LF精炼炉招标技术要求Word格式文档下载.docx
《LF精炼炉招标技术要求Word格式文档下载.docx》由会员分享,可在线阅读,更多相关《LF精炼炉招标技术要求Word格式文档下载.docx(40页珍藏版)》请在冰豆网上搜索。
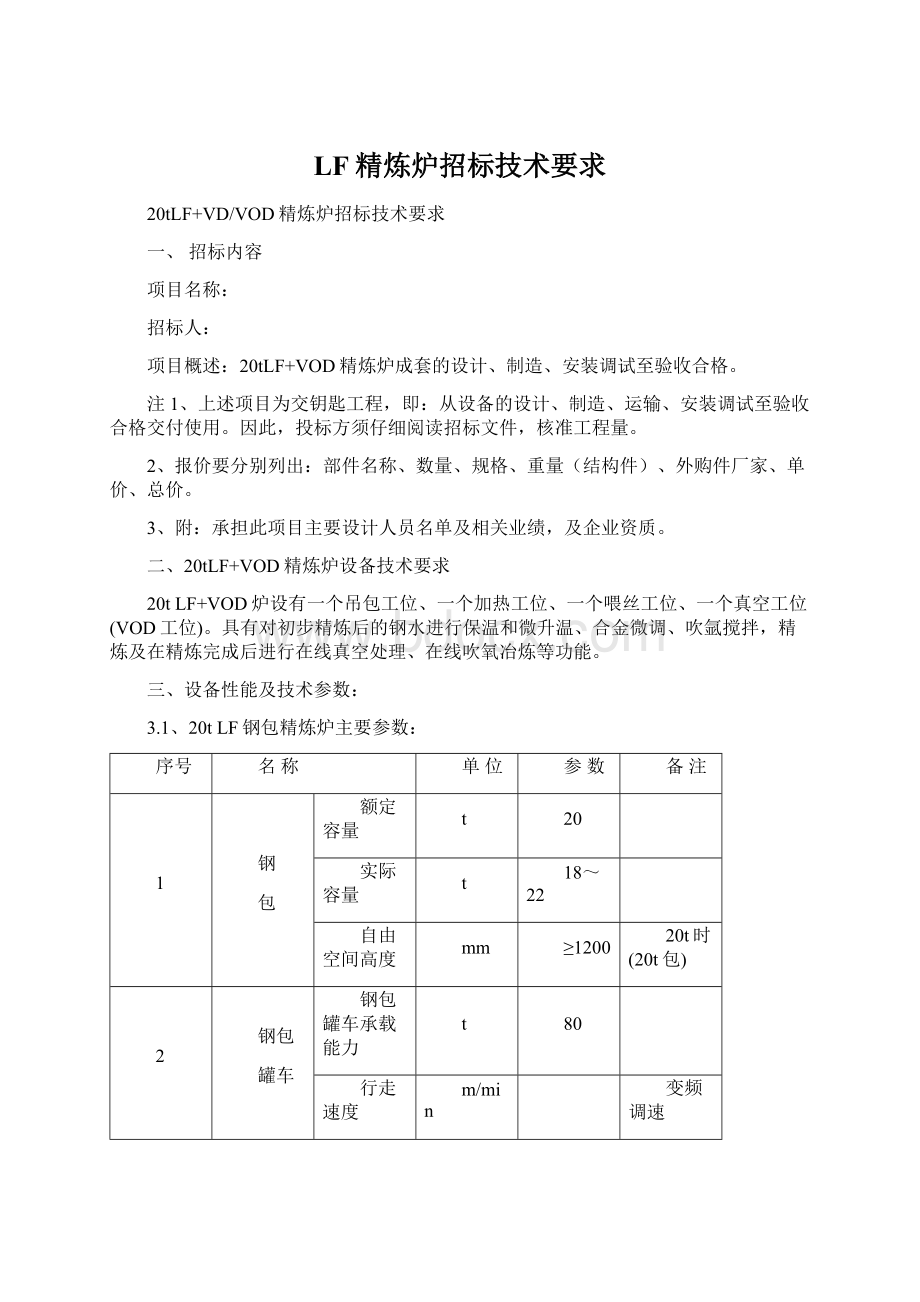
定位精度
±
10
3
电
极
升
降
机
构
电极直径
Φ300
电极分布园直径
投标方详细核定
电极升降最大行程
投标时写明
电极升降速度(自动)
电极升降速度(手动)
钢水升温速度
℃/min
≥4.5
20t钢水
4
炉盖
升降行程
升降速度
mm/s
5
液压
工作压力
MPa
工作介质
脂肪酸脂
6
短
网
阻抗
mΩ
≤2.46
三相不平衡系数
%
≤4
7
氩
气
0.3~0.8
事故1.6MPa
流量要求
NL/min
10~300
8
冷却水系统
闭环0.5~0.6
开环0.3~0.4
进水温度
℃
≤35
回水温度
≤50
冷却水耗量
M3/h
9
气动
0.45
耗量
L/min
200
干燥无油
变
压
器
kVA
4000
过负荷能力20%
一次电压
kV
35
二次电压
V
有载调压
二次端子出线方式
A
短网侧出,内三角形
冷却方式
OFWF强油水冷
二次额定电流
KA
工艺流程图
3.2、机械技术要求:
3.2.1钢包
1)、滑动水口钢包体由Q345R钢板制造,钢包高度沿材料轧制方向下料,钢板横向不得有接缝,钢包桶体按照国标、行业标准设计。
(钢包设计图需招标方确定)
钢包底部配滑动水口及底吹氩口。
滑动水口由液压驱动。
液压站共配3套均为双缸。
滑动水口机构及驱动液压站选用宜兴耐火材料有限公司产品。
精炼炉配钢包型号为20t单滑动水口钢包设备主要组成(钢包本体5台,包括VOD专用包2台,LF包3台,吊具2台)
单台钢包主要组成:
钢包本体1套
滑动水口装置1套
底吹氩口装置1套
吊具1套
材质Q345R
主要技术参数
最大容量25t
最小容量15t
钢包自由空间(mm):
≥1200按20tVOD时计算
2)、投标方按照国标、行业标为招标方配15t塞杆包若干,塞杆包不在LF精炼炉使用。
15t塞杆包需配钢包本体5台,吊具2台
单台15t塞杆包主要组成:
塞杆1套
钢包本体1套
15t钢水电动倾转包(钢包本体1台)
3.2.2、钢包罐车及拖缆装置(一套)
钢包罐车应设计合理实用,车体采用优质钢材焊接结构。
真空罐布置在钢包罐车上。
可沿轨道在吊包工位、LF工位、VOD工位移动。
真空罐是底部加强的钢板焊接结构件,主要由筒体、密封法兰、钢包座架等组成。
真空罐与真空罐盖一起构成真空容器,钢液包就放置在罐里进行脱气处理。
罐与罐盖间水冷法兰的密封靠O型密封圈,密封圈采用气动挡板保护。
真空罐内部设有二个具有导向功能的钢结构钢包座架,用来在作业时支撑钢包,和方便钢包顺利进入并定位。
