VCM装置工艺管道安装技术总结文档格式.docx
《VCM装置工艺管道安装技术总结文档格式.docx》由会员分享,可在线阅读,更多相关《VCM装置工艺管道安装技术总结文档格式.docx(17页珍藏版)》请在冰豆网上搜索。
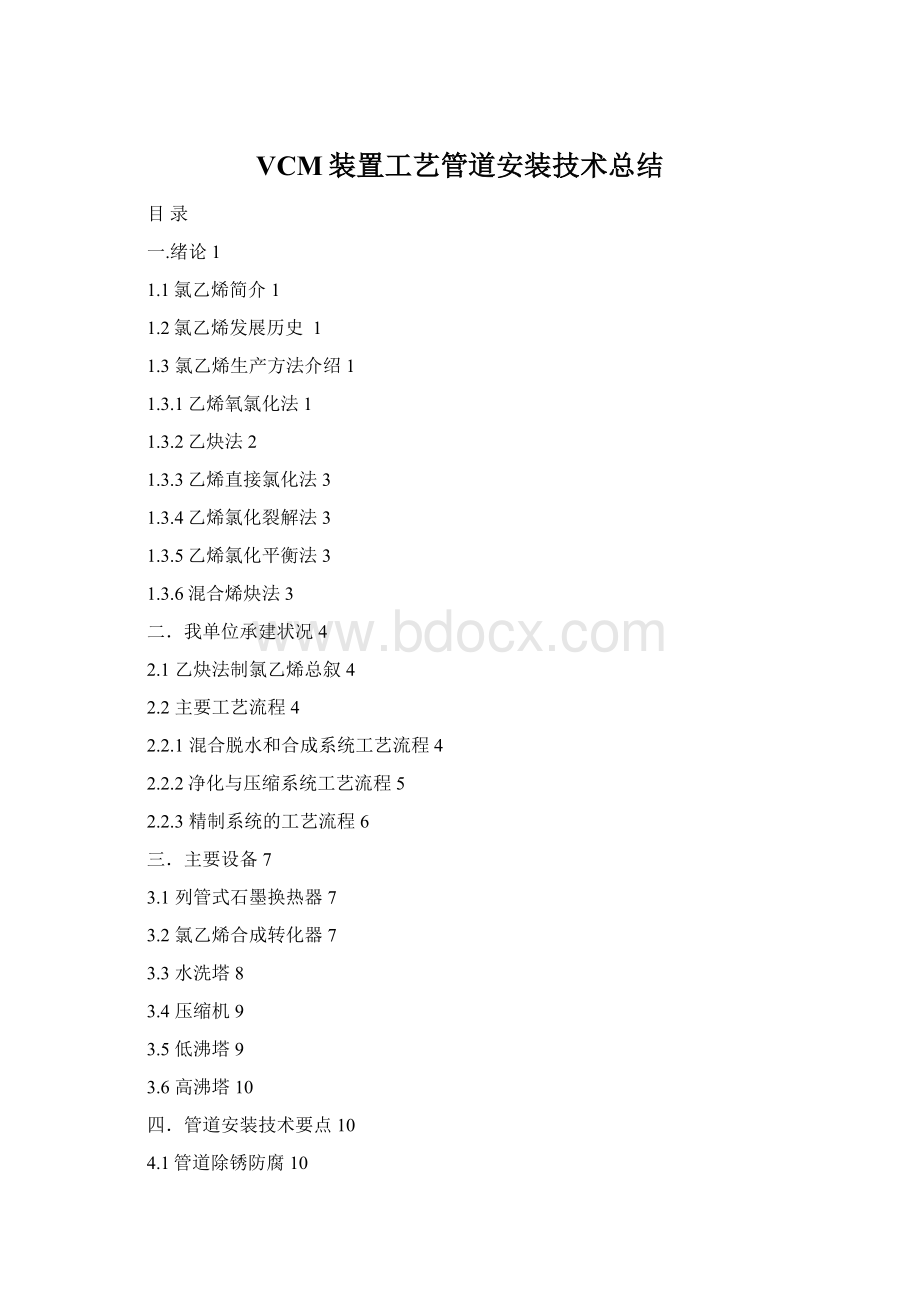
一.绪论
1.1氯乙烯简介
氯乙烯是一种应用于高分子化工的重要的单体。
化学式为CH2CHCl,是卤代烃的一种,工业上大量用作生产聚氯乙烯(PVC)的单体。
它在室温下是无色有毒的气体,微溶于水,有醚香的气味。
沸点-13.9℃,临界温度142℃,临界压力5.22MPa。
氯乙烯是有毒物质,肝癌与长期吸入和接触氯乙烯有关。
它与空气形成爆炸混合物,爆炸极限4%~22%(体积),在压力下更易爆炸,贮运时必须注意容器的密闭及氮封,并应添加少量阻聚剂。
1.2氯乙烯发展历史
1835年法国人V.勒尼奥用氢氧化钾在乙醇溶液中处理二氯乙烷首先得到氯乙烯。
20世纪30年代,德国格里斯海姆电子公司基於氯化氢与乙炔加成,首先实现了氯乙烯的工业生产。
初期,氯乙烯采用电石,乙炔与氯化氢催化加成的方法生产,简称乙炔法。
以后,随著石油化工的发展,氯乙烯的合成迅速转向以乙烯为原料的工艺路线。
1940年,美国联合碳化物公司开发了二氯乙烷法。
为了平衡氯气的利用,日本吴羽化学工业公司又开发了将乙炔法和二氯乙烷法联合生产氯乙烯的联合法。
1960年,美国陶氏化学公司开发了乙烯经氧氯化合成氯乙烯的方法,并和二氯乙烷法配合,开发成以乙烯为原料生产氯乙烯的完整方法,此法得到了迅速发展。
乙炔法、混合烯炔法等其他方法由於能耗高而处於逐步被淘汰的地位。
1.3氯乙烯生产方法介绍
1.3.1乙烯氧氯化法
现代工业生产氯乙烯的主要方法。
分三步进行:
第一步乙烯氯化生成二氯乙烷;
第二步二氯乙烷热裂解为氯乙烯及氯化氢;
第三步乙烯、氯化氢和氧发生氧氯化反应生成二氯乙烷。
①乙烯氯化 乙烯和氯加成反应在液相中进行:
CH2=CH2+Cl2→CH2ClCH2Cl
采用三氯化铁或氯化铜等作催化剂,产品二氯乙烷为反应介质。
反应热可通过冷却水或产品二氯乙烷汽化来移出。
反应温度40~110℃,压力0.15~0.30MPa,乙烯的转化率和选择性均在99%以上。
②二氯乙烷热裂解 生成氯乙烯的反应式为:
ClCH2CH2Cl→CH2=CHCl+HCl
反应是强烈的吸热反应,在管式裂解炉中进行,反应温度500~550℃,压力0.6~1.5MPa;
控制二氯乙烷单程转化率为50%~70%,以抑制副反应的进行。
主要副反应为:
CH2=CHCl→HC≡CH+HCl
CH2=CHCl+HCl→ClCH2CH2Cl
ClCH2CH2Cl→2CH2+2HCl
裂解产物进入淬冷塔,用循环的二氯乙烷冷却,以避免继续发生副反应。
