不锈钢铸造工艺环节简述如下.docx
《不锈钢铸造工艺环节简述如下.docx》由会员分享,可在线阅读,更多相关《不锈钢铸造工艺环节简述如下.docx(16页珍藏版)》请在冰豆网上搜索。
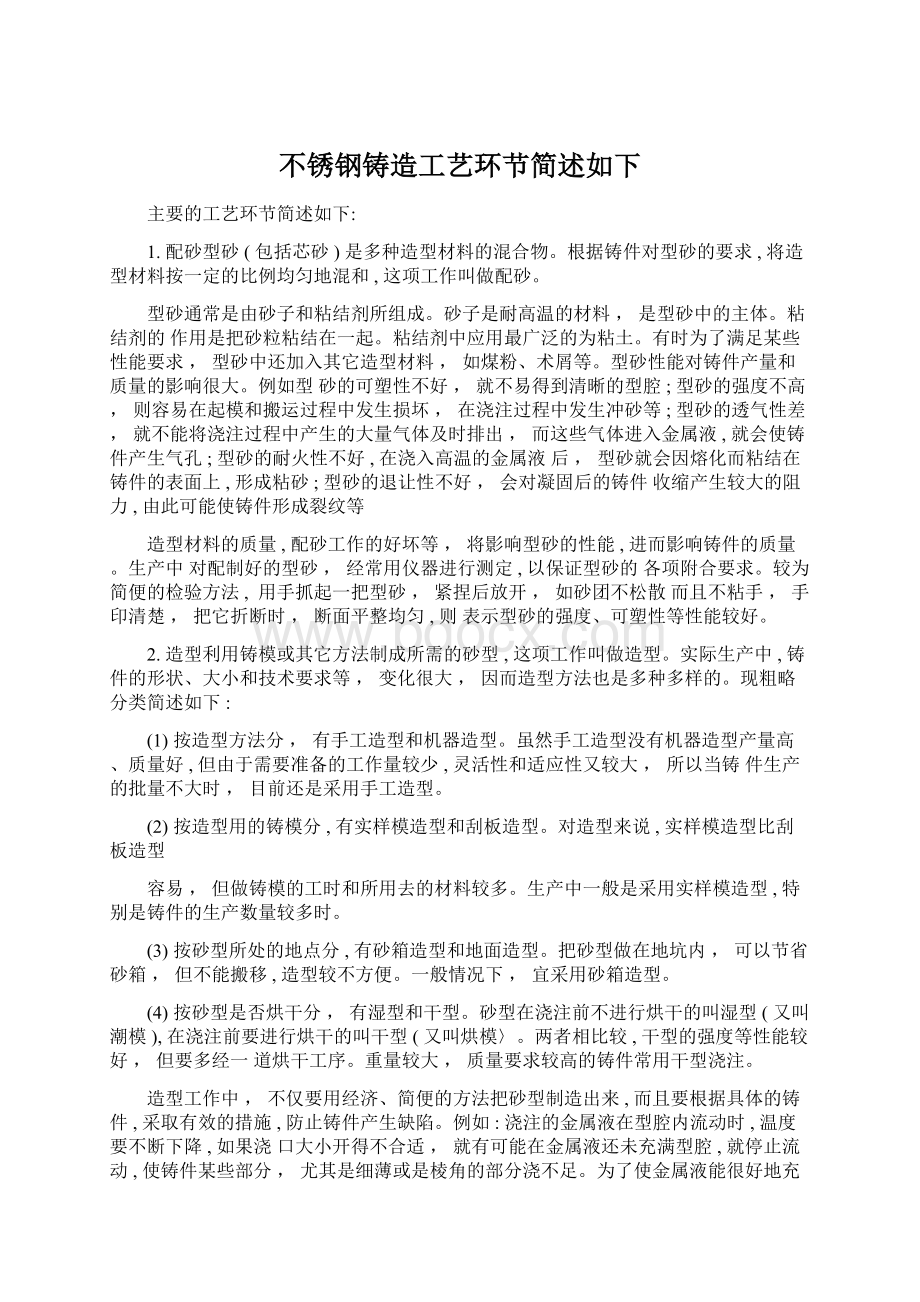
不锈钢铸造工艺环节简述如下
主要的工艺环节简述如下:
1.配砂型砂(包括芯砂)是多种造型材料的混合物。
根据铸件对型砂的要求,将造型材料按一定的比例均匀地混和,这项工作叫做配砂。
型砂通常是由砂子和粘结剂所组成。
砂子是耐高温的材料,是型砂中的主体。
粘结剂的作用是把砂粒粘结在一起。
粘结剂中应用最广泛的为粘土。
有时为了满足某些性能要求,型砂中还加入其它造型材料,如煤粉、术屑等。
型砂性能对铸件产量和质量的影响很大。
例如型砂的可塑性不好,就不易得到清晰的型腔;型砂的强度不高,则容易在起模和搬运过程中发生损坏,在浇注过程中发生冲砂等;型砂的透气性差,就不能将浇注过程中产生的大量气体及时排出,而这些气体进入金属液,就会使铸件产生气孔;型砂的耐火性不好,在浇入高温的金属液后,型砂就会因熔化而粘结在铸件的表面上,形成粘砂;型砂的退让性不好,会对凝固后的铸件收缩产生较大的阻力,由此可能使铸件形成裂纹等
造型材料的质量,配砂工作的好坏等,将影响型砂的性能,进而影响铸件的质量。
生产中对配制好的型砂,经常用仪器进行测定,以保证型砂的各项附合要求。
较为简便的检验方法, 用手抓起一把型砂,紧捏后放开,如砂团不松散而且不粘手,手印清楚,把它折断时,断面平整均匀,则表示型砂的强度、可塑性等性能较好。
2.造型利用铸模或其它方法制成所需的砂型,这项工作叫做造型。
实际生产中,铸件的形状、大小和技术要求等,变化很大,因而造型方法也是多种多样的。
现粗略分类简述如下:
(1)按造型方法分,有手工造型和机器造型。
虽然手工造型没有机器造型产量高、质量好,但由于需要准备的工作量较少,灵活性和适应性又较大,所以当铸件生产的批量不大时,目前还是采用手工造型。
(2)按造型用的铸模分,有实样模造型和刮板造型。
对造型来说,实样模造型比刮板造型
容易,但做铸模的工时和所用去的材料较多。
生产中一般是采用实样模造型,特别是铸件的生产数量较多时。
(3)按砂型所处的地点分,有砂箱造型和地面造型。
把砂型做在地坑内,可以节省砂箱,但不能搬移,造型较不方便。
一般情况下,宜采用砂箱造型。
(4)按砂型是否烘干分,有湿型和干型。
砂型在浇注前不进行烘干的叫湿型(又叫潮模),在浇注前要进行烘干的叫干型(又叫烘模〉。
两者相比较,干型的强度等性能较好,但要多经一道烘干工序。
重量较大,质量要求较高的铸件常用干型浇注。
造型工作中,不仅要用经济、简便的方法把砂型制造出来,而且要根据具体的铸件,采取有效的措施,防止铸件产生缺陷。
例如:
