压缩机测量技术及其自动控制系统.docx
《压缩机测量技术及其自动控制系统.docx》由会员分享,可在线阅读,更多相关《压缩机测量技术及其自动控制系统.docx(42页珍藏版)》请在冰豆网上搜索。
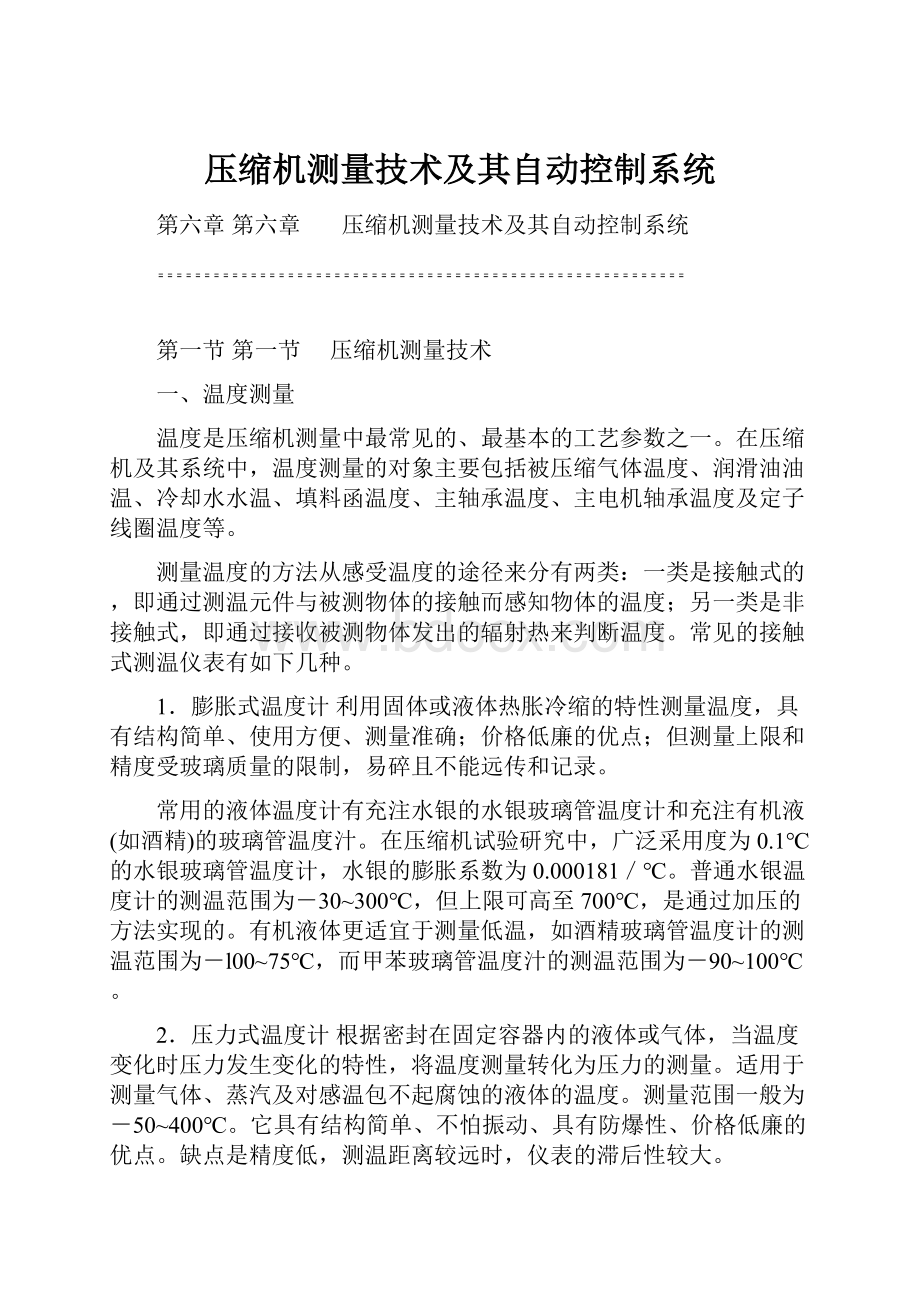
压缩机测量技术及其自动控制系统
第六章第六章 压缩机测量技术及其自动控制系统
第一节第一节 压缩机测量技术
一、温度测量
温度是压缩机测量中最常见的、最基本的工艺参数之一。
在压缩机及其系统中,温度测量的对象主要包括被压缩气体温度、润滑油油温、冷却水水温、填料函温度、主轴承温度、主电机轴承温度及定子线圈温度等。
测量温度的方法从感受温度的途径来分有两类:
一类是接触式的,即通过测温元件与被测物体的接触而感知物体的温度;另一类是非接触式,即通过接收被测物体发出的辐射热来判断温度。
常见的接触式测温仪表有如下几种。
1.膨胀式温度计利用固体或液体热胀冷缩的特性测量温度,具有结构简单、使用方便、测量准确;价格低廉的优点;但测量上限和精度受玻璃质量的限制,易碎且不能远传和记录。
常用的液体温度计有充注水银的水银玻璃管温度计和充注有机液(如酒精)的玻璃管温度汁。
在压缩机试验研究中,广泛采用度为0.1℃的水银玻璃管温度计,水银的膨胀系数为0.000181/℃。
普通水银温度计的测温范围为-30~300℃,但上限可高至700℃,是通过加压的方法实现的。
有机液体更适宜于测量低温,如酒精玻璃管温度计的测温范围为-l00~75℃,而甲苯玻璃管温度汁的测温范围为-90~100℃。
2.压力式温度计根据密封在固定容器内的液体或气体,当温度变化时压力发生变化的特性,将温度测量转化为压力的测量。
适用于测量气体、蒸汽及对感温包不起腐蚀的液体的温度。
测量范围一般为-50~400℃。
它具有结构简单、不怕振动、具有防爆性、价格低廉的优点。
缺点是精度低,测温距离较远时,仪表的滞后性较大。
3.电阻式温度计根据金属或半导体的电阻值随着温度变化的特性测量温度。
一般金属电阻值随着温度升高而增加,而半导体的电阻值却随着温度的升高而减少。
目前使用最广泛的热电阻材料是铂和铜。
热电阻温度计适用于测量液体、气体、蒸汽及固体表面的温度。
铂电阻温度计测温范围为-200~500℃。
铜电阻温度计测温范围为-50~150℃。
热电阻温度计具有远传、自动记录和实现多点测量等优点,而且它输出的信号大,测量准确。
1968年的新温标进一步规定,在-259.34~630.74℃温度范围内,以铂电阻温度计作为基准器。
4,热电偶温度计根据热电效应,将两种不同的导体接触并构成回路时,若两个接点温度不同,回路中便出现毫伏级的热电势,该电势就可准确反映被测物体的温度。
将回路与适当的指示仪表结合,就组成了如图6-1所示的热电偶温度计。
热电偶的测温范围为-100~1600℃,上下限根据需要还可以扩展。
热电偶具有结构简单、价廉、测温范围宽、准确度高、热惯性小、输出信号为电信号便于远传等优点。
适合于测量流体、固体及固体壁面的温度。
微型热电偶还可用于快速及动态温度的测量。
在单元组合式仪表中,将温度传感器输出的信号转变为标准信号(如4~20mA直流电流信号)的变换装置,称为温度变送器(如图6-2)。
二、压力测量
压力是压缩机设计中的重要工艺参数。
不但压力本身是表征流体流动过程的重要参数,而且流速、流量等参数的测量,也往往转换为压力测量问题。