产物温度冷却到50~150℃后,进入脱氯化氢塔。
塔底为氯乙烯和二氯乙烷的混合物,通过氯乙烯精馏塔精馏,由塔顶获得高纯度氯乙烯,塔底重组分主要为未反应的粗二氯乙烷,经精馏除去不纯物后,仍作热裂解原料。
③氧氯化反应 以载在γ-氧化铝上的氯化铜为催化剂,以碱金属或碱土金属盐为助催化剂。
主反应式为:
H2C=CH2+2HCL&
frac12;
O2→CLCH2CH2Cl+H2O
主要副反应为乙烯的深度氧化(生成一氧化碳、二氧化碳和水)和氯乙烯的氧氯化(生成乙烷的多种氯化物)。
反应温度200~230℃,压力0.2~1MPa,原料乙烯、氯化氢、氧的摩尔比为1.05:
2:
0.75~0.85。
反应器有固定床和流化床两种形式,固定床常用列管式反应器,管内填充颗粒状催化剂,原料乙烯、氯化氢与空气自上而下通过催化剂床层,管间用加压热水作热载体,以移走反应热,并副产压力1MPa的蒸汽。
固定床反应器温度较难控制,为使有较合理的温度分布,常采用大量惰性气体作稀释剂,或在催化剂中掺入固体物质。
二氯乙烷的选择性可达98%以上。
在流化床反应器中进行乙烯氧氯化反应时,采用细颗粒催化剂,原料乙烯、氯化氢和空气分别由底部进入反应器,充分混合均匀后,通入催化剂层,并使催化剂处于流化状态,床内装有换热器,可有效地引出反应热。
这种反应器反应温度均匀而易于控制,适宜于大规模生产,但反应器结构较复杂,催化剂磨损大。
由反应器出来的反应产物经水淬冷,再冷凝成液态粗二氯乙烷。
冷凝器中未被冷凝的部分二氯乙烷及未转化的乙烯、惰性气体等经溶剂吸收等步骤回收其中二氯乙烷。
所得粗二氯乙烷经精制后进入热解炉裂解。
乙烯氧氯化法的主要优点是利用二氯乙烷热裂解所产生的氯化氢作为氯化剂,从而使氯得到了完全利用。
1.3.2乙炔法
在氯化汞催化剂存在下,乙炔与氯化氢加成直接合成氯乙烯:
CH≡CH+Cl→CH2=CHCl
其过程可分为乙炔的制取和精制,氯乙烯的合成以及产物精制三部分。
在乙炔发生器中,电石与水反应产生乙炔,经精制并与氯化氢混合、干燥后进入列管式反应器。
管内装有以活性炭为载体的氯化汞(含量一般为载体质量的10%)催化剂。
反应在常压下进行,管外用加压循环热水(97~105℃)冷却,以除去反应热,并使床层温度控制在180~200℃。
乙炔转化率达99%,氯乙烯收率在95%以上。
副产物是1,1-二氯乙烷(约1%),也有少量乙烯基乙炔、二氯乙烯、三氯乙烷等。
此法工艺和设备简单,投资低,收率高;
但能耗大,原料成本高,催化剂汞盐毒性大,并受到安全生产、保护环境等条件限制,不宜大规模生产。
1.3.3乙烯直接氯化法
这是石油化工发展后以石油为基础开发的生产工艺。
此法的最大缺点是伴随反应生成了大量的1,2-二氯乙烷,产率较低。
CH2=CH2+Cl2→CH2=CHCl+HCl
