00000毕业论文渤海油脂浸出法制取大豆油工艺报告Word格式文档下载.docx
《00000毕业论文渤海油脂浸出法制取大豆油工艺报告Word格式文档下载.docx》由会员分享,可在线阅读,更多相关《00000毕业论文渤海油脂浸出法制取大豆油工艺报告Word格式文档下载.docx(17页珍藏版)》请在冰豆网上搜索。
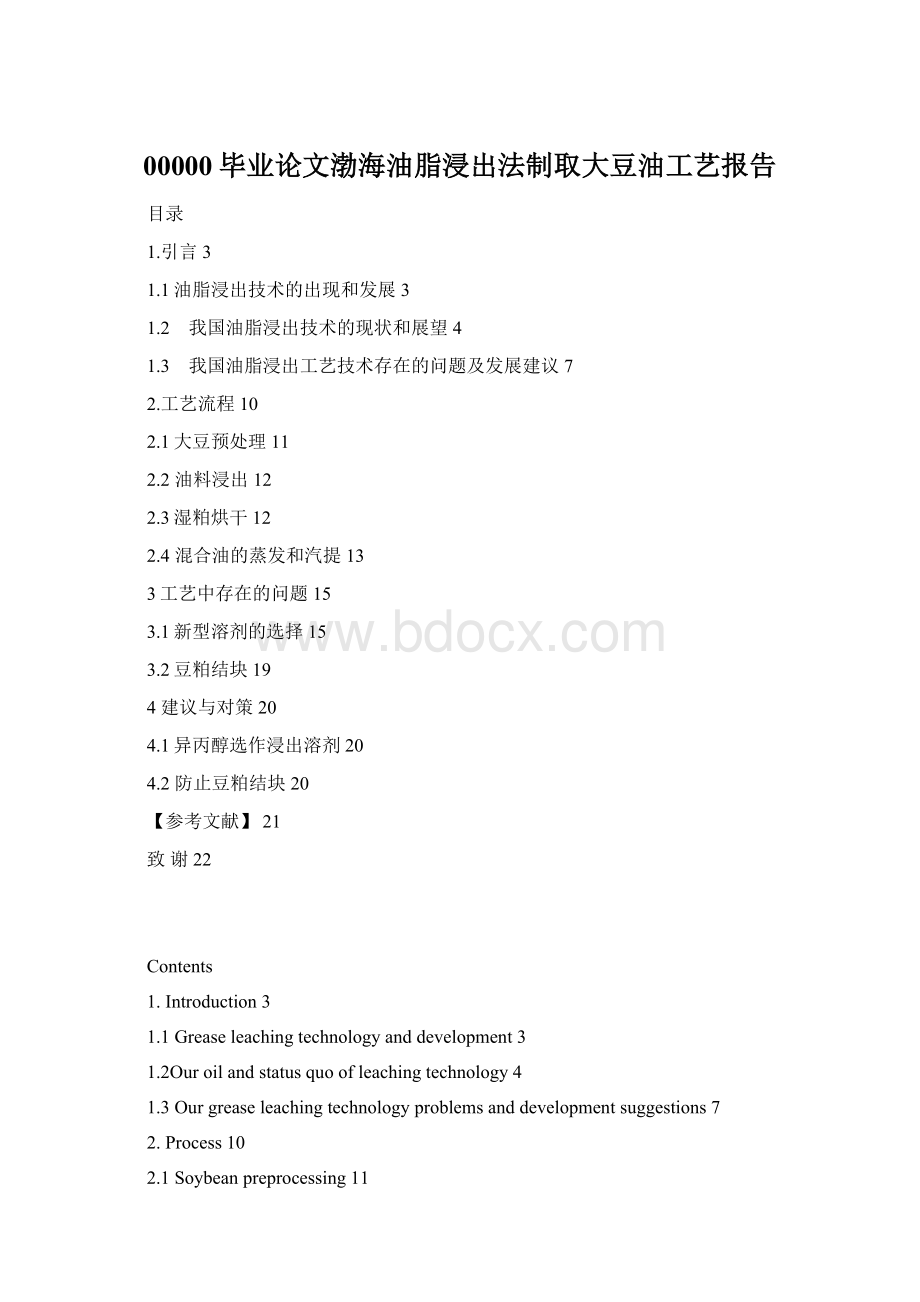
2.Process10
2.1Soybeanpreprocessing11
2.2Oilleaching12
2.3Wetmealdrying12
2.4Mixtheoilevaporationandsteam13
3.1Thenovelsolvents15
3.2Soybeanagglomerate19
4Suggestionsandcountermeasures20
4.1Theisopropylalcoholforleachingsolvent20
4.2Preventcakingmeal20
References21
Acknowledgment22
渤海油脂浸出法制取大豆油工艺报告
邱万伟
(山东农业大学食品学院,山东泰安271018)
指导教师:
乔旭光(教授)
摘要:
本文论述了浸出制油的发展历程、我国油脂浸出技术的现状以及在油脂浸出工艺技术存在的问题及发展建议。
以渤海油脂大豆油加工工艺为线,论述其工艺流程,分析了工艺中存在的普遍问题。
在新型溶剂的选择和防止豆粕结块等方面给予了一些改进措施和建议,对渤海油脂及同行业发展有一定的指导意义。
关键词:
浸出;
大豆;
加工工艺;
工艺报告
StudyonTheBohaiSeafatLtd.infusionlegalinstitutionsfetchesthesoybeanoilhandicraftreport
QiuWan-wei
(CollegeofFoodScienceandEngineering,ShandongAgriculturalUniversity,Tai’an,Shandong271018)
Supervisor:
QiaoXu-guang
Abstract:
Course,ourcountryfathavingdiscussedinfusionmakingdevelopmentofoilleachoutthemainbodyofabookaswellasthetechnologycurrentsituationleachingouttechnologyhaveproblemanddevelopingsuggestioninthefat.TakethattheBohaiSeafatsoybeanoilprocessesahandicraftastheprocessflowdiscussingthepersongleam,havecommonprobleminhavinganalysedhandicraft.Havegivenalittleimprovementmeasureandsuggestioninthefieldofnewmodelmenstruumchoosingthesoymealpackingandguardingagainstandsoon,havehadcertainguidingsignificancetotheBohaiSeafatandwithindustrydevelopment.