在压缩机及其系统中,压力测量的对象主要包括被压缩气体压力、润滑油油压、冷却水水压、填料函及中体充氮压力、仪表风压力等。
根据工作原理,目前所采用的压力指示仪器主要有液柱式、弹性式、活塞式、电气式或电子式等。
(1)液柱式压力计它是根据流体静力平衡的原理制成的,有单管压力计和双管压力计(u形管压力计),具有结构简单、精度高、使用方便价格低的特点。
u形管压力计测量压差的范围很广,其测量上限取决于工作液体的密度,但受管子的强度限制,都有一个最高压力限度:
下限由测量精度要求决定,不应小于2000Pa。
微压计用来测量很小的压差,如20~5000Pa,是一种灵敏、精度高的测压仪器。
(2)弹性式压力计它是用各种形式的弹性元件作为感受件,使弹性元件受压后发生的反作用力与被测压力平衡。
此时,弹性元件的变形就是被测用力的函数,通过测量变形的方法测得压力。
根据测压范围不同,常用的有膜片(分平膜片与波纹膜片)、膜盒(分单膜盒与双膜盒)、波纹臂(分单波纹管与双波纹管)、弹簧管(分单圈弹簧管与多圈弹簧管)。
膜片、膜盒与波纹管等元件多用于微压和低压的测量;弹簧管则可用于高、中、低压直到真空度的测量。
多圈弹簧管压力计最高压力为16MPa。
(3)活塞式压力计它是以直接作用在已知面积上的重力来平衡被测压力的。
常被作为实验室的压力标准器,精度高。
简单活塞式压力计的测量上限为6×l07Pa,具有差动活塞的压力计上限可达25×107Pa。
压力变送器是将弹性元件受压输出的位移或力等信号。
变成标准电信号的变换装置。
在压缩机测量中,常用的压力测量仪表有以下几类:
1)霍尔片式远传压力表,其原理是通过压力—弹簧管位移—霍尔电势的产生,实现压力信号的远传或显示。
适用于静态压力测量。
2)应变片式远传压力表。
通过应变片将被测压力转换成电阻值的变化,远传至桥式电路,获得相应的毫伏级电量输出信号,然后在毫伏计或记录仪上显示。
适用于测量快速变化的压力和高压力。
3)电容式远传压力表。
采用变电容原理,用弹性元件受压变形来改变可变电容器的电容量,用测量电容的方法测出电容量,便可知被测压力大小,从而实现压力-电容转换。
适用于测量快速变化的压力和高压力。
4)差动式电感压力传感器。
由弹簧管和差动式电感转换器组成差动式电感转换器,由公共衔铁和两个相同的简单电感转换器结合在一起构成,通过变化引起电感量变化,引起电流变化,引起或输出电压变化,可知被测压力的大小。
适用于静态压力测量。
三、流量测量
流量是压缩机的主要性能参数之一,它表征了机组在甲位时间内生产压缩气体量的多少。
流量可以采用质量流量(kg/s)表示;也可以用体积流量(m3/s)表示。
工程上常用m3(标)/min表示往复压缩机的容积流量。
流量测量方法分为直接测量和间接测量两种。
直接测量就是同时测出流体质量(或体积)和所用时间。
间接测量主要是测出与流量有关的物理量(如压差),再换算成流量。
工程上除了小流量有时用直接测量外,大多用间接测量方法。
间接测量常用的以下一些方法。
1、差压式流量计利用流体流经节流装置时产生的压力差来实现流量测量。
通常是由能将被测流体的流量转换成压差信号的节流装置,和能将此压差转换成对应的流量值显示出来的差压流量计所组成。
可用于测量液体、气体和蒸汽的流量。
目前国内外节流装置的型式已标准化,称为标准节流装置:
标准节流装置的结构型式、尺寸要求、取压方式、使用条件等均有统一规定。
在管道通路上安装孔板、喷嘴或文丘利管等节流装置。
当流体流过节流元件时,流束局部收缩。
其流速增加,静压降低,使节流元件前后产生静压差。
静压差△p与体积流量qv(m3/s)之间有如下关系:
(6-1)
式中,α为流量系数,与节流元件的形式、孔口对管道的面积比及取压方式等因素有关;ρ为流体密度(kg/m3);A0为节流孔流通面积(m2);p1,p2为节流孔前后的绝对压力(pa)。
同理,质量流量qm(kg/s)为
(6-2)
因此测出节流元件前后的静压差,就可间接确定流体流量。
上式也说明,可使用差压变送器测量节流元件前后的压差,由此换算成流量。
差压流量计原理如图6-3所示。
2、转子流量计在小流量测量中,广泛使用转子量计。
其工作原理是根据节流现象,节流元件是一个能上下浮动的可以转动的转子,置于圆锥形测量管中。
当被测流体自下而上通过时,由于转子的节流作用,在转子前后出现压差△p。
此压差对转子产生一个向上的推力,使转子向上移动,由于测量管上口较大,因而能取得平衡位置。
平衡时,△p等于转子重量,为恒值,可以由式(38—1)得到流量值。
指示型转子流量计的工作压力不得超过2.0MPa,工作温度范围为-20~120℃。
3、涡轮流量计其结构如图6-4所示。
涡轮的轴装在导管的中心线上,流体横向流过涡轮时,推动叶片,使涡轮转动,其转速近似正比于流量。
涡轮流量计具有测量精度高、反应快、耐压高、适应范围广的特点,但不适于测量脏污介质的流量。
涡轮流量计可用于测量压缩机冷却水消耗量。
精度一般为0.25%~1.0%。
四、液位测量
压缩机组中需要测量的液位有主油箱润滑油液位、注油器油箱液位、中间分液罐凝液液位及填料漏气收集罐液位。
1、玻璃液位计这是使用最早、结构最简单的一种直读式液位计。
它的一端接容器的气相,另一端接液相,根据连通器的原理工作,有玻璃管和玻璃板两种形式,如图6-5所示。
对于低压罐体(如油箱),可以采用透明材质镶嵌在容器上,以随时观测罐体内液位。
对于大的承压罐体(如中间分液罐),可利用连通器原理,在容器上引两嘴子接到一透明管两端,该管液位就反映了承压容器内液位的高低(如彩色玻璃板液位计)。
工业上应用的玻璃管液位计的长度为300~1200mm,工作压力不大于1.6MPa。
玻璃板液位计的长度为500~1700mm,最大耐压为5.0MPa,耐温400℃。
2、浮力式液位计分为恒浮力式液位计和变浮力式液位计两种形式,主要利用感测元件在液体中的浮力测量液位。
主要用于低压力场合的液位测量。
3、差压式液位计它是利用容器内的液位改变时,由液柱产生的静压也相应变化的原理而工作的。
各种压力计、差压计和差压变送器都可以用来测量液位高度。
液位变送器和液位开关可以对液位信号进行远传,它是利用传感器将液位信号转换成电压或电流信号。
五、转速测量
转速是压缩机的一个重要特性参数。
测定活塞式压缩机的排气量时,若实际转速与设计转速不同时,须按照转速比修正。
往复压缩机在运行过程中,转速直接影响着机组的机械强度、振动及零部件的磨损情况。
转速是指单位时间内被测轴旋转的圈数,以每分钟的转数(r/min)表示。
按照测量工作原理,转速测量仪表大致可分为模拟式、计数式和闪频式等。
1、模拟式转速计它是利用与瞬时转速成比例的物理现象。