1.3.4乙烯氯化裂解法
这是为解决乙烯直接氯化法存在的问题而开发的生产工艺,此法产率高。
CH2=CH2+Cl2→CH2ClCH2Cl
CH2ClCH2Cl→CH2=CHCl+HCl
1.3.5乙烯氯化平衡法
比较乙烯氯化裂解法和乙烯氧氯化法,可以发现,乙烯氯化裂解法产生氯化氢,乙烯氧氯化法消耗氯化氢。
如果将两种方法结合起来,让乙烯氯化裂解法和乙烯氧氯化法的第一步按照一定的比例生产,可以使氯化氢变为中间产物,这是目前世界上生产氯乙烯的主要方法。
不久的将来,我国的氯乙烯生产将主要采用这种方法。
1.3.6混合烯炔法
该法是以石油烃高温裂解所得的乙炔和乙烯混合气(接近等摩尔比)为原料,与氯化氢一起通过氯化汞催化剂床层,使氯化氢选择性地与乙炔加成,产生氯乙烯。
分离氯乙烯后,把含有乙烯的残余气体与氯气混合,进行反应,生成二氯乙烷。
经分离精制后的二氯乙烷,热裂解成氯乙烯及氯化氢。
氯化氢再循环用于混合气中乙炔的加成。
二.我单位承建状况
2.1乙炔法制氯乙烯总叙
我单位承建青海盐湖海纳化工有限公司聚氯乙烯一体化项目年产24万吨VCM装置,VCM装置主要是由以下几大单元组成即:
原料处理单元、VCM合成转化单元、净化与压缩单元、VCM精馏单元、解析气碱洗与尾气变压吸附单元、VCM罐区单元、含汞废水处理单元等几个生产单元和公用工程设施组成。
其中原料处理单元、VCM合成转化单元、净化与压缩单元、VCM精馏单元、是生产产品的主要生产单元。
装置利用经分别干燥处理的乙炔和氯化氢原料气,按设定比例混合后,通过一段、二段反应器反应生成氯乙烯,再经净化、压缩、精馏得到氯乙烯成品。
精馏尾气采用变压吸附技术,回收氯乙烯,尾气经解吸气碱洗及排放气排放单体达标排放,含汞废水经含汞废水处理单体达标后排入全场废水处理系统。
VCM装置管线繁多,介质类别也比较多。
管道材料分为20#,304,304L,L245,FRP/PVC,20#/PTFE,16MnDG。
VCM各装置管道累计40000米,压力管道28Km,累计寸径22万达因。
2.2主要工艺流程
2.2.1混合脱水和合成系统工艺流程
图2-1示出混合脱水和合成系统的工艺流程.
由乙炔装置送来的精制乙炔气,经砂封和乙炔预冷器预冷后,与氯化氢装置送来的干燥氯化氢,经缓冲器通过流量计调节分子配比(乙炔/氯化氯=1/1.05~1.1),在混台器2中充分混合后,进入串联的石墨冷却器3a,3b,用-35℃盐水(尾气冷凝器下水)间接冷却,混合气中水分一部分则以40%盐酸排出,部分则夹带于气流中,进入串联的酸雾过滤器4a,4b,由硅油玻璃棉捕集分离。
然后该气体经预热器5预热,由流量计控制进入串联的第1组转化器6a,借列管中填装的暖附于活性炭上升汞催化剂,使乙炔和氯化氢合成转化为氯乙烯.第一组出口气体中尚有20一30%未转化乙炔,再进入第Ⅱ组转化器6b继续反应,使出口处未转化的乙炔控制在3%以下。