Keyword:
Infusion;
Soybean;
Processhandicraft;
ProcessReport
1.引言
1.1油脂浸出技术的出现和发展
1843年法国人迪斯(Diss)开始利用二硫化碳作溶剂浸出橄榄油,1856年利用溶剂浸出法在单罐浸出器内从油料中提取油脂获得专利并应用于工业生产。
1919年德国人波尔曼(Bollman)设计的第一台连续式的直立篮斗式浸出器问世。
之后,美国BlowKnox公司(1948)的平转浸出器、美国皇冠(Crown)公司的环型浸出器、比利时迪斯梅(DeSmet)公司的履带式浸出器(1945)、德国鲁奇(Lurgi)公司的框式浸出器相继应用于油脂工业。
溶剂浸出取油使世界油脂工业进入了现代化的生产阶段。
我国的浸出工业在1949年以前是十分落后的,全国仅有大连一家罐组式浸出厂(当时采用苯作溶剂)。
1955年下半年在大连油脂总厂成立的连续化浸出工艺和设备设计小组在无现成经验可借鉴的条件下,正确地选择了以平转浸出器为主体的工艺路线,并与锦州石化厂合作,选用6号溶剂作为油脂浸出溶剂,为我国油脂浸出工艺技术的发展奠定了基础。
1956年我国自行设计并建造的第一个30t/d的油脂浸出厂在吉林省蛟河投产,1959年初济宁浸出油厂成功试车投产,并首次采用自行设计的立式蒸烘机[1]。
1957年6月青岛植物油厂建成90~95t/d花生预榨、50~60t/d预榨饼罐组式浸出的预榨浸出油厂。
将4台200型榨油机,改造成28~32t/d的预榨机,用苯作溶剂,12月正式投产。
至此,我国第一套预榨-浸出生产线已诞生[2]。
20世纪60年代后期和70年代,我国油脂浸出技术得到应用和推广。
1972年召开了全国油脂浸出会议,提出大力推广浸出法制油。
80年代,油脂浸出技术被列为国家“六五”重点推广项目,将浸出法制取植物油列为40个重点推广项目之一。
由此,我国的浸出法制油得到了飞跃发展。
1983年,我国油脂浸出厂有300多个,1996年有3300个,1999年我国城镇以上的食用植物油厂有5846个,油料总加工能力达到7000万t。
1.2 我国油脂浸出技术的现状和展望
我国的油脂工业经过油脂界多年的艰苦努力,取得了长足的发展和进步。
特别是近年来,随着我国经济的高速持续发展和改革开放的深入进行,我国的油脂工业发展迅猛,油脂浸出技术呈现出又一个飞跃发展。
特别是大型外资企业的建立及国外先进技术的引进和消化吸收,更是大大加快了我国油脂浸出工艺技术的发展进程,使油脂浸出工艺技术、生产装备、产品质量以及综合经济技术指标等都达到相当高的水平,促进了中国油脂工业的现代化。
1.2.1 油脂浸出生产规模的不断扩大
近年来,我国油脂浸出建设规模呈现出不断扩大的特点。
这是因为大型化油脂工厂采用先进的工艺技术、生产设备以及自动化装置,更具有其投资的经济合理性,大型化油脂工厂有可能实现油料资源和能源的综合利用,使产品质量稳定可靠,生产成本大大降低,综合经济技术指标更具优越性。
