拨叉机械加工工艺规程及铣槽夹具设计.docx
《拨叉机械加工工艺规程及铣槽夹具设计.docx》由会员分享,可在线阅读,更多相关《拨叉机械加工工艺规程及铣槽夹具设计.docx(25页珍藏版)》请在冰豆网上搜索。
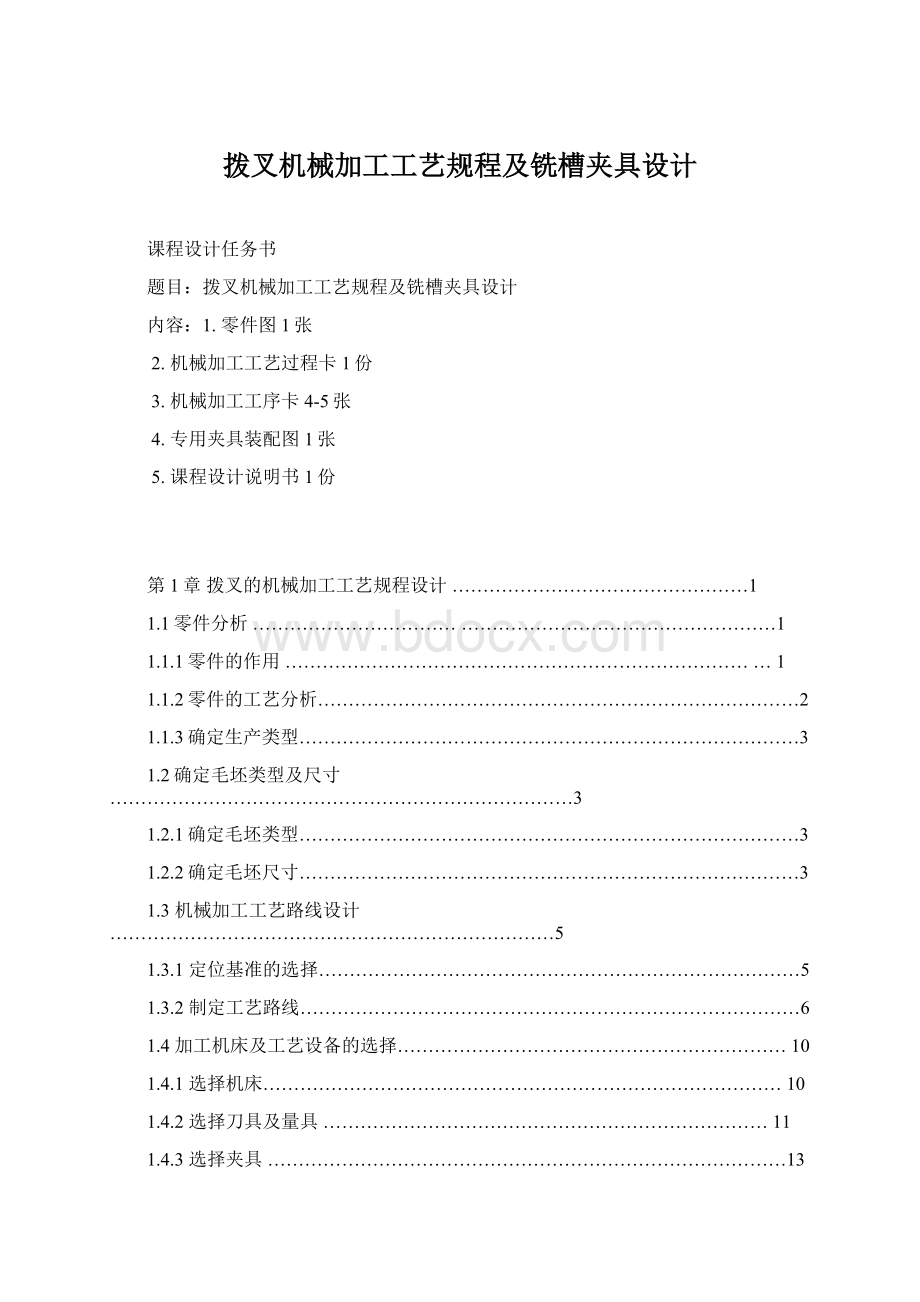
拨叉机械加工工艺规程及铣槽夹具设计
课程设计任务书
题目:
拨叉机械加工工艺规程及铣槽夹具设计
内容:
1.零件图1张
2.机械加工工艺过程卡1份
3.机械加工工序卡4-5张
4.专用夹具装配图1张
5.课程设计说明书1份
第1章拨叉的机械加工工艺规程设计…………………………………………1
1.1零件分析…………………………………………………………………………1
1.1.1零件的作用……………………………………………………………………1
1.1.2零件的工艺分析……………………………………………………………………2
1.1.3确定生产类型………………………………………………………………………3
1.2确定毛坯类型及尺寸…………………………………………………………………3
1.2.1确定毛坯类型………………………………………………………………………3
1.2.2确定毛坯尺寸………………………………………………………………………3
1.3机械加工工艺路线设计………………………………………………………………5
1.3.1定位基准的选择……………………………………………………………………5
1.3.2制定工艺路线………………………………………………………………………6
1.4加工机床及工艺设备的选择………………………………………………………10
1.4.1选择机床…………………………………………………………………………10
1.4.2选择刀具及量具………………………………………………………………11
1.4.3选择夹具…………………………………………………………………………13
1.5确定每道工序尺寸…………………………………………………………………13
1.6确定切削用量………………………………………………………………………15
1.6.1工序1(钻、扩、粗铰、精铰Φ25孔)………………………………………17
1.6.2工序2(镗孔Ф55)…………………………………………………………18
1.6.3工序3(铣40圆周面上16*8的槽)…………………………………………18
1.6.4工序40(铣40圆周面上斜面)………………………………………………19
1.6.5工序50(铣拨叉脚上端面)……………………………………………………19
第2章专用夹具设计…………………………………………………………………20
2.1确定设计任务………………………………………………………………………20
2.2夹具设计方法………………………………………………………………………20
