圆孔拉刀与矩形花键铣刀的设计说明书详解Word下载.docx
《圆孔拉刀与矩形花键铣刀的设计说明书详解Word下载.docx》由会员分享,可在线阅读,更多相关《圆孔拉刀与矩形花键铣刀的设计说明书详解Word下载.docx(22页珍藏版)》请在冰豆网上搜索。
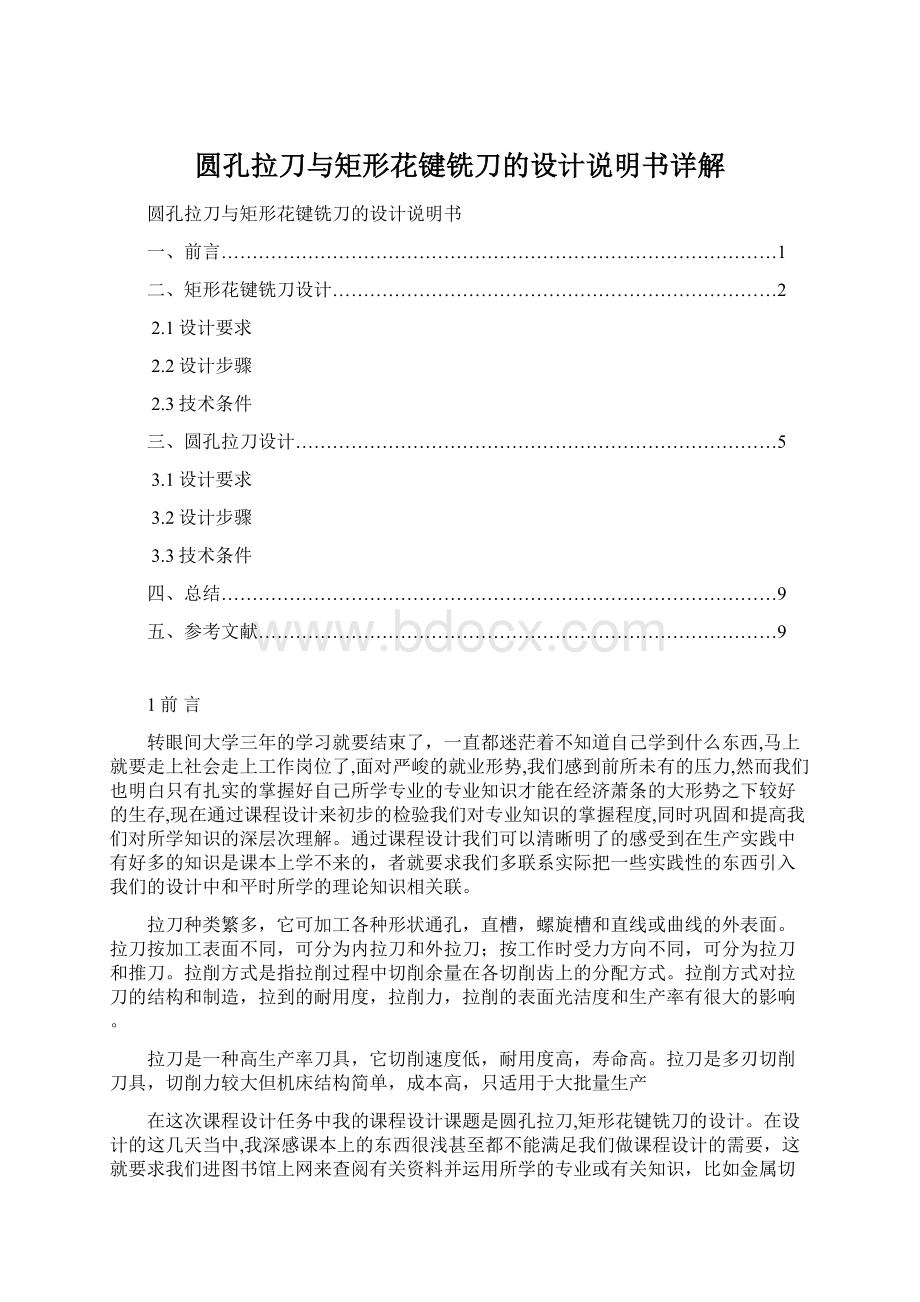
5.铣刀的外径do
对于平底形式的容屑槽,铣刀外径可按下面公式计算:
do=d+2m+2H
式中:
d-铣刀孔径
m-壁厚,一般取(0.3-0.5)d
H-全齿高
由于全齿高的计算又需依据外径do,因此,用上式直接计算铣刀外径是困难的,我国一些工厂采用下式估算铣刀外径:
do=(2-2.2)d+2.2h+(2-6)
根据上面公式的计算结果再取外径的推荐值。
6.铣刀的圆周齿数Zk
铲齿成形铣刀的圆周齿数Zk可按下式计算
Zk=Πdo/S
式中S为铣刀的圆周齿距,粗加工时,可取S=(1.8-2.4)H
精加工时,可取S=(1.3-1.8)H,式中H为容屑槽的高度。
但是在设计成形铣刀时,直接按公式计算圆周齿数是困难的,因为式中H尚未确定,而确定它时,又要反过来依据铣刀的圆周齿数。
因而在设计时,可根据生产经验按铣刀外圆直径的大小预先选定圆周齿数,在设计计算出铣刀的其他结构参数后再反过来校验圆周齿数设计得是否合适。
7.铣刀的后角及铲削量K
设铲齿成形铣刀的顶刃径向后角为αf,一般取αf=10o-15o。
相应的铲削量可按下式计算:
K=tgαfΠdo/Zk,式中do为铣刀外径,Zk为圆周齿数。
求出铲削量后,应按附录表40所列的铲床凸轮的升距选取相近的K值。
初步选定径向后角和计算出铲削量以后,需验算刀齿侧刃上一点x的主剖面后角αox,验算应选ψx最小处的x点,验算公式可按下面公式:
tgαox=tgαfsinψx
应使αox不小于2-3o。
实际计算表明,当ψx<
15时,常满足这宜要求,可采用增大顶刃后角,斜置工件,斜铲齿等方法增大侧刃后角。
对于精度要求高的成形铣刀,其齿背除铲齿外尚需进行铲磨。
为使铲磨时又砂轮空刀,齿背后部应做出深铲部分。
选择II型深铲形式,经计算选K=4,K2=0.7-0.8
8.容屑槽尺寸
(1)容屑槽底半径r
可按下式计算:
r=Π[do-2(h+K)]/2AZh
式中A为系数,当铲齿凸轮空程角δ=60时,A=6,当δ=90时,A=4。
对于需要铲磨齿背的成形铣刀,通常取δ=90o计算出的r应圆整刀0.5mm。
(2)容屑槽间角θ:
一般取20o-35o
(3)容屑槽深度H:
H=h+K+K2+r
9.分屑槽尺寸
当铣刀宽度B<
20时,切削刃上不需要作分屑槽。
10.刀齿、刀体强度和砂轮干涉的校验
