连铸用耐火材料Word文档下载推荐.docx
《连铸用耐火材料Word文档下载推荐.docx》由会员分享,可在线阅读,更多相关《连铸用耐火材料Word文档下载推荐.docx(20页珍藏版)》请在冰豆网上搜索。
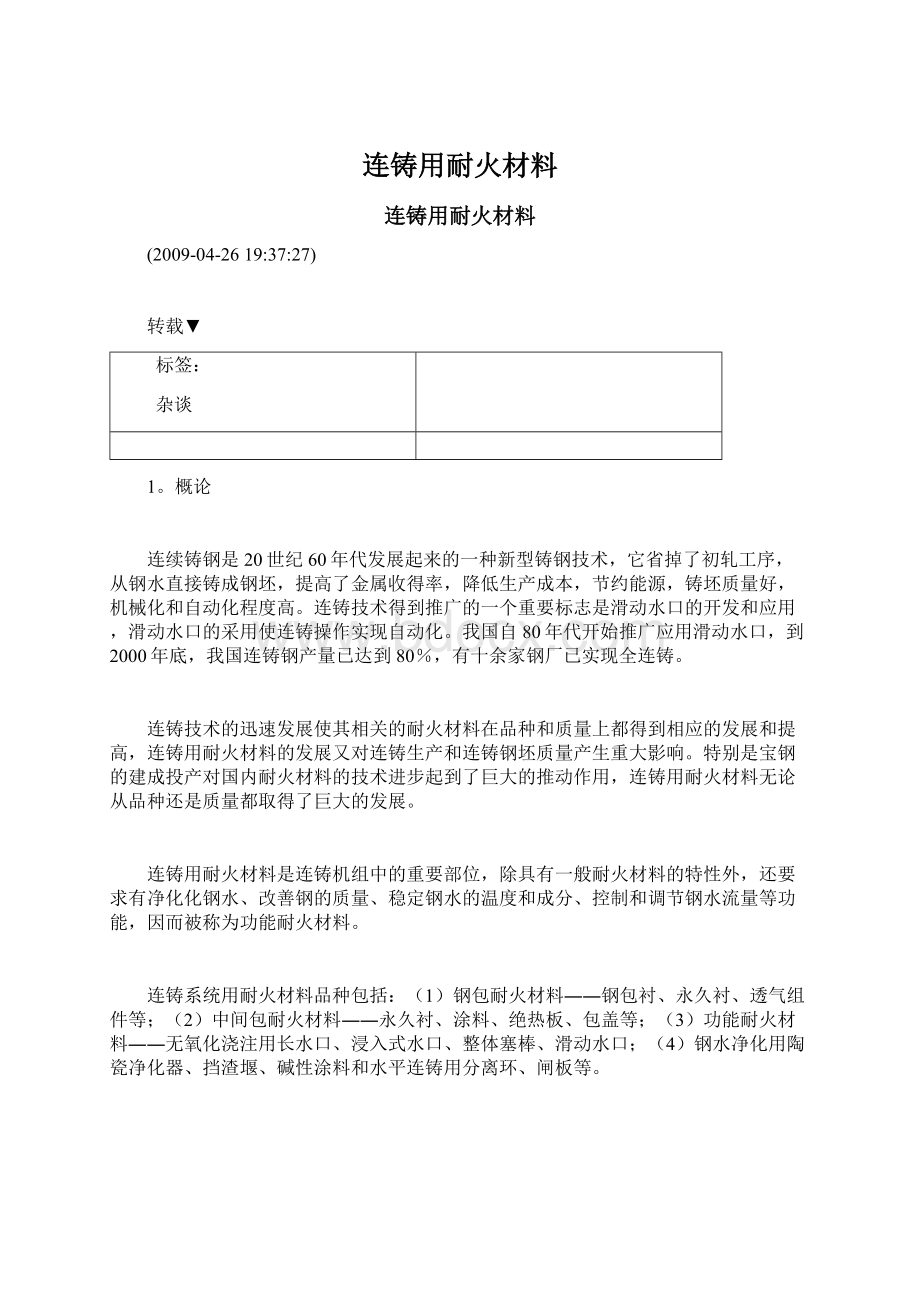
特别是包底不能因为收缩开裂造成脱落;
(3)
钢包为间歇式作业,经受冷却――高温的反复热循环作用,砖必须有良好的抗热震性和抗剥落性;
(4)
为保持钢水的洁净度,要求钢包有良好的抗侵蚀性,高温下耐火材料尽量少熔入钢水;
(5)从经济角度出发,要求钢包衬有良好的施工性能且价格适当。
包衬用耐火材料已从定形制品向不定形材料发展。
2.1包衬用材料
2.1.1永久衬用耐火材料
钢包一般采用三层砌筑结构即隔热层、永久层和工作层。
绝热层一般采用轻质粘土砖、硅酸铝纤维毡或轻质浇注料砌筑。
而永久层目前普遍采整体打结的方式,材质有水玻璃结合的铝镁浇注料、低水泥或超低水泥高铝浇注料。
永久衬的施工是在隔热层砌筑完后,在其表面粘一层牛皮纸以防吸浆,然后放上胎模浇注永久层,永久层施工一般采用振动成型,为改善施工条件、减轻劳动强度,我厂开发了钢包永久衬用自流浇注料,取得了较好的使用效果。
2.1.2包壁用耐火材料
我国在80年代钢包普遍采用高铝砖和叶蜡石砖,随着连铸的发展,钢水在钢包内停留的时间延长,砖衬出现熔损、剥落,寿命降低。
为提高包衬寿命,减少渣的侵蚀,开发了在Al2O3-SiO2系材料中引入MgO的Al2O3-SiO2-MgO系材料,利用MgO与Al2O3高温下生成镁铝尖晶石,且产生一定的膨胀作用,具有极好抗侵蚀和抗渣渗透性。
同时MA尖晶石可与渣中的FeO反应形成铁铝尖晶FeO+MgO•Al2O3≒MgO+FeAl2O4;
过量的FeO与MgO形成固溶体,提高了渣的粘度,减少了渣的侵蚀与渗透。
2.1.2.1水玻璃结合不烧砖
水玻璃结合铝镁砖骨料采用一级矾土,细粉用特级矾土粉和一级镁砂粉,采用水玻璃作结合剂,机压成型后经低温热处理即为成品.该产品在模铸的大、中型钢包上使用,取得了较好的使用效果。
为提高铝镁砖的抗侵蚀性,在不烧铝镁砖的基础上添加石墨制成的不玻璃结合铝镁碳砖,在中小型模铸钢包上使用,寿命达到50~100次,因其价格低廉,在中小钢厂得到推广。
2.1.2.2树脂结合铝镁碳砖和镁铝碳砖
树脂结合铝镁碳砖原料采用特级矾土熟料、高铝刚玉和镁铝尖晶石等作骨料,添加镁砂细粉、磷片石墨、碳化硅及氧化铝粉,用树脂作结合剂经高压成型,低温热处理。
该产品具有强度高、抗侵蚀性好、抗剥落性好、抗热震性和不粘渣等优点。
在大型连铸钢包上使用,寿命达到50~100次;
特别是在LF-VD精炼炉上得到应用。
树脂结合镁铝碳砖与铝镁碳砖生产工艺基本相同,主要原料是在镁砂中添加预合成的镁铝尖晶石,利用两者在高温下线膨胀系数差别较大的特性,来缓冲因温度变化产生的热应力,减轻热剥落;
添加炭素材料,高温下形成碳网结构,有效地阻止熔渣的侵蚀和渗透。
镁铝碳砖有较好的抗侵蚀性,适用高碱度渣及LF精炼包等更苛刻的条件。