我国至20世纪90年代中后期,浸出油厂的建设规模通常在300t/d左右。
近年,随着外资在中国新建浸出油脂工厂的数目迅速增多,所建油厂生产规模逐渐扩大,引进工艺和设备的技术水平愈加先进,为我国油脂工业的发展注入了活力,也为深入了解和消化吸收国外先进技术提供了条件,促进和带动了国内大型化油脂工厂的建设。
目前,我国1000t/d以上的浸出油厂超过60家,4000t/d以上的浸出油厂超过10家,最大的浸出油厂生产能力超过12000t/d。
1.2.2 采用更先进的油脂浸出工艺技术,加快技术更新
单靠扩大生产规模降低生产成本不是无限的,提高油脂生产的综合效益还要靠先进的工艺技术。
随着科学技术的快速发展,油脂生产理论和工艺技术也在不断发展和完善,新技术和新设备在油脂生产中得到广泛应用。
如油料预处理过程不再只是重视料坯结构性能对取油效果的影响,同时更重视对油料中各种成分的影响,以及由此造成的对毛油品质、精炼效果、最终产品质量的影响。
为此,油料脱皮、料坯膨化、料坯湿热处理等预处理工艺技术被人们接受并应用于生产。
油脂浸出生产则更重视降低粕残油、溶剂损耗、能量消耗及提高浸出毛油质量。
为此,混合油负压蒸发工艺,湿粕脱溶中的预脱、自蒸、蒸脱、干燥、冷却工艺,更科学合理的溶剂蒸汽冷凝回收工艺,尾气中溶剂的矿物油吸附回收工艺,乏汽的余热利用等技术得到深入细致的研究,并应用于生产中取得了显著的效果。
油脂精炼则在追求更高的精炼得率、更好的产品质量(好的感官指标和质量稳定性)和更低的辅料消耗方面取得成效。
此外,自动化及计算机的应用为保证油脂生产在最佳生产条件下连续稳定运行,提高生产管理效果,降低生产成本上起到了重要作用。
除常规的油脂生产技术之外,油脂超临界流体萃取技术、超滤和反渗透技术等也有望在油脂工业生产上最终获得应用。
以酶工程、微生物工程、蛋白质工程为代表的生物工程技术也已经在油脂生产及功能性油脂产品的开发中获得成功。
油脂工业正在不断地积极吸纳和分享着技术的进步,为其自身的发展创造新的生机。
1.2.3 装备更精良的生产设备
具备优良的工艺性能和机械性能的生产设备是保证生产连续高效稳定运行的前提条件,对提高产品质量也起着重要作用。
国外的油脂生产企业和国内的外资企业都十分重视生产设备的装备水平对提高油脂生产综合效果的作用,因此其生产设备的装备水平通常都很高。
近年,国内的许多油脂生产企业也正在改变原有的为节省投资而轻视生产设备质量的观念,在设备的装备水平方面显示出很大的进步,油脂浸出油厂正在逐渐摆脱传统的生产装备简陋、粗糙的局面,向现代化的生产装备水平方向迈进。
当然,这得益于国内油脂机械制造业的发展和进步;
得益于对国外引进设备的消化吸收和应用。
同时,大型化油脂工厂的建设也促进和带动了大型生产设备、输送设备及其他配套设备的研制和发展。
1.2.4 提高产品和副产品的质量,增加产品品种
传统的油脂生产以获取油脂为主要目的,而当今油脂工业的产品和副产品种类繁多,产品质量优良。
色拉油、高级烹调油、风味调和油、营养调和油、浓香花生油、小磨芝麻香油、调味油、人造奶油、起酥油等多种油脂产品,可以满足不同人群、不同用途的消费需求。