例如离心力、发电机输出电压等的变化,以转速单位连续指示在刻度盘上,故也称瞬时式转速计,这类转速计精度较差(约1%~2%),有较大的温度误差,但结构简单,使用方便。
此类转速计有离心式转速表、感应式转速计、发电机式转速表等。
可以测量低、中、高速。
2、计数式转速计它是用某种方法数出一定时间内的总转数,测量内容包括计数和测时。
计数式是转速测量的一种主要方式,测量精度高,测量转速范围为30r/min至48万r/min。
其测量方法有机械式和数字电子式。
数字电子式是利用传感器将转速值变成电脉冲信号,然后用数字频率计显示出转速值。
转速传感器通常有光电式和磁电式两类。
投射式光电传感器是由装在旋转轴上的开孔圆盘、光源及光敏元件组成,开孔元件旋转一周,光敏元件感光的次数与圆盘的孔数相同,从而产生相应数量的电脉冲信号,磁电式传感器是利用旋转着的齿盘与磁极之间气隙磁阻中感应出电势的原理制成。
3.闪频测速法它是基于已知频率的闪光与被测轴转速的关系,用闪光照射以转速n旋转的圆盘,若以同一时间单位度量,当闪光的频率f和转速n相同,或转速n比闪光频率大,且n/f=m,m为正整数时,则圆盘上的p点看上去是静止的。
一般在f=mn(m=1、2、3、…)时,看上去p点静止于一点、二点、三点、……。
利用这种机械转速与闪光频率的关系测量转速的方法,称为闪频测速法。
闪频测速法测量精度一般为±1%~2%,为非接触式测速法。
六、功率测量
测量压缩机的功率一般采用以下方法:
1)用测得的指示功乘以转速,再除以机械效率。
2)用测量转矩和转速的方法,直接测定压缩机轴功率。
3)当为电动机驱动压缩机时,测量电动机的输入功率(用两瓦计法得到),乘以电动机效率、传动效率等,便可得到压缩机的轴功率。
4)对透平压缩机可采用热平衡方法间接确定其功率。
5)当为内燃机驱动压缩机时,可通过测量内燃机油耗获得。
转矩可以通过扭力架测功法或扭力测功法来测量。
转矩测量仪由转矩传感器和数字显示仪表组成。
转矩传感器是利用转轴受扭后产生的弹性变形来测量转矩的大小。
对于大型往复压缩机,一般在高电压回路中测量电压和电流来测量压缩机轴功率。
七、振动测量
振动测量的目的在于测试压缩机装置的运转是否平稳,分析和解决与振动有关的故障等。
各类型压缩机在出厂前的机械试运转及在现场安装之后的试车阶段,都必须对机械的振动量进行检验。
描述振动的三个主要参量是振幅、频率和相位。
振动测量有两种:
一种是测量随时间变化的位移、速度和加速度直线振动值及其频率;另一种是测量随时间变化的角度、角速度和角加速度的扭转振动值及其频率。
(1)振动测量的方法常用的方法有机械测量、电测量、光学测量等。
振动电测量是将振动运动量变为与之成正比的电量或其他便于观察、显示或处理的物理信号,然后经过适当放大,由记录装置和显示器显示出来。
电测振动传感器有电动式、电感式、电阻式和压电晶体式。
电动式传感器的主要部分是永久磁铁,磁路和运动线圈,磁路内留有气隙,运动线圈在磁路内的空气隙中。
当测量振动时,线圈跟随振动体运动,并在固定磁场里切割磁力线,结果在线圈两端就产生感应电动势,此输出电压与相对运动速度成正比。
其基本环节如下图6-6所示。
图6-6振动测量的基本环节
压电式传感器的原理是将传感器基座固定在被测振动体上,压电元件受到惯性质量块惯性力作用而变形,在两导电极面上,由于压电效应而产生电荷,此传感器的输出电量瞬时值与感受到的机械振动加速度成正比。