要确保当钢水包放入真空管体内部时,罐车在行走状态下钢包无晃动。
在罐底底部设有一耐材砌筑的漏钢接槽,当钢水大量漏入接钢槽,钢水会融化安装在罐体底部的漏钢排放装置铝板,钢水会自动排到罐车轨道之间的漏钢坑内。
在真空罐底部设有漏钢报警装置。
氩气供应管路穿过法兰底下的罐壁与软管连结。
钢包就位后,人工通过快速接头接通钢包。
真空罐侧壁还开有与真空管路系统连接的伸缩接头对接法兰。
真空罐体同罐车同步设计,在满足使用的条件下,确保加热工位导电横臂长度为最小值,达到最佳使用条件。
钢包罐车传动方式为电机-减速器传动、分别驱动,选用变频器变频调速(所有变频器进出线必须增加电抗器,钢包车变频器选用西门子系列产品),可实现工频和变频之间转换。
定位误差±
10mm。
满足能够单台慢速驱动要求。
拖缆选用耐高温150℃电缆,拖缆架设隔热防护罩。
拖缆布置须满足现场工艺要求。
不得采用电动机内附抱闸。
车体上表面敷设有一层耐火砖以防止高温喷溅物体对车轮的损害。
钢包耳轴轴线方向与钢包罐车的行走方向垂直,钢包罐车传动机构上方设检修用活动盖板。
车体上部设平台供操作用。
钢包罐车上前后都设置牵引环,地面双向安装事故滑轮,以便在故障状态下,用外力将钢包车拖动。
考虑到工艺上的需要和操作上的安全,罐车的三个工位可以自动停止,也可在轨道的任意位置停留。
罐车的驱动设有联锁保护装置。
罐车的一侧与拖链(及水、电、氩气输送带)相连接。
精炼炉配1台钢包罐车,钢包罐车上座真空罐,随钢包罐车一起移动。
钢包罐车与真空罐的连接能拆卸。
单台设备的主要组成
真空罐体材质Q345R
耐材(招标方提供,投标方砌筑)
钢包车运行速度2~12m/min
钢包车驱动方式变频驱动
钢包车定位精度±
10mm
钢包车承载能力80t
密封圈直径:
投标方设计
主体材料:
Q235B
3.2.3、电极升降机构
电极升降机构由电极升降液压缸、电极升降立柱、立柱升降导向轮装置、导轮润滑系统、导电横臂、电极夹头、夹紧弹簧及电极放松液压缸等部分组成。
电极升降立柱上托架与横臂之间为高强度耐高温云母板。
电极升降柱塞式液压缸安装在立柱内,立柱采用无缝钢管及钢板焊接成前后对称的菱形结构,其上面设有四个导轨面,导轨面需经中频淬火处理,有很好的耐磨性。
导电横臂、立柱升降导向轮装置安装在机架上,导向轮采用电动集中润滑。
并设置三相电极立柱锁定装置。
电极升降柱塞式液压缸需带自锁功能。
导电横臂用铜-钢复合板(铜板4mm/钢板12mm)焊接成水冷箱形结构。
电极夹头主体采用T2紫铜锻件,内通水冷却,顶部进出水,水路外置。
电极抱紧带采用非导磁奥氏体不锈钢焊成水冷结构,与石墨电极接触的压块与抱紧带绝缘。
电极放松缸具有互换性,是特殊设计的专用油缸,内装有蝶形弹簧。
为了便于检修、更换活塞密封圈,活塞与活塞杆是分开的,在夹持电极的状态下即可方便的更换密封圈。