2.2.1夹具类型的确定…………………………………………………………………20
2.2.2定位方案的确定…………………………………………………………………20
2.2.3夹紧机构设计……………………………………………………………………21
2.2.4导向装置设计……………………………………………………………………22
2.2.5夹具体设计………………………………………………………………………24
2.3确定夹具技术要求和有关尺寸、公差配合………………………………………24
2.3.1技术要求…………………………………………………………………………24
2.3.2夹具装配图应有尺寸及公差……………………………………………………24
参考文献………………………………………………………………………………26
第1章拨叉的机械加工工艺规程设计
1.1零件分析
1.1.1零件的作用
图1-1813006拨叉的零件图
零件初步分析:
该零件为CA6140车床上的拨叉813006,零件图如1-1所示。
零件功用分析:
拨叉主要用于车床的变速机构中,主要起换档作用,使主轴回转运动按照工作者的要求工作,获得所需的速度和扭矩的作用。
拨叉通过插Φ25安装在变速轴上,拨叉脚则夹在双联变速齿轮中。
当需要变速的时候,操作变速杆,变速操纵机构就通过拨叉头部的16*8的操纵槽带动拨叉实现滑移,拨叉脚拨动双联齿轮在轴上的位置,来实现变速的。
零件结构分析:
Φ25为拨叉的结合部分,通过该孔与轴相连接。
厚度为8mm的肋板为连接作用,工作部分则为拨叉脚的两个端面。
由于拨叉的工作部分,即拨叉脚的两个端面与结合部分被连接部分所隔开,呈现为细长杆件,在加工过程中容易产生装夹变形,故刚性较差。
1.1.2零件的工艺分析
表1-1拨叉813006加工要素及技术要求表
加工表面
尺寸及公差/mm
精度等级
表面粗糙度Ra/um
行位公差/mm
Φ25mm孔
Φ25
IT7
1.6
拨叉脚两端面
12
IT9
3.2
垂直度要求0.1
操纵槽内侧面
16
IT10
6.3
操纵槽底面
8
IT9
3.2
垂直度要求0.08
Ф55mm孔
Ф55
IT9
3.2
Φ40mm圆周的斜面
35*72
IT9
3.2
分析零件图结合拨叉的功用,拨叉脚两端面在轴的方向均高于相邻表面,这样既减少了加工面积,又提高了换挡时叉脚两端面的接触刚度;叉脚拨叉脚的两个端面因夹在齿轮的槽中,故增加其耐磨性,其表面要求淬火处理,保证拨叉拨叉拨动齿轮齿轮换挡时拨叉脚受力均匀,要求叉脚两端面对Φ25的垂直度要求为0.1mm,所要加工的槽,在其操纵槽两侧面有垂直度公差要求0.08mm。
拨叉的工作表面和Φ25的孔内表面的加工精度要求比较高,但可以在正常的条件下,选择较经济的方法保质保量地加工出来。
其余表面(表中未列出)加工精度比较低,通过一次铣削加工就可以达到要求。