今后,人们对油脂产品不仅在色泽、味觉、嗅觉等感官方面,而且在营养、人体机能调节方面会提出更高的要求。
各种功能性油脂和食品专用油脂的开发和生产将受到重视。
根据油料饼粕的用途不同,可以在油脂生产过程中通过调节工艺条件生产多种饼粕产品。
如不同蛋白质含量的饲用豆粕,适用于提取食用油料蛋白的低温豆粕。
利用低温豆粕生产脱脂大豆粉、低脂大豆粉、大豆浓缩蛋白、大豆分离蛋白、大豆组织蛋白和功能性大豆蛋白等。
此外,如菜籽蛋白、花生蛋白等其他油料蛋白也将得到开发和利用。
对米糠、玉米胚芽、油茶籽、红花籽等小宗油料资源的开发利用也有很大潜力。
随着油脂生产技术的进一步提高,将会有更多的新产品问世,为油脂企业创造更高的经济效益。
1.2.5 关注油料的综合利用和精深加工,提高生产附加值
在植物油料中含有多种微量成分和生物活性成分,在油脂生产中或之后将这些成分提取出来,可以大大提高其利用价值,提高油脂生产的附加值。
如从豆粕、豆皮、油脚、脱臭馏出物中提取磷脂、脂肪酸、维生素E、异黄酮、皂甙、低聚糖等;
从棉籽或棉籽粕中提取棉酚等。
在油脂生产工艺和技术条件的选取上就要考虑其副产物的提取和利用,加大对副产物综合利用的开发力度,也将成为油脂工业发展的一项内容。
1.2.6 加强环保意识,对油脂生产废弃物进行有效控制和处理
植物油脂生产与其他工业生产一样,总会伴随着生产过程产生一些废弃物,尽管这些废弃物不会像某些化学工业的废弃物那样对环境造成严重的污染,但仍对环境保护形成不良的影响和潜在的危害。
随着我国油脂工业逐步向高标准的新型工业化产业发展,对油脂生产废弃物的有效控制和处理,也将成为油脂生产的一项重要内容。
对油脂生产中废水、废气、固体废物的控制和处理,在国内小型油厂是一个薄弱的环节,几乎没有有效的处理装置。
新建的大型油厂基本都配置了有效的废物处理设施,然而大多是对废水处理,对其他废弃物的控制和处理还显欠缺。
随着环境保护法规实施力度的加大,所有油脂生产企业都必须积极主动地在生产过程中控制废物的产生,减少废物排放量及废物的污染物浓度。
之后,采用完善的废物处理工艺技术,有效地对其进行处理,使其达到国家要求的废物排放标准,甚至实现生产废物的零排放。
因此,研究和应用排污少的油脂生产工艺,改进浸出溶剂质量或寻找新型溶剂,选用安全的油脂脱臭高温热媒介质等等,都是油脂生产中环境保护需要考虑的问题。
1.3 我国油脂浸出工艺技术存在的问题及发展建议
1.3.1 浸出油厂的建设规模及布局不均衡
尽管近年来我国浸出油厂的建设规模趋向大型化发展,但仍然有不少小型浸出油厂在建设,这些小型浸出油厂一般技术水平较低、能源消耗高、产品质量不稳定、缺乏三废处理装置,必须加强管理并对其进行限制。
大型浸出油厂集中建设在沿海地区及中东部,内地及西部地区大型浸出油厂很少。
外资企业控制的大型浸出油厂主要由外资投资和控股,国有控股的大型浸出油厂所占比例减少,不利于国家宏观调控和突发事件时的市场应急供应。
因此,应控制和引导浸出油厂合理的区域布局和建设规模。
1.3.2 深入研究油脂浸出理论及油脂浸出新工艺技术
近年来,在我国的外资油脂生产企业新引进的油脂浸出工艺技术达到了国际先进水平。