目前国内大中型钢包包壁普遍采用树脂结合的铝镁碳砖和镁铝碳砖,已经满足了钢厂的需要。
LF(电弧加热钢包精炼)法及LFV(真空电弧加热钢包精炼)法钢水温度更高、熔渣碱度大、加之吹气搅拌以及真空或还原气氛,耐火材料要承受化学反应与熔损、高温真空下的挥发、熔渣的侵蚀以及热冲击和机械冲刷,要求耐火材料的强度要高、热震稳定性好、抗渣侵蚀性好。
精炼炉包壁采用铝镁碳砖或镁铝碳砖,使用寿命普遍达到50炉以上;
在真空冶炼的情况下,使用镁钙碳砖的效果要优于铝镁碳砖。
ASEA-SKF(电弧加热电磁搅拌精炼)法冶炼,耐火材料要经受电极电弧的强烈辐射、高碱度高温熔渣的强烈侵蚀与溶解、高温真空下的还原、电磁搅拌和包底吹氩所造成强烈冲刷和磨损以及内衬温度的急剧变化。
我国在SKF炉内衬高侵蚀区采用电熔再结合镁砖及镁铬砖,低侵蚀区采用高铝砖,平均寿命达到30炉左右。
欧洲普遍采用镁白云石砖,寿命在20~30炉。
表1优质钢包衬砖
铝镁尖晶石碳砖
铝镁碳砖
镁铝碳砖
镁碳砖
PN-SPC1
PN-SPC2
PN-AMC
PN-MAC
PN-MT10
PN-MT14
Al2O3
%
≥
60
70
65
15
MgO
10
78
74
C
7
8
14
显气孔率
%
≤
11
5
4
体积密度g/cm3
2.72
2.82
2.75
2.8
2.85
耐压强度
MPa
80
85
55
50
40
重烧线变化
%
(1550×
3h)
0~+1.0
+0.5~+2.0
+0~+1.0
+0.5~+2.5
高温抗折强度
≥
(1400℃×
0.5h,埋炭)
6
6.5
2.1.2.3包衬用浇注料
80年代,国内中小钢包采用水玻璃结合的铝镁浇注料,以一级高铝矾土作骨料,添加镁砂细粉,用不玻璃作结合剂,外加氟硅酸钠作促凝剂,在中小钢厂模铸钢包上使用平均寿命达到60~80次,基本满足了模铸生产的需要。
但随着连铸的发展,浇钢时间延长,浇钢温度提高,水玻璃结合的铝镁浇注料其抗侵蚀性、抗剥落性已不能满足生产的需要。
在90年代,又开发了低水泥、超低水泥结合的尖晶石质浇注料,其品种有适应中小钢厂使用的矾土尖晶石浇注料、适应大型钢包和精炼需要的刚玉尖晶石浇注料。
矾土尖晶石浇注料是以特级矾土为骨料,添加预合成的尖晶石,利用尖晶石抗侵蚀性好和热震稳定性好的特点,同时适量添加镁砂在更高的温度下与矾土颗粒继续反应生成尖晶石,伴随着持续性的膨胀有利于保持高温下的体积稳定性;
采用SiO2超微粉和MgO与水形成凝聚结合以及合适的减少剂,实现低水分下有较好的流动性和较高的强度,具有较好的抗侵蚀性和抗剥落性。
矾土基尖晶石浇注料在国内中小型连铸钢包上使用寿命达到100炉以上。
随着大型钢包连铸及精炼的发展,普通的铝镁浇注料已不能满足使用寿命的要求,在此基础上又开发了刚玉尖晶石浇注料,降低水泥用量,合理控制MgO含量,调整尖晶石含量;
具有更好的抗侵蚀、抗渗透以及抗剥落性,在宝钢、首钢、武钢等钢厂大型连铸钢包上使用寿命均超过150次,且使用过程中没有大的裂纹和剥落现象。
表2
钢包浇注料理化指标
项目
铝镁浇注料
矾土尖晶石浇注料
刚玉尖晶石浇注料
68
72