由此可见,该零件的工艺性很好。
1.1.3确定生产类型
依设计题目知:
N=5000件/年。
表1-2不同机械产品的零件质量型别表
机械产品类别
加工零件质量/kg
重型零件
中型零件
轻型零件
电子工业机械
>30
4-30
<4
中、小型机械
>50
15-50
<15
重型机械
>2000
100-2000
<100
根据零件图上,该拨叉的质量为1.12kg,可确定为轻型零件。
再查机械加工零件生产类型的划分表,可知该拨叉的生产类型为中批生产。
1.2确定毛坯类型及尺寸
1.2.1确定毛坯类型
由于该拨叉尺寸较小,但形状尺寸比较复杂,同时,该拨叉在工作过程中,也经常要承受变载荷及冲击性载荷,且它的外型复杂,不易加工。
因此,应该选用铸件以提高劳动生产率,保证精度。
铸件材料为灰铸铁,零件的材料为HT200,灰铸铁生产工艺简单,铸造性能优良,但塑性较差、脆性高。
1.2.2确定毛坯尺寸
1.公差等级
根据铸件毛坯的尺寸公差,同时由拨叉的功用和技术要求,确定该零件的公差等级为普通级。
2.铸件质量
已知该拨叉的经机械加工的质量为1.12kg,机械加工前的质量为2.5kg。
3.毛坯的工艺要求
(1)由于铸造件尺寸精度和表面粗糙度值低,因此零件上有与其它机件配合的表面需要进行机械加工。
(2)为了使金属容易充满膛摸和减少工序,铸造件外形应力求简单、平直,尽量避免铸件截面间差别过大,或具有薄壁、高筋、高台等结构。
(3)铸件的结构中应避免深孔或多孔结构。
(4)铸件的整体结构应力求简单。
4.确定毛坯的形状和尺寸
在确定毛坯时,要考虑经济性。
虽然毛坯的形状尺寸与零件接近,可以减少加工余量,提高材料的利用率,降低加工成本。
同时应该满足以下要求:
各加工面的几何形状应尽量简单,工艺基准以设计基准相一致,便于装夹、加工和检查结构要素统一,尽量使用普通设备和标准刀具进行加工。
确定毛坯尺寸时,应根据铸件的机械加工余量,公差等级以及零件的使用性能的情况下确定毛坯尺寸。
根据以上结果,绘制毛坯简图如图1-2所示。
图1-2拨叉铸造毛坯简图
1.3机械加工工艺路线设计
零件的材料为HT200,灰铸铁生产工艺简单,铸造性能优良,但塑性较差、脆性高,不适合磨削,为此以下是拨叉需要加工的表面以及加工表面之间的位置要求:
1.Ф40圆周上的φ25;
2.拨叉脚孔Ф及其端面;
3.16*8操纵槽;
4.φ40外圆斜面;
5.拨叉脚两端面与φ25中心线的垂直度误差为0.1mm;
槽端面与φ25中心线的垂直度误差为0.08mm。
1.3.1定位基准的选择
定位基准的选择是工艺规程设计中的重要工作之一,定位基准选择的正确与合理,可以使加工质量得到保证,生产率得以提高。
否则,加工工艺过程中会问题百出,更严重的还会造成零件大批量报废,使生产无法正常进行。
1.粗基准的选择
选择粗基准时,考虑的重点是如何保证各加工表面有足够的余量,使不加工表面与加工表面间的尺寸、位置符合图纸要求。
