放
排放
6、换201、炉203、容205水冲洗及试压
7、水冲洗结束后,各底点排净水。
8、循环水冲洗时设备一次通过。
(二)水联运
1、目的:
考察设备及仪表性能能否达到使用要求,检查充程是否畅通。
2、条件:
各调节阀、记录表、压力表、液位计安装就位,以表位于备用状态。
各机泵达到备用状态。
3、还原冷却系统水联运
介质:
新鲜水
泵201/1、2入口给新鲜水→滤202/1、2→冷201→塔201液位达70-80%时,停止给新鲜水→启动泵201/1、2建立循环。
循环正常后,可将LIC-201检查投用。
4、吸收再生部分
脱氧水
容203顶放空
↑
脱氧水缓慢→容203(注满80-90%)→启动泵203→FRC-310→塔202液位达80%→启动202(富液泵)→换201/1、2管程→塔203液位达50%时→换202/1、2、3、4壳程→冷202→容203
5、调整建立正常循环,循环正常后可将仪表投自动控制。
6、FRC-310循环量控制分别为:
水联运初期:
10t/h,运转8h;
水联运中期:
20t/h,运转8h
水联运后期:
30t/h,运转16h,45t/h运转8h。
7、水联运过程中,每24小时换水一次,泵202/1运行24h可切换至泵202/2。
8、关闭塔203底出口阀,将塔202注满,缢流至容202,容202液位达80%停泵202、203启动泵304/1,流程如下:
容202→泵304/1→塔203→容202;
运转4小时后将泵304/1切换至泵304/2再循环4小时(注水前打开塔顶放空)
(三)配置胺液
配置方法:
1.水联运时,R203注脱氧水至2.4m,注水前一定要打开放空阀,缓慢注入。
2.水联运完毕后,用氮气吹干净系统内积水,起动泵203带罐循环。
循环正常后把胺液桶运往现场,从泵203入口接胶带,关小容203出口阀,以泵不抽空为原则,把胶带放到胺液桶内,使胺液桶进入系统。
3.桶内胺液一定要抽干净。
现场十吨胺液全部注入系统。
4.配置完毕后分析胺浓度。
(四)炉201升温
1、点火准备
炉201按临时表(表量程0-600℃)
(1)反201入口Dg900处法兰处加盲板。
(2)与调度、动力、仪表、电气、制氢等有关单位加强联系,车间化验做好分析准备。
(3)准备好点火工具(火柴,煤油,点火棒)消防器材,防毒面具。
(4)引氢气至炉201前排放,采样分析氢气>80%为合格。
2、点火步骤
(1)拆除炉201前氢气阀后盲板(拆除TIC-201前氢气线盲板),打开开工烟筒阀,启动机202吹扫10分钟。
(2)吹扫完毕后适当关风阀,保持点火孔处微正压,从点火孔处送入点燃的火棒,引氢气进炉。
(3)点燃炉201后,迅速调节氢气进炉阀及空气量,将氢气完全燃烧。
(4)一次点火未染或中途熄火,可用氮气吹扫十分钟,再用风吹扫5-10分钟,方可重新点火。
(5)点火时,严禁正视点火孔,以防回火伤人。
3、炉201升温
(1)升温时,以炉膛前部热偶为准。
(2)严格按升温曲线进行控制并绘制出实际升温曲线。
(3)当混合室出口温度达250℃时,打开容208手孔,启动机201向混合室吹入掺合气,控制温度不超过300℃。
(4)当燃烧室温度达500℃时,炉201火嘴处注入少量氮气。
(五)炉202升温
1、点火步骤及调试方法
(1)因瓦斯前瓦斯气给气伴热。
(2)将瓦斯引至炉202前接胶带排放,采样氧含量<
1.0%后方可点火。
(3)打开汽包放空阀,关闭蒸汽出口阀,炉203注脱氧水,液面在50-70%。
(4)将空气自机202引至炉202前。
(5)打开点火孔的法兰盖,用风吹扫炉202、203至烟囱10-15分钟。
(6)把点燃的火把送入炉内,再看火孔处看到火焰。
(7)稍开风阀保持点火出微正压,稍开瓦斯进炉阀,观察瓦斯是否燃着。
(8)瓦斯燃着后,取出火把装好法兰盖。
(9)调节瓦斯、空气进炉量,使瓦斯当量燃烧,防止碳黑生成,分析氧含量数据后,及时作出调整。
(10)如一次点火未燃,应加大风量,吹扫10-20分钟,赶净瓦斯后,再次点火。
(11)炉膛温度达550℃以上,如风中断熄火,则应立即关闭瓦斯进炉阀,用氮气吹扫10-15分钟,重新点炉,若没有氮气,可用1.0MPa蒸汽(先排净凝结水)吹扫,如瓦斯中断熄火则重新引瓦斯点火即可。
2、注意事项
(1)点火时操作人员不得正视点火孔,以防回火伤人。
(2)按升温曲线严格控制,温度不得超过±
5℃。
(3)描绘出实际升温曲线,要详细记录。
(六)反201床层升温
1、条件
(1)炉201温度达1000℃。
(2)塔201、反201入口盲板拆除。
(3)换201注脱氧水至规定液位。
(4)塔201注新鲜水循环。
2、流程
炉201→反201→换201→塔201→机201→烟囱
3、拆除反201入口盲板,封好塔201人孔及容208手孔,启动泵201向塔201内注水,保持塔201液位70-80%,并建立循环,换201注除氧水保持液面50~80%;
塔201内注氨水,pH值控制在6-8。
4、按炉201升温时氢气和空气的比例,重新点燃炉201,调整进炉201氢气量和空气量,关闭开工烟囱,同时启动机201,把烟道气引入反201内,用风机201的循环量调节反应器入口温度,使床层以20℃/h速度升至200℃,在一般情况下,反应器入口温度控制在200℃左右即可。
5、机201出口压力要小于机202出口压力,如压力过高时可从机201出口向烟囱部分排放,维持每小时一次氧含量分析,含量控制在1-2%。
(七)催化剂预硫化
1、在没有硫磺尾气的情况下,避免氢气与催化剂在高于200℃时接触。
2、当催化剂床层温度达到200℃时,调整硫磺操作,使尾气中H2S/