金工实训Word下载.docx
《金工实训Word下载.docx》由会员分享,可在线阅读,更多相关《金工实训Word下载.docx(11页珍藏版)》请在冰豆网上搜索。
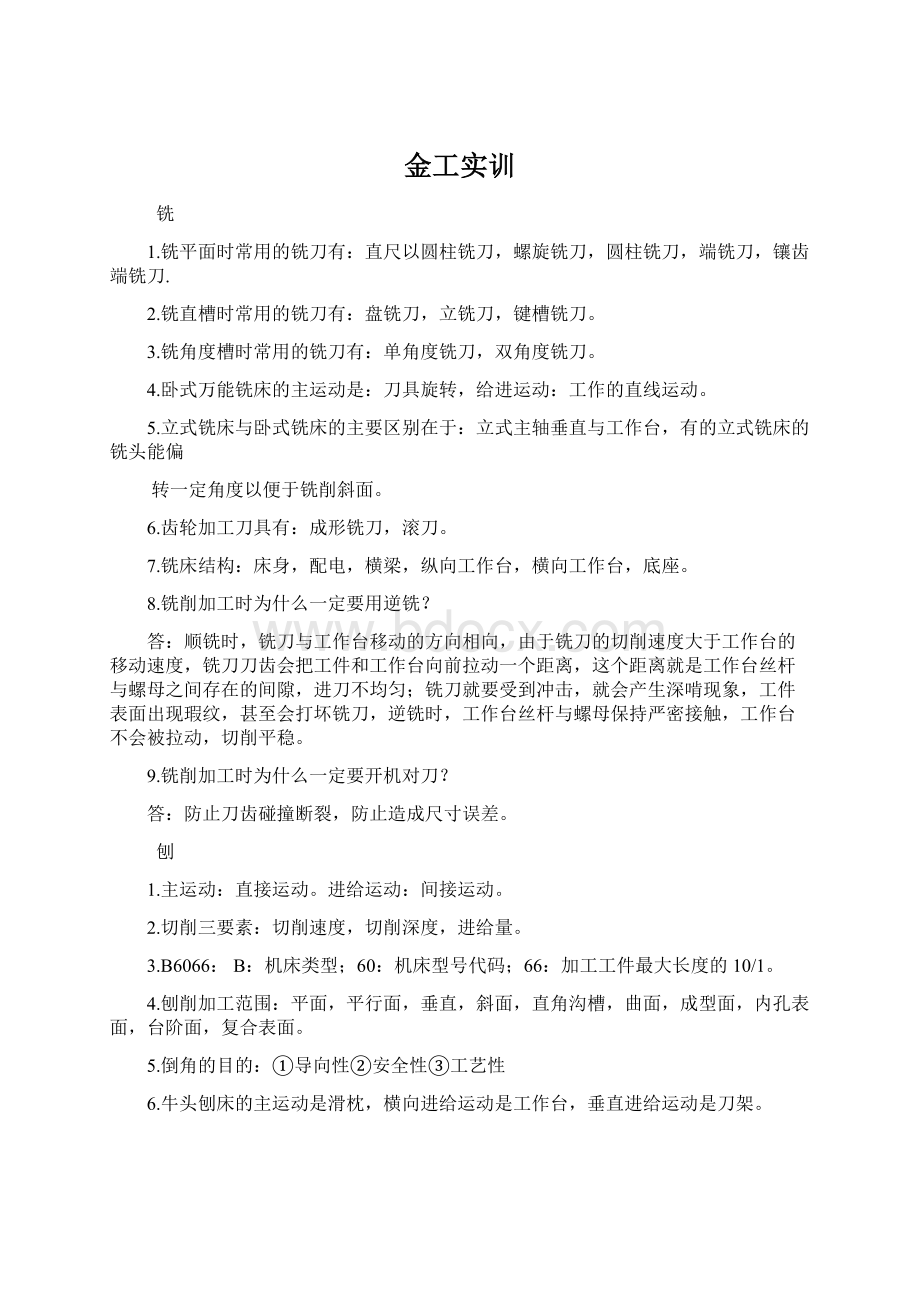
1.主运动:
直接运动。
进给运动:
间接运动。
2.切削三要素:
切削速度,切削深度,进给量。
3.B6066:
B:
机床类型;
60:
机床型号代码;
66:
加工工件最大长度的10/1。
4.刨削加工范围:
平面,平行面,垂直,斜面,直角沟槽,曲面,成型面,内孔表面,台阶面,复合表面。
5.倒角的目的:
①导向性②安全性③工艺性
6.牛头刨床的主运动是滑枕,横向进给运动是工作台,垂直进给运动是刀架。
7.牛头刨床是由曲柄摇杆机构把电动机的旋转运动变为滑枕的往复直线运动。
牛头刨床工作台的间歇进给运动,是由棘轮机构实现的,进给量的大小用调整棘轮的位置来改变,紧急方向靠改变棘爪的方位来实现。
8.刨削的特点:
①可以刨削各种平面、沟槽;
②刨削时,滑枕带动刀具主运动,工作台为横向间歇进给运动;
③刨削时一种断续切削;
④刨床结构简单,调整操作方便,加工精度不高,加工公差等级可达IT7--IT9,表面粗糙度Ra值可达3.2--1.6um。
9.牛头刨床刨削工件前,机床须作哪些方面的调整?