第二组转化器(可由数台并联操作)填装活性较高的新催化剂,第Ⅱ组转化器(也可由数台并联操作)则填装活性较低的,即由第Ⅱ组更换下来的旧催化剂.合成反应的热量.系通过离心泵送来的95~100℃左右的循环热水移去。
在混合脱水系统石墨冷却器之后,也有采用先经旋风分离器分离酸液,再用一台酸雾过滤器脱酸的流程.在合成转化器系统,小型装置由于转化器台数少,如3~4台,也有采用可串联可并联的流程,遇个别转化器损漏时候可以灵活切换。
2.2.2净化与压缩系统工艺流程
图2-2粗氯乙烯净化压缩系统工艺流程图
1-汞吸附器;
2-水洗泡沫塔;
3-碱洗泡沫塔;
4-气柜;
5-冷碱塔;
6-机前预冷器;
7-氯乙烯压缩机;
8-机后冷却器
粗氯乙烯在高温下带逸的氯化高汞升华物,在填装活性炭的汞吸附器1中除去,然后由石墨冷却器将合成气冷却到15℃以下,通入水洗泡沫塔2回收过量的氯化氢。
泡沫塔顶是以高位槽低温水喷淋,一次(不循环)接触制得20%的盐酸,由塔底借位差注入酸盐大贮槽供灌装外销。
气体再经碱洗泡沫塔3除去残余的微量氯化氢后,送至氯乙烯气柜4,气柜中氯乙烯经冷碱塔5进一步除去微量酸性气体。
至机前冷却器6和水分离器7,分离出部分冷凝水,借往复式压缩机8加压至0.49—0.59MPa(表压),并经机后油分离器、冷却器9及分离器等设备,进一步除去油及水后送精馏系统水洗泡沫塔后,可串联第二台水洗泡沫塔或水洗填料塔(图中未标出),以备开停车通氯化氢时,或氯化氢纯度波动较大时,通入吸收水操作,其含少量氯化氢的酸性水可排至中和处理。
2.2.3精制系统的工艺流程
自压缩机送来的0.49~0.59MPa(表压)的粗氯乙烯;
,先进入冷凝器la,1b。
借工业水或0℃冻盐水进行间接冷却,使大部分氯乙烯气体液化。
液体氯乙烯借位差进入水分离器2,借密度差连续分层,除水后进入低沸塔3。
全凝器中未冷凝气体(主要为惰性气体)进入尾气冷凝器5,其冷凝液主要含有氯乙烯及乙炔组分,作为回流液返入低沸塔顶部,低沸塔底部的加热釜借转化器循环热水采进行间接加热,以将沿塔板下流的液相中的低沸物蒸出。
气相沿塔板向上流动并与塔板上液相进行热量及质量的交换,最后经塔顶冷凝器以0℃冷冻盐水将其冷凝作为塔顶回流盘,不冷凝气体亦由塔顶经全凝器通人尾气冷凝器处理。
低沸塔底脱除低沸物的氯乙烯借位差进入中间槽4。
尾
图2-3所示了氯乙烯精馏工艺流程
1a,1b—全凝器;
2—水分离器;
3—低沸塔;
4—中间槽;
5a,5b—尾气冷凝器;
6—水分离器;
7—高沸塔;
8—成品冷凝器;
9—单体贮槽
尾气冷凝器(用-35℃冷冻盐水冷却)排出的不冷凝气体,经尾气吸附装置(图中未示出),回收其中氯乙烯组分后,惰性气体经压力自控的减压阀排空。