由以上所述可以看出,在确定铲齿成形铣刀的外径do,齿数Zk,铲削量K,容屑槽深度H......等参数时,常常互相牵涉,难以直接确定某一参数。
因此,需采取试算的方法,首先假设几个参数的数据,再根据他们确定其他一些参数。
这样选定成形铣刀的各参数后,还需进行校验,检验铣刀结构是否紧凑,合理,刀体,刀齿强度是否足够。
2.1设计要求
被加工零件如图2.所示,工件材料为:
可锻铸铁KTB400-05;
硬度HBS210;
强度σb=400Mpa;
工件长度L=32mm。
外径
内径
键数
键宽
2.2设计步骤
⑴齿槽半角
=180/Z=180/6=30o
⑵齿顶圆弧中心半角ψ=
=
⑶齿顶宽
⑷齿廓高度
⑸铣刀宽度
取B=13
⑹铣刀齿顶圆弧半径
⑺铣刀前角
⑻容屑槽形式在铣削深度较小和刀齿强度足够的情况下,应采用平底式;
在铣削深度较大时,宜采用加强式。
故该容屑槽选择采用平底式。
⑼铣刀孔径根据切削宽度B=13查表3-4,可得d=22mm
⑽铣刀外径
⑾铣刀齿数查表3-6
⑿铣刀后角
故
=
可满足要求
⒀铲削量
查附表—2取k=3
=4.5
⒁容屑槽半径
取r=2
⒂容屑槽间角
⒃容屑槽深度
⒄分屑槽尺寸因为该铣刀宽度小于20,故切削刃上不需做分屑槽
⒅键槽尺寸和内孔空刀尺寸
查附录表1得d=22,r=1.0,t=17.6,
=24.1,h=4
查附录表3
=9
⒆校验
①检验刀齿强度
齿根宽度C
所以刀齿强度满足要求
②检验刀体强度
所以刀体满足要求
2.3矩形花键铣刀的技术条件
1.光洁度(按GB1031-68)
(1)刀齿前刀面,内孔表面、端面及铲磨铣刀的齿背表面--不低于7
(2)铲齿铣刀的齿背面--不低于6
(3)其余部分--不低于4
2.尺寸公差:
表4
序号
名称
符号
公差
1
铣刀外径
do
h16
2
铣刀宽度
B
h12
3
铣刀孔径
d
H7
4
铣刀键槽宽度
b
(Dc7)
5
内孔至键底距离
t1’
H14
3.形状位置公差
表5
项目
铣刀尺寸范围
切削刃的径向及端面跳动
do<
100
do≥100
0.03
0.04
刀体端面跳动
0.02
前面的径向性(只许凹入)
H≤10
10<
H≤20
20<
H≤30
H>
30
0.06
0.09
0.12
4.齿形误差
表6
铣刀齿形高度h
透光度
齿形的基本部分
齿顶及圆角部分
≤4
4-12
12-22
>
22
0.05
0.07
0.08
0.15
5.材料及热处理
铣刀材料一般用高速钢,热处理后硬度应为HRC63-66。
在铣刀的工作部分,不得有脱碳层和软点。
三、拉刀的设计
拉刀是一种高生产率的刀具,可以用来加工各种形状的通孔、直槽、螺旋槽以及直线或曲线外表面,广泛的用于大量和成批生产中。