应如何调整?
①工作台的调整;
(顺--上升,反之下降)②滑枕行程长短的调整(顺--伸长,反之缩短)③滑枕起始位置的调整(顺--后退,反之前移)④变速机构的调整(改变把手方位)⑤紧急方向及进给量大小的调整(改变棘轮棘爪方位)⑥刀架的调整(正负15度--正负60度)
10.如何刨削正六面体工件?
装夹工件时应注意些什么?
⑴①一般先刨出大面A作为精基面②将已加工的大面A作为基准面紧贴固定钳口,在活动钳口与工件之间的中部垫一圆棒后夹紧,然后加工相邻的面B③把加工过的面B朝下,按上述方法,使基面A紧贴固定钳口,夹紧时用手锤轻轻敲打工件,使面壁紧贴虎钳,就可以加工面D,同时加工面C,把面A放在平行垫铁上,工件直接夹在两面之间,夹紧时要求用手锤轻轻敲打,使面A与垫贴实⑵注意:
①工件的被加工面必须高出钳口,工作低于钳口,用加平行垫的方法垫高工件②找正平口钳钳口画线找正(或用百分表正找)③精刨时,夹紧工件时,在钳口上垫上铜皮④用手挪动垫铁,检查松紧程度。
磨削
1.砂轮是由磨粒,空隙,结合剂组成。
2.砂轮硬度是指表面磨粒脱落的难易程度,磨削较硬的材料应用软砂轮(白刚玉),磨削较软的材料应选用硬砂轮(SiC)。
3.砂轮在安装前需经过声音及外观的检测和平衡调节,其目的是检查砂轮的外观是否完好,防止砂轮高速旋转时产生破裂。
4.磨削外圆时工件作圆周运动及纵向往复运动,砂轮作高速旋转运动及横向运动。
5.砂轮:
多刀多刃,周圆线速度35m/s,高速问50m/s。
6.砂轮切削作用:
刻划作用,抛光作用。
7.砂轮:
白刚玉,棕刚玉,SiC,人造金刚石。
8.评判砂轮的指标:
1,粒度:
砂轮颗粒粗细程度;
2,硬度。
9.磨削加工有哪些特点?
为什么会有这些特点?
①磨削软材料②加工硬材料③可以降低工作的表面粗糙度④可以获得高精度IT5--IT6⑤磨削量小,效率低
10.冷却液的作用是什么?
①冷却降温②润滑③冲洗④防锈。
11.平行砂轮——磨外圆,内圆,平面。
双面凹——外圆,无心磨。
12.标志含义:
GB46ZR,A。
GB——磨粒,46——粒度,ZP——硬度,A——结合剂。
P40X50X203。
P——平行砂轮,400——外径50宽度,203——孔径。
平面磨削分为周磨法和端磨法。
锻压
1.始锻温度一般应低于该金属材料熔点的100--200度。
2.锻造前加热的目的是为了提高金属的塑性和降低变形抗力。
3.机器自由锻所用的设备通常有空气锤,蒸气--空气锤和水压机等,板料冲压所用的设备有剪床,冲床。
4.自由锻造的基本工序有镦粗,拔长,冲孔,弯曲,切割,扭转,错移等。
5.加热锻件时,若出现过烧现象,正确的处理方法是报废。
6.坯料加热时,常产生的主要缺陷有:
氧化,脱碳,过热,过烧,开裂。
7.自由锻造有哪些优缺点?