电极立柱为无缝钢管焊接而成。
导轨采用含Mn厚钢板经机加工并硬化处理。
导轨为倒燕尾形状。
电极升降油缸置于立柱内部,为独立的、可整体拆卸的结构;
油缸的密封端盖材质为球墨铸铁。
横臂与立柱连接的托架,采用钢板焊接制成,采用低导磁奥氏体不锈钢材质,横臂设调整装置,可方便前后左右调节横臂位置,以保证三相电极极心圆的正确位置。
横臂所有管路均采用不锈钢材质。
设备主要组成投标时需提供部件明细及报价
立柱与横臂连接紧固所需工具1套
电极直径Φ300mm高功率电极
电极分布园直径投标方详细核算
导电横臂形式铜钢复合
钢水升温速度≥4.5℃/min(20t钢水时)
电极调节器性能参数投标时说明选型及参数
3.2.4、水冷炉盖
水冷炉盖能够接收合金料、造渣料并导入钢包,具有观察和人工测温取样门。
水冷炉盖采用全水冷管式炉盖,用无缝钢管(壁厚≥10mm,密排弯头处钢管厚度要≥10mm,材质GB35310-2008高压锅炉用无缝钢管)焊接而成,形成均流无死点的高效水冷强制循环。
本炉盖在结构上分成两层,底层环盖有侧壁。
本水冷炉盖内部各处均布有V型挂渣钉,在冶炼过程中自动挂渣,以提高炉盖的使用寿命和热负荷效率。
电极孔上层三个孔,电极孔周边放置打结成形的绝缘耐火模块,以保护水冷管。
顶层小盖与炉盖本体为固定连接,顶层小盖上做一水冷炉盖锥圈,打结耐火材料。
炉盖前侧开有炉门,用于测温、取样、加料,炉门设计为手动,可保证炉门封闭严合。
在炉顶上部要预留在线喂丝口,喂丝口要加装护盖。
电极孔绝缘材料(耐火材料)两套(投标方提供图纸及一用一备)
水冷炉盖直径投标时说明
水冷炉盖使用寿命≥6000炉次(正常冷却条件下)
3.2.5加热桥架
加热桥架是加热工位的基础构架,横跨钢包车运行轨道,由导向托架、立柱、横梁、平台、栏杆及扶梯等组成,加热炉盖上方更换电极的平台采用不锈钢材质。
加热桥架主要为钢板和型钢焊接而成。
导向托架上设有导向装置,用于电极升降机构立柱的导向,分上、下两层,上下层滚轮数量一致。
导向轮须设计为可调整方式。
由于除尘采用半密闭罩形式,为节省空间设计加热桥架时,预留半密闭罩的安装空间及载荷(按20吨计算)。
设备主要组成投标时需提供部件明细及报价
3.2.6炉盖提升机构
炉盖提升机构由两个单向作用活塞液压缸、导向链轮(内装滚动轴承)、链条及联接件组成。
安装在加热桥架的横梁上,由液压缸带动链条来实现炉盖的上升,炉盖的下降靠自重来实现,炉盖的同步由同步轴来实现,以保证其平衡升降。
炉盖升降行程提升至最高处时要确保罐车带防溅盖可以通过
炉盖升降速度根据参数设计
3.2.7液压系统
液压系统是用于驱动电极升降、炉盖升降、电极放松、真空罐盖升降、管道连接器的开闭、真空主阀开闭的液压动力装置。