该型传感器是利用某些晶体在承受压力(或拉力)时,其表面产生电荷的性质来进行工作的,这种现象称为压电效应。
石英、酒石酸钾钠、碳酸钡及锆钛酸铅等材料具有压电效应。
(2)机器振动故障诊断机器在其传递能量和完成工作的过程中,会产生激发机器或结构中个别零件振动的力。
处于力传递途径中的某些零件,可以很容易的从外部接近。
由此可以很方便地测量由激振力引起的振动。
只要工作过程保持不变或仅在一定限度内变化,则所测量的振动实际上是不变的。
对大多数机器来说,在正常工作条件下,振动频谱有一定特征形状。
当机器中开始出现故障时,机器的某些动态过程发生改变,作用在零件上的力,或零件本身的力学特性也发生变化,导致振动频谱改变。
这就是利用振动信号测量分析和进行机器故障诊断的基础。
八、噪声测量
压缩机的噪声性能也是一项重要指标。
压缩机噪声主要是由空气动力性噪声和机械噪声所组成。
空气动力性噪声是由气体振动而产生的,是压缩机噪声的主要来源。
机械噪声是固体振动产生的。
噪声是由不同频率的各种声音组成的。
表征噪声的基本物理量有声压、声功率和声强。
在噪声研究中,还采用声压级、声强级和声功率级的概念。
声压一般把没有声波存在时的大气压力称为静压力。
有声波存在时,空气压力就在大气压附近发生起伏变化。
此起伏变化量就是某瞬时的瞬时声压,单位用Pa表示。
把瞬时声压的有效值(即瞬时声压的均方根值)定义为声压。
声强它是指在垂直于声波传播方向上,单位时间内通过单位面积的声能,单位为W/m2。
声强与声压关系为
(6-3)
式中,I为声强(w/m2);p为声压(N/m2);ρ为介质密度(kg/m3);c为介质声速(m/s)。
声功率是声源在单位时间内辐射出来的总声能,单位为瓦,表示为
(6-4)
式中,W为声功率,(W);In为声强在基元面积ds法线上的分量,(W/m2);S为包围声源的封闭面积,(m2)。
噪声测量主要是声压级测量。
通常将声压传感器信号转换成电信号放大显示。
常用的有声级计、频谱分析仪器和声级记录仪等。
所谓声音就是物体的振动,在弹性介质中以疏密波的形式进行传播的过程。
因此对噪声的测量,也可采用类似振动测量的方法进行,测声传感器有电容式传声器、压电式传声器和电动式传声器等。
它们的共同点是采用金属弹性振膜来感受声波而产生相应的位移。
电容式传声器是在振膜背后有一极板与振膜构成电容,振膜的位移导致电容的变化。
压电式传声器原理是由振膜的位移,导致压电晶体产生应变,从而因压电效应产生电压输出。
电动式传声器是由振膜拖动—个线圈在固定磁场中往复运动,使线圈产生电压输出。
第二节压缩机自动控制系统
一、自动控制原理
现代化生产装备都是自动化的。
它由各种检测、控制器件及数字计算机等,按照一定规律组成控制系统,对设备和生产过程进行自动控制。
自动控制是指在没有人直接参与的情况下,利用控制系统或自动化仪表,使被控对象或生产过程自动地按照预定的规律工作。
自动控制技术的应用,可以实现生产过程自动化,从而确保设备安全运行,改善劳动条件,提高劳动效率,创造更多经济价值。
压缩机系统是为完成某种工艺任务,提高气体压力而采用的一套机器设备。
在完成其指定的工艺过程任务中,需要对有关参数进行调节和控制,以保证装置正常工作,并满足根据各项要求拟定的工艺指标。
自动地实现这种调节和控制是压缩机自动化的任务。
(一)、概述
一般的自动控制也称为自动调节。
自动调节是使生产过程中的某些被调参数保持恒定,或者按照一定规律变化的一种自动控制过程。