中间槽的粗氯乙烯借阀门减压后连续进人高沸塔7,向下流的液相经塔底的加热釜将氯乙烯组分蒸出,上升的蒸气与塔板上液相进行同样的热量及质量交换,至塔顶排出精氯乙烯气相,经塔顶冷凝器以0℃冷冻盐水将其冷凝作为塔顶回流,大部分气相剐则进入成品冷凝器8,借工业水或0℃冷冻盐永间接冷却将氯乙烯全部冷凝下来,借位差流入成品贮槽9中.根据聚合装置需要,借氯乙烯气化槽中单体气化压力,将成品单体间歇压送至该装置使用。
自高沸塔底分离收集到的以1,1-二氯乙烷为主的高沸点物质,间歇排放人高沸物受槽,并由填料式蒸馏塔(又称Ⅲ塔)回收其中氯乙烯或40~70℃的馏分。
三.主要设备
3.1列管式石墨换热器
石墨换热器是用于冷却或加热氯化氢或其他腐蚀性气体的设备,主要有列管式和块孔式,图4浮头列管式石墨换热器。
图3-1列管式石墨换热器结构
1—法兰2—上管板3—填料4—压盖5—半开环6—底盖7—浮头8—钢壳9—石墨列管10—折流板11—支耳
由图3-1可见,与气体接触部分均用石墨材料制造,这种石墨是浸渍过酚醛或酚醛树脂的“不透性石墨”。
如上下管板2与7是由小尺寸石墨块交叉胶接后,经过车圆、浸渍、钻孔、浸渍、再精加工而完成的;
列管9则是由石墨粉与酚醛树脂捏和挤压成型的;
列管与管板(或浮头)间借酚醛胶泥粘合而成。
列管外的壳体8是通入冷却水,所以可用普通低碳钢制作,折流板10选用硬聚氯乙烯材料。
下管板7又称浮头,当操作温度高于或低于安装温度时,石墨列管由于具有较大的热膨胀系数,使它比钢质的外壳体发生较大的伸长或收缩,钢壳体与浮头间的填料函结构,就是为了防止因这种温差引起的伸缩,不致使石墨管或胶接处拉裂而产生泄漏。
也就是说,借支耳11,立式安立式安装的石墨换热器,上管板和钢壳是固定的,当操作温度变化时,由于列管与外壳伸缩不一致,导致浮头、底盖、乃至与底盖相连的管道都有观察不到的伸缩(或称作浮动),这就是浮头式石墨换热器的重要特性,所以,当与底盖连接的管道直径较夫,弯头直管段较短难以自然热补偿时,应根据伸缩情况加设管道热补偿器。
显而易见,对于列管式再墨换热器,立式安装比斜式或卧式安装更有利于浮头的自由伸缩。
3.2氯乙烯合成转化器
图3-2示出了大型转化器的结构。
转化器实际上就是一种大型的换热器。
其列管
8均采用毋无缝钢管与管板4胀接而成,
列管内放置催化剂,根据列管内的容积。
转化器的列管与管板胀接的技术要求较严格,因为它与一般换热器不同的是:
只要有微小的渗漏,将使管间的热水泄漏到设备内;
与气相中的氯化氢接触而生成浓盐酸,并进一步腐蚀直到大量盐酸从底部放酸口放出而造成停产事故,因此,对于转化器。
无论是新制造还是检修者,在安装前均应对管板胀接处作气密性试漏(用0.2~0.3MPa压缩空气)。
为减少氯化氢对列管胀接或焊缝的腐蚀,有的工厂采用耐酸树脂玻璃布进行局部增强。