它由主液压源装置(电机、液压泵、油箱及液压附件)各个控制回路(滤油回路、溢油回路、电极升降回路、炉盖提升回路、电极放松回路、真空罐盖升降回路、管道连接器的开闭回路、真空主阀开闭回路)以及循环泵装置、事故用蓄能器等组成。
1)液压泵装置
a)液压系统采用2台进口美国派克恒压变量泵,控制形式为1用1备。
如一台工作泵出现故障,可通过电气控制系统及时将故障泵切除,将备用泵导入,采用落地布置。
b)每台泵装置配压力保护功能和压力过滤器,以保证向系统输入高精度工作介质。
c)液压泵装置配单向阀,高压球芯截止阀等液压附件。
d)液压泵装置上配压力表、测压点和测压装置,检测人员可随时对系统进行检测。
2)油箱总成
a)液压系统油箱及管道均采用不锈钢材质。
b)油箱配液位计和液位传感器,用于对油箱液位进行监控和报警,同时还可参与系统PLC控制。
液压泵吸油口碟阀有限位开关并保证碟阀关闭后液压泵不能启动。
c)油箱配双金属温度计与一个温度传感器,用于对油箱温度进行监控和报警,同时还可参与系统PLC控制。
d)油箱配单独的循环过滤冷却系统,60min可将油箱的介质按照控制要求过滤(10μ)冷却一次,以满足液压系统对介质的要求,确保系统在正常范围内运行,介质温度保证自动调节。
e)油箱配空气滤清器、排污口等必备附件。
3)蓄能器站
蓄能器采用国产皮囊式储能器组(采用若干个),在停电状态下能实现一次将电极和水冷炉盖提至最高,使钢包车具有移动条件。
仍能保证VD真空处理顺利完成主要的操作。
4)控制阀组
a)电极升降控制:
电极升降采用了四台电液比例阀(3台工作,1台在线备用),分别对三相电极升降进行自动控制及手动控制。
电极升降控制具有失去动力源情况下的自锁功能。
b)电极松开控制:
采用二位四通电磁换向阀控制,结构简单、动作可靠。
c)其它动作控制:
均采用滑阀控制,并根据动作要求采用不同的液压原理控制。
d)各液压阀块的进、回油管路上都需增加检修用球阀门,主油管路上安装卸荷用球阀门。
4)液压系统总体要求
a)恒压变量泵和比例阀、滑阀、球阀、倾炉油缸用单向阀选用派克产品,所有液压缸均选用天津尤瑞纳斯产品,所有密封件全部使用派克产品。
所有压力传感器选用美国罗斯蒙特(就地显示及远传)产品,所有滤油器选用温州黎民产品。
所有管道均采用不锈钢材质。
b)液压系统恒压变量泵及全部阀站必须与油箱分离落地安装。
c)系统各过滤器过滤精度必须保证比例阀等液压元器件对介质的清洁度要求。
并提供一套备用过滤芯,过滤器污染度应能由控制系统自动监测同时在工控机屏幕上显示。
液压油品清洁度要求比例阀系统NAS6级。
d)液面、各部分压力指示仪表应安排在容易观察巡视的位置和方向。
e)液压站配线与电炉控制系统要求一致,各阀台出线箱一律用端子板,不得采用航空插头,液压站电气线路线号标识清晰,且应提供准确的液压站电气接线图纸。
f)提供配套的变量泵、比例阀中文技术资料。