在研究自动控制系统时,通常以方框图来描述系统内各组成部分(环节)间的相互影响和信号传递的关系,如图6-7所示。
图中每个方框表示一个具体的作用环节,每个环节都有输入信号和输出信号。
方框间的连线和箭头表示环节间的信号联系和信号传递方向。
图6-7自动控制系统方框图
自动调节系统是由调节对象、发信器、调节器和执行器这四个基本环节组成的。
有时,又把发信器、调节器和执行器合起来叫做调节装置,因此自动调节系统由调节装置和调节对象两部分组成。
被调参数是调节对象中的某个受控工艺参数,发信器检测被调参数的变化,并与给定值比较,向调节器输入偏差信号;调节器根据偏差信号按照一定的调节规律传递调节指令;执行器按调节指令完成调节动作,作用于调节对象。
在方框图中,被调参数是调节对象的输出信号。
凡是引起被调参数波动的外来因素(除了调节作用外)统称为干扰作用。
干扰作用和调节作用对被调参数影响的信号传递通道,分别称为干扰通道和调节通道。
从信号传递的角度说,自动调节系统是个闭合回路,故称为闭环系统。
另外,系统的输出是被调参,但它经过发信器后又返回到调节器的输入端。
这种把系统的输出信号又引到系统输入端的作法叫做反馈,若反馈信号使被调参数的变化减小,称为负反馈,反之称为正反馈。
按被调参数给定值的变化规律,自动调节系统分类如下:
1)定值调节系统。
给定值为某一确定的数值。
2)程序调节系统。
给定值按指定的规律变化。
3)随动调节系统。
给定值事先不能确定,随机变化。
按照实现调节动作的特征可以分为:
1)连续调节系统。
系统所有参数在调节过程中连续变化。
2)断续调节系统。
在调节过程中系统中有一个以上的断续变量。
按照调节规律可分为:
双位调节、三位调节、比例调节、比例积分调节、比例微分调节和比例积分微分调节。
(二)、自动调节系统的调节品质
原来处于稳定平衡态的自动调节系统,当对象受到干扰时,被调参数开始变化,但通过调节作用,可以克服干扰,使系统在一个新的平衡态重新稳定下来,系统的稳定态称为“静态”。
从干扰发生、经历调节再到新的平衡这段过程中,系统的各环节和各参数在不断变化,这种状态称为“动态”。
被调参数在动态过程中随时间的变化叫做过渡过程。
通过对过渡过程的特性分析,可以获得调节系统的调节品质。
一般来说,对象受阶跃干扰后,系统的过渡过程有图6-8所示的四种基本类型:
1)增幅振荡。
被调参数越来越偏离给定值,系统不能稳定。
这种调节系统无法实现调节,在自动调节系统中是不允许的。
2)等幅振荡。
被调参数呈既不发散、也不衰减的等幅振荡。
它也是不稳定过程,在双位调节中就呈现这样的过程。
但在连续调节系统中是不允许的。
3)单调过程。
被调参数偏离给定值后,逐渐地趋近给定值。
它属于非周期调节,系统能够回到稳定。
在自动调节系统中是允许的,但调节时间较长,并不理想。
4)衰减振荡。
被调参数偏离给定值后,经过两、三个周期的振荡能够很快趋于平衡值。
这种过渡过程比较理想。
在连续调节过程中希望得到它。
对照衰减振荡的过渡过程曲线图6-9,可以得到调节系统的下述品质指标:
1)衰减比。
衰减比是反映被调参数振荡衰减程度的指标。
它等于前后两个波峰之比,即
n=M/M'(6-5)
用n判断振荡是否衰减和衰减程度。
n>1时,系统稳定;n=1时,等幅振荡;n<1时,增幅振荡。