设备的大部分材质可用低碳钢,其中管板由16Mn低合金钢制作,列管选用20#钢管。
下盖为防止盐酸腐蚀,用耐酸瓷砖衬里防护。
图3-2转化器结构
1-气体分配板;
2-上盖;
3-热电偶;
4-管板;
5-排气;
6-支耳;
7-折流板;
8-列管9-膨胀节;
10-活性碳;
11-小瓷环;
12-大瓷环;
13-多孔板;
14-下盖;
15-排水;
16-拉杆;
17-手孔
为减少转化器管间热水对外管壁的电化腐蚀,可采用如下的措施:
①减少水中氯根含量;
②提高pH值到8~10;
③补充水脱氧;
④添加缓蚀剂(如水玻璃)等。
比较普遍的办法是使用无离子水并借液碱控制pH值,可获得较好的效果。
3.3水洗塔
水洗塔结构、工作原理及操作
图3-3为典型水洗泡沫塔的结构。
塔身l为防止盐酸的腐蚀和氯乙烯的溶胀作用,采用衬一层橡胶作为底衬,再衬两层石墨砖。
包括衬胶泥厚度在内,其衬里总厚度为33mm左右。
筛板2采用厚度6-8mm的耐酸酚醛玻璃布层压板,经钻孔加工而成。
筛板共4~6块.均夹于塔身大法兰之间,这种不加支撑环的筛板结构有利于增加整个塔截面积的利用率。
溢流管1可由硬聚氯乙烯焊制(呈“山”字型)外包耐酸树脂玻璃布增强,再借硬聚氯乙烯套环夹焊固定于筛板上,上管端伸出筛板的高度自下而上逐渐减小。
吸收水自塔顶第一块塔板加入,在该筛板上与上升的粗氯乙烯气体接触,形成具有一定高度的泡沫层,在泡沫层内气液相进行质量传递过程,使气相中的氯化氢被水吸收为盐酸,经由溢流管借位差流入下一层筛板,在下面几块塔板上重复上述的质量传递过程。
借塔顶加入水量的调节可以控制吸收过程的气液比,控制液体在筛板上泡沫层的停留时间,以使塔底排出稀酸浓度达到20~25%。
通过视镜3可以观察到筛板上泡沫层的高度及气液湍动接触的情况,判断塔设备的工作质量。
根据经验,塔的上部几块筛板与下部筛板的开孔率可以不同,下部筛板开孔率可以大些,以适应塔的进出口气体洗量的差异。
常见的泡沫水洗塔尚有用厚度30mm的石墨板制作筛板的,但气相的阻力大些。
在小型工厂中,由于设备的散热表面积相对大些,可使塔内温度低于60℃以下,其塔身及筛板可以用硬聚氯乙烯材料加工制作。
3.4压缩机
氯乙烯压缩一般选用L型空气压缩机,为双缸、两级、双作用,水冷式空气压缩机。
主要由机身、曲柄、连杆机构,活塞、气缸及冷却器等组成,两气缸互为直角配置(见图3-4)。
压缩机由电动机通过皮带轮带动运输。
压缩机工作时,自由状态的空气经过滤器进人一级气缸,被压缩到0.18~0.77Mpa压力后排出,并进入中间冷却器冷却,然后进入二级气缸继续压缩到额定压力(0.8Mpa)后排入贮气罐。
经二级气缸排出的压缩空气,可根据用户的需要,经后冷却器冷却后输人贮气罐。
压缩机片用水冷却。