g)液压系统安装严格按《YBJ207-85冶金机械设备安装工程施工及验收规范-液压、气动和润滑系统》进行安装、焊接、酸洗、冲洗及试运转。
所有的管道安装结束,应全部拆下进行酸洗、钝化。
h)提供土建资料时,应同时提供液压站预埋穿线管布置图。
I)每个阀台带有用铝板制作的系统原理图,并用螺钉将其固定在阀台正面面板上,该面板上还配置有压力表与测压软管。
各液压元件上也牢固地装贴相应于原理图上的元件编号的硬质标牌。
控制阀的电磁铁应根据原理图的代号进行统一标号,并牢固打印在阀块的相应位置或相应的电磁铁上。
J))每个阀台的结构形式为:
带集油盘,正面树面板;
P,T,L总管从侧面进出,到液压缸的支管从背面敷出。
阀台的每个出口(到液压缸)都配置成对的进口法兰(或接头)、球阀。
L)阀块联接采用高强度螺栓,为每台比例阀、伺服阀配冲洗板。
M)所有箱体内的端子采用国内一线品牌,并留有20%以上的余量。
N)控制阀尽量使用叠加阀。
所有电磁线圈均为湿式。
恒压变数泵2台(美国派克)
主泵电机2台
比例阀4件(美国派克)
截止阀1套
不锈钢件油箱1件
附件1套
皮囊式蓄能器(100L)1套
循环装置1台
液压介质脂肪酸脂
系统过滤精度10μ
3.2.8水冷系统
系统由两个回路组成:
第一路为一般水冷系统,采用开环系统。
主要冷却部位有短网中的导电铜管、水冷电缆、导电横臂、电极夹头、立柱上部水箱、液压站、变压器油水冷却器、车载罐口水冷法兰密封槽、VD/VOD系统等。
供水压力0.3-0.4MPa。
第二路为专用水冷系统,采用闭环系统,主要冷却水冷炉盖、VD/VOD炉盖、氧枪。
供水压力为0.5~0.6MPa,回水压力为0.2~0.25MPa。
两个水冷回路均应设置进回水流量监测(并在控制界面显示流量数值及流量差),系统总进水设有压力、温度的监测、显示(就地和远传)、报警装置。
总回水设有压力、温度监测、显示(就地和远传)、报警装置。
回水各支路设有温度显示(就地和远传)、报警装置。
所有仪表全部更换,采用上仪、川仪产品,水冷各支路进、回水阀门全部为不锈钢阀门。
集中水箱材质要求为不锈钢水箱,其上部进回水管路全部为不锈钢管路,其余管路可根据需要采用焊接管路或带钢网的软性管路。
水冷系统所有设计和信号采集必须符合最新国家安全标准。
正常用水:
工作压力闭环0.5-0.6MPa,开环0.3-0.4MPa
进水温度≤35℃
回水温度≤55℃
水质要求按照GB10067.1-88《电热设备基本技术条件》有关规定。
3.2.9氩气系统
吹氩系统采用管道氩气供应,精炼炉加热工位设调压装置,由氩气系统为钢包罐车提供氩气。
氩气系统由总进气管路、阀站箱、输气管路等组成。
总进气管路为一路,设有就地压力表、压力变送器、过滤器、手动阀门。
总进气管路进入阀站箱内再分成两路。
氩气装置主要由质量流量计、精量调节阀(美国费西尔)、截止阀、减压阀、单向阀、压力表、压力变送器、旁通支路等组成。