虽然国内油脂工程设计人员在努力对其技术进行消化吸收,但由于受到外资企业对国内油脂技术人员交流保密条件的限制,影响了国外油脂浸出新技术在国内油脂工程上的及时应用。
另一方面,我国的一些油脂浸出厂或工程技术人员对油脂浸出新技术发展、研究和应用的重视程度不够,使得不少新建浸出油厂的技术水平仍然与国外先进水平存在一定差距。
应该着重研究、应用推广的油脂浸出新技术应包括:
油料生坯膨化浸出;
混合油全负压蒸发;
矿物油尾气回收;
高效节能的湿粕蒸脱工艺;
湿粕低温脱溶工艺技术;
高效可靠的混合油净化工艺技术;
混合油精炼工艺技术;
大型浸出车间(防爆超高)的现代防火防爆消防新技术(水喷淋系统、消火用蒸汽、强制空气循环系统)和安全管理;
油脂浸出生产自动控制技术;
窄馏程低燃爆性安全程度高的浸出溶剂的应用;
混合溶剂浸出工艺等。
1.3.3 注重对多种油料油脂浸出工艺技术的研究应用
近年来由于大豆加工量的增加,对大豆油脂浸出工艺研究较多,并且日趋成熟,而对其他油料的油脂浸出工艺技术的研究相对缺乏和重视不够。
譬如,油菜籽、棉籽、米糠膨化浸出工艺,玉米胚芽、红花籽、葵花籽浸出工艺技术,以及小油种、特殊油料的油脂浸出技术。
1.3.4 研究适应于油料综合加工利用的油脂浸出工艺技术
油脂浸出工艺技术应与油料综合加工利用紧密联系起来,满足油料综合利用的工艺要求。
譬如,大豆油脂生产工艺技术应与大豆磷脂生产、异黄酮生产联系起来,为保证大豆磷脂的品质,应在大豆预处理及浸出时就采用相应的工艺技术。
如在大豆预处理工艺中采用脱皮、膨化工艺技术,在浸出生产中采用严格的混合油粕末分离、混合油负压蒸发工艺,而这与料坯结构、浸出器结构、混合油含粕末量以及高效混合油净化装置的应用等有关。
1.3.5 研究开发能够快速检测和指导生产的在线检化验仪器
浸出毛油残溶检测方法和仪器。
虽然新的国标中规定了浸出毛油残溶指标,但由于大多数浸出油厂没有配备气相色谱等检测仪器,无法完成浸出毛油残溶等指标的测定,因此此项指标的检测和控制难以落到实处。
而外资企业已普遍采用根据浸出毛油闪点判定浸出毛油残溶的方法,浸出毛油闪点测定仪对毛油残溶的测定快捷、投资少、便于操作。
因此,应研究开发并推广应用浸出毛油闪点测定仪。
油脂磷脂含量测定。
HACH2100AN浊度仪快速测定油脂含磷脂量,此法检测快速、便于操作。
1.3.6 修订和完善相关的油脂浸出标准
随着油脂浸出技术的发展,油脂浸出生产技术指标以及产品质量有了很大提高,但现行的国家标准和行业规范却没有及时修订和完善。
例如,在现行的大豆成品粕国家标准中,某些指标不尽合理和空缺,如大豆粕尿素酶指标没有下限值,没有对现行优质大豆粕贸易中的某些指标作出要求,如大豆粕蛋白质KOH溶解度、纤维素含量、颗粒度等。
随着浸出油厂向大规模的发展,原有的浸出油厂设计规范与安全防火标准,已不能适应当前油脂浸出工业发展的需要,大型化油脂浸出车间建筑消防安全超高成了大型化油脂加工厂在设计、建设、验收等工作中的一个棘手问题,原有的设计规范在许多方面需要进行修订和增补新的内容,标准升级的工作势在必行。
如美国全美火灾预防协会(NFPA)制定的“溶剂浸出油厂防火规范”几年就要修订一次,而我国自1992年后至今没有修订。