浇注的金属液在型腔内流动时,温度要不断下降,如果浇口大小开得不合适,就有可能在金属液还未充满型腔,就停止流动,使铸件某些部分,尤其是细薄或是棱角的部分浇不足。
为了使金属液能很好地充满型腔,对于薄壁的铸件,造型时,浇口就要开得大些。
还要指出的,各种金属液的流动性是不相同的,例如灰铸铁比铸钢的流动性要好得多,所以灰铸铁可以浇出壁厚更薄的铸件。
金属液从高温冷却到凝固,再冷却到室温,在体积或尺寸方面都要缩小,也就是说具有收缩性。
收缩性大的铸件,当表层凝固而内部金属液继续收缩时,往往会在铸件厚大的部分形成孔洞,即所谓缩孔,为防止铸件产生缩孔,造型时要考虑补缩的问题,最常用的方法就是设置冒口。
当铸件凝固后继续收缩时,如果受到砂型和泥芯的阻碍,就可能产生裂纹。
为此,造型时常需要采用一定的防裂措施。
各种金属的收缩性是不相同的,例如:
灰铸铁的收缩性比铸钢小得多,是常用金属中最小的一种,所以灰铸铁件比较不容易产生缩孔、裂纹缺陷。
3.熔炼将固态的金属炉料熔成具有一定成分和温度的液态合金,这项工作叫做熔炼。
铸工车间中,熔炼金属的炉子的类型很多,如冲天炉、电炉、增锅炉等。
熔炼铸铁的炉子,最广泛应用的为冲天炉。
冲天炉的炉壁是用耐火材料制成,外面围以钢板炉壳。
金属炉料和焦炭等按一定的比例分批从加料口加入炉中。
从鼓风机来的空气,经过炉身下部的风箱和进风口进入炉中。
焦炭燃烧时放出的热量使金属炉料熔化。
熔化了的铁水贮在炉底或前炉,待积到一定数量时,凿去出铁口内的泥塞,铁水便流出,通过出铁槽流入铁水包中。
熔炼工作中,要控制好金属浓的成分和温度,否则会产生成批的废品。
4.浇注以合适的温度和速度,将符合要求的金属液浇入砂型中,这项工作叫做浇注。
浇注是通过浇包进行的。
浇注的时候,浇包要靠近浇口,不要太高,否则金属液会从浇口溅出来;要使浇口保持注满状态,以免熔渣(垃圾)进久型中,使铸件产生夹渣缺陷。
浇注前,要穿戴好防护用具,和金属液接触的工具要预热,以免引起金属液飞溅时伤人。
5.清理清除铸件上的浇冒口和表面粘砂等,这项工你叫做清理。
铸铁件的浇冒口可用敲断方法去除,铸钢件等常用气割方法去除。
铸件表面清理工作可用滚筒、抛丸等设备来完成。
在缺乏设备或是铸件上难以清理的部位,可用手锤、凿子和钢丝刷等来进行。
锤击时应注意锤打的方向和力的大小,以兔损坏铸件。
用粘土粘结砂作造型材料生产铸件,是历史悠久的工艺方法,也是应用范围最广的工艺方法。
说起历史悠久,可追溯到几千年以前;论其应用范围,则可说世界各地无一处不用。
值得注意的是,在各种化学粘结砂蓬勃发展的今天,粘土湿型砂仍是最重要的造型材料,其适用范围之广,耗用量之大,是任何其他造型材料都不能与之比拟的。
据报道,美国钢铁铸件中,用粘土湿型砂制造的占80%以上;日本钢铁铸件中,用粘土湿型砂制造的占73%以上。