氩气调节精度要达到5ppm以下。
系统单独设置氩气阀站箱。
精炼炉加热工位吹氩操作均在主画面进行,氩气流量可自动调节。
系统可对吹氩压力和流量自动跟踪。
主路及旁通支路可通过管路上压力的变化进行自动切换。
当系统出现断路情况,系统自动关闭并发出警告。
在现场设置手动氩气调整装置。
设备主要组成及数量投标时需提供部件明细及报价
工作压力0.3~0.8Mpa事故1.6Mpa
耗量(10~300)NL/min
纯度99.999%
3.2.10压缩空气系统
压缩空气系统用于各气缸的气路控制、喂丝机的调整。
真空炉盖气动动作部分,喂丝机气动动作。
3.2.11集中润滑系统
设备功能:
集中润滑系统其润滑点为电极立柱导向轮轴承及炉盖升降装置的链轮轴承。
当需要润滑时,通过操作电动干油泵,经润滑脂分配器到导向轮轴承和链轮轴承,从而达到集中润滑目的。
润滑主管路为不锈钢管,支管路为紫铜管。
电动泵自动控制可将润滑周期编入程序,电动泵周期运转,润滑脂定期润滑设备,亦防止管路中的润滑脂凝固,造成管路阻塞。
主管路为不锈钢管,支管路为紫铜管。
润滑系统要进入PLC连锁,确保在生产过程中可以人工启停。
贮油器容积根据参数设计
最大工作压力根据参数设计
润滑介质耐高温干油脂
润滑脂针入度≥350
3.2.12测温装置
钢水测温表选用带字高5英寸大显示二次仪表(带蜂鸣器),信号线长约50米,测温枪共8支,长度根据现场的工况设计。
测温设备主要组成及数量
测温枪8只
测温仪2套(一套贺力士,一套北京科海)
测温两处显示大屏幕(带蜂鸣器)2套
3.2.13电极接长装置4套
电极接长装置由电极夹放装置、支座、防护筒以及卡具等组成。
每套电极接长装置能同时接长与存放四根电极。
3.2.14喂丝设备
喂丝机采用四线喂丝机,设置高喂丝平台,满足在加热工位通过喂丝孔直接进行喂丝,喂丝速度要求为20-300m/min,丝线直径为8-18mm。
平台搭建完成后喂丝机及其现场控制柜放置在二层平台,丝线放置在精炼炉平台上,通过平台孔洞进入喂丝机后,经喂丝设置,由弯管进行四孔汇聚后,进入加热炉盖喂丝孔。
平台设计、喂丝管路设计、安装等全部由投标方完成。
喂丝机可满足现场、远程双控制的能力。
远程控制画面,必须能显示、记录丝线运行长度、速度、种类。
喂丝机型式四线喂丝
喂丝速度20~200m/min
包芯丝直径Φ8~18mm
铝丝直径Φ8~18mm
3.2.15在线定氢、在线定氧各一套
配置在线定氢仪、在线定氧仪各1套,选用贺利氏产品。
并配置枪体各三套。
(预留)
设备安装和调试由招标方负责。
3.3高低压电气及自动化系统
3.3.1二次短网与大截面水冷电缆
二次短网主要包括软连接补偿器、穿墙铜管、大截面水冷电缆以及短网不锈钢支架、阻容保护装置等。
变压器采用顶进侧出,大电流线路是指变压器二次侧出铜管以后,由补偿器组、穿墙铜管组、大截面水冷电缆、导电横臂、以及石墨电极等组成。