随着油脂浸出工艺技术的改进和发展,原有的“油脂浸出生产操作规程”许多内容也已不适合当前的发展形势,需要修订。
1.3.7 大型先进的浸出设备的研究开发
研究开发大型浸出生产设备,提高设备的机械性能和工艺性能,提高其制作精良程度,以保证高的设备安全稳定运行率,提高浸出生产的整体效果。
如大豆调质干燥塔,大型油料膨化机,生坯和膨化料冷却干燥机,大型浸出器,大型湿粕蒸脱机,湿粕低温脱溶机等。
1.3.8 浸出生产自动化
随着浸出油厂生产规模大型化,在浸出生产中采用计算机对其过程进行检测与控制,实现浸出工艺参数最优化操作,对保持生产高效稳定运行、节能降耗、安全生产及提高工艺效果都具有很现实的意义,因此应对浸出生产中的自控系统硬件和软件进行开发并促进其在生产中推广应用。
近年来,浸出技术的自动化进程飞速发展,国产自动化元件及软件设施基本上能满足浸出的工业化生产,国内的外资企业基本都采用了自控系统,但国内大多数浸出油厂在建设时对自控的重要性认识不足或不愿对此进行过多投资,因此浸出油厂的自动控制普及应用率不高。
自动化控制需要进一步解决的问题:
固体物料流量(料坯预榨饼等)的计量与控制元件的研制;
物料组分(水分)残留物(残油、溶剂)以及混合油浓度等在线检测装置的进一步完善与研制;
生产过程实现智能化自动调节;
安全报警的选择性与准确可靠性研究;
新型计算机硬件的适应性问题;
工厂的工艺设备的配套;
专业人员(管理、操作、维修)的培训。
1.3.9 油脂浸出生产中环境保护
应注重油脂生产中废气、废水排放的控制及处理,对排空尾气量及尾气含溶剂气体量、废水排放量及废水含污染物量、以及其他废物排放进行控制。
在工艺设计时应考虑减少废水形成及排放问题,采用合理的生产工艺控制和减少废水的产生,并控制其含污染物的量,采用废水循环利用技术,力争少排或不排废水,直至实现废水零排放;
规范或强制油脂浸出生产中的废水处理系统的建设。
例如,先进的浸出工艺中废水排放量大约30kg/t料,传统工艺中废水排放量约150kg/t料,而落后工艺中废水排放量高达250kg/t料。
这无疑是增加了废水处理的负荷和生产成本。
若不进行废水处理,将对环境造成很大程度的危害。
废气还没有引起足够的重视,应在工艺设计和选择时,考虑减少和控制排气量。
譬如,国外先进浸出工艺生产中,经吸收塔排放的废气量不足1m3/t料,而我国浸出油厂的废气排放量约为2~3m3/t料,即使经过矿物油尾气回收,随排空尾气损耗的溶剂量必定增加。
而要减少废气排放量就需要在浸出生产的多环节进行控制。
譬如,进料的密封性、系统的负压大小、系统的密封性、直接蒸汽中含空气量等。
1.3.10 降低浸出生产的能量消耗
油脂浸出生产中的能量消耗是影响生产成本的重要因素,必须深入研究影响能量消耗的因素,在工艺设计、设备质量等方面采取措施,降低生产中的能量消耗。
应对蒸汽消耗、电力消耗、溶剂消耗等应有指导指标。
推广能量消耗低的工艺技术和设备,如湿粕蒸脱机二次蒸汽的余热利用,油-油热交换,具有自蒸作用的DTDC蒸脱机、低电耗的卧式软化锅等。
2.工艺流程
浸出制油就是应用萃取的原理,选择某种能够溶解油脂的有机溶剂,经过对油料的浸泡、喷淋,把油脂从油料中提取出来的一种方法。