下面是一些常用的圆孔拉刀和对应加工的工件(如下图)
图
用于拉削的成形刀具。
刀具表面上有多排刀齿,各排刀齿的尺寸和形状从切入端至切出端依次增加和变化。
当拉刀作拉削运动时,每个刀齿就从工件上切下一定厚度的金属,最终得到所要求的尺寸和形状。
拉刀常用于成批和大量生产中加工圆孔、花键孔、键槽、平面和成形表面等,生产率很高。
拉刀按加工表面部位的不同,分为内拉刀和外拉刀;
按工作时受力方式的不同,分为拉刀和推刀。
推刀常用于校准热处理后的型孔。
拉刀的种类虽多,但结构组成都类似。
如普通圆孔拉刀的结构组成为:
柄部,用以夹持拉刀和传递动力;
颈部,起连接作用;
过渡锥,将拉刀前导部引入工件;
前导部,起引导作用,防止拉刀歪斜;
切削齿,完成切削工作,由粗切齿和精切齿组成;
校准齿,起修光和校准作用,并作为精切齿的后备齿;
后导部,用于支承工件,防止刀齿切离前因工件下垂而损坏加工表面和刀齿;
后托柄,承托拉刀。
拉刀的结构和刀齿形状与拉削方式有关。
拉削方式通常分为分层拉削和分块拉削两类。
前者又分成形式和渐成式;
后者又分轮切式和综合轮切式。
成形式拉刀各刀齿的廓形均与被加工表面的最终形状相似;
渐成式拉刀的刀齿形状与工件形状不同,工件的形状是由各刀齿依次切削后逐渐形成。
轮切式拉刀由多组刀齿组成,每组有几个直径相同的刀齿分别切去一层金属中的一段,各组刀齿轮换切去各层金属。
综合轮切式拉刀的粗切齿采用轮切式,精切齿采用成形式。
轮切式拉刀切削厚度较分层拉削的拉刀大得多,具有较高的生产率,但制造较难。
拉刀常用高速钢整体制造,也可做成组合式。
硬质合金拉刀一般为组合式,因生产率高、寿命长,在汽车工业中常用于加工缸体和轴承盖等零件,但硬质合金拉刀制造困难。
(一)选定刀具类型和材料的依据
1选择刀具类型:
对每种工件进行工艺设计和工艺装备设计时,必须考虑选用合适的刀具类型。
事实上,对同一个工件,常可用多种不同的刀具加工出来。
采用的刀具类型不同将对加工生产率和精度有重要影响。
总结更多的高生产率刀具可以看出,增加刀具同时参加切削的刀刃长度能有效的提高其生产效率。
例如,用花键拉刀加工花键孔时,同时参加切削的刀刃长度l=B×
n×
Zi,其中B为键宽,n为键数,Zi为在拉削长度内同时参加切削的齿数。
若用插刀同时参加切削的刀刃长度比插刀大得多,因而生产率也高得多。
2正确选择刀具材料:
刀具材料选择得是否恰当对刀具的生产率有重要的影响。
因为硬质合金比高速钢及其他工具钢生产率高得多,因此,在能采用硬质合金、的情况下应尽力采用。
由于目前硬质合金的性能还有许多缺陷,如脆性大,极难加工等,使他在许多刀具上应用还很困难,因而,目前许多复杂刀具还主要应用高速钢制造。