选择粗基准主要是选择第一道机械加工工序的定位基准,以便为后续工序提供精基准。
选择定位粗基准是要能加工出精基准,同时要明确哪一方面的要求是主要的。
粗基准的选择应以下面的几点为原则:
1)应选能加工出精基准的毛坯表面作粗基准。
2)当必须保证加工表面与不加工表面的位置和尺寸时,应选不加工的表面作为粗基准。
3)要保证工件上某重要表面的余量均匀时,则应选择该表面为定位粗基准。
4)当全部表面都需要加工时,应选余量最小的表面作为基准,以保证该表面有足够的加工余量。
5)作为粗基准的表面应平整,没有飞边、毛刺、或其表面缺陷。
该拨叉选择其Φ40圆周面和上端面为粗基准。
采用Φ30圆周外圆定位,可保证内孔加工壁厚比较均匀,采用拨叉Φ40圆周外圆作为粗基准加工下底面,接着以下底面加工Φ40外圆的上端面,可为后序的工序准备好精基准。
2.精基准的选择
1)基准重合原则。
即尽可能选择设计基准作为定位基准。
这样可以避免定位基准与设计基准不重合而引起的基准不重合误差。
2)基准统一原则,应尽可能选用统一的定位基准。
基准的统一有利于保证各表面间的位置精度,避免基准转换所带来的误差,并且各工序所采用的夹具比较统一,从而可减少夹具设计和制造工作。
例如:
轴类零件常用顶针孔作为定位基准。
车削、磨削都以顶针孔定位,这样不但在一次装夹中能加工大多书表面,而且保证了各外圆表面的同轴度及端面与轴心线的垂直度。
3)互为基准的原则。
选择精基准时,有时两个被加工面,可以互为基准反复加工。
例如:
对淬火后的齿轮磨齿,是以齿面为基准磨内孔,再以孔为基准磨齿面,这样能保证齿面余量均匀。
4)自为基准原则。
有些精加工或光整加工工序要求余量小而均匀,可以选择加工表面本身为基准。
例如:
磨削机床导轨面时,是以导轨面找正定位的。
此外,还应选择工件上精度高。
尺寸较大的表面为精基准,以保证定位稳固可靠。
并考虑工件装夹和加工方便、夹具设计简单等。
因此,根据拨叉零件图的技术要求和装配要求,选择拨叉的设计基准是孔Φ25的中心线和拨叉脚的下底面作为精基准,符合“基准重合”的原则;同时,零件上很多表面都可以采用孔Φ25的中心线和拨叉的下底面作为精基准,又遵从了“基准统一”的原则。
孔Φ25的中心线是设计基准,选用它作为精基准定位加工拨叉两端面,有有利于保证拨叉脚的两端面的垂直度的要求。
选用下底面作为精基准同样是服从了“基准重合”的原则,因为拨叉上在轴向方向上的尺寸多以下底面作为设计基准,另外,由于拨叉的刚性比较差,受力易产生变形,以下底面作为精基准,夹紧力可作用在Φ40圆周上端面上,夹紧可靠。
1.3.2制定工艺路线
1.各表面加工方案的确定
根据拨叉零件图上的各加工表面的尺寸精度和表面粗糙度,查外圆加工方案的经济精度和表面粗糙度表和孔加工方案的经济精度和表面粗糙度表,确定了各加工表面的加工方案,如表1