适应造型条件的能力极强,也是粘土湿型砂的一大特点。
1890年震压式造型机问世,长期用于手工造型条件的粘土湿型砂,用于机器造型极为成功,并为此后造型作业的机械化、自动化奠定了基础。
近代的高压造型、射压造型、气冲造型、静压造型及无震击真空加压造型等新工艺,也都是以使用粘土湿型砂为前提的。
各种新工艺的实施,使粘土湿型砂在铸造生产中的地位更加重要,也使粘土湿型砂面临许多新的问题,促使我们对粘土湿型砂的研究不断加强、认识不断深化。
现今,随着科学技术的速发展,各产业部门对铸件的需求不断增长,同时,对铸件品质的要求也越来越高。
现代的铸造厂,造型设备的生产率已提高到前所未有的水平,如果不能使型砂的性能充分适应具体生产条件,或不能有效的控制其稳定、一致,则不用多久就可能将铸造厂埋葬于废品之中。
随着科学技术的发展,目前采用粘土湿型砂的铸造厂,一般都适合其具体条件的砂处理系统,其中包括:
旧砂的处理、新砂及辅助材料的加入、型砂的混制和型砂性能的监控。
粘土湿砂系统中,有许多不断改变的因素。
如某一种或几种关键性能不能保持在控制范围之内,生产中就可能出现问题。
一个有效的砂处理系统,应能监控型砂的性能,如有问题,应能及时加以改正。
由于各铸造厂砂处理系统安排不同,选用的设备也不一样,要想拟定一套通用的控制办法是做不到的。
这里,打算提出一些目前已被广泛认同的控制要点。
各铸造厂认真地理解了这些要点之后,可根据自己的具体条件确定可行的控制办法。
而且,还要随着技术的进步和工厂的实际能力(包括人员和资金)不断改进对型砂系统的控制。
一.旧砂的处理
用粘土湿型砂造型,浇注以后,除贴近铸件的部分型砂中活性膨润土受热失效成为死粘土外,大部分型砂可以回收使用。
这是粘土湿型砂的主要优点之一。
配制粘土湿型砂时,旧砂用量一般都在90%以上,如果对旧砂的处理不当,无论怎样加强混砂,无论添加什麽辅助材料,都不可得到好的型砂。
所以,对旧砂进行有效的处理,是保证型砂质量的前提。
1.旧砂温度的控制
热砂问题,已被公认为粘土湿型砂铸造必须面对的最大问题。
型砂温度太高,铸件容易产生夹砂、表面粗糙、冲砂、气孔等缺陷。
热砂对铸件质量的负面影响,主要由于以下几个方面:
·由于热砂使水分蒸发,混砂时无论怎样注意,也难以控制型砂的性能;
·将热型砂送往造型机的过程中,由于水份损失,型砂性能改变,造型时实际上用的型砂,其性能与混砂时控制的性能差别很大;
·造型时,热型砂的水分容易在模样表面上凝结,型砂粘模;
·合型后,热砂的水分蒸发,凝结在冷的芯子上,会使芯子的强度降低,铸件也易于产生气孔;
·如果旧砂要贮存在砂斗中备用,则热砂容易粘附在砂斗壁上。
严重时,砂斗四周堵满了型砂,只剩中间一个孔洞,使系统中的型砂只有一部分周期使用,这部分型砂周转快、温度又会进一步提高,使热砂问题更加严重。
多高温度的砂算是热砂?