拉刀结构复杂,造价昂贵,因此要求采用耐磨的刀具材料,以提高其耐用度;
考虑到还应有良好的工艺性能,根据《刀具课程设计指导书》表29,选择高速工具钢,其应用范围用于各种刀具,特别是形状较复杂的刀具。
根据表30,选择W18Cr4V。
(二)刀具结构及各部分功用
1拉刀的结构
图1
表1
代号
名称
功用
柄部
夹持拉刀,传递动力
颈部
连接柄部和后面各部,其直径与柄部相同或略小,拉刀材料及规格等标记一般打在颈部。
过度锥
颈部到前导部的过渡部分,使拉刀容易进入工件孔中。
前导部
起引导拉刀切削部进入工件的作用,
切削部
担负切削工作,包括粗切齿、过渡齿及精切齿。
6
校准部
起刮光、校准作用,提高工件表面光洁度及精度,并作为切削部的后备部。
7
后导部
保持拉刀与工件的最后相对位置,防止在拉刀即将离开工件时因工件下垂而损坏工件已加工表面及刀齿。
8
尾部
支持拉刀使之不下垂,多用于较大较长的拉刀,也用于安装压力环。
2切削方式:
采用分层拉削方式中的同廓式拉削方式
拉刀刀齿结构:
表2
功用
前刀面
切削流出的表面
后刀面
最终形成已加工表面的面
副后刀面
刀齿上和已加工表面相对的表面、分屑槽两侧面
刃带
也称第一后刀面,是主切削刃和后刀面之间的后角为零的窄面,它有稳定的拉削过程,防止拉刀摆尾的作用
主切削刃
是前后刀面的交线
副切削刃
是前刀面和副后刀面的交线,分屑槽中也有两条副切削刃
过渡刃
可以是直线或圆弧,它有助于减缓刀尖的磨损
刀尖
主副切削刃的相交点
容屑槽
其形状必须有利于切屑卷曲,并能宽敞地容纳切屑
分屑槽
减小切削宽度,降低切削卷曲阻力,便于切削容纳在容屑槽内,从而改善拉削状况
棱
刀齿后刀面与齿背的交线
齿背
容屑槽中靠近后刀面的部分
3圆孔拉刀
3.1设计要求
孔的直径:
3.2设计步骤
拉刀的结构和刀齿形状与拉削方式有关。
硬质合金拉刀一般为组合式,因生产率高、寿命长,在汽车工业中常用于加工缸体和轴承盖等零件,但硬质合金拉刀制造困难
根据表30,选择W18Cr4V整体制造。
(二)刀具结构参数、几何参数的选择和设计
设计步骤
选择L6110拉床进行加工,其参数如下。
拉床
型号
公称拉力
Ft(KN)
床壁孔径
床壁厚度Bs
花盘孔径
花盘厚度a
法兰盘厚度a
最大行程
(mm)
L6110
125
60
1400
1、拉削余量
2、选择切削几何参数
按表5-2,5-3选择。
前角γ=10°
粗切齿后角
精切齿后角
校准齿后角
3、齿升量选择
查表5-1,取粗切齿齿升量0.05mm。
为使拉削平稳,令第一个过渡齿到最后一个精切齿间各刀齿的齿升量均匀递减。
取过渡齿和精切齿齿数5齿,齿升量可先按0.8αf、0.5αf、0.3αf、
0.2αf、0.lαf,精切齿齿升量选取0.005mm。