优点:
工艺灵活,设备工具简单,通用性较大,投资少,故广泛用于单件,小批量及大
型锻件。
缺点:
精度不高,形状不能复杂,尺寸难于精确,对锻工技术要求高,劳动强度大,生
产效率低。
8.锻造的工艺包括哪些内容,常用的锻造方法有哪些?
工艺:
下料,坯料加热,锻造成形,检验,冷却。
方法:
自由锻造,模型锻造。
9.什么事始锻温度和终锻温度?
低碳钢和中碳钢的始锻温度和终锻温度各是多少?
金属材料锻造分析的最高加热温度为该材料的始锻温度,停止锻造的温度称为该材料的
终锻温度。
低碳钢的始锻温度为1200--1500度,终锻温度为800度。
中碳钢的始锻温度为1150--1200度,始锻温度为800度。
热处理
1.淬火、回火的目的?
①提高钢的强度,增加耐磨性。
②减小或消除工件在淬火时产生的内应力,降低淬火钢的脆性,以获得较好的强度,韧性,弹性等综合力学性质。
2.何为退火?
退火是将金属或合金加热到适当温度,保温一定时间,然后缓慢冷却的热处理工艺。
3.表面淬火可分哪两种?
火焰加热表面淬火和感应加热,表面淬火。
4.实习中工具钢(锯条)淬火的工艺如何?
将工具钢加热到760--800度,保温一段时间,快速水冷,然后测试。
5.硬度不统一,通过正火后,硬度相同。
6.热处理的三要素:
加热,保温,冷却。
铸造
1.型砂应当具备的性能是强度,透气性,可塑性,退让性,耐火性。
2.常用的手工型砂铸造方法有塑模造型,分模造型,挖砂造型,活块造型,假箱造型等。
3.典型的浇铸系统是由外浇道,直浇道,内浇道,横浇道等四部分组成的。
4.砂型铸造生产的工艺流程是:
(芯盒)—(芯砂)—(造芯)—(型芯)
—刷涂料烘干—合箱—浇注—落砂清理—检验—铸件
(模型)—(型砂)—(造型)—(型砂)
5.铸型一般由上砂型,下砂型,型芯,排气孔,型腔,浇注系统,分型面等几部分组成。
6.直浇道的作用:
引导金属液进入横浇道。
7.分型面应选择在零件的最大截面处。
7.如铸件壁厚不均匀,其内浇道应开设在壁厚处。
8.分型面的确定:
⑴分型面一般选在铸件的最大截面处⑵应尽量减少分型面的数量⑶应尽量选取平直的分型面⑷应尽量使铸件上的重要加工面或大部分加工面及进准面置于同一砂箱中。
9.造型时为何要舂砂?
使砂型具有一定强度,在搬运,起模,浇注时不致损坏,更重要的是使砂型能够承受金属液的压力的冲击,不致变形和损坏。
10.造型中,开设内浇道时应注意哪些问题?
⑴内浇道开设不要正对型芯或型砂薄弱的部分⑵内浇道不要开的过深过宽⑶内浇道的数量不要太多⑷内浇道不要开在横浇道的尽头⑸内浇道要清理的光滑平整。
11.简述整模造型,分模造型,挖砂造型?
⑴整模造型:
特点是模样截面由大到小递减,零件的最大截面在端部,并选定作分型面,将模样做成整体置于一个砂箱内当型腔。
一般在下箱模中可以一次由沙型中取出的造型过程。
⑵分模造型:
分模造型的特点是当零件截面中间小两端大时,将模样的最大截面作为分型面,并把模样分开以便于造型时顺利起模,分模造型适合旋转类铸件。
⑶挖砂造型:
当模样无法分开而只能制成整型,而分型面又是曲面时,在造型过程中,部分型砂会阻碍模样的取出,此时,必须使这部分覆盖在模样上的型砂挖去,才能顺利取模,这种造型方法成挖砂造型,挖砂造型生产率低,操作技术要求高,故只适合于单间小难生产,形状复杂的小铸件。
焊接
1.焊接常见的缺陷有:
未焊头,气口,咬边,加渣,裂纹,变形。
2.手工电弧焊引弧有两种方法,即划擦法和敲击法。
3.怎样选择焊条直径和焊接电流?