88
12
SiO2
1.5
体积密度g/cm3
2.65
3.05
耐压强度110℃×
24h
Mpa
1100℃×
3h
1550℃×
23
110
抗折强度
110℃×
MPa
9
7.0
线变化率%
+0.30
+0.8~+2.0
钢包整体耐火材料的不定形化技术介绍
以往,炼钢所用的耐火材料一直以耐火砖为主,但由于砌砖操作需要熟练的技术,加之近年来筑炉操作工的年龄老化等问题,因此采用耐火材料的不定形化技术来实现筑炉操作的自动化和节省劳力已成为重要课题。
最近,以浇注耐火材料的开发为主,开发了低水泥、高密度耐火材料,广泛应用于高炉出铁槽、钢包、中间包和RH等,推进了钢铁行业耐火材料的不定形化技术。
为减少钢包筑炉操作和降低耐火材料成本,日本大同特殊钢公司Shibukswa厂作为特殊钢生产厂之一,于1995年首次在VLF(真空钢包炉)的钢包内衬采用了耐火材料的不定形化技术。
自1997年以后,该厂在SUS(不锈钢)和超合金钢生产用的钢包包底和包壁筑炉中实现了Al2O3质浇注料的浇注施工。
特别是最近在把不定形化技术扩大应用于各种耐火材料时,由于引进了新型湿式喷补施工技术,因而确立了钢包整体耐火材料不定形化的技术,其概况介绍如下。
不定形耐火材料浇注施工技术的引进
作为钢包包底和包壁不定形耐火材料的施工方法,当初引进的是最普通的浇注施工方法。
1浇注施工
浇注施工方法:
首先,在包底施工后进行半天左右的自然养护。
接着,安装框架和混合搅拌机,在浇注耐材之后,为使整个缝隙填充均匀,用棒式振捣器进行助振。
再经半天左右的自然养护后进行脱模,然后对渣线部位进行耐火砖的砌筑施工。
2浇注材质的选择
对用于包底和包壁耐火材料的特性,不仅要求其抗腐蚀性和抗渣性要好,而且结构要稳定。
一般认为Al2O3-MgO质耐火材料能满足上述条件要求。
Al2O3-MgO质耐火材料中的MgO量在7-28%范围时,会形成组织致密、稳定的尖晶石固溶体,因此一般用作炼钢钢包的耐火材料。
该厂重视降低成本,提高钢水冲击部的抗磨损性,重视残余膨胀性的影响作用,因此采用Al2O3-MgO材质作浇注料。
另外,即使在长施工体的厚度较薄(最薄40mm)的情况下,为确保浇注料的流动性,因此规定Al2O3骨料粒度在8mm以下,而且还添加了金属Al,作为防止干燥时发生爆裂的措施。
3实际应用的结果
对15t钢包包壁最上部的熔损速度进行了调查。
与耐火砖比,浇注料各部位的最大熔损速度为0.4mm/炉,而渣线砖的修补周期(大约40炉钢水)是在砖的熔损达16mm左右时才进行的,因而不会对钢包寿命产生不良影响。
另外,使用后的工作面在清除粘附的金属和对表面进行若干清理后,只要工作面没有全部熔损,就可以进行接长修补,由此能减少新喷补施工时耐火材料的使用量和减少钢包产生的废砖达30%左右。
4扩大不定形化技术的课题
虽然已知浇注材料在耐用性能方面是没问题的,但为降低整个炼钢耐火材料的成本,今后有必要将不定形化技术扩大应用于其它耐火材料的施工体(例如,25t钢包、VLF钢包和出钢槽等)。
采用该方法进行浇注施工时担心有以下问题:
①由于浇注体需要固化养护(为使浇注体的强度能达到渣线筑炉部位的强度,需要时间养护),因此降低了筑炉效率。
②各施工部位需要专用的框架,因此难以确保框架的安装位置。
为解决这些问题,必须改进施工方法。
湿式项补施工技术的引进
1改进施工方法
为解决上述问题,最近以炼钢厂为主引进了正在不断被推广的湿式喷补施工技术。
喷补操作程序如下。
首先,用混合机将不定形材料与水混合后分批装入料斗,然后把装入料斗的喷补料用活塞式压力泵通过管道送到喷嘴,同时通过另外一根管道采用压缩空气将固化剂送到喷嘴端部,在喷出之前与喷补料混合后喷补在施工体上。
与以往的浇注施工相比,湿式喷补施工的主要特征如下:
①由于不需要框架,因此能在任意位置进行任意厚度的施工。
②由于添加固化剂,缩短了固化养护时间,因此能进行连续施工。
③由于施工效率高(5-10t/hr),因此可缩短施工时间。
除此之外,它还能使耐火材料发生的熔化损失均匀,并可应付紧急情况。
即可以说喷补施工法就是利用不定形耐火材料的特性来弥补浇注施工缺陷的施工方法。
2改进材质
以上述的浇注材料为基础,对浇注材质的压力输送性能、抗腐蚀性能和抗爆裂性能进行了改进。
(1)提高压力输送性能
为使湿式喷补材料能在压力下从内径Ф38mm的管道和喷嘴通过,因此事先对各种喷补料在喷嘴内的流动性进行了确认试验,其结果示于表1。
由该表可知,如果直接采用象浇注料那样的粒度,就会发生喷嘴堵塞,因此降低了粗粒度比,并将Al2O3骨料的粒度从8mm降低到5mm。
表1压送试验的结果
试样ABCD
骨料比粗颗粒/中等颗粒2/12/13/21/1
上限粒度(mm)8555
添加的水分(%)6.26.46.66.9
排出的流量(mm)182********8
压送压力(Mpa)﹥141384
压送评价不好不好好好
(2)提高抗腐蚀性能
根据上述试验结果可知,采用表1的试料C和D时,不会发生喷嘴堵塞,但由于这两种试料添加的水分量比浇注料的大,因此会影响抗腐蚀性能。
基于此因,在试料C和D中,以水分低的试料C为基础,通过高频炉的侵蚀试验,调查了通过增加MgO量来提高抗腐蚀性能的效果。
结果,考虑到抗腐蚀性能和炉渣侵蚀的深度,将MgO量增加到10%,能弥补抗腐蚀性能的恶化。
3提高抗爆裂性能
采用上述材质对15t钢包和25t钢包的包底及包壁进行湿式喷补施工后,在预热1小时左右时喷补料会频繁发生爆裂故障,爆裂宽度大约30-50mm。
作为防止发生爆裂的措施,由于当初采取的是添加有机纤维的办法,但不理想,因此在改善钢包干燥条件的情况下进行了研究。
(1)爆裂发生的机理
采用一般干燥曲线模型对干燥中耐火材料内部的温度和水蒸气压力的变化进行了模拟,结果表明,干燥过程中施工体内部存在3个区域,一是靠近加热面含水率为0的干燥区域;
二是水分迅速蒸发的蒸发区域;
三是在蒸发区域产生的水蒸气流向被加热的背面,压力超过了饱和水蒸气压,形成凝结现象的凝结区域。
干燥时的爆裂只有在蒸发区域满足了下列条件时才会发生。
Pa+UT<Ps
Pa:
表面热风蒸气压(MPa)
Ps:
蒸发面内部的蒸气压(MPa)
UT:
材料强度(MPa=与抗拉强度和抗拉变形有关的抗折强度
在加热面一侧的含水量减少到一定程度后进行快速加热时,由于蒸发区域中的温度变化小,因此内部蒸气压的增幅小,但另一方面在干燥初期含水量的状态下进行快速加热时,由于蒸发区域靠近加热面,因此表层一侧内部蒸气压的增幅明显。
如上式表明的那样,可以推测蒸发区域的内部蒸气压增大后,会造成材料自身的强度无法承受这一压力,因此发生了爆裂。
(2)改进干燥方法
对实际干燥中各部位温度变化进行实测,摸索出了最佳干燥条件。
结果,根据以上喷嘴耐火材料的表面温度为基准,进行了干燥,基本抑制了爆裂。
目前,把以下3点作为抑制爆裂的条件是很重要的。
①干燥开始3小时后:
加热速度<90℃/hr。
②在3-6小时后:
加热速度<200℃/hr(6小时后,以表面温度800-900℃为标准)。
③在6小时后:
炉壳温度>60℃时,加热不能超过1200-1300℃。
但是,在冬季室外气温低的情况下,由于干燥前的养护强度(抗折强度)低,因此无法确保材料具有耐蒸气压的强度,故频繁发生爆裂。
作为其措施是采取预热干燥的办法,即筑炉后在钢包内对发热体进行燃烧,但这种干燥条件有待进一步改善。
在实机使用的情况
1熔损速度
15t钢包的包壁采用湿式喷补材料后的熔损速度表明,采用喷补材料的平均熔损速度为1.57mm/炉,虽然比耐火砖的增大5%,但与浇注材相比,却取得良好的结果,受钢水冲击部位的烙损速度最大为2.5mm/炉,与浇注材料的呈相同趋势,但其绝对值低。
与浇注材料的主要区别在于透气砖和受钢水冲击部周围的熔损速度非常低,这两处分别是采用吹氩搅拌和采用AOD(氩氧脱碳法)装入钢水时因钢水冲击而造成熔损严重的部位,由此可知采用喷补料的施工体具有良好的抗磨损性能。
2断面组织
从15t钢包在使用39炉后喷补材的断面组织照片和炉渣的侵蚀深度来看,包底的侵蚀深度比包壁的大30-40mm,在微变层内部能看见有一部分横向裂纹,还能看见有部分金属侵人。
包壁的炉渣侵蚀深度较浅,为15-20mm,与浇注材的基本相同。
另一方面,由于原始层的组织非常致密,且气孔率也低,只有12%,因此形成了良好的组织。
使用后的钢包包壁经取样做X线衍射后可知,工作面的组织主要是a-Al2O3、硅铝酸二钙(2CaO-Al2O3-SiO2:
耐火度1590℃)、尖晶石(MgO-Al2O3:
耐火度2135℃);
母材由β-Al2O3和尖晶石构成,由此可以推测浇注材和喷补材的化合物相同。
这种CaO-Al2O3-SiO2系低熔点化合物的形成是造成熔损的主要原因。
另外,尖晶石不是作为材料添加的,它是材料中的Al2O3骨料和基料中的MgO细粉在高温下反应后形成的,即使在母材中,尖晶石也已形成分布范围广的组织形态。
施工效率和成本
各种施工方法的施工天数比较结果表明,以一座钢包的筑炉操作天数为例,采用浇注施工时,由于能连续接长修补,因此包底和包壁的解体时间可以缩短,与耐火砖相比,可缩短总的工期25%;
采用喷补施工时,由于添加了固化剂,节省了养护时间,因此可缩短工期40%。