4.齿距及同时工作齿数
齿距p是相邻两刀齿间的轴向距离,确定齿距的大小时,应考虑到拉削的平稳性及足够的容屑空间,一般应有3~8个齿同时工作为好。
粗切齿的齿距p按经验公式计算:
最大同时工作齿数
,取整数部分为4。
过度齿齿距
P<
10mm,精切齿齿距
(便于制造)
5.容屑槽形状及尺寸
容屑槽要有足够的容屑空间,能使切屑卷曲自由,又能使刀齿有足够强度,并可多次重磨,常见的容屑槽有三种形式,分别为齿背为直线的槽形,齿背为曲线的槽形,加长齿距的槽形。
其中齿背为曲线的槽形有利于卷屑,适用于拉削韧性材料,所以选择此种槽形,并为基本槽。
图3
根据相关标准,取K=2.5(齿升量0.05mm,加工材料为可锻铸铁)
所以
根据相关标准,取h=2.5mm,g=2.5mm,r=1.3mm,R=4mm。
槽形形状及参数见图。
6.分屑槽的设计
分屑槽的作用是减小切屑宽度,便于切屑容纳在容屑槽里。
当切削韧性金属时,若没有分屑槽,则圆孔拉刀的每个刀齿切下的金属层是一个圆筒,它会套在容屑槽中,是清除切屑十分困难,对拉削过程十分不利。
故对切削宽度较大的拉刀,在切削齿的切削刃上都要做出交错分布的分屑槽,将切屑分成许多小段。
图4
根据相关标准,取分屑槽数n=6,槽宽b=1.0mm,槽深
=0.4mm,槽角
为了保证拉削质量,在最后一个精切齿上不加工分屑槽。
7.拉刀的校准齿数
表1拉刀校准部齿数
拉刀类型
校准齿齿数
圆拉刀
加工公差等级H7~H9的孔
5—7
加工公差等级H10~H11级精度的孔
4—5
加工公差等级H12~H13级精度的孔
3—4
花键拉刀、方拉刀、键槽拉刀及具有单面刀齿的拉刀
校准部的校准齿无齿升量,只作校准和修光作用,不做出分屑槽。
为了便于制造,校准齿的前角、后角与齿形均可做成与精切齿相同。
所加工圆孔精度等级为H7,所以根据上表选取校准齿数为5,取校准齿齿距p等于粗切齿齿距即p=6.5mm。
8.切削齿齿数与直径
切削齿齿数为
粗切齿的齿数根据它切去的余量与齿升量
来决定,第一个粗切齿的直径与前导部的直径相同,即没有齿升量。
这是为了避免第一个切削齿因拉削余量不均匀或金属内含有杂质而承受过大的偶然负荷。
由前面的计算得拉削余量
0.625mm,
由前面的计算可知粗切齿齿升量为0.05mm,过渡齿齿数5齿,精切齿齿数7齿,齿升量分别为0.8αf、0.5αf、0.3αf、0.2αf、0.lαf,精切齿齿升量选取0.005mm。
得
所以
得
取粗切齿5齿。
第一齿齿升量为0,第二齿齿升量取0.045mm,后三齿齿升量为0.05mm。
切削部的长度
9.非工作部分的设计
(1)柄部
柄部的作用是供拉床夹头夹住以传递动力。
其直径
至少应比拉削前的孔径小0.5mm。