其一般包括油料预处理、油料浸出、湿粕烘干、混合油处理、溶剂冷凝与回收主要五个工序。
2.1大豆预处理
图一大豆预处理工艺流程图
油料预处理即在油料取油之前对油料进行的清理、破碎、脱皮、软化、压胚、膨化等一系列的处理。
其目的是除去杂质并使其具有一定的结构,以符合制油工艺的要求。
大豆经斗提G002进入预处理的物料缓存箱F003,在自动计量称G101的控制下连续的进料。
通过计量称控制进料量并将大豆的数量累计在控制盘上。
已计量的大豆由斗提G102通过分配器进入三台清理筛G104,分离出大杂质和细碎杂质,清理的大豆经F105暂存箱进入磁选机将铁质物质分离出来,然后进入三台并列安装的破碎机G106,每粒大豆被破碎成4-8片,因为整个大豆不能通过压胚机而导致进料中断。
通过刮板G107和斗提G109,破碎的豆粒进入软化锅E108,经7bar间接汽被加热到55℃,经刮板G120和斗提G116进入8台并联安装的压胚机G111,压成0.25mm-0.35mm厚的胚片。
若胚片厚度超出这个范围,经浸出后,豆粕残油将会升高。
胚片通过刮板G112和G130斗提进入绞龙G131后进入G132膨化机膨化。
通过干燥、冷却箱E133干燥冷却后经刮板进入浸出车间。
2.2油料浸出
浸出器进料装置为一个圆筒形结构,作用其中的的豆片使浸出器D201中的溶剂气与外界隔离。
浸出器内有一条带有无底料斗的带式料斗机构—料格。
料斗通过6条喂料绞龙分配进料,豆片先进入到上层栅板的料格内,当料格运转到浸出器末端时,物料从上层落入下层料格。
在此过程中,豆片被溶剂萃取其中的油脂,当豆粕行至底层栅板末端时,脱溶粕落入出料斗,经刮板G261和旋转阀G605输送到预蒸脱机E606。
2.3湿粕烘干
图二湿粕烘干流程图
离开浸出器D201的脱脂豆粕含有大约25—28%的溶剂。
为脱去豆粕中的溶剂,通过刮板G261和旋转阀G605将其送入预蒸脱机E606。
在E606中装有一个用蒸汽加热的旋转管,通过升高温度到大约64℃,豆粕中的溶剂被部分的蒸发,蒸发的溶剂输送到蒸脱机第一层。
经预脱溶的豆粕,仍含有15%左右的溶剂,通过刮板G262输送到蒸脱机D652。
脱溶蒸烘部分有五层,每层装有搅拌装置以在脱溶期间保持豆粕移动。
在五层脱溶蒸烘后,通过直接蒸汽,豆粕残留的正己烷大约0.04%。
在干燥层,干燥风机G661将通过加热器E662加热的空气吹进底部夹层,后通过干燥层底部的孔进入干燥部分,经D652干燥后豆粕含水量大约13—14%。
在冷却层豆粕冷却到大约40℃,水分含量减少到12%。
表1浸出油料的成品粕质量标准
指标
食用级
饲料级(一级)
水分%
<
=12.0
=13.0
粗蛋白%
>
49.0
=44.0
粗纤维素%
=5.0
=5.0
粗灰分%
=6.5
6.0
残溶量%
0.07
2.4混合油的蒸发和汽提
2.4.1工艺过程:
混合油过滤→混合油贮罐→第一蒸发器→第二蒸发器→汽提塔→浸出毛油;
从浸出器泵出的混合油(油脂与溶剂组成的溶液),须经处理使油脂与溶剂分离。
分离方法是利用油脂与溶剂的沸点不同,首先将混合油加热蒸发,使绝大部分溶剂汽化而与油脂分离。
然后,再利用油脂与溶剂挥发性的不同,将浓混合油进行水蒸气蒸馏(即汽提