焊接电流为什么不能过大或过小?
①根据工件厚度决定焊条直径,厚度大于4mm的工件可用4mm以上的焊条,厚度小于4mm的工件可用4mm以下的焊条。
②根据焊条直径决定电池大小,I=(30~60)d(A),还需根据具体情况灵活调节电流,电流过大,易造成焊穿,咬边电流过小易造成未焊透。
4.简述电焊条组成部分及其作用。
⑴焊芯和药皮⑵焊芯的作用:
①作为电极产生电弧②作为填充金属和工件一起形成焊缝。
药皮的作用:
①使电弧容易引燃,并保持电弧燃烧的稳定性②在高温的作用下,产生一定气体的形成熔渣,以保护融化的金属不被氧化;
同时添加有益的合金元素,改善焊缝质量。
5.能用氧割的金属材料必须符合以下条件:
①金属材料的燃点必须低于其熔点②金属燃烧所生成的氧化物的熔点应低于金属本身的熔点,并且流动性要好③金属材料的导热性要低。
6.接头形式:
对接,角接,T形接,搭接。
7.焊缝位置:
平焊,横焊,立焊,仰焊。
8.坡口形式:
I,V,K,X,U形坡口。
钳工
1.划线工具有划线平台,V形铁,高度游标尺,角尺,千斤顶,方箱,划针,样冲等。
2.锯条按齿距大小分粗齿,中齿,细齿。
3.手工起锯的适宜角度为15度。
4.锯条安装时松紧要适当,太紧时,锯条容易折断,太松时锯条容易扭曲,也可能断折,而且锯出的锯缝易发生歪斜。
5.锉削时的速度一般为每分钟30--60次左右,速度太快容易疲劳和加快锉齿的磨损。
6.锉刀的种类很多,按齿纹分有单齿纹和双齿纹两种。
按锉刀齿纹的齿距大小一般分为粗锉刀,中锉刀,细锉刀。
普通锉刀按其断面形状的不同又分为平锉,方锉,半圆锉,圆锉,三角锉五种。
7.如何选择划线基准?
一般以选择重要孔的中心线或已加工面为划线基准。
8.打孔就是扩大已加工出得孔。
(对)
9.一毛坯上所划的线在加工中作为参考尺寸。
10.手用锯条目前的长度为300mm,宽度为12mm,厚度为0.8mm。
11.锯齿崩落和锯条折断的原因是什么?
①锯条安装得过紧②锯条安装得过松③强行纠正,压力过大④速度过快,产生高温。
车削
1.切削用量(车削用量)三要素是切削速度(米/分),进给量(毫米/转),切削深度(毫米)。
2.车削加工时,工件的旋转是主运动,车刀的纵向(或横向)运动是进给运动。
3.车削加工时,如需更换主轴的转速,应当遵循的原则是:
先停机,再换挡。
4.车削锥角大且长度较短的锥面时应采用宽刀法,而车削锥角小而长度大的锥面时可采用偏移尾架法。
5.车外圆时,带动溜板箱做前进运动的是光杆运动,而车螺纹是,带动溜板箱做纵向移动的是丝杆运动。
6.C6132E的含义是C车床,6普通车床组,1普通车床型,32工作最大直径的0.1,E第五次改进。
7.主轴转速是否就是切削速度?
当主轴转速提高时,刀架移动速度加快,这是否意味着进给量的加大?
不是切削速度。
当主轴转速提高时,刀架移动速度加快,但此时,刀具仍保持着卡盘转一周,走一个进给量,并不意味着进给量加大。
8.用中拖板进刀时,如果刻度盘的刻度多转了4格,可否直接退回4格?
为什么?
当作何处理?