通常希望n=4~10为宜,表明调节作用能够很快克服干扰,将被调参数的波动恢复到允许的范围之内。
2)静差C。
过渡过程终了时,被调参数稳定在给定值附近,稳定值与给定值之差叫做静差,│C│=0时为无静差;│C│≠0时为有静差。
生产工艺要求静差限制在一个允许的范围内。
3)超调量(动差)M。
过渡过程中,被调参数相对于新稳态值的最大波动量。
4)最大偏差A=M+C。
它是被调参数相对于给定值的最大偏差。
若A过大,且偏离时间过长,系统离开指定的工艺状态越远,调节品质越差。
5)振荡周期Tp和振荡频率f。
相邻两个波峰所经历的时间为振曲周期Tp;其倒数为振荡频率f。
6)调节过程时间ts它指调节系统受干扰后,从被调参数开始波动,至达到新稳态值所经历的时间间隔。
(三)、调节对象的特性
调节对象的特性对于选择适当的调节装置极为重要。
(1)对象的负荷自动调节对象处于稳态时,单位时间流入或流出对象的物流量或能量叫做对象的负荷。
(2)对象的容量及容量系数容量是指被调参数为给定值时,对象中能够蓄存的能量或者物流量。
容量系数是指被调参数改变一个单位量时,对象容量的变化。
容量系数反映同样干扰下,被调参数偏离给定值的程度。
容量系数越大,偏离程度越小,系统越容易稳定。
反之,越不容易稳定。
(3)对象的自平衡特性当干扰不大时,即使没有调节作用,被调参数变化到使对象流入与流出间建立起新的平衡时,也将稳定下来。
这就是对象的自平衡性。
对象在受干扰时,靠自身参数调整自动恢复平衡的能力叫做自平衡能力。
对象达到自平衡所经历的过程叫自平衡过程。
(4)调节对象的动态特性微分方程理论分析调节对象特性的方法是根据支配对象的物理规律,例如能量平衡、质量平衡、力平衡……等,找出对象输出量与输入量的数学关系,从而建立起对象的动态特性微分方程。
(5)调节对象的特性参数描述调节对象的特性参数包括放大系数K1、时间常数T1、滞后τ。
下面以图6-10所示的有滞后的单容对象的反应曲线加以说明。
1)放大系数K1。
放大系数又叫传递系数。
它等于飞升过程中被调参数新、旧稳定值的差与干扰幅之比。
K1只与干扰前后的两个稳态值有关,而与变化过程无关,所以它代表对象的静特性。
反映了对象的自平衡性。
Kl越大,自平衡能力越差;反之,自平衡能力越强。
2)时间常数T1。
它是对象受干扰后,若被调参数以初始最大变化速度,恒速变化到新稳态值所需的时间。
时间常数又是被调参数变化到新稳态值的0.632倍时所经历的时间。
时间常数反映对象过程时间的长矩。
3)滞后τ。
在对象的输入变化后,输出信号总要迟后一段时间才开始变
化,这段时间间隔叫做滞后。
滞后对调节过程产生不利影响。
由于某种原因,不能对干扰和调节立即作出反应,在滞后时间内,被调参数将按原来的趋势继续变化,结果使调节系统的稳定性变差,被调参数的最大偏差增大,过渡过程时间延长。
所以应注意尽量减小滞后。
对象的上述特性参数K1、T1、τ和特性比τ/T1是选择调节装置和进行参数整定的重要依据。
(四)、调节器的构成原理
1.常用调节器的调节规律调节器是自动调节系统中的专用仪器。
调节器根据被调参数测量值和给定值的偏差信号,按某一调节规律和精度自动调节,使被调参数保持在规定范围或者按照指定的规律变化。
它是调节系统的重要组成部分之一。
调节器输出信号y与输入信号(偏差)e的关系叫调节规律。
通常按照调节规律来划分调节器。
(1)双位调节器它只有两种输出状态,当正偏差量超