冷却水分两路分别进入中间冷却器和一、二级气缸水套。
一、二级气缸水套为串联水路,冷却水先进入二级气缸水套,再选入一级气缸水套。
两路冷却水最后汇合,由总排气管排走。
压缩机传动机构采用齿轮油泵循环润滑。
贮于机身由2润滑油,在进入油泵前先经过滤油盒,再由油泵压到滤油器,然后通过曲轴中央的油孔,到达曲柄销摩擦表面,进行润滑;
同时,部分润滑油沿连杆中心的油孔,润滑十字头销及十字头的磨擦表面。
曲轴两端的轴承利用飞溅的油进行润滑。
为降低油温,本机备有水冷式油冷却器。
图3-4.空气压缩机总布置
1-电动机;
2-空气过滤器;
3-压缩机;
4-油冷却器;
5-中间冷却器
3.5低沸塔
低沸塔又称为乙炔塔或初馏塔,是用来从粗氯乙烯中分离出乙炔和其他低沸塔馏分(包括惰性气体)的精馏塔。
在大型装置中,低沸塔多用板式塔,如泡罩塔盘,浮阀塔盘或舌形孔喷射塔盘,小型装置则以填料塔为主。
图3-5给出了板式塔的总体结构。
该塔主要由三部分组成,即塔顶冷凝器,塔节3及加热釜5。
为了便于清理换热器的列管和塔盘构件,采用法兰连接的可拆结构。
经全凝器冷凝的氯乙烯液体自上面第四块塔盘加入。
其塔顶回流液,应包括塔顶冷凝器内回流和尾气冷凝外回流部分。
低沸塔由于向下流的液体流量较大,而上升蒸汽流量较小些,而降低管截面积与塔截面积的相对比率则较大些。
生产实践证明在原有低沸塔上改装截面积较大的降液管,将使塔的生产能力大幅度的增长,低沸塔的设备材质一般选用普通低碳钢。
有的工厂曾采用不锈钢材料制作部分构件。
因塔内上升蒸汽中含微量氯化氢,导致不锈钢材料的晶间腐蚀反而不及低碳钢耐用。
3.6高沸塔
高沸塔又称为二氯乙烷塔,或精馏塔,是用来从粗氯乙烯中分离出l,1-二氯乙烷等高沸点物质的精馏塔。
在大型的装置中,高沸塔多用板式塔,如浮动喷射塔盘、浮阀塔盘或泡罩塔盘.小型装置则常用填料塔。
图3-6给出了高沸塔的总体结构。
可见设备结构与低沸点塔相类似,仅因其处理的上升蒸汽量较大,相应使塔顶冷凝器,加热釜的换热面积,以及塔身直径都比低沸点塔大些。
此外在塔身部分,根据馏分要求,当塔低残液允许含有较多氯乙烯(XW值较高),残液定期排放入Ⅲ塔蒸馏回收单体时,加料粗氯乙烯可以选择塔身较低部位,即精馏段具有较多的塔板数。
提馏段具有较少的塔板数;
当无Ⅲ塔回收单体时,塔底残液为降低氮乙烯含量(即XW较低)以减少单体损失,加料粗氯乙烯可选择在塔身较高部位,但为保证成品单体的纯度,总的塔板数也应相应增加。
四.管道安装技术要点
4.1管道除锈防腐
除锈刷漆:
首先要进行外管检查,在符合规范要求的同时必须有符合要求的质保资料,检查无误后进行报验。
之后再进行除锈刷漆,除锈等级不低于Sa2.5级,程度以见金属色为止,对于管道内部锈蚀较重的管材可采用拖曳钢丝球的手段进行除锈处理;
除锈完成后要立即刷一层防锈漆。