拉削前的孔径D=
,所以
根据相关资料查得:
,
,C=3,
。
详细见图纸。
(2)颈部
连接柄部与其后各部分。
其长度应能使拉刀第一刀齿未进入工件孔之前,拉床夹头可以夹住柄部。
拉刀的标记就打在颈部。
颈部长度
其中
为过度锥长度,取10mm。
根据经验设计,颈部直径
(3)过度锥
其作用是使拉刀容易进入工件孔中,起对准中心作用。
过度锥长度
,其直径前端等于颈部直径,后端等于前导部直径。
(4)前导部
起导向和定心的作用,防止拉刀歪斜,并可检查拉削前孔孔径是否太小,以免拉刀第一刀齿负荷太大而损坏。
应等于拉削前孔的最小直径,长度
一般等于拉削孔长度l。
(5)后导部
保持拉刀最后的正确位置,防止拉刀即将离开工件时,工件下垂而损坏已加工表面。
其直径等于拉削后孔的最小直径,长度等于(.5~0.7)
,但不小于20mm。
。
(6)支托部
防止长而重的拉刀自重下垂,影响加工质量和损坏刀齿。
支托部长度
10.拉刀强度与拉床拉力的校验
为了不拉断拉刀和损坏拉床,在设计拉刀时,必须进行拉刀强度与拉床拉力的校验。
(1)拉削力的计算
普通拉削式圆孔拉刀的最大拉削力为
其中
为拉刀拉削刃单位长度上的拉削力,查相关资料得
=123N。
(2)拉刀强度校验
拉削是产生拉应力
应小于材料许用应力
,即
高速钢(W18Cr4V)的
=343~392MPa。
拉刀最小截面在拉刀在第一刀齿容屑槽处,d=24.45-2.5*2=19.45mm。
带入计算得
(3)拉床拉力校验
拉削时产生的最大拉削力
应小于拉床的实际拉力
L6110型拉床公称拉力为100KN,所以符合条件。
齿形
齿号
直径基本尺寸
直径尺寸公差
24.375
10
24.993
24.475
11
24.994
24.580
12
24.995
24.695
13
24.996
24.775
14
24.997
24.883
15
24.998
24.933
16
24.999
24.963
17
25.000
9
24.983
(1)拉刀各部分的表面粗糙度:
刀齿前面Ra0.8µ
m后导部表面Ra0.8µ
m
刀齿后面Ra0.8µ
m柄部表面Ra1.6µ
刃带表面Ra0.4µ
m颈部表面Ra6.4µ
前导部表面Ra0.8µ
m过渡锥表面Ra1.6µ
(2)拉刀外径在全长上的径向跳动不超过0.06mm
总结
记得当时上课的时候武老师就说过课程结束之后要进行课程设计,所以当时就特别认真的听了拉刀和铣刀的内容,那天老师通知要进行课程设计的时候,我就想还好我认真听了课,可是当我按照任务说明书里的要求去查每一个数据去去演算去校核每一个数据的时候才发现设计内容根本就不是我想的那么简单又好多的东西都是经验值还有好多的东西需要一个一个的去图书馆从