判断热砂的温度界限,是看其是否使混砂、造型及铸件质量方面出现问题。
对此,许多研究者从个方面进行了研究;有人研究了型砂温度对其性能稳定性的影响;有人研究了温度对膨润土-水系统流变性的影响;有人研究了型砂温度与铸件质量的关系。
各方面的研究,得到了一致的结论,即:
为保证型砂的性能稳定,温度应保持在50℃以下。
使型砂冷却,最有效的办法是加水,但是,简单的加水,效果是很差的。
一定要吹入大量空气使水分蒸发,才能有效地冷却。
以下,给出一个简略的计算比较:
型砂的比热大致是:
9.22×102J/kg·℃,
水的比热是:
4.19×103J/kg·℃,
水的蒸发热是:
2.26×106J/kg,
1吨砂中加20℃的水10kg(加水1%),使其温度升到50℃,所能带走的热量为4.19×103
×10×30,即12.57×105J。
1吨砂温度降低1℃,需散热9.22×102×1000J,即9.22×105J。
所以,在旧砂中加水1%,只能使温度降低24.5℃。
使1吨砂中的水分蒸发1%(10kg),能带走的热量为2.26×107J,却可使砂温降低24.5℃。
以上的分析表明:
简单地向皮带机上加水或向砂堆洒水,冷却效果是很差的。
即使加水后向砂表面吹风,也不能有多大的改善。
加水后,要使水在型砂中分散均匀,然后向松散的砂吹风,使水分迅速蒸发,同时将蒸汽排除。
目前,型砂冷却装置的品种、规格很多,主要有冷却滚筒、双盘冷却器和冷却沸腾床等,都是利用水分蒸发冷却型沙。
其中,冷却沸腾床效果较好。
2.旧砂的水分控制
几乎所有的铸造厂都检查和控制混成砂的水分,但是,对于严格控制旧砂水分的重要性,很多铸造厂的领导和技术人员还缺乏足够的认识。
进入混砂的旧砂水分太低,对混砂质量的影响可能并不亚于砂温过高。
试验研究和经验都已证明,加水润湿干膨润土比润滑湿膨润土难得多。
型砂中的膨润土和水,并非简单的混在一起就行,要对其加搓揉,使之成为可塑状态。
这就像用陶土和水制陶器一样,将水和土和一和,是松散的,没有粘接能力;经过搓揉和摔打,使每粒土都充分吸收了水分,就成为塑性状态,才可以成形,制成陶器毛坯。
铸型浇注以后,由于热金属的影响,很多砂粒表面上的土-水粘结膜都脱水干燥了,加水使其吸水恢复塑性是很不容易的。
旧砂的水分较低,在混砂机中加水混碾使之达到要求性能所需要的时间就越长。
由于生产中混砂的时间是有限的,旧砂的水分越低,混成砂的综合质量就越差。
目前,各国铸造工作者已有了这样一种共识:
进入混砂机的旧砂,水分只能比混成砂略低一点。
较好的做法是:
在旧砂冷却过程中充分加水冷却后所含的水分略低于混成砂。
这样,从砂冷却到进入混砂机还有一段相当长的时间,水可以充分润湿旧砂砂粒表面上的膨润土。
更好的做法是:
在系统中设混砂机对旧砂进行预混,冷却后的旧砂在预混混砂机中加水进行预混,以改善旧砂中膨润土和水的混合状态。
国外,有的铸造