4.1.1管道涂漆要求
不保温的管道:
当t≤90℃时,刷环氧富锌底漆2道(干漆膜厚度75um),环氧云铁中间漆1道(干漆膜厚度100um),聚氨酯面漆3道(干漆膜厚度75um);
当200℃≥t≥90℃时管道刷无机富锌漆2道(干漆膜厚度75um),有机硅耐热漆2道(干漆膜厚度75um)。
保温的管道:
当t≤300℃时管道刷无机富锌底漆2道(干漆膜厚度75um);
当t≥450℃时管道刷铝粉有机硅耐热漆2道(干漆膜厚度75um)。
4.1.2防锈漆要求
油漆使用前要搅拌均匀,然后用稀料调配成合适的浓度,油漆过稀或过抽稠都将影响刷漆的效果;
管道两端均留出50~60mm长不刷漆,待焊接工序完成后补刷;
已经刷防锈漆的管道材料在存放过程中,要注意防潮,避免再度锈蚀。
环氧富锌底漆以环氧树脂和聚酰胺为基料双组分涂料,具有环氧树脂良好的附着力和较强的耐酸碱盐性能。
涂装温度为10-30℃,相对湿度85%以下,表面温度高于露点3℃以上稀释剂为环氧稀释剂。
对于漆膜损坏和脱落处,修复时应重新表面处理并涂刷与原来相同的外防腐涂料。
4.2管道预制
管道预制应在平台上进行,预制尺寸按修正后的管段图进行,并留有调整管段,为了保证运输和吊装顺利,管段上应贴上标示,标明材质、规格、管段号。
敞口要及时封堵,避免污染;
卷板管应在平台上预制,预制过程中必须保证两焊缝间距大于300㎜;
4.3管道切割
当管道直径<DN25时,可采用手锯或割刀切割,当管道直径≤DN150时,采用砂轮切割机进行切割,当管道直径≥DN200时,采用氧-乙炔火焰切割,但必须氧化铁清理干净,管端打磨平整,不锈钢管子采用等离子切割。
4.4.管道焊接
碳钢管道DN≤200,壁厚大于4㎜时(卷管采用电弧焊)采用氩弧焊打底,电弧焊盖面;
焊条严格按照规定进行烘烤发放(焊材选用详见表1,烘烤温度及时间详见表2)
焊接坡口的加工:
坡口可采用手提砂轮机、锉刀等进行加工,掉到管子里的焊渣要清理干净。
焊接坡口的型式:
开65°
(60°
~70°
)“V”坡口,钝边为1-2mm,对口间隙为2~3mm焊接操作:
a.焊接前点固时,根部必须焊透。
不得有焊接缺陷。
管径≤150mm点固4点,每点长度为5mm。
管径>150mm点固6点,每点长度为5mm;
b.管子组对焊口时应保持其轴线平直。
在不得以时,距焊口中心200mm处测量平直度如图1示,管径<100mm时允许偏差为1mm;
管径≥100mm时允许偏差为2mm,但全长允许偏差均不大于10mm。
万一超差时,只能用冷矫正,严禁加热矫正。
表1焊接材料选用表
序号
母材材质
焊材及规格
焊条
焊丝
1
20#
E4015φ3.2
ER50-6φ2.5
2
L245
J422φ3.2
ER-50φ2.5
3
16MnDG
J507RHφ3.2
H08Mn2S