其铜管的起始端与变压器二次出线铜管之间,采用柔性补偿器,连接补偿器是由0.5mm紫铜皮叠加而成。
穿墙铜管组及水冷电缆的支承处均由强非导磁不锈钢的支架承托,并用绝缘件衬垫。
铜管组选用了较大截面,使其每相短网系统的电阻和电抗最小,同时使其三相电抗相等。
每相两根水冷电缆,电极升降机构升到顶和降到底时水冷电缆两端均有一定的直线段。
二次短网空间布置充分考虑三相电参数的平衡,在出墙铜排和大电缆段,对中相横臂电抗缺失进行补偿;
出墙铜排与大截面水冷电缆的联结处,为空间三角形布置;
使短网静态三相不平系数≤4%,每相电抗绝对值≤2.46mΩ(包括电极)。
设备主要组成及数量投标时需提供部件明细及报价
短网系统阻抗≤2.46mΩ
三相阻抗不平衡系数≤4%
3.3.235KV高压供电系统
高压供电系统主要用于10t电弧炉高压供电及高压保护。
招标方负责将一次进线引入高压室内,其余部分全部由投标方负责。
所有高压检测实验投标方负责,招标方可以提供信息。
高压开关柜功能满足行业标准“五防”要求,壳体采用静电喷塑处理。
(1)高压主回路系统
高压供电系统由进线隔离手车开关及电压互感器、真空断路器、电流互感器、氧化锌避雷器及阻容吸收保护装置等组成,构成高压进线柜、真空断路器柜、避雷器及阻容吸收保护柜。
所用高压断路器为真空型,主要用来接通或断开主回路、切断由于电弧短路而造成的过电流。
设备名称
数量
安装位置
高压进线柜
1面
高压室
真空断路器柜
高压保护柜
(2)基本功能
高压供电系统向10t电弧炉提供35kV主电源,并可进行主回路短路保护,在高压回路设置过电压吸收装置,吸收操作过电压及浪涌电压,以保护变压器,氧化锌避雷器能够进行防雷击保护。
高压开关柜满足“五防”要求。
高压系统的真空断路器合、分闸在高压室的柜面设本控/远控选择开关,可在高压室和主控室两地操作控制。
调压方式:
有载电动调压,采用直调调压。
高压开关柜上安装有高压电压、电流等计量仪表。
高压开关柜选用KYN型交流金属封闭式高压开关柜。
高压开关柜配有直流屏,能够保证:
当低压电源故障时,高压真空断路器仍能实现正常合、分闸操作功能。
高压开关柜具有防止误操作联锁装置,闭锁功能符合SD318<
<
高压开关柜闭锁装置技术条件>
>
的要求。
高压开关柜由具有相应生产能力和资质的专业厂家生产。
随设备附符合国家标准的出厂试验报告。
变压器油选用克拉玛依炼油厂产品(投标方提供首次运行添加油),油水冷却器选用不锈钢螺旋板式。
(3)高压主回路保护:
采用微机综合保护仪,选用南京南瑞,西门子,ABB产品。
计量和保护包括高压系统二次侧监测仪表及保护,能够对高压系统的电压、电流、三相有功功率、三相多功能电度表、三相功率因数进行显示及监测。
1)35kV进线,电磁操作真空断路器(两台断路器手车,一工一备,手车导轨应有足够强