成本的比较结果表明,与浇注料相比,喷补料的价格仅仅是固化剂这一项的价格比浇注料高,但由于可延长使用寿命,因此比耐火砖可节约成本28%左右,比浇注材料的节约14%。
今后如果能将不定形化的喷补技术应用于目前仍采用耐火砖的容器(如,25tVLF钢包和中间包等),估计可以大幅度降低耐火材料成本。
可以认为这是一种非常理想的施工技术。
结束语
15t钢包包底和包壁采用湿式喷补施工的结果表明,不论是施工效率,还是成本,都优于浇注施工法。
为实现将来中间包等也能采用不定形化技术和出钢槽采用喷补修补技术来延长使用寿命,因此期待着这种湿式喷补机能成为广泛应用于各种物体施工的通用设备,从而进一步降低耐火材料成本。
洁净钢技术与工艺简介
(1)
(2009-05-0819:
56:
34)
1目标与目的
钢洁净度在钢铁应用的发展中是最重要的。
钢的性能决定了它的用途与竞争能力,而化学成分和最终的显微组织确定了钢的性能。
因此,不会有一个完整的洁净钢定义,它仅仅是与应用有关的一个术语。
氧化物在改变钢的显微组织上扮演了重要角色,因此,成为本次研究的焦点。
它们要么以钢水二次氧化的形式存在,要么以耐材或保护渣吸卷的方式进入钢中。
因此,炼钢,尤其是二次冶金处理和连铸工序是实现所要求的洁净度的关键。
为判定最佳操作和建立科学的概念,收集了关于设备、工艺和控制方面的数据。
这些数据来自22个国家的64套设备上,各个数据表包含了800条不同的信息,总共获得了5万余条可用信息。
选择了低碳钢、超低碳钢、管线钢、高碳长材和弹簧钢进行研究,应用领域涵盖了汽车裸露件、管线和滚珠轴承等。
比较工业实践仅仅是该项目的一个部分,此外,还进行了深入的文献调查,以确定今后的发展与进步。
氧化洁净度是优质钢最重要的一个指标。
全世界在改进二次炼钢和连铸工艺技术方面付出了巨大努力。
主要目的是要将钢水中夹杂物含量减少到最低程度,促进颗粒分离,避免被大气、炉渣和耐火材料二次氧化等。
有害夹杂物一个主要成因是非常小的夹杂物在紊流区凝结,这出现在从大包到中间包、中间包再到结晶器传输钢水的过程。
相反,外来非金属夹杂物源于炉渣夹带,因此,保护渣绝不能乳化进入钢水。
这是对钢铁工业在这个艰难冶金领域里继续发展提出的挑战。
2洁净钢
这次的研究不是要建立洁净钢的通用定义,因为洁净度是钢材使用的直接结果,对洁净度的要求各不相同。
本次研究集中在氧化物夹杂方面。
氧化物夹杂数量根据使用要求可以不同,但在位置、形状、分布和其它许多方面要仔细考虑。
一般而言,钢和食品一样干净。
人们所不希望的成分浓度大约是百万分之的数量级。
而且,钢中局部含有杂质不会影响使用。
当讨论钢的洁净度时,氧化物夹杂是讨论的重点。
氧化物颗粒是在生产加工中由脱氧、二次氧化生成的,或与各种容器的耐火材料反应形成的。
多数颗粒能在钢包、中间包和结晶器中与钢水分离、熔入渣中。
留在钢水中的氧化物颗粒非常小,只有几个微米。
显微洁净度是用钢水中总氧含量定义的。
必须假定这些显微夹杂对高性能钢是无害的。
即便如此,显微洁净度仍具有重要的意义,它是紊流区凝聚形成宏观夹杂物的基础。
钢材缺陷的起因通常是钢铁生产中必须避免的宏观夹杂物。
夹杂物含量低是洁净