不能直接退回4格。
因为中拖板手柄丝杆和螺母间的间隙会影响进刀的准确,往往回退直到消除间隙,重新进刀。
9.在车床切削加工过程中,车床所使用的刀具材料应具备哪些特征?
①高硬度②耐磨性③耐热性④强度韧性⑤公益性
10.在一般情况下,车床上的加工范围有哪些?
钻中心孔,钻孔,铰孔,攻螺纹,车外圆,镗孔,车端面,切槽,车成型面,车锥面,滚花,车螺纹等。
数控车削
1.数控机床主要由控制介质,数控装置,伺服系统和机床本体组成。
2.数控车床按伺服系统的控制方式不同可分为开环,半闭环和闭环控制系统等三种类型。
3.数控机床标准坐标系采用笛卡尔直角坐标系,规定空间直角坐标系X,Y,Z三者的关系及其方向关系用右手定则判断。
4.直线插补指令G01的特点是刀具以直线进给的方式由某坐标移到另一坐标点,由指令F设定进给进度。
5.G01X500Z100F40表示以F=40的进给速度移动至X500Z100处。
6.若输入程序段为G02X40Y70F40,则不运动。
7.G92X0Y0Z10,表示刀位点在共建坐标系中坐标值是X0,Y0,Z10.
8.数控车床上,刀尖圆弧只有在加工圆弧时,才产生加工误差。
9.检查刀架实际位移的系统为闭环系统。
10.数控车床的加工特点。
数控车床具有加工灵活,通用性强且能适应产品的品种和规格频繁变化的特点,能满足新产品的研发和多品种小批量生产自动化的要求。
11.常用的编程坐标系有哪几种?
数控车床的坐标系是如何规定的?
①常用的编程坐标系由G54--G59等G代码选择②数控车床一般为两轴坐标系,主轴轴线方向为Z轴方向,刀具远离工件的方向为Z轴方向,X轴的轴线方向为垂直Z轴的水平方向,对应于转塔刀架的径向移动,刀具远离工件旋转中心的方向为X轴的正方向。
数控铣削
1.数控机床按运动轨迹分类的三种数控系统是点位控制,点位直线控制,轮廓控制。
2.工作原点的主要选择原则:
一是保证加工精度,二是尺寸计算方便。
3.自动编程软件一般由CAD和CAM两部分组成。
4.数控铣床默认的加工平面是X,Y。
5.数控铣床半径补正值就是刀具的实际半径。
6.数控铣床在自动加工过程中,进给倍率归零后,机床处在暂停状态。
(错)
7.数控机床的主轴调速技术一般采用的是PLC技术。
8.数控机床编程研究的是工作台的运动轨迹。
9.多品中国小批量加工和单件加工选用数控设备最合适。
10.数控机床送电后,为什么要首先做一次手动参考点复归?
因为机床断电后,所有的坐标轴都会位置丢失,所以要做一次手动参考点位置复位,找回已丢失的坐标,使机床重新建立正确的坐标系。
11.简述加工中心的组成。
①基础部分:
基础部分是加工中心机床的基础,它主要由床身,工作台,立柱三大部分组成(一般材料为铸铁)②主轴部分:
主轴部分由主轴箱,主轴电机,主轴等零部件组成。
主轴是加工中心,切削加工的工艺输出部件,它的启动,停止,变速,换向等都由数控系统控制,主轴的旋转精度和定位精度是影响加工精度的重要参数③数控部分:
数控系统由CNC23装置,可编程控制器,伺服驱动系统等组成④自动换刀装置⑤辅助系统:
润滑,冷却,排屑,气动等。
数控线切割
1.电火花线切割加工时,在电极丝和工件之间进行脉冲放电。
2.电火花线切割机床按走丝速度可分为快走丝,慢走丝。
3.电火花线切割编程的方法分手工编程,自动编程。
4.电极丝和工件之间产生的是电弧放电。
5.电火花线切割可以加工一定锥度的通孔。
6.简述电火花加工的原理。
电火花加工又称放电加工,是一种利用电热能进行加工的方法,它在加工过程中是工具与工件之间不断产生耐冲性的火花放电时局部瞬间产生的高温将金属蚀除下来,对工件进行加工的一种方法。